Технология изготовления арболита. Арболит: технология производства, состав
Производство строительных материалов на сегодняшний день — довольно прибыльная отрасль. Обусловлено это высоким спросом на все, что связано с возведением зданий. Все застройщики стараются применять и проверенные материалы и внедрять новые технологии, которые будут менее затратными в себестоимости и более практичными в применении.
Несмотря на огромный ассортимент строительных блоков, огромной популярностью стал пользоваться и арболит. Технология производства его зависит от того, в каких условиях он изготавливается. Сам материал обладает отличными эксплуатационными свойствами и характеристиками.
Что такое арболит?
Это строительный материал, который выпускается в виде блоков. Они имеют определенные размеры и состав. Благодаря тому, что в его производстве используется натуральное сырье, он обладает отличными техническими характеристиками.
Способы производства арболитовых блоков
Технология изготовления арболита может быть применена:
- в заводском производстве;
- при домашнем изготовлении.
Сырье для производства арболита
Технология изготовления арболита характеризуется применением определенных материалов:
- бетон марки 400 или 500;
- химическая добавка;
- органический заполнитель.
Есть некоторые рекомендации по выбору сырья. Например, бетон нужно покупать тот, который изготавливается на основе вяжущего вещества. Также можно применять бетон более высокой прочности. В качестве химической добавки используют жидкое стекло, хлорид или нитрат кальция. Органические наполнители: древесная стружка, дробленые стебли хлопчатника, дробленая рисовая соломка и многое другое.
Арболит, технология производства которого отличается применением определенных средств, может иметь различный удельный вес. Например, блоки, имеющие плотность менее 500 кг/м3 относят к группе теплоизоляционного арболита. А те, которые имеют плотность более 500 кг/м3, принадлежат уже к группе конструкционных блоков.
Соответственно, первый вариант арболита наиболее часто используется для сооружения межкомнатных перегородок, а вот из второго выстраиваются несущие арболитовые конструкции.
Стадии изготовления материала
Технология изготовления арболита состоит из нескольких этапов:
- подготовка определенного количества органического заполнителя;
- работа по замачиванию древесной щепы в растворе хлорида кальция;
- дозирование определенных составляющих арболита;
- непосредственно изготовление блоков.
Подготовка органического заполнителя
Любое производство строительных материалов характеризуется предварительной подготовкой всего необходимого сырья. Древесина в брусках измельчается и формируется в определенные кучки. Их надо положить под навес и выдержать при оптимальной наружной температуре +15…+25 градусов около 1 месяца. После этого древесина измельчается в специальном оборудовании на щепку.
Только к такому действию нужно подходить ответственно. Щепа имеет свою определенную фракцию. Именно от нее зависит качество арболитовой смеси. Щепка размером в 10-20 мм характеризует фракционный состав в 70%, 5-10 мм уже относят к 30% фракции.
Замачивание древесины и приготовления раствора хлорида кальция
Полученную в ходе дробления щепку необходимо замочить в воде. Температура жидкости при этом должна быть не менее +20 градусов. Весь процесс замачивания длится до 6 часов. Все эти действия помогают увеличить прочность арболитовых блоков. Необходимо постоянно следить за наполняемостью древесины водой. Влажность полученного сырья должна быть не более 30%.
По истечении этого времени в бак с жидкостью выливается заранее приготовленный раствор хлорида кальция. В эту же емкость отправляется и пенообразователь.
Дозирование составляющих будущего строительного материала
Важный этап, которым обладает технология изготовления арболита, является правильное дозирование всех компонентов. Именно от этого зависит качество арболитовых блоков и его показатель прочности. Дозировка дробленой замоченной щепки должна учитывать влажность сырья. Все ингредиенты взвешиваются и дозируются согласно определенным установленным параметрам (ГОСТ). Можно использовать для этого процесса специальное оборудование. Нужно учитывать, что оно достаточно дорого, и в условиях некоммерческого производства покупать его нецелесообразно.
Процесс изготовления блоков
Необходимо подготовить специализированное оборудование для арболита. К нему на этапе смешивания ингредиентов относят бетономешалки и другие приспособления, которые могут качественно перемешивать смеси высокой плотности и доводить их до определенной консистенции.
Большую роль играет очередность закладки составляющих. Изначально засыпается подготовленная древесная щепка. Затем – цемент. После этого заливается вода и химические наполнители. Они могут меняться местами в производстве. Кому как будет удобно. Только подачу всех жидкостей стоит пропускать через специальный расходомер.
Далее происходит смешивание сырья. Мешать нужно до тех пор, пока смесь не станет однородной.
Необходимо заранее изготовить формы для блоков. Как правило, они деревянные, а размеры могут быть любыми. Внутри нее по всему периметру выкладывается линолеум. Он даст возможность после застывания смеси свободно вытащить блок из формы. Также его поверхность промазывается специальным средством.
Довольно часто в домашних условиях изготовления арболитовых блоков применяется вибростол. Он позволяет равномерно распределить смесь. После этого залитые составом формы выставляются под навес и находятся там до полного застывания. В некоторых случаях применяют определенные добавки, которые помогают сократить время отвердения цементного состава.
Строительство из арболита, который сделан в домашних условиях, может проводиться только по истечении определенного срока, обычно через 14-20 дней. За это время блоки полностью отвердеют, высохнут и будут готовы к кладке.
Технология изготовления качественного арболита — ЭкоДревПродукт
Состав, требования и этапы изготовления арболита
Технология производства арболита заключается в объединении двух натуральных компонентов: чистого портландцемента и отходов деревообрабатывающей/лесозаготовительной промышленности — древесной щепы. Главным критерием, обеспечивающим соответствие строительных блоков на основе арболита регламентам стандарта, является применение качественных деревоматериалов. Они должны соответствовать следующим параметрам:
- Низкая сучковатость. В идеале сучков не должно быть вовсе.
- Отсутствие коры. Примеси древесной коры способны испортить готовые блоки, поскольку данный биологический материал обладает совершенно иными свойствами, нежели древесина, намного быстрее разлагается.
- Низкая влажность. При использовании древесных компонентов с высоким уровнем влажности добиться качества арболита не представляется возможным, поэтому щепу предварительно просушивают.
- Отсутствие разрушающих структуру древесины биологических процессов. Щепа, на которой обнаружены следы гнили, колоний плесневых грибов, непригодна для производства арболитовых блоков.
Для измельчения деревоматериалов, древесных отходов до состояния щепы используются специализированные щепорубительные агрегаты. Готовый компонент блоков из арболита — щепа — должна быть практически однородной по размерам.
Этапы изготовления арболита
- Изготовление щепы. Преимущественно для этих целей используется древесина большинства видов деревьев хвойных пород, но можно применять и другие, характеризующиеся повышенной стойкостью к биологическому разрушению — осина, береза. Плохое качество готового арболита может быть обусловлено применением деревоматералов из бука, лиственницы.
- Минерализация щепы. Данная процедура необходима для придания этому компоненту повышенного уровня адгезии с портландцементом. Для этих целей применяется хлористый кальций, реже — сернокислый алюминий.
- Смешивание предварительно минерализованной щепы с остальными компонентами — цементной массой и связующим составом. После тщательного перемешивания полученную смесь заливают в предварительно подготовленные формы, затем оставляют для затвердевания. Длительность данного процесса зависит от многих условий, главным из которых является температурный режим.
Бизнес план производства арболитовых блоков. Свой цех с нуля.
Арболит в народе еще называют древесным кирпичом. Это недорогой, а главное экологически чистый материал, который используется при малоэтажном строительстве или в качестве утеплителя для несущих стен. В его состав входит деревянная щепа или стружка, цемент и вода. А для организации всего бизнеса на производстве арболита, вам потребуется совсем немного оборудования, которое можно будет окупить в течение года.
Если говорить о процентном соотношении состава этих блоков, то в большинстве случаев стружка занимает около 60% – 85%, а цемент 15% – 40%, в зависимости от рецептуры.
Где брать сырье?
Содержание статьи
Наверное, это один из наиболее часто задаваемых вопросов, который касается этой бизнес идеи. Основным материалом, из которого изготавливаются эти блоки – это отходы от древесного производства (опилки, стружка). Часто это сырье можно купить по невысокой цене, или же и вовсе доставать бесплатно. За счет такой экономии, получается и невысокая себестоимость произведенной единицы блока, а рентабельность при этом растет. Главное подписать договор с несколькими деревообрабатывающими предприятиями, для того чтобы иметь стабильный поток нужного сырья для бизнеса на арболите.
Преимущества материала
В строительстве арболит позиционируется как материал для возведения малоэтажных конструкций, с отличными техническими показателями. К тому же ценник его ниже чем, скажем того же газоблока, что тоже играет важную роль для многих клиентов. Вот основные плюсы, которые вам нужно знать об арболите.
1.) Этот материал является экологически чистым, что в свою очередь привлекает клиентов, которые заботятся о здоровье своей семьи.
2.) Такие блоки при правильной технологии изготовления не подвергаются действию грибка и гниению, а также с ними удобно производить любые нужные операции – распил, шлифовка.
3.) Высокие звуко и теплоизоляционные характеристики.
4.) Высокие показатели огнестойкости. Из такого материала можно строить объекты, которые имеют повышенный показатель пожарной безопасности.
5.) За счет своей структуры, которая состоит из пор, обеспечивает конвекцию воздуха в помещении, а также нормальный уровень влажности.
6.) Арболит достаточно легкий, и здания, построенные с его использованием достаточно долговечны.
7.) Хорошая рентабельность, простой процесс производства, а также минимальная себестоимость.
Весь этот перечень характеристик и обеспечил арболиту популярность на рынке строительных материалов.
Из таких блоков возводят не только жилые дома, но и летние кухни, подсобные помещения, гаражи и прочее.
Документы
Перед тем как запустить производство вам нужно зарегистрироваться как ИП или как юр. лицо. Вторым шагом станет подбор системы налогообложения и указание ОКВЭ на деятельность.
Из разрешительной документации нужно будет еще разрешение от СЭС и пожарного надзора.
Поскольку данный вид деятельности подразумевает под собой подключение рабочих (4 разнорабочих, бухгалтер, менеджер по продажам), вам нужно будет оформить их и платить ежемесячные взносы.
Не забудьте заключить договор аренды или купли-продажи на помещение.
Технология производства арболитовых блоков
Стоит сразу отметить, что арболитовые блоки бывают также разных марок, которые в зависимости от процента в составе древесной стружки используются для различных целей. Например, марки: М5, М10, М15 используются для утепления стен, а от марки: М25, М35 для возведения несущих конструкций.
Для запуска технологического процесса вам нужно будет следующее сырье:
- цемент марки 400 или 500.
- деревянная щепа и опилки.
- химические смеси для обработки древесины.
- вода.
К примеру, для изготовления 1 куб.м. арболитного блока марки М15 используют следующую рецептуру:
- щепа — 240-300 кг.
- цемент — 250-280 кг.
- химические смеси — 12 кг.
- вода 350-400 л.
Для следующих марок, уменьшают объем щепы и увеличивают процент цементного состава.
Сам технологический процесс производства можно разделить на несколько этапов:
- загрузка отходов древесины в устройство для рубки. Также сюда добавляют сернокислый алюминий или хлористый калий и прочие химические добавки, для обработки древесины. В установке производит разрубка отходов до необходимых размеров.
- далее в смесительную установку (бетономешалку) кроме щепы добавляют цемент и воду. На этом этапе получаем готовую арблитную смесь.
- готовый раствор разливают по пресс формам, и с помощью ручной трамбовки производится ее уплотнение. Если позволяет бюджет для этого этапа покупают вибростол.
- после завершения предыдущего процесса, блоки извлекаются из формы и отправляются в сушильную камеру на 2-3 дня.
- перемещение готовых блоков можно производить только через неделю. А сам материал можно использовать для строительства только через месяц.
Как видите, производство арболита, как бизнес не содержит в себе каких-то сложных технологических решений. Здесь главное соблюдать рецептуру и этапы трамбовки и сушки блоков в целом.
Помещение
Для небольшого цеха нужно будет арендовать как минимум 200 кв.м. 50 кв.м. площади, из которых выделить на цех, 75кв.м. на сушильную камеру и 75 кв.м. на складские помещения для готовой продукции.
Помещение должно быть вентилируемым, а также нужно, чтобы была подведена холодная вода. Обязательно наличие электросети 380В.
Не забывайте о системе пожарной безопасности, а также видеонаблюдении и охранной сигнализации. Это снизит риски потери оборудования, и вы точно будете спать спокойней.
Узнайте, как запустить собственное производство брусчатки. Выбор сырья, оборудования и технологии изготовления.
Оборудование
Комплект оборудования можно покупать либо в формате готовой производственной линии, либо формировать его самостоятельно. К тому же можно сэкономить, покупая б/у установки, и снизить ценник на оборудование до 40%. Но нужно внимательно смотреть на степень износа станков и просчитывать реальную выгоду от такого шага.
1.) Смесительная станция — $3750.
2.) Ручные трамбовки — $500/комплект. Или же вибростол – $700 за шт.
3.) Пресс формы — $120 за штуку. Для начала вам нужно будет закупить около 25 – 35 штук. Приблизительная сумма будет около $3600.
4.) Камера для сушки продукции – $8000.
5.) Устройство для рубки щепы — $4600.
6.) Поддоны для готовой продукции — $1000.
7.) Машина для транспортировки готовой продукции на поддонах (при наличии достаточного финансирования). В общие расходы мы не будем включать этот пункт.
Общая сумма – около $21 450.
Ту же сушильную камеру, которая съедает львиную долю бюджета, на первых порах можно не покупать и использовать для этого просто сухие помещения с отоплением, а со временем уже задуматься о таком профессиональном оборудовании.
Рынки сбыта
Наилучшим решением будет наладить оптовый сбыт продукции. В таком случае вы сможете работать с большими объемами.
Реализовывать можно на:
- оптовые и розничные базы и магазины строительных материалов;
- напрямую через менеджеров продаж с личными связями;
- через объявления в СМИ.
Но не стоит полностью отказываться от розничных продаж. Ведь даже частный клиент при постройке дома может закупать неплохие партии блока, да еще и по розничной цене. Поэтому тут, скорее всего, нужно комбинировать и то и другое. И очень большую роль в росте продаж будет отыгрывать менеджер по реализации арболита.
Расходы на бизнес
Какой же бизнес план без расчета основных затратных частей. Тут стоит выделить что в случае с арболитом стартовый капитал нужен совсем небольшой, и при этом его всегда можно подкорректировать за счет покупки того или иного оборудования. Мы будем разбирать покупку сразу готовой производственной линии.
Базовые затраты:
- покупка и наладка оборудования – $21000
- ремонт в помещении и подвод нужных коммуникаций – $80 на 1 кв.м.
- закупка сырья – $8000
- оформление документов – $200
Ежемесячные вложения:
- арендная плата за помещение – $9 — $12 за 1 кв.м.
- коммунальные платежи
- налоги – от $150
- заработная плата – от $200 на одного сотрудника
- транспортные расходы – $100
Стоимость ежемесячного содержания бизнеса можно снизить за счет работы в своем помещении, или же сокращении штата сотрудников, для более эффективного использования рабочей силы в целом.
Сколько можно заработать?
Допустим, что объем вашего производства будет равен 450 куб.м. арболита в месяц. Так в случае реализации по оптовой цене, которая в среднем равна $40/куб.м. тогда сумма выручки составит – $18000 в месяц. При розничной реализации ($50/куб.м.) выйдет – $22500.
Из этих сумм можно вычесть ежемесячные расходы, а также себестоимость производства блока. Чистая прибыль будет в районе $5000 – $7000.
Окупаемость бизнеса при таких объемах продаж составит около 9 – 14 месяцев.
Выводы. Заработок на арболитовых блоках – это вполне реализуемая бизнес идея малого производства, которая при сравнительно небольших денежных вложениях может приносить хороший доход. Важно только найти рынки сбыта и закупить хорошее оборудование для получения качественных блоков, а далее можно масштабировать бизнес.
Есть опыт работы в этом сегменте рынка? Ждем ваших отзывов и рекомендаций.
Технология изготовления арболита
Арболит, технология изготовления которого проста и малозатратна, как строительный материал известен достаточно давно.
На территории СССР действовали более трехсот предприятий по производству изделий из опилкобетона и этот материал был чрезвычайно востребован в гражданском и промышленном строительстве, благодаря низкой себестоимости, отличным теплоизоляционным характеристикам и простоте изготовления.
Преимущества арболита
Арболит, состав которого разработан в исследовательских институтах Советского Союза в 60-е годы 20 века, является одним из самых простых в изготовлении штучных строительных материалов. Универсальность опилкобетона такова, что из него можно производить блоки любой формы и размера.
Арболитовые блоки могут быть армированными, декорированными, пустотными и т. д. Несмотря на то, что основой арболита являются отходы древесины, блоки из этого материала получаются прочными, легкими и устойчивыми к деформации. Арболит отлично обрабатывается, его можно сверлить, распиливать, штукатурить.
Технология
Несмотря на то, что технологически возможен выпуск арболитовых элементов любой формы и размера, чаще всего встречаются прямоугольные арболитовые блоки стандартного размера 250×250×500 миллиметров.
Именно такой тип блоков наиболее удобен при кладке наружных стен и перестенков и позволяет комбинировать арболит с другими строительными материалами, например стандартными пенобетонными блоками.
Арболитовые блоки изготавливают путем отливки в специальных формах, которые могут быть изготовлены как из металла, так и из досок толщиной 2–2,5 сантиметра.
Внутреннюю поверхность формы обязательно покрывают полиэтиленовой пленкой, что обеспечивает минимальную агдезию и облегчает выемку готовых изделий.
Масса для заполнения форм изготавливается из опилко-стружечной массы, химических реактивов, цемента и воды. Опилки и стружки перемешивают в одинаковой пропорции и добавляют немного известкового раствора. В этом состоянии масса выдерживается несколько дней.
Это необходимо для того, чтобы из древесины ушли сахариды, которые будут мешать застыванию готовых блоков в формах. Вяжущим веществом в арболите является портландцемент марки не ниже М400, к которому добавляют различные присадки, которые препятствуют гниению и повышают огнестойкость и пластичность раствора.
Для придания арболиту различных дополнительных свойств используют гашеную известь, жидкое стекло, сернокислый алюминий, кальций.
Пропорции арболита
Чтобы правильно подготовить раствор, в воде сначала растворяют жидкое стекло и известь. Только после этого воду добавляют в опилочную смесь и добавляют цемент. Полученное сырье тщательно перемешивают в растворомешалке, после чего раствор готов к укладке в подготовленные формы.
Арболит в формах тщательно трамбуют и оставляют на сутки. После этого блоки можно аккуратно вынуть из форм и на две-три недели разложить для просушки под навесом.
Опыт показывает, что для изготовления 10 блоков стандартного размера, нужно 70–75 кг цемента, 2 литра жидкого стекла, 2–2,5 кг извести и 80–90 кг древесных отходов. Расход воды в этом случае составит приблизительно 130 литров.
Таким образом, при небольших затратах, путем несложного технологического процесса, в котором не участвует дорогостоящее оборудование, любой хозяин может получить качественный теплый материал для дома, хозяйственной постройки или цеха.
Видео: Как делают арболит
youtube.com/embed/ATLV8D9ettY?feature=player_detailpage» allowfullscreen=»» frameborder=»0″/>
Технология изготовления арболитовых блоков своими руками
Слово «арболит» произошло от французского «arbre», что в дословном переводе означает дерево.
Арболит представляет собой легкий бетон, изготовленный на базе цементного вяжущего, химических добавок и органических заполнителей, которых в составе смеси содержится до 90% от общего объема.
В качестве строительного материала арболит был стандартизирован в Советском Союзе еще в шестидесятые годы.
Такой материал известен еще под названием древобетон. Арболитовые блоки начали использовать еще в период 60-х годов прошлого века. Производство и дальнейшее использование арболита имеет множество преимуществ, если сравнивать его с традиционными стройматериалами.
Арболитовые блоки способны снизить массу зданий, сократить трудоемкость их возведения, снизить расход цемента и песка в 2,5 раза на 1 квадратный м. Кроме того, конструкция из этого материала способна демонстрировать значительное термическое сопротивление. Арболитовые блоки, имея крупнопористую структуру, способны обеспечить отличный воздухообмен во внутреннем пространстве помещений и превосходные теплотехнические показатели, что значительно снижает расходы на вентиляцию и отопление зданий. Применение арболита в строительстве исключает необходимость проводить дополнительные работы по наружной звуко- и теплоизоляции.
Строение блока арболита.
В современном строительстве многоэтажных домов, которое предполагает применение несущих каркасных монолитных элементов, в особенности актуальным считается использование мелкоштучных блоков из арболита, когда как оптимальная толщина самонесущей ограждающей стены равна З90 мм, что эквивалентно 1 метру кладки из кирпича. Это позволяет получить экономию материальных затрат и стройматериалов.
При индивидуальном строительстве в особенности ощутим эффект в процессе возведения несущих стен, где применяются такие блоки. В этом случае при идентичной толщине стен экономия стенового материала равна 60 процентам, что в 2,5 раза позволяет сократить расходы на обогрев или охлаждение помещений в неблагоприятные климатические периоды года.
Стены из этого материала отлично поддаются отделке традиционными и самыми современными отделочными материалами. Экономия применения этого материала заключается еще и в том, что он не нуждается в возведении сложных и тяжелых фундаментов, так как его относят к группе легких бетонов, а в простонародье такие блоки получили название опилкобетон.
Технология производства
В состав арболита входит цемент марки 400 или 500. В некоторых случаях в процессе изготовления этого материала своими руками используется цемент, который способен обеспечить еще более высокую прочность изделий. В качестве наполнителей к составу бетона добавляют мелкую древесную стружку, щепу, а также опилки. В случае недостатка какого-либо из наполнителей его можно заменить остатками хвои, листвы либо коры, однако процент такого заменителя не должен превышать 5 процентов от общего веса заменяемого наполнителя.
Схема стены из арболита.
Размеры применяемых материалов в составе арболита не должны превышать по толщине 5 мм, а вот их длина не должна быть больше 25 мм. Именно по этой причине при изготовлении арболита своими руками всю органику прежде следует пропустить через дробилку, а уже после можно переходить к смешиванию с цементом. В условиях заводов к органическим отходам добавляют химические вещества, нейтрализующие сахар, который имеется в органике. Это делают потому, что сахар способен негативно влиять на прочность материала, именно поэтому процесс нейтрализации так необходим. В качестве химреактивов применяется сернокислый алюминий и хлористый кальций. Естественно, при изготовлении арболита своими руками таких веществ можно не найти, поэтому в процессе можно обойтись и без них. Но если не позаботиться о нейтрализации сахара, то смесь станет вспучиваться. Способ этого избежать все же есть, для этого древесные отходы предстоит выдержать в течение примерно 4 месяцев под открытым небом.
1%22%20viewBox%3D%220%200%2068%2048%22%20width%3D%22100%25%22%3E%3Cpath%20class%3D%22ytp-large-play-button-bg%22%20d%3D%22M66.52%2C7.74c-0.78-2.93-2.49-5.41-5.42-6.19C55.79%2C.13%2C34%2C0%2C34%2C0S12.21%2C.13%2C6.9%2C1.55%20C3.97%2C2.33%2C2.27%2C4.81%2C1.48%2C7.74C0.06%2C13.05%2C0%2C24%2C0%2C24s0.06%2C10.95%2C1.48%2C16.26c0.78%2C2.93%2C2.49%2C5.41%2C5.42%2C6.19%20C12.21%2C47.87%2C34%2C48%2C34%2C48s21.79-0.13%2C27.1-1.55c2.93-0.78%2C4.64-3.26%2C5.42-6.19C67.94%2C34.95%2C68%2C24%2C68%2C24S67.94%2C13.05%2C66.52%2C7.74z%22%20fill%3D%22%23f00%22%3E%3C%2Fpath%3E%3Cpath%20d%3D%22M%2045%2C24%2027%2C14%2027%2C34%22%20fill%3D%22%23fff%22%3E%3C%2Fpath%3E%3C%2Fsvg%3E%3C%2Fspan%3E%3C%2Fbody%3E%3C%2Fhtml%3E» allowtransparency=»true»/>
Процесс изготовления арболита начинается с этапа обработки органики. Дробленая древесная масса для этого заливается водой и тщательно перемешивается. Профессионалы советуют выдержать древесные отходы около 3 часов в известковом растворе, что будет способствовать разложению сахара. Органику, которую предварительно замачивают в известковом растворе, следует перемешать до однородной массы с цементом. Соотношение воды, цемента и опилок должно быть таким, 4:3:3.
Тонкости изготовления
Для перемешивания компонентов арголита, советуется использовать бетономешалку, чтобы избежать оброзование комков.
Перемешивается вышеописанный раствор из древесины и цемента в бетоносмесителе, образование комков в этом случае недопустимо. Полученная масса при соблюдении всех требований должна получиться слегка рассыпчатой, однако после сжатия в кулаке она должна удерживать форму. Если раствор способен удержать форму, значит, его уже можно использовать по назначению.
Арболит подходит не только для изготовления блоков, с его применением можно производить плиты или перемычки, подходит этот материал и для заливки монолитных стен. Затвердевший арболит отлично поддается обработке, именно поэтому его можно сверлить, пилить, а также подгонять всевозможными способами под требуемый размер.
При выдерживании опилок и стружки на открытом воздухе следует их периодически перелопачивать. В том случае когда такая возможность отсутствует, необходимо обработать смесь, используя окись кальция. Данный известковый раствор делают из расчета 200 литров 1,5-процентного раствора на объем сырья в количестве 1 кубического метра. Обработанные таким раствором стружку и опилки оставляют на 4 дня с учетом перемешивания, что необходимо делать несколько раз в течение дня.
ytimg.com%2Fvi%2Fll4iEmYVSnA%2Fsddefault.jpg%27%29%3Bbackground-position%3Acenter%3Bbackground-size%3Acover%3Bbackground-repeat%3Ano-repeat%3B%22%3E%3C%2Fa%3E%3Cspan%20style%3D%22position%3Aabsolute%3Bleft%3A50%25%3Btop%3A50%25%3Bwidth%3A68px%3Bheight%3A48px%3Bmargin-left%3A-34px%3Bmargin-top%3A-24px%3Bpointer-events%3Anone%3B%22%3E%3Csvg%20height%3D%22100%25%22%20version%3D%221.1%22%20viewBox%3D%220%200%2068%2048%22%20width%3D%22100%25%22%3E%3Cpath%20class%3D%22ytp-large-play-button-bg%22%20d%3D%22M66.52%2C7.74c-0.78-2.93-2.49-5.41-5.42-6.19C55.79%2C.13%2C34%2C0%2C34%2C0S12.21%2C.13%2C6.9%2C1.55%20C3.97%2C2.33%2C2.27%2C4.81%2C1.48%2C7.74C0.06%2C13.05%2C0%2C24%2C0%2C24s0.06%2C10.95%2C1.48%2C16.26c0.78%2C2.93%2C2.49%2C5.41%2C5.42%2C6.19%20C12.21%2C47.87%2C34%2C48%2C34%2C48s21.79-0.13%2C27.1-1.55c2.93-0.78%2C4.64-3.26%2C5.42-6.19C67.94%2C34.95%2C68%2C24%2C68%2C24S67.94%2C13.05%2C66.52%2C7.74z%22%20fill%3D%22%23f00%22%3E%3C%2Fpath%3E%3Cpath%20d%3D%22M%2045%2C24%2027%2C14%2027%2C34%22%20fill%3D%22%23fff%22%3E%3C%2Fpath%3E%3C%2Fsvg%3E%3C%2Fspan%3E%3C%2Fbody%3E%3C%2Fhtml%3E» allowtransparency=»true»/>
Арболитовые блоки своими руками получатся качественными только с учетом использования бетономешалки. В качестве добавок можно применять жидкое стекло, хлористый кальций, сернокислый кальций или алюминий и гашеную известь. Эти добавки следует готовить в количестве 4 процентов от общей массы цемента. Лучшей комбинацией добавок для блоков станет смесь сернокислого алюминия и сернокислого кальция в соотношении 50/50 или смесь, в составе которой жидкое стекло и окись кальция присутствуют в том же соотношении. После того как древесина для будущих блоков была пропущена через рубильную машину, что предполагает первичную обработку, следует осуществить дробление материала, используя молотковую дробилку.
Следующим этапом станет сортировка, в процессе этого должна отсеяться земля, кора, пыль и недопустимые вещества в составе арболитовых блоков. После предстоит добавить 20% просеянных опилок. Полученный материал должен быть подвергнут химической обработке, что предполагает замачивание в воде, в которую предварительно добавлено жидкое стекло.
Материалы для работы
- цемент;
- мелкая древесная стружка;
- щепа;
- опилки;
- вода;
- хлористый кальций;
- жидкое стекло;
- сернокислый кальций;
- сернокислый алюминий.
1%22%20viewBox%3D%220%200%2068%2048%22%20width%3D%22100%25%22%3E%3Cpath%20class%3D%22ytp-large-play-button-bg%22%20d%3D%22M66.52%2C7.74c-0.78-2.93-2.49-5.41-5.42-6.19C55.79%2C.13%2C34%2C0%2C34%2C0S12.21%2C.13%2C6.9%2C1.55%20C3.97%2C2.33%2C2.27%2C4.81%2C1.48%2C7.74C0.06%2C13.05%2C0%2C24%2C0%2C24s0.06%2C10.95%2C1.48%2C16.26c0.78%2C2.93%2C2.49%2C5.41%2C5.42%2C6.19%20C12.21%2C47.87%2C34%2C48%2C34%2C48s21.79-0.13%2C27.1-1.55c2.93-0.78%2C4.64-3.26%2C5.42-6.19C67.94%2C34.95%2C68%2C24%2C68%2C24S67.94%2C13.05%2C66.52%2C7.74z%22%20fill%3D%22%23f00%22%3E%3C%2Fpath%3E%3Cpath%20d%3D%22M%2045%2C24%2027%2C14%2027%2C34%22%20fill%3D%22%23fff%22%3E%3C%2Fpath%3E%3C%2Fsvg%3E%3C%2Fspan%3E%3C%2Fbody%3E%3C%2Fhtml%3E» allowtransparency=»true»/>
Качество материала
Для ускорения процесса отвердевания и минерализации материала следует добавить хлористый кальций в древесную массу. В качестве дезинфекции используется гашеная известь. Готовая масса замешивается с цементом, а после подается в вертикальные и горизонтальные формы. Для придания будущим изделиям большей плотности материал следует подвергнуть обработке пневматическими или электрическими трамбовками и вибропрессом. Формы для арболитовых блоков, которые вы намерены сделать своими руками, рекомендуется изготавливать из досок. Упростит процесс выемки изделий линолеум, который необходимо набить на стенки форм.
Производство арболита своими руками: состав, пропорции, оборудование
Арболит (он же деревобетон) все чаще используется в малоэтажном строительстве. Во многом это связано с простотой производственной технологии и доступностью исходных компонентов. Именно о технологии, оборудовании и способах производства я расскажу в этой статье.
Производственное оборудование
Оборудование для производства арболита не отличается особой сложностью и габаритами. Его можно разместить на приусадебном или дачном участке, в любом боксе, цеху или просто на улице под навесом. Главное условие – наличие электроэнергии и удобство эксплуатации. Полный перечень заводского оборудования, необходимого для промышленного производства арбоблоков выглядит следующим образом:
- Шредер – измельчитель органических наполнителей (щепы, соломы и т.д.).
- Ёмкость для приготовления и розлива химических компонентов.
- Дозатор цемента.
- Дозатор органических наполнителей.
- Дозатор заполнителей для бетонного раствора.
- Бетоносмеситель для арболита принудительного типа действия.
- Подъёмно-поворотный бункер для приёма и дальнейшего розлива готового арболитового раствора.
- Система лебёдок для погрузочно-разгрузочных работ.
- Самозапечатываемые формы для отливки блоков.
- Вибропресс для арболита.
При кустарном производстве деревобетона, для собственных нужд, могут использоваться самодельные станки.
Состав арболита
Состав арболита регламентируется ГОСТ №19-222-84. Готовая к заливке арболитовая смесь состоит из следующих компонентов:
- Цементный раствор;
- Химические добавки;
- Органические наполнители.
Цемент
В качестве связующего компонента в производстве используется раствор на цементной основе. По ГОСТу, портландцемент для приготовления арболита должен иметь марку не ниже М-400.
Таблица . Технические характеристики цемента М-400
Добавлять песок в состав арболитного раствора не рекомендуется, так как это ухудшает показатели сцепки органических наполнителей с цементным вяжущим веществом. В результате блоки становятся менее прочными и склонными к расслоению и растрескиванию.
Химические добавки
Химические добавки предназначены для улучшения эксплуатационных характеристик арболита. В состав арболита входят следующие химические компоненты:
- Сернокислый алюминий, он же сульфат алюминия – неорганическая соль, хорошо растворимая в воде. При изготовлении арболита он используется в качестве гидроизолятора, увеличивающего стойкость материала к воздействию сырости.
Из-за высокой гигроскопичности, хранение сернокислого алюминия должно производиться в помещениях с низким уровнем влажности и в герметичной упаковке.
- Хлористый кальций – химический элемент, получаемый при промышленном производстве соды. Добавляется в арболитную смесь для связывания сахаров, содержащихся в органических заполнителях, что значительно повышает прочностные характеристики получаемого цементного раствора и позволяет повысить степень его сцепления с древесными компонентами.
- Жидкое стекло – водорастворённые силикаты натрия или калия. При изготовлении смеси для деревобетона, жидкое стекло выполняет роль отвердителя, а также для придания цементному раствору кислотоупорных и гидроупорных свойств.
- Гашёная известь добавляется в раствор для нейтрализации содержащихся в органических добавках природных сахаров и улучшения связующих качеств цемента и древесины.
Органические заполнители
В качестве наполнителя при производстве арболита используются отходы деревообрабатывающего производства. Главное отличие арболита от других видов лёгких бетонов состоит в том, что в его состав входят достаточно крупные компоненты – древесная щепа, костра льна, конопляная солома и т. д. От процентного содержания органического наполнителя зависят основные показатели материала: плотность, гигроскопичность, коэффициент теплопроводности и т.д.
- Древесная щепа – наиболее часто используемый заполнитель. Согласно ГОСТу, её размер не должен превышать 4 х 1 х 0,5 см. В связи с этим, технические характеристики арболитовых конструкций отличаются от характеристик опилкобетона и фибролита (стружкобетона).
Древесная щепа – главная составляющая арболитового блока
Нужный размер органической фракции получают при помощи специального станка-щепореза (шредера). Содержание щепы в общем объёме арболита может быть разным, и составлять от 30% до 90%.
- Льняная костра добавляется в таком же виде, в каком она получается на льноперерабатывающем заводе после предварительной обработки сырья.
- Конопляную солому перед использованием следует перемолоть в шредере.
Согласно техническим нормативам, льняные и конопляные наполнители должны иметь следующие размеры:
- Длина – от 15 до 25 мм.
- Ширина – от 2 до 5 мм.
В разных регионах для производства арболитовых блоков и панелей могут применяться и другие органические заполнители: рисовая и гречневая солома, отходы обработки хлопчатника и т.п.
В таблице даны технические характеристики арболита, изготовленных с применением разных органических наполнителей:
Технология производства
Технология производства арболита имеет ряд отличительных особенностей, которые касаются подготовки сырья, рецепта приготовления, дозировки компонентов. Её соблюдение обязательно как при промышленном выпуске, так и при производстве арболита своими руками в домашних условиях.
Подготовка органических заполнителей
Для деревобетона может использоваться щепа древесины хвойных пород – ели, сосны, пихты, а также лиственных деревьев с твёрдой древесиной – дуба, ясеня, берёзы.
Не рекомендуется применять в производстве щепу лиственницы и бука из-за химического состава – их древесина содержит значительно больше сахаров, что приводит к значительному снижению качества блоков. В крайнем случае, при производстве раствора с лиственничной или буковой щепой, придётся, как минимум, вдвое увеличить количество химдобавок – извести или хлористого кальция.
Щепа березы и ясеня – лучший наполнитель для арболитового блока
Первым шагом древесные отходы измельчаются посредством щепореза до размеров, регламентируемых ГОСТ №19-222-84 – не более 40х10х50 мм. Фактически же оптимальными размерами древесной фракции для формовки блоков являются 25х5х3 мм, так как более крупные компоненты хуже связываются цементным раствором и более склонны к расслаиванию в процессе эксплуатации.
После измельчения щепа просушивается. На крупных производственных линиях для этих целей применяют специальные сушилки барабанного типа, в которые подаётся горячий воздух.
Если арболит производится в домашних условиях, щепу складируют для просушки под навесами на срок не менее месяца, при температуре воздуха +15С.
Непосредственно перед замешиванием щепа замачивается на 6-8 ч в растворе воды с химическими добавками. Вода для этого должна соответствовать ГОСТу №23-732-79, где регламентируется её химический состав, кислотность и т.д. На деле же, при кустарном производстве деревобетона применяется любая доступная вода – из водопровода, реки или колодца. Единственное необходимое условие – она должна быть чистой и иметь температуру не ниже +15…+20С. После замачивания древесный наполнитель должен иметь влажность не более 30%.
Костра льна и солома конопли, для удаления из неё излишков сахаров, выдерживается на открытом воздухе не менее 2 – 3 месяцев при плюсовой температуре, либо замачивается в известковом молоке на 3-4 дня. Известковый раствор приготавливается в следующих пропорциях на 1 куб. м органики.
Органический заполнитель | Гашёная известь | Вода | Дополнительные условия |
1 куб. м костры льна или конопли | 2 – 2,5 кг | 150 – 200 л в зависимости от влажности наполнителя | Смесь перемешивается каждые 2 дня |
Пропорции смеси
Пропорции замеса могут незначительно изменяться, в зависимости от класса прочности деревобетона. Для получения более высокой марки арболита увеличивают долю цемента в общем объёме раствора. Ниже представлены рекомендуемые пропорции замеса раствора для деревобетона различных марок на куб готового раствора:
Марка | Портландцемент М-400 | Органический наполнитель | Химдобавки | Вода |
М-5 | 200 – 220 кг | 280 – 320 кг | 12-14 кг | 350 – 400 л |
М-15 | 250 – 280 кг | 240 – 300 кг | 12 кг | 350 – 400 л |
М-25 | 300 – 330 кг | 240 – 300 кг | 12 кг | 350 – 400 л |
М-50 | 350 – 400 кг | 220 – 240 кг | 10-12 кг | 350 – 400 л |
Химические добавки могут добавляться как по отдельности, так и комплексно. К примеру, строительные нормативы СН №54982 допускают смешивание сернокислого алюминия с известью в пропорции 8 кг и 4 кг на куб раствора.
Очерёдность загрузки
При замесе раствора важно соблюдать не только пропорции, но и очерёдность загрузки компонентов. Для изготовления качественной арболитной смеси обычные бетоносмесители, используемые для замеса бетона, не подойдут – щепа в них не сможет хорошо перемешаться с цементным раствором. Бетономешалка для арболита должна быть принудительного типа, например отечественные модели серии СБ, РН, импортные ZZBO и т.д. В них перемешивание компонентов производится не вращением барабана, а расположенным внутри него шнеком или лопастью.
Таблица 3. Технические характеристики принудительных смесителей серии СБ:
- Первым шагом в барабан смесителя насыпается подготовленная щепа в нужной пропорции.
- Затем бетоносмеситель запускается и в него заливается вода с растворёнными в ней химическими добавками. Органический заполнитель размешивается с химраствором в течение 30-60 секунд, чтобы щепки хорошо пропитались.
- После этого добавляется цемент и продолжается размешивание смеси в течение 3-5 минут, до получения однородной массы.
Формирование блоков
Формовка арбоблоков происходит с помощью специальных матриц, в которые заливается готовый раствор. Они изготавливаются из нержавеющей стали разборной конструкции для более лёгкого извлечения блоков.
Также такие формы можно изготовить самому из дерева или фанеры, обив их изнутри линолеумом или жестью. Размеры ячеек матрицы могут быть различными, в зависимости от потребностей в блоках тех или иных габаритов.
Трамбовка производится вручную, либо для этого используется вибростанок. В первом случае раствор заливается в формы слоями толщиной в 5 см, каждый из которых уплотняется металлической трамбовкой.
Во втором случае уплотнение раствора производится на вибростоле, которым обычно оборудуется промышленный станок для производства арболита.
Также при формовке для уплотнения раствора можно использовать ручной или механический пресс. Чтобы из уплотняемых блоков лучше выходил воздух, они периодически прокалывается металлическим стержнем.
Сушка
Сушка готовой продукции является завершающим этапом производственного процесса. В связи с особенностью конструкции, наилучшим вариантом является мягкий режим просушки.
Пропаривать арбоблоки по примеру железобетонных конструкций, не рекомендуется, так как материал теряет прочность из-за возрастающих внутренних напряжений. По этой же причине не следует пытаться ускорить высыхание блоков при помощи сушильных камер и других приспособлений.
Оптимальный режим просушки для арболита – температура 40-50 градусов, при влажности воздуха порядка 70-80%. В этом случае блоки набирают необходимую для распалубки прочность уже спустя 18-20 ч. что составляет около 1/3 от окончательной марочной. Дальнейшая выдержка материала производится при температуре 15-20 С в течение одной-двух недель – за это время деревобетон набирает окончательную прочность.
Технология изготовления арболита блоки
Основой получения качественного арболита является прочное соединение древесной щепы с цементом. Водорастворимые вещества, имеющиеся в древесине, играют отрицательную роль в этом процессе, тормозят твердение цемента и препятствуют прочному соединению цемента с древесной стружкой.
Поэтому древесную щепу перед смешиванием с цементом необходимо освободить от водорастворимых веществ или нейтрализовать их путем химической обработки. Наиболее распространенным химикатом, применяемым для этих целей, является хлористый кальций (плавленый), отвечающий требованиям ГОСТ 450—58. При отсутствии хлористого кальция применяется жидкое стекло, отвечающее требованиям ГОСТ 962—41. Приготовление концентрированного раствора из плавленого хлористого кальция производится в деревянных чанах с перемешивающим устройством при температуре воды 70—80° С. На 1 м3 арболита (плотной массы) расходуется до 8 кг хлористого кальция или 4 кг жидкого стекла с удельным весом 1,5.
Древесная щепа должна быть по возможности однородной по размерам и конфигурации и иметь длину (вдоль волокон) 15—20, толщину 2—3 и ширину 10—12 мм. Приготовление щепы, идущей на изготовление изделий из арболита, производится на рубительных машинах дисковой или другой конструкции, применяемых в целлюлозно-бумажной промышленности или в лесопильной промышленности для дробления отходов. Щепа сортируется на плоских или барабанных сортировках, при этом удаляются вся мелочь и пыль.
После сортировки щепа подвергается обработке (минерализации) 5%-ным раствором хлористого кальция или жидкого стекла при помощи механизмов окунанием щепы в раствор или же обрызгиванием. Расход хлористого кальция — 0,1—0,12 кг сухого вещества на 1 кг щепы. Длительность обработки минерализатором зависит от породы древесины, влажности и других факторов и определяется в каждом отдельном случае опытным путем. При организации пропитки следует предусмотреть возможность повторного использования раствора, стекающего со щепы. Пропитывание щепы раствором считается законченным, как только щепа оказывается равномерно смоченной, на что требуется 2—3 мин. Общее время смачивания и перемешивания составляет от 8 до 12 мин. Механизмами для минерализации щепы могут служить сетчатые транспортеры, мешалки и чаны, если операция производится по способу окунания.
Минерализованная щепа смешивается с портландцементом марки 400 при расходе последнего от 300 до 400 кг на 1 м3 изделий (плотной массы). Дозировка цемента производится по весу и устанавливается опытным путем в зависимости от требований, предъявляемых к физико-механическим свойствам изделий из арболита, и его объемного веса. Смешивание щепы с цементом продолжается 2—3 мин и заканчивается после того, как вся стружка оказывается покрытой цементом, что распознается по однородному серому цвету смеси.
Количество цемента, которое необходимо добавлять во время смешивания, определяется экспериментальным путем. Необходимо следить, чтобы смесь была достаточно смочена и представляла собой мягкую и пластичную массу. В жаркое время массу приготавливают с несколько большим содержанием воды, чем обычно, для компенсации потери воды во время формирования. В среднем на 1 м3 арболита расходуется до 265 л воды, включая и воду химического раствора.
При изготовлении стеновых блоков желательно в массу добавить 10—12% дробленого сланца, что придает массе пластичность и способствует более легкому освобождению изделий из формы.
Формование арболита производится путем заполнения специальных металлических форм на станках, применяемых при изготовлении подобных изделий из бетона, глины и других материалов. Для изготовления стеновых блоков можно приспособить станок, которым пользуются при производстве шлакобетонных камней; для изготовления плитных материалов — прессы, применяемые для изготовления фибролитовых плит, и др.
При ручной работе сначала производится частичное заполнение форм с последующей утрамбовкой краев железным инструментом для получения правильных и прочных граней. Сжатие материала при его нормальном качестве составляет 20%. Эту усадку необходимо учитывать при конструировании и определении размеров форм. Хорошие результаты формования дает также вибрирование, особенно при применении высоких форм.
Изделия из арболита после их формования подвергаются искусственному твердению в специальных камерах при температуре 35° С. Время выдержки —от 12 до 24 ч. При производстве фибролита выявлено, что режим искусственного твердения для цемента разных марок неодинаков и существенно отражается на прочности и качестве плит. Поэтому при организации производства арболита режимы твердения плит в каждом отдельном случае должны устанавливаться опытным путем.
Камеры твердения, в которых происходит термическая обработка изделий, оборудуются продольными и поперечными траверсными узкоколейными путями и механическим устройством для передвижения тележек во время загрузки и разгрузки камер.
Распалубка форм производится в зависимости от конфигурации и размеров изделий вручную или при помощи тельферов.
После выдержки в камерах твердения изделия на тележках по узкоколейным путям направляются в сушильные камеры. Время сушки —от 24 до 30 ч при температуре 60—65° С. Готовые изделия после сушки зачищают от возможных заусенцев и подают на склад готовой продукции, где их укладывают и хранят в штабелях высотой до 2 м.
Сделайте арболиты своими руками в домашних условиях Арболитные блоки своими руками
Арболит считается отличным строительным материалом, который подходит для возведения стен в любых помещениях. Этот материал относится к группе легкого бетона и в простонародье иногда называется бетонными опилками.
Технология производства
Поскольку арболит — это бетон на опилках, несложно догадаться, что в его состав, как и в любой другой бетон, входит цемент марок 400 и 500.Иногда при изготовлении арболита для повышения прочности готовых изделий используют цемент с еще более высокими показателями. Что касается наполнителя, то в бетон добавляют мелкую древесную стружку, стружку и, конечно же, опилки. При отсутствии какого-либо из перечисленных наполнителей его заменяют остатками листвы, хвои или коры, количество которых не должно превышать 5% от веса заменяемого наполнителя.
Размеры материалов, используемых в арболите, не должны превышать 5 мм в толщину и 25 мм в длину.Поэтому все органические вещества сначала пропускают через дробилку, а уже потом смешивают с цементом. На заводах в органические отходы добавляют специальные химические вещества, нейтрализующие сахар, присутствующий в органических веществах. Этот сахар очень негативно влияет на прочность арболита, поэтому его нейтрализация просто необходима.
Хлорид кальция и сульфат алюминия используются в качестве химических реагентов. Естественно, что если арболит в домашних условиях, то таких веществ может просто не оказаться под рукой, поэтому можно обойтись без них.Однако, если сахар вообще не убирать, арболит набухнет, и чтобы этого не произошло, нужно 3-4 месяца выдерживать древесные отходы на открытом воздухе.
Производство арболита должно начинаться с обработки органических веществ. Для этого измельченную древесную массу залить водой и тщательно перемешать. Специалисты рекомендуют подержать древесные отходы в известковой ступке около 3 часов, что также способствует разложению сахара. Замоченные в известковом растворе органические вещества смешивают с цементом до однородной массы.
Соотношение воды, опилок и цемента должно выглядеть примерно так: 4: 3: 3.
Такой древесно-цементный раствор замешивают в бетономешалке, ведь образование комков здесь недопустимо. Полученная масса должна быть слегка рассыпчатой, но при сжатии в кулаке должна держать форму комка. Если раствор сохраняет форму, значит, он готов к дальнейшему использованию по назначению.
Преимущества арболита
На западе арболит является одним из самых востребованных материалов и постепенно начинает завоевывать наш рынок благодаря ряду значительных преимуществ:
- блоки, перемычки, плиты могут изготавливаться из арболита, а также использоваться для монолитной заливки стен; Армированный бетон
- легко поддается любой обработке, поэтому его можно распиливать, просверливать и другими способами доводить до нужных размеров; Арболит
- — очень выгодный строительный материал, потому что ингредиенты, используемые при его изготовлении, очень доступны, а сама технология производства не требует много времени и денег;
- любая отделка очень подходит для затвердевшего арболита, поэтому стены из него можно оштукатурить, облицевать облицовочным кирпичом и даже обшить гипсокартоном без установки каркаса и армирующей сетки; Арболит
- может похвастаться хорошей теплоизоляцией, поэтому дома из паркетных блоков требуют гораздо меньше обогрева, чем кирпичные и черепичные аналоги;
- одно из главных достоинств материала в том, что он абсолютно пожаробезопасен, так как, несмотря на наличие древесных отходов, он не загорается;
- также арболит не гниет и не подвергается грибковым поражениям;
- морозоустойчив, поэтому широко применяется при строительстве жилых домов в северных регионах;
- кроме того, арболит отличается хорошей звукоизоляцией, что также является весомым преимуществом.
Самостоятельное производство арболитов
Чаще всего из готовой арболита делают блоки, которые легко транспортировать, не много весят и подходят как для строительства разных типов … Изготовить такие блоки можно так же просто, как и сам арболит, так как ничего для этого требуется специальный.
Формы для арболитов могут изготавливаться из деревянных ящиков со съемным дном. Некоторые бывалые домовладельцы рекомендуют обивку изнутри линолеумом, чтобы облегчить извлечение готового блока.В готовом виде арболит укладывается в два-три этапа слоями, причем каждый слой необходимо тщательно утрамбовать. Поверхность последнего слоя должна оставаться неровной, а до края сторон нужно оставить около 2 см, чтобы это пространство еще можно было заполнить штукатуркой.
Наружную поверхность блоков можно смазать цементным раствором, что повысит их прочность и устойчивость к атмосферным воздействиям. Рекомендуется держать блоки в форме не менее суток, чтобы смесь успела застыть. После этого блоки переносят под навес, так как они могут высохнуть на солнце и впоследствии осыпаться.
Арболит считается экологически чистым материалом, поэтому постройки из него не оказывают негативного воздействия на здоровье человека.
Характеристики арболита заслуженно привлекают внимание, если вы хотите построить одно- или двухэтажный дом … Не последний фактор при выборе — это то, что достаточно просто сделать монолитные стены и арболиты своими руками.Полный комплект необходимого оборудования зависит от того, есть ли где купить готовые фишки, или вам придется делать это самостоятельно. Для полноты картины рассмотрена полная технология производства арболита.
Основной компонент арболит
Арболит на 90% состоит из древесной щепы, поэтому первым делом нужно уделить внимание ее покупке или закупке. Лучше всего, если материалом для него послужат сосновые доски, но ничего не имеет против использования других ГОСТов.
Одним из нюансов производства арболитов является использование дерева, поскольку это натуральный материал, содержащий в своем составе соединения сахара. Если их не нейтрализовать, то впоследствии они вступят в реакцию с остальными компонентами арболита, что как минимум спровоцирует его набухание. Чтобы этого не произошло, доски, а лучше уже готовые чипсы, месяц выдерживают на открытом воздухе.
Более быстрый способ — это замачивание стружки в химических растворах, которое проводят в течение 3 суток. Для их приготовления используют сульфат алюминия (сульфат алюминия), хлорид кальция, гашеную известь или жидкое стекло. Эти компоненты имеются в продаже, и их нетрудно найти в сельскохозяйственных магазинах.
Практика показала, что лучший раствор — сульфат алюминия, который после реакции с сахарами укрепляет арболит. Не рекомендуется использовать жидкое стекло — оно увеличивает хрупкость готового материала.
Многие рецепты изготовления арболитов своими руками также пропускают этот этап, добавляя нейтрализующие химические вещества непосредственно во время замешивания арболита. В этом случае их пропорции соблюдаются примерно на уровне 3% от общего веса используемого цемента.
Фреза для стружки
Если ведется масштабное строительство, и купить щепу в таком количестве не всегда возможно, то без фрезы для стружки не обойтись. Это устройство измельчает доски в щепы, которые затем полностью готовы к использованию (если древесина выдержана).
Принцип работы устройства очень прост — на вал надевается металлический диск (обычно диаметром 50 см), в котором проделываются проймы (3-4, в зависимости от модели), расположенные друг относительно друга под углом. 120 ° или 90 °.Возле каждого выреза под углом к нему прикреплен нож, который отрезает кусок доски и подает в пройму, после чего попадает в камеру дробления, где доводится до окончательных размеров.
Создание и работа фрезы для стружки хорошо видно на следующем видео:
Несмотря на кажущуюся простоту конструкции, фрезер для стружки, сделанный своими руками, есть не у всех, ведь станок токарный и фрезерный … Это оборудование для обработки арболитов придется заказывать хотя бы частично снаружи.
Если токарный станок — не неразрешимый вопрос, то как сделать стружколом показано на следующей схеме.
Приготовление раствора: пропорции
Особых секретов здесь нет — нужно просто смешать все компоненты. Есть только одно ограничение — с момента окончания замеса и до попадания раствора в формовочную емкость должно пройти не более 15 минут. По истечении этого времени начинается химическая реакция цемента.
Основной порядок заполнения емкости смесителя (соотношение компонентов в ведрах на одну замес):
- Щепа разливается.Если он ранее был замочен в растворе, то сушить его не нужно — следующий компонент все равно будет добавлять воду. Количество — 6 ведер.
- В воду добавлен хлорид кальция (или другой компонент). Пропорции — 2-4% от массы цемента, который будет использован для замеса (1 ведро). Визуально это примерно 1-2 полных стакана. Все перемешивается и выливается в миксер к стружке и миксер запускается. Также берется одно ведро воды.
- Когда щепа равномерно намокнет, пора добавить цемент.Его заливают в миксер, и теперь нужно дождаться, пока все стружки равномерно покроются цементом — все они должны быть соответствующего цвета. Марка используемого цемента — 500.
Формовка арболитов
Когда раствор готов, его переливают в подходящую емкость, и теперь его нужно использовать в течение 15 минут. Для формования и изготовления арболитов своими руками придумано множество способов — в производстве это сборно-разборная опалубка на 6-12 блоков, а в домашних условиях их обычно изготавливают по частям по самодельным трафаретам.
Один из способов изготовления на видео:
Технология изготовления арболита предусматривает два варианта формовки:
- Быстрая зачистка — после первоначального схватывания цемента. По сути, это непрерывный процесс — формирование блока (заливка раствора в форму), прессование (или вибропрессование), зачистка и отправка на сушку. Вместе с приготовлением раствора даже один человек может сделать 80-100 блоков в сутки.
Достоинством метода является скорость изготовления новых арболитов и непрерывный технологический процесс.
- Зачистка через сутки — после прессования блок оставляют в форме на 24 часа, после чего производится только зачистка и сушка. Изготовление арболитов своими руками таким способом может получиться даже быстрее, но только при наличии достаточного количества форм, в которых арболит можно оставить на ночь. Достоинства метода — близкая к идеальной форма блока, который после схватывания бетона не имеет возможности даже малейшего перекоса.
Чем хуже геометрия блоков, тем толще будут цементные швы между ними, образующие мостики холода. Для уменьшения теплопроводности блокам придают зигзагообразную форму, которая ломает такую перемычку, препятствуя прямому оттоку тепла.
Для формования блоков используется специальный станок или трафареты — все это оборудование для арболитов можно изготовить своими руками.
Использование станка
Оба устройства могут использоваться любым из способов, но их машина часто предназначена для быстрого извлечения из формы, чтобы увеличить скорость производства. Их неоспоримое преимущество — прессование блока на вибростоле. Сам процесс формирования прост, а оборудованию могут доверять рабочие с минимальной подготовкой.
Работа полуавтомата на видео:
- Готовую смесь переливают в мерную емкость (1), которую перемещают по направляющим (2), сливая раствор в форму (3).
- Сверху раствора устанавливается крышка (5) пресса (ее высота регулируется пальцами (6) для людей разного роста) и прижимается рычагом (7).
- После нажатия включается вибростол (8). Он работает 20-30 секунд и автоматически отключается (можно использовать простейшее реле времени) — дольше протаранить нельзя, потому что тогда цемент будет стряхиваться на дно блока.
- Рычаг откидывается назад (9), крышка пресса снимается (10) и форма поднимается вверх (11), для чего нажимается педаль.
Готовый арболит можно сдавать на сушку (12). Через 2-3 дня он наберет достаточную прочность для транспортировки.
Для использования метода зачистки через сутки форму делают разборно-съемной, а верхнюю крышку можно закрепить в ней защелками или другим удобным способом . .. После утрамбовки блок вынимается прямо из формы и отправлен на заселение.
Арболит по трафарету
Применяются два основных типа форм — в виде ящика без дна и верха, а также разборные в виде двух букв «G», которые защелкиваются вокруг дна, образуя жесткую коробку, покрытую крышка.Он, в свою очередь, также фиксируется отдельными защелками, которые врезаны в боковые стенки.
Независимо от того, какая форма используется, основной алгоритм следующий:
- Готовится ящик для заливки арболитной смеси. Проход помещается на твердую поверхность (1), покрытую целлофаном (чтобы блок не прилипал), вся коробка смачивается изнутри.
- Заливают первый слой смеси, уплотняют, сверху добавляют второй слой, при необходимости третий и накрывают крышкой.На сквозном ящике (2) лежит гнет (грузик или что-то подходящее), в складной верхней части фиксируется защелками (3).
- Если у вас под рукой есть перфоратор, вы можете провести им по крышке, он заменит вибростол.
- В зависимости от используемой технологии опалубка снимается или форма остается стоять.
Если быстро снять проходную коробку, то сначала она поднимается вверх (4), затем снимается изгиб и снимается крышка. Блок отправляется на сушку вместе с основанием, на котором он был сформирован.
Кратко о главном
Производство качественного арболита в домашних условиях — задача не из обычных. Найти стружколом может быть единственной серьезной трудностью. В крайнем случае его можно изготовить или заказать, но если есть где купить готовые фишки, то эта проблема снимается.
Используемые чипсы необходимо выдержать около месяца на солнце, чтобы нейтрализовать органические вещества внутри. Для раствора можно использовать влажный.
Есть два основных способа снятия опалубки из готовых блоков.Чтобы выбрать подходящий, есть смысл сделать пробные блоки и сравнить результаты.
В условиях, когда цены на все растут, люди все чаще прибегают к старым проверенным «старомодным» методам. Этот тренд не обошел стороной и строительство.
Стоимость теплоизоляции растет вместе с ценами на другие строительные материалы. Поэтому в последние два-три года былую популярность вернулся арболит, который еще называют арболит.Причина не только в его изоляционных качествах, но и в относительной дешевизне. И, конечно же, то, что можно сделать арболиты своими руками.
Арболит: достоинства и недостатки
Арболит — легкий стеновой блок из смеси древесной щепы, цемента и химических герметиков.
Арболит применялся в СССР еще в 60-х годах прошлого века и был оценен советскими строителями за легкость и неприхотливость.Но рынок диктует свои условия: со временем арболит был заменен более современными видами теплоизоляционных блочных материалов. Сейчас возрождается технология изготовления, и в магазинах снова стал появляться арболит. Однако не всегда его можно найти на свободном рынке. Поэтому актуальная тема — как сделать арболиты своими руками.
В арболите четыре основных компонента:
- Цемент.
- Древесная щепа.
- Вода.
- Связующие химические.
ВАЖНО: арболит не следует путать с опилками бетона. Это разные материалы с различными параметрами и областями применения. В опилочном бетоне основным наполнителем, как следует из названия, являются опилки. В состав арболита входят также отходы деревообработки. Но это щепа строго определенных размеров — не более 40х10х5 см. Такие параметры прописаны в ГОСТ 19222-84.
Разберемся с несколькими основными параметрами арболита:
- Теплопроводность … В зависимости от плотности блока теплопроводность материала варьируется от 0,08 до 0,14 Вт / м ° С (чем выше плотность, тем выше теплопроводность). Эта характеристика значительно превышает теплопроводность керамического кирпича (0,06-0,09 Вт / м ° С). Поэтому дом, утепленный арбоблоками, будет теплым. Для зон с умеренным климатом вполне достаточно толщины кладки 30-35 см.
- Водопоглощение … Оно находится в пределах 40-85% (опять же, в зависимости от марки и плотности арболита).Это очень высокий показатель: помещенный в воду блок способен впитать несколько литров влаги. Соответственно, при строительстве необходимо продумать гидроизоляцию. Кладку необходимо отрезать как от фундамента, так и от внешней среды с помощью внешней отделки.
- Гигроскопичность (способность накапливать водяной пар из воздуха). Благодаря высокой проницаемости (вентиляции) арболит практически не накапливает водяной пар.Поэтому арболит отлично подходит для утепления домов во влажном климате — теплоизоляционный материал не промокнет.
- Морозостойкость … От 25 до 45 циклов. Есть особо плотные марки арболита с морозостойкостью до 50 циклов. Для частных домов, в которых они живут круглый год, особой роли этот показатель не играет. Но для дачных участков и других сезонных построек подобный показатель морозостойкости означает, что блоки выдержат не менее 25 раз промерзания и оттаивания.
Что говорит о довольно долгом сроке эксплуатации построек.
- Усадка … У арболита она одна из самых низких — не более 0,5%. Геометрия стен из арболита практически не меняется со временем от нагрузок.
- Прочность на сжатие … Диапазон здесь большой — от 0,5 до 5 МПа. То есть, если вы уроните арболитовый блок, и на нем образуется глубокая вмятина, то через некоторое время она исчезнет — блок примет первоначальный вид… Таким образом, арболит разрушить крайне сложно.
- Прочность на изгиб — 0,7-1 МПа. В принципе, этот показатель считается выше среднего. Арболит прощает многие ошибки при заливке фундамента — если он сядет, кладка не лопнет и не скроет перекос конструкции.
- Класс огнестойкости G1 … Древесный бетон не поддерживает горение, что делает его одним из самых безопасных материалов среди материалов конкурентов.
Все вышеперечисленное позволяет судить о плюсах и минусах арболита.Начнем с недостатков. На самом деле их всего два:
- Высокая степень водопоглощения. Эта проблема решается запорной гидроизоляцией, а также водонепроницаемой внешней отделкой.
- Арболит полюбился грызунам за натуральность и способность сохранять тепло. Избавиться от этого эксплуатационного недостатка поможет плинтус высотой от полуметра и более.
А теперь перейдем к преимуществам арболита:
- Перечисленные выше высокие технические характеристики.
- Низкая стоимость.
- Арболит из-за своей пористой органической структуры практически не пропускает внешний шум. То есть и со звукоизоляцией проблем не будет.
- Легкость материала от 400 до 900 кг на кубометр. Это преимущество позволяет сэкономить не только на транспортировке к месту строительства, но и на фундаменте. Арболитовый дом просто не нуждается в тяжелом основании из-за небольшого веса несущего ящика.
- Арболит отлично подходит для строительства зданий в районах с высокой сейсмической активностью.
Благодаря пластичности и высоким демпфирующим свойствам, нагрузки не вызовут обрушения здания.
- Экологичность. Благодаря своему составу и паропроницаемости в арболите не образуется грибок или плесень. Как уже отмечалось, единственной проблемой могут быть грызуны. Кроме того, арболит аморфен — он не вступает в реакцию с атмосферой или декоративными строительными смесями, не выделяет токсичных веществ.
- Высокая степень адгезии — стена из арболита не требует дополнительного армирования и отлично подходит практически для всех видов наружной отделки. №
- Легкость обработки арболитов — отлично пилится без специальных инструментов (обычной ножовки), не крошится при сверлении, держит шурупы и гвозди.
- Если делать арболиты своими руками, то благодаря пластичности исходной массы можно формировать элементы практически любой формы и размера. Что дает простор для дизайна геометрии помещения.
Видео — изготовление арболитов своими руками
Арболит делаем сами: инструкция для новичков
Прежде чем перейти непосредственно к пошаговому производству арбоблоков, стоит обсудить несколько нюансов:
- Для арболита ЗАПРЕЩЕНО использовать опилки.
Только щепа.
- Для получения наполнителя подходят практически любые отходы деревообработки — плита, ветки, обрезка бруса, верхушек деревьев.
- Если вы планируете использовать в конструкции здания крупногабаритные арболиты (например, длинные поперечные балки), то стоит позаботиться об их дополнительном армировании. Речь идет не только о прочности рамы, но и о подъемных проушинах для облегчения транспортировки.
Примечание: лучшей древесиной для армирования блоков считаются хвойные породы: сосна, ель.Для лиственных деревьев подходят береза, тополь, осина. Категорически не рекомендуется использовать отходы лиственницы, бука, вяза для изготовления арболита.
Соединение
Для арболита используется цемент высоких марок — М-400 и М-500 … Цемент должен быть свежим и сухим.
Щепа, как уже было сказано, необходимо измельчить до определенного размера — 25х8х5 мм (оптимальный) или 40х10х5 (максимальный) мм. Старайтесь избегать высокой концентрации переклейки — из-за этого конечная прочность арбоблока снизится.
В качестве химических добавок используются:
- Пищевая добавка Е509 — кальция хлорид и нитрат.
- Сульфат алюминия.
- Жидкое стекло.
- Вода питьевая используется (из-под крана). Делать арболитовую смесь с использованием воды из водоемов не стоит — грязь и другие примеси дестабилизируют соединительные связи между составляющими блока, что приведет к его преждевременному разрушению.
ВАЖНАЯ ИНФОРМАЦИЯ: Следуйте процедуре при смешивании ингредиентов.Помните твердо: сначала мы смешиваем воду и химические примеси, затем добавляем туда стружку и только после того, как она равномерно намокнет, добавляем цемент.
Размер арболита
Арбоблоки классифицируются по плотности на:
- Конструкционная — от 500 до 850 кг / м3.
- Теплоизоляция — до 500 кг / м3.
Какие блоки вы будете использовать, зависит от строящегося здания. Для дома в два этажа или одноэтажного дома с цоколем или мансардой следует использовать строительные блоки плотностью 600 кг / м2.Для обычного одноэтажного дома без дополнительных уровней подходят самые легкие конструкционные блоки — 500 кг / м3. При возведении стен теплоизоляционные блоки обычно не используют. Их используют как дополнительную защиту от холода, обшивая стены из других материалов.
Стандартный размер арболита 50х20 см. Но толщина варьируется от 10 до 50 см. Но вы сами можете предусмотреть другие габариты, которые подходят непосредственно вам.
С типичными габаритными параметрами блоков из арболита вы можете ознакомиться из приведенной ниже таблицы:
Также стоит учитывать прочность самодельных арболитов. Он разделен на классы. Если вы планируете построить жилой дом из арболита своими руками, то вам понадобится максимальный класс прочности В2.5:
.
Видео производства арболитов
Пошаговая инструкция
Итак, приступаем к производству арболитов своими руками.
Пропорции для смешивания компонентов берем из этой таблицы:
Обратите внимание: древесная щепа (щепа) должна быть очищена от сахара, иначе она начнет брожение и приведет к поломке блока. Его, конечно, можно удалить химическим путем. Но обычно чипсы просто дают три месяца полежать в воздухе. Помните об этом при подготовке сырья для арболита.
- Вам понадобится бетономешалка принудительного действия. Можно использовать обычную грушу, но качество смешивания будет ниже.
- Добавьте в воду химические добавки в необходимом количестве. Тщательно перемешайте.
- Насыпьте опилки. Немного перемешать. Подождите, пока они полностью намокнут, не осталось сухих «островков».
- Начать добавление цемента порциями. Ни в коем случае не заправляйте сразу весь объем — справиться с комкованием будет очень сложно.
- Поочередно перемешивая и добавляя цемент, добиваемся равномерного обволакивания опилок полученной смесью. Это возможно только в том случае, если опилки достаточно влажные.
- Когда у вас получится однородная смесь, можно начинать раскладывать ее по формочкам.
- Если у вас есть формовочная машина с вибромотором, процесс значительно упростится. Вам просто нужно загрузить сырье, подождать и получить готовый блок.
- Но в кустарных условиях чаще всего используют самодельные формы и ручное прессование (в лучшем случае — вибростол).
- Форма представляет собой металлический ящик без дна. Ставят на ровную поверхность (например, доску) и начинают заливать смесь.Если вы используете ручной прессинг, то делать это нужно послойно. Количество слоев зависит от высоты формы. Обычно делают не менее четырех-пяти слоев.
- Каждый слой утрамбовывается металлической площадкой с ручкой (желательно, чтобы она совпадала по площади с сечением формы). Чтобы воздух из смеси получился лучше, ее в нескольких местах протыкают арматурой, а затем снова утрамбовывают.
- Советуем изготовить (или приобрести) пресс-подборщик. Тогда вы сможете лучше контролировать плотность получившегося блока.Кроме того, в этом случае вы можете вылить в форму сразу весь объем смеси. Это значительно ускорит процесс изготовления.
- Если вам нужны блоки с высокой плотностью, во время трамбовки чередуйте низкое и сильное давление. При такой технике нажатие (изменение формы из-за эластичности раствора) менее выражено, блоки более прочные.
- По окончании утрамбовки удалить излишки раствора металлическим скребком.
- Вибрация еще больше увеличивает прочность готового строительного материала… Если у вас вибростол, то навеска не нужна. Просто положите форму на поверхность стола, загрузите арболит, поместите сверху груз и включите вибрацию.
- После окончания формирования блока его переносят в место сушки. Когда у вас получится достаточно густая смесь, вы можете удалить форму с необработанного блока. Но при изготовлении блоков низкой плотности из арболита раствор получается слишком жидким и теряет геометрию.
В этом случае позаботьтесь о создании достаточного количества форм, чтобы не тратить время зря.
- Летом сушить арбоблоки на открытом воздухе можно 15-20 дней. Но по технологии их предполагается держать двое суток в помещении с температурой 60 ° С.
После всего этого блоки в принципе готовы к использованию в строительных работах … При необходимости их можно обработать для придания нужной формы.
Вместо послесловия
В заключение мы подготовили для вас небольшой дайджест нюансов, которые помогут сделать арболиты своими руками:
- Щепа для арболитов можно изготовить самостоятельно при наличии необходимого оборудования — дробилки и дробилки.Но купить его можно на ближайших деревообрабатывающих заводах или в цехах по производству арбоблоков.
- Чтобы упростить удаление блоков, оберните внутренние стенки формы линолеумом или другим гладким и тонким материалом.
- При необходимости изготовления конструкционного арболита максимальной прочности следует провести гидратацию.
Для этого готовый блок поместите под фольгу на 10 дней при температуре 15 С.
- Если арболит используется не для возведения стен, а для утепления уже построенного здания, некоторыми точностями в технологии изготовления смеси и блоков можно пренебречь.Но не переусердствуйте.
- Если вы избавляетесь от сахара в чипсах с помощью кондиционера, не забудьте перемешать.
- Есть способ сразу подготовить арболит для наружной отделки. Для этого после утрамбовки на верхнюю часть блока наносится слой штукатурки и разравнивается шпателем.
- Если у вас нет специальной сушильной комнаты с нужным температурным режимом, то сушка блоков на открытом воздухе займет не менее двух недель.
Пошаговая технология изготовления арболита предусматривает подготовку основания, определение компонентов и состава блочного материала.В этой статье мы рассмотрим особенности изготовления своими руками с использованием необходимого оборудования, с расчетом массы и заливки.
Достоинства и недостатки арболита
Для многих строителей арболит — ценный и качественный материал для строительства домов. Главная особенность теплоизоляционных свойств позволяет изготавливать листы пола из раствора. Технология изготовления и принципы выдержки и сушки блоков дают арболиту ряд преимуществ:
1.Прочность материала 600-650 кг / м3, что по компонентному составу не уступает любому другому строительному материалу. Главная особенность — пластичность, которая образуется в результате использования древесины, которая качественно армирует блоки. Таким образом, арболит не растрескивается под весом других материалов, а может лишь незначительно деформироваться, сохраняя при этом обычные системные конструкции.
2. Устойчивость к низким температурам, что очень важно в процессе строительства дома и его эксплуатации.Дело в том, что если постройка несколько раз нагреется и промерзнет, это никак не отразится на качестве материала. На самом деле дом из арболита может прослужить не менее 50 лет при любых погодных условиях. Конструкции из пеноблоков такими свойствами не обладают, потому что при постоянном промерзании они быстро потеряют свою функциональность.
3. Арболит не поддается действию углекислого газа, поэтому не беспокойтесь о карбонизации блоков, потому что их структура не позволит материалу превратиться в мел.
4. Теплопроводность блоков говорит о популярности материала. Сравнивая показатели, стоит отметить, что стена из арболита в 30 см равна 1 метру толщины кирпичной кладки … Структура материала позволяет сохранять тепло в помещении даже в самые холодные зимы, что очень экономично при строительстве. .
5. Звукоизоляционные свойства свидетельствуют о высоком коэффициенте звукопоглощения арболита, который колеблется от 0,7 до 0.6. Для сравнения, древесина имеет показатели 0,06 -0,1, а кирпич чуть больше, примерно 0,04-0,06.
6. Легкость материала, позволяющая сэкономить на заливке фундамента.
7. Арболит — экологически чистый и прочный строительный материал, от которого зависит компонентный состав блоков. После постройки дома на стенах не образуется плесень и грибок.
8. Материал безопасен, поэтому не воспламеняется.
9. Арболитовые блоки удобны в строительных работах, ведь можно легко забить гвозди, просверлить отверстие, использовать шурупы и так далее. Внешняя структура материала позволяет покрыть его штукатуркой без использования специальных сеток и дополнительного утеплителя.
Мы рассмотрели преимущества арболитов, но для полного воссоздания картины об этом строительном материале приведем некоторые недостатки:
1. Стеновая панель может не выделяться точными геометрическими параметрами, из которых для восстановления ровности стены используют вагонку, сайдинг или гипсокартон, а сверху все отделывают штукатуркой.
2. Блоки — не дешевый строительный материал, потому что производство древесной щепы для арболита требует определенных затрат. При расчетах по сравнению с газобетоном этот строительный материал будет стоить всего на 10-15 процентов дороже, что не дает полного преимущества.
Технология производства арболита
Производство арболита требует соблюдения производственных технологий с расчетом состава и объема на один блок.Арболитовые блоки — это строительный материал с простым компонентным составом, в который входят древесина, вода, опилки, цемент и другие предметы.
Основной базой производства считается древесная щепа. Составная часть арболита определяет его прочность и устойчивость к повреждениям, которая рассчитывается на более высокий уровень, чем пеноблоки или пеноблоки. Домашнее производство осуществить несложно, но необходимо придерживаться распределения массы объекта и следовать инструкции.
Подготовка фундамента к работе
Основным компонентом для изготовления щепы для арболита является соотношение пропорций стружки и опилок — 1: 2 или 1: 1. Все предметы хорошо просушены, для чего их помещают на свежий воздух на 3 — 4 часа. месяцев, время от времени обработка известью и переворачивание.
Примерно на 1 кубический метр продукта потребуется около 200 литров 15-процентной извести. Все чипсы помещают в них на четыре дня и перемешивают от 2 до 4 раз в день.Все работы проводятся для того, чтобы удалить из дерева сахар, который может спровоцировать гниение блоков. Стружка покупается в готовом виде, однако с помощью стружколомов можно сделать своими руками.
Компоненты и состав арболита
Компонентный состав арболита является важнейшим этапом в технологии производства и требует тщательного соотношения всех материалов. При изготовлении блоков важно следить за качеством и разнообразием покупаемых материалов, от которых зависит готовый строительный материал.После процесса изготовления в чипы добавляются следующие материалы, например:
- известь гашеная;
- стекло жидкое растворимое;
- портландцемент;
- хлорид калия;
- сульфат алюминия и кальция.
Производство арболита в пропорциях представлено в таблице 1. Следует отметить, что для всех компонентов масса рассчитана на четыре процента доли цемента. Такое расположение помогает сохранить огнестойкость объекта и придает пластичность.
Таблица 1. Состав арболита по объему
Производственный процесс и принципы
Оптимальные параметры блоков для технологии производства арболита — 25х25х50 сантиметров. Указанные размеры удобны при кладке стен домов, а также в процессе производства. Заливка блока состоит из трех рядов смеси и арболита; после каждого этапа необходимо утрамбовать раствор молотком, отделанный жестью.
Избыточная масса скатывается шпателем. Блок хранится на открытом воздухе при температуре 18 градусов Цельсия. Через сутки арболит вытаскивают из формы на плоскую поверхность, где он удерживается в течение 10 дней.
Оборудование: применение на практике
Для производства требуются разные расходные материалы, например, станки для производства арболита, которые подбираются в соответствии с объемом производства и количеством сырья. Технология производственного процесса должна соответствовать требованиям и критериям СН 549-82 и ГОСТ 19222-84. Основной материал для разработки — хвойные деревья … Измельчение древесины осуществляется измельчителями типа ППМ-5, ДУ-2, а более щепетильное измельчение — на оборудовании ДМ-1.
Смесь арболита приготовлена с использованием смесителей и растворителей различного циклического воздействия на материал. Доставляют большие объемы обработанной смеси в формы с помощью устройства в качестве бетонораспределителей или кубелей.Подъем или опускание машины необходимо производить с параметрами 15o для верхнего подъема и 10o для нижнего, а скорость оборудования рассчитывается в 1 м / с. Арболит заливается в формы на высоте до 1 метра.
Раствор уплотняют с помощью вибромашины или ручного трамбовки. Для изготовления небольшого количества блоков нужно использовать мини-станок. Изготовление арболита своими руками не представляет особых сложностей, однако на промышленных объектах используется специальное оборудование для перемешивания, изготовления блоков. На некоторых заводах есть термокамеры с инфракрасным излучением или нагревательными элементами, что позволяет определять необходимую температуру для сушки блоков.
Блочные формы для арболита
Существуют различные формы блоков для обработки арболита, и примерные значения могут быть: 20x20x50 см или 30x20x50 см. Также производятся объекты других размеров, особенно для устройства систем вентиляции, покрытий и так далее. Формы можно приобрести в строительных магазинах или приготовить все самостоятельно.Для этого используются доски толщиной 2 сантиметра, которые крепятся до образования определенной конструкции. Внешне форма отделывается фанерой или пленкой.
В зависимости от класса арболиты используются в малоэтажном строительстве для возведения несущих стен, перегородок, а также для теплоизоляции и звукоизоляции конструктивных элементов здания.
Процесс изготовления своими руками
Рассмотрев технологию изготовления арболита, можно приступать к работе самостоятельно. Для начала вам понадобятся материалы и оборудование:
- лоток специальный для смеси;
- падающий и вибростол;
- стол с ударно-встряхивающим эффектом;
- формы и стойки разъемные; Поддон металлический
- для форм.
Сделать арболит своими руками без использования необходимых инструментов, станков и оборудования очень сложно. Как правило, в производстве потребуется несколько устройств:
1. Для получения качественного раствора необходимо использовать бетономешалку.Конечно, в процессе все можно сделать своими руками, однако для получения раствора необходимой консистенции придется потратить немало времени.
2. Для формирования структуры блоков важно приобретать формы соответствующего размера. Как правило, арболит имеет прямоугольную форму, в производстве используются пластиковые формы.
3. С помощью станка вы профессионально измельчаете щепу.
4. С помощью пресса можно получить материал хорошей плотности при уплотнении, при этом важно удалить воздух из консистенции. Вибростол используется в качестве аксессуаров.
5. Обязательное наличие камеры сушки арболита, которая даст возможность превратить его в прочную однокомпонентную конструкцию.
6. В домашних условиях понадобится лопата для загрузки смеси в формы, а для скрепления блоков используется армирующая сетка.
При наличии вышеперечисленных устройств можно производить около 350-450 м3 раствора в месяц в сутки. Для установки потребуется около 500 квадратных метров, а стоимость электроэнергии составит 15-45 кВт / час.Для самостоятельного процесса органические продукты заливаются водой и цементом до образования однородной смеси. Все пропорции и расчеты приведены в таблице 1, главное, чтобы выпускаемая смесь была сыпучей.
Перед тем, как разлить раствор по формам, они покрываются изнутри известковым молоком. После этого изделие аккуратно и бережно укладывается и утрамбовывается специальными приспособлениями. Верхняя часть блока выравнивается шпателем или линейкой и заливается гипсовым раствором слоем в 2 сантиметра.
После того, как арболит сформируется, его нужно будет тщательно утрамбовать деревянной конструкцией, проложенной железом. Блоки, которые простояли и схватились десять дней при температуре 15 °, считаются прочными и надежными. Чтобы арболит не высыхал, рекомендуется периодически поливать его водой.
Технология изготовления арболита своими руками не представляет определенной сложности, а потому все работы легко провести при наличии необходимых инструментов и приспособлений.При соблюдении правил и критериев производства, правильного расчета комплектующих, строительный материал получится качественным и прочным в эксплуатации.
Рекомендации специалистов по производству арболитов основаны на практике их использования и применения. Для достижения высокого качества необходимо учитывать определенные факторы. При производстве рекомендуется использовать не только крупную стружку, но и использовать опилки, стружку. Обработка консистенции и выдавливание из нее сахара позволяет избежать дальнейшего разбухания строительного материала, которое не опускается при постройке дома.
В процессе изготовления раствор следует тщательно перемешать, чтобы все части были в цементе. Это важно для качественного и прочного склеивания дерева и других материалов в блоке. При производстве не менее важно добавлять следующие компоненты, например, алюминий, гашеную известь и так далее. Весь состав формирует дополнительные свойства арболита, например, жидкое стекло не позволяет блокам впитывать влагу, а известь служит антисептиком.
Хлорид калия способствует уничтожению микроорганизмов и других веществ, не оказывающих благоприятного воздействия на структуру. При добавлении всех компонентов стоит руководствоваться таблицей соразмерности, чтобы готовый раствор соответствовал требованиям для производства арболитов.
— очень необычный вид бетона, где основным наполнителем являются отходы деревообрабатывающей промышленности — стружка, иглы и прочее. Именно состав обеспечивает этот строительный материал.Итак, сегодня поговорим о составе для и блоков из него по ГОСТу, пропорциях, рецептуре и технологии производства.
Как и любой бетон, в состав материала входит и наполнитель — только органического происхождения, а также различные добавки. Происхождение и свойства ингредиентов влияют на качество конечного продукта.
Органические наполнители придают древесному бетону очень значительные тепло- и звукоизоляционные свойства. По прочности материал не сильно уступает бетону с такими же показателями плотности. Такое сочетание качеств возможно только при правильном выборе сырья.
О том, как сделать щепу для производства арболита своими руками, расскажем ниже.
Более подробно о том, как выбрать состав для арболита и опилок, расскажет это видео:
Органические ингредиенты
В качестве шпатлевки для дерева используется несколько видов материала. Не вся стружка подходит в качестве сырья — не путайте материал с опилками бетона.Новый ГОСТ четко регламентирует размер и геометрию фракций, добавляемых в арболит.
- Щепа — получают путем измельчения нетоварной древесины — плит, сучков, вершин и т.
п. Для производства арболита используется щепа длиной 15–20 мм — не более 40 мм, шириной 10 мм и толщиной 2–3 мм. В промышленных условиях дробление осуществляется на специальных установках. Практические исследования показывают, что для достижения наилучшего качества щебень при древесном бетоне должен иметь игольчатую форму и быть меньшего размера: длиной до 25 мм, шириной — 5-10 мм, толщиной 3-5 мм.Дело в том, что древесина по-разному впитывает влагу вдоль и против волокна, и указанные выше размеры нивелируют эту разницу.
Не всякое дерево подходит для щепы: можно использовать ель, сосну, осину, березу, бук, но нежелательно лиственницу. Перед использованием древесный материал необходимо обработать антисептическими составами для предотвращения развития плесени или грибка.
- Можно также использовать измельченную кору и иглы . Однако их доля меньше: кора должна составлять не более 10% от массы продукта, а хвоя — не более 5%.
- Сырьем может быть рисовая солома , костровый лен и конопля , а также стебли хлопка.
Материалы измельчаются: длина не должна превышать 40 мм, ширина — 2–5 мм. Перья и пакля, если они есть в наполнителе, не превышают 5% по весу. ГОСТ 19222-84 регламентирует размер фракций, получаемых при измельчении того или иного сырья. И хотя допускаются отклонения в пропорции ингредиентов, отклоняться от стандартов на сырье нельзя.
Лен содержит большое количество сахаров, которые, вступая в реакцию с цементом, разрушают его. Предварительно льняной костер замачивают в известковом молоке — 1-2 дня или выдерживают на воздухе 3-4 месяца.
Неорганические компоненты
Следующие вещества действуют как вяжущие в арболите, именно так и называется арболит:
- — материал традиционный и самый популярный;
- Портландцемент с минеральными добавками — обычно, повышая морозостойкость блоков; Сульфатостойкий цемент
- , за исключением пуццоланового, обеспечивает стойкость к химически агрессивным веществам.
Согласно требованиям ГОСТ может использоваться только материал соответствующей марки:
- не менее 300 для теплоизоляционного арболита;
- не менее 400 для конструкционных.
А теперь поговорим о пропорциях химических добавок в составе арболита.
Химические добавки
Общее количество дополнительных ингредиентов может составлять до 2–4% от веса цемента. Большинство из них повышают прочность арболита: вещества взаимодействуют с сахарами, присутствующими в древесине, и образуют безвредные для цемента соединения.
Конкретное количество ингредиентов определяется маркой арболита. Например, арболит марки 30 может включать:
- хлорид кальция и сульфат алюминия в соотношении 1: 1 — не более 4% от массы цемента;
- хлорид кальция и сульфат натрия в соотношении 1: 1 — не более 4%;
- хлорид алюминия и сульфат алюминия в соотношении 1: 1 — не более 2%;
- хлорид кальция и хлорид алюминия в соотношении 1: 1 — не более 2%.
Силикаты натрия и калия также могут использоваться для тех же целей.
Вода
ГОСТ регламентирует степень чистоты воды, но на практике применяется любая — центральный водопровод, колодцы, колодец. Для качества арболита решающее значение имеет температура воды. Его добавляют в состав вместе с дополнительными ингредиентами.
Для того, чтобы скорость гидратации цемента была достаточной, необходима вода с температурой не ниже + 15 ° C.Уже при + 7– + 8 ° С скорость схватывания цемента заметно снижается.
Пропорции
Состав арболита строго не регламентирован. Если материал соответствует требованиям ТУ, то этот показатель считается более важным, чем точность состава. Примерные пропорции следующие: 1 часть заполнителя, 1 связующее и 1,5 части строительного раствора с химическими добавками.
Точнее состав рассчитан на конкретную марку, где важно добиться необходимой прочности и плотности.
Например, коэффициент для обычного арболита, рассчитанный на получение 1 кубометра. м.
Если древесный наполнитель неоднородный, то доля стружки и стружки в нем определяется как соотношение объемов, например, 1 ведро опилок и 1 ведро стружек. Также допускается 1 ведро опилок и 2 стружки.
- В смеси с измельченными пропорции щепы и опилок будут равны — 1: 1: 1.
- Огонь льна и стебли хлопка могут заменить опилки в той же пропорции.
О том, как замешивают арбалитобетонную смесь по указанным пропорциям, расскажет этот видеоролик:
ГОСТ
.Состав арболита регламентируется ГОСТ 19222-84. Стандарт позволяет подбирать состав смеси в лабораторных условиях, но предъявляет жесткие требования к сырью и параметрам конечного результата. В зависимости от прочности на сжатие и показателей теплоизоляции различают 2 вида арболита:
- теплоизоляционные, то есть предназначены для утепления стен;
- конструкционный — допускается возведение самонесущих стен.
Показатели у этих материалов разные.
Тип арболита | Класс прочности на сжатие | Класс прочности на осевое сжатие | Средняя плотность, кг / куб. м. | |||
---|---|---|---|---|---|---|
На рубленых дровах | На костре стеблей льна или хлопка | На костре конопли | На рисовой соломке | |||
Теплоизоляция | B0.![]() | M5 | 400–500 | 400–450 | 400–450 | 500 |
B0.75 | M10 | 450–500 | 450–500 | 450–500 | ||
B1.0 | M15 | 500 | 500 | 500 | ||
Строительный | B1,5 | — | 500–650 | 500–650 | 550–650 | 600–700 |
B2.0 | M25 | 500–700 | 600–700 | 600–700 | — | |
B2.5 | M35 | 600–750 | 700–800 | — | — | |
B3.5 | M50 | 700–850 | — | — | — |
Поскольку условия эксплуатации арболитов могут быть самыми разными, к ним могут быть предъявлены дополнительные требования, регламентированные ГОСТ 4. 212-80.
присвоены по ГОСТ 25192-82. Также может быть указана структура материала.
Габаритные отклонения в изделиях
ГОСТ регламентирует возможные отклонения размеров в изделиях:
- длиной, при общей длине блока до 3,0 м — не более 5 мм;
- при длине изделия от 3 до 6 м — 7 мм;
- отклонения по высоте и толщине могут быть только в пределах 5 мм;
- погрешность размеров выступов, выемок, полок, ребер и так далее не превышает 5 мм.
Допускается армирование арматурных изделий сеткой и стальными стержнями, регламентированное соответствующим ГОСТом.
Поскольку материал не отличается высокой влагостойкостью, внешняя поверхность изделий покрывается слоем декоративного бетона или другого материала с минеральными наполнителями. Внутренний слой может отсутствовать. Допускается отделка цементным или цементно-известковым раствором.
Проверка арбалетной смеси
По ГОСТу не менее 2 раз в смену проверяют арбалитовую смесь:
- оцените показатель плотности;
- удобоукладываемость;
- уровень расслоения;
- оценка межкристаллитных пустот.
Для проверки прочности проводится серия лабораторных испытаний смеси через 7 дней отверждения, смеси через 28 дней и смеси, испытанной через 7 дней и 28 дней.
- оценено для отделочного и несущего слоев,
- Теплопроводность измерена на образцах смеси,
- Влага рассчитана на образцах готовой продукции.
Только если смесь пройдет испытания, предлагаемые ГОСТом, она может быть полностью признана рабочей и принята в производство.
Арболит — пример удачного сочетания органического наполнителя и неорганического связующего. Как и для всех видов бетона, от состава во многом зависит качество конечного продукта.
Как выбрать состав арболита и замесить ингредиенты для строительства гаража, вы узнаете из видео ниже:
Как правильно делать? Подготовка древесной массы
Арболитовые блоки используются в малоэтажном строительстве с середины 40-х годов прошлого века.В то время было построено множество заводов по его производству. В наше время он остается популярным строительным материалом.
Арболитовые блоки производятся из опилок, стружки, цемента, воды и химикатов. Они относятся к классу легких бетонов. Их использование зависит от показателя плотности. Их можно использовать:
- как теплоизоляционный материал;
- для возведения стен без нагрузки;
- на строительство хозяйственных построек.
Если показатель плотности менее 500 кг / м3, то арболит считается теплоизоляционным.Если этот показатель находится в пределах от 500 до 800 кг / м3, то он конструктивный. Преимущества использования арболитов заключаются в дешевизне компонентов, а значит, и в общей стоимости материала.
Арболитовые блоки (бетонные опилки) — хорошие теплоизоляторы. Они отлично аккумулируют и сохраняют тепло в доме. Изготовление блоков достаточно простое, поэтому вы можете изготовить их самостоятельно.
Преимущества и недостатки
Для того, чтобы оценить бетонные блоки из опилок как строительный материал, необходимо разобраться, в чем их плюсы и минусы. У них есть следующие преимущества:
Самым большим недостатком арболитов является их высокая влагопроницаемость. Если материал накапливает слишком много влаги, он может даже разрушиться.
С этим недостатком борются за счет применения специальных защитных покрытий, покрывающих стены слоями гидро- и пароизоляции. Кроме того, арболиты не устойчивы к грызунам.
Стены можно защитить от грызунов обшивкой OSB, сеткой, а после возведения фундамента можно сделать бетонную заливку высотой 50 см.
Смотрите нашу видео-подборку по теме:
Технология производства
Производство бетонных блоков из опилок состоит из следующих этапов:
Собственное производство
Низкая стоимость сырья, невысокие трудозатраты и простая технология производства привлекательны при производстве деревянных блоков. Поэтому сделать арболиты своими руками можно. Такие блоки нельзя использовать для несущих стен, так как в домашних условиях невозможно соблюдать всю технологию.
Производство вручную занимает много времени. Поскольку на просушку опилок, чтобы избавиться от сахарозы, потребуется три месяца, а также потребуется не менее трех месяцев для достижения необходимой плотности деревянных блоков.
Если вас не пугает длительность изготовления, то вы можете приступить к изготовлению блоков своими руками. В первую очередь нужно подготовить необходимое количество опилок, стружки или однородной стружки.
Могут остаться после столярных работ, можно получить опилки с помощью измельчителя, договориться на лесопилке, где их сожгут или выбросят.Опилки можно заменить хвоей, корой или листвой. При этом добавляемые компоненты не должны составлять более 5% от общего количества древесного наполнителя.
Размер наполнителя должен быть толщиной не более 5 мм и длиной не более 25 мм. Если размеры больше, то наполнитель пропускают через болгарку до получения нужного размера.
Далее по технологии необходимо выдержать опилки на воздухе до 90 дней, чтобы сахароза испарилась.
При этом опилки необходимо все время перемешивать, чтобы воздух попадал во все слои и сахароза равномерно испарялась. Для максимального эффекта опилки можно залить оксидом кальция.
После высыхания опилки просеивают через сито, чтобы избавиться от загрязнений. Готовые опилки смачивают водой и смешивают с цементом марки 400 или 500. Пропорции смешивания следующие: 4 части воды, 3 части древесины и 3 части цемента.
Материал химически обрабатывают путем добавления жидкого стекла в воду.Чтобы ускорить процесс, можно добавить в древесную массу хлорид кальция. Также в качестве добавок для блоков используется смесь сульфата алюминия и сульфата кальция в соотношении 50/50. Гашеная известь добавляется для дезинфекции.
Готовую смесь загружают в бетономешалку и перемешивают. Если смесь качественная, то она должна быть рассыпчатой и при сжатии не менять форму и не растекаться.
Полученный арболит заливают в подготовленные формы.
Формы следует обшить линолеумом, чтобы раствор не приставал к стенкам формы.
Раствор, налитый в формы, необходимо хорошо встряхнуть, чтобы удалить воздух. Можно стучать по стенам молотком, а лучше всего использовать вибратор. В формах смесь выдерживают трое суток. Затем готовые блоки следует выдержать в помещении с температурой не ниже 15 градусов еще три недели.
В производстве арболита своими руками может потребоваться следующее оборудование:
Дополнительное оборудование обойдется примерно в 50 000 руб.Если учесть другие затраты, которые составляют 75 000 рублей, то для организации производства арболита своими руками вам потребуется порядка 900 000 рублей.
Стоимость готовых блоков указана ниже.
Посмотрите нашу видео-подборку по производству арболита:
Отечественная строительная отрасль регулярно пополняется новыми технологическими решениями. В последнее время резко увеличилось производство арболитов. Учитывая преимущества, которыми характеризуется представленный материал, строители из разных регионов все чаще выбирают его.
Арболитовые блоки — описание материала
Арболит — один из видов легкого бетона, для создания которого используется органический наполнитель в виде древесной стружки. Цемент увеличивает структурную прочность материала. Дополнительно производители включают воду и химические добавки.
В зависимости от назначения арболит делится на две категории — теплоизоляционные и конструкционные.
Определяющим фактором является плотность материала.При возведении несущих частей здания не допускается использование блоков плотностью не более 500 килограммов на кубический метр. Они подходят для устройства теплоизоляции наружных стен в конструкциях с дополнительными несущими элементами, принимающими на себя основную нагрузку от перекрытий и кровли.
Разница между блоками на основе арболита — показатель плотности, который колеблется от 550 до 700 килограммов на кубический метр. В домах из арболита, проекты которых предусматривают использование материалов плотностью 850 килограммов на кубический метр, они отличаются высокой прочностью, но худшими теплоизоляционными свойствами.С увеличением плотности показатель теплоизоляции уменьшается. Плотность измеряют после получения стабильной массы после выделения лишней влаги.
Состав из арболитов
Технология производства арболитов предусматривает использование следующих видов материалов:
- щепа хвойная. Его производство осуществляется на территории специализированного предприятия по производству арболита;
- минерализатор.Создан на основе сульфата алюминия. Компонент не выделяет вредных веществ, популярен в медицинской и пищевой сфере. Без очистки промышленной и бытовой питьевой воды не обойтись;
- Портландцемент. Марка продукции — М500. Используется как связующее между древесной стружкой и сульфатом алюминия.
Технология производства
При наличии блоков внутри формы специалисты проводят зачистку с последующей смазкой деталей эмульсолом. После завершения процедуры производится сборка. Далее запускается стандартный цикл, по которому производятся блоки из арболита. Его выполнение занимает не более 15 минут при работе 4 сотрудников.
Последовательность действий при производстве каждого арболита следующая.
- Заполнитель загружается в дозатор. Последний закреплен на подъемнике, который подает материал внутрь смесителя. В некоторых моделях производственного оборудования предусмотрено использование механизма подъема дозатора.
- В заполнитель добавляется минерализующий раствор, затем портландцемент.
- Методика самостоятельно смешивает компоненты в течение трех-пяти минут, после чего готовую смесь подают на вибропресс с вибростолом.
- Смесь выравнивается, каждая ячейка получает свою контактную пластину. Затем вибростол поднимается до уровня трамбующих плит. Здесь материалы прессуются с помощью пресса и формы.
- Специалисты своими руками устанавливают фиксаторы контактной пластины, взаимодействующей с формой.
После завершения процедуры прессования форма отправляется в сушильную камеру. В соответствии с нормативными требованиями ГОСТ, штабелирование друг на друга допускается, но при обязательном использовании деревянных брусков. Конкретные температуры, при которых сушатся блоки, не предусмотрены ГОСТом. Микроклимата должно хватить для полного застывания блока через сутки. Самостоятельно сделать качественный блок в домашних условиях не получится.
К положительным характеристикам материала можно отнести следующие.
Недостатки арболита
Идеальных стройматериалов не существует, и арболит не исключение. У него тоже есть свои недостатки.
- Состав на 80 процентов состоит из древесной щепы. Продукция, изготовленная в соответствии с нормативными требованиями ГОСТ, не нуждается в дополнительной защите антисептическими препаратами. При использовании дешевых блоков нужно дополнительно покупать препарат для биобезопасности.
- Строение из арболита может иметь неровную форму.
Недостаток может проявляться в разной степени, исходя из качества и пропорций, используемых при производстве. Чтобы получить идеальные геометрические формы, нужно выбирать изделия премиум-класса.
Недостатки проявляются только тогда, когда покупатель сознательно отказывается от заказа качественных стройматериалов. Такой вывод напрашивается сам собой — арболит нельзя воспринимать как строительный материал с большим количеством недостатков.На полученный результат влияет только надежность материала и добросовестность строителей.
Для строительства домов используются различные виды блочных материалов для ускорения строительства. При выборе блоков важно учитывать прочность материала, экологичность, теплоизоляционные и звукопроводящие свойства. Возрос интерес девелоперов к арболиту, который изготавливается на основе цемента и щепы.Изготовить блочные арболиты и арболиты своими руками несложно, предварительно подготовив древесные породы и портландцемент. Остановимся на свойствах материала, рассмотрим достоинства и недостатки изделий, а также познакомимся с нюансами технологии.
Что такое готовый арболит
Чип-блоки — это разновидность легкого бетона. Их отличает крупнопористая структура и наполнитель, который используется в качестве стружки.Стандартные изделия имеют форму прямоугольного параллелепипеда размерами 0,5×0,3×0,2 м. Выпускаются также блочные изделия с другими размерами, соответствующими габаритам формовочной коробки. Наряду с блоками арболитовые изделия выпускаются в виде плит, для увеличения прочности которых выполняется армирование.
Арболит состоит из следующих компонентов:
- древесный наполнитель в виде стружки определенных размеров;
- специальных активных добавок с химическими компонентами;
- вяжущее на основе портландцемента М400;
- вода, обеспечивающая пластичность арболитов.
Одним из условий получения качественного материала является равномерное перемешивание ингредиентов. Сначала определяется масса каждого вида сырья в зависимости от необходимого количества раствора. Затем смешиваются подвешенные компоненты и выполняется следующий этап — заполнение ящиков опалубки раствором. Чтобы обеспечить повышенную плотность блоков, смесь уплотняют в формах. Строителям, занимающимся производством, несложно освоить этот способ производства арболита.
В малоэтажных домах возводятся сплошные стены из арболитов и возводятся внутренние перегородки:
- жилых домов;
- хозяйственных объекта;
- производственных здания.
Блоки и плиты из арболитной смеси различаются по удельному весу и функциональному назначению. Коэффициент запаса прочности и удельный вес арболита связаны прямо пропорционально. Более плотные изделия превосходят по прочностным характеристикам блоки с пониженной плотностью.
Арболит подразделяется на следующие виды:
- материал плотностью до 500 кг / м3, применяемый для утепления различных типов строительных конструкций;
- конструкционных изделия с удельным весом 500-800 кг / м3, которые используются для возведения несущих стен.
Использование древесного наполнителя и крупноячеистая структура массива арболита не позволяют использовать материал при высоких нагрузках.В качестве материала стоит убедиться, приобретая арболит для строительства частного дома. Не всегда используется качественное сырье и рабочая смесь пропитана жидким стеклом, что снижает гигроскопичность.
Для строительства частного дома следует убедиться в качестве материала.
Основные эксплуатационные характеристики арболитов
Планируя изготовить блоки или арболиты своими руками, следует ознакомиться со свойствами строительного материала.
Рабочие характеристики материала зависят от следующих факторов:
- качество сырья;
- пропорции компонентов в растворе;
- выполнение требований технологического процесса.
Основные характеристики:
- плотность. В зависимости от плотности используемого сырья и особенностей технологии изготовления удельный вес материала варьируется в пределах от 0.
От 5 до 0,85 т / м3;
- силы. Он характеризует способность материала воспринимать сжимающие нагрузки. Допустимая нагрузка по конструкционным материалам В1,5-В3,5, по теплоизоляционным материалам — В0,35-В1,0;
- теплопроводность. Способность арболита проводить тепло выражается коэффициентом теплопроводности, который увеличивается с 0,09 Вт / м ° C для теплоизоляционных материалов до 0,14 Вт / м ° C для конструкционных блоков;
- Морозостойкость. Устойчивость материала к воздействию перепадов температур зависит от влажности пористого арболита, который способен сохранять свою целостность при циклическом замораживании;
Арболит — материал с высокой теплоизоляцией.
- влагопоглощение.Материал отличается повышенной гигроскопичностью, связанной с капиллярным заполнением древесного наполнителя влагой. В процессе насыщения арболита влагой через воздушные ячейки объем материала увеличивается в 1,5 раза;
- усадка. Способность материала изменять свой первоначальный объем зависит от исходного содержания влаги.
Окончательно процесс уменьшения размера останавливается через пару месяцев после изготовления блоков;
- Пожарная безопасность.Несмотря на древесную стружку внутри арболитов, блоки входят в группу трудногорючих материалов. Арболитовый материал относится к продукции группы G1;
- паропроницаемость. Пористый массив плит из арболита не создает препятствий для выхода пара из помещения, что способствует поддержанию комфортного микроклимата внутри здания.
К важным характеристикам изделий из арболита относятся также звукоизоляционные свойства, благодаря которым материал препятствует проникновению внешнего шума в помещение.По шумопоглощению арболит превосходит традиционно используемые материалы — кирпич, дерево и др.
Строительные блоки из арболита — преимущества и недостатки материала
Арболит постепенно завоевывает популярность в строительной отрасли благодаря своим серьезным преимуществам:
Арболит превосходит традиционно используемые материалы по шумопоглощению.
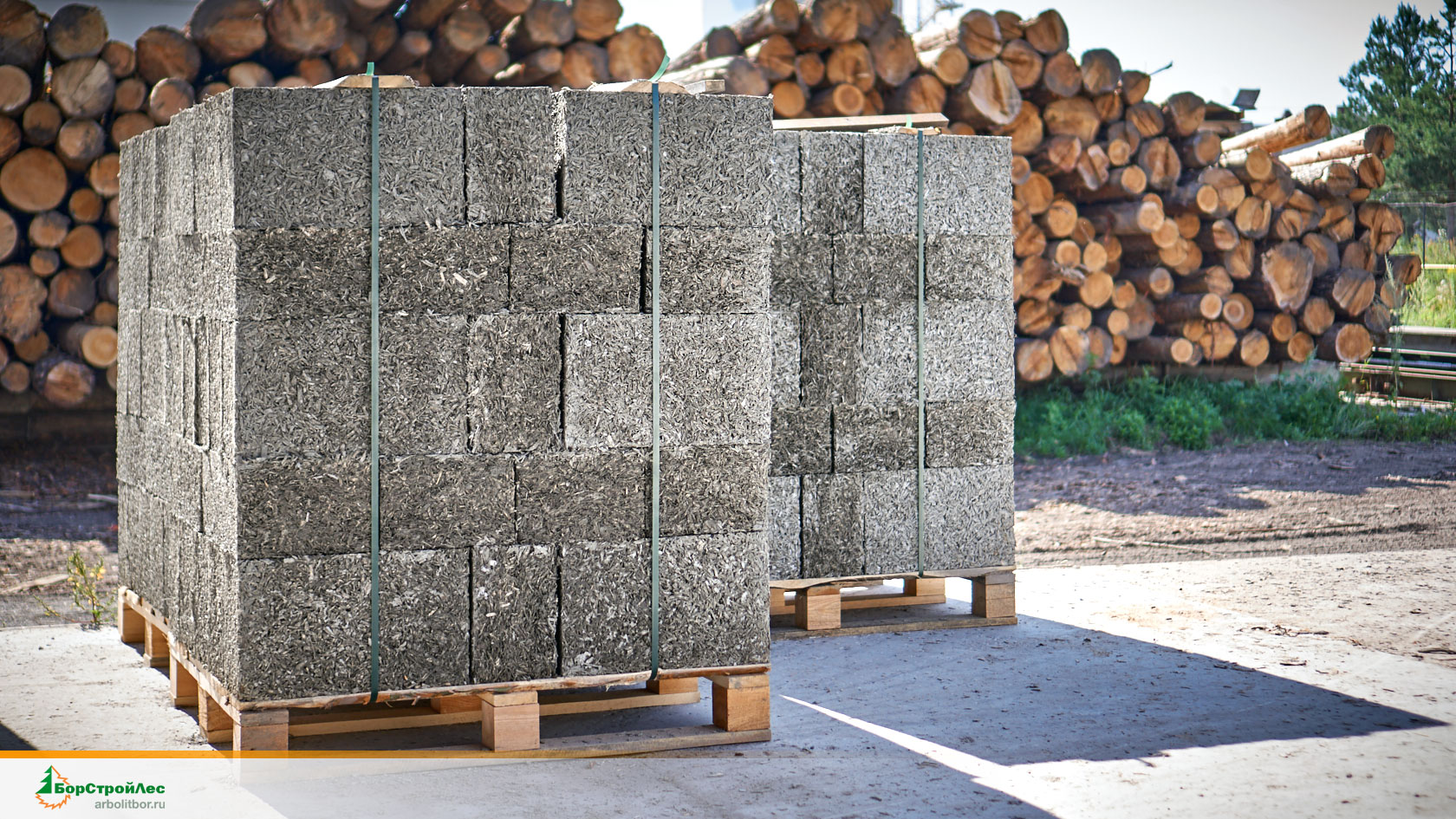
- Пониженный коэффициент теплопроводности. В домах, построенных из арболитов, круглый год поддерживается температура, благоприятная для жилых помещений.К тому же за счет пониженной теплопроводности снижаются затраты на отопление;
- достаточный запас прочности. При сжимающей силе 5 МПа и изгибающей нагрузке 1 МПа материал не разрушается. Благодаря прочности материала арболиты постепенно восстанавливают свою форму и первоначальные размеры;
- морозостойкость. Производители арболитов и плит гарантируют морозостойкость изделий. Испытания подтверждают сохранение характеристик материала после 40-60 циклов интенсивного охлаждения с последующим резким оседанием;
- возможность снижения уровня шумового воздействия.Звукоизолирующие характеристики древесной щепы, используемой в качестве наполнителя, позволяют создать в помещении благоприятные условия для проживающих за счет поглощения внешнего шума;
- уменьшенной массы при увеличенном объеме. Используя легкие и объемные арболиты, несложно быстро возвести капитальные стены дома.
Уменьшенная масса блочного материала позволяет значительно снизить нагрузку на фундамент;
- Безвредность для здоровья и окружающей среды. Технология изготовления изделий из арболита предусматривает использование экологически чистого сырья.Отсутствие вредных выбросов от арболита подтверждает безвредность материала для окружающих;
- простота использования. Арболит легко разрезать на заготовки нужного размера с помощью подручного инструмента. Исключаются проблемные ситуации при резке материала и формировании в нем каналов. Кроме того, для армированной штукатурки армирующей сетки не требуется;
- с сохранением исходных размеров под нагрузкой. За счет малой усадки арболитов, не превышающей 0.На 6% снижается вероятность появления трещин на стенах здания. Размеры блочного материала сохраняются после извлечения из формы и сушки;
- доступная цена. Низкая стоимость материала обеспечивается использованием дешевых отходов, которые накапливаются на деревообрабатывающих предприятиях в процессе изготовления различной продукции;
Арболит безвреден для здоровья и окружающей среды
- прочность.
Несмотря на то, что арболит в последнее время приобрел популярность на строительном рынке, это строительный материал с длительным сроком службы.Безопасная эксплуатация арболитов гарантируется до полувека.
Арболит востребован в строительной отрасли благодаря комплексу преимуществ. Проанализировав недостатки арболита, мы получаем полное представление о характеристиках строительного материала.
Итак, слабые места арболита:
- нестабильность размеров изделия. Более высокие значения допусков на размеры связаны с использованием форм разных производителей, которые различаются по размеру.Избежать повышенного расхода гипсового состава, связанного с размерными отклонениями, позволяет покупка блоков у одного поставщика;
- Необратимые изменения структуры арболита при интенсивном нагревании. И хотя открытый огонь не вызывает возгорания в арболите, из-за высокой температуры, связанной с резким нагревом, стружка тлеет.
Это значительно снижает прочность материала;
- склонность к впитыванию влаги. Из-за повышенной гигроскопичности арболита происходит ускоренное насыщение влагой незащищенных стен.Поверхность материала требует обязательного оштукатуривания снаружи и изнутри здания. Также требуется гидроизоляционная защита фундамента, с которым контактируют арболиты.
К другим недостаткам можно отнести:
- возможность развития микроорганизмов из-за пониженной концентрации извести;
- необходимость в дополнительном утеплении из арболита, который легко продувается;
- характерный запах, связанный с введением в материал химических реагентов;
- Повреждаемость блоков различными грызунами, проявляющими к этому интерес.
Решив сделать своими руками арболиты для строительства дома, ознакомьтесь с преимуществами материала и внимательно проанализируйте недостатки.
Благодаря комплексу преимуществ арболит широко применяется в строительстве.

Как сделать арболиты своими руками
Ответ на вопрос, как сделать арболиты своими руками, интересует многих застройщиков. Для изготовления продукции необходимо:
- разбираются в технологии;
- выберите проверенный рецепт;
- закупить необходимые комплектующие;
- подготовить оборудование и инструменты;
- изготовить формовочные ящики.
Остановимся на основных моментах подробнее.
Какие материалы и оборудование используются для производства блоков
Для самодельного арболита следует подготовить:
- стартовых компонентов в необходимом количестве;
- лопаты и ведра для загрузки ингредиентов в миксер;
- рубильный агрегат для предварительного измельчения материала;
- сепаратор для очистки щебня;
- дробилка для измельчения щепы до необходимой фракции;
- бетономешалка для смешивания компонентов;
- формовочная коробка; Трамбовка
- для уплотнения смеси.
Для промышленного производства арболита потребуется виброплатформа, позволяющая изготавливать блоки повышенной плотности.
Приготовление щепы для производства арболитов
Состав рабочей смеси и пропорции ингредиентов
Несмотря на простой рецепт изготовления арболита и доступность сырья, следует уделять внимание вопросам качества.
Наполнитель, который используется в виде древесных опилок, стружки или щепы, требует специальной подготовки:
- очистка от инородных включений;
- измельчение до крупности не более 0.5х1х4 см;
- сушка от двух до трех месяцев;
- обработка известью для предотвращения гниения.
Раствор извести 15% концентрации вводится в количестве до 500 литров на кубометр стружки. Замачивание отходов деревообработки осуществляется при регулярном перемешивании материала. Процесс длится не более недели. В этот период в древесине снижается содержание сахара, что снижает вероятность гниения. Допускается использование покупного сырья или измельчение древесных отходов в бытовых условиях с помощью дробилки.
Кроме древесной стружки, для изготовления арболита вам также понадобятся:
- цемент марки М400 или М500. Не используйте затвердевший материал. Нужен свежий цемент, который легко крошится. Прочность блоков и плит зависит от качества связующего;
- специальные добавки, снижающие влагопоглощение и предотвращающие развитие микроорганизмов. Технология предусматривает возможность использования гашеной извести, хлористого кальция, жидкого стекла и глинозема.
Требуемая пластичность арболитной смеси обеспечивается введением воды, абсорбированной наполнителем.
Арболитные блоки своими руками
Для приготовления кубометра арболита вам потребуется:
- чипсов в количестве от 200 до 300 кг; Цемент
- , вес которого 250-350 кг;
- минерализующие добавки — 8-12 кг.
Плотность блоков меняется в зависимости от процентного содержания ингредиентов.
Как сделать форму для арболита своими руками
Для заливки раствора необходима форма для арболитов. Сделать своими руками из различных материалов несложно:
- фанера влагостойкая;
- листовой металл;
- доски строганные.
Конструкция формовочной коробки проста. Это разборная тара, у которой нет дна, а есть ручки для переноски.Внутренние размеры формы определяются размерами блоков.
Требования к технологии производства смеси
Самодельные блоки сегодня популярны. Это позволяет снизить затраты. Мастера, которые его изготовят, легко овладеют технологией производства арболита.
Включает в себя следующие шаги:
- Сушка щепы.
- Измельчение дерева до желаемого размера.
- Минерализация стружки замачиванием.
- Взвешивание сырья и загрузка в смеситель.
- Тщательное перемешивание компонентов.
- Разлив приготовленной смеси по формам.
- Уплотнение формованных изделий.
- Защищаем товар в течение недели.
- Извлечение изделий из формовочных ящиков.
Готовый продукт нужно выложить в проветриваемом помещении и просушить в течение трех недель.
Доступная технология и несложная рецептура позволяют изготавливать арболиты своими руками.Использование качественного сырья, соблюдение рецептуры и технологии позволит получить прочный арболит.
Характеристики арболита заслуженно привлекают внимание, если вы хотите построить одно- или двухэтажный дом. Не последний фактор при его выборе — достаточно просто сделать монолитные стены и арболиты своими руками. Комплектация необходимого оборудования зависит от того, где можно купить готовые фишки, или вам придется сделать это самостоятельно.Для полноты картины рассмотрена полная технология производства арболита.
Основной компонент арболит
Арболит на 90% состоит из древесной щепы, поэтому первым делом нужно уделить внимание ее покупке или закупке. Лучше всего, если материалом для него послужат сосновые доски, но ничего не имеет против использования других ГОСТов.
Одним из нюансов производства арболитов является использование дерева, поскольку это натуральный материал, содержащий в своем составе соединения сахара.Если их не нейтрализовать, то впоследствии они вступят в реакцию с остальными компонентами арболита, что как минимум спровоцирует его набухание. Чтобы этого не произошло, доски, а лучше уже готовые чипсы, месяц выдерживают на открытом воздухе.
Более быстрый способ — замачивание щепы в химических растворах, которое проводят в течение 3 дней. Для их приготовления используют сульфат алюминия (сульфат алюминия), хлорид кальция, гашеную известь или жидкое стекло. Эти компоненты имеются в продаже, и их нетрудно найти в сельскохозяйственных магазинах.
Практика показала, что лучшим решением является сульфат алюминия, который, вступив в реакцию с сахарами, твердеет арболит. Не рекомендуется использовать жидкое стекло — оно увеличивает хрупкость готового материала.
Многие рецепты изготовления арболитов своими руками также пропускают этот этап, добавляя нейтрализующие химические вещества непосредственно во время замешивания арболита. В этом случае их пропорции соблюдаются примерно на уровне 3% от общего веса используемого цемента.
Фреза для стружки
Если ведется масштабное строительство, и купить щепу в таком количестве не всегда возможно, то без фрезы для стружки не обойтись. Это устройство измельчает доски в щепы, которые затем полностью готовы к использованию (если древесина выдержана).
Принцип работы устройства очень прост — на вал надевается металлический диск (обычно диаметром 50 см), в котором проделываются проймы (3-4, в зависимости от модели), расположенные друг относительно друга под углом. 120 ° или 90 °.Возле каждого выреза под углом к нему прикреплен нож, который отрезает кусок доски и подает в пройму, после чего попадает в камеру дробления, где доводится до окончательных размеров.
Создание и работа фрезы для стружки хорошо видно на следующем видео:
Несмотря на кажущуюся простоту конструкции, фреза для стружки, сделанная своими руками, есть далеко не у всех, так как для изготовления вала и маховика с ножами нужны токарный и фрезерный станок. Это оборудование для обработки арболитов нужно будет заказывать хотя бы частично со стороны.
Если токарный станок — не неразрешимый вопрос, то как сделать фрезу для стружки показано на следующей схеме.
Приготовление раствора: пропорции
Особых секретов здесь нет — нужно просто смешать все компоненты. Есть только одно ограничение — с момента окончания замеса и до попадания раствора в формовочную емкость должно пройти не более 15 минут.По истечении этого времени начинается химическая реакция цемента.
Основной порядок заполнения емкости смесителя (соотношение компонентов в ведрах на одну замес):
- Щепа разливается. Если он ранее был замочен в растворе, то сушить его не нужно — следующий компонент все равно будет добавлять воду. Количество — 6 ведер.
- В воду добавлен хлорид кальция (или другой компонент). Пропорции — 2-4% от массы цемента, который будет использован для замеса (1 ведро).Визуально это примерно 1-2 полных стакана.
Все перемешивается и выливается в миксер к стружке и миксер запускается. Также берется одно ведро воды.
- Когда щепа равномерно намокнет, пора добавить цемент. Его заливают в миксер, и теперь нужно дождаться, пока все стружки равномерно покроются цементом — все они должны быть соответствующего цвета. Марка используемого цемента — 500.
Формовка арболитов
Когда раствор готов, его переливают в подходящую емкость, и теперь его нужно использовать в течение 15 минут.Для формования и изготовления арболитов своими руками придумано множество способов — в производстве это сборно-разборная опалубка на 6-12 блоков, а в домашних условиях их обычно изготавливают по частям по самодельным трафаретам.
Один из способов изготовления на видео:
Технология изготовления арболита предусматривает два варианта формовки:
- Быстрая зачистка — после первоначального схватывания цемента. По сути, это непрерывный процесс — формирование блока (заливка раствора в форму), прессование (или вибропрессование), зачистка и отправка на сушку.
Вместе с приготовлением раствора даже один человек может сделать 80-100 блоков в сутки. Достоинством метода является скорость изготовления новых арболитов и непрерывный технологический процесс.
- Зачистка через сутки — после прессования блок оставляют в форме на 24 часа, после чего производится только зачистка и сушка. Изготовление арболитов своими руками таким способом может получиться даже быстрее, но только при наличии достаточного количества форм, в которых арболит можно оставить на ночь.Достоинства метода — близкая к идеальной форма блока, который после схватывания бетона не имеет возможности даже малейшего перекоса.
Чем хуже геометрия блоков, тем толще будут цементные швы между ними, образующие мостики холода. Для уменьшения теплопроводности блокам придают зигзагообразную форму, которая ломает такую перемычку, препятствуя прямому оттоку тепла.
Для формования блоков используется специальный станок или трафареты — все это оборудование для арболитов можно изготовить своими руками.
Использование станка
Оба устройства могут использоваться любым из способов, но их машина часто предназначена для быстрого извлечения из формы, чтобы увеличить скорость производства. Их неоспоримое преимущество — прессование блока на вибростоле. Сам процесс формирования прост, а оборудованию могут доверять рабочие с минимальной подготовкой.
Работа полуавтомата на видео:
- Готовую смесь переливают в мерную емкость (1), которую перемещают по направляющим (2), сливая раствор в форму (3).
- Сверху раствора устанавливается крышка (5) пресса (ее высота регулируется пальцами (6) для людей разного роста) и прижимается рычагом (7).
- После нажатия включается вибростол (8). Он работает 20-30 секунд и автоматически отключается (можно использовать простейшее реле времени) — дольше протаранить нельзя, потому что тогда цемент будет стряхиваться на дно блока.
- Рычаг откидывается назад (9), крышка пресса снимается (10) и форма поднимается вверх (11), для чего нажимается педаль.
Готовый арболит можно сдавать на сушку (12). Через 2-3 дня он наберет достаточную прочность для транспортировки.
Для использования метода зачистки через сутки форму делают разборно-съемной, а верхнюю крышку можно зафиксировать в ней защелками или другим удобным способом. После утрамбовки блок вынимается непосредственно из формы и отправляется на отстаивание.
Арболит по трафарету
Используются два основных типа форм — в виде ящика без дна и верха, а также разборные, в виде двух букв «G», которые защелкиваются вокруг дна, образуя жесткую коробку, покрытую крышкой. с крышкой.Он, в свою очередь, также фиксируется отдельными защелками, которые врезаны в боковые стенки.
Независимо от того, какая форма используется, основной алгоритм следующий:
- Готовится ящик для заливки арболитной смеси. Проход помещается на твердую поверхность (1), покрытую целлофаном (чтобы блок не прилипал), вся коробка смачивается изнутри.
- Заливают первый слой смеси, уплотняют, сверху добавляют второй слой, при необходимости третий и накрывают крышкой.На сквозном ящике (2) лежит гнет (грузик или что-то подходящее), в складной верхней части фиксируется защелками (3).
- Если у вас под рукой есть перфоратор, вы можете провести им по крышке, он заменит вибростол.
- В зависимости от используемой технологии опалубка снимается или форма остается стоять.
Если быстро снять проходную коробку, то сначала она поднимается вверх (4), затем снимается изгиб и снимается крышка. Блок отправляется на сушку вместе с основанием, на котором он был сформирован.
Кратко о главном
Производство качественного арболита в домашних условиях — задача не из обычных. Найти стружколом может быть единственной серьезной трудностью. В крайнем случае его можно изготовить или заказать, но если есть где купить готовые фишки, то эта проблема снимается.
Используемые чипсы необходимо выдержать около месяца на солнце, чтобы нейтрализовать органические вещества внутри. Для раствора можно использовать влажный.
Есть два основных способа снятия опалубки из готовых блоков.Чтобы выбрать подходящий, есть смысл сделать пробные блоки и сравнить результаты.
Использование арболита в строительстве довольно распространено. Часто для возведения стен используются арболиты ручной работы. При ответственном подходе к производству крафтовый арболит полностью отвечает всем требованиям стандартов качества строительных материалов.
Состав любого многокомпонентного строительного материала подбирается таким образом, чтобы добиться максимальной производительности при наименьших экономических затратах.Компонентный состав арболитов позволяет добиться достаточно высокой прочности, огнеупорности и срока службы. В общем, его можно разделить на органический наполнитель, воду, связующее и химические добавки для достижения максимальной производительности.
Состав арболита
- Органический наполнитель
Чаще всего используется в побочных продуктах деревообрабатывающих предприятий (щепа) или сельскохозяйственных предприятий (льняные пожары).
- Древесная щепа является наиболее часто используемым наполнителем.К этому компоненту применяется ряд требований. Размеры фишек не должны превышать 15 сантиметров в длину и 2 сантиметра в ширину. Чипсы не должны содержать листьев, коры и других примесей. Предпочтение отдается хвойным деревьям, лиственные используются крайне редко. Добавленную стружку можно смешивать с опилками или стружкой в соотношении один к одному.
- Костры из льна — тоже довольно распространенный вид органического наполнителя для арболита. Форма, которую они приобретают при сельскохозяйственной переработке льна, не требует дополнительного измельчения и сразу может применяться при производстве арболита.Наивысшего качества блоки достигаются, когда огонь составляет около 20 сантиметров в длину и около 5 сантиметров в ширину.
- Химические добавки
Дитерпеновые кислоты и сахара являются неотъемлемым компонентом органических наполнителей. Они препятствуют слипанию частей наполнителя со связующим. Чтобы этого не произошло, при изготовлении арболита необходимо добавлять изолирующие наполнители, например, щелочной раствор силикатов натрия (жидкое стекло).Для усиления эффекта эту добавку можно комбинировать с хлоридом кальция или сульфидом алюминия. Помимо изолирующих частей наполнителя, эти добавки обычно повышают стойкость блоков к разложению, улучшают влагоизолирующие свойства и, соответственно, продлевают срок службы материала.
Добавление хлорида кальция вместе с нитритом и нитратом этого щелочноземельного металла сокращает время затвердевания блоков.
- Вяжущий компонент
В качестве вяжущего для наполнителя используется обыкновенный портландцемент четырехсотого или пятисотого сорта.
Подойдет обычная техническая вода.
Получение древесной щепы для арболитов
Среди органических наполнителей наибольшим спросом пользуется щепа. Лен костров содержит гораздо больше веществ, снижающих характеристики арболита, поэтому при их использовании требуется больше химических добавок. И хотя процесс разведения костра намного проще, изготовление чипсов — более актуальный вопрос.
Есть специальные машины для производства щепы.В быту их называют древесной стружкой. Существует множество модификаций этих агрегатов, различающихся своими характеристиками. Как правило, щепа с необходимыми данными для изготовления качественной щепы стоит от 200 до 300 тысяч рублей. Кроме того, после получения щепы ее необходимо рассортировать (избавиться от остатков коры и зелени), а также для этого требуется специальное оборудование.
Если не планируется создавать малый бизнес по производству и продаже арболитов, а ставится цель построить один дом, то, скорее всего, будет выгоднее покупать готовую щепу.Еще один аргумент в пользу этого решения — четырехмесячная сушка свежеприготовленных чипсов, о которой говорилось выше.
К счастью, щепы купить нет ничего сложного. С целью уменьшения количества отходов производства на многих деревообрабатывающих предприятиях запускаются побочные линии по производству щепы для арболитов.
Технология производства самодельного арболита
Важным условием создания качественных строительных материалов в домашних условиях является неукоснительное соблюдение всех технологических требований.Поэтому перед запуском производства следует внимательно изучить все связанные с ним аспекты.
Пропорции компонентов
Условия не предъявляют жестких требований к пропорциям смеси для производства арболитов в домашних условиях. Примерное соотношение компонентов следующее: органический наполнитель — 28,5%, связующее — 28,5% и вода вместе с химическими добавками — 43%. Это соотношение будет меняться при получении арболита разных марок.
Для наиболее популярных из них это выглядит так:
- Сорт 15: цемент — 250-280 килограммов, органический наполнитель — 240-300 килограммов, химические добавки — 12 килограммов, вода — 350-400 литров.
- Марка 25: цемент — 300-330 кг, органический наполнитель — 240-300 кг, химические добавки — 12 кг, вода 350-400 литров.
Дана масса компонентов, необходимая для создания одного кубометра арболита.
Виды и размеры арболитов
Стоит отметить, что при самостоятельном производстве арболитов их тип и размер определяет исключительно сам производитель. Все зависит от потребностей и фантазии того, кто занялся этим делом.
Однако можно выделить и габариты блоков, которые чаще всего используются в строительстве. Среди них три модели блоков для возведения несущих стен:
- Высота — 20 сантиметров, ширина — 30 сантиметров, длина — 50 сантиметров.
- Высота — 25 сантиметров, ширина — 30 сантиметров, длина — 50 сантиметров.
- Высота — 20 сантиметров, ширина — 40 сантиметров, длина — 50 сантиметров.
Также существуют две основные модели возведения перегородок:
- Высота — 20 сантиметров, ширина — 20 сантиметров, длина — 50 сантиметров.
- Высота — 25 сантиметров, ширина — 20 сантиметров, длина — 50 сантиметров.
На выбор конкретного размера блока для несущей стены часто влияют климатические условия региона, в котором предполагается строительство. Как нетрудно догадаться, самые большие по ширине блоки чаще всего встречаются в северных регионах. Соответственно, самые тонкие — у южных.
Кроме того, есть блоки различной формы. Так для перемычек над дверями, окнами или для укладки армированного ремня изготавливают различные блоки П-образной формы.В том, чтобы делать их дома, тоже нет ничего сверхъестественного.
Способы прессования блоков
Наиболее простым в техническом плане и в то же время наиболее трудоемким является способ прессования арболитов своими руками, без использования специального оборудования. Потребуется форма, в которую будет укладываться арболит, доска или другая доска, соответствующая размеру формы, и какой-нибудь тяжелый предмет с плоским основанием.
После заполнения формы в нее помещается доска, по которой в разных частях производятся нарезки для равномерного уплотнения.Стоит отметить, что смесь следует заливать в форму слоями, в несколько этапов. Каждый слой проходит промежуточное прессование. Для большей эффективности в доске необходимо просверлить отверстия для выхода воздуха, с помощью которых происходит трамбовка. Этот метод наиболее примитивен, и получаемые с его помощью блоки — самого низкого качества.
Домашнее производство может быть и более качественным, но в этом случае потребуется дорогое оборудование. Существуют специальные вибрационные станки непосредственно для прессования арболитов.Они уже оснащены формами для заливки смеси. Вам просто нужно заполнить эти формы и включить машину. При прочих равных, блоки, изготовленные на таком станке, будут на порядок превосходить по качеству штампованные вручную.
Промежуточным вариантом является использование компактных ручных вибрационных машин. Для их использования также понадобится форма и планка, но качество отжима будет намного выше, чем при ручном нарезании резьбы.
Оптимальные условия для изготовления блоков
Технологический процесс производства арболитов не отличается предъявлением завышенных требований к условиям окружающей среды. Критично соблюдение двух параметров: температура воздуха в процессе сушки блоков должна быть не менее 12 градусов, а хранение сырцовых блоков должно осуществляться в закрытом помещении, защищенном от атмосферных осадков. В противном случае смесь будет очень медленно обезвоживаться.
Для высыхания блоков до состояния, пригодного для использования, требуется около 20 дней. Не рекомендуется начинать кладку раньше, это может привести к деформации блоков под действием давления верхних рядов кладки.
При использовании исключительно ручного метода изготовления арболитов, когда скорость процесса крайне низкая, необходимо начинать изготовление задолго до начала строительства. Еще больше затягивается производственный процесс в случае самостоятельного производства щепы. Это связано с тем, что с момента поступления до момента использования в составе арболита она должна сохнуть не менее четырех месяцев. В противном случае концентрация дитерпеновой кислоты и сахаров в наполнителе будет слишком высокой, и даже добавление добавок не гарантирует надежного сцепления его частиц со связующим.

Раствор для кладки арболитов
Существует несколько вариантов растворов для кладки блоков, не все они подходят при возведении стен из арболита. Ниже приведены примеры решений с обоснованием их пригодности для кладки арболитов:
- Смесь цемента и песка. Хотя этот раствор широко применяется в строительстве, он наименее оптимален для кладки арболитов. При затвердевании эта смесь образует своего рода камень, который имеет очень высокую теплопроводность.Это свойство существенно снизит теплоизоляционные качества стен из арболита, практически лишив их одного из основных преимуществ. Использование такого раствора допустимо только в случае строительства неотапливаемых помещений, например, навесов.
- Раствор песчаного перлита. Этот вариант гораздо больше подходит для возведения стен жилых помещений из арболитов, чем предыдущий. Обладает низкой теплопроводностью, за что и получил название «теплый» раствор.Правда, работать с ним несколько сложнее. При его изготовлении нужно учитывать, что перлит очень легкий и улетает от малейшего порыва ветра.
Это связано с чрезвычайно маленьким размером его частиц. Благодаря этому свойству перлита раствор с его использованием проникает во все полости блоков и обеспечивает их высокопрочное сцепление.
- Клей специализированный. Идеальным вариантом будет использование клея для газобетона. Он специально разработан для укладки блоков из легких пористых материалов.Обладает высокой адгезией, что позволяет делать максимально тонкие швы между блоками. В сочетании с низкой теплопроводностью это качество обеспечивает практически полное отсутствие потерь тепла через швы кладки.
В связи с ростом популярности этого стройматериала все большую актуальность приобретает вопрос: как сделать арболиты своими руками? На основании приведенных данных можно сделать вывод, что при соблюдении всех рекомендаций и технологий производства сделать качественные арболиты вполне возможно.Вопрос только в актуальности их изготовления, ведь этот процесс требует много времени и сил. В некоторых случаях наиболее логичным решением будет покупка готового стройматериала.
Оптимизация процесса виброуплотнения древесно-бетонных блоков
ADEME (2013) Chiffres clés du bâtiment — Издание 2013. ADEME, Sophia Antipolis
Google Scholar
Amziane S, Sonebi M (2016) Обзор строительных материалов на биологической основе, изготовленных из растительных заполнителей.RILEM Tech Lett 1:31. https://doi.org/10.21809/rilemtechlett.2016.9
Артикул Google Scholar
Trouy-Triboulot MC, Triboulot P (2000) Matériau bois — structure et caractéristiques. Tech Ing 27
Guinard L, Deroubaix G, Roux ML, Levet AL, Quint V (2015) Evaluation du gicing de déchets bois et son positionnement dans la filière bois / bois ennergie. АДЕМЕ, Анже
Google Scholar
CRPF (2006) Schéma Régional de Gestion Sylvicole. Centre Régional de la Propriété Forestière — Nord Pas-de-Calais Picardie, Амьен
Google Scholar

Ling T-C (2012) Влияние метода уплотнения и содержания резины на свойства бетонных блоков для мощения. Строительный материал 28: 164–175. https://doi.org/10.1016/j.conbuildmat.2011.08.069
Артикул Google Scholar
Торкаман Дж., Ашори А., Садр Момтази А. (2014) Использование отходов древесного волокна, золы рисовой шелухи и отходов известнякового порошка в качестве материалов, заменяющих цемент для легких бетонных блоков. Строительный материал 50: 432–436. https://doi.org/10.1016/j.conbuildmat.2013.09.044
Артикул Google Scholar
Джелал К., Пейдж Дж, Када Х, Ванхове Й. (2020) Технико-экономическое обоснование использования тополевых отходов в качестве песка в цементных растворах. J Mater Cycles Waste Manag 22: 488–500.https://doi.org/10.1007/s10163-019-00946-x
Артикул Google Scholar
Ашори А., Табарса Т., Амоси Ф. (2012) Оценка использования деревянных шпал для железных дорог в древесно-цементных композитных материалах. Материал сборки 27: 126–129. https://doi.org/10.1016/j.conbuildmat.2011.08.016
Артикул Google Scholar
Мохаммед Б.С., Абдуллахи М., Хунг С.К. (2014) Статистические модели для бетона, содержащего древесную стружку, как частичную замену мелкозернистому заполнителю.Строительный материал 55: 13–19. https://doi.org/10.1016/j.conbuildmat.2014.01.021
Артикул Google Scholar
Семпл К.Э., Каннингем Р.Б., Эванс П.Д. (2007) Производство древесно-цементных композитов из марганцевой акации: исследование механических свойств соединений, улучшающих совместимость сердцевины марганцевой древесины акации с портландцементом. Wood Fiber Sci 36: 250–259
Google Scholar
Бедерина М., Марморет Л., Мезреб К., Хенфер М.М., Бали А., Квенудек М. (2007) Влияние добавления древесной стружки на теплопроводность песчаных бетонов: экспериментальное исследование и моделирование. Строительный материал 21: 662–668. https://doi.org/10.1016/j.conbuildmat.2005.12.008
Артикул Google Scholar
Домингес-Сантос Д., Мора-Мелиа Д., Пинчера-Орельяна Г., Баллестерос-Перес П., Ретамаль-Браво С. (2019) Механические свойства и сейсмические характеристики древесно-бетонных композитных блоков для строительства.Материалы 12: 1500. https://doi.org/10.3390/ma120
Артикул Google Scholar
Хошроо М., Ширзади Джавид А.А., Шальчиян М., Ник Ф. (2019) Оценка механических свойств и свойств прочности бетона, содержащего природный пуццолан Chekneh и древесную стружку. Иран J Sci Technol Trans Civ Eng. https://doi.org/10.1007/s40996-019-00305-8
He T, Xu R, Da Y, Yang R, Chen C, Liu Y (2019) Экспериментальное исследование высокоэффективного газобетона в автоклаве, произведенного из переработанного древесного волокна и резинового порошка.J Clean Prod 234: 559–567. https://doi.org/10.1016/j.jclepro.2019.06.276
Артикул Google Scholar
Xu R, He T, Da Y, Liu Y, Li J, Chen C (2019) Использование древесного волокна, полученного из древесных отходов, для армирования пенобетона в автоклаве. Строительный материал 208: 242–249. https://doi.org/10.1016/j.conbuildmat.2019.03.030
Артикул Google Scholar
Ndong Engone JG, Vanhove Y, Djelal C, Kada H (2018) Оптимизация экструзии раствора с использованием древесных опилок тополя для кирпичной кладки. Int J Adv Manuf Technol 95: 3769–3780. https://doi.org/10.1007/s00170-017-1323-9
Артикул Google Scholar
Ndong Engone JG, Djelal C, Xing X, Vanhove Y, Kada H (2014) Исследование влияния древесных заполнителей на экструдируемость песчаного раствора. В: Proc. Междунар. Конф. по достижениям в гражданском, строительном и машиностроении.Бирмингем, Великобритания, стр. 150–154
Page J, Khadraoui F, Gomina M, Boutouil M (2019) Влияние различных обработок поверхности на водопоглощающую способность льняных волокон: реология свежих армированных строительных смесей и механические свойства. свойства в затвердевшем состоянии. Строительный материал 199: 424–434. https://doi.org/10.1016/j.conbuildmat.2018.12.042
Артикул Google Scholar
Пейдж Дж., Амзиане С., Гомина М. (2019) Оптимизация обработки льняным маслом льняных волокон: влияние на свежие свойства армированных волокнами строительных смесей.Acad J Civ Eng 37: 73–79. https://doi.org/10.26168/icbbm2019.10
Артикул Google Scholar
Вэй Ю.М., Гуан Чжоу Ю., Томита Б. (2000) Гидратационные свойства древесно-цементного композита I: оценка влияния пород древесины на совместимость и прочность с обычным портландцементом. J Wood Sci 46: 296–302. https://doi.org/10.1007/BF00766220
Артикул Google Scholar
Wei YM, Tomita B, Hiramatsu Y, Miyatake A, Fujii T., Fujii T., Yoshinaga S (2003) Гидратационные свойства и прочность на сжатие цемента, смешанного с взорванной древесной волокнистой прядью, полученной в процессе взрыва водяного пара. J Wood Sci 49: 317–326. https://doi.org/10.1007/s10086-002-0479-5
Артикул Google Scholar
Frybort S, Mauritz R, Teischinger A, Müller U (2008) Цементно-связанные композиты — механический обзор. Биоресурсы 3: 602–626
Google Scholar
Djelal C, Page J, Vanhove Y, Kada H (2019) Экспериментальное исследование по повышению ценности побочных продуктов тополя в материалах на основе цемента. В: Proceedings of CIGOS 2019. C. Ha-Minh et al., Ханой, Вьетнам, стр. 603–608
Al Rim K, Ledhem A, Douzane O, Dheilly RM, Queneudec M (1999) Influence of доля древесины в термических и механических характеристиках композитов глина-цемент-дерево. Cem Concr Compos 21: 269–276. https://doi.org/10.1016/S0958-9465(99)00008-6
Артикул Google Scholar
Ли М., Хелифа М., Эль Ганауи М. (2017) Механическая характеристика бетона, содержащего древесную стружку в качестве заполнителей. Int J Sustain Built Environ 6: 587–596. https://doi.org/10.1016/j.ijsbe.2017.12.005
Артикул Google Scholar
Бельхадж Б., Бедерина М., Монтреле Н., Уэсу Дж., Кенудек М. (2014) Влияние замены древесной стружки ячменной соломой на физико-механические свойства легкого песчаного бетона.Материал сборки 66: 247–258. https://doi.org/10.1016/j.conbuildmat.2014.05.090
Артикул Google Scholar
Агуа Э., Аллоньон-Хуэсу Э., Аджови Э., Тогбеджи Б. (2013) Теплопроводность композитов из отходов древесины и пенополистирола. Строительный материал 41: 557–562. https://doi.org/10.1016/j.conbuildmat.2012.12.016
Артикул Google Scholar
Кудер К.Г., Шах С.П. (2010) Обработка высокоэффективных композитов на основе цемента, армированных волокном. Строительный материал 24: 181–186. https://doi.org/10.1016/j.conbuildmat.2007.06.018
Артикул Google Scholar
Кудер К.Г., Шах С.П. (2007) Изготовление экструдированного HPFRCC для крепления гвоздями. ACI Mater J 104
Trouy-Triboulot MC, Triboulot P (2012) Matériaux bois —structure et caractéristiques. Техник 36
Сулейман Б.М., Ларфельдт Дж., Лекнер Б., Густавссон М. (1999) Теплопроводность и коэффициент диффузии древесины. Wood Sci Technol 33: 465–473. https://doi.org/10.1007/s002260050130
Артикул Google Scholar
Xing Z, Djelal C, Vanhove Y, Kada H (2015) Древесные отходы в бетонных блоках, полученные методом вибропрессования. Процесс Environ 2: 223–232. https://doi.org/10.1007/s40710-015-0104-4
Артикул Google Scholar
Када-Бенамер Х., Виркин Э., Дютуа Б. (2000) Определение кажущейся энергии активации бетона с помощью изотермической калориметрии. Cem Concr Res 30: 301–305. https://doi.org/10.1016/S0008-8846(99)00250-1
Артикул Google Scholar
Goudjil N, Vanhove Y, Djelal C, Kada H (2012) Электроосмос, применяемый для снятия опалубки с бетона. J Adv Concr Technol 10: 301–312. https://doi.org/10.3151/jact.10.301
Артикул Google Scholar
Hewlett PC (2004) Леа по химии цемента и бетона, 4-е изд. Эльзевир, Баттерворт-Хайнманн
Google Scholar
Wei YM, Tomita B, Hiramatsu Y, Miyatake A, Fujii T (2002) Исследование гидратационных свойств древесно-цементных смесей: совместимость цемента, смешанного с древесным волокном, полученным в процессе пароводяного взрыва. J Wood Sci 48: 365–373. https://doi.org/10.1007/BF00770695
Артикул Google Scholar
Перейра С., Хорхе Ф.К., Феррейра Дж.М.Ф. (2005) Адсорбция катионов из цементной суспензии на лигноцеллюлозных субстратах и ее влияние на схватывание цемента. J Wood Chem Technol 25: 231–244. https://doi.org/10.1080/02773810500366672
Артикул Google Scholar
Sedan D (2007) Этюд физико-химического взаимодействия с интерфейсами волокон шанвера / волокна — влияние на механические свойства композитов. Докторская диссертация, Лиможский университет
Govin A, Peschard A, Guyonnet R (2006) Модификация гидратации цемента в раннем возрасте с помощью натуральной и нагретой древесины. Cem Concr Compos 28: 12–20. https://doi.org/10.1016/j.cemconcomp.2005.09.002
Артикул Google Scholar
Page J, Khadraoui F, Boutouil M, Gomina M (2017) Мультифизические свойства конструкционного бетона, включающего короткие льняные волокна. Строительный материал 140: 344–353. https://doi.org/10.1016/j.conbuildmat.2017.02.124
Артикул Google Scholar
Ajouguim A, Djelal C, Page J, Waqif M, Abdelouahdi K, Saâdi L (2019) Экспериментальное исследование использования альфа-волокон в качестве армирующих материалов вяжущих. Acad J Civ Eng 37: 557–563. https://doi.org/10.26168/icbbm2019.81
Артикул Google Scholar
Tonoli GHD, Joaquim AP, Arsène M-A, Bilba K, Savastano H Jr (2007) Характеристики и долговечность композитов на основе цемента, армированных очищенной сизалевой пульпой.Mater Manuf Process 22: 149–156. https://doi.org/10.1080/10426
- 1062065
Артикул Google Scholar
Page J, Khadraoui F, Boutouil M, Gomina M (2017) Использование альтернативных связующих для разработки армированных льняным волокном строительных растворов. Acad J Civ Eng 35: 188–195. https://doi.org/10.26168/icbbm2017.28
Артикул Google Scholar
Назериан М., Гозали Э., Дахмарде М. (2011) Влияние древесных экстрактивных веществ и добавок на кинетику гидратации цементного теста и цементно-стружечных плит.J Appl Sci 11: 2186–2192. https://doi.org/10.3923/jas.2011.2186.2192
Артикул Google Scholar
Page J, Sonebi M, Amziane S (2017) Дизайн и мультифизические свойства нового гибридного композитного материала из конопли и льна. Материал сборки 139: 502–512. https://doi.org/10.1016/j.conbuildmat.2016.12.037
Артикул Google Scholar
Bouguerra A, Ledhem A, de Barquin F, Dheilly RM, Quéneudec M (1998) Влияние микроструктуры на механические и термические свойства легкого бетона, полученного из глины, цемента и древесных заполнителей.Cem Concr Res 28: 1179–1190. https://doi.org/10.1016/S0008-8846(98)00075-1
Артикул Google Scholar
Wastiels L, Schifferstein HNJ, Heylighen A, Wouters I (2012) Связь материального опыта с техническими параметрами: тематическое исследование визуального и тактильного восприятия тепла стеновыми материалами в помещении. Сборка Environ 49: 359–367. https://doi.org/10.1016/j.buildenv.2011.08.009
Артикул Google Scholar
Amziane S, Collet F (2017) Строительные материалы на основе биоагрегатов: новейший отчет Технического комитета RILEM 236-BBM. Спрингер, Нидерланды
Забронировать Google Scholar
Kada H, Djelal C, Xing Z, Vanhove Y (2016) Etude des propriétés thermomécaniques d’un béton mis en forme par vibrocompactage. В: Actes des IXèmes Journées d’Etudes Techniques. Хаммамет, Тунис
Bouguerra A, Sallée H, de Barquin F, Dheilly RM, Quéneudec M (1999) Свойства изотермической влажности древесно-цементных композитов.Cem Concr Res 29: 339–347. https://doi.org/10.1016/S0008-8846(98)00232-4
Артикул Google Scholar
Taoukil D, El Bouardi A, Sick F, Mimet A, Ezbakhe H, Ajzoul T (2013) Влияние содержания влаги на теплопроводность и коэффициент диффузии древесно-бетонного композита. Строительный материал 48: 104–115. https://doi.org/10.1016/j.conbuildmat.2013.06.067
Артикул Google Scholar
Асади И., Шафиг П., Абу Хассан ЗФБ, Махьюддин Н.Б. (2018) Теплопроводность бетона — обзор. J Build Eng 20: 81–93. https://doi.org/10.1016/j.jobe.2018.07.002
Артикул Google Scholar
Ledhem A, Dheilly RM, Benmalek ML, Quéneudec M (2000) Свойства композитов на древесной основе, составленных из совокупных промышленных отходов. Строительный материал 14: 341–350. https://doi.org/10.1016/S0950-0618(00)00037-4
Артикул Google Scholar
Невилл А.М. (2011) Свойства бетона, 5 изд. Пирсон, Харлоу
Google Scholar
Донди М., Маззанти Ф, Принципи П, Раймондо М., Занарини Дж. (2004) Теплопроводность глиняных кирпичей. J Mater Civ Eng 16: 8–14. https://doi.org/10.1061/(ASCE)0899-1561(2004)16:1(8)
Артикул Google Scholar
Zhang L, Yang L, Jelle BP, Wang Y, Gustavsen A (2018) Гигротермические свойства прессованного земляного кирпича.Строительный материал 162: 576–583. https://doi.org/10.1016/j.conbuildmat.2017.11.163
Артикул Google Scholar
Venuat M (1994) Производство силикатных кальций. Tech Ing 10
Uysal H, Demirboğa R, ahin R, Gül R (2004) Влияние различных дозировок цемента, осадка и соотношения заполнителей пемзы на теплопроводность и плотность бетона. Cem Concr Res 34: 845–848. https://doi.org/10.1016/j.cemconres.2003.09.018
Артикул Google Scholar
Древесный цемент, обладающий высокой прочностью и многофункциональностью
Формирование и трехмерная архитектура из древесного цемента. а) Схематические иллюстрации микромеханизмов образования древесного цемента в процессе замораживания, оттаивания и отверждения. б) Объемные визуализации XRT цемента с ледяной структурой, полученного из цементных растворов со значениями W / C, равными 0.4 и 1.3 для сравнения с древесиной березы Betula schmidtii. Поры в материалах обозначены синим цветом. FD и GD представляют направление замерзания льда и направление роста древесины соответственно. Кредит: Advanced Science, DOI: 10.1002 / advs.202000096.Природа часто вдохновляет на создание биомиметических искусственных материалов. В новом отчете, опубликованном в номере Advanced Science , Фахенг Ван и группа ученых из Китая в области современных материалов, инженерии и науки разработали новые цементные материалы на основе однонаправленной пористой архитектуры, имитирующие конструкции из натурального дерева.Полученный в результате древесный цементный материал показал более высокую прочность при одинаковой плотности, наряду с многофункциональными свойствами для эффективной теплоизоляции, водопроницаемости и легкости регулирования водоотталкивания. Команда одновременно достигла высокой прочности и многофункциональности, что сделало древесный цемент новым многообещающим строительным материалом для создания древесно-имитирующих конструкций с высокими характеристиками. Они представили простую процедуру изготовления для повышения эффективности при массовом производстве с приложениями, подходящими для других систем материалов.
Разработка биоинспирированных древесных материалов
Пористые материалы на основе цемента обладают низкой теплопроводностью для теплоизоляции, высокой звукопоглощающей способностью, отличной проницаемостью для воздуха и воды при сохранении небольшого веса и огнестойкости. Тем не менее, ключевой задачей по-прежнему остается достижение одновременного улучшения как механических, так и многофункциональных свойств, включая механическую поддержку, эффективную транспортировку и хорошую теплоизоляцию.Поэтому крайне желательно создавать материалы с улучшенными механическими и многофункциональными свойствами, чтобы активно реализовывать принципы проектирования натурального дерева. В ходе экспериментов Wang et al. разработан древесный цемент с однонаправленной пористой структурой, сформированной методом двунаправленной обработки замораживанием. Процесс позволил сформировать мосты между составляющими конструкции, а затем команда оттаяла полностью замороженные тела, пока лед постепенно не растаял, а цемент не затвердел.Последующий процесс гидратации произвел новые минералы и гели в цементе, в том числе гидроксид кальция в форме шестиугольника, игольчатый эттрингит и гели силиката-гидрата кальция. Фазы в основном образовывались в цементных пластинах и перерастали в промежутки между ними в процессе оттаивания и отверждения для лучшей структурной целостности с улучшенными межсоединениями ламелей во время образования пористого цемента. Затем с помощью рентгеновской томографии (XRT) команда выявила образование однонаправленных микропор в цементе с ледяной структурой.
Микроструктурные характеристики древесного цемента. а) СЭМ-изображения поперечного сечения цемента с ледяной структурой, полученного из суспензий с W / C 1,3. б – г) СЭМ-изображения взаимосвязей между цементными пластинами. б) Мосты и пересечения, образованные в процессе замораживания, как показано желтыми стрелками, вместе с минеральными продуктами реакций гидратации в) гидроксида кальция и г) эттрингита. д) Схематическое изображение различных типов взаимосвязей и пор в цементе с ледяной структурой.Кружками обозначены элементы A и L для определения прочности с использованием метода эквивалентных элементов. е) Вариации общей пористости Ptotal, открытой пористости Popen и межламеллярной пористости Пинтера в цементе с W / C в исходных цементных растворах. Данные на панели (f) получены по крайней мере из трех измерений для каждого набора образцов и представлены в виде среднего значения ± стандартное отклонение. Кредит: Advanced Science, DOI: 10.1002 / advs.202000096. Понимание микроструктурыWang et al.использовали изображения сканирующей электронной микроскопии (СЭМ), чтобы выявить однонаправленные поры между пластинами в цементе с ледяной структурой, которые охватывают большое количество межсоединений, соединяющих ламели. Команда классифицировала взаимосвязи на три типа: (1) мосты и пересечения, образованные из-за частиц цемента, захваченных кристаллами льда в процессе замерзания, (2) гидроксид кальция шестиугольной формы и (3) игольчатый эттрингит. Последние минералы являются результатом реакций гидратации цемента во время процессов оттаивания и отверждения.Цементные ламели содержали обильные поры, образовавшиеся в процессе сушки цемента из-за обезвоживания гелей и удаления воды. Ученые классифицировали поры древесного цемента на три типа, включая (1) межламеллярные открытые поры, (2) внутриламеллярные открытые поры и (3) внутриламеллярные закрытые поры. Межламеллярная пористость в основном определяется содержанием воды, которая играет роль порообразователя.
- Механические свойства древесного цемента.a, b) Типичные кривые напряжения-деформации сжатия древесно-подобного цемента, изготовленного из суспензий с различным соотношением W / C а) без и б) с добавками SF. c, d) Вариации в c) деформации разрушения, d) плотности поглощения энергии, представленной с использованием площади под кривой зависимости напряжения от напряжения до пикового напряжения, и удельной прочности (вставка на панели (d)) в зависимости от общей пористости. Ptotal. Общие изменяющиеся тенденции обозначены пунктирными кривыми для ясности. д) Зависимость прочности на сжатие от относительной плотности древесного цемента.е) Интерпретация прочности согласно подходу эквивалентных элементов с учетом различных типов пор. Данные на панелях (c) — (f) получены по крайней мере из трех измерений для каждого набора образцов и представлены в виде среднего значения ± стандартное отклонение. Кредит: Advanced Science, DOI: 10.1002 / advs.202000096.
- Многофункциональность древесного цемента. а) Изменения коэффициента теплопроводности древесного цемента в поперечном профиле в зависимости от номинальной плотности.0,4-C указывает на цемент, изготовленный из суспензий с В / Ц 0,4, но без обработки ледяной матрицей. Данные для пористых цементных материалов с произвольными ячейками также показаны для сравнения. [35, 36] б) Инфракрасные изображения цемента, изготовленного из растворов с разными значениями W / C 0,4, 0,9, 1,6 и 2,4, помещенного на нагревательную пластину. 100 ° С. в) Зависимость коэффициента водопроницаемости в вертикальном направлении от общей пористости Ptotal древесного цемента. Установка, используемая для измерения водопроницаемости, показана на вставке.г) Изображения и схематические иллюстрации, показывающие водопроницаемую и отталкивающую природу цемента до и после гидроизоляционной обработки, а также эффекты капиллярного притяжения и отталкивания внутренних поверхностей из-за гидрофильных и гидрофобных характеристик. Данные на панелях (а) и (с) получены по крайней мере из трех измерений для каждого набора образцов и представлены в виде среднего значения ± стандартное отклонение. Общие изменяющиеся тенденции обозначены пунктирными кривыми для ясности.Кредит: Advanced Science, DOI: 10.1002 / advs.202000096.
Механические и многофункциональные свойства материала
Команда получила характерные кривые напряжения-деформации сжатия древесного цемента с добавками паров кремния или без них в его состав.Прочность на сжатие монотонно снижалась с увеличением соотношения вода / цемент в растворах, используемых для разработки материала, что в конечном итоге привело к увеличению пористости цемента. Поскольку деформация разрушения материала увеличивается с увеличением общей пористости, прочность пористого твердого тела может определяться по его пористости. Затем команда измерила коэффициент теплопроводности древесного цемента с ледяной структурой, чтобы показать уменьшение теплопроводности с увеличением пористости материала.Они также использовали инфракрасные (ИК) изображения для четкого наблюдения за прочными теплоизоляционными свойствами цементного материала с ледяной структурой. Для регулирования эффективности теплоизоляции Wang et al. регулировали твердую нагрузку в цементных растворах, увеличивая содержание воды / цемента. Полученный цементный материал впитывает воду из-за гидрофильного (водопривлекательного) характера его внутренних поверхностей. Напротив, они могут предотвратить проникновение воды в поры за счет гидроизоляции поверхностей кремнийорганическим агентом; такие усилия по гидрофобности могут даже заставить материал плавать на воде.Таким образом, этот метод может облегчить переключаемые применения в качестве проницаемых или водонепроницаемых конструкций, подходящих в качестве строительных материалов.
Сравнение древесного цемента с натуральным деревом и другими пористыми цементными материалами. [3-8, 31, 43, 53, 59-61] a) Прочность на сжатие и плотность для широкого диапазона пористых материалов на основе цемента, демонстрирующих относительно более высокую прочность современного древесного цемента при одинаковой плотности. LAC: легкий агрегатный контент; OPC: обычный портландцемент; ПФ: полипропиленовое волокно; ПК: портландцемент; CSA: бетонный осадок; S / C: соотношение песка и цемента по весу.б) Схематические иллюстрации стратегий проектирования натурального дерева и древесного цемента для оптимизации их механических и многофункциональных свойств, связанных с однонаправленными пористыми архитектурами. Данные по прочности и плотности современного древесного цемента на панели (а) представлены в виде среднего значения ± стандартное отклонение. Кредит: Advanced Science, DOI: 10.1002 / advs.202000096.Перспективы древесных цементных материалов
Таким образом, Фахенг Ван и его коллеги представили технику создания ледяных шаблонов как жизнеспособный подход к созданию однонаправленных микропор для применения в керамике, полимерах, металлах и их композитах.Ученые разработали процесс обработки сублимационной сушкой, основанный на самоотвердевающем поведении цемента при контакте с реакциями гидратации. Полученная в результате архитектура из цемента, напоминающая древесину, содержала множество пор в открытой или закрытой форме и множество соединений, соединяющих их ламели. Когда пористость увеличивалась, прочность цемента снижалась. Древесный цемент также отличался более низкой теплопроводностью и хорошей водопроницаемостью. Команда могла изменить цементный материал на водоотталкивающий или водоотталкивающий с помощью гидрофобной или гидрофильной обработки соответственно.Простая и практичная стратегия разработки материалов в сочетании с самозатвердевающей природой его составляющих может значительно улучшить временную и экономическую эффективность метода ледового моделирования для формирования устойчивого бетона с потенциалом для переноса этого метода на другие системы материалов.
Цемент с применением наноинженерии перспективен для герметизации газовых скважин с утечками
Дополнительная информация: Ван Ф.и другие. Цемент под дерево с высокой прочностью и многофункциональностью, Advanced Science , doi: doi.org/10.1002/advs.202000096
Монтейро П. и др. На пути к устойчивому бетону, Nature Materials , doi.org/10.1038/nmat4930
Рой Д. М. Новые прочные цементные материалы: химически связанная керамика, Science , 10.1126 / science.235.4789.651
© 2021 Сеть Science X
Ссылка : Цемент на основе дерева, обладающий высокой прочностью и многофункциональностью (2021 г., 5 января) получено 5 января 2022 г. с https: // физ.org / news / 2021-01-древесный-цемент-высокопрочный-многофункциональный.html
Этот документ защищен авторским правом. За исключением честных сделок с целью частного изучения или исследования, никакие часть может быть воспроизведена без письменного разрешения. Контент предоставляется только в информационных целях.
Бетон, сталь или дерево: поиск конструкционных материалов с нулевым содержанием углерода
Для продвижения своих проектов легких конструкций Бакминстер Фуллер спросил: «Сколько весит ваше здание?» Сегодня, когда архитекторы понимают, что необходимы как структурная, так и углеродная эффективность, возникает вопрос: «Сколько углерода содержит ваше здание?»
Многие архитекторы настаивают на сокращении или устранении воплощенных выбросов углерода, как это уже происходит с производственной энергией.Например, начиная с 2020 года, глобальная архитектурная и инженерная компания HOK планирует провести оценку жизненного цикла конструкций всех своих новых проектов целостного здания и «искать возможности для оптимизации наших спецификаций», — говорит Аника Ландрено, доц. . AIA, директор по устойчивому дизайну.
Действительно, строительная конструкция и подконструкция — хорошие места для охоты, потому что вместе они составляют более половины углеродного следа коммерческого здания. Более того, архитекторы и разработчики должны искать возможности для повторного использования и обновления существующих конструкций, чтобы не тратить впустую энергию, уже израсходованную (и уже выделенный углекислый газ), на их создание.Палитра углеродных интеллектуальных материалов в архитектуре 2030 и калькулятор воплощенного углерода в строительстве, или EC3, инструмент, разработанный Carbon Leadership Forum, C Change Labs и Skanska, — отличные места для изучения влияния выбора материалов как для проектов модернизации, так и для новых строительных проектов. .
Источник: Carbon Leadership Forum. Пример диаграммы Сэнки доступных сокращений на основе текущей цепочки поставок, взятой из калькулятора воплощенного углерода в строительстве. Источник: Carbon Leadership Forum. Вставка для точки данных стальной арматуры в приведенном выше примере диаграммы СанкиПри взвешивании вариантов стали, бетона или дерева необходимо учитывать такие факторы, как местоположение проекта, масштаб, ожидаемый срок службы, потенциал повторного использования и даже сравниваемые показатели материалов (см. «Как измерить воплощенный углерод»).По мере того, как растет осведомленность о воплощенном углероде, отрасли стремятся сделать свою продукцию более привлекательной. Сами по себе архитекторы не могут уменьшить воплощенный углерод в своих проектах, но они, скорее всего, будут прислушиваться к клиенту и могут повлиять на цепочку поставок через свои спецификации. Прежде чем принимать окончательные решения по материалам, воспользуйтесь все более удобными для пользователя инструментами сравнения и вовлеките в диалог строителей и поставщиков — чем раньше, тем лучше.
Мировой сталелитейный сектор имеет огромный углеродный след, на который приходится более 10% глобальных выбросов углекислого газа.«Крупные сталелитейные компании очень хорошо осведомлены о требованиях общества по сокращению выбросов и ищут способы отреагировать на это», — говорит Мэтью Венбан-Смит, исполнительный директор международной некоммерческой организации ResponsibleSteel. базируется в Вуллонгонге, Новый Южный Уэльс, Австралия.
Производство новой стали из железной руды энергоемко. В кислородных печах (кислородных конвертерах), являющихся нормой для большинства развивающихся стран, требуется кокс — очищенная версия угля — для извлечения железа из руды и легирования ее углеродом.Полученный чугун затем очищается до низкоуглеродистой стали, которая содержит около 25% переработанного железа и стального лома. Производители экспериментируют со способами замены угля и кокса не ископаемыми веществами, такими как водород и электролиз на конвертерных фабриках.
Источник: EPD International. Образец шаблона экологической декларации продукции (EPD)По оценкам Американского института стальных конструкций, 98% конструкционной стали из снесенных зданий восстанавливается и перерабатывается в новые стальные изделия.Таким образом, отечественная конструкционная сталь, которая производится на заводах с электродуговыми печами (EAF), может похвастаться содержанием вторичного сырья 93%, согласно утвержденной UL экологической декларации продукции (EPD), составленной AISC в 2016 году. стальную балку, транспортный контейнер или старый холодильник можно продать на металлолом и превратить в стальную балку с широкими полками, которая переходит в новый небоскреб », — говорит советник AISC Люк Джонсон.
Поскольку заводы из ДСП работают на электричестве, они в основном такие же экологически чистые, как и их источники энергии.В сентябре прошлого года сталелитейный завод в Колорадо XIX века, принадлежащий российскому конгломерату Evraz, заключил сделку с местной энергетической компанией о строительстве прилегающей солнечной батареи мощностью 240 мегаватт, которая будет обеспечивать значительную часть энергии комбината. Сталелитейная компания Nucor строит в Миссури завод стоимостью 250 миллионов долларов, который будет полностью работать за счет ветра. Другие похожие проекты находятся в разработке.
ResponsibleSteel недавно опубликовала первую версию своего одноименного стандарта, добровольного международного эталонного теста, разработанного для поддержки «ответственного поиска поставщиков и производства стали» и разработанного в рамках процесса с участием многих заинтересованных сторон с участием производителей, таких как ArcelorMittal, и групп по защите окружающей среды, таких как Могучая Земля.Сертификация основана на стороннем аудите и одобрении независимой комиссии.
Венбан-Смит, который помогал разработать стандарты устойчивого развития в лесном хозяйстве до того, как сосредоточился на стали, хочет сделать сталь одним из самых чистых материалов в мире: «Когда энергетический след для EAF становится нейтральным, мы можем думать о стали в полностью замкнутой экономике. ,» он говорит. Осуществление этой мечты, если возможно, скорее всего, произойдет сначала в развитых странах, где большое количество металлолома доступно для вторичной переработки.
Что спрашивать при указании стали
- Доступна ли сталь на электростанциях с электродуговыми печами и, в частности, на станах, работающих на возобновляемых источниках энергии?
- Можно ли в конструкции использовать скрепленные рамы вместо стойких к моменту рам, чтобы уменьшить требуемую массу стали?
- Можете ли вы закупить сталь, сертифицированную ResponsibleSteel?
Люди ненавидят бетон почти так же сильно, как любят его использовать. Как самый распространенный в мире строительный материал, на него приходится от 6% до 11% глобальных выбросов углекислого газа.Большая часть этих выбросов связана с производством связующего, портландцемента, который составляет в среднем около 10% бетонной смеси по весу. Производство заполнителя — песка и щебня, которые в среднем могут составлять от 70% до 80% смеси — также требует энергии, но в гораздо меньшей степени. Добыча песка может нанести ущерб речным и прибрежным экосистемам.
Почти половина выбросов углекислого газа цемента возникает в результате сжигания ископаемого топлива для нагрева цементных печей до примерно 2500 F. Достижения в области производства чистой энергии могут помочь сократить эти выбросы: прототипы цементных заводов на солнечных батареях в Калифорнии и Франции от Heliogen и Solpart соответственно, успешно нагрели печи до температуры около 1800 F с использованием огромных массивов зеркал.Однако большая часть выбросов углекислого газа происходит в результате химических реакций, присущих производству цемента: в процессе, называемом кальцинированием, известняк распадается на углекислый газ, который уходит в атмосферу, и негашеную известь, составляющую цемента.
Некоторые компании связали углекислый газ в бетон, в том числе компания CarbonCure в Дартмуте, Канада, и Blue Planet в Лос-Гатосе, Калифорния. Эти процессы остаются исключением и на сегодняшний день не полностью компенсируют выбросы углерода при производстве бетона.
Предоставлено Carbon Leadership Forum Скриншот из инструмента EC3 (Embodied Carbon in Construction Calculator) Предоставлено Carbon Leadership Forum Скриншот из инструмента EC3 (Embodied Carbon in Construction Calculator)В настоящее время наиболее простой способ уменьшить углеродный след бетона — это использовать меньше цемента, как показывает палитра углеродных интеллектуальных материалов. Так называемые смешанные цементы используют некальцинированный известняк и другие дополнительные вяжущие материалы (SCM) вместо части клинкера — твердых гранул, полученных в печи, которые измельчаются и смешиваются с другими ингредиентами — при производстве цемента.Включая природные пуццоланы, такие как зола рисовой шелухи, и промышленные побочные продукты, такие как летучая зола, доменный шлак и микрокремнезем, SCM могут улучшить структурные характеристики бетона, а также снизить содержание в нем углерода.
Северная Америка отстает от Европы в использовании цементов с добавками, говорит Джули Баффенбаргер, старший научный сотрудник и директор по вопросам устойчивого развития компании Beton Consulting Engineers из Мендота-Хайтс, штат Миннесота. Спецификации — хороший способ сделать бетонное строительство более эффективным, отмечает она, но слишком строгие предписания могут быть контрпродуктивными.Вместо того, чтобы диктовать пропорции ингредиентов в бетонной смеси, она предлагает проектным группам указать критерии эффективности с точки зрения измеримых пластических и твердосплавных свойств, «чтобы производитель мог предоставить варианты в рамках ограничений». Имейте в виду, что SCM могут увеличивать время, необходимое для достижения требуемых показателей прочности.
Что спрашивать при указании бетона
- Можно ли уменьшить количество цемента в бетонной смеси?
- Можно ли уменьшить общую массу бетона в проекте?
- Какая цементная печь является наименее энергоемкой из имеющихся в наличии?
- Какие методы улавливания углерода агрегатами или смесями могут быть включены?
Инновации в области массового производства древесины, в частности, отечественное производство инженерных изделий, таких как древесина, клееная поперечно, клеем, гвоздями и дюбелями, подогревают надежды на то, что строительство с нулевым выбросом углерода станет возможным в больших масштабах.Согласно отраслевым исследованиям, деревья, срубленные и замененные для производства массивной древесины, могут улавливать больше углерода во время своего роста, чем то, что выбрасывается при производстве, транспортировке и строительстве. Повышенный спрос на древесину из экологически чистых источников может стимулировать лесовозобновление. «Мы должны заново покрыть часть этой планеты лесами», — говорит Ландрено из HOK. «Мы можем повлиять на это, выбрав деревянную конструкцию, где это возможно».
Спроектированные деревянные панели могут заменить стальные настилы и бетонные перекрытия в коммерческих структурах, а клееные колонны могут выдерживать нагрузку на среднеэтажные и высотные конструкции от своих стальных и бетонных аналогов.Эти изделия из дерева также могут быть огнестойкими и быстро монтируемыми. «В тот день, когда они будут установлены и подключены к несущей конструкции, они смогут нести полную проектную нагрузку», — говорит Кеннет Бланд, вице-президент American Wood Council.
Но оправдывает ли массовая древесина заявленную экологическую устойчивость?
По данным Министерства сельского хозяйства США, общий объем деревьев, произрастающих в лесах США, с 1953 года увеличился на 60%. По мере роста спроса на конструкционные изделия из древесины, леса, производящие массовую древесину, должны будут управляться устойчиво, с повторной посадкой деревьев. после сбора урожая.Различия в методах ведения лесного хозяйства приводят к большим различиям в количестве улавливаемого углерода, поэтому важно знать, где и как были произведены ваши лесоматериалы.
Требуются дополнительные исследования выбросов углерода при заготовке, переработке и транспортировке изделий из древесины. Новые средние отраслевые EPD для древесины и изделий из нее ожидаются в первом квартале 2020 года, но заявления конкретных производителей древесины будут еще более полезными. Помимо углерода, заключенного в самой древесине, существуют выбросы от воздействия почвы и леса, а также от производства смол и клеев, связывающих массивные слои древесины.
Наконец, преимущество массового хранения углерода в древесине сохраняется только в том случае, если балки и панели остаются в эксплуатации или не допускаются разложения, в результате чего углерод будет высвобождаться обратно в атмосферу. Чтобы деревянные конструкции были долговечными, они должны быть защищены от проникновения воды, насекомых или грибков, возможно, за счет использования герметиков в сочетании с продуманным дизайном и деталями ограждающей конструкции. Чтобы деревянные элементы можно было использовать повторно, они должны соединяться съемными застежками.
Что спрашивать при указании древесины
- Рекуперируется ли ваша деревянная продукция? Если нет, то происходит ли это из устойчивого лесного хозяйства?
- Можно ли собрать конструкцию с помощью съемных креплений, чтобы можно было повторно использовать элементы?
- Используются ли в проекте эффективные методы обрамления, позволяющие минимизировать требуемую массу древесины?
[Ознакомьтесь с этими советами и инструментами для измерения воплощенного углерода, а также посетите палитру углеродных интеллектуальных материалов.]
Эта статья появилась в выпуске за январь 2020 года под заголовком «Проблема конструкционных материалов».
Проблема углерода
Утилизация золы древесных отходов в технологии строительства: обзор
https: // doi.org / 10.1016 / j.conbuildmat.2019.117654Получить права и контентОсновные моменты
- •
Сообщается о влиянии ВАВ на удобоукладываемость, механические свойства и долговечность бетона.
- •
WWA вместе с RHA и SCBA значительно повысили прочность в бетоне FA.
- •
Выделены подходящие оптимальные процентные доли для использования WWA в цементе и бетоне.
- •
Сообщается о экологических проблемах, связанных с использованием ВАВ в бетоне.
Реферат
Быстрый рост урбанизации и строительства увеличивает спрос на цемент и заполнитель, особенно для производства бетона. Однако производство цемента и бетона увеличивает выбросы углекислого газа, и источник природных заполнителей истощается. Следовательно, для конкретных приложений необходимы альтернативные материалы. Зола из древесных отходов (WWA), материал-заменитель, получается из древесных, целлюлозно-бумажных и других промышленных предприятий, работающих на древесине.Однако производственная отрасль WWA требует больших площадей земли в населенных пунктах. Некоторые древесные отходы разбросаны по земле, в то время как некоторые отрасли промышленности сжигают древесные отходы в мусоросжигательных заводах, что способствует загрязнению воздуха, что является серьезной экологической проблемой. В этой статье представлен всесторонний обзор эффективного использования WWA в качестве материала, заменяющего цемент или заполнители в бетоне. Представлен обзор использования WWA в строительном секторе, и изучаются тенденции развития в соответствии со временем схватывания, прочностью и долговечностью.Между тем, влияние WWA как пуццолановой добавки суммируется для применения в экобетонировании. Результаты показывают, что использование WWA в цементе и бетоне полезно для устойчивого развития и безотходной технологии. Также представлены экологические вопросы использования WWA и способы снижения вредного воздействия на окружающую среду.
Ключевые слова
Заменители цемента
Прочность на сжатие
Долговечность
Воздействие на окружающую среду
Зола древесных отходов
Рекомендуемые статьи Цитирующие статьи (0)
Полный текст© 2019 Elsevier Ltd.Все права защищены.
Рекомендуемые статьи
Ссылки на статьи
Что такое процесс трансформации деревообрабатывающей промышленности?
Сушилки для пиломатериалов — это отрасль, которая превращает деревья в изделия из древесины. На протяжении всего процесса преобразования содержание влаги в древесине (MC) колеблется в зависимости от относительной влажности (RH) и температуры окружающего воздуха.
Процесс трансформации производства древесины:
- Головной станок: основная пила разрезает дерево на распиленные части.
- Кромка: Удаление неровных кромок и дефектов с пиломатериалов.
- Обрезка: Триммер срезает концы пиломатериалов на однородные части в соответствии с рыночными размерами.
- Сортировка необработанных пиломатериалов: Куски разделяются по размеру и конечному продукту: необработанные (так называемые сырые) или сухие.
- Наклейка: пиломатериалы, предназначенные для сухого производства, укладываются прокладками (известными как наклейки), которые позволяют воздуху циркулировать внутри штабеля. (Зеленый продукт пропускает этот этап).
- Сушка: пиломатериалы сушатся в печи для естественного испарения MC.
- Строгание: Выравнивание поверхности каждого куска пиломатериала и выравнивание его ширины и толщины.
- Оценка: процесс оценки характеристик каждой части пиломатериала с целью присвоения ее «оценки» (качества).
Успех производства древесины зависит от способности комбината сохранять качество древесины на протяжении всего производственного процесса. Древесина постоянно теряет или набирает влагу до тех пор, пока ее количество не будет сбалансировано с окружающей средой.Количество влаги в этой точке называется равновесным содержанием влаги (EMC), и оно в основном зависит от относительной влажности и температуры окружающего воздуха. Сушка в печи обычно требует контроля условий ЭМС древесины путем мониторинга и регулирования относительной влажности и температуры в печах. Основная задача мельницы — стабилизировать и поддерживать оптимальные условия сушки древесины в процессе сушки в печи.
Технология MC — жизненно важный компонент современного производства сушки пиломатериалов.Техники следят за системами управления влажностью. Фактически, существует множество производителей электроники, которые производят ряд систем измерения MC для пиломатериалов для крупных производственных операций по сушке пиломатериалов.
Поддерживая и контролируя уровни относительной влажности и температуры в печах, производители пиломатериалов постоянно измеряют и отслеживают изменения MC древесины, чтобы исключить пересушивание или недосушивание древесины. Эти измерения MC могут применяться к целой штабеле древесины в печи или к отдельной единице древесины, прошедшей точечную проверку.С момента ввода бревна в производство и до его отгрузки производители пиломатериалов полагаются на интегрированные системы измерения и управления MC для обеспечения качественного производства каждого куска пиломатериала, производимого комбинатом.
Бесплатная загрузка — Как выбрать правильный промышленный портативный измеритель влажности для вашей фабрики
Процесс сушки пиломатериалов является исходной точкой, требующей, чтобы заводы полагались на надлежащие процедуры управления влажностью древесины. Однако многие потребители и строители ошибочно полагают, что проблемы с древесиной MC прекращаются, когда древесина отправляется с завода.