Рейсмусовые станки – принцип работы и правильная наладка…
В принцип работы рейсмуса заложена методология плоского строгания доски. Основным рабочим инструментом у рейсмусового станка является ножевой вал. Заготовки для обработки подаются на горизонтальный рабочий стол вручную или же вальцами, которые прижимают их к столу и тянут в область обработки. Материал строгается сверху ножиками, и, в итоге получаются детали, практически одинаковые по размеру. Многие рейсмусовые станки имеют автоматическую систему подачи заготовок с определенной скоростью, для того чтобы опрятно и точно снимать строго необходимый слой.
На сегодняшний день можно купить односторонний или же двусторонний рейсмус. У первых – присутствует один ножевой вал. В двусторонних моделях есть ещё и добавочный ножевой вал на рабочем столе. Перед обработкой деталей рейсмусом они должны быть уже подструганными в фуговальном станке. По конструкции, в принципе два станка весьма схожи между собой. Нередко двусторонний рейсмус и фуганку комбинируют в один механизм.
Традиционно на рейсмусовом станке строгают заготовки длиной чуть больше расстояния, что сформировалось между подающими вальцами, как на видео о рейсмусовом станке. В случае применения подкладных шаблонов (цулаги) можно строгать на рейсмусовом станке заготовки (щиты, бруски, доски) с непараллельными противоположными гранями. Поверхность данного шаблона должна наклоняется таким способом, чтобы при процедуре горизонтального строгания изделий можно было получить необходимую конусность.
В некоторых моделях рейсмусовых станков для удобства пользователя фирмами-изготовителями увеличена длина стола. Именно поэтому, брус имеет существенную площадь опоры, а изделия обрабатываются намного точнее. Для того чтобы заготовка по столу нормально скользила, в них делают особые канавки, сокращающие силу трения. Подобные модели ранее применялись преимущественно на производстве, а на данный момент эти принципы обширно внедряются и в любительские рейсмусовые агрегаты.
Одним из основных преимуществ рейсмусового станка выступает высокое качество обработанных поверхностей. Толщина получаемых деталей задается при помощи подъемного механизма, когда стол перемещается по отношению к ножевому валу вверх. Но стоит учитывать то, что при высокой скорости резания заготовок, а так же сравнительно большой глубине резания ухудшается качество обработанной поверхности. Именно поэтому, для того чтобы добиться гладкой поверхности, нужно делать финишные проходы при малой глубине и небольшой скорости вращения ножевого вала, если конечно же станком предусмотрена регулировка.
Рейсмусовый станок является одним из особенно высокопроизводительных деревообрабатывающих станков. Стоит один раз настроить размеры обрабатываемой заготовки при помощи линейки и подъемника, и вся партия изделий будет идентичной, в пределе допустимого показателя. На рейсмусовых станках вы можете обрабатывать детали с шириной до 1250 миллиметров и с толщиной 5 — 160 миллиметров, кроме особых станков, предназначенных для строго определенных видов работ.
О наладке рейсмусового станка
Рейсмусовые станки перед работой должны быть тщательно налажены. Фактически любая неточность наладки спровоцирует дефекты обработки или же приведет к уменьшению эффективности станка. Чаще всего наблюдаются следующие упущения в наладке рейсмусов:
Перекос на рабочем столе.
Строгаемая поверхность не будет получаться параллельной фугованной стороне.
Рифленый валик располагается весьма низко и нажимает слишком сильно на поверхность деталей при малой глубине строгания.
Строганные поверхности получаются с поперечными вмятинами.
Нижние валики подачи размещаются над уровнем стола выше, чем необходимо, на 0,1-0,2 миллиметра.
В результате этого имеет место вибрация обрабатываемого изделия под ударами ножиков, а более тонкие детали прогибаются. Строгание выходит непрямолинейным, а так же не таким гладким, концы изделий больше прострагиваются.
Задняя нажимная колодка на обрабатываемую деталь давит.
По этой причине изделие при выходе из передних подающих валиков благодаря уменьшению силы подачи останавливается. Поскольку ножи будут продолжать вращаться, строгается на поверхности детали одно место, то в результате здесь появляется желобок во всю ширину строгания.
Вообще желобки формируются при всякой, даже наиболее короткой остановке изделия. Остановки достаточно часто случаются во время, когда детали поступают в задние валики. Это случается при весьма низком размещении верхнего заднего валика, а так же при его слишком большом нажиме на материал. Причинами кратковременной задержки или же остановки детали бывают: недостаточный нажим на изделие подающих валиков, слишком высокое расположение нижних валиков, сильное засорение стола при обработке сосновых деталей смолой.
Стружка попадает под задний гладкий валик из-за неправильного монтажа накидного козырька или же неисправностей эксгаустера.
По этим причинам на строганной поверхности появляются вмятины, иногда задержка детали.
Именно поэтому, при наладке рейсмусового станка необходимо помнить, что при существенном заполнении стола, например, при строгании широкого щита или же одновременной подаче изделий во всю ширину рабочего стола, повышенным должно быть давление подающих вальцов, так как в этих случаях сопротивление резанию существенно возрастает. При строгании узких деталей или же при маленьком заполнении стола необходимо уменьшить давление подающих вальцов, для того чтобы избежать смятия дерева.
В заключение…
К особенно распространенным в деревообрабатывающем деле относятся фуговальные, фрезерные, строгальные и рейсмусовые станки, которые предназначаются для плоскостного, объемного и профильного фрезерования прямо- , а также криволинейных заготовок из массивного дерева и древесных материалов, для нарезания проушин и шипов в брусках дверных коробок, оконных блоков.
Что такое рейсмус и рейсмус-калибр?
Рейсмусы становятся все более популярными. Эти переносные станки обеспечивают идеальную поверхность и миллиметровую точность. Но можно ли их назвать настоящим строгальным универсалом?
На фото:
Назначение рейсмуса
Калибровка досок по толщине. Что такое рейсмус и для чего он нужен? Рейсмус — это станок (переносной или массивный стационарный), предназначенный для чистового строгания досок под заданную толщину. Рейсмус пропускает доску через себя, строгая верхнюю пласть широким валом с лезвиями. На выходе пользователь получает доску нужной толщины с ровной гладкой поверхностью. Рейсмусы востребованы в первую очередь в столярном деле, так как позволяют откалибровать заготовки под стык заподлицо: детали одинаковой толщины образуют ровную поверхность.
Конструкция рейсмуса
На фото: рейсмусный станок DW733 компании DeWALT.
Механизм регулировки, автоподача.
Большинство станков имеет автоматическую подачу заготовки: два вальца (перед ножевым валом и за ним) двигают доску со скоростью порядка 7-8 метров в минуту. От пользователя требуется положить заготовку на стол, подать ее в станок и получить с обратной стороны. Эта функция очень полезна, так как позволяет сэкономить силы. У некоторых моделей имеется две скорости автоподачи: высокая обеспечивает быстрое выполнение работы, а низкая позволяет получить максимально качественную поверхность.
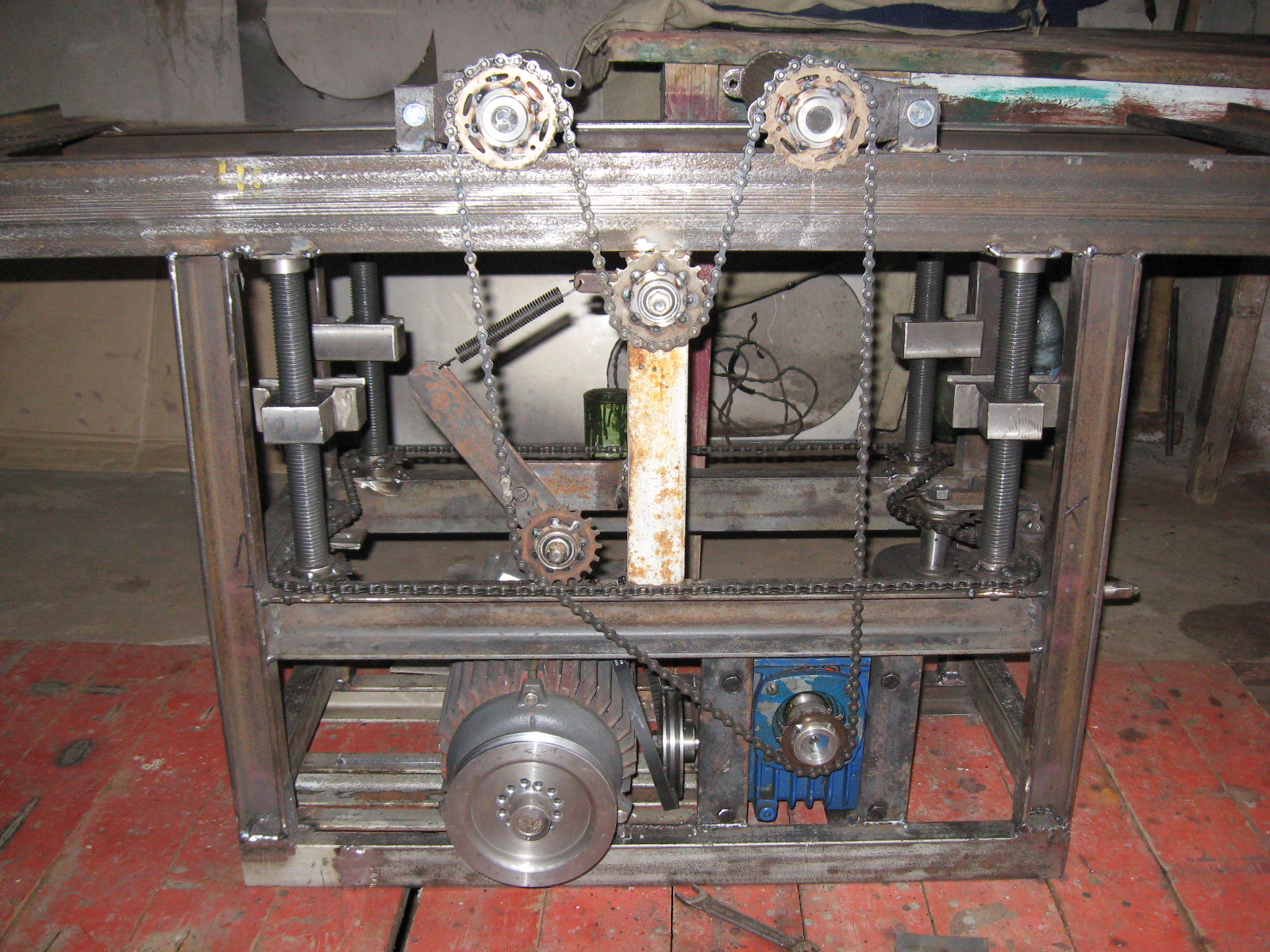
Технические характеристики
Мощность, размеры заготовки, вес. Мощность у рейсмусов, как правило, составляет 1500-1800 Вт. Ширина строгания и максимальная толщина заготовки — это своего рода калибр рейсмуса. Данные характеристики описывают допустимые размеры доски. Предельная ширина, как правило, составляет 310-330 мм, а толщина — 150-152 мм. Кстати, по максимальной толщине видно, насколько широкую доску вы сможете обработать, если поставите ее на ребро. Приведенные цифры, конечно, не означают, что рейсмус предназначен для строгания очень массивных длинных досок (их станок даже не сможет протащить). Оптимальный калибр рейсмуса — это сравнительно небольшие заготовки.
На фото: рейсмусный станок P13F компании Hitachi.
Глубина строгания показывает, какой слой древесины станок способен снять за раз. У рейсмусов максимальная глубина доходит до 3-3,2 мм. Обратите внимание: широкие доски не рекомендуется строгать с предельной глубиной — чем размашистее заготовка, тем меньше с нее надо снимать за один проход.
Частота вращения ножевого вала у рейсмусов находится в диапазоне от 8000 до 10000 об/мин. Чем выше скорость, тем качественнее получается строганная поверхность. Впрочем, на практике качество обработки зависит от целого ряда факторов.
Отвод стружки
Лучше работать с пылесосом. Во время работы рейсмус выбрасывает очень большое количество стружки, которую лучше удалять при помощи строительного пылесоса. Если этого не делать, то отходы будут забиваться в станке. Они могут приникнуть в подвижные механизмы и попадут в область строгания, что значительно снизит качество обработки (поверхность не получится гладкой). В конце концов, чистота на рабочем месте — это тоже важно.
В статье использованы изображения: metabo.ru, dewalt.ru, hitachi-pt.ru
Рейсмусовый станок своими руками | Строительный портал
Часто мастера, которые любят работать с деревом, или хозяева дачных домиков, сталкиваются с необходимостью строгания множества досок, чтобы придать им визуальной привлекательности. Нужно выровнять толщину материала, вывести размеры досок и щитов, получить гладкую поверхность заготовок, из которых впоследствии предстоит смастерить мебель, или использовать их для отделки пола или помещения. Решением проблемы может стать покупка рейсмуса или изготовление рейсмусового станка своими руками, ведь аппарат с автоматической подачей заготовок и ножевыми валами из быстрорежущей стали значительно ускоряет и облегчает процесс строгания древесины.
Содержание:
- Предназначение рейсмусового станка
- Конструкция рейсмусового станка
- Принцип работы рейсмусового станка
- Изготовление рейсмусового станка
- Наладка рейсмусового станка
Предназначение рейсмусового станка
Рейсмусовые станки предназначаются для плоскостного строгания заготовок — щитов, брусков и досок по толщине в заданный размер, поэтому и являются основными на деревообрабатывающих предприятиях. К тому же рейсмусы имеются практически у каждого столяра. Главное назначение рейсмусовых станков состоит в равномерном обслуживании досок и прочих деревянных изделий по всей площади и получении заготовок, что имеют равную толщину по всей ширине и длине.
Рейсмусы при использовании в строительстве за один проход способны обрабатывать в большом количестве широкие доски. В отличие от промышленных аппаратов, бытовые рейсмусы являются небольшими по размерам и намного легче, что облегчает их транспортировку. К тому же современные модели имеют облегченную систему смены рабочих ножей и увеличенный контроль глубины резания, чтобы точно выверивать толщину снимаемой стружки.
Как правило, перед проведением данной процедуры деревянные поверхности подвергают предварительной обработке на фуговальном станке. Для нестандартных разновидностей материала (полимеры, мягкие пластики, утеплители на вспененной основе) предназначаются рейсмусовые станки с обрезиненными металлическими подающими вальцами, которые не способны портить поверхности заготовок.
Секционные подающие вальцы, которыми оснащено деревообрабатывающее оборудование, позволяют на входе в станок одновременно подавать разнотолщинные заготовки. Рейсмусовый станок является одним из важных установок в плотницком деле и строительстве, а также в мебельной промышленности, позволяя изготовить точные планки для гарнитуров из древесины или рейки для обшивки кухни.
На самодельном рейсмусовом станке нельзя строгать очень тонкие заготовки, потому что возникают вибрации, что сказываются на качестве обрабатываемой поверхности. Наименьшая длина обрабатываемой заготовки должна на 100 миллиметров быть большей расстояния от переднего до заднего подающего валка. При возникновении необходимости фрезеровать более короткий материал, то его нужно надежно закреплять на основании. С помощью соответствующих приспособлений на рейсмусовых станках получится обработать даже клинообразные заготовки и выровнять непараллельные плоскости.
Глубина пропила показывает срез рейсмуса за один проход: этот показатель колеблется в пределах 1 — 3 миллиметров, зависимо от ширины материала. Ширина заготовки характеризует возможности обработки изделий, что имеют определенный размер: оптимальное решение – 30 — 330 миллиметров. На производительность работы влияет мощность станка. Для частных мастерских подходит рейсмусовый станок в 1,9 кВт. Аппараты, мощность которых выше 1,8 кВт, пригодятся для строгания твердых пород древесины – ели, бука, груши, вяза, ясеня.
Конструкция рейсмусового станка
Рейсмусовым станком называют специальное устройство, которое относится к категории деревообрабатывающих станков, которые успешно справляются с плоскостным, объемным и профильным фрезерованием прямо- и криволинейных заготовок, выполненных из массивного дерева.
По конструкции различают:
- Односторонние рейсмусовые станки, на которых производится строгание только с верхней стороны;
- Двухсторонние рейсмусовые станки, где строгаются одновременно две противоположные стороны – нижняя и верхняя;
- Специальные рейсмусы – трех-, четырех- и много-ножевые.
Наибольшее распространение получили односторонние рейсмусовые станки, которые являются более простыми по конструкции и соответственно в эксплуатации. Их устройство мы сегодня и будем рассматривать.
Стол рейсмусового станка в отличие от фуговального станка кроется из одной сплошной плиты, что точно выстрогана и отшлифована, а также он не имеет в своей конструкции направляющей линейки. Кроме горизонтального стола, на котором регулируется толщина снимаемого слоя, рейсмус состоит из таких основных элементов, как специальная фреза, что представлена несколькими отдельными ножами и системы автоматической подачи деревянной заготовки по роликовым направляющим.
Станина для рейсмусового станка чугунная, пустотелая, цельнолитая, на ней крепят все детали и механизмы станка. Опорным столиком может служить металлический уголок размерами 100 на 100 миллиметров и длиной не меньше 1000 миллиметров. Эта длина объясняется мерами безопасности. Опорный столик навешивают на технологические уголки станка, крепят с одной стороны болтами, с другой – струбцинами. По высоте стол можно перемещать по направляющим салазкам с помощью подъемного механизма.
Над столом размещен ножевой вал. Механизм подачи заготовки представлен двумя парами валиков. Первая из них располагается перед ножевым валом, другая — за валом. Нижние валики устанавливают точно под верхними. Вращаются верхние валики от электрического двигателя через зубчатую передачу, поэтому они называются приводными, питающими или подающими. Нижние валики устанавливаются свободно и приводятся во вращение подаваемым материалом. Эти валики – поддерживающие или направляющие. В двусторонних рейсмусовых станках ножевые валы располагаются в столе и над рабочим столом.
Назначение нижних валиков состоит в облегчении подачи на ножи материала, они выступают над поверхностью рабочего стола на 0,2—0,3 миллиметра. Строгаемый материал при более высоком расположении нижних вальцев вибрирует от ударов ножей, тонкий будет прогибаться, и строгание получится неровным. Передний верхний валик принято делать рифленым для лучшего сцепления с нестроганой поверхностью заготовки. Такой валик устанавливается на 2—3 миллиметра ниже поверхности материала, что подается на ножи.
Верхний задний валик необходимо делать гладким, потому что рифление способно портить строганную поверхность дерева. Размещают его ниже на 1 миллиметр режущих кромок ножей. Валики механизма подачи располагаются параллельно, поэтому в рейсмусовый станок одновременно можно подавать исключительно детали одинаковой толщины. Изделия меньшей толщины, даже на 2—3 миллиметра, дойдя до ножевого вала, получат сильный удар в торец ножом и вылетят обратно.
Для одновременного строгания пиломатериалов, что имеют разную толщину, в схему рейсмусового станка вводят рифленый валец секционный, что позволяет применять всю ширину станка и резко увеличивать его производительность. Состоит секционный валик из 12 рифленых колец, которые насажены на общую ось и соединены с ней пружинами. При прохождении под валиком изделия, толщина которого больше толщины других, что одновременно обрабатываются, секции, что надавливают на него, смещаются кверху и сохраняют сцепление с материалом под действием пружин.
Перед подобным рифленым валиком располагаются подвески, предназначение которых кроется в том, чтобы не допустить обратного вылета детали из станка. Сверху ножевой вал закрыт подъемным массивным колпаком, который служит надежным ограждением и является качественным приспособлением, что направляет стружку в воронку эксгаустера. Помимо этого, колпак совершает подпор волокон при строгании, нижняя его кромка для этого подведена к самым ножам.
Сменные ножи вы можете увеличить от двух до четырех. В качестве инструмента кроме фрезы можно применять гладкий барабан, что обтянут шлифовальной шкуркой. Выточить барабан получится из термостойкого пластика, алюминия или твердой древесины. Подходящие размеры: диаметр 80 миллиметров, длина 100 миллиметров. На одном из торцов делают проточку под гайку с шайбой. На боковой поверхности для прикрепления шкурки прорезан продольный паз, что имеет трапециевидную форму, под прижимную планку аналогичной формы. Просверливают в планке три отверстия для винтов с потайными головками.
Подача проводится верхними вальцами — задним гладким и передним рифленым. Два гладких вальца, которые свободно вращаются в подшипниках, способны уменьшать трение при движении по столу материала. Типовая максимальная ширина обрабатываемого изделия 315 — 1250 миллиметров, толщина — 5 — 160 миллиметров, диаметр ножевого вала 100 — 165 миллиметров, имеется на валу 2 — 4 ножа. Мощность электрического мотора достигает 1 — 44 кВт.
Чем быстрее будут вращаться валовые ножи, тем чище и ровнее получается поверхность заготовок после строгания. Выбирать для использования можно аппараты со скоростью вращения 6 — 10 тысяч оборотов в минуту. Вес, устройство рейсмусового станка, а также компактность рейсмуса характеризуют напрямую возможность перемещения оборудования. Компактные станки, что имеют вес 27 — 39 килограммов, являются самым хорошим выбором.
При определенном расстоянии рабочего стола от ножевого вала строгают заготовку в размер, который показан на шкале, укрепленной на станине станка. Прижимы устанавливают по двум сторонам ножевого вала, они способны предотвратить вибрацию заготовок. Стружколоматель, что расположен перед ножевым валом, способствует надламыванию стружки и заготовку прижимает к столу, образуя полость для накопления стружек вместе с прижимом.
Принцип работы рейсмусового станка
В принцип работы рейсмуса заложена методика плоского строгания доски. Главным рабочим инструментом у рейсмусового станка является ножевой вал. Заготовки для обработки подаются на горизонтальный рабочий стол вручную или вальцами, которые прижимают их к столу и тянут в область обработки. Материал строгается сверху ножами, и в результате получаются детали, абсолютно идентичные по размеру. Многие рейсмусовые станки имеют автоматическую систему подачи заготовок с определенной скоростью, чтобы аккуратно и точно снимать необходимый слой.
Можно приобрести односторонний или двусторонний рейсмус. У первых рейсмусовых станках присутствует один ножевой вал, в двусторонних есть ещё и дополнительный ножевой вал на рабочем столе. Перед обработкой деталей рейсмусом они должны быть уже подструганными в фуговальном станке. По конструкции, в принципе два станка очень схожи между собой. Зачастую двусторонний рейсмус и фуганку комбинируют в один механизм. Такое оборудование имеет два стола – для фуганка сверху и для рейсмуса снизу.
Обычно на рейсмусовом станке строгают заготовки длиной чуть больше расстояния, что сформировалось между подающими вальцами, как на видео о рейсмусовом станке. В случае использования подкладных шаблонов (цулаги) можно строгать на рейсмусовом станке заготовки (щиты, бруски, доски) с непараллельными противоположными гранями. Поверхность данного шаблона должна наклоняется таким способом, чтобы при процедуре горизонтального строгания изделий можно было получить нужную конусность.
В некоторых моделях рейсмусовых станков для удобства производителями увеличена длина стола. Поэтому брус или имеют значительную площадь опоры, а изделия обрабатываются точнее. Чтобы заготовка по столу оптимально скользила, в них делают специальные канавки, уменьшающие силу трения. Подобные модели раньше использовались преимущественно на производстве, а сегодня эти принципы широко внедряются и в бытовые рейсмусовые аппараты.
Одним из основных преимуществ рейсмусового станка выступает высокое качество обработанных поверхностей. Толщина получаемых деталей задается с помощью подъемного механизма, когда стол перемещается по отношению к ножевому валу вверх. Но стоит учитывать то, что при высокой скорости резания заготовок и большой глубине резания ухудшается качество обработанной поверхности. Поэтому чтобы добиться гладкой поверхности, необходимо делать финишные проходы при малой глубине и небольшой скорости вращения ножевого вала, если станком предусмотрена регулировка.
Рейсмусовый станок является одним из наиболее высокопроизводительных деревообрабатывающих станков. Стоит один раз настроить размеры обрабатываемой заготовки с помощью линейки и подъемника, и вся партия изделий будет одинаковой, в пределе допустимого показателя. На рейсмусовых станках вы можете обрабатывать детали с шириной до 1250 миллиметров и с толщиной 5 — 160 миллиметров, кроме специальных станков, предназначенных для определенных работ.
Изготовление рейсмусового станка
Все хозяева, которые сталкиваются с изготовлением строительной столярки, вагонки и мебели из древесины, пришли к выводу о необходимости иметь в своем пользовании хотя бы самый примитивный рейсмус. Без такой установки крайне сложно получить откалиброванные заготовки по толщине заготовки, кроме того процедура займет кучу времени. Не всем по карману купить оборудование промышленного изготовления, цены рейсмусовых станков «кусаются», поэтому умельцы приходят к решению своими руками изготовить установку.
Перед тем, как приступить к изготовлению рейсмусового станка, стоит изучить процесс использования и хранения рейсмуса. Миниатюрные станки много места не требуют. Конструкция должна располагаться таким способом, чтобы её получалось обойти вокруг для удобного произведения подачи материала. Подобную технику вы можете установить перед гаражом или домом: главное, чтобы поверхность под станком была ровной для избегания возникновения вибраций. Габариты рейсмуса зачастую не больше метра в ширину и толщину, поэтому оборудование легко сможет поместиться в сарае или гараже.
Для домашнего создания предлагается следующая конструкция. Рама и рабочий стол станка являются сварными, выполненными из уголка 50 на 50 миллиметров и квадратной трубы 40 на 40 миллиметров, можно использовать и материал больших размеров. Помните, что излишняя массивность только увеличивает устойчивость рейсмусового станка и уменьшает вибрации, возникающие при работе. Для изготовления станка необходимы: токарный и сверлильный станки, болгарка, сварочный аппарат и дрель.
Следующим обязательным элементом конструкции выступает ножевой вал. Его желательно приобрести готовым с буксами, потому что самодельные валы абсолютно не всегда являются хорошо сбалансированными. В варианте, что приведён нами, использовался трехсотмиллиметровый вал с тремя ножами. Шкивы двигателя и вала следует взять ступенчатые, для выбора оптимальных оборотов вала, в границах 4000-7000 оборотов в минуту.
Для подобного размера вала вполне подходит асинхронный мотор, что имеет мощность 4-5 кВт, нет надобности использовать шкивы большего размера, кроме того двигатель подобной мощности вполне запускается от одной фазы известными способами. Прижимные ролики рекомендуется выточить или использовать готовые из выжимки старых советских стиральных машин. Рама роликов – сварная, крепят её с одной стороны на подпружиненных болтах, с другой — для крепления используется кусок рулевой тяги от «Москвича». Опыт показывает, что неплохо два таких крепления применить на один ролик.
Стол согласно чертежу рейсмусового стола устанавливается на регулировочных болтах. Болты для избегания потребности регулировки каждого оснащены приваренными велосипедными звездочками, что соединены цепью. Пружины возьмите с клапанов мотора грузовика. К сожалению, в данном рейсмусовом станке предусмотрена ручная подача заготовок. В перспективе при наличии желания можно применить механическую.
До начала работы необходимо проверить правильность расположения ножей, а также остроту их заточки. Помните, что огражденным должен быть ножевой вал. Не допускается обработка заготовки длиной меньше расстояния между задними и передними валами. Запрещается чистить, ремонтировать и налаживать рейсмусовый станок на ходу.
Подавать заготовки необходимо торец в торец, используя при этом всю ширину стола. Помните, что материал после обработки не должен иметь вырывов, заколов, а также рисок. Ворсистость и мшистость получаются при обработке сырого материала или строгании тупыми ножами, непрострожка наблюдается при неплотном прижатии заготовки валиками к столу, неодинаковой толщине заготовки и неодинаковом выступе лезвий ножей из вала.
Наладка рейсмусового станка
Рейсмусовые станки перед работой должны быть тщательно налажены. Любая неточность наладки спровоцирует дефекты обработки или приведет к уменьшению производительности станка. Чаще всего наблюдаются такие упущения в наладке рейсмусов:
- Перекос на рабочем столе. Строгаемая поверхность не будет получаться параллельной фугованной стороне.
- Рифленый валик располагается очень низко и нажимает слишком сильно на поверхность деталей при малой глубине строгания. Строганные поверхности получаются с поперечными вмятинами.
- Нижние валики подачи размещаются над уровнем стола выше, чем нужно, на 0,1—0,2 миллиметра. Вследствие этого имеет место вибрация обрабатываемого изделия под ударами ножей, а более тонкие детали прогибаются. Строгание выходит непрямолинейным и не таким гладким, концы изделий больше прострагиваются.
- Задняя нажимная колодка на обрабатываемую деталь давит. По этой причине изделие при выходе из передних подающих валиков благодаря уменьшению силы подачи останавливается.
Так как ножи будут продолжать вращаться, строгается на поверхности детали одно место, и в итоге здесь возникает во всю ширину строгания желобок.Вообще желобки формируются при всякой, даже наиболее короткой остановке изделия. Остановки часто случаются во время, когда детали поступают в задние валики. Это случается при очень низком размещении верхнего заднего валика и при его слишком большом нажиме на материал. Причинами кратковременной задержки или остановки детали бывает также недостаточный нажим на изделие подающих валиков, чрезмерно высокое расположение нижних валиков, сильное загрязнение стола при обработке сосновых деталей смолой.
- Стружка попадает под задний гладкий валик из-за неправильного монтажа накидного козырька или неисправностей эксгаустера. По этим причинам на строганной поверхности возникают вмятины, иногда задержка детали.
Поэтому при наладке рейсмусового станка следует помнить, что при значительном заполнении стола, к примеру, при строгании широкого щи¬та или одновременной подаче изделий во всю ширину рабочего стола, повышенным должно быть давление подающих вальцов, потому что в этих случаях сопротивление резанию сильно увеличивается. При строгании узких деталей или при небольшом заполнении стола нужно уменьшить давление подающих вальцов, чтобы избежать смятия дерева.
К наиболее распространенным в деревообрабатывающем деле относятся фуговальные, фрезерные, строгальные и рейсмусовые станки, которые предназначаются для плоскостного, объемного и профильного фрезерования прямо- и криволинейных заготовок из массивного дерева и древесных материалов, для нарезания проушин и шипов в брусках дверных коробок и оконных блоков. Если вы планируете заниматься только плоскостным строганием, то вам стоит отдать предпочтение рейсмусу. Вы можете приобрести этот станок в торговой точке или собрать своими руками, используя информацию, представленную на нашем сайте, и нашу пошаговую инструкцию.
Станок рейсмус деревообрабатывающий MB108F — Станкофф.RU
Назначение
Станок предназначен для плоскостного строгания досок, брусков, щитов шириной до 800 мм в заданный размер по толщине.
Рейсмусовые станки «MB108F» в течение многих лет зарекомендовали себя как надежное и удобное в эксплуатации оборудование
Схема обработки
Конструктивные особенности
Литые подшипниковые опоры |
|
Клиноременная передача |
|
Ножевой вал |
|
Единый приводной двигатель |
|
Вальцы подающего стола |
|
Секционные подающие и прижимные вальцы |
|
Механизм подъема стола |
Страна изготовления: Китай
Технические характеристики рейсмусового станка MB108F | |
Максимальная ширина обрабатываемой детали | 800 |
Максимальная толщина обрабатываемой детали | 200 |
Минимальная толщина обрабатываемой детали | 8 |
Минимальная длина обрабатываемой детали | 240 |
Скорость вращения вала строгального ножа, об/мин | 5000 |
Толщина снимаемого слоя, мм | До 4 |
Скорость подачи материала, м/мин | 7-10 |
Мощность электродвигателя, кВт | 7,5 |
Габариты (Д х Ш х В), мм | 1000х760х1105 |
Масса, кг | 620 |
Отзывы о Станке рейсмус деревообрабатывающий MB108F
Пока нет отзывов на данный товар.
Оставить свой отзыв
Ваш отзыв поможет другим людям сделать выбор. Спасибо, что делитесь опытом!
В отзывах запрещено:
Использовать нецензурные выражения, оскорбления и угрозы;
Публиковать адреса, телефоны и ссылки содержащие прямую рекламу;
Писать отвлеченные от темы и бессмысленные комментарии.
Информация не касающаяся товара будет удалена.
Макита-2012 Станок рейсмусовый (рейсмус). Паспорт, схемы, описание, характеристики
Сведения о производителе рейсмусового станка Макита-2012
Поставщиком рейсмусового деревообрабатывающего станка Макита-2012 является Компания Makita Corporation. Адрес сайта: http://www.makita.biz
Компания Makita была основана в 1915 году господином Масабуро Макита в японском городе Нагоя. В первые годы компания занималась продажей и ремонтом электромоторов и трансформаторов. В 1935г. компания начала экспортировать электромоторы и генераторы в Россию.
Корпорация Makita включает в себя 8 производственных предприятий, из которых два расположены в Европе: в Великобритании и Германии.
Представительство компании Makita в России — ООО Макита г. Москва уже более 15 лет занимается продажей профессионального электроинструмента в Москве и по всей России. Адрес сайта: http://makita.ru
Станки, выпускаемые компанией Makita
Макита-2012 Станок рейсмусовый переносной электрический. Назначение, область применения
Деревообрабатывающий рейсмусовый станок Макита-2012 предназначен для строгания заготовок из древесины в предварительно заданные размеры. Станок Makita 2012 предназначен для индивидуальной эксплуатации и не рассчитан на работу при непрерывном производстве.
Легкий и компактный рейсмусовый станок Макита-2012 предназначен для индивидуального использования в столярных мастерских и «на выезде» в условиях стройки. Благодаря коллекторному мотору он весит всего 27 кг, обладая при этом мощностью 1,65 кВт. Двигатели этого типа требовательны к соблюдению температурного режима, поэтому Makita 2012 оснащен датчиком перегрева, отключающим питание, когда нужен перерыв на охлаждение.
Станок рейсмусовый Макита-2012NB
Рейсмусовыйстанок Макита-2012NB заменил более раннюю устаревшую модель Макита-2012.
Основные отличие станка Макита-2012NB от Макита-2012:
- Мощность двигателя — 1,65 кВт вместо 1,33 кВт
- Скорость вращения ножевого вала — 8500 вместо 8000 об/мин
- Максимально возможная глубина строгания — 3,0 мм вместо 2,5 мм
Кроме того, станок Макита-2012NB имеет более жесткую конструкцию силового каркаса и двойную изоляцию электрических цепей.
Обладая высокой производительностью, станок весит 27 кг и остается мобильным: его можно взять на стройку или в одиночку перемещать по мастерской. Предусмотрена установка на пол (открытая подставка входит в стандартную комплектацию) или на верстак. При эксплуатации станка следует учитывать, что точная и безотказная работа возможна только при качественном стружкоудалении, например, с помощью вытяжных установок.
На станках не допускается обработка металлов, асбоцементных материалов, камня и подобных материалов, мягких пластмассовых и резиноподобных материалов.
По качеству строгания станок не уступает стационарным моделям начального уровня, напротив, высокая скорость вращения ножевого вала делает его в ряде случаев более предпочтительным. Есть все стандартные системы, характерные и для стационарных аналогов: механизм автоподачи, подающий и разгрузочный столы с роликами (для удобства транспортировки и хранения они сделаны складными), ролики сверху корпуса для обратной подачи заготовки. Регулировку высоты ножевого вала, в зависимости от размера детали, производят единственной вращающейся рукояткой.
Накопленный опыт эксплуатации Макита-2012 показал, что при соблюдении всего нескольких простых правил станок очень долговечен и надежен. Требуется лишь избегать работы без подключения к пылеотсосу и вовремя прочищать все механизмы от стружки.
Станок работает от однофазной сети переменного тока напряжением 220 В частотой 50 Гц.
Станок может эксплуатироваться в нормальных климатических условиях:
- температура окружающей среды от 1 до 35 °C
- относительная влажность воздуха до 80 % при температуре 25 °C
Комплект поставки рейсмусового станка Макита-2012NB
- Два магнитных держателя (для замены лезвий станка)
- Торцовый ключ на 9
- Шестигранный ключ
- Сменные не затачиваемые лезвия
- Съёмный пенал для принадлежностей
Дополнительные принадлежности рейсмусового станка Макита-2012NB
- Прижимные планки перезатачиваемых лезвий
- Перезатачиваемые лезвия
- Ключ
- Комплект столов для сопряжения станка со станком Mod. 410
Макита-2012NB Общий вид рейсмусового станка
Фото рейсмуса Макита-2012NB
Макита 2012 фото станка рейсмусового. Смотреть в увеличенном масштабе
Фото рейсмуса Макита-2012NB
Макита 2012 фото станка рейсмусового. Смотреть в увеличенном масштабе
Макита-2012NB Строгальный узел рейсмусового станка
Строгальный узел рейсмусового станка Макита-2012NB
Основные конструктивные особенности рейсмуса 2012NB
Основные конструктивные особенности рейсмуса Макита-2012NB
Основные конструктивные особенности рейсмуса 2012NB. Смотреть в увеличенном масштабе
- Компактные размеры и небольшой вес 27 кг облегчают транспортировку автоматического рейсмусового станка
- Рабочая головка с резцами приводится в действие двигателем мощностью 1,650 кВт, который, несмотря на свою мощность, обладает низкими шумовыми характеристиками (83 дБ)
- Для большей стабильности и чистоты обработки строгальный узел расположен на четырёх опорах
- Уникальный механизм подачи заготовок обеспечивает высокое качество обрабатываемой поверхности и делает работу более безопасной
- Высокая скорость вращения ножевого вала обеспечивает качественную поверхность после обработки
- Для регулировки высоты строгания поднимается и опускается строгальный узел, содержащий электродвигатель, ножевой вал и подающие валы
- Регулировка высоты строгания вращающейся рукояткой
- Наличие системы отключения двигателя при перегрузке
- Наличие откидных роликовых подающего и разгрузочного столов
- Станок имеет массивное основание для надёжной установки на рабочий стол
- Встроенный стопор работает от минимальной толщины детали 3 мм до максимальной толщины детали 155 мм
- Автоматический рейсмусовый станок имеет уникальную двойную электроизоляцию и оснащён лампой, которая сигнализирует о готовности станка к работе
- Имеется встроенный съёмный пенал для принадлежностей
Монтаж натяжителя цепи привода прижимных валов станка Макита-2012
Монтаж натяжителя цепи привода прижимных валов станка Макита-2012
- Установите цепь на звездочки
- Временно закрепите торсионную пружину 9 винтом, предварительно подтянув её короткую часть за ребро
- Удерживая длинную сторону пружины 9 щипцами, подожмите ею цепь
- Окончательно затяните винт торсионной пружины 9
- Затяните торцевым ключом болты с шестигранными головками, которые крепят звёздочки
Снятие моторного модуля с рейсмуса Макита 2012
Снятие моторного модуля с рейсмуса Макита 2012
- Поворотом ручки регулировки глубины поднимите главную раму в самую высокую точку
- Снимите боковую крышку, цепь и клиновидный ремень
- Моторный отсек крепится к главной раме 4 винтами.
Два самонарезающих винта 5 х 30 расположены со стороны V ролика. Два самонарезающих стяжных винта 4 х 25 расположены со стороны выключателя. Для работы с винтами потребуется короткая отвёртка. Обратите внимание. Эти винты должны попасть при сборке в те же самые отверстия.
- Вращая ручку регулировки глубины опустите главную раму в самую низкую точку и снимите моторный отсек.
- Открутите саморезы и снимите сначала крышку блока управления (самонарезающий винт для пластика 4 х 18 штуки), а затем и сам блок управления (самонарезающий стяжной винт для алюминия СТ 4 Х 12 2 штуки). Обратите внимание. Эти винты должны попасть при сборке в те же самые отверстия.
Установка моторного модуля рейсмуса Макита 2012
Установка моторного модуля рейсмуса Макита 2012
- Моторный модуль (состоящий из корпуса двигателя, редуктора и крышки редуктора) должен быть установлен так, чтобы его нижняя поверхность была строго параллельна основанию главной рамы.
- При сборке не забудьте установить на ведущий вал плоскую шайбу 14 (смотри рисунок 4).
Макита 2012 Схема сборки рейсмусового станка
Схема сборки рейсмусового станка Макита 2012
Схема сборки рейсмусового станка Макита-2012. Смотреть в увеличенном масштабе
Схема сборки рейсмусового станка Макита 2012
Макита-2012NB Схема сборки рейсмусового станка
Схема сборки рейсмусового станка Макита 2012
Схема сборки рейсмусового станка Макита 2012
Пояснения к рисункам станка Макита-2012NB
- Adjusting screw — регулировочный винт
- Belt cover — крышка ремня
- Blade guage — измерительное устройство для ножа
- Bolt — болт
- Brush holder cap — крышка щеткодержателя
- Cap — резиновый колпачок
- Chain — цепь
- Chip cover — защитный кожух
- Clan of magnetic holder — прорезь магнитного держателя
- Depth gauge — шкала глубиномера.
- Drum — барабан
- Elevating handle — ручка подъема
- Groove — паз
- Handle securing screw — ручка блокировки
- Heel of set plate — пятка установочной пластины
- Hex bolt — шестигранный болт
- Hex nut — шестигранная гайка
- Hex wrench — шестигранный ключ
- Hood — крышка с пылеотводным отверстием
- Indicator platе — пластина указателя
- Leg — ножка
- Limit mark — ограничительная метка
- Lock plate — запорная пластина
- Lug — выступ
- Magnetic holder — магнитный держатель
- OFF — ВЫКЛ
- ON — ВКЛ
- Planer blade — нож рубанка
- Post card — открытка
- Pulley — блок
- Push — толкай
- Ruler — линейка
- Scale label — шкала
- Screw — винт
- Screwdriver — отвертка
- Set plate — установочная пластина
- Socket wrench — торцевой ключ
- Spring washer — пружинная шайба
- Stand — станина
- Stay (A) — кронштейн А
- Stay (B) — кронштейн В
- Sub-table — подставка
- Wing bolt — болт-«барашек»
- Wood block — деревянный блок
- Workpiece — заготовка
Макита-2012NB Станок деревообрабатывающий рейсмусовый.

Технические характеристики рейсмусового станка Макита-2012NB
Наименование параметра | JWP-12 | Макита-2012NB |
---|---|---|
Строгание в размер — рейсмус. Основные параметры | ||
Максимальная ширина строгания, мм | 318 | 304 |
Диапазон толщины обрабатываемых заготовок, мм | 6.![]() | 3..155 |
Скорость механической подачи заготовки, м/мин | 7 | 8,5 |
Минимальная длина обрабатываемой заготовки, мм | 250 | |
Максимальная глубина строгания при ширине строгания 3..150 мм, мм | 2,5 | 3,0 |
Максимальная глубина строгания при ширине строгания 150..240 мм, мм | 1,5 | |
Максимальная глубина строгания при ширине строгания 240..304 мм, мм | 1,0 | |
Частота вращения строгального вала (на холостом ходу), об/мин. | 9000 | 8500 |
Количество строгальных ножей на строгальном валу | 2 | 2 |
Диаметр строгального вала, мм | 48 | |
Размер ножа: Длина, ширина, толщина, мм | 319 х 18 х 3 | |
Длина рейсмусового стола (с удлинителями), мм | 690 | 771 |
Электрооборудование станка | ||
Род тока питающей сети | 220В 50Гц | 220В 50Гц |
Количество электродвигателей на станке, шт | 1 | 1 |
Электродвигатель — номинальная мощность, кВт | 1,8 | 1,65 |
Рабочий ток, А | 8 | 8 |
Тип электродвигателя | Коллекторный | Коллекторный |
Плавкий предохранитель, А | 16 | |
Соединительный провод | 3 x 1мм² | 3 x 1мм² |
Габарит и масса станка | ||
Габарит станка (длина х ширина х высота), мм | 580 х 560 х 463 | 483 х 771 х 401 |
Масса станка, кг | 27 | 27 |
Полезные ссылки по теме. Дополнительная информация
Каталог справочник деревообрабатывающих станков
Паспорта деревообрабатывающих станков
Купить каталог — Купить справочник — Купить базу данных: Прайс-лист информационных изданий
Рейсмус (рейсмусовый станок) JWP-2510 шириной 635 мм со строгальным валом helical
Скачать инструкцию JWP-2510
Станок рейсмус предназначен для плоского фрезерования (простругивания) досок, брусьев или щитов из древесины в размер по толщине. Станок имеет один ножевой вал, которым осуществляется рейсмусование (калибрование) заготовок. Именно ножевой вал этого рейсмуса существенно отличает его от аналогичных станков европейских производителей. Вместо четырёх плоских ножей, как в классическом рейсмусе, в станке JWP-2510 на вал установлено 174 режущих элемента, заточенных с четырёх сторон, размером 15х15х2,5 мм. Разделением длины ножа на короткие участки – элементы – и смещением их режущих кромок путём поворота относительно друг друга на некоторый угол получают ступенчатый вал. При таком расположении режущих элементов сила резания по всей ширине заготовки распределяется на части тех секций, которые участвуют в резании. При узких секциях величина мгновенной силы резания снижается в несколько раз. Также снижается необходимая мощность привода резания и подачи. Когда видишь строганную поверхность после прохода детали через этот рейсмус, понимаешь всю прелесть конструкции ножевого вала helical.
Особенности станка JWP2510
- Строгальный вал со спирально расположенными 174 четырехгранными элементами не требует регулировки после смены ножей;
- Низкошумный двигатель;
- Встроенная система цифровой индикации и управления обеспечивают легкую регулировку стола по высоте, 10 программируемых положений;
- Сегментный вал с подпружиненными валами для движения заготовки позволяет обрабатывать неравномерные по высоте заготовки;
- Каждый сегмент ножевого вала может выбирать до 4 мм;
- Выходной и подающий валы диаметром 76 мм имеют четыре закрытых подшипника, не требующих технического обслуживания;
- Быстро регулируемая маленькая ручка позволяет легко отрегулировать ролики стола от 0 до 1 мм;
- Прочная чугунная конструкция обеспечивает устойчивость станка, минимальные вибрации и точность обработки;
- 3 скорости подачи позволяют правильно подобрать скорость движения заготовки;
- Встроенные ролики снижают трение;
- 2 стальных выходных вала для движения заготовки;
- Вытяжной штуцер диаметр 127 мм (150 мм).
Строгальный вал со спиральным расположением режущих насадок и стружколоматель. Цифровая индикация для регулировки стола по высоте и необходимой толщины съема поверхности. Пластинчатая гребенка и сегментный ребристый вал подачи заготовки.
Стандартное исполнение
- 10 запасных четырехгранных ножевых вставки;
- 10 винтов под звездообразный ключ;
- 2 звездообразные отвертки;
- Адаптер для вытяжного штуцера Ø 150 / Ø 127 мм;
- 4 опоры по сторонам;
- Инструмент для обслуживания;
Принадлежности
1791212 четырехгранные ножевые вставки (набор из 10 шт.)
709207 роликовая подставка
Технические характеристики рейсмуса JET:
|
Строгальный вал со спиральным расположением режущих элементов «helical»
Многие специалисты по деревообработке знают, что строгание лезвием, расположенным под наклоном к поверхности лучше, чем вертикальный заход строгального ножа.![]() Если вал попал в заготовке на твердый сучок или гвоздь, Вам не придется менять строгальные ножи целиком, можно заменить только поврежденные сегменты ножа и возвратиться к работе. Секрет успеха заключается в том, что новый строгальный вал JET имеет правильную, очень оптимально подобранную спиралевидную форму (Helix). Он работает в 20 раз дольше, чем обычный строгальный вал.
|
При таком исполнении вала режущие элементы (ножи) работают во много раз дольше, их можно переставить четыре раза режущими гранями. Они легко и быстро заменяются. Во время работы станка существенно меньше уровень шума и треска при прохождении заготовки.
Подающий вал движения детали сделан не цельным рифлёным, а отдельными секциями. Каждая секция обеспечивает прижим детали к столу с помощью спиральных пружин внутри. Это позволяет производить одновременную обработку нескольких заготовок с неравномерностью по толщине до 3 мм. Прижим подающего вала и двух вальцов на выходе заготовки из станка должен быть достаточным, но не слишком большим, чтобы не создать смятие поверхности или перекос сечения заготовки. Регулирование прижима валов движения заготовки на данном станке выполняется очень легко, путём закручивания или раскручивания гайки на оси, где установлена спиральная пружина, с обеих сторон валов, которая создаёт необходимое давление прижима.
Кинематическая схема, характерная для американских станков, сделана с большим запасом прочности, а электродвигатель мощнее, чем у всех европейских рейсмусов. Конечно, этот станок делался для обработки тех пород дерева с высокой плотностью, которые произрастают в Америке.
Подъём массивного чугунного стола шириной 635 мм производится кнопками на пульте и набором установки размеров на клавиатуре дисплея с точностью до сотых миллиметра.
Есть и ручной штурвал. В случае необходимости всегда можно поднять или опустить стол. Станок имеет ещё различные конструктивные особенности, что серьёзно улучшает качество рейсмусования.
Рейсмус Makita 2012 NB
Технические характеристики Makita 2012NB
- Мощность, Вт:1650
- Частота холостого хода, об/мин:8500
- Скорость подачи, м/мин.:8.5
- Ширина строгания, мм:304
- Глубина строгания, мм:3
- Длина, мм:483
- Высота, мм:771
- Ширина, мм:401
- Сетевой шнур, м:2.
5
- Вес, кг:28
- Ширина базы, мм:304
- Длина базы, мм:771
- Двойная изоляция:есть
- Напряжение питания, В:220
Технические данные могут отличаться в зависимости от экспортного исполнения. Возможны конструктивные и технологические модификации инструмента и оснастки.
Описание рейсмуса Makita 2012NB
Станок рейсмусовый, он же электрорубанок производства makita предназначен для обработки деревянных заготовок (брусков). Этот малогабаритный инструмент подходит для профессионального использования, так как рассчитан на работу в течение 8-часового рабочего дня.
Преимущества
- Рейсмусы макита отличаются удобством транспортировки и эксплуатации. Кнопки и рычаги управления интуитивно понятны. Хорошие показатели эргономичности.
- Рабочая поверхность (304х771 мм) позволяет строгать заготовки шириной до 304 мм. При этом через рейсмус можно одновременно пропускать несколько узких деталей одинаковой толщины.
- Крепление станка производится к верстаку при помощи специальных крепежных болтов.
4-опорная конструкция и диагональная крестовина обеспечивают устойчивость станка и стабильность обработки.
- Для включения и выключения станка используется большая педаль
- Уникальный механизм подачи заготовок обеспечивает гладкую листовую обработку с минимальной потерей материала
- Для фиксации глубины обработки предусмотрен специальный ограничитель
- Замена режущего лезвия отличается легкостью и быстротой. В конструкции станка предусмотрено использование восстанавливаемого двустороннего лезвия.
- Рейсмус Makita 2012NB является самым тихим станком в своем классе и по уровню шума не превышает 83 дБ.
- Безопасность работы со станком обеспечивается системой регулировок и рядом технических приспособлений
Профессиональный электрорубанок для получения чистовых поверхностей заготовок шириной до 304 мм. Идеальная повторяемость толщины при серийной обработке.
В столярном деле рейсмусом раньше называли совсем иной инструмент, но с современным рейсмусовым станком у него всё-таки есть что-то общее. Это – обеспечение точности параметра деталей из дерева, связанного с параллельностью. Агрегат Makita 2012NB предназначен не просто для деревообработки, но для её конечной, чистовой стадии. Через этот прецизионный электрорубанок можно прогонять заготовки шириной в 30,4 см, м он будет надёжно, без задиров, снимать с них стружку толщиной до 3 мм.
Весит рейсмус Makita 2012NB 28 кг и занимает в плане площадь в 48,3х40,1 см. Длина базы, на которой устанавливается заготовка, составляет 77 см, а компоновка агрегата позволяет заправлять в него детали различной длины и ширины. Можно даже пакетом рядом лежащих узких брусков.
Электродвигатель мощностью в 1,65 кВт работает на скорости 8,5 тыс. об/мин, а скорость подачи заготовки составляет 8,5 м/мин. Однако, главным у описываемого инструмента является всё-таки не энергетика, а конструкторские решения, которые применили в нём японские разработчики.
Прежде всего, это касается устойчивости рейсмусового станка Makita 2012NB. Конструкция имеет крестообразную диагональную станину и четыре опоры, что практически исключает какие-либо механические перемещения, недопустимые при чистовой обработке материала. Крепление к рабочему столу – болтовое, а оригинальный механизм подачи в сочетании с конструкцией ножа позволяет получить чуть ли не зеркальную поверхность получаемой детали.
Управление включением у рейсмуса Makita 2012NB традиционное для этого класса оборудования – с помощью педали. Гораздо интересней придумана на этом агрегате замена ножа – операция проводится исключительно легко. Кстати, нож у электрорубанка – восстанавливаемый, двухсторонний. Для профессионального инструмента важнейшее значение имеет воспроизводимость точности операций при серийной обработке. Пользователи рейсмуса отмечают в этой связи его важное отличие от аналогов – у агрегата Makita 2012NB фиксированный упор глубины обеспечивает идеальную повторяемость толщины получаемых деталей. Глубина строгания у инструмента, разумеется, регулируется, для этого имеется специальный глубиномер.
Ещё одна особенность рейсмусового станка Makita 2012NB, выделяющая его из ряда аналогов – это уникально низкий уровень шума. Это тоже важно для профессионального инструмента – ведь он рассчитан на эксплуатацию в течении всего рабочего дня. Пользоваться описанным агрегатом несложно (всё подробно расписано в инструкции), а техобслуживание рейсмуса сводится к замене угольных щёток при износе до метки, смазке механизма привода и заточке затупившихся ножей.
Они имеются в комплекте поставки рейсмуса Makita 2012NB, как и вся необходимая оснастка для его использования. Это гаечный и шестигранный ключи, а также пара магнитных держателей. Кстати, именно они и обеспечивают отмеченную выше лёгкость замены лезвий в этом агрегате.
Комплектация Макита 2012NB
- рейсмус
- нож для рубанка
- держатель магнитный (2 шт.)
- шестигранный ключ
- гаечный ключ
- коробка
Для хранения инструментов предусмотрен специальный отсоединяемый ящик.
В устройстве рейсмуса предусмотрена возможность установки пылесборника (в комплектацию не входит).
*Возможно изменение комплектации и внешнего вида станка компанией-производителем Makita!
Расходные материалы Makita 2012 NB
Ножи и лезвия для рейсмуса
Как работают ультразвуковые толщиномеры неразрушающего контроля?
Как работают ультразвуковые толщиномеры неразрушающего контроля?
youtube.com/embed/hkAl5rVddgw?rel=0″ frameborder=»0″>
Ультразвуковые толщиномеры, способные неразрушающим образом измерять широкий спектр материалов, когда доступна только одна сторона, идеально подходят, в частности, для контроля коррозии и эрозии или проверки на наличие дефектов в сложных, изготовленных компонентах.
ультразвуковые датчики неразрушающего контроля, такие как датчики толщины материала Elcometer MTG и прецизионные толщиномеры Elcometer PTG; предназначены для точного и надежного измерения толщины материала в широком диапазоне применений, включая, например, трубопроводы, резервуары для хранения, резиновые футеровки или тонкие пластиковые бутылки.
Итак, как они работают?
Ультразвуковые измерители толщины материалов Elcometer MTG могут измерять как материалы без покрытия толщиной до 500 мм, так и материалы с покрытием толщиной до 25 мм. Для этого они используют двухэлементный преобразователь.
Двухэлементные преобразователи состоят из двух независимых кристаллов, разделенных акустическим барьером. Два элемента расположены под углом, так что, когда один кристалл излучает ультразвуковой импульс, путь энергии создает V-образную форму, проникая в материал через ультразвуковой контакт, ударяясь о заднюю стенку материала и отражаясь эхом в направлении другого кристалла, где он обнаружен.Затем датчик использует скорость импульса и время, необходимое для прохождения от одного кристалла до другого (от импульса до эха), для расчета толщины материала — с акустическим барьером, предотвращающим любой звук, достигающий приемника непосредственно от излучателя. , прежде чем импульс завершит свой путь.
Когда дело доходит до измерения материалов с покрытием, чтобы игнорировать толщину покрытия и измерять только толщину материала под ним, датчик настраивается на измерение времени между двумя эхосигналами.Первое эхо возникает, когда импульс сначала попадает на заднюю стенку материала, а второе эхо возникает, когда импульс в следующий раз попадает в заднюю стенку материала во второй раз. Преобразователь обнаруживает оба этих эхосигнала и использует скорость импульса и время между эхосигналами для вычисления толщины материала, игнорируя покрытие над ним и любое другое эхо.
В качестве альтернативы в линейке прецизионных ультразвуковых толщиномеров Elcometer PTG используются одноэлементные преобразователи для измерения непокрытых материалов толщиной до 0.15мм.
Одноэлементные преобразователи, как следует из названия, состоят из одного кристалла, который излучает и принимает ультразвуковой импульс. Импульс снова проходит между датчиком и материалом через ультразвуковой контакт.
Однако измерение тонких материалов означает, что ультразвуковой сигнал вернется на преобразователь невероятно быстро, и в результате не всегда бывает достаточно времени между импульсом, покидающим элемент, и возвращением эхо-сигнала.Вот почему при использовании Elcometer PTG одноэлементные преобразователи используют линию задержки для увеличения времени между отправкой импульса и получением эхо-сигнала, обеспечивая более точные результаты.
Хотя путь энергии от одноэлементного преобразователя все еще проходит от импульса к эхо-сигналу, чтобы убрать длину линии задержки из измерений и измерить только толщину материала, датчик не отсчитывает время от импульса к эхо-сигналу. . Вместо этого Elcometer PTG измеряет от интерфейса до интерфейса эхо-сигнала, когда импульс проходит между линией задержки и материалом; и эхо, когда импульс ударяется о заднюю стенку материала и возвращается к элементу.Затраченное время, наряду с известной скоростью импульса, позволяет измерителю не учитывать длину линии задержки и измерять только толщину материала.
Для точного и надежного измерения невероятно тонких материалов толщиной всего 0,15 мм Elcometer PTG настроен на измерение между двумя эхосигналами. Пока датчик все еще считывает интерфейс, точку, в которой импульс проходит между линией задержки и материалом, чтобы снова удалить линию задержки из измерения; датчик показывает только время между двумя последующими эхо-сигналами. Первый из них возникает, когда импульс сначала попадает на заднюю стенку материала, второй, когда импульс снова попадает в заднюю стенку материала. Время между этими двумя последовательными эхо-сигналами и скорость импульса гарантирует, что Elcometer PTG может измерять невероятно тонкие материалы с максимальной точностью.
Щелкните здесь, чтобы загрузить сценарий на английском языке
Все о толщиномерах — определение, размеры и использование
Цифровой (электронный) измеритель толщины материалаИзображение предоставлено: nattanan726image / Shutterstock.ком
Толщиномеры — это измерительные приборы, которые можно использовать для определения толщины или толщины материала. На самом деле существует несколько различных типов толщиномеров, каждый из которых работает по-своему, в зависимости от предполагаемого применения толщиномера. В этой статье будут обсуждаться распространенные типы толщиномеров и их использование, а также представлена информация о спецификациях, связанных с этими типами устройств.
Чтобы узнать больше о других разновидностях манометров, см. Соответствующее руководство по типам манометров.
Типы толщиномеров
Термин толщиномер имеет несколько возможных значений и может относиться к одному из следующих основных типов:
- Толщиномеры материала
- Толщиномеры покрытия
- Толщиномеры для проволоки и листового металла
Первый из этих датчиков измеряет толщину материала механическими средствами — откалиброванный инструмент замыкается вокруг образца до тех пор, пока не произойдет контакт с обеими сторонами материала — процесс, похожий на микрометрический.В данной статье эти датчики будут называться датчиками толщины материала.
Второй тип толщиномера предназначен для измерения толщины покрытий, нанесенных на поверхность — они известны как толщиномеры покрытий.
Третий тип толщиномера представляет собой более простое механическое устройство, которое используется для измерения толщины проволоки и листового металла.
Некоторые характеристики толщиномеров могут включать в себя такие инструменты, как щупы или калибры зазора.Эти устройства больше связаны с измерением зазора или зазора между двумя поверхностями, а не с толщиной материала или нанесенного покрытия. Как таковые, они не рассматриваются в этой статье. Для получения дополнительной информации об этих инструментах см. Соответствующее руководство «Все о щупах».
Толщиномеры
В случаях, когда есть доступ к обеим сторонам материала, толщина которого измеряется, может использоваться толщиномер материала. Эти измерительные приборы доступны в нескольких вариантах, в том числе:
- Аналоговые (механические) толщиномеры
- Цифровые (электронные) толщиномеры
- Карманные толщиномеры
Толщиномеры аналоговые (механические)
Аналоговые толщиномеры имеют губку со стальными контактными штифтами, рукояткой и рычагом.Когда рычаг отпускается после того, как материал вставлен между контактными штифтами, штифты смыкаются с поверхностью материала, и измеренное значение толщины записывается на аналоговом циферблате по положению иглы на градуированной шкале на лицевой стороне циферблата. Подход, при котором штифты закрываются при отпускании рычага, обеспечивает точность и согласованность показаний, поскольку прибор прикладывает равномерное измерительное давление к поверхности материала, которое будет одинаковым от пользователя к пользователю.
Кромки контактных измерительных штифтов часто имеют закругленную форму, чтобы прижатие штифтов к поверхности материала не повредило или не оставило следов на поверхности.
Цифровые (электронные) толщиномеры
Электронный (цифровой) толщиномер работает так же, как аналоговый толщиномер, но заменяет стрелочный дисплей цифровым дисплеем. Значение толщины можно непосредственно просмотреть на цифровом индикаторе без необходимости интерпретировать измерение, исходя из положения иглы по шкале на лицевой стороне циферблата.
Карманные толщиномеры
Меньшие версии аналоговых и цифровых толщиномеров известны как карманные толщиномеры или карманные толщиномеры с круговой шкалой. Вместо того, чтобы работать с манометром всей рукой, пользователь держит инструмент между большим и указательным пальцами. Эти устройства предназначены для быстрой проверки толщины материалов, таких как бумага, пленка или другие типы плоского материала. Карманные толщиномеры доступны либо с аналоговыми (циферблат и стрелка), либо с электронными (цифровыми) дисплеями.
Размеры и характеристики
Размеры и технические характеристики толщиномеров приведены ниже. Обратите внимание, что технические характеристики могут отличаться в зависимости от типа рассматриваемого измерителя толщины с круговой шкалой. Параметры, показанные ниже, предназначены для того, чтобы дать общее представление о том, что следует искать и учитывать при поиске толщиномера с круговой шкалой. Размер толщиномера может относиться к диапазону толщиномера, но другие параметры, такие как радиус действия, также являются относительным показателем размера.
- Тип дисплея — для аналоговых приборов используется механический индикатор часового типа. Для цифровых (электронных) датчиков обычно используются ЖК-дисплеи или светодиоды.
- Контактный тип (опора и шпиндель) — типичные контактные штифты выполнены из плоской стали, поверхности которой параллельны друг другу, с закругленным краем. Некоторые имеют округлую форму, а другие имеют форму лезвия. Другие материалы включают керамические поверхности для более длительного ношения.
- Диаметр контакта — измеряет диаметр контактного штифта.
- Диапазон толщиномера — указывает диапазон значений, для которых датчик может обеспечить показание толщины материала, например, от 0 до 0,0500 дюйма.
- Вылет датчика — (также называемый глубиной горловины или горловины), это значение является показателем расстояния, на которое датчик может быть вставлен от края материала до того, как край материала коснется задней части рамы. Глубина горловины может быть долей дюйма или может быть намного больше, например, 12 дюймов или 16 дюймов. Когда горловина толщиномера увеличивается до больших значений, прочность рамы должна увеличиваться, чтобы избежать деформации рамы из-за ее веса, вызывающей проблемы с точностью измерений толщины.
- Горловой зазор — есть также модели, которые больше похожи на суппорты, называемые измерителями толщины суппорта. Для них зазор в горловине — это максимальное расстояние, когда челюсти устройства открыты
- Разрешающая способность — показатель степени зернистости или тонкости, для которой толщиномер может обеспечить измерение. Датчик с диапазоном от 0 до 0,0500 дюйма может иметь разрешение 0,0001, что означает, что он может разрешать значения с точностью до десятитысячной доли дюйма.
- Точность датчика — это мера способности датчика отражать фактическую толщину материала, выраженную в виде значения +/- или процента от показания полной шкалы (например, +/- 0,0002).
- Измерительная сила — величина силы (в метрических единицах в Ньютонах), которая прилагается к материалу, когда контакты замыкаются на материале для измерения толщины. Для более мягких материалов, таких как пластмассы или ткани, может возникнуть необходимость учитывать величину измерительного усилия.
- Система измерения — значения толщины могут отображаться в метрических или британских (английских) единицах.
- Тип батареи — для цифровых датчиков указывает конкретную батарею, установленную в устройстве.
Толщиномеры покрытия
В некоторых случаях важно измерить толщину материала, который был нанесен на другую поверхность, например, покрытия или краски, нанесенной на трубу. В таких случаях измерителя толщины материала будет недостаточно, потому что доступна только одна сторона покрытия или краски, и поэтому измеритель толщины материала, как описано ранее, не может функционировать для измерения.Измерители толщины покрытия (иногда называемые измерителями краски) обеспечивают измерение толщины покрытия, чтобы убедиться, что покрытие соответствует требуемым стандартам.
Обычно существует два типа толщиномеров покрытия. Более простым из них является разрушающий процесс измерения, при котором датчик протыкает сухое покрытие до основы и, таким образом, напрямую определяет толщину покрытия. Очевидная проблема этого метода заключается в том, что он требует нарушения целостности покрытия, чтобы считывать показания.Существуют также датчики мокрого покрытия, которые измеряют толщину покрытия до того, как оно затвердеет.
Второй тип толщиномера покрытия использует неразрушающий процесс для определения толщины покрытия. Есть несколько технологий, которые используются для этих типов толщиномеров, наиболее распространенной из которых являются ультразвуковые волны.
Ультразвуковые толщиномеры
Ультразвуковой толщиномер содержит ультразвуковой преобразователь, излучающий импульс энергии звуковой волны в покрытие.Когда звуковые волны попадают на границу материала, в данном случае на границу между нижней частью покрытия и подложкой, происходит отражение, посылая обратный импульс обратно на преобразователь. Измеряя время, необходимое для обнаружения отраженного импульса, измеритель толщины покрытия может установить толщину покрытия или краски.
Эта методология работает с множеством материалов, включая металлы, пластмассы, композиты, стекловолокно и керамику, и это лишь некоторые из них. К преимуществам этого метода замера можно отнести:
- Требуется доступ только к одной стороне материала, что делает его идеальным для труб, насосно-компрессорных труб, полых отливок и других случаев с ограниченным доступом
- Неразрушающий
- Предлагает широкий диапазон измерений
- Обеспечивает быстрые результаты
- Простота использования
Толщиномеры сухой пленки
Когда покрытия, толщина которых измеряется, являются немагнитными, но нанесены на магнитную подложку, такую как железо или сталь, существует несколько типов магнитных толщиномеров, которые можно использовать для определения толщины нанесенного покрытия.Так называемый магнитный датчик отрыва типа 1 использует оценку силы, необходимой для оттягивания магнита от подложки с покрытием, для оценки толщины покрытия. Эти датчики содержат постоянный магнит и калиброванную пружину с градуированной шкалой. Чем толще покрытие, тем меньше сила, необходимая для удаления магнита — чем тоньше покрытие, тем больше необходимое усилие. Следовательно, силу отрыва можно использовать для оценки толщины покрытия.
Магнитный датчик типа 2 работает с использованием измерения изменений магнитного поля, создаваемого датчиком, когда это устройство помещается на покрытие (это снова используется в случае немагнитного покрытия, которое находится над магнитной подложкой).Изменение напряженности магнитного поля будет варьироваться в зависимости от расстояния между магнитной подложкой и зондом на поверхности покрытия. Во многих из этих устройств используется датчик постоянного давления, поэтому давление оператора на покрытие не является фактором при оценке толщины покрытия.
Существуют также магнитные толщиномеры с откатом, которые работают аналогично описанным выше магнитным толщиномерам. Эти устройства имеют постоянный магнит, прикрепленный к одному концу балансира, который может поворачиваться, когда пользователь вращает циферблат пальцем.Калиброванная пружина используется для отображения силы, необходимой для оттягивания магнита от поверхности, что также является показателем толщины покрытия между магнитом и лежащей под ним подложкой.
Толщиномеры и инструменты прочие
Три дополнительных прибора, которые можно использовать для измерения толщины покрытия: приборы магнитной индукции, электромагнитные приборы и вихретоковые толщиномеры. Первые два из этих трех функционируют путем измерения изменения плотности магнитного потока на поверхности магнитного зонда, когда он приближается к поверхности стальной поверхности с покрытием.Измеренные значения плотности потока можно использовать для оценки толщины покрытия, нанесенного на поверхность.
Вихретоковый толщиномер работает с непроводящими покрытиями, которые наносятся на подложки из цветных металлов. Эти устройства генерируют высокочастотный переменный ток, который создает переменное магнитное поле. Когда поле приближается к поверхности, переменное магнитное поле создает на поверхности вихревые токи, которые, в свою очередь, приводят к созданию противоположного магнитного поля.Противоположное поле может быть обнаружено вихретоковым измерителем толщины и использовано для оценки толщины покрытия.
Калибровка
Измерители толщины материала и толщиномеры покрытия требуют калибровки по стандартным образцам для испытаний материалов, чтобы гарантировать, что показания устройства обеспечивают и поддерживают точные значения. Например, при использовании ультразвуковых измерителей толщины покрытия скорость распространения звуковой энергии будет зависеть от материала, в котором она распространяется. В таблице 1 ниже показана скорость передачи звука в метрах в секунду для различных типов материалов.Эту характеристику необходимо сохранить и использовать для определения времени прохождения импульса (и, следовательно, толщины материала).
Таблица 1 — Величина скорости звука для различных материалов
Материал | Скорость (м / с) |
Алюминий | 3040–6420 |
Кирпич | 3600–4200 |
Бетон | 3200–3700 |
Медь | 3560–3900 |
Стекло | 3950–5000 |
Утюг | 3850–5130 |
Свинец | 1160–1320 |
Сталь | 4880–5050 |
Дерево | 3300–5000 |
Данные таблицы: Cygnus Instruments Inc.
Аналогичным образом, измерители толщины материала часто продаются с калибровочными блоками, которые можно использовать для калибровки измерителя путем размещения материала известной толщины между контактными штифтами или кронштейнами суппорта для проверки показаний.
Толщиномеры для проволоки и листового металла
Измерители толщины проволоки и листового металла представляют собой металлические шаблоны, в которых вырезаны прецизионные отверстия и пазы. Эти устройства могут позволить пользователю легко оценить размер листового металла для стали или железа и размер проволоки для стали, алюминия, латуни и медной проволоки.Калибры охватывают стандартный калибр чугуна и стали США, калибр американской проволоки (AWG) и калибр стальной проволоки США. Датчики позволяют пользователю напрямую считывать соответствующие номера датчиков из этих шаблонов, а также получать доступ к десятичным эквивалентным размерам. Несмотря на то, что они называются термином толщиномеры, они отличаются по смыслу от других типов толщиномеров, упомянутых в этой статье, тем, что они больше предназначены для проверки материала на соответствие стандартному набору размеров, а не для измерения значения, величина которого неизвестна.
Для получения дополнительной информации о стандартных размерах листового металла см. Соответствующее руководство по толщине листового металла.
Сводка
В этой статье представлен краткий обзор толщиномеров, включая то, что они собой представляют, типы, размеры, технические характеристики и способы их использования. Для получения информации по другим темам обратитесь к нашим дополнительным руководствам или посетите платформу Thomas Supplier Discovery Platform, где вы можете найти потенциальные источники поставок для более чем 70000 различных категорий продуктов и услуг, включая более 100 поставщиков инструментов для измерения толщины и испытаний, а также поставщиков ультразвуковых толщиномеры, резьбовые пробки и кольцевые калибры, щупы, цифровые манометры, калибры внутреннего диаметра, глубиномеры, профильные калибры, кольцевые калибры, пробки и кольцевые калибры, калибры для резьбы и манометрические манометры.
Источники:
- https://www.
pce-instruments.com/us/measuring-instruments/test-meters/thickness-gauge-kat
- https://www.measurementshop.co.uk/blog/guides/all-you-need-to-know-about-thickness-gauges
- https://www.reliabilitydirectstore.com/Thickness-Gauges-s/440.htm
- https://www.elcometer.com/en/coating-thickness-gauge.html
- https://www.greatgages.com/collections/deep-throat-thickness-gages?page=2
- http: // www.longislandindicator.com/p12.html
- https://www.olympus-ims.com/en/applications-and-solutions/introductory-ultrasonics/introduction-thickness-gaging/
- https://www.cygnus-instruments.com/
- https://www.corrosionpedia.com/7-methods-of-coating-thickness-measurement/2/6545
- https://www.qualitymag.com/articles/87956-quality-101—understand-coating-thickness-measurement-test-methods
- https://www.starrett.com/category/precision-measuring-tools/special-function-dial-gages/110507#currentPage=1&displayMode=grid&itemsPerPage=12&sortBy=wp/asc
- http: // www.
davis.com
- https://www.grainger.com/category/machining/precision-measuring-tools/thickness-gages
- https://www.mcmaster.com/thickness-gauges
Прочие изделия для манометров
- Механические манометры: подробный обзор различных типов манометров
- Магнитные уровнемеры для жидкости
- Все о калибрах-щупах — определение, размеры и применение
- Все о цифровых манометрах — определение, размеры и применение
- Все о калибрах для внутреннего диаметра — определение, размеры и применение
- Все о глубиномерах — определение, размеры и применение
- Все о профильных калибрах — определение, размеры и применение
- Все о кольцевых калибрах — определение, размеры и применение
- Все о манометрах — определение, размеры и применение
- Все о манометрах для пробок — определение, размеры и применение
- Все о манометрах — определение, размеры и применение
- Все о высотомерах — определение, размеры и применение
- Все об уровнемерах — определение, размеры и применение
Больше от Instruments & Controls
Что нужно знать о толщиномерах
Что такое толщиномер?
Толщиномер — это переносное измерительное устройство, используемое для измерения толщины данного материала или образца. Они часто используются в производстве продукции и инженерных операциях, требующих определенной толщины объекта в соответствии с государственными постановлениями.
Как работает толщиномер?
Это будет зависеть от типа толщиномера, однако ультразвуковые толщиномеры работают, измеряя количество времени, необходимое для прохождения звука от датчика через материал к заднему концу объекта и обратно к датчику. Благодаря этому датчик может обрабатывать данные в зависимости от количества времени, необходимого для прохождения звука через обозначенный образец.
Типы толщиномеров
Ультразвуковой толщиномер
Ультразвуковые толщиномерыиспользуют звуковые волны для измерения толщины образца путем измерения количества времени, необходимого для прохождения звука через образец и обратно к измерителю.
Толщиномеры покрытий
Толщиномеры для покрытий — это универсальные модели толщиномеров, разработанные специально для измерения толщины немагнитных и изоляционных покрытий на черных материалах, таких как сталь, и цветных материалах, включая пластик и латунь, которые применяются в инструментах промышленного класса.
Эти датчики могут измерять толщину формованного пластика на промышленных пилах, сверлах и рукоятках шлифовальных инструментов, а также на медицинских изделиях, используемых в хирургии и стоматологии, чтобы обеспечить необходимый комфорт и безопасность. Определенные разновидности измерителей толщины, такие как измерители толщины лакокрасочного покрытия, также могут использоваться для измерения толщины краски в автомастерских и кузовных мастерских.
Что можно измерить толщиномером?
Цифровые толщиномеры и измерители толщины — это универсальные устройства, которые можно использовать в широком спектре приложений:
Транспортное средство / автомобильная промышленность — Большинство типов толщиномеров используются в автомобильной промышленности и могут использоваться для измерения толщины металлических листов и выявления дефектов кузова автомобиля, а также для измерения толщины стекол, используемых в транспортных средствах. лобовые стекла. Ультразвуковые датчики толщины часто требуются для выявления производственных дефектов, в то время как специальные датчики толщины лакокрасочного покрытия используются при ремонте автомобилей и кузовных мастерских для нанесения соответствующей толщины металлических красок.
Машиностроение и производство — Вслед за автомобильной промышленностью, крупные фабрики и машиностроительные заводы, которые производят все, от игрушек до автомобилей и деталей машин, часто требуют толщиномера для обеспечения качества и стабильности деталей на производственной линии.В машиностроении, в частности детали самолетов, необходимо тщательно проверять на наличие дефектов и дефектов; Толщиномеры используются для точного измерения толщины материалов в целях обеспечения безопасности.
Jewelers — Специальные измерительные приборы для золота могут использоваться для измерения толщины золота и других драгоценных металлов. Используя ультразвуковое оборудование для измерения толщины, ювелиры могут определить, есть ли в золотом изделии сердцевина из другого материала.
Строительство — Толщиномеры часто используются для проверки толщины стен и строительных материалов.Проводя испытания на толщину, строители и геодезисты могут убедиться, что сплошные стены не содержат дефектов, которые могут сделать здание нестабильным. Аналогичным образом медные трубы и промышленные трубопроводы также могут регулярно проверяться на предмет коррозии.
Шоссе и местные органы власти — Толщиномеры также могут использоваться для проверки толщины опорных металлических и бетонных колонн мостов, чтобы убедиться, что они соответствуют нормам и не разрушаются преждевременно.Эти устройства чаще всего используются для обнаружения воздушных карманов в бетоне и коррозии на стальных каркасах и опорах.
Емкости с топливом / химикатами — Ультразвуковые датчики контроля могут указать, имеет ли место чрезмерная коррозия в резервуарах для хранения топлива и химикатов.
Археология — Студенты и ученые могут использовать методы неразрушающего ультразвукового контроля для анализа толщины выкопанных горшков и чувствительных материалов.
Производство стекла — Ультразвуковые толщиномеры используются для измерения толщины стекла в мебельных зеркалах, оконных стеклах корпусов, а также в лобовых стеклах и отражающих поверхностях транспортных средств.
Medical — Измерители толщины покрытия используются для обеспечения того, чтобы формованные пластмассовые покрытия на медицинских инструментах и посуде обеспечивали достаточную защиту и были безопасны в использовании.
Промышленные инструменты — Одно из наиболее распространенных применений для толщиномеров покрытия, промышленные инструменты, такие как пилы и электроинструменты, требуют соответствующих покрытий, чтобы инструмент был износостойким и безопасным в обращении.
Калибровка толщиномера
Процесс калибровки толщиномеров будет отличаться в зависимости от типа используемого вами толщиномера.Измерители толщины покрытия можно откалибровать несколькими способами, включая калибровку по одной точке, калибровку по фольге и калибровку по двум фольгам. Для ультразвуковых толщиномеров требуются утвержденные калибровочные блоки.
Калибровка по одной точке
Одноточечная калибровка — это стандартный процесс калибровки, не требующий фольги. Процедура проводится на образце без покрытия путем нанесения измерительного щупа как можно ближе к обозначенной точке измерения. Эта процедура калибровки имеет только одну контрольную точку, которая является нулевым значением, отсюда и метка «одна точка».
Калибровка по фольге (калибровка по двум точкам)
В этой процедуре калибровки используется калибровочная фольга с известной толщиной. Для начала проводится одноточечная калибровка, затем фольга помещается на образец без покрытия. Затем зонд помещается в ту же обозначенную зону измерения, затем указатели на устройстве используются для изменения отображаемого значения толщины до тех пор, пока оно не будет соответствовать значению толщины фольги.
Эту процедуру часто выбирают вместо калибровки по одной точке, когда пользователям требуется более высокая точность. Для этого фольга должна иметь толщину, немного превышающую толщину слоя испытуемого объекта.
Калибровка по двум фольгам
Часто используемая для более сложных процедур проверки толщины, процедура калибровки с двумя фольгами требует наличия двух фольг разной толщины (они обычно градуированы, причем одна фольга составляет примерно 0,5 толщины объекта испытания, а вторая — примерно 1,0 толщины объекта). Этот метод калибровки использует две контрольные точки для датчика, которые относятся к более толстым и более тонким значениям.
Этот процесс чаще всего используется для грубых или неравномерных материалов.
Ультразвуковая калибровка
Стандартная процедура калибровки ультразвукового толщиномера заключается в использовании утвержденных калибровочных блоков (также известных как ультразвуковые калибровочные стандарты) для проверки линейности толщиномера; размеры блоков варьируются от 1,5 мм до 50 мм. Типичная процедура включает 4-5 отдельных испытаний с блоками разных мм для обеспечения согласованности. Зонд помещается в обозначенное место на калибровочном блоке, из которого излучаются и принимаются звуковые волны, когда звук проникает к задней стороне блока; затем это испытание повторяется, начиная с более тонких блоков и переходя к более толстым блокам после каждого последующего испытания.
Примечание. Некоторые ультразвуковые толщиномеры требуют использования связующего геля для устранения зазоров между проверяемой поверхностью и датчиком.
На что следует обратить внимание при покупке толщиномера
Материал образца — Материал образца может повлиять на тип нужного вам толщиномера. Толщиномер идеально подходит для большинства металлов, пластмасс и керамики, однако для изделий из резины и композитов могут потребоваться более совершенные толщиномеры с более высокими уровнями проникновения.
Толщина — При покупке толщиномера вам необходимо убедиться, что диапазон измерения толщины соответствует образцу, который вы хотите измерить. Более толстые материалы, как правило, измеряются на более низких частотах, тогда как более тонкие образцы требуют более высоких частот.
Геометрия / поверхность — Поверхность образца может повлиять на способность датчиков соединяться и получать точное измерение толщины. Для измерений на выпуклых образцах могут потребоваться бесконтактные погружные манометры для адекватной звукоизоляции.
Разрешение / точность — Более дорогие профессиональные толщиномеры обычно обеспечивают более высокий уровень точности по сравнению со стандартными моделями. При работе с тонкими образцами, такими как линзы, стекло и краски, может потребоваться более высокая точность.
Стоимость — Сегодня на рынке продается множество типов толщиномеров, от высокотехнологичных моделей, одобренных для ультразвуковой диагностики, до недорогих моделей толщиномеров. При покупке толщиномера очень важно регулярно учитывать необходимые вам функции; например, если вы работаете в соответствии с законодательством, вам потребуется сертифицированный толщиномер, который обычно будет дороже, чем стандартный толщиномер.
Выбор толщиномеров в «Измерительном цехе»
The Measurement Shop — ведущий поставщик высококачественных толщиномеров в Великобритании. У нас есть широкий выбор лучших ультразвуковых датчиков и толщиномеров покрытий, произведенных Reed and Sauter; вот некоторые из наших самых популярных устройств измерения толщины:
Толщиномер покрытия | PCE Instruments
Большинство продуктов и устройств, используемых в повседневной жизни, имеют определенный тип покрытия на поверхности по ряду причин: это может быть оптическое улучшение внешнего вида, может быть улучшение гладкости (или наоборот) или другие качества, или защитная функция.Покрытия не одинаковы и различаются не только типом материала / краски / лака, но и толщиной, которую можно измерить толщиномером покрытия. В настоящее время покрытия могут быть толщиной всего в несколько нанометров или, наоборот, очень толстыми, поэтому необходимость иметь возможность измерить толщину пленки на поверхности стала настолько острой, и именно здесь покрытие толщиномер вступает в игру.
Тонкие покрытия нашли широкое применение во многих отраслях промышленности (текстильная, медицинская, фармацевтическая, химическая, морская, нефтегазовая, производство и упаковка и многие другие).
Несмотря на толщину, такие нанопокрытия способны значительно улучшить качество, долговечность и стойкость основного материала и, следовательно, всего продукта. Производители выбирают тонкое нанопокрытие, поскольку оно обеспечивает дополнительную защиту от коррозионных и аналогичных негативных воздействий, плохой погоды и изменчивых условий окружающей среды, тепла / воды / льда, снижает трение и, таким образом, износ, обладает антибактериальной функцией, защищает от ЭМП. . При производстве зеркал используются тонкие покрытия, чтобы стекло могло отражать, а не быть прозрачным.Тонкие покрытия термическим напылением часто наносят с защитной целью даже на поверхности конструкций, зданий, самолетов.
В зависимости от подложки покрытия могут быть абсолютно разными: металлические, оксидные, неорганические, непроводящие, нанесенные термическим напылением и т. Д. Тип покрытия выбирается исходя из свойств материала подложки. Например, в медицинской сфере проводились эксперименты с хром-нитридом. Одним из покрытий, наносимых в прошлом, был гальванический хром (VI), но в настоящее время его применение сокращено с возможностью прекращения.Поверхности, требующие защиты, гладкости и прочности, получают металлооксидную пленку, а также сплавы; кроме того, родий, медь и даже основа на золоте или серебре. Стеклянная подложка часто имеет различные оптические отражающие и неотражающие покрытия, в зависимости от задачи применения. Некоторые покрытия обеспечивают высокий уровень защиты от инфракрасного излучения с абсолютной прозрачностью. Инновационные технологии представляют собой кремниевые покрытия, которые подходят для нанесения на объекты различной формы. Помимо металла, в качестве подложки могут использоваться пластмассы / полимеры, керамика, текстильные материалы.
В то время как тонкие покрытия становятся все более популярными среди производителей, существует спрос на толстые покрытия, которые иногда достигают толщины 50 и даже 60 мм, которую можно измерить с помощью толщиномера покрытия PCE. Такие покрытия необходимы для защиты металлических (железных) и цветных металлических поверхностей от экстремальных внешних воздействий, таких как огонь, вода, удары и т. Д. Они наиболее подходят для судов, трубопроводов и для тех сред, где объект / устройство подвергается воздействию. экстремальные температуры.Основная задача толстого покрытия — уменьшить взаимодействие основного вещества с внешними факторами и снизить риск трения, износа или повреждения. Измеритель толщины покрытия может помочь оценить, было ли выполнено это требование или нет. Для трубопроводов очень важна защита от коррозии, поэтому рекомендуется использовать толстые покрытия (полипропилен). Толстое покрытие часто состоит из нескольких слоев, наносимых путем нанесения определенной пасты / раствора / смеси с последующей сушкой, тогда как тонкое покрытие наносится другими методами (например, напылением).Здесь необходимо тщательно выбирать толщиномер покрытия. Оцинкованное цинковое покрытие — еще один пример толстого покрытия, нанесенного на сталь, хотя есть несколько проблем, связанных с твердостью и оптическим внешним видом.
Для достижения лучших результатов цинкование поддерживается покраской.
Тип покрытия и требования к методам нанесения определены в стандартах ISO, и измерения следует проводить в соответствии с существующими правилами. Современные технологии, помимо разрушающих методов, позволяют применять метод неразрушающего контроля для измерения толщины с помощью различных доступных толщиномеров (ультразвуковой датчик, электронный датчик толщины магнитного покрытия, вихретоковый датчик и т. Д.).
Как использовать ультразвуковой толщиномер
Базовое понимание того, как работает ультразвуковой толщиномер, является ключом к использованию этого жизненно важного оборудования. Сверхлегкие и прочные модели, в которых используются преимущества микрокомпонентов, означают, что расчет толщины широкого диапазона материалов теперь может выполняться быстро и с высоким уровнем точности.
Такие датчики работают за счет излучения ультразвуковых сигналов, которые поглощаются и рассеиваются через измеряемый материал. Затем эти данные анализируются для определения толщины материала.
- Такой инструмент можно использовать практически на любом инженерном материале, таком как пластик, металлы, композиты, стекловолокно и другие.
- Подходит для измерения отдельных слоев или покрытий в многослойных изделиях.
- Инструмент полностью неразрушающий, не требует разрезания или резки.
Как работает инструмент
Инструмент использует звуковые волны, которые распространяются на частотах выше, чем может быть обнаружено человеческим слухом, в основном на уровнях от 500 кГц до 20 кГц, хотя в некоторых случаях это выходит за пределы этих параметров.
- Звук передается от элемента, известного как преобразователь, в виде пакета ультразвуковых волн.
- Этот всплеск проходит через материал в виде серии организованных механических колебаний, которые затем отражаются обратно в приемник — короче говоря, он «слушает» в течение времени, необходимого для того, чтобы это эхо вернулось.
- Время, необходимое для этого. Затем can используется для расчета толщины материала.
Рекомендации по правильному использованию
Важно правильно откалибровать инструмент перед использованием и выполнять ее в соответствии с инструкциями производителя.Перед тем, как проводить какие-либо измерения, необходимо провести различные подготовительные мероприятия.
- Выберите правильный преобразователь : Это будет зависеть от измеряемого материала, температуры материала, физических ограничений в окружающей среде (например, ограниченного местоположения), температуры материала и других аспектов, включая наличие поверхности однородный или изогнутый.
- Подготовьте поверхность : Чем более неровная или шероховатая поверхность, тем менее надежными будут показания.Очистите весь мусор, ржавчину и окалину металлической щеткой или, при необходимости, шлифовальными и / или шлифовальными машинами.
- Использование связующего вещества : это жидкость, которая гарантирует отсутствие зазора между датчиком и измеряемым материалом.
Перед измерением следует нанести небольшое количество на поверхность — отсутствие надлежащего уплотнения приведет к ошибочным результатам.
- Ориентация преобразователя при измерении трубок и труб : Диаметр трубы определяет количество необходимых измерений и то, под параллельным или перпендикулярным углом измерения.При измерении большего диаметра (более 10 см) датчик следует держать перпендикулярно длинной оси. Для труб меньшего размера сделайте это и дополнительное параллельное измерение. Следует записать меньшее из измерений.
- Колебания температуры : Звуковые волны медленнее проходят через горячий материал. При проведении измерений на поверхностях с высокой температурой рекомендуется использовать датчик, специально разработанный для работы в таких условиях, и поддерживать его в контакте только на время измерения, чтобы предотвратить любое тепловое расширение и, как следствие, точность результатов.
Процедура измерения
После того, как будут учтены все приготовления, фактический процесс измерения станет быстрым и легким.
- Включите прибор
- Выберите правильную функцию для измеряемого материала
- Добавьте небольшое количество связующего вещества на поверхность
- Поместите датчик на покрытую гелем поверхность
- Запишите показания
Ультразвуковой Толщиномеры являются жизненно важными инструментами, которые могут помочь безопасно продлить срок службы различных конструкций.Их роль в эффективном обслуживании в таких отраслях, как нефтехимическая, нефтегазовая, обрабатывающая и энергетическая, очень важна. Поставщик оборудования, ориентированного на решения, Nexxis, предлагает широкий спектр передового испытательного оборудования с множеством опций для удовлетворения всех потребностей и решения самых сложных проблем.
Применение динамичной стратегии, ориентированной на меняющиеся потребности клиентов, — это лишь одна из причин, по которой наша всемирная компания стала ведущим поставщиком технического оборудования для мировой промышленности. Чтобы узнать больше о том, как этот инновационный подход может сэкономить ваше рабочее время и деньги, посетите ближайший офис в Австралии, Сингапуре или США.
Написано NexxisMar 6, 2020 · 4 мин чтения
Ультразвуковое измерение толщины краски — пластиковые подложки | Ресурсы
DeFelsko производит портативные неразрушающие ультразвуковые измерители толщины покрытий, которые идеально подходят для неразрушающего измерения толщины сухой пленки покрытий на пластике.Многие отрасли промышленности теперь используют эту неразрушающую технологию в своих программах обеспечения качества.
Две модели идеально подходят для пластиковых подложек.
- PosiTector 200 B1 (стандартная модель) — это экономичное и наиболее распространенное решение для измерения ОБЩЕЙ толщины системы покрытия.
- PosiTector 200 B3 (расширенная модель) может измерять как ОБЩУЮ толщину покрытия, так и до 3 толщин отдельных слоев в многослойной системе.
Он также имеет графический режим для детального анализа системы покрытия.
Измерение:
- Общая толщина покрытия на пластике
- Измерение шероховатой поверхности покрытия
- Измерение толщины отдельного слоя в многослойном приложении
- Измерение на автомобильном пластике
Дополнительные примечания:
- Как проводить измерения
- Графический режим
- Другие методы измерения
- Справочная информация о пластиковых покрытиях
- Зачем проводить измерения с помощью ультразвука?
- Где рынок?
Приложение №1: Измерение общей толщины
Некоторые системы пластиковых покрытий наносятся в несколько слоев для достижения желаемой цели.Наш PosiTector 200 B1 — идеальное решение, когда аппликаторам нужно знать только конечную общую толщину покрытия.
PosiTector 200 B1 готов к измерению большинства применений пластиковых покрытий прямо из коробки. Он имеет диапазон измерения от 13 до 1000 микрон (от 0,5 до 40 мил) и идеально подходит для измерения общей толщины системы покрытия. Он не требует настройки калибровки для большинства применений, имеет возможность переключения мил / микрон и имеет большой, толстый, ударопрочный дисплей Lexan.
Для тех, кто знаком с измерителями толщины магнитного покрытия, использование ультразвуковых измерителей толщины покрытия является простым и интуитивно понятным.Метод измерения прост и неразрушает.
Приложение № 2: Измерение шероховатых поверхностей покрытия
Покрытия с шероховатыми поверхностями бросают вызов любому методу измерения, и ультразвуковые испытания не являются исключением. PosiTector 200 способен справиться с этими ситуациями.
На микроскопическом уровне толщина может варьироваться (см. Рис. 2). Значимые измерения толщины лучше всего получить, выполнив несколько измерений в одном и том же месте и усреднив результаты.
На шероховатых поверхностях PosiTector 200 обычно определяет толщину от вершины выступов покрытия до основы. Это представлено расстоянием №1 на рисунке 2. Связующее вещество заполняет пустоты между зондом и покрытием, помогая ультразвуковому импульсу проникать в покрытие.
Из-за сильной шероховатости прибор может отображать низкие значения толщины (расстояние №2). Это происходит потому, что эхо-сигналы от поверхности раздела контактное вещество / покрытие сильнее, чем от границы раздела покрытие / подложка. PosiTector 200 имеет уникальную настраиваемую пользователем функцию УСТАНОВКИ ДИАПАЗОНА для игнорирования эхо-сигналов от шероховатости.
Для этих приложений режим памяти PosiTector 200 предоставляет помощь.Когда память включена, PosiTector 200 вычисляет и отображает количество снятых показаний, среднее значение этих показаний, стандартное отклонение этих показаний, а также максимальное и минимальное значения (см. Рисунок 3). Прилагаемый контактный агент действует лучше, чем вода на неровных поверхностях.
Рис. 3 Для получения значимых измерений толщины на шероховатых поверхностях режим памяти PosiTector 200 используется для вычисления скользящего среднего.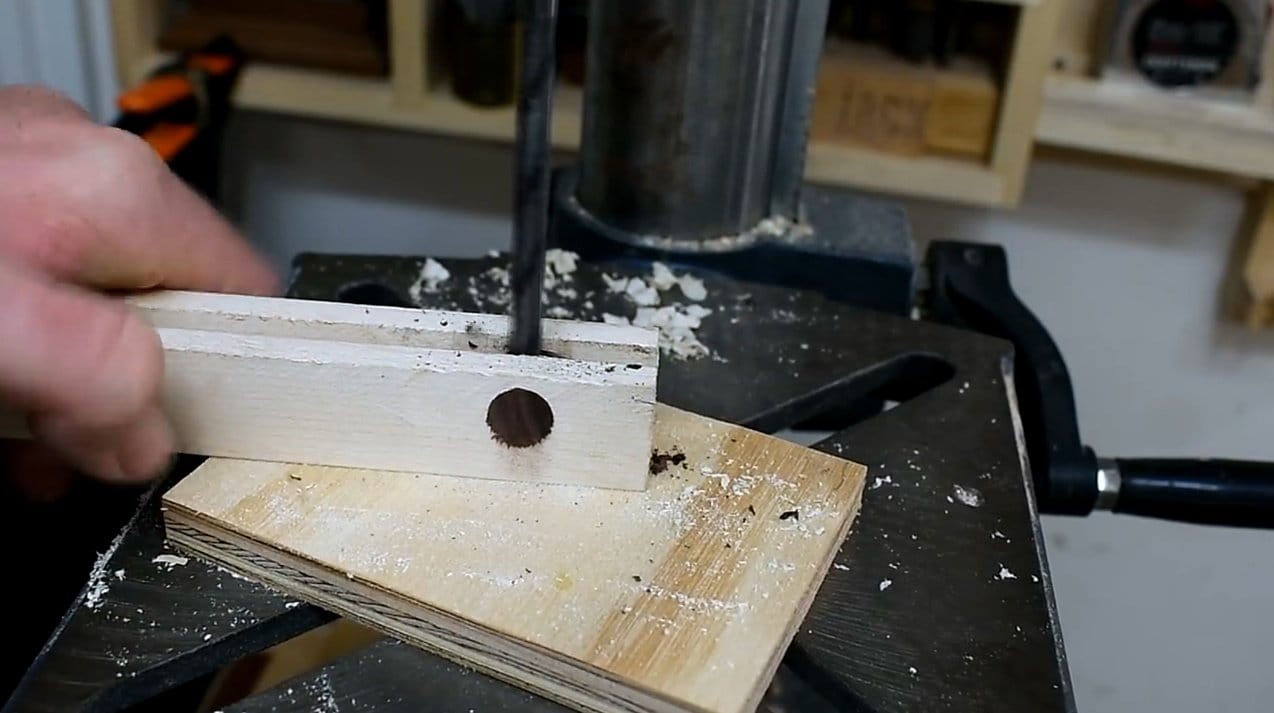
Приложение № 3: Измерение толщины отдельных слоев в многослойном приложении
PosiTector 200 B3 может измерять как общую толщину системы покрытия, так и до 3 толщин отдельных слоев в многослойной системе.Он также имеет графическое отображение для подробного анализа системы покрытия.
Рис. 4В приведенном выше примере толщина слоя 1 составляет 1,5 мил. Слой 2 имеет толщину 1,5 мил. Общая толщина составляет 3,0 мил. Графический ЖК-дисплей отображает два «пика», представляющих две границы раздела материалов. Двухэтапный процесс настраивает инструмент для многоуровневых приложений.
Приложение №4: Измерение автомобильного пластика
Большое количество пластиковых компонентов присутствует как в салоне, так и снаружи автомобиля.Очень часто эти пластиковые компоненты необходимо покрывать из соображений эстетики и защиты.
Внутренние компоненты, такие как приборные панели, дверные панели, крышки подушек безопасности, рулевые колеса и т. Д., Сложнее измерить по двум причинам. Во-первых, многие компоненты слишком малы или слишком сложны геометрически для того, чтобы зонд PosiTector 200 мог получить надлежащий доступ. Во-вторых, некоторые детали имеют либо очень тонкое покрытие, либо покрытие слишком грубое, чтобы прибор мог его измерить постоянно. Измеритель лучше всего работает на гладкой, плоской, твердой поверхности с толщиной покрытия не менее 13 микрон (0.5 мил).
Внешние компоненты, такие как бамперы, корпуса зеркал, боковая облицовка и т. Д., Могут быть измерены при условии, что датчик PosiTector 200 снова сможет получить доступ к измеряемой поверхности. Измеритель может измерять общую толщину в большинстве случаев и может измерять отдельные слои в многослойной системе.
Автомобильные системы покрытий состоят из нескольких слоев покрытия. Базовая модель PosiTector 200 B1 может измерять общую толщину этих систем покрытий.
Слои промотора адгезии и грунтовки в автомобильной промышленности обычно слишком тонкие, чтобы более продвинутая модель PosiTector 200 B3 могла измерять индивидуально. Таким образом, инструмент комбинирует их толщину с толщиной основного покрытия для получения общего результата. Верхний прозрачный слой покрытия измеряется отдельно и индивидуально.
На рис. 5 показаны типичные результаты PosiTector 200 B3 на внешнем автомобильном пластике. На изображении слева показано измерение в британских единицах (милы). Правое изображение — это эквивалентное измерение в метрических единицах (микронах). Хотя система покрытия состоит из 4 слоев, прибор объединяет толщину первых 3 слоев (усилитель адгезии, грунтовка, базовые слои) в одно значение, равное 1.7 мил (43 микрона). Размер конечного верхнего прозрачного покрытия индивидуально составляет 1,7 мил (43 микрона). Общая толщина системы покрытия составляет 3,4 мил (86 мкм).
Этот результат полезен, когда окончательная толщина прозрачного покрытия является важным слоем, который необходимо определить. Автодетейлеры используют эту функцию для просмотра оставшегося количества лака во время полировки. Аппликаторы используют эту функцию для обеспечения постоянной толщины нанесения.
Ультразвуковые датчики, обсуждаемые в этой статье, имеют диаметр 8 мм (0.3 дюйма) плоская измерительная поверхность, которая должна полностью контактировать с пластиком с покрытием для получения наилучших результатов измерения. Измерения, проведенные на изогнутых поверхностях, могут потребовать усреднения нескольких показаний для получения значимых результатов.
Дополнительные примечания
Как проводить измерения
Ультразвуковое измерение толщины покрытия работает, посылая ультразвуковые колебания на покрытие с помощью зонда с помощью связующего вещества, нанесенного на поверхность.К каждому прибору прилагается флакон объемом 4 унции обычного гелевого геля на водной основе.Как вариант, капля воды может служить связующим веществом на гладких горизонтальных поверхностях.
Рис. 6 Проведение измерения. После того, как капля связующего вещества была нанесена на поверхность детали с покрытием, зонд помещается на поверхность плашмя. Нажатие вниз инициирует измерение (см. Рис.6). Поднимая датчик, когда слышен двойной звуковой сигнал или когда мигает зеленый индикатор, отображается последнее измерение на ЖК-дисплее. Второе показание можно снять в том же месте, продолжая удерживать зонд на поверхности.По окончании протрите зонд и поверхность тканью или мягкой тканью.
Точность измерения
Точность любого ультразвукового измерения напрямую соответствует скорости звука измеряемой отделки. Поскольку ультразвуковые инструменты измеряют время прохождения ультразвукового импульса, они должны быть откалиброваны по «скорости звука» в этом конкретном материале.
С практической точки зрения значения скорости звука не сильно различаются между материалами покрытия, используемыми в пластмассовой промышленности.Поэтому ультразвуковые толщиномеры покрытия обычно не требуют настройки заводских настроек калибровки.
Графический режим (только модель PosiTector 200 B3)
Правая сторона экрана PosiTector 200 может использоваться для отображения графического представления ультразвукового импульса, проходящего через систему покрытия. Этот мощный инструмент позволяет пользователю лучше понять, что датчик «видит» под поверхностью покрытия.
По мере того, как зонд опускается и ультразвуковой импульс проходит через систему покрытия, импульс сталкивается с изменениями плотности на границах раздела между слоями покрытия и между покрытием и подложкой.
«Пик» изображает эти интерфейсы. Чем больше изменение плотности, тем выше пик. Чем плавнее изменение плотности, тем больше ширина пика. Например, два слоя покрытия, сделанные по существу из одного и того же материала и «смешанные», приведут к низкому и широкому пику.Два материала с очень разной плотностью и четко определенной границей раздела приведут к высокому узкому пику.
PosiTector 200 B3 выбирает самый высокий из пиков при попытке определить толщину слоя покрытия. Например, если количество уровней установлено на 3, 3 самых высоких пика между диапазонами Lo, и Hi, выбираются в качестве интерфейсов между этими уровнями. Пики, выбранные датчиком, обозначены красными треугольными стрелками (см. Рис.9).
На рис. 9 верхнее ( Lo = 0,5 мил) и нижнее ( Hi = 15,0 мил) значения диапазона отображаются в виде двух горизонтальных линий вверху и внизу графической области. Lo (минимальный предел) находится вверху. Hi (максимальный предел) внизу. Эхо-сигналы или пики (значения толщины) вне этих диапазонов игнорируются. Значения диапазона устанавливаются и изменяются с помощью опции меню УСТАНОВИТЬ ДИАПАЗОН.
Этим графическим дисплеем можно управлять с помощью параметра меню УСТАНОВИТЬ ДИАПАЗОН.Помимо возможности настройки значений диапазона, курсор можно расположить в любом месте между двумя значениями диапазона, чтобы исследовать другие пики.
В этом примере прибор объединяет два нижних слоя в результат 3,9 мил. Курсор определяет верхний слой толщиной 5,9 мил.
Третий слой, таким образом, составляет 2,5 мил (5,9–3,4 (сумма слоев 1 и 2).
Другие методы измерения
Обычные магнитные и вихретоковые датчики работают только с металлами.Таким образом, промышленность пластмасс полагалась на другие методы измерения, в том числе:
- Оптическое поперечное сечение (разрезание детали с покрытием и микроскопический просмотр разреза)
- Измерение высоты (измерение до и после с помощью микрометра)
- Гравиметрическое (измерение массы и площадь покрытия для расчета толщины)
- Погружение измерителей толщины мокрой пленки во влажную краску и расчет толщины сухой пленки с использованием процентного содержания твердых веществ по объему
- Замена (размещение стального купона рядом с пластиковой частью и нанесение на нее покрытия одновременно время).
Эти методы требуют много времени, трудны в исполнении, могут быть интерпретированы оператором и подвержены другим ошибкам измерений. Аппликаторы считают деструктивные методы непрактичными. Чтобы получить статистически репрезентативный образец, несколько деревянных изделий из партии, возможно, потребуется утилизировать в рамках процесса разрушающих испытаний.
Типичный метод разрушения требует разрезания покрытой детали в поперечном сечении и измерения толщины пленки под микроскопом.В другом методе поперечного сечения используется масштабированный микроскоп для просмотра геометрического разреза через покрытие из сухой пленки. Для этого специальный режущий инструмент проделывает небольшую точную V-образную канавку через покрытие в подложке (см. Рис. 11). Доступны измерительные приборы, которые поставляются в комплекте с режущими наконечниками и лупами с подсветкой. Подробное описание этого метода испытаний приведено в ASTM D4138-07a, «Стандартная практика измерения толщины сухой пленки систем защитных покрытий с помощью разрушающих средств поперечного сечения».
Хотя принципы этого метода легко понять, существует множество возможностей для внесения ошибок. Подготовка образца и интерпретация результатов требуют умения. Кроме того, настройка сетки измерений на неровный или нечеткий интерфейс может привести к неточности, особенно между разными операторами. Этот метод используется, когда недоступны недорогие неразрушающие методы, или как средство подтверждения результатов неразрушающего контроля.
С появлением ультразвуковых инструментов многие компании по нанесению покрытий перешли на неразрушающий контроль.
Справочная информация о пластиковых покрытиях
Каково применение?
Покрытие пластмасс, особенно в автомобильной промышленности, включает нанесение нескольких слоев покрытия для достижения полного эстетического вида и защитных свойств. Не только внешняя отделка, как правило, является сильным отражением качества и долговечности дорогостоящих потребительских товаров, но и покрытия для пластиковых компонентов должны решать проблемы, уникальные для пластиковых подложек, включая адгезию, гибкость и температурные ограничения.
Обычные пластиковые подложки (например, полиэтилен, полипропилен, термопластичный полиолефин, АБС, нейлон, ПВХ) непористые, устойчивые к большинству растворителей и имеют низкую поверхностную энергию по сравнению с другими материалами. Это затрудняет смачивание пластиковой поверхности и дает покрытиям мало возможностей для прилипания за счет проникновения или физического сцепления с неровностями поверхности. Чтобы противостоять этим трудностям, промоторы адгезии используются в качестве добавок к краскам или в качестве грунтовок для улучшения адгезии покрытий к их субстратам.Промотор адгезии обычно имеет сродство к субстрату и нанесенному покрытию, что позволяет нанесенным покрытиям соответствовать намеченным эксплуатационным требованиям.
Покрытия для автомобилей
В автомобильных покрытиях термин «усилитель адгезии» относится к грунтовке (обычно хлорированному полиолефину или другим модифицированным полиолефинам), которая облегчает адгезию последующего слоя краски к пластику. Обычно промоторы адгезии наносятся для достижения толщины сухой пленки 0.3 — 0,5 мил (7,5 — 12,5 мкм). Поскольку толщина промотора адгезии ниже рекомендуемой толщины отдельного слоя в 1 мил (25 мкм), ультразвуковому датчику может быть трудно отличить его от последующих слоев.
Грунтовки заполняют любые небольшие дефекты процесса формования и могут обеспечивать проводящий слой, который облегчает электростатическое нанесение последующих слоев покрытия. Грунтовка также защищает основание от потенциально вредного воздействия ультрафиолетового излучения от солнца, а также обеспечивает устойчивость к химическим веществам (бензину) и влажности.Часто составы грунтовок подбираются по цвету, чтобы обеспечить минимальную толщину пленки базового покрытия и свести к минимуму эффект отслаивания камня.
Basecoat — это слой покрытия, обеспечивающий большую часть цвета, физических характеристик и эстетических эффектов. Устойчивые к выцветанию базовые покрытия часто включают особую пигментацию внешнего вида, такую как металлическое покрытие, обычное для автомобильных покрытий. Базовые покрытия можно наносить в один или несколько слоев. В зависимости от метода нанесения, ультразвуковому датчику может быть сложно различить несколько слоев базового покрытия.
Стойкие лаки образуют защитные поверхности от таких факторов окружающей среды, как травление, птичий помет, царапины на автомойках и каменные сколы. Хотя прозрачные лаки используются в сочетании с базовым покрытием для формирования окончательной отделки, акустически они обеспечивают значительную границу раздела между слоями покрытия и, таким образом, отличаются от ранее нанесенных слоев.
Рис. 12 PosiTector 200 B3 может вычислять среднее значение и стандартное отклонениесерии измерений для каждого уровня в многослойной системе.
Поскольку автомобильное покрытие — один из самых дорогостоящих процессов при сборке автомобилей, производители и сборщики постоянно стремятся к совершенствованию технологий. Когда-то такой метод нанесения называется мокрым по мокрому, когда покрытия на водной основе наносятся непосредственно поверх друг друга, не позволяя предыдущим слоям отвердеть. Такие методы сводят к минимуму использование энергии, красок и требований к переоснащению, не жертвуя при этом качеством готового внешнего вида. К сожалению, нанесение покрытия «мокрым по мокрому» имеет тенденцию вызывать эффект «переходного слоя» (смешение отдельных слоев).Отсутствие четких границ акустических минимизирует возможность ультразвукового прибора для обнаружения толщины отдельного слоя.
Зачем проводить измерения с помощью ультразвука?
Производители и специалисты по нанесению покрытий давно считают, что не существует простых и надежных средств неразрушающего контроля покрытий на пластиковых подложках. Их обычным решением было разместить металлические (стальные или алюминиевые) купоны рядом с деталью, а затем измерить толщину, нанесенную на купон, с помощью механического или электронного (магнитного или вихретокового) манометра.Это трудоемкое решение основано на предположении, что плоский купон, помещенный в общую зону покрытия, получает тот же профиль окраски, что и рассматриваемая пластиковая деталь. Ультразвуковое решение позволяет пользователю измерить общую толщину покрытия реальной детали. В зависимости от используемого ультразвукового датчика и процесса нанесения покрытия дополнительным преимуществом является возможность идентифицировать несколько отдельных слоев.
Ультразвуковое измерение толщины покрытия в настоящее время является общепринятой и надежной программой контроля, используемой в деревообрабатывающей промышленности.Стандартный метод испытаний описан в ASTM D6132-08. «Стандартный метод испытаний для неразрушающего измерения толщины сухой пленки нанесенных органических покрытий с помощью ультразвукового датчика» (2008, ASTM). Для проверки калибровки манометра доступны стандарты толщины с эпоксидным покрытием с сертификацией, проводимой национальными организациями по стандартизации.
Теперь можно проводить быстрые неразрушающие измерения толщины материалов, которые ранее требовали разрушающего контроля или лабораторного анализа. Эта новая технология улучшает стабильность и производительность в отделочном цехе. Потенциальное снижение затрат включает:
- Минимизация отходов от чрезмерного покрытия за счет контроля толщины наносимого покрытия
- Минимизация переделок и ремонта за счет прямой обратной связи с оператором и улучшенного управления процессом
- Устранение необходимости уничтожать или ремонтировать объекты путем снятия измерения толщины разрушающего покрытия.
Сегодня эти инструменты просты в эксплуатации, доступны по цене и надежны.
Где рынок?
За последние несколько лет использование пластмасс быстро расширилось.Хотя автомобильная промышленность, безусловно, является лидером, другие отрасли также широко используют пластмассы. По данным Общества производителей пластмасс, прочие изделия из пластмасс (на долю которых приходится большая часть отрасли по переработке пластмасс) являются четвертой по величине обрабатывающей промышленностью в Соединенных Штатах. Только автомобили и оборудование, нефтепереработка и электронные компоненты и аксессуары превосходят его. Хотя пластмассы часто окрашиваются непосредственно в процессе производства, многие пластмассовые детали необходимо красить, чтобы улучшить внешний вид, добиться совпадения цвета с другими деталями, улучшить стабильность пластмассовой поверхности или добиться желаемого особого эффекта.
По данным консультанта PG Phillips & Associates, мировой рынок автомобильных красок в 2001 году составил 6,6 миллиарда долларов. Растущая доля этого рынка включает покрытие из пластика, используемого для бамперов, внешних панелей и декоративной отделки. Специалисты по нанесению покрытий и сборщики в конкурентной автомобильной промышленности должны соответствовать критическим эстетическим критериям и критериям ожидаемого срока службы. Поскольку покраска является наиболее дорогостоящим процессом в автомобилестроении, существует конфликтующий приоритет — минимизировать количество времени, материалов и необходимых доработок, при этом соблюдая требования технологии повышения производительности и соблюдения экологических требований. Таким образом, необходим эффективный метод измерения для точного и надежного обнаружения и исправления проблем нанесения как можно раньше в процессе нанесения покрытия.
Связующее вещество
Связующее вещество используется для распространения ультразвуковых колебаний от датчика на покрытие. Вода — хорошее связующее для гладких покрытий. Для более грубых покрытий используйте прилагаемый гликоль-гель. Хотя маловероятно, что связующее вещество повредит отделку или оставит пятно на поверхности, мы рекомендуем протестировать поверхность, используя контактное средство на образце.Если тестирование показывает, что произошло окрашивание, вместо контактной жидкости можно использовать небольшое количество воды. Если вы подозреваете, что контактный агент может повредить покрытие, обратитесь к паспорту безопасности материала, доступному на нашем веб-сайте, и у поставщика покрытия. Также можно использовать другие жидкости, такие как жидкое мыло.
Режим памяти
Стандартные модели PosiTector 200 могут записывать 250 измерений. Модели PosiTector 200 Advanced могут сохранять 100 000 измерений в 1000 пакетов для статистических целей на экране, для печати на дополнительный беспроводной принтер Bluetooth или для загрузки на персональный компьютер с помощью прилагаемого USB-кабеля и одного из решений PosiSoft.
Ультразвуковые толщиномеры | Instrumart
Ультразвуковые толщиномеры определяют толщину образца, очень точно измеряя, сколько времени требуется звуковому импульсу, сгенерированному датчиком, чтобы пройти через него. образец и отразите его от внутренней поверхности или дальней стены. Сравнивая этот измеренный интервал времени с известными данными о типе материала, можно рассчитать толщину образца с чрезвычайно высокой точностью.Ультразвуковые толщиномеры во многих отношениях очень похожи на дефектоскопы, но, в то время как дефектоскопы отображают А-сканирование ультразвуковых формы сигналов, детекторы толщины обычно предоставляют числовой формат точных измерений.
Ультразвуковые толщиномеры имеют ряд применений в области неразрушающего контроля. Поскольку звуковые волны отражаются от границ между разнородными материалами, они превосходны
инструменты для измерения толщины красок и других покрытий в рамках программы контроля качества.Толщиномеры также обычно используются для сканирования резервуаров для хранения, трубопроводов, корпусов судов,
и многое другое для любых признаков повреждения или слабости, которые могли быть вызваны коррозией, экологическим ущербом или просто износом.
Ультразвуковые толщиномеры могут работать с широким спектром материалов, включая металлы, пластик, керамику, композиты, эпоксидные смолы и стекло. Возможность работать при доступе только Одна сторона тестового образца позволяет легко использовать их в различных областях применения.Также был разработан ряд типов преобразователей для повышения универсальности прибора.
Ультразвуковые преобразователи обычно работают на частотах от 500 кГц до 100 МГц. Как правило, более низкие частоты будут использоваться для оптимизации проникновения при измерении толстых, сильно затухающих,
или сильно рассеивающих материалов, в то время как более высокие частоты будут рекомендованы для оптимизации разрешения в более тонких, не ослабляющих, не рассеивающих материалов. Преобразователи обычно требуют
акустический связующий агент, такой как пропиленгликоль, для обеспечения полного акустического пути между датчиком и измеряемым материалом.
С ультразвуковыми толщиномерами используются три типа преобразователей:
- Контактные преобразователи — универсальные преобразователи для ультразвуковых толщиномеров. Они, как и все ультразвуковые преобразователи, должны находиться в прямом контакте с тестируемого материала, и они излучают звуковые волны перпендикулярно поверхности тестируемого материала.
- Преобразователи линии задержки используются для тестирования очень тонких материалов, поскольку они включают короткий пластиковый волновод или линию задержки между активным элементом. и образец для испытаний, который улучшает разрешение вблизи поверхности.
- Двухэлементные преобразователи оптимальны для улучшения разрешения, когда испытуемые поверхности шероховатые или изъеденные из-за коррозии.
Калибровка
Как и большинство испытательного и измерительного оборудования, ультразвуковые толщиномеры необходимо периодически калибровать для поддержания точности. В случае оборудования неразрушающего контроля калибровка выполняется с использованием прецизионных испытательных блоков, которые имитируют условия и служат эталоном. Различные типы тестовых блоков моделируют разные условия.Блоки тестов могут включать в себя этапы разных толщины для использования с толщиномерами, отверстиями и другими «дефектами» для использования с дефектоскопами или заданной твердости для датчиков твердости.
Что следует учитывать при выборе ультразвукового толщиномера:
- Какой параметр (толщина, дефектоскопия и т. Д.) Проверяется?
- Требует ли оборудование специальной подготовки?
- Какие аксессуары (преобразователи, контакт, калибровочные блоки) необходимы?
- Существуют ли профессиональные стандарты, которых необходимо придерживаться?
Если у вас есть какие-либо вопросы относительно ультразвуковых толщиномеров, не стесняйтесь обращаться к одному из наших инженеров, отправив нам электронное письмо по адресу sales @ instrumart.