Прочность эпоксидки — Литье полимеров
Доброго времени суток всем.
Господа, помогите решить проблему.
Возникла необходимость изготовить несколько деталей, что-то вроде наконечника.
В качестве сырья была выбрана смола ЭД20 и отвердитель Пэпа ввиду доступности, «кухонных» условий работы и полного отсутствия какого-либо оборудования и опыта в литейном деле.
Долго не мудрил — форму сваял из пары крышек от лимонада и кусочка полиэтиленовой трубки. Смешал смолу с отвердителем 1:10. Залил. Отлично получилось. Даже крышки снимать не стал, эстетика особо не важна, а лишняя защита от УФ не помешает.
«Недолго музыка играла», при случайном падении со стола моё изделие ээм.. потеряло целостность.
Повторное изготовление с меньшим кол-вом отвердителя и последующая проверка на прочность особой радости тоже не принесли — легко сломал руками.
Попробовал наполнитель — нашинковал стеклоткани, смешал. Получилось вроде прочнее, но при смешивании состава смола превратилась в «малотекучий» комок, который никак не хотел заливаться в форму через трубку 15мм. Грел, заталкивал карандашом, уделал всю кухню. Итог -воздушные полости в толще детали, и общая нетехнологичнось и «гемморность» процесса.
Подскажите, знатоки, что делаю не так? Ошибся с выбором сырья? Наполнителя? Технологии?
Прочности полипропилена (из которого трубы дома), например, хватило бы, но лить его не имея ни опыта ни оборудования у меня вряд ли выйдет.
Выпилить из фанеры/текстолита — без токарки не обойтись, а её нет.
P.S. Задавал тот же вопрос на другом ресурсе. Прошу прощения заранее, если это является признаком дурного тона.
Правила нанесения стеклоленты и стеклоткани
Эпоксидная смола — прекрасный клей. Его основные преимущества – высокая прочность и отсутствие усадки при затвердении. Смолой можно не только склеивать твердые детали и использовать в качестве защитного покрытия. Из смолы создаются стеклопластиковые изделия, даже такие большие, как катера и яхты. Для их производства эпоксидную смолу обязательно армируют. Лучшие материалы для армирования: стеклоткань и стеклолента. В этом обзоре будут рассмотрены основные технологии создания различных форм с использованием стеклопластика. В том числе, нанесение стеклоткани «сухим» и «влажным» методом. Стеклоткань всегда наносят на твердую выровненную поверхность, накладывая нескольким слоями, и комбинируют с различными материалами.
- При «сухом» нанесении ткань заматывают на сухую поверхность, потом пропитывают эпоксидной смолой.
- При «влажном» — покрывают смолой, а потом накладывают стеклоткань.
Метод «сухого» нанесения
- Поверхность очищают и обезжиривают.
- Ткань прикладывают, обрезают с запасом на 30-35 мм в обе стороны. Можно укладывать материал внахлест, если заготовка больше ширины ленты. На вертикальных поверхностях, используют скобы, скрепки или скотч для временной фиксации.
- Далее готовят смолу. Обычно ее смешивают в пропорции 10:1 с отвердителем. Хотя сейчас в продаже есть тюбики со смолой и отвердителем, в пропорции 1:1. На горизонтальной поверхности, эпоксидку наливают в центр ткани. Вертикальную плоскость, пропитывают кистью или валиком. С помощью пластикового скребка смолу равномерно распределяют на сухие участки. Пропитанная ткань становится прозрачной. Если поверхность основания пористая, смола пропитает и ее. Состав наносят, параллельно разравнивая складки стеклоткани, избегая появления пузырьков в смоле. Готовый к затвердеванию материал — это прозрачная стеклоткань с едва заметной фактурой, на ней не должно быть глянцевых пятен от не впитавшейся смолы. При необходимости, следующие слои стеклоленты накладывают незамедлительно. Через пару часов, когда смола перестанет липнуть, можно обрезать выступающую ткань острыми ножницами, после чего их тщательно очищают.
Метод «влажного» нанесения
- Поверхность так же очищают и обезжиривают.
- Отрезают ткань нужного размера. Она хрупкая, поэтому разворачивают рулон осторожно, чтобы иметь возможность завернуть материал назад.
- Слой эпоксидной смолы намазывают на поверхность и накладывают сверху стеклоткань. Для потолочного или вертикального монтажа, необходимо подождать, чтобы смола немного загустела.
- Разглаживают все неровности ткани от центра к краям. Если нужно вырезать складку, делают надрез ножницами и на небольшой промежуток времени прикладывают края друг к другу.
- Белые сухие участки ткани промазывают смолой.
- Излишки собирают с помощью скребка.
- Поверх первого слоя можно по этой же технологии наложить еще несколько.
- Лишнюю ткань обрезают.
- Выравнивание поверхности.
Оставшиеся неровности на поверхности выравнивают с помощью эпоксидной шпаклевки, которая состоит из смолы с наполнителем в виде кварцевой муки или других сыпучих компонентов. Особенно важно, это для изделий, которые предстоит покрасить (на глянцевой поверхности неровности более заметны). Застывшую шпатлевку рекомендуется еще раз покрыть чистой эпоксидкой.
Удаление излишков ткани
Поверх перехлеста кладут металлическую полосу и прорезают ткань острым ножом. Не следует прорезать нижестоящие слои, т.к. это ухудшит прочность изделия. Обрезки перехлеста убирают, пропитывают края еще раз, поверхность разглаживают.
Соединение стеклоткани встык создает гладкую поверхность, в то время, как перехлест увеличивает прочность конструкции. Для перехлестов идеально подходит стеклолента с зауженными кромками.
Для описанных работ прекрасно подойдет стеклолента ЛЭС (электроизоляционная стеклотканевая) и стеклолента ЛЭСБ (электроизоляционная стеклотканевая бандажная). Они производятся из стеклянных крученых нитей. Края ЛЭСБ обработаны для предотвращения расползания. Если эпоксидная смола приобретается просто в качестве клея, стоит купить и стеклоленту, чтобы расширить круг применения столь универсального состава.
Смотрите также:
Силикон для форм, который еще называют компаундом или силиконовой резиной, изготавливается из двух компонентов. Одним из них является основа, оловянная или платиновая, а вторым
Читать далееЭпоксидная смола — прекрасный клей. Его основные преимущества – высокая прочность и отсутствие усадки при затвердении. Смолой можно не только склеивать твердые детали и использовать в качестве защитного покрытия. Из смолы создаются стеклопластиковые изделия, даже такие большие, как катера и яхты.
Читать далееpolymax10.ru
Наполнитель для эпоксидной смолы своими руками
Эпоксидная смола – это универсальный материал, который используется для изготовления интересных поделок, ремонта помещений, судостроения. Обычно вещество продается в комплекте со специальным отвердителем. Объем пузырька небольшой, поэтому домашние мастера изобретают специальные наполнители для эпоксидной смолы, сделанные своими руками. Они позволяют изменить внешний вид готового изделия, сделать его непохожим на другие.
Для чего нужна эпоксидка
Синтетический олигомер был изобретен еще в 20-м веке, но до сих пор народные умельцы придумывают новые сферы его применения. Он прекрасно подходит как для выполнения красивых поделок, так и для шпатлевания различных поверхностей. Материал никогда не применяют в чистом виде. Для полимеризации необходимо смешать основной компонент с затвердителем.
Наполнитель эпоксидной смолы — что это такое?
Это специальная добавка, позволяющая увеличить объем вещества, изменить его вид и структуру. К этой группе также относят красители природного и синтетического происхождения. В строительных магазинах продаются готовые составы. Однако можно изготовить любые наполнители эпоксидной смолы своими руками.
Разновидности
Самое распространенное применение этого материала — заполнение различных пустот, замазывание щелей и стыков. Для этой цели эпоксидный клей не подойдет, поэтому смола, смешанная с наполнителем, будет идеальным решением. Следует выбирать вещество для наполнения тщательно. Оно должно быть однородным и не утяжелять состав. Существует несколько видов наполнителей для эпоксидной смолы. Условно их подразделяют на натуральные и искусственные (синтетические). Все они имеют преимущества и недостатки.
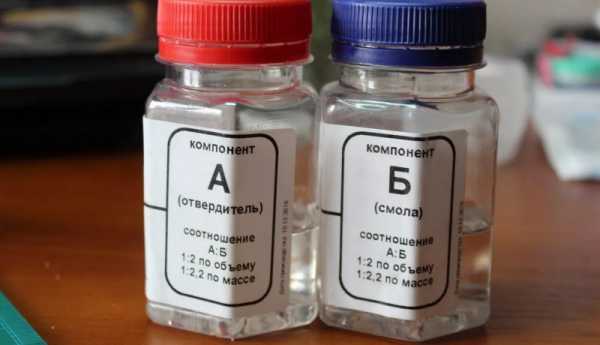
Аэросил
Добавка нужна для предотвращения подтеков. Она необходима при использовании материала на вертикальных поверхностях. Смесь имеет сметанообразную консистенцию, после затвердевания приобретает повышенную плотность, поэтому аэросил используют в качестве наполнителя для эпоксидной смолы для прочности. Хорошо добавка сочетается с другими компонентами.
Микросфера
Вещество представляет собой мельчайшие шарики, которые наполнены газом. Они выглядят как мелкозернистый порошок. Наполнитель для эпоксидной смолы микросферу отличает низкая плотность и небольшой вес. При смешивании со смолой появляется вязкость, необходимая для обработки наклонных плоскостей, угловых стыков и швов. Получается большое количество прочной смеси с пенистой структурой. Прекрасно поддается шлифовке после отвердения. К недостаткам компонента относится понижение прочности клеевого шва.
Графитовый порошок
Может использоваться как для окрашивания вещества, так и для создания идеально ровной и гладкой структуры на поверхности. Черный мелкозернистый порошок используется в автомобилестроении и добавляется к специальному покрытию, которым обрабатывают днище машины. Это позволяет повысить ударопрочность деталей. Минусы покрытия — увеличение хрупкости материала при попадании солнечных лучей и повышение электропроводности в соленой воде.
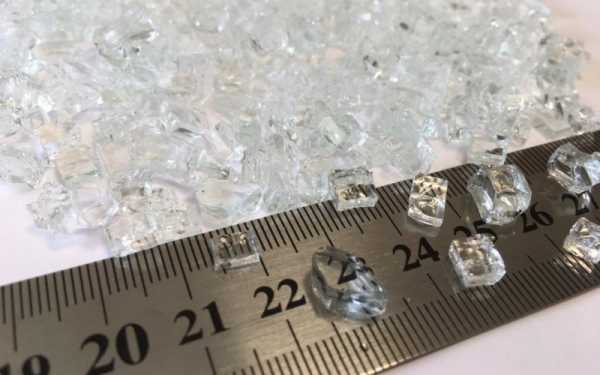
Тальк
Простая детская присыпка, купленная в магазине промтоваров или аптеке, прекрасно справляется с функцией наполнителя для эпоксидной смолы. По своим свойствам тальк схож с аэросилом, но имеет более тонкую мелкую структуру. Благодаря этому можно получить ровную и довольно прочную поверхность. Минусом добавки является то, что она способна поглощать влагу. Это приводит к деформированию поверхности, если на нее попадет вода.
Алюминиевая пудра
Помогает придать составу приятный серебристо-серый цвет, поэтому этот компонент часто используется в качестве декоративной отделки. Если добавить немного больше вещества, сделав консистенцию гуще, — прочность материала после застывания значительно увеличится.
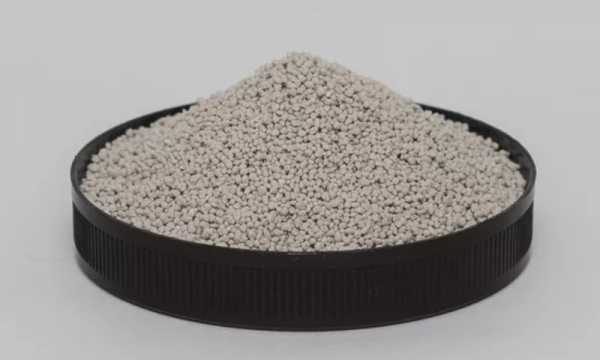
Двуокись титана
Этот компонент, как и алюминиевая пудра, может служить не только добавкой для увеличения объема, но и веществом для пигментации. При смешении получится наполнитель для эпоксидной смолы белый. Если поверхность, на которую планируется нанести состав, будет подвергаться воздействию прямых солнечных лучей, следует обработать ее дополнительно.
Натуральные добавки
Отличие натуральных наполнителей для эпоксидной смолы в том, что они имеют природное происхождение. Самыми распространенными компонентами для смешивания являются:
- Древесная мука. Она используется для того, чтобы повысить густоту шпатлевки, придать составу натуральную структуру и цвет, схожий с деревом. Недостаток смеси — потеря однородности. С таким материалом намного сложнее работать, она труднее ложится на ровную поверхность.
- Волокно. Этот компонент бывает как натуральным, так и искусственным. Обычно используется хлопчатобумажное, льняное, стеклянное, целлюлозное волокно. Оно сначала мелко измельчается путем перемалывания. Вещество значительно повышает связывающие и склеивающие свойства. Добавка хорошо справляется с пропиткой, заполнением зазоров.
- Мелкие древесные опилки или сухая листва. Этот доступный материал можно найти где угодно. Однако нужно учитывать, что перед смешиванием с эпоксидкой материал следует измельчить, иначе структура шпатлевки получится грубой.
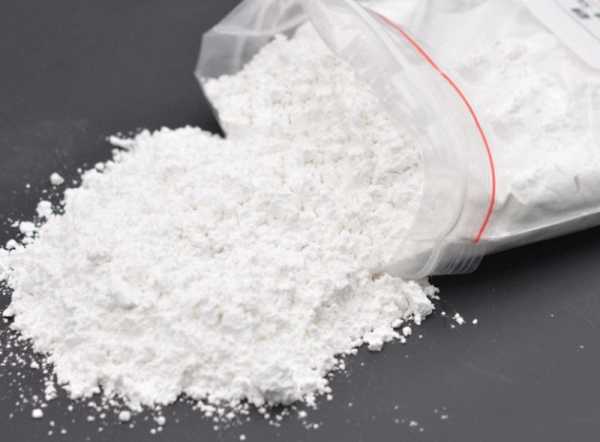
Наполнители своими руками
Для приготовления шпатлевки не обязательно приобретать специальные добавки. Всегда можно изготовить наполнитель для эпоксидной смолы своими руками из подручных материалов. Многие мастера с помощью домашних опытов добились интересных результатов, используя:
- Цемент. Хорошо справляется с обязанностями добавки. После того как эпоксидная смола полностью застынет, поверхность станет очень прочной, хотя нужно строго соблюдать пропорции и добавлять сухое вещество не больше 2 частей на 1 часть эпоксидки, иначе покрытие получится очень хрупким и может растрескаться.
- Зубной порошок. Так же как и мел, эта добавка слишком гигроскопична. Из-за способности поглощать влагу состав не может прослужить долго, поэтому можно использовать этот наполнитель только в местах, где не слишком большая влажность.
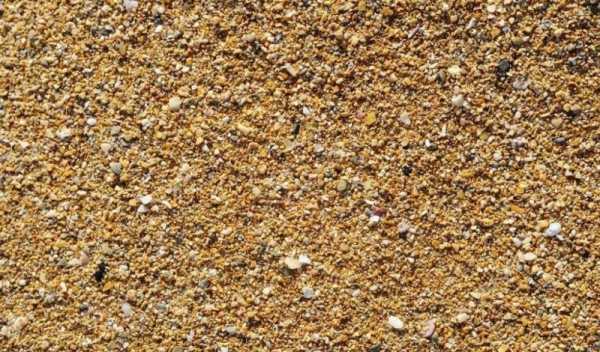
- Алебастр или гипс. Эти вещества делают состав намного прочнее. После добавления тягучесть смолы уменьшается, и можно намазывать ее на любую поверхность. Из-за сильного утяжеления таким материалом сложно работать на горизонтальной поверхности, которая направлена вниз.
- Муку. В крайнем случае, когда нет других добавок, можно использовать самую простую муку, которая найдется на любой кухне. Материал хорошо поддается обработке после затвердевания. Однако тогда время застывания эпоксидки увеличивается в несколько раз.
- Песок. Этот наполнитель для эпоксидной смолы для облегчения не подойдет. Его используют крайне редко. Перед началом работы нужно тщательно просеять песок через мелкое сито. После того как состав затвердеет, поверхность будет иметь слегка шероховатую структуру. Можно использовать такую шпатлевку для декорирования на открытом воздухе. Она хорошо выдерживает солнечные лучи и не подвержена воздействию влаги.
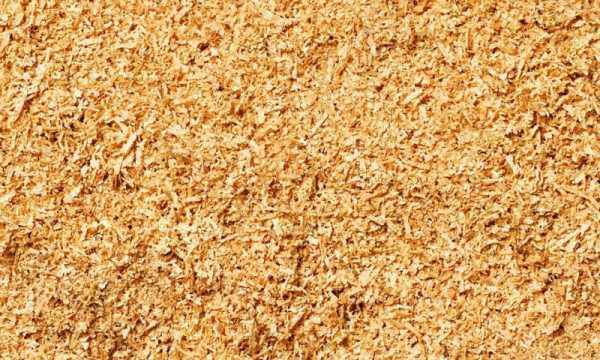
- Стеклоткань. Используется на поверхностях, где необходимо улучшить изоляционные свойства. При работе с этим материалом нужно соблюдать правила безопасности, надевая на лицо респиратор, а на руки перчатки.
Когда нужно добиться декоративного эффекта и окрасить эпоксидную смолу в определенный цвет, можно использовать разные красители:
- чернила от шариковых или гелевых ручек;
- анилиновые красители;
- колеры для нитрокрасок;
- высушенные и измельченные гуашевые краски;
- красители для пасхальных яиц.
Часто в изделия из эпоксидки добавляют блестки, сделанные из конфетти или елочной мишуры. Благодаря этому поделка становится еще более нарядной и красивой.
fb.ru
Способ изготовления армированных волокном изделий на основе эпоксидной смолы
Настоящее изобретение относится к способу изготовления армированных волокном изделий на основе эпоксидной смолы.
Техническим результатом заявленного изобретения является разработка способа изготовления по ЛПС-технологии изделий с исключительно высокой ударной вязкостью и при этом без влияния на другие их механические или термические характеристики.
Технический результат достигается в способе изготовления армированного волокном изделия на основе эпоксидной смолы. При этом предварительно формуют волокнистый материал и помещают его в форму, покрытую разделительным слоем, с последующим ее смыканием, что сопровождается приданием помещенному в нее волокнистому материалу определенной формы. В форму под обычным давлением инжектируют смесь, которая в пересчете на 100 мас. частей содержит (I) эпоксидную смолу в количестве от 50 до 70 мас. частей, (II) ароматический диамин в количестве от 25 до 50 мас. частей и (III) сшиваемые эластомерные частицы на основе полиорганосилоксанов в количестве от 2 до 25 мас. частей. При этом средний диаметр частиц от 1×10
Настоящее изобретение относится к способу изготовления армированных волокном изделий на основе эпоксидной смолы.
Способы подобного типа известны из уровня техники как литьевое прессование смол (ЛПС). Технология изготовления армированных волокном изделий этим методом предусматривает проведение по меньшей мере следующих стадий:
— при необходимости предварительное формование волокнистого материала,
— помещение волокнистого материала в форму, при необходимости покрытую разделительным слоем, с последующим ее смыканием, что сопровождается приданием помещенному в нее волокнистому материалу определенной формы,
— инжекцию смоляной смеси под обычным давлением,
— сшивание смоляной смеси, при необходимости с нагревом формы, и
— извлечение готовой детали из формы.
Подобным методом можно перерабатывать только смоляные смеси с соответствующим набором свойств, которыми, с одной стороны, вообще определяется возможность его проведения (легкая инжектируемость, низкая вязкость), а с другой стороны, возможность изготовления изделий с требуемыми механическими или химическими свойствами. Так, в частности, по такой технологии обычно можно перерабатывать смоляные смеси на основе сложных полиэфиров, виниловых эфиров и эпоксидов. Особое преимущество эпоксидных смол перед сложными полиэфирами и виниловыми эфирами состоит в их малой усадке, что в целом положительно сказывается на механических характеристиках готового изделия.
Однако изделия, изготавливаемые по ЛПС-технологии из традиционных смоляных смесей на основе эпоксидов, в целом обладают, несмотря на легкую инжектируемость таких смоляных смесей, не достаточно высокими показателями ударной вязкости и стойкости к повреждениям при ударной нагрузке, тогда как во многих областях применения требуется, как очевидно, именно наличие высокой ударной вязкости и стойкости к ударной нагрузке.
Один из известных возможных путей повышения ударной вязкости изделий из смол состоит, в частности, в добавлении к смоляным смесям мягких порошковых наполнителей, например резиновой муки с диаметром частиц примерно от 5×10-5 до 1×10-3 м. Однако и подобная мера не позволяет повысить ударную вязкость до необходимого уровня. Более того, твердые частицы, добавляемые к смоляным смесям, перерабатываемым по ЛПС-технологии, не способны проникать сквозь волокнистый материал. В результате этого не удается достичь гомогенной пропитки волокнистого материала смоляной смесью, соответственно гомогенного покрытия отдельных волокон волокнистого материала смоляной смесью, что отрицательно влияет на свойства готового изделия.
Исходя из вышеизложенного, в основу настоящего изобретения была положена задача разработать способ, который позволял бы изготавливать по ЛПС-технологии изделия с исключительно высокой ударной вязкостью и одновременно с этим не влиял бы на другие их механические или термические характеристики.
Указанная задача решается согласно изобретению с помощью способа изготовления армированных волокном изделий на основе эпоксидной смолы, заключающегося в том, что
— при необходимости предварительно формуют волокнистый материал,
— этот волокнистый материал помещают в форму, при необходимости покрытую разделительным слоем, с последующим ее смыканием, что сопровождается приданием помещенному в нее волокнистому материалу определенной формы,
— в форму под обычным давлением инжектируют смесь, которая в пересчете на 100 мас.частей содержит следующие компоненты:
(I) эпоксидную смолу в количестве от 50 до 70 мас.частей,
(II) ароматический диамин в количестве от 25 до 50 мас. частей и
(III) сшиваемые эластомерные частицы на основе полиорганосилоксанов в количестве от 2 до 25 мас. частей со средним диаметром частиц от 1×10-8 до 5×10-6 м и средней молекулярной массой от 1000 до 100000, при этом реакционно-способными группами, способными вступать в химическую реакцию с эпоксидной смолой, модифицирована в основном только поверхность таких эластомерных частиц, а также
(IV) необязательно другие обычные добавки в количестве от 0,05 до 2 мас. частей,
— эту смесь подвергают сшиванию, при необходимости с нагревом формы, и
— готовую деталь извлекают из формы.
При добавлении к смоле эластомерных частиц, имеющих соответствующую крупность, определенную молекулярную массу и модифицированную поверхность, в целом следовало бы ожидать значительного повышения вязкости такой смолы и связанных с этим серьезных проблем технологического характера при ее переработке по ЛПС-технологии. Однако при применении смоляных смесей указанного выше состава подобный негативный эффект, что является неожиданным фактом, не наблюдался. Помимо этого, не было выявлено и описанных выше ожидавшихся проблем со способностью эластомерных частиц проникать сквозь волокнистый материал, которые равномерно и однородно распределялись по объему детали. Извлеченное из формы изделие обладало далее более высокой ударной вязкостью по сравнению с изделиями, изготовленными из обычно используемых при ЛПС смол на основе эпоксидных смол. Кроме того, использование смесей предлагаемого в изобретении состава позволило значительно снизить по сравнению со смесями, не модифицированными соответствующими эластомерными частицами, поглощение воды готовыми изделиями (при их выдержке в воде), что, в свою очередь, свидетельствует о наличии у них повышенной стойкости к гидролизу. Благодаря высокой температуре стеклования (>200°С), достигаемой за счет использования эпоксидных смол, появляется возможность простого изготовления по ЛПС-технологии изделий и для тех областей их применения, в которых к ним предъявляются особо высокие требования (например, в авиационной промышленности).
В качестве эпоксидных смол предпочтительно использовать диглицидиловые эфиры бисфенолов, прежде всего бисфенола А и F, и полученные из них смолы с улучшенным набором свойств, эпоксидированные новолаки, эпоксидированные флуоренонбисфенолы, эпоксидированные о- или n-аминофенолы, а также эпоксидированные продукты полиприсоединения дициклопентадиена и фенола. Эпоксидная эквивалентная масса таких смол обычно составляет от 170 до 450 г. На долю эпоксидной смолы в пересчете на всю массу компонентов смеси приходится от 50 до 70 мас. частей, предпочтительно от 60 до 70 мас. частей. Для применения в составе используемых в предлагаемом в изобретении способе смесей наиболее пригодны многофункциональные эпоксидные смолы благодаря их функциональности и связанной с этим возможности согласования их свойств с особенностями других компонентов смеси или же волокнистого материала. При этом тетрафункциональные эпоксидные смолы благодаря их исключительно высоким механическим свойствам, а также благодаря их высокой формоустойчивости при нагревании зарекомендовали себя как наиболее предпочтительные для применения в составе смесей, используемых в соответствии с изобретением. Среди таких смол особо предпочтительным, в свою очередь, является тетраглицидилдиаминодифенилметан, поскольку изготовленные из него готовые изделия обладают исключительно высокой водостойкостью при повышенной температуре, а также стойкостью к химикатам. Наличие подобных свойств у таких готовых изделий в сочетании с высокой температурой стеклования (>200°С) позволяет использовать их в авиационной и космической промышленности.
Следующим необходимым компонентом смоляной смеси является ароматический диамин в качестве отвердителя, добавляемый к смеси в стехиометрическом соотношении между ним и смолой. В пересчете на одну эпоксидную группу содержание ароматического диамина должно составлять от 80 до 100% от его стехиометрического количества. Сказанное означает, что содержание диамина в смеси составляет от 25 до 50 мас. частей, предпочтительно от 25 до 35 мас. частей, в пересчете на массу всех компонентов смеси. В качестве примера подобного ароматического диамина можно назвать диаминодифенилсульфон и 4,4′-диаминодифенилметан. Предпочтительно далее использовать ароматический диамин, который по меньшей мере в одном орто-положении по отношению по меньшей мере к одной аминогруппе содержит алькильную группу, прежде всего метильную, этильную или изопропильную группу. При соблюдении указанного условия практически полностью исключается канцерогенное действие ароматического диамина. В качестве примера такого ароматического диамина можно назвать 4,4′-метиленбис(2,6-диизопропиланилин). Преимущество, связанное с применением диаминодифенилметана, состоит в возможности его смешения с остальными компонентами смеси (прежде всего с эпоксидной смолой) без опасности возникновения химических реакций в этой смеси уже при комнатной температуре. Использование подобного ароматического диамина позволяет получить пригодную для переработки по ЛПС-технологии однокомпонентную систему, стабильную при хранении при комнатной температуре, связанные с чем преимущества, в свою очередь, состоят в упрощении ее хранения, транспортировки и применении непосредственно на месте ее переработки. Еще одно преимущество, связанное с использованием диаминодифенилметана, состоит в том, что он придает содержащей его смоляной смеси хорошую перерабатываемость, сохраняющуюся в течение нескольких часов при повышенной температуре.
Следующим компонентом смоляной смеси, используемой при осуществлении предлагаемого в изобретении способа, являются сшитые с образованием трехмерной сетчатой структуры эластомерные частицы на основе полиорганосилоксанов типа тех, которые описаны, например, в DE-OS 3634084, при этом содержание таких эластомерных частиц составляет от 2 до 25 мас. частей, предпочтительно от 2 до 5 мас. частей, в пересчете на массу всей смеси. Конкретно используемое количество эластомерных частиц определяется требуемыми свойствами готового изделия и в соответствии с этим может варьироваться в указанных пределах.
Средний диаметр эластомерных частиц составляет от 1×10-8 до 5×10-6 м, предпочтительно от 0,1 до 3 мкм. Средняя молекулярная масса таких эластомерных частиц составляет от 1000 до 100000, предпочтительно от 1200 до 30000. Поверхность эластомерных частиц модифицирована в основном реакционно-способными группами, способными вступать в химическую реакцию с эпоксидной смолой. Так, например, можно использовать те полиорганосилоксаны, которые предпочтительно можно представить общей формулой -(R2SiO)-. При этом в качестве значений R можно назвать остатки, описанные в DE-OS 3634084. Возможно также использовать смеси различных полиорганосилоксанов. Так, в частности, предпочтительно использовать полиорганосилоксаны общей формулы -(R′2SiO)x-(R″2SiO)y— с указанными в DE-OS 3634084 значениями остатков. В целом же предпочтительны полиорганосилоксаны, у которых по меньшей мере 50% остатков R, R′, R″ представляют собой метильные и/или фенильные группы. На поверхности полиорганосилоксанов присутствуют реакционно-способные группы, способные образовывать химическую связь с эпоксидной смолой. Примерами таких реакционно-способных групп, присутствующих на поверхности полиорганосилоксана, служат эпоксидная группа, которая является предпочтительной, или же аминогруппа, карбоксигруппа и/или группа ангидрида карбоновой кислоты. Способ модификации поверхности полиорганосилоксана подобными реакционно-способными группами также описан в DE-OS 3634084.
Другими необязательными добавками, которые при необходимости можно добавлять к смеси, используемой при осуществлении предлагаемого в изобретении способа, являются обычные компоненты, например ускорители реакции, диспергаторы, сшивающие агенты, а также технологические добавки, например деаэраторы. Подобные добавки используют в количестве от 0,05 до 2 мас.частей, предпочтительно от 0,07 до 1 мас. частей, в пересчете на 100 мас. частей всей смеси.
Приготовление смоляных смесей является исключительно простой операцией. Так, в частности, дисперсию, содержащую от 25 до 50 мас. частей (в пересчете на 100 мас. частей всей смеси) одного или нескольких сшиваемых с образованием трехмерной сетчатой структуры полиорганосилоксанов, смешивают с добавляемыми при необходимости к смеси вспомогательными веществами, такими как сшивающие агенты, диспергаторы, катализаторы, а также с эпоксидной смолой и диамином и при необходимости с иными обычными добавками. Подобная смоляная смесь обладает высокой стабильностью при хранении при комнатной температуре. Другие предпочтительные варианты способа получения смоляной смеси описаны в DE-OS 3634084.
В процессе ЛПС в форму помещают практически сухой волокнистый материал (например стеклянное, углеродное или арамидное волокно), имеющий вид ткани, плетеных изделий, формованного волокна, матов из рубленой пряжи или волокнистых холстов. Предпочтительно при этом использовать углеродные и стеклянные волокна. Подобный волокнистый материал сначала подвергают предварительному формованию, которое в простейшем случае состоит в предварительном прессовании обработанного связующим волокнистого материала для придания ему формоустойчивости при хранении. До помещения волокнистого материала в форму ее покрывают антиадгезивами (разделительными слоями). Таким антиадгезивом может служить твердый тефлоновый слой или же любое средство, которым форму соответствующим образом покрывают перед изготовлением в ней каждой детали. После этого форму смыкают и затем в нее под обычным давлением (<6 бар) инжектируют низковязкую смоляную смесь. После заполнения формы достаточным количеством смолы, что определяют по ее уровню в выпоре, инжектирование смолы прекращают. После этого происходит отверждение смолы и сшивание полиорганосилоксановых частиц в форме, которую для интенсификации этих процессов обычно нагревают. Одновременно с этим происходит связывание полиорганосилоксановых частиц с эпоксидной матрицей, обусловленное реакцией реакционно-способных групп полиорганосилоксана с эпоксидной смолой. В результате такой реакции плотность полимерной сетки отвержденной смолы не уменьшается. По завершении процесса отверждения, соответственно сшивания, смолы деталь можно извлечь из формы, для чего при необходимости можно задействовать, например, выталкивающие системы.
Как уже говорилось выше, изготовленные предлагаемым в изобретении способом изделия могут использоваться в авиационной и космической промышленности. Другой возможной областью их применения является, например, автомобилестроение.
Ниже изобретение более подробно рассмотрено на примере одного из вариантов его осуществления.
На прилагаемом к описанию чертеже показана схема процесса литьевого прессования смол (ЛПС), который подразделяется на стадии (1)-(5).
Сначала на не показанной на чертеже стадии помещенный в форму волокнистый материал 2 (мат толщиной 3 мм, состоящий из 8 слоев углеродного волокна; продукт 445 Т фирмы Kramer, объемная доля волокна составляет 52%) подвергают предварительному формованию в форме путем ее смыкания. При определенных условиях можно отказаться от проведения этой стадии. На следующей стадии (1) эту заготовку 2 из волокнистого материала помещают в форму 1, покрытую разделительным слоем. Затем форму 1 смыкают (стадия (2)). После этого на следующей стадии (3) в форму 1 с помощью соответствующего инжекционного устройства 3 под давлением 4 бара подают смоляную смесь 4. При этом компоненты смоляной смеси можно смешивать между собой непосредственно в смесителе, встроенном в инжекционное устройство. Преимущество смоляной смеси, используемой при осуществлении предлагаемого в изобретении способа, состоит в ее стабильности при хранении при комнатной температуре, что позволяет без каких-либо проблем использовать однокомпонентную систему.
Таблица 1 | ||
Состав смоляной смеси | ||
Компонент | Состав смеси (мас.%) согласно уровню техники | Состав смеси (мас.%) согласно изобретению |
эпоксидная смола: тетраглицидилдиаминодифенилметан | 69,4 | 63,6 |
диамин: 4,4′-диаминодифенилметан | 30,6 | 29,2 |
полиорганосилоксан | — | 7,0 |
Компонент | Состав смеси (мас.%) согласно уровню техники | Состав смеси (мас.%) согласно изобретению |
А 530** | — | 0,2 |
Примечание: **продукт фирмы Byk GmbH, Германия. |
Результаты, полученные при исследовании свойств отвержденной (нагрев со скоростью 2°С/мин до 180°С, выдержка в течение 60 мин при 180°С) смоляной смеси (указанного в табл.1 состава), приведены ниже в табл.2.
Таблица 2 | ||
Свойства | Смоляная смесь согласно уровню техники | Смоляная смесь применяемого в изобретении состава |
Температура стеклования [°С] | 217 | 217 |
Температура стеклования [°С], измеренная после выдержки в дистиллированной воде (в течение 14 дней при 70°С) | 215 | 205 |
Прочность на изгиб согласно DIN 53452 ISO 178 [МПа] | 3100 | 3200 |
Водопогощение [%], измеренное после выдержки в дистиллированной воде (в течение 14 дней при 70°С) | 2,5 | 1,7 |
Энергия распространения трещины [Дж/м2] | 160 | 250 |
Из приведенных в табл.2 данных следует, что водопоглощение (выдержка в течение 14 дней при 70°С в дистиллированной воде) у смоляной смеси согласно уровню техники превышает тот же показатель смоляной смеси, используемой в предлагаемом в изобретении способе. Благодаря меньшей влагоемкости используемой в соответствии с изобретением смеси изготовленное из нее готовое изделие обладает соответственно повышенной стойкостью к гидролизу. Из приведенных в табл.2 данных следует далее, что используемая согласно изобретению смоляная смесь обладает более высокими по сравнению с используемой согласно уровню техники смоляной смесью показателями прочности на изгиб и удельной энергии распространения трещины, что свидетельствует об улучшенном поведении отвержденной смеси при разрушении.
После инжектирования смоляных смесей указанных в табл.1 составов в показанную на чертеже форму 1 их подвергают отверждению, нагревая с 30°С до 180°С со скоростью 2°С/мин (стадия (4)). В процессе такого нагрева не удалось выявить каких-либо различий в вязкости между смоляной смесью, используемой согласно уровню техники, и смоляной смесью, используемой в соответствии с изобретением. Окончательному отверждению смолу подвергают ее выдержкой при 180°С в течение 2 ч. После непродолжительной стадии охлаждения деталь извлекают из формы (стадия (5)). Характеристики изготовленного таким путем готового армированного волокном изделия приведены в табл.3.
Таблица 3 | ||
Свойства | Смоляная смесь согласно уровню техники | Смоляная смесь применяемого в изобретении состава |
Температура стеклования [°С] | 216 | 205 |
Прочность на изгиб согласно DIN 53452 ISO 178 [МПа] | ||
при комнатной температуре | 693 | 881 |
при 120°С | 611 | 656 |
Прочность на изгиб при кратковременной нагрузке согласно DAN 432 [МПа] | ||
при -55°С | 69 | 76 |
при комнатной температуре | 58 | 61 |
при 120°С | 38 | 44 |
Приведенные выше значения прочности на изгиб свидетельствует о том, что детали, изготовленные предлагаемым в изобретении ЛПС-способом, способны выдерживать более высокую механическую нагрузку по сравнению с деталями, изготовленными из использовавшихся до настоящего времени смоляных смесей.
1. Способ изготовления армированного волокном изделия на основе эпоксидной смолы, заключающийся в том, что при необходимости предварительно формуют волокнистый материал (2), этот волокнистый материал (2) помещают в форму (1), при необходимости покрытую разделительным слоем, с последующим ее смыканием, что сопровождается приданием помещенному в нее волокнистому материалу (2) определенной формы, в форму под обычным давлением инжектируют смесь (4), которая в пересчете на 100 мас. ч. содержит следующие компоненты: (I) эпоксидную смолу в количестве от 50 до 70 мас. ч., (II) ароматический диамин в количестве от 25 до 50 мас. ч. и (III) сшиваемые эластомерные частицы на основе полиорганосилоксанов в количестве от 2 до 25 мас. ч. со средним диаметром частиц от 1·10-8 до 5·10-6 м и средней молекулярной массой от 1000 до 100000, при этом реакционноспособными группами, способными вступать в химическую реакцию с эпоксидной смолой, модифицирована в основном только поверхность таких эластомерных частиц, а также (IV) необязательно другие обычные добавки в количестве от 0,05 до 2 мас. ч., эту смесь (4) подвергают сшиванию, при необходимости с нагревом формы, и готовую деталь (5) извлекают из формы.
2. Способ изготовления армированного волокном изделия на основе эпоксидной смолы по п.1, заключающийся в том, что инжектируемая смесь (4) в пересчете на 100 мас. ч. содержит следующие компоненты: (I) эпоксидную смолу в количестве от 60 до 70 мас. ч., (II) ароматический диамин в количестве от 25 до 35 мас. ч. и (III) сшиваемые эластомерные частицы на основе полиорганосилоксанов в количестве от 2 до 5 мас. ч. со средним диаметром частиц от 1·10-8 до 5·10-6 м и средней молекулярной массой от 1000 до 100000, при этом реакционноспособными группами, способными вступать в химическую реакцию с эпоксидной смолой, модифицирована в основном только поверхность таких эластомерных частиц, а также (IV) необязательно другие обычные добавки в количестве от 0,07 до 1 мас. ч.
3. Способ по любому из предыдущих пунктов, отличающийся тем, что используют многофункциональную эпоксидную смолу.
4. Способ по п.3, отличающийся тем, что используют тетрафункциональную смолу.
5. Способ по п.4, отличающийся тем, что в качестве тетрафункциональной смолы применяют тетраглицидилдиаминодифенилметан.
6. Способ по любому из предыдущих пунктов, отличающийся тем, что в качестве ароматического диамина применяют диаминодифенилметан.
7. Способ по любому из предыдущих пунктов, отличающийся тем, что ароматический диамин содержит по меньшей мере в одном ортоположении по отношению по меньшей мере к одной аминогруппе алкильную группу, прежде всего метильную, этильную или изопропильную группу.
8. Способ по любому из предыдущих пунктов, отличающийся тем, что средний размер модифицированных эластомерных частиц составляет от 1·10-7 до 3·10-6 м.
9. Способ по любому из предыдущих пунктов, отличающийся тем, что средняя молекулярная масса эластомерных частиц составляет от 1200 до 30000.
10. Применение изготовленного способом по меньшей мере по п.1 изделия в авиационной и космической промышленности.
findpatent.ru
Армированная эпоксидная клеевая композиция (варианты)
Изобретение относится к армированным эпоксидным клеевым композициям горячего отверждения и может быть использовано в качестве срединных слоев многослойных конструкций радиотехнического назначения с широким диапазоном диэлектрических свойств в авиакосмической технике и других отраслях промышленности. Армированная эпоксидная клеевая композиция включает жидкую эпоксидную диановую смолу с количеством эпоксидных групп 20,0-22,5%, дициандиамид и дополнительно содержит продукт поликонденсации дифенилолпропана с 4,4′-дихлордифенилсульфоном, в качестве наполнителя — микросферы стеклянные полые с объемной плотностью 250,0-300,0 кг/м3 и ткань кварцевую. Изобретение обеспечивает расширение диапазона и возможность варьирования диэлектрических свойств, использование в современных широкополосных многослойных (взаимосогласованных по диэлектрическим свойствам слоев) конструкциях радиотехнического назначения. 2 н.п. ф-лы, 2 табл., 6 пр.
Изобретение относится к армированным эпоксидным клеевым композициям горячего отверждения и может быть использовано в качестве срединных слоев многослойных конструкций радиотехнического назначения с широким диапазоном диэлектрических свойств в авиакосмической технике и других отраслях промышленности.
Известна клеевая композиция, включающая бутадиеннитрилстиролкарбоксилатный каучук, эпоксидную диановую смолу или ее смесь с эпоксиноволачной смолой, отвердитель — ароматический диамин или дициандиамид и растворитель — смесь ацетона и толуола, может дополнительно содержать наполнители, антипирены, ускорители и т.д. (а.с. 1691382, опубликовано в 1991 г.).
Эта композиция имеет довольно узкий диапазон применения, так как не может использоваться в многослойных конструкциях радиотехнического назначения, что обусловлено ее составом. Кроме того, в составе клеевой композиции содержится растворитель, провоцирующий в процессе отверждения образование неконтролируемого количества пор, что вызывает разброс диэлектрических свойств.
Известна полимерная композиция, содержащая эпоксидную диановую смолу, аминный отвердитель и аддукт эпоксидиановой смолы с полиарилен-2,5-диокси-1,4-бензохиноном (а.с. 1564175, опубликованное в 1991 г.), используемая для пропитки, герметизации покрытий, в качестве клея. Эта полимерная композиция имеет после отверждения определенное значение диэлектрических свойств, без возможности их варьирования, что ограничивает область ее применения.
Наиболее близкой по составу к заявляемой является клеевая композиция (патент RU 1678043, опубликован в 1997 г.), включающая, мас.ч:
твердая эпоксидная диановая смола | 15-46 |
жидкая эпоксидная диановая смола | 25-74 |
твердый сополимер бутадиена с акрилонитрилом | 0,5-20 |
полигидроксиэфир | 10-90 |
эпоксидная диановая смола | |
с количеством эпоксидных групп 1,8-2,8% | 15-45 |
эпоксирезорциновая смола | 30-90 |
дициандиамид | 5-21 |
полиангидрид себациновой кислоты | 4-12 |
бис-(N,N′-диметилкарбамид)-дифенилметан | 21-10 |
низкомолекулярный бутадиен-акрилонитрильный карбоксилсодержащий каучук | 2-25 |
армирующий наполнитель и/или пигмент или краситель | 2-40 |
Однако она не может быть использована в конструкциях радиотехнического назначения, что обусловлено ее составом.
Задачей изобретения является разработка композиции, обеспечивающей широкий диапазон диэлектрических свойств и использование ее в современных широкополосных многослойных (взаимосогласованных по диэлектрическим свойствам слоев) конструкциях радиотехнического назначения.
Для решения поставленной задачи предлагается: 1. Армированная эпоксидная клеевая композиция, включающая жидкую эпоксидную диановую смолу с количеством эпоксидных групп 20,0-22,5%, дициандиамид и наполнители, отличающаяся тем, что она дополнительно содержит продукт поликонденсации дифенилолпропана с 4,4′-дихлордифенилсульфоном, а в качестве наполнителя — микросферы стеклянные полые с объемной плотностью 250,0-300,0 кг/м3 и ткань кварцевую, при следующем соотношении компонентов, мас.%:
жидкая эпоксидная диановая смола | 34,5-35,0 |
дициандиамид | 7,3-7,7 |
продукт поликонденсации дифенилпропана | |
с 4,4′-дихлордифенилсульфоном | 19,2-19,4 |
микросферы стеклянные полые | 0,6-1,9 |
ткань кварцевая | 36,7-37,3 |
2. Армированная клеевая эпоксидная композиция, включающая жидкую эпоксидную диановую смолу с количеством эпоксидных групп 20,0-22,5%, дициандиамид и наполнители, отличающаяся тем, что она дополнительно содержит продукт поликонденсации дифенилолпропана с 4,4′-дихлордифенилсульфоном, а в качестве наполнителя — микросферы полимерные и стеклосотопласт с плотностью 44,0-45,0 кг/м3, при следующем соотношении компонентов, мас.%:
жидкая эпоксидная смола | 50,0-52,1 |
дициандиамид | 10,9-11,0 |
продукт поликонденсации дифенилпропана с 4,4′ | |
дихлордифенилсульфоном | 27,5-30,3 |
микросферы полимерные | 5,5-10,0 |
стеклосотопласт | 1,5-1,7 |
Предлагаемая клеевая композиция обладает широким диапазоном диэлектрических свойств, которые можно использовать в срединных взаимосогласованных слоях радиотехнических конструкций. Регулируя соотношение наполнителей в клеевой композиции, можно варьировать диэлектрическую постоянную срединных слоев конструкции от 1,5 до 3,0 при tgδ от 190 до 130. Отсутствие растворителей способствует стабилизации физико-механических и диэлектрических характеристик и дает возможность рассчитать получаемые значения диэлектрических свойств композиции.
В композиции используется:
— жидкая эпоксидная диановая смола, в которой массовая доля эпоксидных групп от 20 до 22,5%;
массовая доля летучих веществ не более 0,2%,
массовая доля гидроксильных групп не более 1,5%.
— продукт поликонденсации дифенилолпропана с 4,4′-дихлордифенилсульфоном с молекулярной массой 30000 в качестве пластификатора и имеет следующие характеристики:
число вязкости от 37 до 50 мл/г;
массовая доля летучих веществ не более 2%;
растворимость в эпоксидно-диановой смоле — полная.
— дициандиамид, в котором массовая доля дициандиамида не менее 98,5%, температура плавления не ниже 208°C.
— микросферы стеклянные полые марки МС ВП ТУ 6-48-91-92 с объемной плотностью 250-300 кг/м, размером 70-125 мкм, гидростатическое давление разрушения 50% микросфер 25,4-13,5 МПа, диэлектрическая проницаемость при 1010 Гц при 20°C — 1,2-1,4.
— микросферы полимерные сухие облегченные предварительно расширенные марки 461 DET80d25 с истинной плотностью 25 кг/м3, примерный размер частиц после расширения 80 мкм, диэлектрическая проницаемость при 1010 Гц при 20°C 1,1-1,2;
— в качестве наполнителя используется:
— ткань кварцевая ТС 8/3-К-ТО ТУ 6-48-112-94;
— стеклосотопласт ССП-1-8Э ТУ 1-596-452-2005 плотность 45-55 кг/м3,
прочность при сжатии 1,8-2,2 МПа.
В таблице приведены составы и свойства предлагаемой и известной клеевой композиции.
Пример 1. Готовили клеевую массу из расчета на 13,5 кг жидкой эпоксидной диановой смолы 7,5 кг продукта поликонденсации дифенилолпропана с 4,4′-дихлордифенилсульфоном; 3,0 кг смеси жидкой эпоксидной диановой смолы с диметилформамидом и 0,66 кг микросфер стеклянных полых. С использованием оборудования для изготовления пленочного клея (поливочной машины) получали клеевую композицию с содержанием микросфер 2,5-2,7%, максимальной толщиной до 0,65 мм. Производили полуфабрикат путем совмещения кварцевой ткани и клеевой композиции вакуумным формованием при температуре 130°C и давлении 0,8 МПа в течение часа. Далее набирали из готовых листов полуфабриката пакет заданной толщины и производили вакуумное формование при давлении 0,8 МПа, температуре 170°C в течение 3-х часов. Количество листов рассчитывали в зависимости от заданных диэлектрических параметров. Состав композиции приведен в таблице п. 1, а свойства в таблице п. 2.
Пример 2-3. Проводили по примеру 1, но количество введенных микросфер стеклянных составило 1,900 кг во втором примере и 2,090 кг в третьем примере. Клеевую пленку получали на каландре с подогреваемыми вальцами (рабочая температура 130-135°C), при установленном зазоре «на ноже» около 1 мм была получена пленка с толщиной 1,0-1,7 мм, которая использовалась для изготовления полуфабриката синтактного стеклопрепрега вакуумным способом. Состав композиции приведен в таблице п. 1, а свойства в таблице п. 2.
Пример 4-6. Проводили по примеру 1, но в качестве армирующего наполнителя использовали стеклосотопласт ССП-8Э и полимерные микросферы. Клеевую пленку, изготовленную по примеру 2-3, вдавливали в ячейки стеклосотопласта, заполняя их плотно на всю высоту. Проводили режим вакуумного формования при давлении 0,8 МПа и температуре 170°C в течение 3-х часов. Состав композиции приведен в таблице п. 1, а свойства в таблице п. 2.
Технический результат изобретения — изготовление клеевой композиции, обеспечивающей расширение диапазона и возможность варьирования диэлектрических свойств, использование в современных широкополосных многослойных (взаимосогласованных по диэлектрическим свойствам слоев) конструкциях радиотехнического назначения.
1. Армированная клеевая эпоксидная композиция, включающая жидкую эпоксидную диановую смолу с количеством эпоксидных групп 20,0-22,5%, дициандиамид и наполнители, отличающаяся тем, что она дополнительно содержит продукт поликонденсации дифенилолпропана с 4,4′-дихлордифенилсульфоном, а в качестве наполнителя — микросферы стеклянные полые с объемной плотностью 250,0-300,0 кг/м3 и ткань кварцевую, при следующем соотношении компонентов, мас.%:
жидкая эпоксидная смола | 34,5-35,0 |
дициандиамид | 7,3-7,7 |
продукт поликонденсации дифенилпропана с 4,4′- | |
дихлордифенилсульфоном | 19,2-19,4 |
микросферы стеклянные полые | 0,6-1,9 |
ткань кварцевая | 36,7-37,3 |
2. Армированная клеевая эпоксидная композиция, включающая жидкую эпоксидную диановую смолу с количеством эпоксидных групп 20,0-22,5%, дициандиамид и наполнители, отличающаяся тем, что она дополнительно содержит продукт поликонденсации дифенилолпропана с 4,4′-дихлордифенилсульфоном, а в качестве наполнителя — микросферы полимерные и стеклосотопласт с плотностью 44,0-45,0 кг/м3, при следующем соотношении компонентов, мас.%:
жидкая эпоксидная смола | 50,0-52,1 |
дициандиамид | 10,9-11,0 |
продукт поликонденсации дифенилпропана с 4,4′- | |
дихлордифенилсульфоном | 27,5-30,3 |
микросферы полимерные | 5,5-10,0 |
стеклосотопласт | 1,5-1,7 |
findpatent.ru
Эпоксидная смола — как правильно применять
Прочнейший клей, который склеит почти все, за исключением капрона, оргстекла, полиэтилена и других непористых эластичных материалов — двухкомпонентная эпоксидная смола. Вещество также применяется в рукоделии, изготовлении мебели, декупаже, авто, творчестве, строительстве. Иначе оно называется компаунд эпоксидный. В свободном виде эпоксидка не применяется, только в сочетании с отвердителем, который дает возможность проявиться после реакции полимеризации ее уникальным свойствам. По этой причине важно знать, как развести эпоксидную смолу правильно.
Что такое эпоксидная смола
Эпоксидная смола — это олигомеры, которые содержат эпоксидные группы и при воздействии отвердителей формируют сшитые полимеры. Отвердителями могут быть полиамины и другие соединения. Самыми распространенными эпоксидными смолами являются продукты поликонденсации с бисфенолом А либо поликонденсации с фенолами эпихлоргидрина.
Жидкая эпоксидная смола может быть различных оттенков: от белого, прозрачного, до винно-красного. Но обычно имеет вид желто-оранжевой прозрачной жидкости, по консистенции напоминающей мед, или твердой, коричневой (как гудрон) массы.
Состав
Эпоксидная смола по химическому составу представляет собой синтетическое олигомерное соединение. Подобные вещества на сегодняшний день востребованы практически во всех отраслях промышленности. После соединения эпоксидной смолы с отвердителями получаются:
- прочные и мягкие материалы;
- твердые и жесткие;
- материалы, напоминающие резину.
Эпоксидная смола обладает устойчивостью к воздействию кислот, галогенов, щелочей, но растворяется в ацетоне и сложных эфирах без формирования пленки. После отвердения летучие вещества не выделяются, происходит совсем незначительная усадка состава.
Как работать с эпоксидной смолой
Для работы с эпоксидной смолой понадобится отвердитель, одноразовый стаканчик, 2 шприца и палочка для перемешивания.
Совет
Вливайте отвердитель в смолу, а не наоборот. Обычно отвердитель имеет жидкую консистенцию и при резком нажатии на шприц может разбрызгиваться, поэтому делаете это осторожно.
Инструкция по применению:
- Возьмите шприц, наберите в него необходимое количество смолы и выпустите в стаканчик. То же самое проделайте с отвердителем. Пропорции смешивания у разных производителей различны, потому перед началом работы внимательно прочитайте инструкцию по применению. Неправильно разведенная эпоксидка плохо застывает.
- Хорошенько перемешайте смолу с отвердителем, масса должна стать однородной. Смешивать необходимо медленно и осторожно, если делать это резкими движениями и быстро, то в массе появятся пузырьки. Жидкая консистенция состава обеспечит быстрый выход пузырьков наружу, в изначально густых компонентах они останутся. Плотность смолы зависит от производителя. Недостаточно хорошо смешанные компоненты обусловят плохое застывание состава.
- Полимеризация не происходит мгновенно, необходимо немного подождать пока масса приобретет требующуюся для работы консистенцию.
- Залейте в форму или сделайте линзу.
- Подождите указанное производителем в инструкции время, пока эпоксидная смола окончательно застынет.
Совет
Во время застывания к массе хорошо прилипают пылинки и разная грязь. Предотвратить это поможет использование емкостей и коробок с крышкой. Сделайте изделие в коробке и закройте крышкой на время затвердевания состава.
Эпоксидная смола имеет условные стадии застывания:
- Вначале масса очень жидкая и легко стекает, что делает ее максимально подходящей для заливки в форму. Жидкая консистенция позволяет эпоксидке проникнуть в мельчайшие углубления, более густому составу это не под силу, и рельеф получится не очень явным.
- По прошествии некоторого времени эпоксидная смола становится гуще и подходит для изготовления выпуклых линз на плоской основе. Сделать подобную линзу из жидкой смолы не удастся — состав будет скатываться вниз с заготовки. На этой стадии лучше всего заливать нерельефные формы в домашних условиях.
- Наименее подходящая консистенция смеси для работы — наподобие густого меда. При набирании эпоксидки на палочку легко формируются пузырьки, убрать которые очень сложно. На этой стадии состав подходит для того, чтобы склеить детали между собой. Эпоксидка характеризуется отличной адгезией и прекрасно прилипает к большинству материалов (на основе этого свойства был разработан клей ЭДП.), но легко отслаивается от полипропилена, полиэтилена, силикона, резины, поверхностей, покрытых пленкой жира.
- Эпоксидная смола становится очень густой и липкой, отделить немного от основной массы проблематично.
- Следующая стадия — резиновая. Эпоксидка не прилипает к рукам, но легко мнется и гнется, из нее получится сделать множество изделий, но если вы хотите, чтобы она затвердела в нужном положении, то закрепите ее, иначе она вернется в первоначальное состояние.
- Окончательно затвердевшая эпоксидная смола. Ее нельзя продавить ногтем, на ощупь она похожа на пластик.
Совет
Если нет формы из специального материала, то смажьте имеющуюся растительным маслом, но сначала проверьте, как отреагирует на него конкретно этот состав эпоксидки.
Эпоксидна смола от разных производителей характеризуется различным временем отвердения. Время наступления стадий определяются исключительно опытным путем. Существует мягкая эпоксидная смола, которая остается резиновой даже после полного застывания, что для некоторых изделий является идеальным вариантом.
Как развести
Разводить пропорции необходимо очень тщательно, так как недостаточное либо избыточное количество отвердителя в смеси отрицательно сказывается на качестве образующегося полимера.
Избыток отвердителя характеризуется тем, что состав остается устойчивым к нагреванию, действию химических веществ и воды, но становится менее прочным. Кроме того, излишек выделяется на поверхности при эксплуатации изделия, поэтому необходимо точно знать, как развести эпоксидную смолу правильно.
Недостаточное количество отвердителя делает смолу липкой, так как ее часть остается несвязанной.
Для получения различных смесей отвердитель и эпоксидная смола смешиваются в различных пропорциях, о чем вы узнаете, прочитав инструкцию по применению. Современный состав обычно делается так: на 1 часть отвержающих компонентов берутся 2 части смолы или отвердитель и смола смешиваются 1 к 1.
На скорость полимеризации оказывают влияние тип отвердителя и температура состава. Чтобы ускорить процесс, слегка нагрейте массу. Повышение температуры на 10° С обеспечит ускорение полимеризации в 3 раза. Существуют составы, которые включают в себя ускорители отвердения, есть и такие, которые застывает при низких температурах.
Эпоксидная смола становится твердой при температуре от —10 до +200° С, что зависит от вида применяемого состава. Чаще всего в быту применяются отвердитель холодного типа, он встречается в условиях маломощного производства и там, где термическая обработка недопустима.
Отвердители горячего типа применяются в процессе получения изделий с высокой прочностью, которые будут подвергаться значительным нагрузкам и действию высоких температур. Горячая полимеризация способствует формированию густой сетки молекул, которая и обеспечивает устойчивость состава.
Расход на 1м2
Сколько будет израсходовано эпоксидной смолы, зависит от цели ее применения. Если воспользоваться эпоксидкой как клеем, то на расход повлияют свойства соединяемых поверхностей:
- пористость;
- шероховатость;
- способность впитывать вещества.
Совет
Нанесите минимально приемлемое количество эпоксидки на склеиваемые поверхности, затем прижмите их друг к другу и зафиксируйте в таком положении до полного застывания клея.
Расход на площадь имеет большое значение при изготовлении, например, напольного покрытия. Если необходимо покрыть бетонный гладкий пол, просто чтобы он не пылил, то достаточно будет 100 г на 1 м2. При изготовлении более прочного покрытия, армированного и идеально ровного потребуется до 3,5 кг эпоксидной смолы на 1 м2.
Модифицированные эпоксидки различных оттенков применяются при устройстве полимерных наливных полов. Полимер выливается из емкости на пол и растекается благодаря силе тяжести. Подобное нанесение обуславливает расход от 1 кг эпоксидки на 1м2 на один слой.
Сколько сохнет
Полное застывание эпоксидки обычно происходит через 24 часа. Изделия (например, броши, заколки), которые не подвергаются значительным нагрузкам, готовы к эксплуатации уже через 12 часов.
Какую температуру выдерживает
Температура плавления застывшей эпоксидной смолы составляет до +150—180° С, при этом ее прочность уменьшится незначительно. Некоторые марки клея выдерживают кратковременный нагрев до +400° С и продолжительный — до +250° С.
Вредна ли для здоровья
После застывания эпоксидная смола при нормальных условиях эксплуатации абсолютно безвредна для человеческого организма. Но ее применение ограничивается тем, что при отвердении в условиях промышленного производства в составе остается немного растворимого остатка (золь-фракции). Именно этот остаток может нанести серьезный ущерб здоровью, если будет вымыт растворителями и проникнет в организм человека. Эпоксидные смолы до застывания ядовиты и способны отрицательно повлиять на здоровье.
Полезные советы
Советы и рекомендации профессионалов помогут облегчить работу с эпоксидной смолой и сделать все максимально качественно:
- Перед началом работы застелите стол полиэтиленовой пленкой, чтобы избежать протекания и загрязнения его поверхности. Бумага не защитит от пятен, так как эпоксидка пропитывает ее.
- Не допускайте попадание воды в отвердитель, эпоксидную смолу или смесь этих веществ. Если работать с составом при высокой влажности воздуха в помещении, застывание будет происходить плохо.
- Можете придать эпоксидке любой оттенок. Это делается с помощью добавления в состав специальных тоннеров, но их стоимость сравнительно высока. Более приемлемым по цене вариантом являются чернила гелевых ручек, краска, находящаяся внутри фломастеров, маркеров или витражная.
- Не работайте с эпоксидкой при температуре окружающего воздуха ниже +22° С, так как существует вероятность, что состав плохо застынет.
- Если смолу подержать в холодном помещении, например, на балконе, в ней могут появиться хлопья или крупинки. Чтобы вернуть состав в первоначальное состояние, нагрейте его до 40—60° С.
- Поставив изделие на батарею отопления, вы сократите продолжительность застывания эпоксидной смолы. Обеспечьте не слишком сильное повышение температуры, чтобы состав не закипел с образованием множества пузырьков.
- Если близко к поверхности эпоксидной смолы сформировался пузырек — просто подуйте на него через коктейльную трубочку или раскрученную ручку. Образовавшийся пузырек лопнет.
- Эпоксидка характеризуется повышенной текучестью, по этой причине не применяйте состав в качестве покрытия (лака) для рельефных изделий.
- Сделать качественно линзы на заготовках с плоской поверхностью удастся, только разместив их в идеально горизонтальном положении. В противном случае линзы получатся неровными — с одной стороны выше, с другой — ниже.
- Если линза сползается к центру и не закрывает края заготовки, это говорит о том, что эпоксидки было налито мало или она очень жидкая. Попробуйте залить еще один слой, это позволит исправить положение.
- Чтобы с течением времени эпоксидная смола не пожелтела под действием солнечных лучей и тепла, приобретайте продукт, в составе которого имеется УФ-фильтр.
- При попадании эпоксидки на кожу рук оттирайте загрязнения спиртом, после чего вымойте руки с мылом.
- Если смола попала в глаза или была проглочена — обратитесь к врачу.
Эпоксидные смолы токсичны в большей или меньшей степени, в зависимости от состава. По этой причине работать с ними необходимо в хорошо проветриваемой комнате или под вытяжкой. Полностью обезопасить себя от вдыхания паров органических кислот можно, работая с эпоксидкой в респираторе.
goodklei.ru
идеи для творчества и бытового ремонта
Эпоксидная смола появилась на рынке относительно недавно, но ей уже трудно найти альтернативу. Материал конкурирует с деревом, керамикой, пластиком, металлом. Эпоксидка применяется в промышленных целях, в домашнем хозяйстве, для творчества. Когда и чем можно и даже нужно заменить эпоксидную смолу? У состава есть ряд негативных свойств, а иногда его просто не оказывается под рукой — что станет достойной альтернативой? Подборка советов и проверенных методов — в нашей статье.
Об эпоксидной смоле и ее замене
Эпоксидная смола — это олигомерное соединение, и ее не используют в чистом виде. При смешивании со специальным отвердителем состав становится полимером. От соотношения этих двух компонентов зависят механические свойства застывшего материала: он будет твердым как стекло или мягким, похожим на резину.
Преимущества эпоксидки:
- При высыхании становится очень прочной.
- Мало подвержена абразивному износу.
- Ей не страшно воздействие щелочей, галогенов и кислот.
- Низкий уровень влагопроницаемости.
- Не имеет неприятного запаха.
- Не выделяет летучие вещества.
- Усадка при высыхании практически незаметна.
- Прочно пристает к металлу и другим материалам.
- Растворяется в ацетоне или сложных эфирах без образования пленки.
Эпоксидный клей — вещество, основным компонентом которого является эпоксидная смола. Клей обладает универсальными потребительскими характеристиками.
Где применяется эпоксидка:
- Проклейка стеклотканей, изготовление и ремонт стеклопластиковых изделий (автомобильная, авиационная отрасли, кораблестроение).
- Для гидроизоляции помещений с повышенной влажностью (в том числе, подвальных), стенок бассейна.
- Для обработки пористых материалов (дерева, бетона), что делает их более прочными и водонепроницаемыми.
- Для упрочения отделки, в том числе придания химической устойчивости поверхностям.
- Для реализации самых разнообразных дизайнерских идей.
- Для любительского и профессионального творчества.
- В домашнем хозяйстве и т.д.
Эпоксидная смола не зря занимает лидирующие позиции среди отделочных и других материалов. Заменить ее достаточно трудно, но иногда это бывает необходимо.
В каких случаях требуется замена эпоксидной смолы:
- Если вы склонны к аллергическим реакциям (вещество довольно сильный аллерген).
- Форма изделия не позволяет использовать эпоксидку: обработка получаеттся недостаточно аккуратной.
- Требуется склеить посуду для еды или детскую игрушку.
- В конкретный момент у вас нет желания или возможности выложить определенную сумму (эпоксидка довольно дорого стоит).
- Материал закончился в ближайшем магазине (эпоксидная смола востребована и обычно представлена широко, и все же иногда ее не оказывается на витрине).
Использование предметов из эпоксидной смолы в быту безопасно для человека, главное — не подвергать их сильному нагреву. Отмечается вред здоровью при длительном контакте с эпоксидной смолой, вдыхании паров, попадании вещества на эпидермис. Последствия — раздражения кожи, дыхательных путей, глаз.
В творчестве
До каких только интересных идей по применению некоторых веществ не додумывались рукодельницы! Так и в случае с эпоксидной смолой творческие люди нашли ей несколько вариантов замены, представим два из них:
- Прозрачный финишный гель для наращивания ногтей.
- Силликат натрия.
В первом случае замена почти беспроиграшная по качеству. Необходимо лишь придать нужную форму и подержать изделие под ультрафиолетовой лампой. Берется именно финишный гель, а не конструирующий. Второй вид плохо высыхает, остается липким.
Гель для ногтей абсолютно прозрачный, его легко скорректировать в случае неудачной обработки. Еще одно преимущество — он быстро сохнет. Если смоле нужно от 5 до 40 часов, то под UV-лампой гель застывает за 2—4 минуты. Минус геля: в отличие от эпоксидки, он недостаточно прочный. При ударе могут образоваться сколы, при небрежном использовании — царапины.
Во время работы или для ремонта гель дает большие возможности. Лопнувшие при шлифовке пузырьки, случайные сколы довольно легко исправить, чередуя нанесение геля со шлифовкой. Как отмечают рукодельницы, коррекция занимает не больше 15 минут, в зависимости от глубины скола.
Интересный факт
Гели для наращивания, как и эпоксидка, изготавливают из смолы.
Заменить эпоксидную смолу может силикат натрия, или жидкое стекло. Это более капризная субстанция, но иногда ее применение более уместно. Прежде всего, силикат не вызывает аллергии.
Сложности в работе сводятся к долгому сроку высыхания (в среднем, требуется три часа) и возможной липоксти. Если все сделать аккуратно и выждать нужное время, канцелярский клей послушно создаст эффект стекла, придаст поверхности нужный глянец.
Рекомендации по использованию силикатного клея: покрыть предмет тонким слоем, дождаться высыхания. Вполне вероятно, сразу или через некоторое время (обычно на второй день) появится липкость. Теперь нужно протереть поверхность спиртом, нанести еще один слой жидкого стекла, толще первого, и дать высохнуть. Липкость больше не появится.
Совет! На стекле силикат застывает быстрее — по причине близкого химического состава.
В быту. Силикатный клей
Эпоксидка очень популярна в бытовом ремонте, в зависимости, от типа отвердителя, им чинят обувь, пластмассовые изделия, деревянные предметы, в том числе, мебель. Заменить в этих случаях эпоксидку могут специализированные составы либо другой универсальный клей, например, цианакрилатный (а нем чуть позже).
Неплохая альтернатива эпоксидке — все тот же силикатный клей, теперь уже выступающий как скрепляющая субстанция. Вещество хорошо скрепляет картон, стекло, фарфор, керамику. Используется для пропитки тканей и дерева для придания им большей прочности и огнестойкости.
Применение: нанести на скрепляемые поверхности тонким слоем и прижать их друг к другу.
В сочетании с другими компонентами силикатный (канцелярский) клей дает смесь, которая по своим характеристикам будет не хуже эпоксидного. Вот некоторые примеры:
- 50 г силикатного клея + 25 г асбеста + 16 г порошкового стекла. Состав обладает повышенной стойкостью к воздействию химических веществ и выдерживает температуру до 1500 градусов. Хорошо сцепляет фарфор, стекло и керамику.
- Для склеивания сосудов, в которых хранятся кислоты, готовят такую пасту: любое количество мелкого песка, асбеста, магнезии и концентрированного жидкого стекла смешать до получения густой массы.
- Рецепт водостойкой замазки: 8 г силикатного клея + 20 г казеинового порошкообразного клея.
Совет! При гидроизоляции помещений стоит предпочесть силикатные герметики: они обладают такой же влагостойкостью, жаропрочностью, образуют эластичный шов, как и эпоксидка, но при этом более безопасны.
Цианакрилатные клеи
Клеящая продукция этого типа — достойная замена эпоксидке. К ней относятся все суперклеи («Секунда», «Супер Момент» и т.д.) Вещества при засыхании становятся полностью прозрачными, а их прочность после застывания сравнима с прочностью шурупов. Некоторые образцы содержат дополнительные усилители и отличаются тепло- и водостойкостью, теплопроводностью, устойчивостью к растворителям и другими полезными свойствами.
Но у цианакрилатной продукции есть свои недостатки:
- хрупкость, низкая стойкость к механическому воздействию;
- нестабильность при длительном хранении;
- опасность для кожи человека при прямом контакте.
Выбор того или иного цианакрилатного клея зависит от поверхности, которую необходимо прикрепить. Наиболее применимы такие вещества для металлопластика и стекла. Не подходят для склеивания полиэтилена и фторопласта. Продукция бывает разной степени вязкости: низкой и высокой.
В первом случае получаются высокопрочные клеевые швы при условии хорошей стыковки поверхностей. Составы с высокой степенью вязкости позволяют добиться максимально прочных соединений. В частности, такие клеи применяются для сцепления лодочной ПВХ-ткани.
Чем заменить отвердитель для эпоксидной смолы
Иногда из-за некачественной упаковки отвердитель расходуется значительно быстрее смолы или попросту испаряется. Если нет возможности приобрести вещество отдельно, то эти варианты его заменят:
- нашатырный спирт,
- ортофосфорная кислота,
- перекись бензоила.
Хотя альтернатива эпоксидке есть, все же ее замена не всегда дает лучший результат. Такое уж это многофункциональное вещество. При работе с особо важными деталями следует отдавать предпочтение эпоксидной смоле.
goodklei.ru