ТНВД — что это? Принцип работы
ТНВД представляет собой один из ключевых узлов двигателя транспортного средства. Его важность показывает сравнение с сердечной мышцей в организме человека, задачей которой выступает обеспечение циркуляции крови по телу. Назначение ТНВД аналогично, с той лишь разницей, что он отвечает за перемещение горючего по топливной системе.
Определение
ТНВД или топливный насос высокого давления – это сложный с конструктивной и технологической точек зрения узел системы подачи топлива в дизельном или бензиновом двигателе. Английское название устройства — injection pump. Основными функциями ТНВД выступают такие:
- подача горючего к форсункам с одновременным нагнетанием давления;
- дозирование топлива в зависимости от выбранного водителем режима эксплуатации;
- определение оптимальной периодичности впрыска топлива в цилиндры двигателя.
Ключевым отличием топливного насоса высокого давления от выполняющего в целом аналогичные функции карбюратора выступает впрыск четко дозированного количества горючего в камеры внутреннего сгорания двигателя.
История разработки и совершенствования
Разработчиком ТНВД считается Роберт Бош. Активное использование рассматриваемой разновидности топливного насоса на легковых автомобилях началось во второй половине 30-х годов прошлого века.
Изначально топливный насос высокого давления предназначался исключительно для дизельных двигателей. Однако, в настоящее время ТНВД применяется и для бензиновых агрегатов, оборудованных инжекторной системой, обеспечивающей впрыскивание топлива непрямую в цилиндры.
Постоянный рост требований в части охраны труда и соблюдения экологических стандартов объясняет еще одно важное направление улучшения ТНВД. В современных условиях произошло вытеснение механических топливных насосов устройствами, оснащенными электронной регулировкой подачи горючего. Второй вариант системы впрыска топлива намного экономичнее и сводит к минимуму количество вредных выбросов в атмосферу.
Устройство
Различают несколько видов топливных насосов высокого давления. Несмотря на существенные конструктивные различия, основным рабочим узлом ТНВД является так называемая плунжерная пара. Основной ее задачей является нагнетание давления в топливной системе.
Устройство плунжерной пары включает две детали – поршень или плунжер, давший название рабочему узлу, и втулка или гильза. Принцип работы устройства основан на возвратно-поступательном движении, которое плунжер осуществляет внутри втулки. При этом каналы и клапаны, расположенные внутри ТНВД обеспечивают подачу горючего в полость, размещенную над плунжером, а также его отвод после сжатия и нагнетания давления.
Узел может эффективно работать только при обеспечении высокого уровня герметичности. Для этого рабочие поверхности и поршня, и втулки тщательно обрабатываются, что дало еще одно название плунжерной пары – прецизионная, то есть высокоточная. Еще одно обязательное требование к поршню и втулке – изготовление из крайне прочных марок стали, способной выдержать серьезные нагрузки.
Наличие других конструктивных элементов, деталей и узлов топливного насоса высокого давления зависит от конкретной разновидности устройства. Конструкция наиболее простого и широко распространенного рядного ТНВД предусматривает присутствие следующих деталей:
- плунжерная пара, подробно описанная выше;
- специальные канавки, назначение которых – подача горючего к плунжерной паре;
- кулачковый вал, оснащенный центробежной муфтой, который вращается при помощи ремня ГРМ;
- толкатели плунжера, передающие энергию, поступающую от кулачкового вала;
- пружины, предназначенные для возврата плунжера в исходное положение;
- зубчатые рейки, штуцеры и так называемый всережимный регулятор, активируемый педалью газа.
Некоторые особенности других разновидностей ТНВД описываются ниже. Но независимо от различий в конструкции, принцип работы любых топливных насосов высокого давления примерно одинаков.
Принцип работы
Схема работы рассматриваемой модели топливного насоса напоминает эксплуатацию двухтактного двигателя внутреннего сгорания. Она включает в себя несколько последовательно реализуемых этапов:
- Вращение кулачкового вала с оказанием давления на толкатели плунжера.
- Перемещение поршня по втулке.
- Увеличение давления топлива, в результате которого открываются нагнетательные клапаны.
- Поступление горючего к форсункам через открытые клапаны.
Важной особенностью ТНВД выступает попадание в форсунки не всей топливно-воздушной смеси, а только четко определенной дозы. Оставшееся топливо через специальные сливные клапаны возвращается в систему. Наличие центробежной муфты обеспечивает поступление горючего в нужный момент, а присутствие в конструкции всережимного регулятора обеспечивает точное определение необходимого объема смеси.
Дальнейшего увеличения КПД двигателей, оснащенных ТНВД, позволяет добиться использование электронных систем управления работой топливного насоса. Современные высокоточные датчики контролируют все ключевые параметры системы, к числу которых относятся:
- изменение положения педали газа;
- количество оборотов распределительного вала;
- уровень температуры охлаждающей жидкости;
- скорость транспортного средства;
- уровень давления в системе наддува воздуха;
- изменение положения иглы форсунки и т.д.
Дополнительный плюс ТНВД с электронным блоком контроля и управления – наличие эффективных программ самодиагностики системы. Они позволяют быстро выявлять возникшие проблемы и обеспечивают работу двигателя даже в случае отказа отдельных узлов или деталей.
Классификация
Для классификации ТНВД применяется несколько признаков. По принципу работы различают
Вторая разновидность – топливный насос с гидроаккумулятором – разделяет выполнение накачки топливно-воздушной смеси и ее впрыска в форсунки. Сначала горючее собирается в специальном хранилище, который и называется аккумулятором, после чего передается для сжигания. В результате повышается эффективность работы двигателя, но при этом заметно усложняется конструкция ТНВД. Последний аргумент стал главной причиной того, что насосы с гидроаккумулятором не относятся к числу популярных.
Второй классифицирующий признак – конструктивные особенности насоса. В соответствии с ними принято различать три типа ТНВД:
- Рядные. Наиболее простая и надежная конструкция, предусматривающая наличие нескольких ниш или секций, каждая из которых предназначена для подачи топлива в одну форсунку двигателя. При этом плунжерные пары размещаются в ряд, что и дало название агрегату. Сегодня такая разновидность ТНВД применяется исключительно на грузовых автомобилях, что объясняется надежностью и низким уровнем требований к качеству топлива. Однако, из-за больших габаритов и невысокого, по сравнению с альтернативными вариантами, КПД, установка на легковые авто прекращена в 2000 году.
- Распределительные. Данная разновидность насоса предполагает наличие одного или двух плунжеров, количество которых определяется объемом двигателя. Благодаря особенностям конструкции, этого оказывается вполне достаточно для обслуживания цилиндров, число которых варьируется в пределах от 4 до 12. В результате, достигается уменьшение массы и размеров ТНВД, что позволяет использование на двигателях легковых авто.
- Магистральные. ТНВД этого типа предусматривает систему подачи топлива Common Rail, которая стала в последние годы одной из наиболее востребованных. Главная особенность – накапливание топлива перед поступлением к форсункам в специальной рампе. Основное достоинство магистральных ТНВД – высокий уровень давления (свыше 180 МПа), благодаря которому достигается более эффективное сжигание горючего, обеспечивающее рост КПД при снижении расхода топлива.
Частые неисправности
Несмотря на достаточно серьезные конструктивные различия между разновидностями топливных насосов высокого давления, их эксплуатация сопровождается необходимостью выполнение ряда обязательных требований. Первое и главное из них – использование топлива, соответствующего характеристикам конкретной модели насоса.
Второе необходимое условие – своевременное и регулярное техническое обслуживание агрегата. Третье требование – применение в процессе эксплуатации качественных смазочных материалов.
Невыполнение любого из перечисленных условий приводит к необходимости дорогостоящего и весьма трудоемкого ремонта, что связано со сложностью конструкции ТНВД и, как следствие, большим объемом работ по снятию плунжерной пары или других пришедших в негодность деталей. Наиболее частыми неисправностями топливного насоса высокого давления являются:
- увеличение количества образуемого в ходе выхлопа дыма;
- повышенный расход топлива;
- снижение мощности двигателя;
- возникновение посторонних шумов;
- трудности с запуском двигателя;
- скачки такого важного показателя, как количество оборотов.
Несмотря на внушительный перечень возможных неисправностей, необходимо отметить, что качественно изготовленный ТНВД при грамотной эксплуатации является надежным и долговечным устройством. Следование приведенным выше рекомендациям и правильное использование топливного насоса гарантирует экономичную и эффективную работу двигателя в течение всего нормативного срока службы.
виды топливных насосов высокого давления, и принцип работы топливного насоса
Топливный насос высокого давления имеющий сокращенную аббревиатуру (ТНВД) выполняет следующие основные функции:
— подает топливо под высоким давлением в топливную систему ДВС;
— регулирует моменты впрыска топлива.
Топливный насос относится к наиболее важным устройствам, как бензиновых, так и дизельных двигателей.
ТНВД обычно применяются в дизельных двигателях. В бензиновых двигателях применение ТНВД нецелесообразно, ввиду того, что в нем не требуются такие высокие давления, как в дизельном двигателе.
Можно выделить следующие
основные конструктивные элементы топливного насоса:- Плунжер (поршень) + Цилиндр (втулка) = Плунжерная система (пара)
Плунжерная система изготавливается из высокопрочной стали на высокотехнологическом оборудовании (станках), в связи с необходимостью высокой точности.
Всего один завод на все пост Советское пространство изготавливал плунжерные пары. Изготовление плунжерных пар сегодня происходит таким образом.
Если внимательно изучить процесс производства плунжерных пар, то отчетливо видно, что огромное значение уделяют прецизионному сопряжению (зазор между плунжерной парой). Плунжер плавно входит в цилиндр под действием собственного веса.
Как изначально упоминалось, топливный насос служит не только для подачи топлива в топливную систему, но и подает его к форсункам на каждый цилиндр на бензиновом двигателе.
Форсунки являются связующим звеном этой цепи и соединяются с насосом специальными трубопроводами. Для эффективного впрыска топлива форсунки соединяются с нижней распылительной частью с специальными отверстиями для увеличения эффективности впрыска топлива с дальнейшим воспламенением. Момент впрыска топливной смеси в камеру сгорания регулируется углом опережения зажигания.
Типы топливных насосов
Существует три основных типа ТНВД, которые мы с вами рассмотрим:
- распределительный;
- рядный
- магистральный.
Рядный топливный насос высокого давления оснащен плунжерными парами, которые располагаются друг с другом. Их количество зависит от количества рабочих цилиндров двигателя и соответствует ему. Одна плунжерная пара обеспечивает подачу топлива только для одного цилиндра.
Пары устанавливаются в корпусе насоса, в котором имеются каналы входа и выхода. Плунжер приводится в работу при помощи кулачкового вала, который имеет привод от коленчатого вала.
При вращении кулачкового вала топливного насоса, кулачки воздействуют на толкатели плунжеров приводя их в движении внутри втулок насоса. Вследствие впускные и выпускные отверстия начинают последовательно открываться и закрываться. Когда плунжер движется вверх во втулке создается давление, которое приводит к открытию нагнетательного клапана, через который топливо подается к форсунке по топливопроводу.
Момент подачи топлива регулируется специальным устройством (муфтой центробежного типа). Работа муфты центробежного типа основана на перемещении грузиков под действием центробежной силы.
Центробежная сила изменяется по мере роста (или уменьшения) величины оборотов коленчатого вала двигателя, вследствие чего грузики расходятся к внешним краям муфты, либо сближаются к оси. Происходит смещение кулачкового вала относительно привода, что приводит к изменению работы плунжеров.
Когда обороты коленчатого вала увеличиваются – происходит ранний впрыск топлива, когда уменьшаются – поздний впрыск топлива.
Рядные топливные насосы зарекомендовали себя своей надежностью. Они совсем не привередливы к качеству топлива и смазка ТНВД осуществляется обычным моторным маслом.
Недостатки рядных топливных насосов высокого давления – их размер.
Распределительный ТНВДРаспределительный ТНВД включает в себя один или два плунжера, что зависит от объема двигателя.
И эти один или два плунжера работают на все цилиндры двигателя. Таким образом удалось не только обеспечить более равномерную подачу топлива, но и уменьшить габариты топливного насоса высокого давления. Недостатки распределительных ТНВД в их надежности и долговечности.
Распределительные ТНВД имеют различные типы привода:
- торцевой привод;
- внутренний привод;
- внешний привод;
Наиболее эффективными себя показали торцевые и внутренние приводы ТНВД, с меньшей нагрузкой.
Кстати, такие импортные насосы, как Bosch, оснащены именно торцевым и внутренним приводом, а внешний привод имеют насосы отечественного производства.
Основным элементом в торцевом приводе Bosch является распределительный плунжер, который создает давление и распределяет горючую смесь по цилиндрам. Плунжер распределитель при этом совершает вращательные и возвратно-поступательные перемещения при вращательных движениях кулачковой шайбы.
Плунжер совершает возвратно-поступательно движение одновременно с вращением кулачковой шайбы, которая обегает кольцо. Воздействие шайбы на плунжер обеспечивает высокое давление топлива. Возврат плунжера в начальное положение осуществляется с помощью возвратного механизма.
Именно вращательное движение плунжера, что приводится от приводного вала, способствует распределению топлива в цилиндрах. Величина подачи топлива обеспечивается с помощью электромагнитного клапана или центробежной муфты.
Работа насоса ТНВД
Работа насоса состоит из нескольких этапов:
- Закачка порции топлива в надплунжерное пространство;
- Нагнетание давления за счет сжатия и распределение топлива по цилиндрам.
- Возвращение плунжера в исходное положение. Повторение цикла работы.
Такой привод топливных насосов применяется в распределительных ТНВД роторного типа, например, Bosch VR, Lucas DPC. В данном типе ТНВД распределение горючей смеси происходит за счет плунжера и распределительной головки.
Распределительный вал оснащается двумя плунжерами, расположенными друг напротив друга, которые нагнетают топливо. Тем выше давление в насосе, чем меньше расстояние между плунжерами. По мере возрастания давления топливо поступает к форсункам через нагнетательные клапана.
Магистральный ТНВДМагистральный ТНВД используется в известной системе подачи топлива Common Rail. Работа магистрального ТНВД заключается в накапливании топлива в топливной рампе, затем подается на форсунки. Давление в магистральном топливном насосе высокого давления составляет примерно 180 Мпа.
Магистральный насос бывает одно-, двух- или трех плунжерным. Приводится магистральный ТНВД от кулачкового вала.
Когда кулачки воздействуют на плунжер, тот перемещается вниз, происходит расширение компрессионной камеры, давление падает и создается разряжение, которое приводит к открытию впускного клапана, и топливо начинает поступать.
Когда плунжер подымается – давление растет и клапан закрывается. Когда давление достигает необходимой отметки, топливо через выпускной клапан нагнетается в топливную рампу.
Процесс подачи топлива в магистральном ТНВД регулируется дозирующим топливным клапаном, открытие и закрытие, которого осуществляется с помощью электроники.
устройство, схема, принцип работы, характеристики
Основным узлом топливной системы дизельного двигателя является топливный насос высокого давления — ТНВД . Функцией узла является создание рабочего давления в системе, дозированная подача топлива к распылителям синхронно циклам работы двигателя в начале такта сжатия в каждый отдельный цилиндр с учётом режимов работы силового агрегата. Техническое состояние и регулировка узла прямо влияет на работу дизеля и создаваемую им мощность.
ТНВД трактора МТЗ 80
Трактора мтз 80(82) оснащаются ,в зависимости от года выпуска, топливными насосами в ранних комплектациях УТН 5 и более поздних 4 УТНИ, 4 УТНМ производства Ногинского завода топливной аппаратуры. По классификации данные узлы являются механическими со всережимным регулятором и корректором, имеют одинаковый принцип работы и конструкцию. Топливный насос трактора МТЗ 80 (82) установлен с левой стороны машины в передней части моторного отсека. Механический привод узла осуществляется через газораспределительную шестерню от коленчатого вала двигателя.
Марки ТНВД для тракторов МТЗ
Марка двигателя ММЗ | Марка ТНВД старой комплектации | Марка ТНВД новой комплектации |
Д-240 | 4 УТНМ-1111005 | 4 УТНИ-1111005-20 |
Д-243 | 4 УТНМ-1111005-110 | 4 УТНИ-1111005-20 |
Д-241 | 4 УТНМ-1111005-10 | 4 УТНИ-1111005 |
Д-242 | 4 УТНМ-1111005-20 | 4 УТНИ-1111005-10 |
Д-244 | 4 УТНМ-1111005-100-01 | 4 УТНИ-1111005-30 |
Д-245 | 4 УТНМ-Т-1111005 | 4 УТНИ-Т-1111005 |
Д-245.![]() | 4 УТНМ-Т-1111005-30 | 4 УТНИ-Т-1111005-30 |
Д-245.4, Д-245.5 | 4 УТНМ-Т-1111005-20 | 4 УТНИ-Т-1111005-20 |
Д-245Л-83, Д-245.1 | 4 УТНМ-Т-1111005-40 | 4 УТНИ-Т-1111005 |
Принцип работы топливного насоса МТЗ
Нагнетание топлива и создание рабочего давления осуществляется возвратно-поступательной работой плунжерных пар. В состав пары входит цилиндрическая втулка 4 и плунжер 3, выполняющий функцию поршня. Движение плунжерам передаётся вращением кулачкового вала 1 узла через толкатели 2. Всасывание топлива осуществляется из питающего канала в корпусе узла в надплунжерную полость через окно В во втулке при движении плунжера вниз. При набегании кулачка вала на толкатель , плунжер движением вверх и созданным импульсом давления, открывает нагнетательный клапан Е и пропускает дозированную порцию топлива непосредственно к распылителю.
схема работы плунжерной пары
Детали пары не имеют дополнительных компрессионных уплотнителей и давление создают за счёт высокоточной индивидуальной подгонки с точностью до микрона ( 1 микрометр= 1 метр* 10̄̄̄̄ ̄⁶).
В технической терминологии такие пары называются прецизионными и при эксплуатации пары деталей разукомплектовывать запрещено.
В технических учебных заведениях преподаватели для демонстрации подтверждения высокоточной подгонки прецизионной пары показывают небольшой опыт, основанный на принципе действия коэффициента теплового расширения материалов:
- Поршень – плунжер оставляют в руке, передавая детали температуру тела, а цилиндр-втулку плунжерной пары выносят на улицу с температурой ниже 0˚С .
- Затем по истечении 10 мнут части пары получают разницу температуры 36 — 40˚С, при этом втулка в границах коэффициента расширения под действием холода уменьшает свои линейные размеры, а плунжер от тепла руки увеличивает.
- В момент достижения потенциала разности температур преподаватель показывает невозможность вхождения плунжера в цилиндр втулки, тем самым доказывая высокую точность подгонки деталей.
Устройство ТНВД трактора МТЗ 80(82)
УТН 5 и 4 УТНИ представляют собой узел с рядным расположением четырёх секций плунжерных пар с присоединённым регулятором и подкачивающей помпой для преодоления сопротивления прохода топлива через фильтры при заполнении системы. Механизм насоса помещён в алюминиевом корпусе, к передней части которого присоединена чугунная плита для монтажа узла к двигателю. Задний фланец насоса соединяется с регулятором. Кулачковый вал вращается на двух подшипниках. Деталь имеет четыре кулачка для привода плунжеров и один эксцентрик для подкачивающего насоса системы.
Устройство ТНВД УТН 5
В задней части насоса размещён перепускной клапан, который пропускает лишне топливо, подаваемое подкачивающим насосом в его всасывающую полость. Таким образом, давление в головке топливного насоса поддерживается в пределах 0,07- 0,12 мПа обеспечивая бесперебойную подачу к плунжерным парам. В четырёх вертикальных сверлениях корпуса, расположенных в ряд, установлены толкатели с секциями плунжерных пар, каждая из которых работает как отдельный насос.
Секции оборудованы поворотным механизмом плунжера для осуществления изменения количества подачи топлива в автоматическом режиме при взаимодействии с регулятором. Для осуществления поворота каждая пара оснащена поворотной гильзой 14 с зубчатым венцом 6, который зацепляется с рейкой, связанной с регулятором насоса. На гильзу одета возвратная пружина 8 с упорными тарелками 7 и 12 нижняя часть, которой упирается в болт 11 толкателя 10, а верхняя в корпус насоса.
Корпус насоса оборудован боковым люком для регулировки подачи топлива отдельной секцией и контрольным отверстием с резьбовой пробкой для проверки уровня моторного масла в узле. В крышке регулятора установлен сапун с фильтрующим воздух элементом для сообщения внутренней полости насоса с атмосферой. В нижней части регулятора размещена сливная пробка.
Плунжерная пара
В состав каждой секции входит цилиндрический плунжер 13 со втулкой 5, выполняющей функцию цилиндра. Пара выполнена с высоколегированной термически закалённой стали, обеспечивающей повышенную прочность и плотность прилегания рабочих поверхностей. Верхняя часть втулки имеет утолщённое тело для устойчивости к высоким нагрузкам действующего созданного давления и имеет выступ для посадки в корпус. Втулка оборудована двумя окнами 18 и 19, через одно всасывается топливо в надплунжерную полость, а другое выполняет перепускную функцию для отсекания порции топлива. Оба окна соединены с продольными каналами в корпусе насоса. Для противодействия проворачиванию деталь фиксируется штифтом. Верхний торец втулки оборудован полированным седлом, к которому прижат отдельный нагнетательный клапан К секции.
Детали секции ТНВД
Каждый плунжер имеет две спиральные симметрично расположенные проточки. Одна предназначена для регулировки количества, подаваемого плунжером топлива путём поворота детали без изменения хода. При совпадении кромок перепускного окна втулки и проточки плунжера давление в надплунжерной полости резко падает и подача топлива через нагнетательный клапан к форсунке прекращается. Вторая проточка предназначена для обеспечения выравнивания удельного давления топлива, действующего на боковую поверхность плунжера при рабочем ходе детали. Таким образом, устраняется одностороннее действие сил во время впрыска, что значительно увеличивает рабочий ресурс прецизионной пары. В нижней части плунжера находится кольцевая проточка, в которую собирается просочившееся топливо из нагнетательной полости. Собранное топливо в проточке обеспечивает смазку пары. Основание плунжера оборудовано двумя выступами для управления его поворотом и упорной головкой для тарелки возвратной пружины.
Нагнетательный клапан
Клапан служит для разделения нагнетательной полости пары и трубки высокого давления идущей к форсунке, а также для резкого снижения давления в топливопроводе в конце подачи горючего плунжером. Это обеспечивает резкое прекращение подачи топлива без подтекания форсунки в конце впрыска. Детали клапана изготовлены из высокопрочной легированной стали индивидуально подобраны и тщательно притёрты. Разукомплектование деталей клапана при замене или ремонте, так как и плунжерной пары не допускается. Пружина, установленная сверху, прижимает пояски клапана к седлу и старается держать его в закрытом состоянии. Выше основного пояска, отделяющего надплунжерное пространство от трубопровода проточена разгрузочная канавка, которая при закрытии клапана забирает на себя часть топлива, находящегося в трубопроводе. Таким образом, снижается давление в трубке, что обеспечивает резкое прекращение впрыска.
Устройство нагнетательного клапана ТНВД
Подкачивающая помпа топливного насоса
В отдельном чугунном корпусе помпы размещён поршень, приводимый в движение толкателем из прочной легированной стали. Толкатель прижимается пружиной к приводящему его в движение эксцентрику кулачкового вала насоса. Стержень 13 толкателя двигается во втулке, ввёрнутой в корпус. Детали являются прецизионной парой и выполняет функцию основного рабочего органа подкачивающего устройства. Впускной и нагнетательный клапаны изготовлены из капрона. Направляющей впускного клапана является корпус 8 ручного подкачивающего устройства, а нагнетательного корпус 19. Клапаны прижаты пружинами к стальным втулкам, запрессованным в корпус устройства.
устройство подкачивающей помпы ТНВД
Всережимный регулятор топлива насоса
Автоматическое изменение количества подаваемого насосом регулируется устройством в зависимости от действующей нагрузки на двигатель. Принцип работы регулятора заключается во взаимодействии грузов размещённых на конце кулачкового вала насоса через муфту на систему тяг, связанных с поворотной зубчатой рейкой, управляющей поворотом плунжеров.
Механизм регулятора УТН 5
Ступица с четырьмя грузами 6 и муфта регулятора 5 с упорным подшипником 26 установлена на хвостовике кулачкового вала. На оси в нижней части корпуса регулятора установлены шарнирно соединённые основная 23 и промежуточная 22 тяги. Верхний конец промежуточной тяги связан с рейкой 11 ТНВД через тягу 14. Промежуточная тяга оборудована автоматическим корректором топливоподачи 20, который состоит из корпуса и размещённым в нём подпружиненного штока 17. Пружина 10 корректора-обогатителя связывает промежуточную тягу 22 и рычаг 9. Пружина 10 создаёт усилие, поворачивая тягу 9 для обогащения в пусковом режиме. Верхний край основной тяги 23 соединён пружиной 15 с рычагом 9 через серьгу 13, который жёстко соединён с осью рычага управления 29.
Задняя стенка оборудована ввёрнутым регулировочным болтом 19«наминала», который ограничивает амплитуду перемещения основной тяги 23 в сторону увеличения подачи топлива. Таким образом, ограничивается часовая производительность насоса. Болтом 18 регулируют остановку подачи топлива. В опорный прилив корпуса регулятора ввёрнут специальный болт 32, который ограничивает угловой поворот рычага управления 29, а следовательно, и частоту вращения двигателя.
Работа регулятора ТНВД
Параметры режимов работы регулятора устанавливаются путем регулировки механизма устройства и должны соответствовать эксплуатационным показателям силового агрегата согласно данным завода производителя.
Режим пуска
Рычаг управления 29 устанавливают в сторону максимальной скорости вращения до упора в болт 32. Рычаг 9 растягивает одновременно две пружины 10 обогатителя и 15 регулятора. Пружина 15 прижимает основную тягу 23 к головке регулировочного болта «наминала» 19, а пружина 10 обогатителя подаёт промежуточную тягу 22 с тягой 14 в сторону передвижения рейки для увеличения подачи топлива. (рис I) С увеличением частоты вращения после запуска двигателя, грузы на конце вала под действием центробежных сил расходятся и преодолевая усилие основной пружины 15 и обогатителя 10, передвигают муфту 5 назад. При этом тяга 22 перемещается, действуя на рейку насоса через тягу 14 в сторону уменьшения подачи топлива до установки оборотов холостого хода. (рис. II)
Схема работы режимов работы регулятора ТНВД
Рабочий режим
В случае достижения максимальной частоты вращения двигателем центробежная сила грузов регулятора уравновешивается пружиной 15 и рейка занимает промежуточное положение. При этом шток корректора 17 находится в утопленном состоянии, пружина обогатителя 10 сжата, тяги 22 и 23 прижаты друг к другу и работают как одно целое.(рис. II)
При увеличении нагрузки на двигатель до номинальной частота вращения уменьшается, вследствие этого центробежная сила на грузах снижается и муфта перестаёт воздействовать на промежуточную тягу 22. Основная тяга 23 при этом упирается в головку болта «наминала» и под действием пружины 15 перемещают рейку насоса в сторону увеличения подачи топлива.(рис III)
Схема работы режимов работы регулятора ТНВД
С достижением уровня номинальной частоты вращения устанавливается подвижное равновесие механизма регулятора. Усилие пружины 15 уравновешивают центробежные силы грузов, а основная тяга 23 касается головки болта «номинала».
При возникновении кратковременной нагрузки, превышающей номинальную, частота вращения двигателя и насоса резко снижается. Сила действия грузов на промежуточную тягу 22 падает. В этом случае пружина 7 в корректоре выталкивает шток 7 и упирается в основную тягу 23, в следствие чего, промежуточная тяга 22 вместе с рейкой под действием пружины 15 перемещается в сторону увеличения подачи топлива. Таким образом, крутящий момент двигателя возрастает и преодолевает нагрузку. (рис IV)
Корректировка подачи топлива при преодолении временных нагрузок в сравнении с подачей при номинальных оборотах происходит в пределах 15-22% и зависит от степени выхода штока из корпуса корректора, а также от степени натяжения пружины 14.
Режим остановки двигателя
Для остановки рычаг 29 управления переводят до конца в направлении часовой стрелки. При этом рычаг 9 под действием пружины регулятора 15 передвигает основную тягу 23 к задней стенке корпуса регулятора. Упираясь в ограничительный болт 18, тяга 23 увлекает за собой промежуточную тягу 22 и соответственно рейку насоса назад в сторону выключения подачи топлива.
Технические характеристики ТНВД для МТЗ 80 82
Показатели | УТН 5 | 4 УТНИ | 4 УТНМ |
Диаметр плунжера мм | 8,5 | 9 | 9 |
Ход плунжера мм | 8 | 10 | 8 |
Номинальная частота вращения вала ТНВД об/мин | 1100 | 1100 | 1100 |
Частота вращения, соответствующая холостому ходу дизеля об/мин | 1170 | 1160 | 1160 |
Частота вращения начала работы регулятора об/мин | 1115 | 1115-1125 | 1115-1125 |
Частота вращения максимального крутящего момента об/мин | 850 | 850 | 850 |
Частота вращения прекращения коррекции об/мин | 1040-1100 | 1040-1100 | 1030-1090 |
Цикловая подача топлива при 40-50 об/мин.![]() | 120 | 140 | 140 |
Частота вращения автоматического выключения подачи топлива к форсункам об/мин | 950 | 1210 | 1250 |
Неравномерность подачи топлива секциями % мин. частоте вращения/максимальной частоте | 6/30 | 6/30 | 6/30 |
Угол начала подачи топлива секцией по мениску до ВМТ( по профилю кулачка) | 57 | 57 | 57 |
Обслуживание ТНВД
В регламентные мероприятия по уходу за узлом входят:
- Проверка уровня масла в корпусе ТНВД производится через каждые 60 часов работы.
- Замена масла осуществляется с периодичностью 240 рабочих часов.
- Через каждые 960 часов производят проверку насоса на специальном стенде.
В процессе диагностики ТНВД проверяют следующие параметры:
- давление, создаваемое отдельной секцией
- производительность отдельной секции
- равномерность подачи топлива секциями
- производительность секций в режиме коррекции
- режимы работы регулятора
При выявлении несоответствия технических параметров, выдаваемых узлом в процессе проверки, производят регулировку или при необходимости ремонт узла с заменой, вышедших из строя деталей. Для осуществления ремонта, а также правильной настройки узла необходима соответствующая материальная база и специалист соответствующей квалификации.
Устройство и принцип работы ТНВД Bosch
ТНВД и ТННДНа чтение 4 мин. Просмотров 1.3k.
Рано или поздно любой водитель автомобиля может встретиться с проблемой поломки тнвд. В этой статье вы найдете всю основную информацию по теме как: устройство тнвд бош. Начинайте читать уже сейчас!
Топливный насос высокого давления относится к самым сложным узлам системы топливоподачи дизельных двигателей.
Принцип работы ТНВД заключается в подаче к цилиндрам дизельного двигателя в определенный момент и под определенным давлением точно отмеренных порций топливной смеси, которые соответствуют данной нагрузке.
В топливных насосах непосредственного действия проходит механический привод плунжера, а процесс момента впрыска и нагнетания проходят одновременно. Во все цилиндры секцией ТНВД подается необходимая порция топливной смеси. Необходимое давление для впрыска и распыления обеспечивает плунжерный насос. В представленной нами статье мы более подробно поговорим об данной детали производителя bosch, а именно рассмотрим такие довольно распространенные вопросы:
- Где купить ТНВД и комплектующие?
- Что такое топливный насос высокого давления?
- Устройство ТНВД;
- В чем заключается принцип работы ТНВД бош?
- Устройство рядного ТНВД бош;
- Как правильно разобрать ТНВД фирмы bosch?
- Плунжерный ТНВД bosch, его устройство и принцип работы;
- Принцип работы момента впрыска ТНВД фирмы bosch;
- Установка ТНВД bosch.
Основная информация о топливном насосе
Итак, в чем заключается принцип работы ТНВД? Принцип работы ТНВД фирмы бош, так же как и момент впрыска ничем не отличается от ТНВД других производителей. Основным элементом ТНВД фирмы бош является плунжерный насос. Топливный насос рассчитан на то, чтоб под большим давлением передавать определенную порцию топлива к двигателю и не допускать две крайности, такие как его недостаток и избыток. Поэтому поломки на которые владелец автомобиля может не обращать внимание или оценивать их как несущественные, могут привести к ремонту дизельного двигателя или полной его замене. Главным критерием, по которому топливные насосы разделяют на типы, является их устройство. Итак, на основании устройства топливных насосов их разделяют на такие типы:
- Распределительные. Оснащаются форсунками и регуляторами механического типа. Современные моторы оснащаются рядными ТНВД (топливный насос с высоким давлением) с электрическим управлением. Представленный тип насосов считается самым простым, хотя и отличается значительными размерами и весовыми характеристиками;
- Рядные. Оснащается одной или несколькими плунжерными парами, нагнетающими топливную смесь и распределяющими ее по цилиндрам. Данный тип намного меньше и легче по сравнению с рядными. Хотя такое преимущество приводит к некоторым недостаткам, например, быстрый износ деталей распределительного типа;
- Магистральные.
Как правило, они используются в системе впрыскивания commonrail. Их основной и единственной функцией является нагнетание топливной смеси в рампу. Количество плунжеров колеблется от одного до трех. В данном типе ТНВД также применяются такие детали как шайба или кулачный валик, приводящие плунжеры в действие.
Разборка и установление топливного насоса
Достаточно очевидным фактом является то, что без использования ТНВД подавать топливо к двигателю было бы сложно. Именно поэтому достаточно логично, что такому типу топливного насоса уделяется столько внимания автолюбителей, которые занимаются ремонтом моторов такого типа.
Ремонт тнвд boschСамыми распространенными причинами неполадок являются:
- Применение низкокачественного топлива, а это может привести к поломке топливного насоса. Для ТНВД применяется дизельное топливо, в качестве смазывающего материала для движущихся деталей и плунжерных пар. В случае загрязнения топлива разными примесями теряется смазывающее свойство, а это может привести к неисправности топливного насоса в дальнейшем;
- Износ топливного насоса;
- Проблемы с электрической техникой.
Неправильное функционирование электроники автомобиля может сказываться на нормальном функционировании остальных систем.
Для того чтобы качественно отремонтировать топливный насос высокого давления, необходимо знать как проводится разборка и установка, когда восстановление ТНВД невозможно и какие детали нуждаются в замене, для устранения неисправностей. Итак, как правильно проводится разборка и установка топливного насоса высокого давления?
- Открутите 4 винтика на торцевой стороне;
- Освободите кабель клапана опережения впрыска из-под прижимной пластины;
- Открутите 3 винтика, которые закрепляют прижимные пластины дозирующего клапана;
- Снимите дозирующий клапан;
- Открутите 2 винтика, которые закрепляют клапан угла опережения впрыска;
- Снимите клапан опережения впрыска;
- Открутите винтики, закрепляющие так называемые мозги;
- Отодвиньте мозги и открутите винтики, которые закрепляют датчик положения валика топливного насоса;
- Снимите мозги вместе с ливером;
- Установите на метку шкив и запомните расположение валика вместе с дозирующей иглой;
- С помощью двух плоских отверток, закладывая их попарно-диаметрально за уши, осторожно камеру вместе со штуцерами;
- Достаньте подшипник и пластинки;
- Открутите крышку автомата опережения;
- Достаньте автомат опережения впрыска;
- Установите поршень опережения так, чтобы во время поворота из него можно было извлечь кулочковую шайбу;
- Достаньте поршень опережения впрыска;
- Топливный насос разобран, а его сборка выполняется в обратном порядке.
GDI Принцип работы ТНВД GDI
10.09.2006
Непосредственный впрыск топливаДвигатель системы GDI
Во-первых, это большой шаг вперед для нашего с Вами понимания принципов работы ТНВД GDI, потому что нигде ранее и никогда ранее такой материал не публиковался.
Даже можно сказать громче: это революционная статья, ключ к пониманию многих процессов в ТНВД GDI.
А во-вторых, такой «простенький» на первый взгляд материал говорит об уровне «mek»…
(.

(Kublitsky Dmitry Jurjevich)
Топливный насос высокого давления (трехсекционный)
Принцип работы
1 – топливный бак
2 – топливный фильтр
3 — фильтрик
4 – компенсатор-ограничитель пульсаций топлива (низкое давление)
5 – перепускной клапан шарикового типа (низкое давление)
6 — пластины
7– перепускной клапан шарикового типа (высокое давление)
8 – пластинчатый клапан на линии сброса утечек из надплунжерного пространства
9 – компенсационная камера высокого давления
10 – топливная рейка
11 – фильтрик
12 – регулятор высокого давления

Под давлением около 0.3 MPa топливо проходит через топливный фильтр 2 и поступает в ТНВД через фильтрик 3, конструктивно расположенный в компенсаторе-ограничителе пульсаций
топлива 4.
Именно здесь происходит разделение топливных линий (магистралей).
Линия низкого давления:
1 – топливный бак
2 – топливный фильтр
Линия высокого давления:
1 – топливный бак
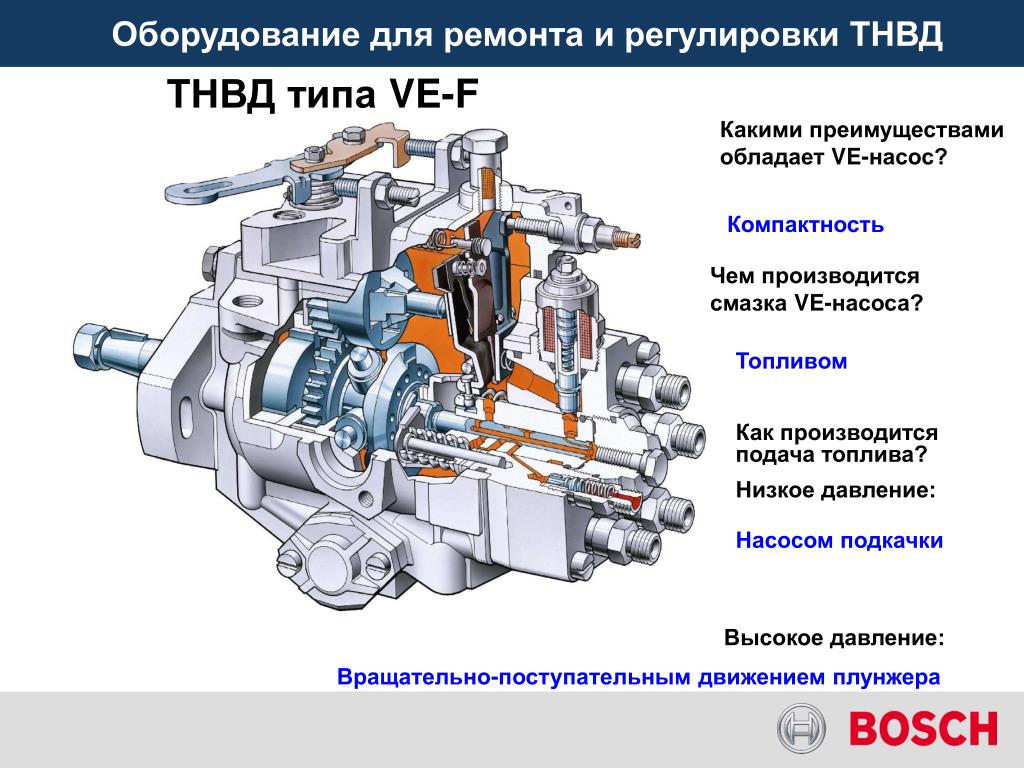

Этот снимок уже публиковался, но не лишне повторить его «в тему».
Возможные неисправности при «забитости» фильтрика:
- — плохой запуск двигателя и не с первого раза
— неустойчивая работа двигателя на ХХ
— неуверенное ускорение
— отсутствии режима «кик-даун»
— неправильный и нестабильный переход из режима работы на сверхобедненной топливной смеси в режим работы на стехиометрическом составе ТВС
Лирическое послесловие:
- Как показывает практика mek, бывало, и не так уж и редко, что при разборке ТНВД оказывалось, что внутри нет положенного «фильтрика».
Нонсенс, но правда.
А нет «фильтрика» — все….скоро к Вашему насосу придет старуха с косой за плечами и позовет его в дальний путь…
Она придет чуть позже и при таком состоянии фильтрика, как на вышеприведенном фото. Видите почему?
«Дырдочка». Наверняка причиной явились чьи-то «шаловливые ручки». -

«The Moscow center of diagnostics and repair of systems GDI»
(Kublitsky Dmitry Jurjevich)
Владимир Петрович
© Легион-Автодата
Потому что есть Увлеченность и желание стать Лучшими.
Более Лучшими.
Принцип работы дизельной системы — Denso
Система впрыска топлива находится в самом сердце дизельного двигателя. Система нагнетает и впрыскивает топливо в камеру сгорания с воздухом под большим давлением.
Система впрыска дизельного топлива включает в себя:
- ТНВД — нагнетает давление топлива
- Топливопровод высокого давления — подает топливо в топливную форсунку
- Топливная форсунка — впрыскивает топливо в цилиндр
- Топливоподкачивающий насос — подает топливо из бака
- Топливный фильтр — фильтрует топливо
В некоторых баках на дне фильтра находится седиметр, отделяющий воду от топлива.
Функции системы
Четыре основные функции системы впрыска дизельного топлива:
Подача топлива
Такие элементы насоса, как цилиндр и плунжер, встроены в корпус впрыскивающего насоса. Когда плунжер под воздействием кулачка поднимается, топливо под высоким давлением подается в инжектор.
Регулировка количества топлива
В дизельных двигателях забор воздуха происходит практически постоянно, вне зависимости от скорости вращения или нагрузки. Если количество впрыска меняется вместе со скоростью двигателя, а регулировка впрыска остается неизменной, то мощность и расход топлива изменятся. Эффективная мощность двигателя почти пропорциональна количеству впрыска, и это регулируется при помощи педали газа.
Установка момента впрыска
Задержка впрыска — это время между моментом впрыска топлива, зажигания и сгорания и моментом достижения максимального давления сгорания. Вне зависимости от скорости двигателя этот период времени остается постоянной величиной. Для изменения момента впрыска используется таймер, что помогает достичь оптимального сгорания.
Распыление топлива
Когда впрыскивающий насос нагнетает давление топлива, которое потом распыляется через распылитель форсунки, то топливо полностью смешивается с воздухом, что улучшает зажигание. Результат — полное сгорание.
Электронные системы управления рядными ТНВД
Рядный ТНВД с электронным управлением. Общий вид рядного ТНВД с электронным управлением: 1 – гильза; 2 – втулка управления; 3 – рейка подачи топлива; 4 –плунжер; 5 – кулачковый вал; 6 – электромагнитный клапан начала подачи топлива; 7 – вал управления регулирующей втулкой; 8 – электромагнитный регулятор количества топлива; 9 – индуктивный датчик положения рейки; 10 – вилочное соединение; 11 – диск; 12 – топливоподкачивающий насос.
Как и в обычном рядном ТНВД, оснащенном механическим регулятором, количество впрыскиваемого топлива является функцией положения управляющей рейки подачи топлива 3 и частоты вращения вала привода ТНВД. Управление рейкой осуществляется с помощью специального электромагнитного регулятора количества топлива 8, присоединенного непосредственно к ТНВД. Электромагнитный регулятор состоит из катушки и сердечника, воздействующего на рейку ТНВД.
Положение рейки насоса определяется индуктивным датчиком положения рейки 9, закрепленным на ней. В катушку электромагнитного регулятора, в зависимости от сигналов входных датчиков температуры двигателя, частоты вращения вала насоса, положения педали управления рейкой и др. от блока управления поступает ток возбуждения различной величины. При этом сердечник регулятора, втягиваясь под воздействием магнитного поля, воздействует на рейку насоса преодолевая усилие пружины, изменяя количество впрыскиваемого топлива.
С увеличением силы тока поступаемого от блока управления, сердечник, втягиваясь на большую величину и воздействуя на рейку, увеличивает подачу топлива. При отключении соленоида пружина прижимает рейку в положение остановки двигателя и прекращает подачу топлива.
На кулачковом валу ТНВД устанавливается зубчатое колесо, которое при вращении подает импульсы на индуктивный измерительный преобразователь. Электронный блок управления использует импульсные интервалы для вычисления частоты вращения коленчатого вала двигателя.
Датчик положения рейки подает сигналы для различных устройств на двигателе и автомобиле:
- сигнал о моменте переключения передач для гидравлической коробки передач; сигнал для подачи максимальной порции топлива скоординированной с давлением наддува для соблюдения норм на дымность отработавших газов;
- сигнал о нагрузке, как указание момента переключения для переключения передач в механической коробке передач;
- сигнал для измерения расхода топлива;
- сигнал для запуска рецеркуляции отработавших газов;
- сигнал диагностики и др.
Датчик положения рейки 1 – контрольная катушка; 2 – сердечник; 3 – короткозамкнутое подвижный контур; 4 – рейка; 5 – лыска; 6 – возвратная пружина; 7 – измерительная катушка; 8 – магнитопровод; 9 – неподвижный контур
Датчик состоит из пластинчатого стального сердечника 2 с двумя наружными открытыми концами. На одном конце закреплена измерительная катушка 7, которая запитывается переменным током 10 кГц, на другом конце контрольная катушка 1. Короткозамкнутый подвижный контур 3, предназначенный для регистрации хода рейки крепится к ней. Датчик хода рейки соединен с блоком управления.
Принцип работы датчика состоит в том, что короткозамкнутый неподвижный контур 9, окружающее конец сердечника, экранирует переменное магнитное поле (индукцию), вырабатываемое контрольной катушкой 1. Распространение магнитного поля ограничивается пространством между катушкой и короткозамкнутым кольцом. Учитывая то, что короткозамкнутое подвижное кольцо перемещается вместе с рейкой и изменяет своё положение относительно измерительной катушки, магнитное поле воздействующее на измерительную обмотку изменяется. Реагирующая цепь преобразует отношение индукции измерительной катушки 7 к индукции контрольной катушки 1 в отношении напряжений, которые пропорциональны ходу рейки. Величина измеряемого напряжения постоянно сравнивается с напряжением контрольной катушки. Датчик информирует о текущем положении рейки с точностью 0,2 мм.
Электронный блок управления сравнивает частоту вращения и другие параметры работы двигателя с целью определения оптимального количества подаваемого топлива (выражаемого как функция положения рейки). С помощью электронного контроллера сравнивается положение рейки насоса с конкретной точкой для определения значения тока возбуждения соленоида, который сжимает возвратную пружину. Когда отклонения определяются, регулируется ток возбуждения, обеспечивая смещение рейки насоса к более точному положению.
Подача топлива к форсункам принципиально не отличается от механических ТНВД. Однако в насосах с электронным управлением отсутствует муфта опережения впрыска и в них угол опережения впрыска управляется по сигналам, подаваемым от блока управления в электромагнитный клапан начала подачи топлива. В зависимости от величины силы тока поступающего в катушку электромагнитного клапана начала подачи топлива 6 (рис. ), его сердечник, преодолевая сопротивление пружины, втягивается в катушку на определенную величину, поворачивая при этом вал управления 7 регулирующей втулкой. В свою очередь вал управления связан с втулкой управления. При повороте вала управляющая втулка может приподниматься или опускаться. При обесточивании электромагнитного клапана вал под воздействием пружины переводит втулки в верхнее положение (поздний впрыск).
Начало подачи может регулироваться при изменении положения втулок в пределах до 40° поворота коленчатого вала. Принцип работы прецизионных деталей гильзы, плунжера и управляющей втулки показан на рисунке.
Принцип работы плунжерной пары с управляющей втулкой. a – НМТ плунжера; b – начало подачи топлива; c – завершение подачи топлива; d – ВМТ плунжера; h2 – предварительный ход; h3 – полезный ход; h4 – холостой ход; 1 – нагнетательный клапан; 2 – полость высокого давления; 3 – втулка плунжера; 4 – управляющая втулка; 5 – винтовая канавка плунжера; 6 – распределительное отверстие в плунжере; 7 – плунжер; 8 – пружина плунжера; 9 – роликовый толкатель; 10 – кулачок; 11 – разгрузочное отверстие; 12 – камера низкого давления.
Плунжер кроме обычной спиральной канавки изменяющей подаваемую порцию топлива к форсункам имеет распределительное отверстие 6, которое может быть закрыто или открыто управляющей втулкой 4. При движении плунжера вниз топливо поступает в надплунжерное пространство.
При движении плунжера 7 вверх, до тех пор, пока распределительное отверстие 6 находится в полости всасывания камеры низкого давления 12, давление в полости нагнетания 2 выравнивается с давлением во всасывающей полости через центральный канал.
Как только распределительное отверстие 6 плунжера перекрывается кромкой управляющей втулки 4 полость всасывания и полость высокого давления разобщаются (рис b) и давление в полости нагнетания начинает расти. После того как под воздействием высокого давления открывается нагнетательный клапан 1, давление в трубопроводе высокого давления растет до величины открытия иглы форсунки (начало впрыска).
Впрыск продолжается при движении плунжера вверх пока кромка спиральной канавки 5 не достигнет разгрузочного отверстия 11 (рис. с) в управляющей втулке 4. После этого давление в полостях выравнивается, и нагнетательный клапан 1 под воздействием пружины и давления топлива закрывается.
Регулирование начала впрыска топлива зависит от частоты вращения коленчатого вала, нагрузки на двигатель и его температуры. Начало впрыска топлива зависит от положения управляющей втулки, размещенной в кольцевой выточке гильзы. Изменение начала впрыска происходит одновременно во всех секциях насоса за счет поднятия или опускания управляющих втулок. Начало впрыска топлива зависит от положения управляющей втулки, так как нагнетание может произойти только после перекрытия распределительного отверстия плунжера 6, в противном случае топливо через вертикальный канал и отверстие 6 будет вытесняться полость 12 и давление в надплунжерном пространстве возрастать не будет. В момент перекрытия отверстия 6 полость в надплунжерным пространством становится герметичной и давление топлива начинает резко возрастать, открывая при этом нагнетательный клапан. Если втулка находится относительно отверстия плунжера 6 выше, впрыск начинается позже, так как позже будет перекрываться окно плунжера. При более низком положении втулки относительно окна плунжера перекрытие окна плунжера будет более ранним и впрыск начинается раньше. Ход втулки составляет около 5,5 мм при изменении угла опережения впрыска топлива 12° по углу поворота коленчатого вала.
Регулирование количества подаваемого топлива осуществляется как и у обычных механических ТНВД поворотом плунжера 7, на котором распределительное отверстие 6 соединено с винтовой канавкой 5 плунжера. Если плунжер повернут на небольшой угол, количество подаваемого топлива будет малым, так как спиральная канавка очень быстро после закрытия распределительного отверстие в плунжере 6 управляющей втулкой достигает разгрузочного отверстия 11 втулки. При большем повороте плунжера подача топлива соответственно увеличивается.
Прекращение подачи топлива осуществляется при останове двигателя. При этом плунжер устанавливается в такое положение, при котором в любой позиции между мертвыми точками полости всасывания и нагнетания соединены через центральное отверстие плунжера.
Основные неисправности рядных электронных ТНВД и их причины.
- Большинство неисправностей электронных рядных ТНВД, аналогичны механическим рядным ТНВД. Отличительными особенностями являются неисправности электронной части насоса.
- Двигатель не запускается. Повреждена обмотка электромагнитного регулятора количества топлива; неисправность блока управления; остальные неисправности характерные как и для механических рядных ТНВД.
- Блок управления двигателя включает программу аварийной работы, двигатель не развивает полной мощности. Замыкание обмоток катушек индуктивного датчика положения рейки или индуктивного датчика частоты вращения кулачкового вала ТНВД.
- Неправильное измерение частоты вращения. Биение зубчатого колеса импульсов более 0,03 мм.
00:4922.05.2013
Проверка механизма опережения на ТНВД H типа с дополнительной втулкой
Для определения работоспособности электромагнита опережения, регулировки втулок опережения, рекомендую выкрутить с регулятора заглушку, вставить внутрь отвёртку, упёршись в сам сердечник электромагнита и прогазовывать, наблюдая за перемещением вниз электромагнита. Чем раньше зажигание, тем ниже перемещается электромагнит. Можно также вручную делать зажигание раньше, имея достаточный опыт в работе дизельных двигателей.
Схема установки центробежной насосной станции (дожимной № 1 и …
Контекст 1
… три насосные станции (с подкачивающим, старым и новым главными насосами) расположены на одной территории, однако , в разных зданиях. Основная схема установки насосных станций показана на рис. 1. Дожимная насосная станция оборудована двумя одинаковыми центробежными …
Context 2
… внутри насосов и Управление трубопроводом осуществляется подкачивающим насосом с регулируемой частотой вращения 900-1500 об / мин.Минимально допустимый расход в трубопроводе — 700 м 3 / час, максимальный -1200 м 3 / час. Клапан, регулирующий расход, устанавливается за основной насосной станцией лицом к трубопроводу (другие клапаны на рис. 1 не показаны). Исходя из схемы работы насосов, подкачивающие насосы могут работать поочередно, однако технологический потенциал позволяет подключать их последовательно (изображение на рис. 1 не приводится) или параллельно. Основные насосы могут работать индивидуально или последовательно, однако не более двух насосов могут быть подключены и работать…
Контекст 3
… -1200 м 3 / ч. Клапан, регулирующий расход, устанавливается за основной насосной станцией лицом к трубопроводу (другие клапаны на рис. 1 не показаны). Исходя из схемы работы насосов, подкачивающие насосы могут работать поочередно, однако технологический потенциал позволяет подключать их последовательно (изображение на рис. 1 не приводится) или параллельно. Основные насосы могут работать индивидуально или последовательно, однако не более двух насосов могут быть подключены и работать…
Context 4
… созданных в опорах подшипников насоса, были измерены в вертикальном и горизонтальном направлениях (см. Рис. 4), в соответствии с требованиями стандарта ISO10816. Положения временно установленных датчиков давления Rosemount 2088 показаны на рис. 1 (M1, M2 и M3). Количество стационарных датчиков давления в трубопроводе достаточно велико; однако в настоящем исследовании использовались только два из них: один в трубе между насосными станциями и один в трубе за основной насосной станцией, обращенной к магистральному трубопроводу (см.рис.1, Т1 и Т2). Анализ вибрации проводился на основе …
Context 5
… установленных датчиков давления Rosemount 2088, показанных на рис. 1 (M1, M2 и M3). Количество стационарных датчиков давления в трубопроводе достаточно велико; однако в настоящем исследовании использовались только два из них: один в трубе между насосными станциями и один в трубе за главной насосной станцией, обращенной к магистральному трубопроводу (см. Рис. 1, T1 и T2). Анализ вибрации проводился на основе измеренных (10-1000 Гц) значений и спектров вибрации БПФ…
Контекст 6
… в трубопроводе показывает, что уровень вибрации обоих бустерных насосов значительно увеличился (до 7,94 мм / с). Уровень вибрации главного насоса №2 практически не изменился. Пульсации давления внутри трубопровода также не изменились (пульсации давления положения М2 уменьшились, так как клапан, не показанный на рис. 1, расположенный напротив датчика давления, был закрыт). Эти режимы работы показали, что основная причина пульсаций давления, возникающих внутри трубопровода, не связана с расходом от подкачивающих насосов.Два подкачивающих насоса во время еще одного экспериментального испытания были подключены последовательно (это технически возможно, хотя это не так …
Контекст 7
… расположенный напротив датчика давления, был закрыт). Эти режимы работы показали, что основная причина пульсаций давления, возникающих внутри трубопровода, не связана с расходом от подкачивающих насосов. Два подкачивающих насоса во время еще одного экспериментального испытания были соединены последовательно (это технически возможно, хотя на рис.1) и пущен в работу главный насос №1. Данные, представленные в таблице 2, показали, что уровень вибрации обоих подкачивающих насосов был не очень высоким (максимальное значение достигало 2,90 мм / с с третьей опорой подшипника насоса № 1), а в случае основного насоса № 1 — уровень вибрации незначительно отличался от других . ..
Контекст 8
… уровень подкачивающих насосов оставался относительно низким (максимальное измеренное значение — 2,65 мм / с 4-го подшипника насоса №1) .Очевидно, что при отсутствии работающих основных насосов пульсации давления в трубопроводе значительно снижаются (до 0,25 бар в положении M3). Спектры скоростей колебаний подкачивающего насоса представлены на рис. 10. Эти спектры демонстрируют, что в опорах подшипников этих насосов преобладают колебания с частотой 4Х. Результаты, полученные из этого рабочего режима, позволили определить, что кавитация, возникшая до достижения основных насосов (с 1-го по 8-й рабочий режим), в подкачивающих насосах, т.е.е. подкачивающие насосы не …
Контекст 9
… Экспериментальные испытания показали, что кавитация в трубопроводе возникла из-за неправильно проложенных трубопроводов между подкачивающей и главной насосной станцией (см. рис. …
Определение откачки и откачки
Что такое Pump-and-Dump?
Накачка и сброс — это схема, которая пытается поднять цену акции с помощью рекомендаций, основанных на ложных, вводящих в заблуждение или сильно преувеличенных заявлениях. Преступники этой схемы уже имеют устойчивую позицию в акциях компании и продают свои позиции после того, как шумиха привела к повышению цены акций. Эта практика является незаконной на основании закона о ценных бумагах и может привести к большим штрафам.
Ключевые выводы
- Накачка и сброс — это незаконная схема повышения стоимости акций на основе ложных, вводящих в заблуждение или сильно преувеличенных заявлений.
- Схемы откачки и сброса обычно нацелены на акции с микро- и малой капитализацией.
- Лица, признанные виновными в реализации схем откачки и откачки, подлежат наложению крупных штрафов.
Основы Pump-and-Dump
Схемы откачки и сброса традиционно реализовывались посредством холодных вызовов. Но с появлением Интернета эта незаконная практика стала еще более распространенной. Мошенники размещают в Интернете сообщения, побуждающие инвесторов быстро купить акции, с заявлениями о том, что у них есть внутренняя информация о том, что развитие событий приведет к скачку цены акций. Как только покупатели прыгают, злоумышленники продают свои акции, в результате чего цена резко падает.Затем новые инвесторы теряют свои деньги.
Эти схемы обычно нацелены на акции компаний с микро- и малой капитализацией, поскольку ими проще всего манипулировать. Из-за небольшого количества акций этих типов не требуется много новых покупателей, чтобы подтолкнуть их вверх.
Насосно-отгрузочная 2,0
Та же самая схема может быть применена любым человеком, имеющим доступ к онлайн-торговому счету и способным убедить других инвесторов купить акции, предположительно готовые к взлету. Планировщик может начать действовать, активно покупая акции, торгующиеся на небольшом объеме, что обычно приводит к росту цены.
Ценовое движение побуждает других инвесторов активно покупать, поднимая цену акций еще выше. В любой момент, когда злоумышленник чувствует, что давление покупателей готово ослабнуть, он может сбросить свои акции с большой прибылью.
Накачка в поп-культуре
Схема выкачивания и сброса стала центральной темой двух популярных фильмов, «Котельная» и «Волк с Уолл-стрит», в обоих из которых был представлен склад, полный биржевых маклеров телемаркетинга, раскидывающих грошовые акции. В каждом случае брокерская фирма выступала в роли маркет-мейкера и владела большим объемом акций компаний с весьма сомнительными перспективами. Руководители фирм стимулировали своих брокеров высокими комиссиями и бонусами за размещение акций на максимально возможном количестве клиентских счетов. При этом брокеры накачивали цену за счет огромных объемов продаж.
Когда объем продаж достиг критической массы, и покупателей больше не было, фирма сбросила свои акции с огромной прибылью. Это привело к падению цены акций, часто ниже первоначальной цены продажи, что приводило к большим убыткам для клиентов, поскольку они не могли вовремя продать свои акции.
Как избежать схем откачки и откачки
Инвесторам следует с осторожностью относиться к уведомлениям о том, что акции вот-вот начнут расти, особенно когда они поступают без запроса, независимо от того, насколько заманчиво это может быть. Рассмотрите источник и проверьте наличие красных флажков. Многие уведомления приходят от платных промоутеров или инсайдеров, которым нельзя доверять. Если в электронном письме или информационном бюллетене говорится только о шумихе и ничего не говорится о риске, это, вероятно, мошенничество. Всегда проводите собственное исследование акций, прежде чем делать вложения.
Комиссия по ценным бумагам и биржам (SEC) дает несколько советов, которые помогут не стать жертвой.
Реальный пример откачки и откачки
В исследовании, проведенном в 2018 году, изучалась распространенность схем накачки и сброса на рынке криптовалют — области, которая в основном не регулируется. Исследователи выявили более 3700 различных сообщений и сигналов, рекламируемых на двух популярных досках обмена сообщениями о криптовалюте в период с января по июль 2018 года, призывая инвесторов покупать определенные монеты.
Новая конструкция прерывистой откачки для скважин с дефицитом жидкости
Использование кривой мощности для получения карты динамометрического стенда
Рабочий насосный агрегат (PU) может отображать различные виды рабочих схем. Приведенный в действие электричеством, двигатель ПУ приводит в движение головку лошади вверх и вниз. Поскольку электрическая энергия преобразуется в механическую, любое изменение напряжения в точке подвеса можно определить по потреблению электроэнергии. Например, если полиуретан застревает в вертикальном движении или вязкость масла становится более вязкой, напряжение в точке подвешивания увеличится, увеличивая входную мощность.Напротив, если полиуретан протекает или вырывается из него, потребление энергии снижается. Таким образом, условия работы можно интерпретировать по кривой потребления энергии.
Изучая взаимосвязь мощности, крутящего момента и нагрузки, можно создать математическую модель между нагрузкой и электрической мощностью.
$$ E = 9549 \ frac {{N} _ {r} \ eta i} {{n} _ {m}} $$
(1)
$$ E = [\ frac {a} {b} {\ rm {P}} — \ frac {c} {b} {{\ rm {W}}} _ {b} (\ cos \, \ theta — \ frac {c} {a} \ frac {{a} _ {A}} {g})] \ frac {r \, \ sin \, a} {\ sin \, \ beta} — {W} _ {c} ^ {{\ prime}} r \, \ sin \, \ varphi $$
(2)
Соотношение между электрической мощностью и нагрузкой затем рассчитывается по двум приведенным выше формулам.
$$ P = f ({{\ rm {N}}} _ {{\ rm {r}}}) $$
(3)
Кривая смещения и карта поверхностного динамометра интерпретируются по углу поворота коленвала и кривой мощности, соответственно.
Получение динамического уровня жидкости с карты поверхностного динамометра
С помощью уравнения Гиббса можно интерпретировать карту динамометра насоса с карты динамометра поверхности 12 . Динамический уровень жидкости определяется как высота жидкости в кольцевом пространстве (как показано на рис.{2} g} $$
(9)
Следовательно, динамический уровень жидкости может быть получен из нагрузки и смещения карты наземного динамометра.
Закон изменения погружения
Убывающий закон погружения
Глубина погружения насоса в скважинный флюид равна глубине насоса за вычетом динамической глубины флюида. Когда ПУ начинает работать, глубина погружения высока. Погружение быстро уменьшается в начале всасывания. Когда погружение падает до определенного низкого уровня, жидкость в насосе также будет в низком уровне. Типичная убывающая кривая погружения показана на Рис. 2.
Убывающая кривая погружения в период эксплуатации.
Возрастающий закон погружения
Во время периода простоя, когда ПУ перестает работать, возрастающий закон погружения можно изучить с помощью характеристик притока скважины 2 . Разница давлений между поверхностью и забоями заставляет жидкость течь в забой скважины.А подъем жидкости в затрубном пространстве приводит к увеличению погружения. Повышение динамического уровня жидкости дополнительно увеличивает забойное давление, что снижает перепад давления и жидкость, поступающую в скважину. В конце периода остановки погружение приближается к плато. Оказывается, более длительный период простоя снижает совокупную добычу. Погружение скважин с дефицитом флюида сначала быстро увеличивается, а в конце стремится к устойчивому положению. Типичная возрастающая кривая в период простоя показана на рис.3.
Возрастающая кривая погружения в период остановки.
Определение периода эксплуатации скважины
После получения кривой убывания погружения из контролируемой электрической кривой, наклон области уменьшения рассчитывается для определения оптимального периода хорошей работы. Абсолютное значение уклона в выбранном временном интервале рассчитывается с начала эксплуатации скважины. Это повторяется до тех пор, пока абсолютное значение наклона не станет меньше заранее определенного значения (ε, как описано ниже), и период до этого момента записывается как рабочее время T 1 для работы скважины.Подробности показаны ниже.
После того, как полученная кривая уменьшения погружения равномерно разделена на N интервалов, наклон каждого интервала можно определить по записанным координатам двух соседних точек ((t 1 , h 1 ) и (t 2 , h 2 ) на рис. 4). ПУ перестает работать, когда абсолютное значение крутизны меньше определенного значения (ε 1 ), т.е. \ (| \ frac {{h} _ {2} — {h} _ {1}} {{t} _ {2} — {t} _ {1}} | \ le {\ varepsilon} _ {1} \); и этот момент записывается как T 1 , как показано на рис.4. Впервые ε 1 может быть получено на основе предыдущего опыта, затем ε 1 будет исправлено с помощью метода, описанного в этой статье. Таким образом, прежнее значение ε 1 можно было бы использовать для определения следующего нового ε 1 в конечном итоге.
Определение срока эксплуатации скважины по падающей кривой погружения.
Рисунок 5Определение периода остановки скважины по возрастающей кривой погружения.
Определение периода остановки скважины
Закон нарастания жидкости по глубине можно интерпретировать по характеристикам притока на забой. Из-за наличия трех фаз (нефть, газ и вода) в позднем периоде добычи здесь используется метод Petrobras для расчета добычи 13 .
$$ d {p} _ {wf} = \ rho gdh $$
(10)
$$ dh = \ frac {Qdt} {s} $$
(11)
Уравнение. (12) можно решить из уравнений. (10) — (11).
$$ \ frac {d {p} _ {wf}} {Q} = \ frac {\ rho g} {s} dt $$
(12)
Кроме того, общий выход жидкости рассчитывается по формуле.{2}] $$
(14)
Общий выход воды рассчитывается по формулам. (15) и (16).
$$ {q} _ {вода} = {J} _ {1} ({{\ rm {p}}} _ {{\ rm {r}}} — {{\ rm {p}}} _ {{\ rm {wf}}}) $$
(15)
$$ {J} _ {1} = \ frac {{q} _ {b}} {{p} _ {r} — {p} _ {b}} $$
(16)
Наконец, уравнение. (17) можно получить из уравнений. {2} -4WZ} $$
(23)
C в уравнении может быть решена при условии t = 0 и погружении в начале периода остановки.{2} -4WZ} $$
(26)
Кривую нарастания погружения можно построить с помощью математической зависимости между погружением и временем. После того как полученная кривая нарастания погружения равномерно разделена на N интервалов, наклон каждого интервала может быть определен по записанным координатам двух соседних точек ((t 3 , h 3 ) и (t 4 , h ) 4 ) на рис.5). ПУ начинает работать, когда абсолютное значение крутизны меньше определенного значения (ε 2 ), т.е.е .; \ (| \ frac {{h} _ {3} — {h} _ {4}} {{t} _ {3} — {t} _ {4}} | \ le {\ varepsilon} _ {2} \); и этот момент записывается как T 2 , как показано на рис. 4. Метод вычисления ε 2 такой же, как ε 1 .
Рисунок 6 Диаграмма рабочего процесса для определения оптимальной схемы прерывистой откачки.
Технический справочник — EnergyPlus 9.0
Интеграция системы и установки [ССЫЛКА]
Для интеграции моделирования системы кондиционирования воздуха с моделированием зон были разработаны методы моделирования воздушного контура системы и его взаимодействия с зонами из-за контроля температуры и относительной разницы между температурой зоны и температуры приточного воздуха.Аналогичная ситуация возникает при интеграции моделирования центрального объекта. Обычно центральная установка взаимодействует с системами через жидкостный контур между компонентами установки и теплообменниками, которые называются змеевиками нагрева или охлаждения. В EnergyPlus характеристики воздушных систем и установки взаимозависимы, поскольку моделирование совмещено. Выходные данные установки должны соответствовать входам системы и наоборот. То есть температура охлажденной воды, выходящей из установки, должна равняться температуре воды, поступающей в змеевики, а расход охлажденной воды должен удовлетворять непрерывности массы. Кроме того, управление змеевиком обычно необходимо для обеспечения того, чтобы значения переменных расхода охлажденной воды на входе и выходе из змеевика оставались в разумном диапазоне. Установки также могут взаимодействовать друг с другом, так что работа контура охлажденной воды и чиллера будет влиять на работу водяного контура конденсатора.
Текущая методология моделирования первичной системы [ССЫЛКА]
В моделировании HVAC в EnergyPlus есть два основных типа контуров: воздушный контур и контур установки.Предполагается, что воздушный контур использует воздух в качестве транспортной среды как часть системы обработки воздуха, в то время как контуры завода используют жидкую текучую среду по выбору пользователя (обычно воду). Контуры конденсатора — это особый случай контуров установки, которые предназначены для отвода тепла и отличаются немного разными вариантами управления и применяемыми типами оборудования. Пользователь может иметь любое количество циклов каждого типа в конкретном входном файле. Нет явных ограничений на количество циклов в программе — пользователь ограничен только компьютерным оборудованием.Скорость выполнения, естественно, зависит от сложности входного файла.
Заводские контуры далее делятся на «полупетли» или «полупетли» для организационной ясности и логистики моделирования (см. Рисунок «Соединения между основными контурами моделирования HVAC и полупетлями»). Эти субпетли или стороны полупетли представляют собой согласованные пары, состоящие из половины основного цикла завода. Производственные циклы разбиты на стороны спроса и предложения. Полуконтроль на стороне спроса станции содержит оборудование, которое создает нагрузку на основное оборудование.Это могут быть змеевики, плинтусы, излучающие системы и т. Д. Нагрузка воспринимается основным оборудованием, таким как чиллеры или бойлеры, на полупетле на стороне подачи. Каждая полупетля на стороне предложения должна быть подключена к полупетле на стороне потребления и наоборот. Аналогичная поломка присутствует в контурах конденсатора, где сторона потребления включает сторону воды конденсаторов чиллера, в то время как сторона подачи включает оборудование конденсатора, такое как градирни.
Разделение на два полупетля позволяет лучше обрабатывать и контролировать поток информации и моделирования во всей программе.Прямые связи между полупетлями контура воздуха, установки и конденсатора усилены компонентами с соединениями между различными типами основных контуров. Например, змеевики (нагревательные или охлаждающие) на самом деле представляют собой теплообменники со стороной воздуха и воды или хладагента. Воздушная сторона змеевика обрабатывается в воздушном контуре, где также поддерживается управление устройством. Жидкостная сторона змеевика обрабатывается на стороне потребления установки, которая передает потребности в энергии змеевика на сторону подачи установки.Все циклы моделируются вместе путем последовательного моделирования каждого полупетля в определенном порядке вызова. Общие итерации гарантируют, что результаты для текущего временного шага сбалансированы, а обновленная информация будет передана на обе стороны субконтур, а также на другую сторону соединений воздушного контура, таких как катушки.
Оборудование предприятия на полупетле описывается набором ответвлений для этого полупетля. Компоненты могут быть расположены на ответвлении последовательно, а ответвления — параллельно, с некоторыми ограничениями.На рисунке «Схема ответвлений для отдельных полупетлей предприятия» представлен обзор предполагаемой схемы расположения ответвлений для каждого полупетля предприятия. Ветви — это отдельные ветви в петлевой структуре. Таким образом, сегмент между точкой A и точкой B определяется как ответвление. , как и участок между точками E и F. Между делителем и смесителем может быть несколько участков (от C1 до D1 через Cn до Dn).
В каждом полупетле может быть только один разветвитель и один микшер. Таким образом, оборудование может быть подключено параллельно между смесителем и разветвителем, однако внутри любой отдельной ветви могут быть только компоненты, включенные последовательно, а не параллельно.Правила топологии для отдельных полупетлей допускают разумную степень гибкости, не требуя сложной процедуры расчета для определения фактических условий расхода и температуры. Обратите внимание, что, поскольку спрос и предложение завода разделены на два отдельных полупетля, чиллеры или котлы могут быть параллельны друг другу на стороне подачи, а змеевики могут быть параллельны друг другу на стороне спроса. Таким образом, ограничение использования только одного сплиттера и микшера на конкретном полупетле не является чрезмерным ограничением допустимых конфигураций.В некоторых случаях одна ветвь может использоваться для определения всего полупетля, но, как правило, полупетля должна иметь разделитель и микшер, даже если все оборудование в суб-контуре просто последовательно.
Кроме того, чтобы избежать необходимости в чрезмерно сложных процедурах решателя, существуют некоторые ограничения на размещение насосов в конкретном полупетле. Есть два основных типа насосов: циркуляционные насосы и насосы ответвления. Насос, который является первым компонентом в первой ветви (между A и B), называется «циркуляционным насосом», а любой насос в параллельной секции (между Ci и Di) называется «насосом ответвления». Самая простая и распространенная схема — наличие одного циркуляционного насоса на входе со стороны подачи. По запросу установки полуконтурные насосы можно размещать только во входном патрубке. Это позволит моделировать первично-вторичные системы. Для получения дополнительной информации о насосах и правилах их размещения см. Раздел «Система трубопроводов: подземные имитационные насосы» в этом документе.
По сути, каждая ветвь состоит из одного или нескольких компонентов, соединенных последовательно. В ветви есть системные узлы, в которых хранятся свойства в определенном месте контура (температура, энтальпия, расход и т. Д.).) в начале и конце ветви, а также между компонентами. Компоненты на ветви принимают условия узла на их входе и используют эту информацию, а также общую управляющую информацию для моделирования компонента и записи данных на выходе в узел, следующий за компонентом. Эта информация затем используется либо следующим компонентом в ветви, либо устанавливает условия выхода для ветви.
Хотя модель завода в EnergyPlus достаточно гибкая, в большинстве случаев топология системы завода в модели будет несколько отличаться от топологии реальной системы завода в здании.EnergyPlus ориентирован на моделирование энергоэффективности зданий в течение длительных периодов времени и не задумывается как полностью гибкая система, которая может напрямую моделировать любую реальную систему завода с ее полной сложностью и точной компоновкой. Учитывая проект реальной сложной производственной системы, разработчику модели, как правило, необходимо разработать более простую систему, которая соответствует возможностям EnergyPlus и стремится охватить вопросы, важные для моделирования энергопотребления. Подобно тому, как сложная геометрия должна быть упрощена в тепловые зоны для моделей энергии, сложные установки следует упрощать до наборов пар замкнутых полупетлей с разрешенными топологиями ответвлений.
Директор завода [ССЫЛКА]
Порядок вызоваPlant Half-Loop [LINK]
Поскольку в модели может быть несколько производственных контуров, которые зависят друг от друга, одна из задач менеджера завода состоит в том, чтобы определить соответствующий порядок вызова для полупетл. Первоначальный порядок вызова (и порядок, который всегда использовался до EnergyPlus версии 7) следующий:
1. Вызвать все полупетли на стороне спроса производственных контуров (в порядке объекта ввода)
2.Вызвать все полупетли на стороне питания производственных контуров (в порядке ввода объекта)
3. Вызвать все полупетли потребляемой стороны контуров конденсатора (в порядке входных объектов)
4. Вызвать все полупетли на стороне питания контуров конденсатора (в порядке объекта ввода).
Этот первоначальный порядок вызова затем пересматривается на этапе настройки выполнения программы, когда модели компонентов предприятия итеративно считываются, инициализируются и устанавливаются размер. Алгоритм основан на информации, предоставляемой моделями компонентов, которые соединяют контуры вместе.Компоненты регистрируют, что две стороны петли соединены, и объявляют, какая из них предъявляет требования к другой. Если полупетля подключена и предъявляет требования к другому циклу, то порядок вызова независимого требуемого цикла помещается непосредственно перед зависимым загруженным полупетлем. Например, модель компонента чиллера с водяным охлаждением сообщает, что сторона подачи контура охлажденной воды подключена к стороне потребления контура конденсатора и что контур охлажденной воды предъявляет требования к контуру конденсатора.Алгоритм менеджера предприятия является итеративным и многократно вызывает все полупетли в общей сложности четыре раза. После этого этапа настройки порядок вызовов фиксируется для остальной части моделирования.
Plant Flow Resolver [ССЫЛКА]
Обзор концепции преобразователя потоков растений [ССЫЛКА]
Важным аспектом процедуры решения в контурах установки является метод, используемый для определения скоростей потока жидкости в различных полупетлях. Это включает в себя обеспечение соответствия стороны предложения конкретной ситуации нагрузки и потока на основе моделирования контуров стороны спроса. Распределение нагрузки — это проблема, которую необходимо решить, а также то, как регулируются скорости потока и обновляются температуры. Эти вопросы обсуждаются в следующих нескольких подразделах, и описанные алгоритмы важны для того, как работает моделирование объекта.
На первом этапе менеджер контура предприятия вызывает соответствующий модуль для моделирования (в порядке потока) всех компонентов на каждой ветви контура, кроме разделителей и смесителей. На этом этапе каждый компонент будет устанавливать условия на выходном узле, включая температуру, расход, максимально допустимый (расчетный) расход, минимально допустимый (расчетный) расход, максимальный доступный расход и минимальный доступный расход.Это будет основано исключительно на собственной схеме управления компонентом, и, таким образом, каждый компонент сможет запросить столько (или меньше) потока, сколько необходимо.
На втором этапе диспетчер шлейфов разрешит поток на всех узлах и через все ветви локального шлейфа. Затем компоненты моделируются с исправленными потоками. Для этой итерации преобразователь потока устанавливает скорость потока через каждый компонент контура.
Общий расход контура [ССЫЛКА]
Модели установки определяют общий расход жидкости для каждого контура на основе динамических запросов и потребностей компонентов контура.Решатель потока проверяет запросы и потребности каждого полупетля и выбирает общую скорость потока. При моделировании отдельных компонентов установки они регистрируют свои запросы на поток жидкости, которые хранятся на входном узле (переменная, называемая MassFlowRateRequest). Эти запросы потока используются для двух целей: общих потоков цикла и разрешения параллельных потоков внутри разделителя / микшера. Для определения общего запроса потока цикла запросы отдельных компонентов дополнительно разделяются на три категории в зависимости от характера устройства.
1. Нужна подача и витки петли на
2. Требуется поток, если петля уже на
3. Возьмите любой поток, который у них есть.
Цикл будет выполняться вообще только в том случае, если есть запросы потока типа 1. Если есть запросы потока типа 2, они не включат цикл, но могут повлиять на общую скорость потока, если он уже включен из-за некоторых не- нулевые запросы типа 1. Запросы потока типа 3 не влияют на общую скорость потока в контуре.Эти классификации жестко запрограммированы и не могут быть изменены пользователем.
Управление насосом для контуров установки и конденсатора. [ССЫЛКА]
Насос — это просто компонент, который управляет потоком (также см. PipingSystem: Underground Simulation Pumps). . Его реакция зависит от нескольких различных условий. Всего существует три различных переменных решения, две из которых определяются пользователем. Этими тремя решающими факторами являются то, имеет ли насос постоянную или регулируемую скорость, будет ли насос работать непрерывно или с перерывами и есть ли запрос на общий расход в контуре. После определения общего запроса потока цикла моделирование знает, что цикл хотел бы сделать. Следующее, что он делает, — моделирует все циркуляционные насосы, чтобы увидеть, что они действительно могут обеспечить. Тогда общий расход в контуре ограничивается минимумом и максимумом, которые циркуляционные насосы могут обеспечить в это время. Насос с постоянной скоростью работает довольно просто. Если пользователь назначает насос с постоянной скоростью, который работает непрерывно, насос будет работать независимо от наличия нагрузки.Это может привести к добавлению тепла в контур, если никакое оборудование не включено. Если насос имеет постоянную скорость и работает с перебоями, насос будет работать на полную мощность, если будет обнаружена нагрузка, и отключится, если в контуре нет нагрузки.
Насос с регулируемой скоростью определяется с максимальной и минимальной скоростью потока, которые являются физическими пределами устройства. Если в контуре нет нагрузки и насос работает с перебоями, насос может отключиться. Для любых других условий, таких как контур, имеющий нагрузку, и насос работает с перебоями или насос работает непрерывно (независимо от условий нагрузки), насос будет работать и выбирать расход где-то между минимальным и максимальным пределами.В этих случаях, когда насос работает, он будет пытаться удовлетворить запрос потока для всего контура.
Во многих случаях первая оценка потока, запрашиваемая стороной спроса, имеет тенденцию быть довольно точной, и скорость потока не меняется в последующих итерациях. Однако, поскольку существует вероятность того, что катушки или какой-либо другой компонент могут запросить больший поток в будущих итерациях в течение того же временного шага, программа должна не только устанавливать скорости потока, но также поддерживать запись текущих максимальных и минимальных ограничений скорости потока.Эта информация важна не только для самого насоса, но и для другого оборудования, которое может контролировать свою скорость потока и, следовательно, требует знания пределов, в которых они могут работать. В общем, решение о том, какой установить максимальный и минимальный расход, напрямую зависит от типа насоса (с постоянной или переменной скоростью). Для насосов с постоянной скоростью максимальные и минимальные значения расхода одинаковы, и поэтому, если запрошенный расход не соответствует этому, другие компоненты должны либо иметь дело с расходом, либо должна быть доступна байпасная ветвь для обработки избыточного расхода.Для насосов с регулируемой скоростью максимальные и минимальные значения расхода устанавливаются в пределах, определенных пользователем.
Сторона подачи установки / конденсатора [ССЫЛКА]
Модели компонентов, таких как котлы, чиллеры, конденсаторы и градирни, моделируются на стороне подачи установки и в контурах конденсатора. Чтобы обеспечить возможность спецификации реалистичных конфигураций, менеджеры контуров завода были разработаны для поддержки параллельного и последовательного соединения моделей компонентов в контуре. Кроме того, менеджеры циклов были разработаны для поддержки обеих полудетерминированных моделей (например,грамм. модели оценки параметров ASHRAE Primary Toolkit [Pedersen 2001]) и модели «на основе спроса» (например, модели карты производительности BLAST и DOE2.1E). В результате менеджер контура должен иметь возможность моделировать модели, требующие массового расхода в качестве входных данных, и модели, которые рассчитывают массовый расход в качестве выходных данных — иногда в контексте конфигурации с одним контуром.
Чтобы достичь этих критериев проектирования, не прибегая к решателю сети потока на основе давления в части кода HVAC, для руководителя предприятия EnergyPlus был разработан основанный на правилах «преобразователь потока».Преобразователь расхода основан на следующих предположениях и ограничениях:
В каждом шлейфе может быть только один сплиттер и один микшер
Из-за того, что в данном контуре может быть только один сплиттер и один микшер, логически следует, что может быть не более одного байпаса на каждой стороне контура
Никакие другие компоненты не могут быть включены последовательно с байпасом, т.
е. ветвь, которая содержит байпас, может не иметь другого оборудования на этой ветке
Оборудование может быть подключено параллельно только между компонентами разветвителя и смесителя контура
Оборудование может быть соединено последовательно в каждом ответвлении петли
Расходы на отдельных ответвлениях будут контролироваться с использованием максимальных и минимальных доступных ограничений расхода
Резольвер потока использует простой алгоритм предсказателя-корректора для обеспечения непрерывности массы через разветвитель контура установки, как показано на следующем рисунке.
Как обсуждалось ранее, насос устанавливает общий массовый расход контура, задавая расход в первом ответвлении на стороне подачи. На втором этапе алгоритм прогнозирования вызывает моделирование каждой единицы оборудования в контуре, и они обновляют свои запросы массового расхода на основе текущих расходов, температур и запросов на распределение нагрузки. Менеджер цикла вызывает соответствующий модуль для имитации (в порядке потока) всех компонентов в каждой ветви цикла, кроме разделителей и смесителей.На этом этапе каждый компонент устанавливает условия на своем выходном узле, включая температуру, и устанавливает потоки компонентов на входном узле. Каждый компонент и ветвь классифицируются по типу управления потоком. До версии 7 это вводился пользователем, где объекты ветвления были помечены в пользовательском входном файле как модель типа АКТИВНЫЙ, СЕРИЙНЫЙ, ПАССИВНЫЙ или ОБХОДНОЙ. Начиная с версии 7 это жестко запрограммировано, и ввод больше не используется. Тип управления потоком АКТИВНЫЙ описывает модель предприятия на основе спроса, которая вычисляет массовый расход в качестве выходных данных.Когда АКТИВНЫЙ компонент выключен, отключает всю ветвь независимо от типа других компонентов в ветке. СЕРИЙНАЯ АКТИВНАЯ ветвь похожа на АКТИВНЫЙ компонент, за исключением того, что в ветке более одного АКТИВНЫХ компонента, поэтому два запроса компонентов могут противоречить друг другу, и поэтому она может не закрывать всю ветвь, когда компонент выключен.
Алгоритм разрешения потока одинаков как для АКТИВНЫХ, так и для ПОСЛЕДОВАТЕЛЬНЫХ компонентов, и в остальной части документа описание одного типа будет соответствовать и другому типу.Тип PASSIVE описывает полудетерминированную модель, которая моделируется с массовым расходом на входе. Тип BYPASS обозначает обход контура.
Алгоритм прогнозирования сначала устанавливает желаемую скорость потока для каждой ветви путем поиска АКТИВНЫХ компонентов на ветви. Первый компонент АКТИВНЫЙ в порядке симуляции устанавливает желаемый поток ветвления. Для ответвлений только с ПАССИВНЫМИ компонентами требуется расход между минимальным и максимальным допустимым расходом на ответвлении. Ветви с компонентом BYPASS имеют поток ветвления только тогда, когда все другие вместе взятые ветки не могут обрабатывать весь поток цикла.
Резолвер потока контура вносит все необходимые «поправки» в запрошенные потоки ветвления, чтобы обеспечить полную непрерывность контура. Если сохранение массы позволяет удовлетворить все АКТИВНЫЕ ветви, то оставшийся поток делится между ПАССИВНЫМИ ветвями и, в крайнем случае, БАЙПАСОМ. Если поток недостаточен для удовлетворения потребности ветвления, запросы АКТИВНОГО ветвления удовлетворяются первыми в том порядке, в котором ветки появляются в списке ветвей во входном файле.
Скорость потока определяется сначала для каждой отдельной ветви.Для каждой ветви программа циклически перебирает каждый узел ветви и определяет, каковы потоки запросов и ограничения потока. Предполагается, что наиболее строгие ограничения потока действительны для всей ветви независимо от типа компонента. Активным компонентам дается наивысший приоритет для запроса определенной скорости потока. Если в конкретной ветви имеется более одного активного компонента, то предполагается, что активный компонент в ветви с самым высоким запросом потока диктует запрос потока для всей ветви.
После того, как все ветви установили свои скорости потока и ограничения, разделитель и смеситель должны разрешить различные запросы потока. Смеситель и любая ветвь, следующая за смесителем, пассивны. Таким образом, все управление потоком происходит на разделителе. Разделитель сначала пытается суммировать максимальные и минимальные ограничения для всех активных ветвей, выходящих из устройства, и сравнивает их с ограничениями, действительными для ветви, ведущей в разделитель. Когда существует несоответствие между ограничениями на выходе и ограничениями на входе, при моделировании будут учитываться ограничения на входе из-за того, что насос в действительности управляет потоком в контуре.Поскольку ограничения насоса будут передаваться на сторону спроса со стороны предложения, предполагается, что змеевики или другие компоненты стороны спроса должны находиться в пределах границ насоса.
После того, как поток на разделителе разрешен, при необходимости можно отрегулировать скорость потока на ответвлении и ограничения между разделителем и смесителем. В некоторых случаях это будет обязательно для поддержания баланса масс на делителе. Когда скорость потока, выходящего из разделителя, не соответствует активным запросам ответвления, скорости потока отдельных ответвлений необходимо отрегулировать, чтобы обеспечить дополнительный поток или «дефицит потока». При наличии дополнительного потока избыточный поток сначала направляется через любую обходную ветвь, а затем направляется в пассивные ветви в порядке, обратном их появлению в списке выходов разделителя. Когда все эти ветви будут исчерпаны, а поток все еще будет избыточным, поток будет увеличен к активным ветвям, также в обратном порядке. Обратный порядок гарантирует, что ветвь, появляющаяся первой, имеет наивысший приоритет для получения запрошенной скорости потока.
Если потока недостаточно для удовлетворения всех активных запросов ветвления (т.е., «дефицит потока»), тогда расходы через байпас и пассивные ветви устанавливаются равными нулю. Расходы через активные ответвления затем будут уменьшаться в обратном порядке до тех пор, пока расход на выходе из разделителя не будет соответствовать имеющемуся потоку на входе в разделитель. Для дефицита потока контура установки байпасный и пассивный потоки ответвления также устанавливаются равными нулю, а расходы для каждого активного ответвления рассчитываются следующим образом:
˙mbr = ˙mbr_request˙mtot_request ∗ ˙mtot_available
где:
mbr = окончательная разрешенная скорость потока в ответвлении
˙mbr_request = запрошенный расход ответвления
˙mtot_request = запрос общего массового расхода контура
˙mtot_available = общий доступный массовый расход контура
Также необходимо контролировать ограничения потока на ответвлениях и компонентах, так как после изменения скорости потока компоненты должны быть повторно смоделированы с помощью контура управления (воздушный контур, оборудование зоны или сторона подачи установки). Контроллеры для этих компонентов должны знать, были ли изменены ограничения, чтобы при моделировании не происходило переключение между компонентом, запрашивающим поток, который насос не может удовлетворить, и насосом, затем сбрасывающим поток до того, который он может обеспечить. Обратите внимание, что как только скорость потока для любого компонента изменилась, это сигнализирует о необходимости повторно моделировать любой подцикл, с которым он может иметь косвенное соединение. В настоящее время это означает, что при изменении расхода на стороне потребности предприятия при моделировании необходимо пересчитать условия как в воздушном контуре, так и в суб-контурах оборудования зоны, поскольку змеевики и другое оборудование могут находиться по обе стороны от главного воздушного контура.Точно так же, если моделирование стороны потребления конденсатора приводит к изменению расхода через конденсатор чиллера, то сторона подачи установки должна быть запущена для повторного выполнения расчетов. Были приняты меры, чтобы избежать случаев, когда различные полупетли могут просто запускать повторное моделирование своих косвенных соединений в бесконечном цикле.
Емкость контура и нагрев насоса [ССЫЛКА]
Модель установки включает упрощенные методы моделирования емкости жидкости и повышения температуры из-за накачки и трения.При переходе от моделей установки на основе нагрузки или энергии к схеме на основе контура меняются как скорость потока, так и температура жидкости. Это означает, что необходимо контролировать большее количество степеней свободы. Обсуждаемая ранее концепция преобразователя расхода контролирует расход жидкости через компоненты и поддерживает общий баланс массового расхода через контур. Однако температуры все еще необходимо контролировать и моделировать. Можно ожидать, что чисто итерационная процедура сойдется к подходящим температурам контура, но процедура может стать медленной, чтобы сойтись в условиях, когда спрос изменяется быстро или компоненты предложения могут не иметь достаточной мощности для удовлетворения системного спроса.Эта ситуация в чем-то аналогична той, которая существует в связи между зоной и воздушной системой. В этом случае сходимость и стабильность итерационного решения были значительно улучшены за счет добавления тепловой емкости воздуха в зоне и другой быстро реагирующей массы внутри зоны. Основываясь на этом опыте, было решено добавить в модель контура установки тепловую емкость, чтобы получить выгоду от дополнительной стабильности. Поскольку тепловая емкость при взаимодействии зона / система относительно мала, необходимо было использовать численное решение третьего порядка.Хотя тепловая емкость жидкости контура установки относительно высока, потоки жидкости также обладают высокой теплоемкостью и могут быстро изменять температуру, простое решение первого порядка не было признано удовлетворительным, и требовалось точное аналитическое решение.
В реальных условиях часто бывает некоторая задержка между изменениями в условиях подачи и соответствующими изменениями в компонентах стороны спроса из-за перемещения жидкости по контуру с конечной скоростью.
Перекачивание жидкости по контуру увеличивает тепло жидкости за счет трения. Небольшое нагревание происходит в насосе и по всему контуру. Количество тепла равно работе, выполняемой насосом с жидкостью. Это так называемое насосное тепло является усложняющим фактором при моделировании установки, поскольку тепловое воздействие насоса изменяет нагрузку на основное оборудование. Необходим простой метод учета нагнетания тепла, который не увеличивает трудностей численного решения и (начиная с версии 7) в EnergyPlus это достигается путем включения тепла насоса в модель емкости контура.
Производственные контуры включают простую модель емкости контура для моделирования этих эффектов на основе модели резервуара с хорошим перемешиванием. Каждая полупетля имеет резервуар с хорошо перемешиваемым резервуаром, расположенный на его входе, как показано на рисунке [рис: модели резервуара-емкости]. Температура резервуара моделируется как функция массы резервуара, расхода жидкости на входе и температуры, а также тепла насоса. Энергия не теряется или не набирается из-за накопления в емкости контура.
Общий объем контура установки разделен на два резервуара на каждом входе полупетля.Для обычных контуров (без обычных труб) каждый резервуар составляет половину объема контура установки. Для обычных контуров трубопровода резервуар на входе стороны подачи имеет три четверти объема, а резервуар на входе стороны потребления — одну четверть. Каждому контуру установки назначается общий объем жидкости, вводимый пользователем, или процедура автоматического расчета на основе расчетного расхода. Размер тепловой емкости влияет на скорость восстановления из ситуаций, когда заданное значение не поддерживалось. Пользователь должен оценить объем жидкости на основе размера труб в контуре.Обратите внимание, что приблизительных оценок вполне достаточно. Емкость контура (м3) можно рассчитать на основе данных о размере трубы, но обычно это не известно. Если задана нулевая емкость, приведенная выше формулировка сводится к мгновенному обновлению температуры обновления потребности, а температура на входе потребности становится температурой на выходе подачи на предыдущем временном шаге. Если указана очень большая емкость, это может привести к нереалистичной временной задержке и может быть плохой ответ на изменения заданной температуры контура.Опция «автосчет» емкости контура устанавливает объем контура как произведение максимальной скорости потока контура и времени циркуляции контура (вводится пользователем, значение по умолчанию составляет 2 минуты).
Температура резервуара моделируется путем рисования контрольного объема и баланса энергии вокруг резервуара и решения для температуры. Температура каждого резервуара пересчитывается всякий раз, когда две полупетли соединяются вместе. История температуры резервуара сохраняется в конце временного шага моделирования.Уравнение модели для резервуара (и температуры на выходе) формулируется следующим образом:
Ttank, новый = ˙mcpTinlet + MtankcpTtank, oldtsys3600 + ˙QpumpheatmcP + Mtankcptsys3600
Температура резервуара в конце временного шага моделирования определяется с помощью аналитического подхода и выражается как
Tttank = ⎛⎝Tt − δttank − ˙mcpTinlet + ˙Qpumpheat˙mcp⎞⎠exp (−˙mcpMtankcpt) + ˙mcpTinlet + ˙Qpumpheat˙mcp
где:
Tt − δttank — температура резервуара с временным шагом предыдущей системы [° C]
Tttank — текущая температура бака и на выходе из бака [° C]
мкм — текущий массовый расход жидкости через резервуар [кг / с]
δt — длительность системного временного шага [секунды]
сП — теплоемкость жидкости [Дж / кг]
Mtank — масса воды в резервуаре [кг]
˙Qpumpheat — тепло, выделяемое насосом в баке [Вт]
При моделировании предприятий, использующих один из обычных режимов трубы для контуров установки, используется та же модель резервуара, но резервуары расположены по-разному и учитывают дополнительные соединения. Для обычных трубных ситуаций резервуары расположены на выходе из полуконтурного соединения с общими трубными соединениями после резервуара.
Средняя температура указывается как температура резервуара. Средняя температура определяется как значение интегральной функции температуры резервуара на интервале [ 0 , δt ].
−T = 1δt∫δt0Tttankdt = Mtankcp˙mcpδt⎛⎝Tt − δttank − ˙mcpTinlet + ˙Qpumpheat˙mcp⎞⎠ (1 − exp (−˙mcpMtankcpδt)) + ˙mcpTinlet + ˙Qpumpheat˙
Вход для преобразователя потоков растений [ССЫЛКА]
Вход, специально связанный с преобразователем потока, состоит из списка ветвей объекта и списка коннекторов объекта, как показано в справочнике ввода-вывода.Определенные пользователем имена связывают цикл предприятия с его ветвями (содержащимися в BranchList) и определяют разделители и смесители цикла, содержащиеся в ConnectorList. Синтаксис Connector: Splitter и Connector: Mixer, в свою очередь, определяет относительное соединение ветвей друг с другом в цикле.
Определение ответвления вводится при моделировании и порядке подключения для всех компонентов в ответвлении. В моделировании предполагается, что входной узел первого компонента, указанного в ответвлении, является входным узлом ответвления, а выходной узел последнего компонента, указанного в ответвлении, является выходным узлом ответвления.Примеры всего синтаксиса ввода показаны в Справочнике по вводу / выводу для соответствующего объекта.
Сводка схем распределения нагрузки [ССЫЛКА]
В EnergyPlus используется пять схем распределения нагрузки. На рисунке ниже показан алгоритм распределения нагрузки предприятия. Общая потребность в контуре рассчитывается и используется в подпрограмме ManagePlantLoopOperation для определения доступного оборудования на основе схемы диспетчерского управления, указанной пользователем.После того, как все доступные компоненты были идентифицированы, потребность в цикле распределяется между доступными компонентами на основе указанной пользователем схемы распределения нагрузки.
Схема ОПТИМАЛЬНАЯ сначала загружает каждый компонент до его оптимального коэффициента частичной нагрузки (указанного во входных данных). Любая оставшаяся потребность в контуре распределяется равномерно по всем компонентам. Схема UNIFORMLOAD сначала распределяет нагрузку равномерно между всеми доступными компонентами. Если некоторые компоненты не обладают способностью выдерживать равномерно распределенную нагрузку, оставшаяся нагрузка делится между оставшимися компонентами.Схема SEQUENTIALLOAD загружает каждый компонент по одному до полной загрузки, пока не будет удовлетворена потребность в цикле. Компоненты загружаются в том порядке, в котором они появляются в списке оборудования, указанном во входных данных. Схема UNIFORMPLR загружает все оборудование равномерно, поддерживая одинаковые коэффициенты частичной нагрузки для всего оборудования в списке оборудования. Если нагрузка ниже нагрузки, требуемой заводом для работы при максимальной минимальной частичной нагрузке компонента, последний элемент удаляется из каждого списка оборудования. Этот процесс повторяется до тех пор, пока установка не сможет работать при максимальной минимальной частичной нагрузке. Схема SEQUENTIALUNIFORMPLR загружает все оборудование в порядке, указанном в списке оборудования, на полную мощность, при этом все рабочее оборудование работает с одинаковыми коэффициентами частичной нагрузки.
Примечание: Для всех схем, если нагрузка для любого отдельного компонента меньше, чем нагрузка на компонент при минимальном PLR, модель отдельного компонента будет ложной нагрузкой или уменьшит рабочий цикл при работе с минимальным коэффициентом частичной нагрузки до тех пор, пока нагрузка не станет равной. встретились.
Сводка схем расчета потребности в контуре завода [ССЫЛКА]
В EnergyPlus есть две схемы расчета потребности в контуре завода. Имеются SingleSetPoint и DualSetPointDeadband ; SingleSetPoint используется по умолчанию, если это поле оставлено пустым в объекте PlantLoop. В схеме SingleSetPoint для Plant Loop требуется, чтобы диспетчер уставок установил единичное значение уставки, которое устанавливает Node% TempSetPoint. Примерами этого Менеджера заданных значений могут быть: объекты SetpointManager: Scheduled, SetpointManager: OutdoorAirReset и т. Д.Для схемы DualSetPointDeadband для Plant Loop требуется один или два диспетчера заданных значений, которые устанавливают высокие и низкие значения заданных значений для узла% TempSetPointHi и узла% TempSetPointLo. SetpointManager: Scheduled: DualSetpoint устанавливает как верхнюю, так и нижнюю уставки. В противном случае требуются два диспетчера заданных значений: один с переменной управления = максимальная температура, а другой — с переменной управления = минимальная температура. Примеры применимых менеджеров заданных значений включают: SetpointManager: Scheduled, SetpointManager: OutdoorAirReset, SetpointManager: FollowOutdoorAirTemperature и т. Д.Обратитесь к Справочнику по входам и выходам для правильного использования этих менеджеров уставок.
Схема расчета потребности в контуре завода определяет количество нагрева или охлаждения, необходимое для доведения температуры контура завода до заданного значения (ей). Когда это значение определено, схема распределения нагрузки, описанная в предыдущем разделе, принимает это значение и распределяет нагрузку на соответствующее оборудование. Схема расчета спроса определяет, как рассчитывается нагрузка.В следующем разделе приводится сводка двух алгоритмов и их использования.
Схема расчета потребности в контуре SingleSetPoint [LINK]
Схема SingleSetPoint для PlantLoop принимает значение, которое помещается в Node% TempSetPoint, и вычисляет нагрузку на нагрев или охлаждение, необходимую для получения этой уставки.
DeltaTemp = LoopSetPoint — LoopTempIn
LoopDemand = mdot * Cp * DeltaTemp
Знак запроса контура определяет, имеет ли контур охлаждающую или нагревательную нагрузку. Затем схема распределения нагрузки распределяет эту рассчитанную нагрузку на соответствующее оборудование.
Схема расчета потребности в шлейфе DualSetPointDeadband [LINK]
Схема DualSetPointDeadband для PlantLoop принимает значение, которое помещается в Node% TempSetPointHi, а Node% TempSetPointLo вычисляет нагревательную или охлаждающую нагрузку, необходимую для получения этой уставки; если в DeadBand, то нагрузка не рассчитывается. Нижеприведенный псевдокод показывает основу алгоритма.
! Рассчитайте потребность в петле
ЕСЛИ (mdot> 0,0) ТО
LoadtoHeatingSetPoint = mdot * Cp * (LoopSetPointLo - LoopTempIn)
LoadtoCoolingSetPoint = mdot * Cp * (LoopSetPointHi - LoopTempIn)
! Возможные комбинации:
! 1 LoadToHeatingSetPoint> 0 и LoadToCoolingSetPoint> 0 -> Требуется нагрев
! 2 LoadToHeatingSetPoint <0 & LoadToCoolingSetPoint <0 -> Требуется охлаждение
! 3 LoadToHeatingSetPoint <0 & LoadToCoolingSetPoint> 0 -> Зона нечувствительности
! 4 LoadToHeatingSetPoint> 0 и LoadToCoolingSetPoint <0 -> Невозможно
ЕСЛИ (LoadToHeatingSetPoint.
GT. 0.0 .И. LoadToCoolingSetPoint .GT. 0.0) ТОГДА
LoopDemand = LoadToHeatingSetPoint
ИНАЧЕ ЕСЛИ (LoadToHeatingSetPoint .LT. 0.0. И. LoadToCoolingSetPoint .LT. 0.0) ТОГДА
LoopDemand = LoadToCoolingSetPoint
ИНАЧЕ ЕСЛИ (LoadToHeatingSetPoint .LT. 0.0. И. LoadToCoolingSetPoint .GT. 0.0) ТО
LoopDemand = 0,0
ЕЩЕ
ВЫЗОВ ShowSevereError
КОНЕЦ ЕСЛИ
ЕЩЕ
LoopDemand = 0,0
КОНЕЦ ЕСЛИ
ЕСЛИ (ABS (LoopDemand)
Знак запроса контура определяет, имеет ли контур охлаждающую или нагревательную нагрузку.Затем схема распределения нагрузки распределяет эту рассчитанную нагрузку на соответствующее оборудование, если таковое имеется.
Схема работы установки и конденсаторного оборудования[ССЫЛКА]
Установки и контуры конденсатора должны иметь какой-либо механизм для управления работой контура и какое оборудование доступно в различных рабочих условиях. После того, как нагрузка контура рассчитана по условиям возврата со стороны спроса и с использованием заданного значения контура, эту нагрузку необходимо распределить для оборудования подачи в соответствии с вводом пользователя. В основном это делается по схемам работы.
Каждая схема работы должна иметь тип схемы работы, ее идентифицирующее имя и расписание, определяющее ее доступность. Первой схеме, фигурирующей в списке, предоставляется наивысший приоритет; вторая схема имеет второй по величине приоритет и т. д. Другими словами, если в соответствии с ее расписанием доступна первая схема работы, то она используется при моделировании для определения того, как работает установка или контур конденсатора. Если он недоступен, вторая схема работы в списке проверяется, чтобы увидеть, доступна ли она, пока не будет найдена схема с наивысшим приоритетом, которая также доступна.Подробную информацию о поле ввода см. В Справочнике по вводу и выводу.
Схема работы завода[ССЫЛКА]
Подробную информацию о поле ввода см. В Справочнике по вводу-выводу. Варианты схем управления установкой:
Неконтролируемый цикл работы [ССЫЛКА]
The PlantEquipmentOperation: Неконтролируемая схема использует полную мощность оборудования подачи и соответственно охлаждает или нагревает контур. Примером может служить градирня, в которой градирня будет охлаждать контур конденсатора со всей его доступной производительностью и не будет ограничиваться диапазоном производительности или уставкой.Неконтролируемая работа контура просто определяет группу оборудования, которая работает «неуправляемо». Если контур работает, это оборудование также будет работать, если оно не будет отключено резольвером потока контура для поддержания непрерывности в контуре жидкости.
Работа на основе диапазона нагрузки охлаждения или Работа на основе диапазона нагрузки нагрева [ССЫЛКА]
PlantEquipmentOperation: CoolingLoad (или PlantEquipmentOperation: HeatingLoad) определяет различные диапазоны и список оборудования, действительный для каждого диапазона.В каждом трио есть нижний предел диапазона нагрузки, верхний предел диапазона нагрузки и имя, которое связано со списком доступности оборудования (PlantEquipmentList). Работа в диапазоне нагрузок используется, когда рассчитывается нагрузка контура, а затем выбирается оборудование в надлежащем диапазоне. Это позволяет наиболее эффективно эксплуатировать оборудование предприятия или определять наиболее эффективную конфигурацию предприятия. Когда список оборудования обнаружен, нагрузка распределяется на оборудование способом, выбранным пользователем с помощью схемы распределения нагрузки «Оптимальная или последовательная».Схема работы, основанная на диапазоне нагрузки, имеет два связанных с ней оператора: основной оператор, который определяет диапазоны, в которых допустимы отдельные настройки приоритета, и списки оборудования, которое может использоваться для каждого диапазона.
[ССЫЛКА]
Это очень похоже на схемы работы установки, но есть еще несколько вариантов, доступных с CondenserLoop. Схемы работы конденсатора применимы к оборудованию на «стороне подачи» контура конденсатора - насосам, градирням, теплообменникам с заземлением и т. Д.Ключевые слова выбирают алгоритм, который будет использоваться для определения оборудования, доступного для каждого временного шага. Схемы «Работа на основе диапазона» выбирают указанный пользователем набор оборудования для каждого указанного пользователем диапазона конкретной переменной моделирования. « Нагрузка Диапазон На основе » Схемы сравнивают спрос на стороне подачи конденсатора с указанной нагрузкой диапазоны и списки сопутствующего оборудования. ' На открытом воздухе… На основе диапазона' Схемы сравнивают текущее значение параметра окружающей среды с указанными пользователем диапазонами этого параметра.Подробную информацию о поле ввода см. В Справочнике по вводу и выводу.
Неконтролируемый цикл работы [ССЫЛКА]
The PlantEquipmentOperation: Неконтролируемая схема использует полную мощность оборудования подачи и соответственно охлаждает или нагревает контур. Примером может служить градирня, в которой градирня будет охлаждать контур конденсатора со всей его доступной производительностью и не будет ограничиваться диапазоном производительности или уставкой. Неконтролируемая работа контура просто определяет группу оборудования, которая работает «неуправляемо».Если контур работает, это оборудование также будет работать, если оно не будет отключено резольвером потока контура для поддержания непрерывности в контуре жидкости.
Работа на основе диапазона нагрузки охлаждения или Работа на основе диапазона нагрузки нагрева [ССЫЛКА]
Оператор PlantEquipmentOperation: CoolingLoad (или PlantEquipmentOperation: HeatingLoad) определяет различные диапазоны и список оборудования, действительный для каждого диапазона. В каждом трио есть нижний предел диапазона нагрузки, верхний предел диапазона нагрузки и имя, которое связано со списком доступности оборудования (CondenserEquipmentList).Работа в диапазоне нагрузок используется, когда рассчитывается нагрузка контура, а затем выбирается оборудование в надлежащем диапазоне. Это позволяет наиболее эффективно эксплуатировать оборудование предприятия или определять наиболее эффективную конфигурацию предприятия. Когда список оборудования обнаружен, нагрузка распределяется на оборудование способом, выбранным пользователем с помощью схемы распределения нагрузки «Оптимальная или последовательная». Схема работы, основанная на диапазоне нагрузки, имеет два связанных с ней оператора: основной оператор, который определяет диапазоны, в которых допустимы отдельные настройки приоритета, и списки оборудования, которое может использоваться для каждого диапазона.
Работа на открытом воздухе с сухой лампой на основе диапазона, работа на улице с влажной лампой на основе диапазона, на улице с относительной влажностью, на основе диапазона [ССЫЛКА]
Различные утверждения «PlantEquipmentOperation: Outdoor *» определяют различные диапазоны различных параметров окружающей среды и список оборудования, действительный для каждого диапазона. После ключевого слова и идентифицирующего имени ожидается серия троек данных. В каждом трио есть нижний предел диапазона нагрузки, верхний предел диапазона нагрузки и имя, которое ссылается на список доступности оборудования («CondenserEquipmentList»).
Работа на открытом воздухе Drybulb на основе разницы температур. Эксплуатация на основе разницы температур с влажной лампой на открытом воздухе [LINK]
Различные стратегии управления заявлениями «PlantEquipmentOperation: Outdoor * Difference» помогают управлять любым конденсаторным оборудованием на основе разницы между температурой эталонного узла и любой температурой окружающей среды. Например, градирней можно управлять с помощью стратегии, которая учитывает разницу между температурой на входе в градирню и температурой по влажному термометру.Диапазон различий указывается для каждого списка оборудования.
Системы первичного-вторичного контура [ССЫЛКА]
Метод моделирования первично-вторичной системы в EnergyPlus называется Common Pipe.
Общая труба [ССЫЛКА]
Функция общей трубы устраняет необходимость указывать по два разных контура EnergyPlus для первичного и вторичного полупетлей. Вместо этого пользователь может настроить систему так, как она используется в реальных приложениях.Обычная симуляция трубопровода требует, чтобы насосы были размещены на обеих сторонах контура (вторичный) и приток (первичный). Типичная компоновка Common Pipe, используемая в EnergyPlus, показана на рисунке [fig: common-pipe-layout-schematic]. Основные допущения при реализации общей трубы следующие:
Насосы размещаются как на стороне спроса, так и на стороне предложения.
Расход вторичного насоса может быть меньше, равен или больше расхода первичного насоса.
Расход во входном узле полупетля равен потоку в выходном узле полупетля.
Насосы могут иметь разные расписания, и любой контур может быть отключен, когда другой контур все еще работает.
Симуляция общей трубы выполняется во время вызова обновления интерфейса как на уровне «предложение-спрос», так и «спрос-предложение». Соответствующие проверки используются, чтобы убедиться, что эффект разворота потока между итерациями учтен.Более того, общая труба отслеживает расход и температуру на всех четырех связанных с ней узлах; а именно входные и выходные узлы каждого вспомогательного контура. Эта запись поможет определить, сошлись ли петли или нет. В ситуациях, когда первичный компонент соответствует заданному значению, а элементы управления змеевиком не изменяют свой запрос потока, общая труба сходится быстро. Простое описание алгоритма управления для общей реализации Pipe выглядит следующим образом:
При FirstHVACiteration общий поток трубы инициализируется нулевым значением.
Общий канал моделируется на интерфейсах, поэтому у нас будет 2 разных обработчика потока с каждой стороны интерфейса.
Петли и соответствующие скорости потока назначаются на входе или выходе (для общей трубы) в зависимости от интерфейса, который их вызывает.
Таким образом, когда общая труба вызывается из интерфейса спроса и предложения, входной контур является стороной спроса, а выходной контур - стороной предложения, и наоборот.
Расход на входе сравнивается с расходом на выходе, и разница устанавливается как общий расход трубы.
На каждом интерфейсе потоку общего трубопровода назначается направление, которое может быть направлено внутрь интерфейса (входящий поток <выходной поток) или от границы раздела (входящий поток> выходной поток).
Температура на выходе рассчитывается в зависимости от расхода и направления потока. Когда поток находится вдали от границы раздела, температура потока на выходе такая же, как температура потока на входе. Для обычного потока в трубопроводе в границу раздела температура выходного потока рассчитывается как смешанная температура входящего потока и общего потока в трубопроводе.
В интерфейсе спроса и предложения температура и скорость потока на входе на стороне подачи обновляются каждую итерацию.
В интерфейсе спроса и предложения обновляется только поток. Температура обновляется только в конце временного шага.
Циклы повторяются до тех пор, пока расход и температура на всех 4 задействованных узлах не изменятся.
Двусторонняя общая труба [ССЫЛКА]
Доступна модель, называемая двусторонней общей трубой, которая позволяет моделировать первично-вторичные системы как единый контур предприятия.В типичном моделировании контура завода EnergyPlus единственным управляемым входным / выходным узлом полупетля является выходной узел стороны подачи. В некоторых случаях это требование становится ограничением при анализе различных вариантов. Хорошим примером является приложение для хранения тепла во льду, где на этапе зарядки уставка змеевика может отличаться от уставки оборудования для хранения льда. В этой модели интерфейс между двумя полупетлями включает в себя два дополнительных пути потока, которые по существу разделяют один контур установки на стороны первичного и вторичного контура. Несмотря на то, что двухсторонний общий трубопровод является общим, некоторые предположения применяются при моделировании компонента. Предположения следующие
Вторичный поток может быть меньше, равен или больше основного потока.
Массовый расход на выпускном узле первичной стороны всегда равен массовому расходу на впускном узле первичной стороны.
Массовый расход на выходном узле вторичной стороны всегда равен массовому расходу на входном узле вторичной стороны.
Можно управлять только одним дополнительным узлом, либо входом первичной стороны, либо входом вторичной стороны (вместе с узлом выхода первичной стороны / стороны подачи). Система уравнений, описывающая интерфейс контура, будет неадекватной, если необходимо управлять как первичным, так и вторичным узлами ввода.
На рисунке [fig: schematic-of-a-two-way-common-pipe-used-in] показана схема двусторонней общей трубы. Имеются два общих участка трубопровода, показанные пунктирными линиями, что обеспечивает некоторую рециркуляцию на уровне полупетля.Модель допускает общий поток трубы в одном или обоих направлениях. Модель определяет расход в обычных трубах и температуру в узлах на основе следующего:
Какой дополнительный узел контролируется для достижения заданного значения температуры? Если впускной узел первичной стороны управляется, то регулируются потоки для обеспечения желаемой температуры на впуске стороны подачи. Если впускной узел вторичной стороны управляется, то регулируются потоки для обеспечения желаемой температуры на впуске стороны потребления.
Достижимо ли указанное заданное значение при текущих условиях вторичного и первичного выхода? Если заданное значение недостижимо, то расход в каждом общем участке трубы уменьшается до минимально возможного значения.
На управляемом узле с известной выходной температурой по запросу, выходной температурой подачи, первичным расходом и вторичным расходом и балансом энергии используется для расчета рециркуляционных потоков в общих трубах для этого конкретного полупетля, так что желаемая уставка температуры Достигнут.
При известном расходе в одном общем участке трубы расход от первичного к вторичному (или от вторичного к первичному) легко получить с помощью баланса массы.
Когда двусторонняя общая труба контролирует условия на вторичной стороне или стороне потребления, входном узле, тогда модель емкости контура, обычно используемая для условий на входе потребления, не используется, поскольку это может помешать управлению.
Контурные системы рекуперации тепла [ССЫЛКА]
Рекуперация тепла достигается путем задания другого набора контуров спроса и предложения.Каждый из компонентов рекуперации тепла, то есть чиллеры с приводом от двигателя и турбины внутреннего сгорания, а также турбогенераторы внутреннего сгорания и внутреннего сгорания, спроектирован так, чтобы использовать существующую структуру компонентов / контуров / решений, чтобы облегчить моделирование с существующим менеджером стороны спроса и менеджером стороны предложения. Рекуперация тепла обычно содержит компоненты, которые выделяют тепло, которое может быть рекуперировано, а также возможность хранить или использовать это тепло в другом месте системы. Компонент, который может накапливать избыточное тепло и позволять использовать его в другом месте в системе или для горячего водоснабжения, - это Водонагреватель: Простой, он определен в Справочнике по входам / выходам.
.
В приведенном выше примере показан контур охлажденной воды, в котором охлажденная вода подается от чиллера с приводом от дизельного двигателя. Есть контур горячей воды, который подается от водонагревателя: простой. Также существует график использования горячей воды для бытового потребления на водонагревателе, избыточный спрос которого может быть удовлетворен за счет ряда источников тепла, указанных пользователем. Затем на стороне потребления контура рекуперации тепла есть чиллер с приводом от двигателя, электрические генераторы внутреннего сгорания и турбины внутреннего сгорания с заданными массовыми расходами для рекуперации тепла.Эта горячая вода подается на подающей стороне насосом рекуперации тепла и обеспечивает теплом водонагреватель для достижения заданного значения водонагревателя. Это, вероятно, одна из наиболее сложных конфигураций и взаимодействий, которые могут иметь место при рекуперации тепла, но с использованием конфигураций со стороны спроса и предложения станции ее можно расширить для удовлетворения большинства пользовательских конфигураций. Водонагреватель также можно использовать только для удовлетворения запланированного потребления горячей воды для бытовых нужд, обеспечения источника горячей воды для оборудования PlantLoop или обеспечения резервуара для хранения горячей воды для рекуперации тепла в качестве единственной функции.Или можно настроить любую комбинацию вышеперечисленного. Файлы примеров некоторых из этих конфигураций предоставляются с установкой.
Моделирование падения давления на заводе [LINK]
Начиная с версии 4.0, добавлена функция, которая позволяет лучше рассчитывать давление в контурах установки и конденсатора. Без какого-либо метода петли по существу игнорируют узловые давления. Это подходит для многих приложений, однако может привести к неточности в мощности насоса. Это особенно заметно в тех случаях, когда расход в контуре может резко меняться в широком диапазоне конфигураций, поскольку мощность насоса зависит от номинального значения мощности и номинального значения напора насоса.По мере того как компоненты контура включаются и выключаются, перепад давления будет изменяться, поэтому мощность насоса должна динамически обновляться с этими изменениями.
Общие характеристики модели: [ССЫЛКА]
Рассчитывает падение давления в контуре на основе информации о падении давления, размещенной на ответвлениях. Они вводятся в виде общих кривых (линейных, квадратичных) или информации о падении давления (незначительные потери / коэффициент трения).
Падение давления в контуре используется в качестве нового напора насоса.Информация о характеристике насоса не вводится, поэтому предполагается, что насос всегда сможет соответствовать этой рабочей точке. Будущие усовершенствования позволят насосу двигаться по кривой на основе заданного напора.
Модельне разрешает расходы на параллельных ветвях для соответствия падению давления, это объясняется ниже, но в основном она берет максимальное падение давления от параллельных компонентов давления и применяет его ко всем параллельным компонентам.
Модельподходит для следующих конфигураций:
Расположение насоса
Петлевой насос
Отводные насосы
Типы петель
PlantLoop
Конденсатор Петля
Впуск на стороне подачи (перед насосом) всегда настроен на стандартное атмосферное давление.Это позволяет давлению в узлах вокруг контура оставаться положительным. Фактические значения давления не так уж и важны, для наших расчетов интерес представляет дельта-давление, но это заставляет значения давления казаться реалистичными, если построить график давления вокруг контура.
Падение давления на уровне ответвления, а не на уровне компонента. Если на одном ответвлении обнаружено несколько компонентов, падение давления всегда применяется к последнему компоненту на ответвлении.Это согласуется с правилом, согласно которому насос всегда должен быть первым компонентом, если он находится в ответвлении.
В расчетах используются расход в ответвлении и температура на входе в ответвление для расчета свойств всей ветви.
Подробные ограничения: [ССЫЛКА]
Кривые падения давления нельзя размещать на ответвлениях, в которых есть только насос. Кривые давления могут быть нанесены на впускной патрубок подачи с насосом, если на том же патрубке после насоса есть другие компоненты.
При использовании насосов ответвления кривые падения давления на впускном патрубке подачи игнорируются. Поместите информацию о падении давления после насосов.
В настоящее время моделирование падения давления не допускается при моделировании обычных труб (насосов по запросу). Будущая версия системы падения давления позволит это сделать, позволяя каждому насосу справляться с падением давления на данной стороне контура (спрос или предложение).
Подробные шаги расчета: [ССЫЛКА]
Перед моделированием стороны потребления инициализируется система давления.Все давления в узлах сбрасываются, а значения перепада давления для ответвлений повторно инициализируются.
После моделирования всех компонентов ответвления рассчитывается падение давления для этого ответвления. Это падение давления регистрируется в системе падения давления для использования в последующих расчетах уровня контура.
После моделирования всего контура (со стороны спроса и предложения) расчеты падения давления на уровне контура выполняются с использованием следующих шагов:
Начиная с выхода на стороне потребления (связанного с входом подачи) и работая в обратном направлении, давление в узле обновляется, и давление в контуре суммируется путем «добавления перепадов давления», которые обнаруживаются вокруг контура.Работая в обратном направлении, мы можем легко сохранить давление на входе насоса как реальное значение (стандартное атмосферное давление).
Когда встречается параллельная система, выполняется специальная операция. Поскольку мы не разрешаем потоки с помощью этой версии моделирования давления, параллельная система настроена на использование наибольшего значения перепада давления, обнаруженного на параллельных ветвях. Таким образом, компонент с наибольшим перепадом давления, по существу, управляет набором параллельных ветвей, а другие компоненты должны соответствовать перепаду давления, чтобы достичь желаемой скорости потока.Для этого в разветвитель устанавливаются «воображаемые» вентили. Это позволяет отдельным ответвлениям сообщать свою собственную информацию о давлении, в то время как делитель учитывает необходимое падение давления для соответствия регулирующему ответвлению. Это показано графически на рисунке ниже.
Поскольку разделитель автоматически регулирует падение давления, необходимое для соответствия давлению в параллельной системе, в смеситель будет поступать и выходить равномерный поток со всех ветвей.
Эти расчеты выполняются вокруг контура и приводят к значению падения давления для всего контура.
Для мощности насоса требуется значение напора, прежде чем он сможет добавить тепло в контур, что выполняется до расчета каких-либо компонентов и выполнения любых расчетов системы давления. По этой причине мощность насоса рассчитывается исходя из номинального напора во время первой итерации. На последующих итерациях мощность насоса основывается на динамическом напоре, рассчитанном на основе информации о падении давления.
Если что-то радикально изменится между одной итерацией, то цикл будет повторно смоделирован, и будет использоваться последнее значение напора. К моменту схождения цикла давление между текущей и большинством предыдущих итераций согласуется с допуском моделирования. Таким образом, насос использует запаздывающее значение напора, но после схождения контура запаздывающее и текущее значения согласуются.
Расчет падения давления: [ССЫЛКА]
Можно ввести два типа кривых падения давления, каждый со своим собственным вычислительным механизмом:
Общий: Кривая любой формы (единственная независимая переменная), например линейная или квадратичная, может представлять падение давления в Паскалях как функцию текущего массового расхода в кг / с.Это обычное дело для регрессии падения давления компонентов, таких как тепловые насосы, в квадратичную форму наилучшего соответствия. Затем рассчитывается перепад давления на ответвлении путем оценки этой кривой с заданным расходом на ответвлении.
Информация о давлении: Этот расчет включает два типа перепада давления: эффекты трения и незначительные потери. Управляющее уравнение:
ΔP = (fLD + K) ρV22
Пользователь вводит значение для коэффициента малых потерь K, чтобы представить все незначительные потери в этой ветви.Если пользователь вводит информацию о трении, коэффициент малых потерь может быть нулевым или пустым.
Пользователь вводит шероховатость, e, или фиксированное значение коэффициента трения для учета потерь на трение на ответвлении, а также эквивалентную длину L. Если пользователь вводит шероховатость, коэффициент трения рассчитывается на основе аппроксимации диаграммы Муди (Хааланд , 1983):
f = − 1.8log⎡⎣ (e / D3.7) 1.11 + 6.9Re⎤⎦⎫⎬⎭ − 2
Если пользователь вводит информацию о незначительных потерях, то информацию о коэффициенте трения можно не учитывать.
Диаметр является эквивалентным значением и используется для расчета относительной шероховатости при расчете трения, а также скорости при любом расчете падения давления.
Кривые рабочего насоса для определения рабочей точки контура [ССЫЛКА]
Помимо возможности расчета падения давления в контуре, EnergyPlus также может выполнять определение расхода насосной системы «на уровне контура». Компоненты падения давления, которые были описаны в предыдущих разделах, объединены с вводом безразмерной кривой давления-расхода насоса, и на каждой итерации они используются для определения надлежащей рабочей точки для контура.
К этой симуляции применяются некоторые ограничения. Как и при моделировании базового падения давления, обычные трубы в текущей версии не действуют. Для этой фазы кривой насоса моделирование также ограничено «насосами контура», поэтому насосы не следует использовать на параллельных ветвях между смесителем и сплиттером.
Идея изменения характеристики насоса в том виде, в каком она реализована в настоящее время, основана на насосе с постоянной скоростью. Насос с регулируемой скоростью в EnergyPlus уже может эффективно изменять свои характеристики расхода / давления в соответствии с потребностями.Таким образом, этот этап реализован только для модели Pump: ConstantSpeed.
Модель работает, аппроксимируя цикл квадратичной формой падения давления, а затем повторяя итерацию, чтобы найти рабочую точку. Затем весь цикл предприятия повторяется, чтобы найти рабочую точку, которая пытается соответствовать запрошенным потокам. Обратите внимание, что при моделировании насоса на основе давления цикл, скорее всего, не будет достигать заданного значения на каждом временном шаге, в то время как выполнение более простого подхода (без давления) может привести к моделированию с более жестким контролем.Принимая это решение, вы должны учитывать реализм подхода, основанного на давлении, по сравнению с подходом без давления, который может быть более жестко контролируемым и потребует меньше входных требований.
На первой итерации установки еще недостаточно информации для определения моделирования давления-потока, поэтому расход через контур устанавливается равным номинальному расходу насоса (независимо от кривой производительности насоса). Для этого номинального расхода падение давления в каждой ветви будет рассчитано системой давления на заводе.Таким образом, после этого первого прохождения через контур система давления теперь имеет действительную точку потока и давления в системе. С этой точки (падение давления в ветви и номинальный массовый расход) рассчитывается постоянная давления для каждой ветви, предполагая квадратичную зависимость между падением давления и массовым расходом.
KB Ветвь (i) = ΔP Ветвь (i) / mRated2
Если есть параллельные ветви, эквивалент K рассчитывается по следующей формуле.
1√KParallelEquivalent = m∑j = 11√KBranch (j)
Из всех этих значений «K» ветвей вычисляется соответствующее значение K для полного цикла.Это репрезентативное значение K для цикла заблокирует системную кривую для одной итерации. Это значение K будет изменяться на протяжении итераций высокоуровневого объекта и временных шагов моделирования.
Безразмерная кривая насоса вводится следующим образом:
ψ = C4 × φ4 + C3 × φ3 + C2 × φ2 + C1 × φ + C0.
C1-4 - коэффициенты кривой с последним обязательным ненулевым постоянным членом C0 (так как кривая насоса не проходит через начало координат).
Безразмерные переменные в предыдущем уравнении определяются с помощью следующих выражений:
ψ - Безразмерный рост давления: ψ = ΔPρN2D2
φ - Безразмерный расход: φ = ˙mρND3
Пользователь предварительно преобразует значения массового расхода и давления в эти безразмерные формы, чтобы построить аппроксимацию кривой.Затем программа преобразует безразмерные формы в фактические значения на основе скорости насоса, диаметра и плотности жидкости. Это дает правильное соотношение давления и расхода для моделирования.
Резольвер потока рабочей точки насосной системы: [ССЫЛКА]
Компоненты падения давления и кривая насоса описаны в предыдущих разделах. Здесь описывается процедура, которая фактически использует эти кривые для перехода к рабочей точке. Эта процедура вызывается моделью насоса, поскольку она определяет, какой поток она должна использовать.Резольвер потока считывает безразмерную характеристику насоса, константу давления в контуре (значение K) и номинальный массовый расход (или массовый расход с последней итерации). Резольвер находит пересечение двух кривых путем последовательной замены с коэффициентом затухания 0,9. Если расход выходит за пределы (или если в какой-либо итерации выходит за пределы) диапазона, для которого предлагается подгонка кривой насоса, резольвер приведет значение в пределы диапазона, поэтому важно указать диапазон подбора кривой (в терминах безразмерного расхода) для характеристики насоса пользователем.Было замечено, что простая последовательная замена (иногда) расходится в зависимости от формы кривых и / или расположения рабочей точки. Коэффициент демпфирования обеспечивает стабильность для последовательной замены, и было замечено, что он сходится за меньшее количество итераций, ускоряя функцию. Коэффициент демпфирования был установлен равным 0,9, поскольку он показал полную стабильность во время испытаний, хотя для определенного набора кривых может быть доступно более оптимальное значение. В будущей версии может быть улучшен алгоритм выбора самого коэффициента демпфирования.
Источники [ССЫЛКА]
Хааланд, SE. 1983. «Простые и явные формулы для фактора трения в турбулентном потоке». Транзакции ASIVIE, Journal of Fluids Engineering 103: pp. 89-90.
Основы параллельного управления насосами
Многие современные насосы устанавливаются для работы в условиях переменного расхода, поэтому понимание концепции параллельного управления насосами является обязательным. Во-первых, очень важно знать, как параллельные насосы будут работать при установке.
Идея параллельно подключенных насосов заключается в способности добавлять или уменьшать пропускную способность и / или обеспечивать резервирование. На рисунке 1 показаны три параллельно подключенных насоса. Для целей этого обсуждения предположим, что все они имеют равную емкость. Кривые напор-производительность насоса показаны на рисунке 2.
Изображение 1 (слева). Три параллельно подключенных насоса. Изображение 2 (справа). Кривые напора насоса (изображения любезно предоставлены Grundfos)На этих рисунках показана установка с тремя насосами, часто называемая «триплексной» системой, в которой пропускная способность увеличивается путем включения дополнительных насосов.P1 показывает кривую напора для одного насоса. P1 + P2 показывает суммарный напор для двух насосов. P1 + P2 + P3 показывает суммарный напор трех насосов. Кривая управления, которая также напоминает кривую системы при 100-процентном расчетном расходе, показывает, что требуется системе трубопроводов с точки зрения расхода и напора.
Обратите внимание, что требуемый напор увеличивается с увеличением расхода. Обратите внимание на взаимодействие между кривыми напора-производительности насоса и кривой регулирования.
В течение многих лет эксперты учили на курсах по гидравлике насосов и подобных статьях, что производительность насоса не обязательно означает, что поток удваивается, когда работают два насоса одинаковой мощности.Этот момент часто подтверждается описанием того, что показано на Рисунке 3.
Изображение 3 (слева). Кривая системы начинается при нулевом расходе / нулевом напоре. Изображение 4 (справа). Напор, необходимый в системе, постояненНа изображении 3 показана кривая системы, которая начинается при нулевом расходе / нулевом напоре и увеличивается при увеличении расхода. Вы заметите, что пропускная способность, добавленная вторым насосом (Q 2 ), не равна пропускной способности (Q 1 ), обеспечиваемой первым насосом. Показанная здесь кривая системы представляет собой кривую чистого трения, при которой в системе трубопроводов нет статического напора или фиксированной управляющей головки.Поэтому становится более практичным показать кривую управления, которая представляет то, что фактически требуется в параллельной насосной системе.
На начальном этапе процесса выбора параллельного насоса мало внимания уделяется контрольной кривой. Например, если требуются расчетные условия 800 галлонов в минуту (галлонов в минуту) на 100 футов [182 кубических метра в час (м 3 / час) на 30,5 м], разработчик системы просто разделит 800 на число желаемых насосов. Таким образом, если требуется система с двумя насосами, каждый насос будет выбран из расчета 400 галлонов в минуту на высоте 100 футов (91 м 3 / час при 30.5 м).
В процессе выбора насоса расход удваивается при добавлении второго насоса. После установки, если поток двух насосов будет ровно вдвое больше, чем у одного насоса, величина напора, необходимого в системе, должна быть постоянной, как показано на рисунке 4. Кривая регулирования в этом случае будет прямой горизонтальной линией. Фактические насосные системы, которые напоминают этот тип кривой управления, представляют собой системы повышения давления с постоянным давлением для высотных зданий или циркуляционные системы, поддерживающие постоянный перепад давления на насосах.
Изображение 5 (слева). Реалистичная кривая управления. Изображение 6 (справа). Кривая управления не пересекает кривую производительности насоса 1.Более реалистичная контрольная кривая показана на рисунке 5. Вы заметите, что контрольная кривая пересекает кривую напора первого насоса при расходе, немного превышающем половину общего расчетного расхода QT. Эта контрольная кривая представляет собой конфигурацию большинства насосных систем с переменным расходом. Ключевым выводом из этого рисунка является то, что контрольная кривая пересекает обе кривые напора-производительности.После выбора параллельных насосов обеспечение того, чтобы кривая управления пересекала все подключенные насосы, поможет предотвратить проблемы управления после того, как насосы будут введены в эксплуатацию.
Что делать, если контрольная кривая не пересекает одну или все кривые напора-производительности насоса? Изображение 6 демонстрирует этот общий сценарий. Обратите внимание, что контрольная кривая не пересекает кривую напора для первого насоса. Во времена насосов с фиксированной скоростью это было реальной проблемой и обычно приводило к каким-либо изменениям оборудования, либо к модификации насоса, либо к какой-либо регулировке клапана.Но в сегодняшнем мире насосов с регулируемой скоростью такая ситуация представляет меньшую проблему и в большинстве случаев может быть решена без модификации оборудования. Решение может быть в виде программного обеспечения или логики управления насосом.
Когда для управления насосом используются приводы с регулируемой скоростью, полный возможный рабочий диапазон может быть показан на рисунке 7. Более темная заштрихованная область полного рабочего диапазона для насоса 1 и более светлая заштрихованная область - это комбинированный рабочий диапазон для обоих насосов. 1 и 2.
Рисунок 7. Рабочий диапазон при использовании частотно-регулируемых приводов для управления насосом.До сих пор мы рассматривали кривые напор-производительность насоса при полной скорости или номинальной скорости двигателя. Пунктирная линия на изображении 7 представляет производительность насоса при пониженной скорости, например 80 процентов. Для поддержания необходимого управляющего напора системы второй насос должен запускаться с этой скоростью или раньше. Как только контрольная кривая выходит за пределы рабочей области (темный оттенок) первого насоса, второй насос должен работать.Этого можно добиться разными способами с точки зрения последовательности насосов. Точка A на кривой показывает, где кривая управления системой выходит из рабочей зоны первого насоса. Нам известна некоторая информация по этому поводу: скорость насоса, расход насоса и напор насоса.
В этом случае два практических способа настроить последовательность: скорость или поток. Скорость - наименее затратный метод, так как эту информацию можно напрямую передать от частотно-регулируемого привода (ЧРП) в блок управления. Расход может быть измерен датчиком потока или рассчитан на основе информации о насосе, содержащейся в органах управления приводом.
Другой метод секвенирования, который может быть эффективным в этом случае, - это стадирование на основе эффективности. Поскольку КПД насоса в конце кривой обычно низок, второй насос включается задолго до того, как насос достигнет 80-процентной скорости.
Типы водяных насосов для строительства
Водяные насосы обычно используются на строительных площадках для обезвоживания или удаления излишков воды. Вода может накапливаться из-за проливных дождей или из-за высокого уровня грунтовых вод, а насосы позволяют быстро перекачивать воду, чтобы минимизировать время простоя.Для этого подходят водяные насосы двух основных типов: электрические, газовые, гидравлические или ручные.
Типы водяных насосов
Есть два основных типа водяных насосов: центробежные и поршневые. Оба типа предназначены для непрерывного перемещения воды из одного места в другое.
В центробежном водяном насосе используется вращающееся рабочее колесо для подачи воды в насос и повышения давления в нагнетаемом потоке. Центробежные водяные насосы бывают нескольких различных типов, включая стандартные, мусорные и погружные модели.С помощью центробежных водяных насосов можно перекачивать все жидкости, даже с низкой вязкостью. Эти насосы хорошо работают с жидкими жидкостями и обеспечивают высокий расход.
Водяные насосы прямого вытеснения обеспечивают постоянный поток за счет механического сжатия и расширения гибкой диафрагмы. Поршневые насосы используются во многих отраслях промышленности, где перекачиваются жидкости с высокой вязкостью и могут присутствовать чувствительные твердые частицы. Они рекомендуются для применений, требующих сочетания низкого расхода и высокого давления.
Рекомендации для центробежных водяных насосов
Центробежные насосы используются во многих сферах строительства и водоснабжения, помимо водоотведения. Они используются для перекачивания воды в зданиях, совместимы с пневматическими системами и там, где не требуется высота всасывания. Они также используются для откачки воды из бытовых колодцев и для повышения давления в водозаборных линиях. Центробежные насосы могут служить источником постоянного давления для систем противопожарной защиты, и они могут служить в качестве отстойных насосов в вертикальной или горизонтальной конфигурации.
Центробежные насосы подвержены ряду общих проблем. Некоторым насосам может потребоваться рециркуляция жидкости для предотвращения перегрева, вызванного низким расходом. Для правильной работы центробежные насосы должны быть залиты или заполнены перекачиваемой жидкостью. Когда положительный напор всасывания системы слишком низкий для выбранного насоса, это может привести к кавитации, состоянию, при котором пузырьки воздуха образуются возле рабочего колеса, что приводит к возникновению ударных волн внутри насоса. Наконец, износ рабочего колеса насоса может усугубляться наличием взвешенных в жидкости твердых частиц.
Рекомендации для поршневых водяных насосов прямого вытеснения
Объемные водяные насосы, иногда называемые ротационными насосами, очень эффективны из-за того, что они удаляют воздух из трубопроводов и, таким образом, устраняют необходимость стравливания воздуха. Эти насосы также эффективны для перекачивания жидкостей с высокой вязкостью.
Основным недостатком поршневых насосов прямого вытеснения является то, что они требуют очень небольшого зазора между вращающимся насосом и внешним краем агрегата.В результате вращение должно происходить с очень низкой скоростью. Если насос работает на более высоких скоростях, жидкости могут разрушиться и в конечном итоге снизить эффективность водяного насоса.
Водяной насос Особенности и характеристики
При выборе водяного насоса для строительства необходимо учитывать несколько важных факторов:
- Мощность - включая расход и мощность
- Материал - атмосферостойкие материалы, необходимые для открытых приложений
- Тип двигателя / тип топлива: электрический, газовый, дизельный, гидравлический или ручной
- Напор - общий или максимальный напор мощность насоса, подходящая для предполагаемого применения
Справочник по воде - Системы подачи химикатов
Хорошо спроектированная система подачи является неотъемлемой частью эффективной программы очистки воды.Если система подачи не спроектирована должным образом, химический контроль не будет соответствовать спецификациям, результаты программы могут быть неадекватными, а эксплуатационные расходы, вероятно, будут чрезмерными. Некоторые из дорогостоящих проблем, связанных с плохим химическим контролем, включают:
- Высокие химические затраты из-за проблем с перекачкой
- Непостоянное качество продукции, снижение производительности и более высокие затраты на пар и электроэнергию из-за загрязнения на воде
- с высокой скоростью коррозии и вытекающим из этого техническим обслуживанием и заменой оборудования (т.е.е. закупорку или замену корродированных трубок или пучков теплообменника)
- Высокие затраты на рабочую силу из-за чрезмерного внимания оператора
- Риск серьезного и широко распространенного повреждения технологического оборудования из-за плохого контроля или утечки кислоты в градирни
Значительные инвестиции в систему подачи химикатов часто могут быть оправданы по сравнению с высокой стоимостью этих проблем управления. Когда система подачи химикатов не спроектирована должным образом, уровни химикатов часто выше или ниже программных спецификаций.Использование правильной системы кормления может предотвратить эту ситуацию.
Системы подачи химикатов можно классифицировать по используемым компонентам, типу подаваемого материала (порошок или жидкость), применяемой схеме управления и применению.
КОМПОНЕНТЫ СИСТЕМЫ ПОДАЧИ
Химический склад
Химические вещества для обработки обычно доставляются и хранятся одним из трех способов: навалом, полубухой и бочками. Выбор из этих трех зависит от ряда факторов, включая интенсивность использования, требования безопасности, правила перевозки, доступное пространство и потребности в инвентаре.
Склад навалом. Крупные пользователи часто находят выгодным осуществлять доставку и хранение жидких химикатов оптом. Обработка жидкости доставляется автоцистерной поставщика или обычным перевозчиком. Большой резервуар, часто поставляемый компанией по очистке воды для хранения очищенной жидкости, размещается на территории пользователя рядом с точкой подачи (рис. 35-3). Представители сервиса часто берут на себя все функции управления запасами.
Очистка может быть получена из этих резервуаров для хранения и закачана непосредственно в водную систему или добавлена в меньшую емкость для вторичного питания, которая служит дневным резервуаром.Дневные резервуары используются в качестве защиты, чтобы предотвратить случайное опорожнение всего материала из основного резервуара для хранения в систему. Они также предоставляют удобный способ измерения дневной нормы использования продукта.
Полубалочное хранилище. Если скорость подачи химикатов недостаточно велика, чтобы оправдать доставку и хранение навалом, химикаты могут поставляться в многоразовых челночных цистернах (рис. 35-4). Обычно эти резервуары конструируются таким образом, что их можно штабелировать или размещать наверху постоянного основного резервуара для легкого заполнения основного резервуара под действием силы тяжести.
Барабан для хранения. Хотя бочки на 40 и 55 галлонов широко использовались для доставки химикатов всего несколько лет назад, растущие экологические проблемы резко сократили их использование. Ограничения на утилизацию бочек и утилизацию бочек снизили популярность этого метода доставки и хранения в пользу многоразовых или возвратных контейнеров.
СИСТЕМЫ ДОСТАВКИ
Системы доставки - это сердце системы подачи химикатов. Наиболее часто используемая система подачи - это дозирующий химический насос.Почти 95% всех систем подачи используют насосы-дозаторы. Однако гравитационная подача становится все более популярной в системах водяного охлаждения. Иногда используются эдукторы.
Дозирующие насосы
Наиболее часто используемые насосы-дозаторы для водоподготовки - это плунжерные, поршневые и диафрагменные насосы с набивкой. Иногда также используются роторные шестеренчатые и винтовые насосы. Все они относятся к категории «поршневые насосы прямого вытеснения».
Конструкция и выбор дозирующего насоса и контура трубопровода имеют решающее значение для обеспечения соответствия производительности насоса техническим характеристикам.Параметры, которые необходимо учитывать, включают статический напор на стороне всасывания, чистый положительный напор на всасывании (NPSH), динамический диапазон насоса, возможное сифонирование, сброс давления и совместимость материалов.
Для обеспечения точной перекачки рабочие условия должны быть близки к проектным. Например, в случае плунжерного насоса увеличение давления в линии нагнетания может значительно снизить производительность насоса. Поскольку на производительность насоса влияет множество факторов, производительность следует часто проверять с помощью калибровочного цилиндра.Некоторые компьютеризированные системы подачи химикатов автоматически проверяют производительность дозирующего насоса и при необходимости вносят коррективы.
Плунжерные насосы с набивкой. Поскольку плунжерные насосы могут быть рассчитаны на высокое давление нагнетания, они часто используются для химической обработки в котельных системах. Перекачивающее действие осуществляется поршнем прямого действия или плунжером, который возвратно-поступательно движется вперед и назад и непосредственно контактирует с технологической жидкостью внутри замкнутой камеры. Скорость двигателя и / или длина хода могут использоваться для регулировки этого типа насоса.Полезный рабочий диапазон для плунжерных насосов с насадкой составляет примерно 10–100% от номинальной производительности.
В плунжерных насосах с набивкой используются уплотнительные кольца для образования уплотнения между плунжером и отверстием плунжера. В некоторых случаях это может потребовать периодической регулировки или замены колец.
Мембранные насосы. Мембранные насосы становятся все более популярными в системах водоподготовки. Конструкция диафрагмы использует возвратно-поступательное действие поршня или плунжера для передачи давления через гидравлическую жидкость на гибкую диафрагму.Диафрагма изолирует и вытесняет перекачиваемую жидкость и приводится в действие механически или гидравлически.
На Рисунке 35-6 показан диафрагменный насос, в котором используется электронная импульсная схема для управления соленоидом, который обеспечивает ход диафрагмы. И длину хода, и частоту хода можно регулировать, чтобы обеспечить полезный диапазон регулирования от 10 до 100% производительности. Мембранные насосы можно настроить на автоматическое регулирование частоты хода по внешнему сигналу. Эта возможность обычно используется для управления соотношением подачи химикатов к расходу воды.
Диафрагменный насос, показанный на рисунке 35-7, использует внутреннюю гидравлическую систему для приведения в действие диафрагмы в контакте с обрабатывающим раствором. Насос доступен в моделях, работающих при давлении нагнетания, превышающем 1500 фунтов на квадратный дюйм. Скорость подачи насоса регулируется вручную во время работы насоса, а также может регулироваться автоматически с помощью пневматического или электрического сигнала управления. Внутренняя гидравлическая система имеет встроенный клапан для защиты от избыточного давления.
Некоторые диафрагменные насосы можно использовать для подачи тяжелых или вязких материалов, таких как суспензии и полимеры.На Рис. 35-8 показан трубчатый мембранный насос, который часто используется в этих приложениях. В конструкции трубчатой диафрагмы также используется поршень, совершающий возвратно-поступательное движение, но трубчатая диафрагма расширяется или сжимается под давлением гидравлической жидкости. Доступны регулируемые насосы с расходом до 60 галлонов в час при давлении 100 фунтов на кв.
Пневматический диафрагменный насос работает со скоростью от 1 до 200 галлонов в минуту. Эта конструкция обычно используется для вязких продуктов, а из-за своей высокой емкости обычно используется для переноса химикатов из резервуара для хранения в дневной резервуар.Его можно использовать для подачи полимерных растворов, чувствительных к сдвигу.
Насос с пневматическим приводом устойчив к абразивным материалам, а также используется для перекачивания песка и шлама. Давление нагнетания ограничено примерно 100 фунтами на квадратный дюйм.
Роторные насосы. Роторные насосы имеют один или два вращающихся элемента для обеспечения положительного или полуположительного перемещения. Насос может состоять из двух зацепляющихся шестерен или одного вращающегося элемента в эксцентричном корпусе. В типе полного объемного вытеснения скорость подачи фиксируется скоростью вращения.Полуположительные поршневые насосы имеют внутреннее проскальзывание, которое влияет на скорость подачи и давление нагнетания. Ротационные насосы обычно зависят от жидкости, перекачиваемой для смазки. Большинство конструкций не допускают попадания абразивного материала в жидкость. Они могут перекачивать высоковязкие жидкости и особенно полезны для полимеров, в которых желателен низкий сдвиг.
На Рисунке 35-9 показан роторный насос с промежуточной шестерней, движущейся внутри шестерни ротора. Перекачивающее действие достигается за счет зацепления зубьев ротора и промежуточной шестерни и использования малых допусков на ход.При каждом обороте вала насоса фиксированное количество жидкости всасывается в насос через всасывающий патрубок. Этот объем жидкости заполняет пространство между зубьями ротора, проходит через насос и вытесняется через выпускное отверстие.
Гравитационная подача
Другой широко используемый метод доставки, конструкция с гравитационной подачей, использует разницу высот между химикатом в резервуаре и точкой приложения в качестве движущей силы. Основными преимуществами самотечной подачи являются простота и надежность.Эта безнасосная конструкция исключает движущиеся части и связанные с ними требования по обслуживанию. Устранение обратных клапанов и их периодических отказов значительно повышает надежность. При использовании методов проверки подачи подача под действием силы тяжести может обеспечить точный химический контроль.
Существует несколько типов систем гравитационной подачи. Устройство подачи дроби представляет собой пример простого, но эффективного способа дозирования предварительно отмеренных «доз» химикатов. В питателе дроби используется мерная емкость известного объема, которая заполняется из бака-накопителя.Клапан в нижней части мерной емкости открывается, и продукт самотеком течет в систему.
Проверка подачи может быть достигнута путем измерения скорости потока продукта или объема за раз. Это обеспечивает точную подачу и измерение продукта в систему без традиционных проблем обслуживания, связанных с дозирующими насосами. Самые сложные системы гравитационной подачи сочетают в себе проверку подачи с компьютеризированным контролем для обеспечения оптимального химического контроля и устранения необходимости в дозирующих насосах.
Правильный размер важен. Установка слишком большого размера вызовет резкие скачки химической обработки (периодические перегрузки). Если система слишком мала, она не сможет обеспечить достаточное количество химической обработки. Ключевые переменные, которые необходимо учитывать при определении размеров системы гравитационной подачи, включают вязкость продукта, доступный статический напор, влияние колебаний уровня в резервуаре и потери на трение в системе.
Водоструйный эдуктор
Водоструйный эдуктор использует кинетическую энергию движущейся жидкости под давлением.Эдуктор увлекает другую жидкость, газ или смесь газа и твердого вещества, смешивает ее с жидкостью под давлением и выпускает смесь против противодавления, как показано на рисунке 35-10. Применение водоструйных эдукторов ограничено необходимой величиной подъема или всасывания, доступным движущим давлением и давлением нагнетания. Как правило, необходимо соотношение рабочего давления к давлению нагнетания не менее 3,5: 1.
Управляемый вместе с клапаном водоструйный эдуктор может использоваться для непрерывной закачки химикатов в поток воды.Обычно он используется в этих приложениях для смешивания, а не для дозирования. Водоструйный эдуктор является важным компонентом хлораторов и сульфонаторов вакуумного типа, а также используется для транспортировки сухих полиэлектролитов.
Эжекторыобладают многими важными преимуществами, включая низкую стоимость, отсутствие движущихся частей и возможность самовсасывания. Кроме того, поскольку для работы не требуется электроэнергия, эдукторы очень хорошо подходят для использования во взрывоопасных зонах, где требуется дорогое взрывозащищенное оборудование.Эдукторы также могут быть адаптированы для работы с автоматизированными системами управления.
Скопление твердых частиц в сопле эдуктора и вокруг него может привести к потере всасывания. Фильтры и сетчатые фильтры могут помочь уменьшить эту проблему. Эжекторы следует периодически проверять и очищать в установках, где вероятно образование отложений.
Принадлежности
Насосные / резервуарные агрегаты. В большинстве случаев одного насоса для подачи химикатов недостаточно.Обычно система подачи химикатов объединяет насос, бак, клапаны, манометры, смеситель, сетчатый фильтр и предохранительные клапаны (для приготовления химического раствора), смешивание (при необходимости) и перекачку.
Смесители. Вертикально установленная крыльчатка с приводом от вала - наиболее распространенный тип смесителя, используемый для систем подачи химикатов. Если химическое вещество представляет собой разбавленный полимер с высокой молекулярной массой, может потребоваться редуктор скорости. Для некоторых химикатов желательно свести к минимуму унос воздуха. В этих случаях для смешивания следует использовать рециркуляционный насос с электрическим или воздушным приводом.
Таймеры. Таймеры находят множество применений в системах подачи, в первую очередь, для управления смесителями и периодической подачи химикатов (особенно противомикробных).
Тревоги. Системы охранной сигнализации становятся все более сложными. Теперь можно осуществлять мониторинг и сигнализацию по мере необходимости в зависимости от состояния насоса, расхода химикатов, высокого и низкого уровней в резервуаре и необычных условий эксплуатации.
Форсунки. Специальные форсунки необходимы для впрыска химикатов в трубопроводы.На рисунках 35-11 и 35-12 показаны типичные форсунки низкого и высокого давления. Сопла низкого давления используются для впрыска в поток жидкости. Пинольные форсунки высокого давления используются в паровых системах. Перо распыляет химикат на мелкие капли, которые уносятся потоком пара. Следует проявлять осторожность, чтобы не допустить нагнетания жидкости в паропроводы непосредственно перед изгибами трубопровода, где высокоскоростные капли жидкости могут удариться о стенки труб и разрушить их.
Уровнемеры. Необходимость контролировать уровни в резервуарах на месте и удаленно привела к разработке множества различных типов мониторов уровня.Среди наиболее известных методов - датчики давления, ультразвуковые мониторы, емкостные датчики, чувствительные к давлению линейные потенциометры и пузырьковые трубки. Необходимо соблюдать осторожность, чтобы обеспечить следующее:
- Совместимость с материалами конструкции
- адекватная температурная компенсация
- изоляция от разрушающих скачков давления
ХИМИЧЕСКИЕ КОРМОВЫЕ СИСТЕМЫ
Жидкое сырье
Химикаты могут подаваться «дробью» (партиями) или на постоянной основе.Выбор между этими двумя методами зависит от требуемой степени контроля, приложения и конструкции системы.
Подача дроби. Химикат может подаваться дробью путем двухпозиционного управления насосом подачи химикатов или путем выгрузки из калиброванного сосуда или измерительной камеры. Подача дробью может использоваться в системах охлаждения, бассейнах биологического окисления и других местах, где отношение объема системы к продувке велико. В этих системах дробь просто восполняет потерянный или израсходованный материал.Подача дробью также используется в тех случаях, когда требуется только периодическая подача. Противомикробные препараты для систем водяного охлаждения обычно вводятся в виде дроби. Подача дробью не может использоваться в прямоточных системах, где требуется равномерная концентрация химикатов.
Непрерывная подача. Системы непрерывной подачи дозируют химикаты в воду постоянно. Более совершенные системы распределяют корм в соответствии с обрабатываемым объемом и требованиями к химическим веществам. Непрерывная подача подходит для многих систем, которые также могут быть дробеструйными.Это абсолютно необходимо в таких применениях, как хлорирование воды для бытовых нужд и контроль отложений в прямоточных системах, где необходимо обрабатывать каждый галлон воды и не существует резервуара для хранения. Это также необходимо при подаче химикатов для осветления воды, чтобы гарантировать, что все частицы мутности столкнутся с молекулами полимера перед поступлением в осветлитель.
Непрерывная подача может быть обеспечена простым методом самотечной капельной подачи, при котором скорость подачи регулируется игольчатым клапаном. Также можно использовать дозирующие насосы или ротометры и регулирующие клапаны, питающие от линии рециркуляции под давлением (Рисунок 35-13).
Сухие химикаты
Большие количества квасцов, извести и кальцинированной соды обычно используются на очистных сооружениях и крупных промышленных установках водоподготовки. Из-за большого количества этих добавок обычно хранят и подают в виде сухих материалов. Основное преимущество сухих кормов - более низкие затраты на транспортировку и хранение. К недостаткам можно отнести пыль, отсутствие контроля, высокие затраты на эксплуатацию и техническое обслуживание, а также повышенное внимание оператора.
Системы сухой подачи, обычно используемые для водоподготовки, включают объемные питатели, гравиметрические питатели и питатели растворения.
Волюметрические питатели. Объемные дозаторы точно дозируют порошкообразный материал. Материал можно наносить непосредственно или использовать для получения суспензии, которая применяется в процессе. Объемные дозаторы используются для подачи и гашения извести, подачи сухих полимеров и глины, а также подачи противопожарных добавок в топки котлов.
Производительность и точность объемных дозаторов сухого вещества во многом зависят от характеристик дозируемого порошка. Основными характеристиками, влияющими на подаваемый порошок, являются гранулометрический состав, насыпная плотность в сыпучем и упакованном виде, содержание влаги и абразивность.
Типичная объемная система подачи включает бункер для хранения насыпных материалов или силос, загрузочный бункер и дозирующее устройство. Наиболее распространенное дозирующее устройство - винтовой или шнековый. Скорость вращения шнека определяет скорость подачи.
Некоторые порошки имеют тенденцию к образованию перемычек или «дыр», вызывая неравномерное кормление. Для обеспечения равномерного поступления порошка в зону спирали могут потребоваться вспомогательные устройства. Среди наиболее распространенных - изгибающиеся стенки бункера, вибраторы бункера и вспомогательные шнеки увеличенного размера, расположенные над спиралью подачи.
Гравиметрические питатели. Гравиметрические дозаторы дозируют химикаты по весу, а не по объему, и имеют точность в пределах 1-2%. Гравиметрический дозатор представляет собой весы, сбалансированные для обеспечения доставки в систему нужного веса химиката. Химикат, выбрасываемый гравиметрическим дозатором, обычно переводится в раствор или суспензию.
Поскольку гравиметрические питатели значительно дороже, чем объемные питатели, они используются только с большими системами, требующими точной подачи, или для химикатов, свойства текучести которых не позволяют использовать объемные питатели.
Питатели растворяющиеся. Питатели для растворения регулируют скорость растворения сухих химикатов. Резервуар для растворения заполняется сухим химическим веществом, и в него подается регулируемый поток воды. Концентрация выходящего продукта определяется площадью контакта между сухим материалом и водой и скоростью растворения. Примеры питателей для растворения включают питатели для твердых галогенов и системы для растворения полиэлектролитов.
В некоторых питателях для растворения требуется дополнительная энергия для обеспечения адекватного растворения (смачивания) и тщательного перемешивания.Например, в устройстве подачи твердых галогенов распылительные форсунки направляют высокоскоростной поток воды в слой продукта. В других питателях для растворения эдуктор используется для смачивания и перемешивания.
Автоматические и полуавтоматические системы были созданы для доставки, увлажнения, старения, переноса и подачи сухих полиэлектролитов (полимеров). Подача и смачивание этих систем подобна питателю для растворения. Для «смачивания» полимера используются либо распылительные завесы (смачивающие камеры), либо эжекторные устройства.Для перемешивания, выдерживания, переноса и подачи разбавленного полимерного раствора используются различные резервуары, элементы управления и насосы (см. Рис. 35-14). Эти системы подачи обычно имеют объемные шнековые питатели для точного дозирования сухих полиэлектролитов. Единственный ручной труд, связанный с этим, - это загрузка бункера, связанного с объемным шнековым питателем.
СИСТЕМЫ ХИМИЧЕСКОГО КОНТРОЛЯ
Другим важным компонентом хорошо спроектированной системы подачи химикатов является схема управления - метод, с помощью которого происходит регулировка скорости подачи химикатов.Схема контроля может иметь огромное влияние на контроль остаточных химических веществ, потребности в рабочей силе и конечные результаты программы обработки. Ключевые переменные, которые необходимо учитывать при выборе схемы управления, включают требуемый диапазон регулирования, период полураспада системы, время простоя, доступность рабочей силы и экономические показатели.
Методы управления могут быть классифицированы в соответствии с тем, как регулируется конечный элемент управления, и степенью сложности логики управления. Типичные схемы управления, используемые в приложениях для обработки воды, включают: ручное, двухпозиционное, упреждающее, соотношение, обратную связь и комбинации упреждающей / обратной связи.Наиболее сложные методы управления требуют использования программируемых логических контроллеров или компьютеров.
Ручное управление
В системе с ручным управлением химикаты добавляются непрерывно и с постоянной скоростью. Регулировки производятся операторами завода через фиксированные интервалы времени - обычно один раз в смену или один раз в день. Эти настройки включают длину или частоту хода насоса, концентрацию химического раствора и положение клапана.
Ручное управление лучше всего подходит для приложений, в которых химический контроль не является критическим, установленные диапазоны регулирования широки, а время удержания системы велико.В таких ситуациях ручное управление поддерживает средний химический баланс в допустимых пределах.
К недостаткам ручного управления относятся возможные потери контроля, высокие затраты на химическую обработку, повышенные потребности в рабочей силе и возможность получения неприемлемых результатов. Сегодня, когда упор делается на улучшенный контроль качества, наблюдается тенденция отказа от ручного управления к использованию более сложного оборудования.
Режим постоянной скорости включения-выключения
При двухпозиционном методе управления насос подачи химикатов (или другое устройство подачи с постоянной скоростью) автоматически включается и выключается с помощью управляющего сигнала.Этот метод применим к системам (например, градирням), которые не требуют непрерывной подачи химикатов и имеют большое отношение объема к продувке.
Примером двухпозиционного управления является насос подачи кислоты, который включается при высокой уставке pH и выключается при низкой уставке pH.
Счетчик-счетчик-таймер - еще одна двухпозиционная система управления, применяемая в системах водяного охлаждения. В этом методе управления химический насос включается на фиксированный период времени после того, как накопится предварительно установленный объем подпиточной воды или продувки.
Управление с прогнозированием
Системы управления с прогнозированием предназначены для обнаружения изменений в спросе на химические вещества и их компенсации, чтобы держать систему под контролем. Напротив, системы управления с обратной связью реагируют только после обнаружения системной ошибки. Управление с прогнозированием обычно используется для регулировки скорости подачи ингибитора коррозии (на основе изменений температуры воды), скорости подачи хелатирующего агента (на основе испытаний на твердость) и скорости подачи коагулянта (на основе показаний входящей мутности).
Контроль соотношения. Управление соотношением - это форма управления с прогнозированием, при которой производительность химического насоса или другого дозирующего устройства автоматически регулируется пропорционально переменной, например расходу воды. Контроль соотношения чаще всего используется для поддержания фиксированной концентрации химического вещества в водном потоке, где скорость потока колеблется. Типичным примером является подача ингибитора коррозии пропорционально расходу воды, подаваемой в мельницу.
Основным недостатком этой схемы управления является отсутствие проверки подачи в реальном времени.Хотя контроллер посылает сигнал насосу, нет гарантии, что производительность дозирующего насоса соответствует сигналу контроллера или даже что дозирующий насос работает. Последние достижения в технологии управления с обратной связью предоставили решение этой проблемы.
Управление с обратной связью. При управлении с обратной связью фактическое значение регулируемой переменной постоянно сравнивается с желаемым значением. Когда обнаруженное значение отличается от заранее определенного заданного значения, контроллер выдает сигнал, указывающий степень отклонения.Во многих системах водоподготовки этот сигнал отправляется на дозирующий насос, и мощность насоса изменяется.
Одним из наиболее распространенных примеров управления с обратной связью является подача кислоты в градирню в зависимости от pH. Когда контроллер обнаруживает разницу между заданным значением и фактическим значением pH, он изменяет скорость насоса или положение клапана, чтобы вернуть pH к заданному значению.
Ручная регулировка насоса подачи химреагентов на основе теста на остаточное содержание фосфатов в котловой воде является простой формой управления с обратной связью.Точность этого метода ограничена только частотой тестирования, временем, необходимым для воздействия на изменение, и надежностью метода мониторинга.
Основным недостатком управления с обратной связью является тот факт, что управляющее воздействие не происходит, пока не возникнет ошибка. Другая ключевая проблема управления с обратной связью заключается в том, что оно сильно зависит от сигнала анализатора. Во многих системах точность и надежность анализатора вызывают сомнения.
ОБРАБОТКА СИСТЕМЫ ОХЛАЖДЕНИЯ
Большинство открытых рециркуляционных систем охлаждения требуют добавления четырех классов химикатов для минимизации коррозии, накипи и загрязнения: ингибиторы коррозии
- Ингибиторы коррозии
- Агенты или диспергаторы против отложений
- противомикробные препараты
- Химикаты для регулирования pH
Контроль продувки также является неотъемлемой частью управления химическим режимом охлаждающей воды.
Химическое сырье
Ингибиторы коррозии и средства контроля отложений часто подают в чистом виде (неразбавленным) в бассейн градирни. Обычные методы доставки химикатов включают в себя дозирующие насосы и программируемые системы подачи самотеком. В системах гравитационной подачи могут использоваться водоструйные эжекторы для переноса химикатов в бассейн. Кислоты или щелочи, используемые для контроля pH, и некоторые противомикробные препараты требуют разбавления перед впрыском в основную охлаждающую воду.
Подающие насосымогут обеспечивать точную непрерывную подачу при условии, что скорость насоса регулируется с учетом изменений в системе.Из-за большого отношения объема системы охлаждающей воды к скорости продувки периодическая подача химиката дробью часто может обеспечить удовлетворительный химический контроль.
Ингибиторы и диспергенты. Ингибиторы и диспергаторы можно подавать в чистом виде в бассейн градирни, где легко может происходить разбавление рециркулирующей воды. Системы подачи варьируются от простого непрерывного насоса или периодической подачи дроби до компьютеризированного автоматического управления.
Две самые простые в использовании системы подачи - это непрерывно работающие насосы подачи химикатов и системы периодической подачи дроби по времени.В некоторых случаях эти методы обеспечивают адекватный контроль, но они неточны, если условия эксплуатации или химический состав системы охлаждения меняются. Когда условия меняются, оператор установки должен стать неотъемлемой частью контура управления, проверяя химические остатки и регулируя скорости подачи химикатов, чтобы поддерживать надлежащие уровни ингибитора и диспергатора в воде.
Для улучшения химического контроля химикат можно подавать пропорционально сигналу расхода от расходомера продувочной или подпиточной воды. Это можно делать на постоянной основе с помощью сигнала потока, напрямую регулирующего скорость откачки.Это также можно делать на полунепрерывной основе с помощью счетчика потока, который запускает подачу химиката.
Дополнительное улучшение контроля возможно с помощью компьютеризированных контроллеров, которые используют измеренные параметры для расчета циклов концентрации и объединяют эту информацию с данными потока в реальном времени для расчета и подачи необходимых количеств ингибитора и диспергатора.
Контроль pH. Для правильного выполнения программы обработки обычно требуется контроль pH и щелочности охлаждающей воды в заданном диапазоне.Хороший контроль pH стал более важным, потому что программы обработки ингибиторами хрома заменяются, а в градирнях используются более высокие циклы для минимизации продувки.
Промышленная концентрированная серная кислота (66 ° Боме) обычно используется для контроля pH охлаждающей воды. В чистом виде он почти в два раза плотнее воды и опускается на дно бассейна градирни. Это может повредить бетон бассейна и вызвать плохой контроль pH. По этой причине кислоту следует хорошо смешать с водой перед тем, как попасть в бассейн.Лоток для разбавления используется для подачи кислоты в бассейн градирни с использованием подпиточной воды в качестве разбавителя.
Резервуары из мягкой стали обычно используются для хранения концентрированной серной кислоты. Для предотвращения скопления взрывоопасного газообразного водорода в резервуаре для хранения необходима соответствующая вентиляция. Рекомендуется использовать фильтры перед кислотными насосами для удаления любых остаточных продуктов коррозии или других твердых частиц, которые могут присутствовать в резервуаре для хранения.
Управление с обратной связью почти всегда используется для управления подачей кислоты в систему охлаждения.Чаще всего используются двухпозиционные схемы управления и пропорционально-интегрально-производная (ПИД). Дозирующие насосы или регулирующие клапаны обычно используются для регулирования подачи кислоты. Расположение датчика pH имеет решающее значение; в большинстве случаев зонд следует размещать рядом с насосами циркуляционной воды.
Правильная конструкция важна при установке линии подачи кислоты. Линии должны быть проложены таким образом, чтобы предотвратить медленное наполнение и слив, которые могут вызвать чрезмерную задержку в контуре управления.Горизонтальные секции должны немного наклоняться вверх по направлению потока. Установка повышенного контура на нагнетательном конце линии выше, чем кислотный насос, обеспечивает непрерывное заполнение линии. В установках, где резервуар для хранения кислоты находится выше точки подачи, можно использовать антисифонное устройство для обеспечения дополнительной защиты от перегрузки кислоты. Линии подачи концентрированной кислоты, как правило, должны быть не больше дюйма и обычно изготавливаются из труб из нержавеющей стали 304 или 316. Трубы из полиэтилена или жесткого ПВХ сортамента 80 могут использоваться, если они защищены от физических повреждений.
Другие важные соображения включают размер насоса / клапана, качество кислоты, процедуры обслуживания и частоту калибровки.
Сульфаминовая кислота, соляная кислота, азотная кислота (жидкости) и бисульфат натрия (твердый) также могут использоваться для снижения pH. Иногда контроль pH связан с подачей газообразного хлора, потому что газообразный хлор соединяется с водой с образованием соляной кислоты вместе с антимикробной хлорноватистой кислотой. Это не рекомендуется, так как это может привести к чрезмерному хлорированию.
Если требуется повышенная щелочность, обычно используется кальцинированная сода или каустическая сода.
Контроль продувки
В охлаждающей воде растворенные твердые частицы (измеряемые по проводимости) поддерживаются на заданном уровне за счет непрерывной или периодической продувки (продувки) рециркуляционной воды. В некоторых случаях достаточно периодически продувать, открывая клапан, пока проводимость воды в градирне не достигнет определенного заданного уровня. Улучшенное управление может быть получено с помощью автоматического контроллера продувки, который открывает и закрывает клапан продувки в зависимости от пределов проводимости или модулирует клапан управления продувкой для поддержания заданного значения проводимости.
Еще более точный контроль растворенных твердых веществ может быть достигнут при использовании компьютеризированных систем контроля. Измеренная проводимость оборотной воды, деленная на проводимость подпиточной воды, позволяет оценить циклы концентрирования. Уставка проводимости рециркуляционной воды затем регулируется онлайн-компьютером для поддержания желаемого количества циклов.
Компьютеризированные системы подачи химикатов и управления
Компьютеризированные системы контроля химического состава охлаждающей воды могут включать некоторые или все функции управления, уже обсужденные в этом разделе, включая подачу ингибитора и диспергатора, контроль pH, продувку и контроль циклов, а также подачу неокисляющих антимикробных препаратов.На рис. 35-15 представлена схема компьютеризированной системы подачи химикатов охлаждающей воды, мониторинга и управления.
Компьютеризированные системы управления обычно можно запрограммировать для подачи химикатов или регулировки рабочих параметров в соответствии со сложными индивидуальными алгоритмами. Это позволяет системе подачи автоматически компенсировать изменяющиеся рабочие условия, которые часто сильно зависят от конкретной установки. Например, в некоторых случаях подпиточная вода может содержать различные количества ингибитора коррозии. Скорость подачи ингибитора коррозии в рециркуляционную воду необходимо регулировать, чтобы компенсировать попадание ингибитора в систему с подпиткой.В других случаях может потребоваться корректировка уставки скорости подачи диспергатора в соответствии с химическим составом воды в системе (например, pH, проводимостью или уровнями кальция). В каждом из этих случаев компьютер может быть использован для выполнения необходимых вычислений и автоматической корректировки.
Некоторые компьютеризированные системы обеспечивают проверку количества химического сырья. В сочетании с онлайн-контролем химического состава и настраиваемыми алгоритмами управления проверка подачи обеспечивает наиболее точный контроль обработки.Система измерения определяет химический состав воды. Затем компьютер вычисляет необходимые дозировки химикатов, а система подачи проверяет количество подаваемых химикатов. Обычно используемая система показана на рисунке 35-16.
Удаленные компьютеры используются для мониторинга и хранения состояния системы охлаждения и результатов программы. Интересующие параметры обычно включают pH и проводимость рециркуляционной и подпиточной воды, скорость подачи химикатов, скорость коррозии и данные о загрязнении. После сбора данных для анализа эффективности программы лечения используются статистические методы.
Модемывстроены в некоторые компьютеризированные системы подачи, так что условия тревоги вызывают автоматический телефонный звонок соответствующему обслуживающему персоналу и извещают его о проблеме. Это предотвращает превращение мелких проблем в серьезные. Например, если клапан непреднамеренно остается открытым и содержимое резервуара с кислотой начинает стекать в бассейн градирни, срабатывает сигнализация низкого pH и автоматически отправляется вызов системному оператору, который возвращается в зону. и закрывает клапан.Модемы также используются, чтобы позволить обслуживающему персоналу вносить изменения в рабочие параметры системы и скорость подачи химикатов из удаленного места.
КОТЕЛЬНАЯ СИСТЕМА ХИМИЧЕСКАЯ ПОДАЧА
Для достижения наилучших результатов все химические вещества для внутренней обработки парогенератора должны подаваться непрерывно и в соответствующие точки впрыска. Химикаты могут подаваться непосредственно из резервуара для хранения (в чистом виде) или могут быть разбавлены в дневном резервуаре водой высокой чистоты. Некоторые химические вещества можно смешивать и подавать из одного дневного резервуара.
Точки подачи химикатов обычно выбираются как можно дальше по потоку в контуре котловой воды. Для подачи химикатов за насосом питательной воды или в паровой барабан насос должен соответствовать давлению в котле. Для котлов высокого давления решающее значение имеет правильный выбор насоса.
Информация о фиде товаров
Как показано на Рис. 35-17, парогенерирующая система включает три основных компонента, требующих обработки: деаэратор, котел и конденсатную систему.Поглотители кислорода обычно поступают в накопительную часть деаэратора. Внутренняя очистка котла подается на всасывание или нагнетание насоса питательной воды либо в паровой барабан. Точки подачи конденсатной системы также различаются в зависимости от химиката и цели обработки. Типичные точки подачи включают паровой коллектор или другие удаленные паропроводы. Химическое сырье также может подаваться непосредственно в сочетании с химическими веществами для внутренней обработки или поглотителями кислорода.
Химическая промышленность
Поглотители кислорода. Поглотители кислорода обычно подают из дневного резервуара в секцию хранения деаэратора. Некоторые поглотители кислорода также применялись в коллекторах пара или трубопроводах для конденсата для уменьшения связанной с кислородом коррозии в конденсатных системах. В коммунальных системах поглотители кислорода обычно подают в горячий колодец поверхностного конденсатора. Скорость подачи поглотителя кислорода зависит от уровня кислорода в системе плюс количество химических добавок в системе.
Сульфит. Некатализированный сульфит натрия можно смешивать с другими химическими веществами.Предпочтительным местом для закачки сульфита является точка в секции хранения деаэрационного нагревателя, где сульфит будет смешиваться с выходом из деаэрирующей секции.
Если сульфит подается отдельно, необходимо следующее оборудование: Резервуар из нержавеющей стали 304
- Мешалка из нержавеющей стали
- предохранительный клапан из нержавеющей стали
- трубопроводы, клапаны и фитинги железные
- насос с механически обработанной жидкой частью из стали или чугуна и затвором из нержавеющей стали
Во всех случаях следует использовать иглу для инъекций.
Сульфит, поставляемый в виде жидкого концентрата, обычно является кислым и при подаче в чистом виде вызывает коррозию резервуаров из нержавеющей стали на уровне жидкости. Емкости должны быть из полиэстера, стекловолокна или полиэтилена. Линии могут быть из ПВХ или нержавеющей стали 316.
Катализированный сульфит. Катализированный сульфит необходимо подавать отдельно и непрерывно. Смешивание катализированного сульфита с любым другим химическим веществом ухудшает работу катализатора. По той же причине катализированный сульфит необходимо разбавлять только конденсатом или деминерализованной водой.Для защиты всей системы предбойлера, включая любые экономайзеры, катализированный сульфит следует подавать в секцию хранения деаэрирующего нагревателя.
Каустическая сода может использоваться для регулирования pH раствора дневного резервуара; поэтому нельзя использовать бак из мягкой стали. Материалы конструкции для загрузочного оборудования такие же, как и для обычного сульфита.
Гидразин. Гидразин совместим со всеми химикатами для обработки котловой воды, кроме органических веществ, аминов и нитратов.Однако хорошей инженерной практикой является подача только гидразина. Обычно он непрерывно подается в накопительную часть деаэрирующего нагревателя. Из-за проблем с обращением и воздействием, связанных с гидразином, закрытые системы хранения и подачи стали стандартом. Материалы конструкции такие же, как и для сульфита.
Органические поглотители кислорода. Доступно множество органических соединений, включая гидрохинон и аскорбиновую кислоту. Некоторые из них катализируются. Большинство следует кормить в одиночку.Как и сульфит, органические поглотители кислорода обычно непрерывно подают в накопительную часть деаэрирующего нагревателя. Материалы конструкции такие же, как и для сульфита.
Химикаты для внутренней обработки
Существует три основных классификации химических веществ, используемых при внутренней обработке: фосфаты, хелатирующие агенты и полимеры. Эти химические вещества могут подаваться отдельно или в комбинации; в наиболее сбалансированных программах обработки два или три химиката подаются вместе.Предпочтительная точка подачи зависит от указанного химического вещества. Например, когда каустическая сода используется для поддержания щелочности котловой воды, она подается непосредственно в корпус котла. Когда каустик используется для регулирования pH питательной воды, он обычно вводится в накопительную секцию деаэрирующего нагревателя.
Фосфаты. Фосфаты обычно подают непосредственно в паровой барабан котла, хотя при определенных условиях они могут подаваться в линию питательной воды. Обработки, содержащие ортофосфат, могут привести к образованию отложений в линии подачи фосфата кальция; поэтому их нельзя подавать через питающую линию котла.Ортофосфат следует подавать непосредственно в паровой барабан котла по линии подачи химикатов. Полифосфаты нельзя подавать в линию питательной воды котла, когда экономайзеры, теплообменники или ступенчатые нагреватели являются частью системы предварительного котла. Если система предварительного кипячения не включает такое оборудование, полифосфаты могут подаваться в трубопровод питательной воды при условии, что общая жесткость не превышает 2 частей на миллион.
Во всех случаях скорость подачи зависит от уровня жесткости питательной воды. Фосфаты следует подавать в чистом виде или разбавлять конденсатом или водой особой чистоты.Подходят резервуары из мягкой стали, фитинги и питающие линии. При подаче кислых фосфатных растворов рекомендуется использовать нержавеющую сталь и полиолефины.
Хеланты. Все хелатирующие агенты должны подаваться в линию питательной воды котла с помощью инжекционной форсунки за пределами выхода питательных насосов котла. Если в питающей линии котла имеются теплообменники или ступенчатые нагреватели, точка впрыска должна находиться на их выходе. Следует проявлять осторожность при выборе металлов для высокотемпературных инъекционных игл.
При концентрации исходного раствора и повышенных температурах хелатирующие агенты могут вызывать коррозию низкоуглеродистой стали и медных сплавов; поэтому для всего загрузочного оборудования рекомендуется нержавеющая сталь 304 или 306. Хелатирующие продукты можно подавать в чистом виде или разбавленными конденсатом. Скорость подачи хеланта необходимо тщательно контролировать в зависимости от жесткости питательной воды, поскольку неправильное применение может иметь серьезные последствия.
Хеланты нельзя подавать непосредственно в бойлер. Потребуются химические линии из нержавеющей стали, а хлоридная или едкая коррозия под напряжением может привести к выходу из строя линии подачи хеланта внутри котла.Тогда произойдет локальная атака котельного металла. Хелатирующие агенты не следует подавать, если питательная вода содержит значительный уровень кислорода.
Полимерные диспергаторы. В большинстве случаев полимерные диспергаторы представлены в составе комбинированного продукта с хелатирующими агентами и / или фосфатами. Для программ хелат-диспергатор и хелант-фосфат-диспергатор следует соблюдать рекомендации по разбавлению и кормлению хелатирующими агентами. Для программ диспергирования фосфатов следует соблюдать рекомендации по разведению и кормлению фосфатов.Эти комбинированные программы обычно дают наилучшие результаты в отношении чистоты котла.
Съемочные амины. Все пленкообразующие амины должны подаваться в паровые коллекторы в точках, обеспечивающих надлежащее распределение. Для некоторых систем достаточно одной точки подачи. В каждом случае следует исследовать парораспределение и устанавливать точки подачи, чтобы гарантировать, что все части системы проходят надлежащую обработку.
Пленочные амины необходимо смешивать с конденсатом или деминерализованной водой.Воду, содержащую растворенные твердые вещества, использовать нельзя, поскольку твердые частицы загрязняют пар и могут образовывать нестабильные аминовые эмульсии.
Стальные резервуары использовались для подачи пленочных аминов, но некоторая коррозия может происходить выше уровня жидкости. Рекомендуется использовать нержавеющую сталь. Технические характеристики оборудования такие же, как и для обычного сульфита, за исключением того, что требуется форсунка парового типа или игла.
Нейтрализующие амины. Нейтрализующие амины могут подаваться в секцию хранения деаэрирующего нагревателя, непосредственно в котел с химическими веществами для внутренней обработки или в главный паровой коллектор.Некоторым системам распределения пара может потребоваться более одной точки подачи, чтобы обеспечить правильное распределение. Для подачи в парораспределительную линию требуется нагнетательная игла.
Нейтрализующие амины обычно подают в зависимости от pH системы конденсата и измеренных скоростей коррозии. Эти амины можно подавать в чистом виде, разбавлять конденсатом или деминерализованной водой или смешивать в низких концентрациях с химическими веществами для внутренней обработки. Для кормления можно использовать стандартный стальной насос и бак в упаковке.
Компьютеризированные системы подачи химреагентов в котлы. Компьютеризированные системы подачи химикатов в котел используются для улучшения результатов программы и сокращения эксплуатационных расходов. Эти системы могут использоваться для подачи поглотителей кислорода, аминов и химикатов для внутренней обработки.
Типичная система, показанная на рис. 35-18, включает в себя дозирующий насос, оборудование для проверки подачи и микропроцессорный контроллер. Эти системы часто связаны с персональными компьютерами, которые используются для мониторинга результатов программы, скорости подачи, состояния системы и рабочих условий завода.Затем могут быть созданы графики тенденций и управленческие отчеты для предоставления документации по результатам программы и помощи в устранении неполадок.
Во многих случаях эти системы можно запрограммировать на подачу химикатов для обработки котлов в соответствии со сложными индивидуальными алгоритмами. Например, подача хелатирующего агента может регулироваться автоматически на основе результатов испытаний на жесткость анализатора или оператора, расхода питательной воды котла и минимальных / максимальных допустимых скоростей подачи продукта. Таким образом, химическая подача точно соответствует системному спросу, практически исключая возможность недостаточной или избыточной подачи.
Проверка кормов - еще один важный аспект некоторых компьютеризированных систем кормления. Фактическая производительность насоса постоянно измеряется и сравнивается с рассчитанной компьютером уставкой. Если выходная мощность не соответствует заданному значению, скорость или длина хода регулируются автоматически. Преимущества этой технологии включают устранение трудоемких измерений просадки, возможность подачи большинства химикатов непосредственно из резервуаров, точный контроль остаточных химических веществ и минимальные потребности в рабочей силе.
СИСТЕМЫ ПОДАЧИ ПОЛИМЕРА ДЛЯ ВОДЫ
Полиэлектролиты, используемые в системах водоподготовки, имеют определенные требования к хранению, обращению, подаче и разбавлению. Крайне важно, чтобы эти материалы подавались точно, чтобы предотвратить недокорм и перекармливание, что может привести к потере химической обработки и снижению производительности системы.
Типы полимеров
Полимеры доступны в виде порошков, жидкостей и эмульсий. У каждой формы разные требования к кормлению, обращению и хранению.
Сухие полимеры. Катионные и анионные высокомолекулярные полимеры доступны в порошковой форме. Преимущество этих продуктов состоит в том, что они на 100% состоят из полимера, что позволяет минимизировать затраты на транспортировку и транспортировку. Тем не менее, абсолютно необходимо, чтобы сухие полимерные материалы обрабатывались и разбавлялись должным образом, чтобы предотвратить недокорм и перекорм.
Раствор полимеров. Растворные полимеры обычно представляют собой катионные продукты с низкой молекулярной массой и высокой плотностью заряда, которые обычно используются для очистки сырой воды.Полимеры в растворах легче разбавлять, обрабатывать и подавать, чем сухие и эмульсионные полимеры. Во многих случаях предварительное разбавление раствора полимера не требуется, и продукт можно подавать непосредственно из транспортного контейнера или резервуара для хранения сыпучих материалов. Полимеры в растворах обеспечивают удобство чистой подачи, и их можно разбавлять до любой удобной концентрации, соответствующей производительности насоса подачи химикатов.
Эмульсионные полимеры. Катионные и анионные высокомолекулярные полимеры доступны в виде эмульсий.Эмульсионный продукт позволяет производителю предоставлять концентрированные жидкие полимерные составы, которые не могут быть приготовлены в форме раствора. Только после того, как эмульсионный полимер «перевернется» с водой, полимер становится доступным в своей активной форме. Поэтому перед использованием эти продукты необходимо правильно разбавить.
Хранилище
Сухие полимеры. Сухие полимеры склонны к слеживанию при хранении в условиях высокой влажности. Слеживание нежелательно, поскольку это мешает процессу восстановления и разбавления полимера.Поэтому сухие полимеры следует хранить в местах с низкой влажностью, а открытые емкости с сухим материалом следует герметично закрыть перед восстановлением. В целом полимерные продукты начинают терять активность после 1 года хранения. Хотя этот процесс постепенный, он в конечном итоге влияет на стоимость химической обработки. Настоятельно рекомендуется использовать полимеры до истечения срока их годности.
Раствор полимеров. Раствор полимеров следует хранить в помещении с умеренной температурой, чтобы защитить их от замерзания.Некоторые продукты в виде растворов подвержены необратимым повреждениям при замораживании. Другие демонстрируют отличное восстановление при замораживании-оттаивании. Ни в коем случае нельзя хранить растворные полимеры при температуре выше 120 ° F. В качестве растворов эти полимеры не требуют периодического перемешивания (для предотвращения разделения) перед использованием. Однако некоторые полимеры в растворах имеют короткий срок хранения, и их запасы следует соответствующим образом скорректировать.
Эмульсионные полимеры. Поскольку эмульсионные полимеры не являются настоящими растворами, они отделяются, если им позволяют стоять в течение длительного периода времени.Следовательно, эмульсионные полимеры необходимо смешивать перед использованием с помощью барабанного смесителя, резервуарного смесителя или устройства для рециркуляции резервуара. Контейнер для рециркуляции наливных резервуаров или контейнеров должен быть спроектирован таким образом, чтобы рециркулировать содержимое резервуара не реже одного раза в день для предотвращения разделения. Эмульсионные полимеры, содержащиеся в бочках, также следует перемешивать ежедневно. Чистый эмульсионный полимер должен быть защищен от загрязнения водой, которое вызывает гелеобразование продукта и может сделать перекачивание трудным или невозможным. В зонах с высокой влажностью вентиляционные отверстия резервуара следует оборудовать осушителем, чтобы предотвратить конденсацию воды в резервуаре для хранения эмульсии.Даже небольшое количество конденсата может вызвать значительное желирование продукта. Как и жидкие продукты, эмульсионные полимеры необходимо защищать от замерзания и хранить при температуре ниже 120 ° F.
Разбавление и кормление
Сухие полимеры. Сухие полимеры перед использованием необходимо разбавить водой. Большинство операций требуют приготовления разбавленных полимеров один раз в смену или ежедневно. Обычно оператор установки несет ответственность за отмерить правильное количество сухого полимера в контейнер.Содержимое контейнера подается в смесительный бак через эдуктор полимера. Эдуктор - это устройство, которое использует давление воды для создания вакуума и сконструировано таким образом, что частицы сухого полимера смачиваются водой по отдельности, когда они проходят через узел эдуктора (Рисунок 35-19). Если частицы сухого полимера не смачивать по отдельности перед введением в резервуар для разбавления, в резервуаре для раствора образуются «рыбьи глаза» (нерастворенные глобулы полимера). Fisheyes представляют собой потраченный впустую полимер и вызывают засорение насосов подачи химикатов.
Содержание сухого раствора полимера должно быть ограничено примерно 0,5–1% или менее по весу, в зависимости от используемого продукта. Это необходимо для поддержания вязкости раствора на приемлемом уровне. Миксер, используемый в резервуаре для раствора, не должен превышать 350 об / мин, и перемешивание должно продолжаться только до тех пор, пока весь материал не растворится. Обычно партия разбавленного сухого полимера должна использоваться в течение 24 часов после приготовления, поскольку разбавленный продукт начинает терять активность по истечении этого времени.
Автоматические системы разбавления сухого полимера могут использоваться для выполнения функций смачивания, разбавления и смешивания, описанных ранее; однако систему необходимо периодически вручную заряжать сухим полимером. Хотя эти системы являются дорогостоящими, они могут значительно сэкономить время для персонала завода, а операции обычно более последовательны при использовании автоматических устройств восстановления.
Раствор полимеров. Полимеры в растворах можно разбавлять перед использованием или подавать в чистом виде из транспортных контейнеров, бункеров или резервуаров для хранения.Разбавление этих продуктов становится необходимым, если смешивание недостаточно для объединения полимера с обрабатываемой водой. Проточные системы разбавления статического смесителя приемлемы для растворных полимеров и являются самым простым методом разбавления и подачи раствора полимера. Полимерный раствор можно подавать через одну из многих коммерчески доступных систем разбавления и разбавления эмульсионного полимера. Однако, как правило, использование этих систем для растворных полимеров не обязательно. Полимеры в растворах легче всего перекачивать с помощью шестеренчатых насосов.Однако многие полимеры в растворах имеют достаточно низкую вязкость, чтобы их можно было перекачивать с помощью диафрагменных насосов-дозаторов химикатов.
Эмульсионные полимеры. Эмульсионные полимеры перед использованием необходимо разбавить. Разбавление позволяет эмульсионному продукту инвертировать и «переводить» полимер в его активное состояние. Правильная инверсия эмульсионных полимеров происходит быстро и эффективно. Неправильная инверсия эмульсионного полимера может привести к потере активности из-за неполного разматывания и растворения молекул полимера.
Для эмульсионных полимеров приемлемы системы периодического и непрерывного разбавления. При приготовлении партии оператор установки подает предварительно отмеренное количество чистой эмульсии в вихревую мешалку резервуара для разбавления. Продукт перемешивают до однородности, а затем миксеры отключают. Как и в случае с сухими полимерными продуктами, скорость миксера всегда должна быть ниже 350 об / мин, и миксер должен быть отключен, как только продукт станет однородным. Это предотвращает чрезмерный сдвиг молекулы полимера и, как следствие, потерю активности полимера.Система периодического восстановления полимерной эмульсии показана на Рисунке 35-20.
Несколько производителей выпускают на рынок системы непрерывной подпитки и подачи эмульсионных полимеров. Эти системы перекачивают чистый полимер из контейнера для хранения в камеру разбавления, где полимер соединяется с водой и полностью активируется. Затем водно-полимерный раствор течет под давлением воды к месту нанесения. Предусмотрено использование вторичной промывочной воды для дальнейшего разбавления полимера перед использованием. Эти системы подачи полимеров на сегодняшний день являются самым простым и лучшим способом непрерывной подачи эмульсий.Их производители заявляют о превосходной способности инвертировать молекулы полимера по сравнению с системами разбавления в резервуарах периодического действия. Коммерчески доступная система непрерывного нанесения эмульсионного полимера показана на Рисунке 35-21.
Недопустимо использовать только поточное статическое перемешивание для разбавления эмульсионных полимеров. Однако для смешивания вторичной разбавляющей воды с разбавленной эмульсией перед нанесением можно использовать поточное статическое смешивание. Первоначальное разбавление эмульсионных полимеров должно составлять 1% или 2% по весу.Такая концентрация раствора обеспечивает правильное взаимодействие частиц с частицами на этапе инверсии, что способствует полной инверсии.
Обычно желательно обеспечить возможности вторичного разбавления водой для систем подачи эмульсионных полимеров, потому что эти продукты имеют тенденцию быть наиболее эффективными при загрузке с концентрацией раствора приблизительно 0,1%.
Общие рекомендации
В дополнение к вышесказанному, некоторые общие правила относятся к подаче и обращению со всеми полимерами для обработки воды.В областях, где температура обычно опускается ниже нуля, рекомендуется изолировать все линии подачи полимера, чтобы не произошло замерзания линии подачи.
Для партий разбавленных полимеров в резервуарах скорость миксера в резервуаре не должна превышать 350 об / мин. При приготовлении разбавленных партий полимера в бак всегда следует добавлять воду. Затем следует запустить миксер и добавить полимер поверх воды.
Мембранные насосы-дозаторымогут использоваться для перекачивания большинства растворов полимеров.Однако из-за вязкости некоторых продуктов могут потребоваться шестеренчатые насосы. В системах подачи полимеров следует использовать пластиковые трубопроводы; также допускается нержавеющая сталь. Большинство полимеров вызывают коррозию мягкой стали и латуни. Следует принять дополнительные меры предосторожности, чтобы предотвратить разлив полимеров, поскольку разливы влажного полимера могут стать очень скользкими и представлять угрозу безопасности. Пролитую жидкость следует покрыть абсорбирующим материалом, а смесь немедленно удалить и утилизировать.