ЭПОКСИДНАЯ СМОЛА, ПРИМЕНЕНИЕ И СВОЙСТВА – ER-KA.RU
Cлово «эпоксидка» знакомо практически каждому человеку сознательного возраста. Эпоксидная смола является разновидностью синтетических смол. Она появилась в пятидесятые годы и сразу получила большую популярность благодаря универсальным потребительским свойствам.
Эпоксидные смолы широко используют и в домашнем хозяйстве, и в промышленном производстве. Возможности применения эпоксидных смол постоянно расширяются за счет разработки новых составов с улучшенными характеристиками.
Что такое эпоксидная смола
По химическому строению эпоксидная смола представляет собой синтетическое олигомерное соединение. Эпоксидные материалы востребованы практически во всех сферах промышленности. В свободном виде эпоксидная смола не применяется. Она проявляет свои уникальные свойства только в соединении с отвердителем после реакции полимеризации.
При комбинировании разных видов эпоксидных смол и отверждающих веществ получаются совершенно непохожие материалы: твердые и жесткие, прочнее стали и мягкие, наподобие резины.
Что такое отвердитель
Эпоксидный состав включает два компонента. При смешивании они вступают в реакцию полимеризации. Полимеризирующий компонент называется отвердителем.
Путем различного комбинирования смол и отвердителей получаются самые разнообразные эпоксидные композиции.
В качестве отверждающих агентов используют фенолы, третичные амины и их аналоги. Соотношение эпоксидной смолы и отвердителя имеет широкие пределы и зависит от ее состава. Эпоксидная смола — это реактопласт, реакция взаимодействия эпоксидной смолы с отверждающим агентом является необратимой, это значит, что застывшая смола не растворяется и не расплавляется как термопласт.
Каким должно быть соотношение смолы и отвердителя
Избыток и недостаток отвердителя в эпоксидном составе негативно отражается на качестве полимера: снижается прочность, устойчивость к нагреванию, сильнодействующим химическим веществам, воде. При недостатке отвердителя изделие становится липким из-за несвязанной смолы. Излишек свободного отвердителя постепенно выделяется на поверхности полимера. Для разных компаундов смола и отверждающий компонент берутся в разной пропорции, что отражено в инструкции. В современных компаундах наиболее часто встречается соотношение 1:2 или 1:1.
От чего зависит скорость отверждения эпоксидной смолы
Существует расхожее заблуждение, что если взять отвердителя больше нормы, то отверждение произойдет быстрее. Самый простой способ ускорения полимеризации — повысить температуру реагирующей смеси. Увеличение температуры на 10°С ускоряет процесс в 2-3 раза. Существуют специальные компаунды, содержащие ускорители отверждения, а также эпоксидные составы, способные застывать при низкой температуре. Температура смеси и тип отвердителя являются основными факторами влияния на скорость отверждения.
Преимущества эпоксидных смол
Эпоксидная смола имеет значительные преимущества перед аналогичными материалами:
- высокая прочность клеевого соединения,
- минимальная усадка,
- незначительная влагопроницаемость в отвержденном виде,
- высокая устойчивость к абразивному износу,
- лучшие физико-механические параметры.
Виды эпоксидных смол
Температура отверждения эпоксидной смолы варьирует от -10 до +200°С в зависимости от вида применяемого состава. Различают смолы холодного и горячего отверждения. Эпоксидная смола и отвердитель холодного типа используется чаще всего в быту, на производствах с малой мощностью и там, где не допускается термическая обработка. Для изготовления высокопрочных изделий, способных выдерживать сильные нагрузки, высокую температуру и активные химические вещества, применяют отверждающие компоненты горячего типа. При горячем отверждении формируется более густая сетка полимерных молекул. Разработаны эпоксиды и составы, которые застывают в условиях влажной среды и даже в морской воде.
Где применяется эпоксидная смола
Эпоксидные материалы широко распространены во всем мире с середины прошлого века.
В последние годы характер их применения претерпел значительные изменения, но остается традиционным использование в следующих областях:
- Для пропитки стеклоткани или стеклонити.
- Покрытия для гидроизоляции. Эпоксидная смола нашла эффективное применение для гидроизоляции пола и стен подвальных помещений и бассейнов.
- Химически стойкие покрытия. Краски и материалы для внутренней и наружной отделки зданий. Пропитки для повышения прочности и гидроизоляции пористых материалов: бетон, дерево и другие.
- Прозрачный твердый материал, получаемый способом заливки в формы с последующей механической обработкой, путем резания и шлифовки. Применяется для изготовления стеклопластиковых изделий в строительстве, электронной промышленности, дизайнерских работах, домашнем хозяйстве.
Подготовка поверхности для нанесения эпоксидной смолы
Независимо от вида поверхности, при нанесении эпоксидного состава необходимо соблюдение ряда правил для качественной адгезии (прилипания):
- Обезжиривание.
На поверхности должны отсутствовать следы жира и нефтепродуктов. Поверхность обычно очищают с применением эффективных моющих средств или растворителей.
- Отсутствие глянца. Тонкий верхний слой снимают путем шлифования. Малые поверхности подготавливают вручную наждачной бумагой. Большие площади обрабатывают шлифовальными машинами, образовавшуюся пыль убирают промышленным пылесосом.
- При изготовлении слоистого стеклопластика или послойной укладке наливных эпоксидных полов, красок и лаков каждое следующее покрытие наносят на не полностью застывший и еще липкий предыдущий слой.
- Если допускает технология и требования к готовому продукту, то подложку (нижний слой) посыпают мелким песком, после отверждения лишний песок удаляют и наносят новый слой.
Эпоксидный клей
Эпоксидная смола особенно хорошо проявила свои свойства и получила широкое применение в качестве клея.
Свойства и применение эпоксидного клея
Именно эпоксидные смолы больше всего подходят для создания защитных слоев или склеивания материалов с непористой поверхностью: алюминий, сталь, тик, дуб, эвкалипт и другие плотные породы дерева, керамика, фаянс.
В качестве универсального клея используют специальные эпоксидные составы с прочной адгезией ко многим материалам. Их конечные свойства после отверждения варьируют в большом диапазоне. Клеевые составы бывают эластичные и жесткие. Для работ в бытовых условиях выпускаются составы, не требующие точного соблюдения пропорции смолы с отвердителем. Она составляет от 100:40 до 100:60. В комплект таких составов входит отвердитель холодного типа.
Эпоксидный клей считается одним из наиболее универсальных и надежных средств, благодаря качественной адгезии и прочности соединения. Применяется для склеивания деталей в самых разных сферах деятельности, начиная с обувных мастерских и заканчивая авиастроением.
Как приготовить эпоксидный клей
Для получения клея эпоксидную смолу смешивают с отвердителем в малом количестве (несколько граммов) при комнатной температуре. Стандартная пропорция эпоксидной смолы и отвердителя – 1:10. Точного соблюдения пропорции не требуется.
Как приготовить большой объем эпоксидной смолы
Незнание специфических свойств эпоксидной смолы приводит к проблемам при изготовлении большого объема смолы с отвердителем. Чем больше количество эпоксидного материала, тем сильнее выделяется тепло. Если эпоксидная смола с отвердителем не рассчитана для смешивания в больших количествах, то сразу после соединения смесь моментально полимеризуется, становится плотной и непригодна к дальнейшему использованию. В худшем случае, смесь вскипает, выделяется едкий дым, наступает самовозгорание. Это связано с лавинообразным разогреванием смолы, что ускоряет реакцию полимеризации и вызывает еще более интенсивное теплообразование.
При покупке эпоксидной смолы и отвердителя, следует уточнить и проконсультироваться у специалиста, для каких целей она предназначена. Из специального состава для большого объема получается чистая, прозрачная, без воздушных пузырей и равномерно застывшая отливка.
Технология производства большого объема эпоксидного состава, например, несколько килограммов, отличается от замешивания нескольких граммов клея. Прежде, чем добавить пластификатор и отвердитель, смолу нагревают для уменьшения вязкости. Иногда смола при длительном хранении становится вязкой или кристаллизуется и мутнеет. Чтобы устранить эти явления, смолу подогревают на водяной бане. Емкость со смолой опускают в воду и нагревают до температуры 50-60С.
Следует знать, что увеличение температуры на 10°С ускоряет реакцию полимеризации в 2-3 раза. При закипании эпоксидная смола вспенивается, становится мутно-белой. Такой состав не пригоден к использованию. Иногда для уменьшения вязкости добавляют растворители и разбавители. Даже небольшая концентрация растворителя (5-7% от всего объема) приводит к выраженному снижению прочности и теплостойкости изделия. Впоследствии любой разбавитель «выпотевает» из полимера, что влечет еще большее ухудшение качества материала.
Необходимо полностью исключить наличие воды в эпоксидной смоле и отвердителе. В результате попадания воды, эпоксидная смола становится мутной, теряет свои свойства. В настоящее время выпускается водоразбавляемая эпоксидная смола. Такие составы специально разводятся дистиллированной водой для получения дисперсии.
Процесс смешивания компонентов эпоксидного материала начинают с добавления пластификатора. Смесь эпоксидной смолы с ДБФ медленно нагревают, при применении ДЭГ-1 – просто перемешивают. Для более тщательного смешивания используют строительный миксер или специальную насадку на дрель. Пропорция эпоксидной смолы и пластификатора подбирается в зависимости от требуемой пластичности, но чаще всего доля пластификатора составляет 5-10%.
В смесь эпоксидной смолы с пластификатором добавляют отвердитель. Желательно остудить эпоксидную смолу до 30°С, чтобы не допустить закипания смеси. Стандартная пропорция смолы с отвердителем – 1:10. Иногда в специфических технологических условиях соотношение сильно варьирует от 1:5 до 1:20. Для равномерного растворения отвердителя в смоляной части необходимо постоянное перемешивание. Иначе отверждение получится неоднородным и несвязанный отвердитель в последствие будет выпотевать. Для качественного смешения отвердитель наливают постепенно, очень медленно тонкой струйкой, при постоянном перемешивании смоляной части.
Даже временное повышение концентрации отвердителя в части емкости приводит к «вскипанию» эпоксидной смолы. Смола становится матово-белой и покрывается пеной и в результате не пригодна к применению. Для большого объема в несколько килограмм понадобится дрель со специальной насадкой и низкими оборотами. Реакция соединения эпоксидной смолы с отвердителем является экзотермической, с выделением тепла. Иногда при добавлении отвердителя происходит слишком быстрое нагревание эпоксидной смолы и практически моментальное затвердевание. Это связано с передозировкой отверждающего компонента и повышенной исходной температурой эпоксидной смолы.
Что такое «время жизни» эпоксидной смолы
«Временем жизни» эпоксидного состава называют промежуток времени, в течении которого композиция сохраняет жидкое или вязкое состояние после соединения смолы с отвердителем и пригодна для переработки. «Время жизни» отличается у разных видов смол и отвердителей. Выпускаются композиции, которые отверждаются при -10°С, а есть — от +100°С и выше. Смесь смолы и отвердителя пригодна для использования обычно в течение 30-60 минут, что зависит от температуры смолы, вида и количества отвердителя.
Как изготовить объемные изделия из эпоксидной смолы
Изготовление крупного изделия из эпоксидной смолы имеет определенные сложности. Оно должно быть прозрачным, без пузырьков воздуха. Отверждение в толще и на поверхности должно быть равномерным.Если толщина изделия более 2 мм, то материал обычно наносят слоями после первичной полимеризации предыдущего покрытия.
Эпоксидную смолу можно заливать в формы. Чтобы готовое изделие легко отделялось, форму смазывают техническим вазелином или другим жиром. С помощью порошкового красителя изделию придается любой цвет. После завершения работы изделие сначала выдерживают при температуре немного выше комнатной. Через 2-3 часа наступает первичная полимеризация, отверждение «до отлипания», после чего изделие прогревают в жарочном шкафу для ускорения процесса отверждения до 5-6 часов.
При комнатной температуре полная полимеризация длится до 7 дней, а при добавлении ТЭТА (триэтилентетрамин) поверхность может остаться липкой.
Отлитое из эпоксидного материала изделие в дальнейшем подлежит механической обработке (резанию и шлифованию).
Эпоксидная смола отечественного производства малопригодна для отливки массивных изделий из-за неравномерного отверждения в толще.
Как придать цвет эпоксидной смоле
В домашних условиях сложно приготовить окрашенный эпоксидный состав определенного цвета. Чтобы пигмент равномерно распределился в смоле и после отверждения получилась качественная поверхность, производители используют в цветных эпоксидных составах десятки различных ПАВ (поверхностно-активных веществ). Следует помнить, что пигментирование снижает прозрачность смолы, иногда темнеет или меняет цвет. Пигмент добавляют до катализатора, но после воска.
С чем можно комбинировать эпоксидную смолу
Эпоксидные составы используют с тканными материалами для усиления прочности сцепления в условиях жесткой эксплуатации, но высокая стоимость ограничивает их широкое применение.
Возможна комбинация эпоксидной смолы с другими видами смол, например, с полиэфирными. Главное правило при комбинации разных видов смол – они не должны контактировать в жидком и неотвержденном виде. Жидкую эпоксидную смолу наносят поверх застывшего полиэфирного слоя. При обратном комбинировании полиэфирная смола на эпоксидном покрытии держится плохо. Если необходима именно такая последовательность нанесения, то отвержденную эпоксидную поверхность зачищают наждачной бумагой или протирают растворителем. Это позволит добиться максимально возможной адгезии.
Правила техники безопасности
В неотвержденном состоянии эпоксидная смола опасна для здоровья. Необходимо принять максимальные меры предосторожности, особенно в отношении аминных отвердителей.
Многие эпоксидные компаунды способны вызвать дерматиты, ожоги кожи, поражение органов дыхания.
При работе с химическими веществами очень важно неукоснительно соблюдать правила безопасности:
- Нельзя использовать посуду, предназначенную для хранения и приготовления пищи.
- Работы с эпоксидными смолами разрешается проводить только в спецодежде, перчатках, с защитным кремом. При шлифовании отвержденных изделий обязательно надевают очки и респиратор.
- Эпоксидно-диановую смолу хранят в плотно закрытой емкости при температуре не более 40°С. Срок хранения 12 месяцев.
- При попадании на кожу эпоксидную смолу немедленно смывают водой с мылом или вытирают денатурированным спиртом.
- Все работы с эпоксидными составами должны выполняться в помещении с приточно-вытяжной вентиляцией.
Характеристики эпоксидной смолы ЭД-20
По химическому составу эпоксидная смола ЭД-20 представляет собой олигомер на основе диглицидилового эфира дифенилолпропана.
Для отверждения диановой эпоксидной смолы ЭД-20 используют различные вещества — алифатические и ароматические амины, полиамиды, поликарбоновые кислоты и их ангидриды, фенолформальдегидные смолы и другие соединения. В зависимости от вида отверждаемого агента, характеристики смолы ЭД-20 изменяются в широких пределах.
- ЭД-20 применяется в промышленном производстве и в чистом виде, и в составе композиционных материалов: заливочные и пропиточные компаунды,
- клей,
- герметик,
- армированный пластик,
- защитные покрытия.
Эпоксидная смола ЭД-20 не является взрывоопасной, но горит в источнике огня. Содержит летучие вещества (толуол и эпихлоргидрин) в микроскопических дозах. По степени воздействия на организм человека эти соединения относятся ко 2-му классу опасности.
Стандарты качества эпоксидной смолы
При покупке эпоксидной смолы, особенно больших объемов для масштабных работ, необходимо проверить характеристики на соответствие стандартам качества по ГОСТ. Например, качественные показатели эпоксидной смолы ЭД-20 высшего сорта по ГОСТ 10587-84 включают:
- Внешний вид — высоковязкая прозрачная без механических включений и следов воды.
- Цвет по железокобальтовой шкале — не более 3.
- Динамическая вязкость, при 20 °С — 13-20 Па*с.
- Время желатинизации с отвердителем — не менее 8,0 ч.
- Кроме того предусмотрены нормы содержания различных химических соединений : массовая доля эпоксидных групп — 20,0-22,5%, хлора — не более 0,001%, омыляемого хлора — не более 0,3%, гидроксильных групп — не более 1,7%, летучих веществ — не более 0,2%.
Упаковочная тара для эпоксидных смол — стальные ведра, барабаны, бочки.
Стоимость эпоксидной смолы ЭД-20 от 140 до 220руб/кг в зависимости от объема упаковочной тары.
Использование эпоксидной смолы для защитного покрытия древесины
Эпоксидное покрытие древесины служит для создания водонепроницаемого барьера и поддержания стабильного уровня влаги. Наиболее часто эпоксидная защита применяется при изготовлении и ремонте лодок и яхт. Для деревянных лодок используют пластифицированную эпоксидную смолу, которая обладает достаточной эластичностью и упругостью. Эта особенность позволяет обрабатывать детали на столе, а затем устанавливать на корпус лодки. Смолу смешивают с отвердителем в нужной пропорции и аккуратно укладывают ровным слоем сначала резиновым шпателем, а затем поролоновым валиком.
Как только поверхность перестанет липнуть, наносят следующий слой. Для большей надежности склеивания каждый слой рекомендуется зашлифовать вручную наждачной бумагой или шлифмашинкой. Шлифование финишного слоя можно заменить циклеванием, снятием тонкой стружки эпоксидной смолы. Эпоксидное покрытие является хорошей основой для лака. В завершении наносят два лаковых слоя. Нежелательно работать на ярком солнце
Применение эпоксидной смолы для пропитывания стеклоткани
Наружные поверхности корпуса лодки или яхты часто покрывают эпоксидной смолой со стеклотканным армированием. Такое покрытие обладает высокой износоустойчивостью, водонепроницаемостью, противостоянием ударам. Независимо от типа стеклоткани и вида смолы процесс оклейки не сложен, нужно просто приклеить ткань к поверхности. Главная задача — не допустить перерасхода эпоксидной смолы. Для этого:
- Наносят предварительный слой смолы.
- После отверждения заделывают впадины смесью смолы.
- Выравнивают выступы и наплывы.
- Протирают пыль чистой влажной тряпкой.
- Раскатывают стеклоткань по поверхности.
- Закрепляют её малярной лентой.
Не следует разводить слишком много смолы с отвердителем, достаточно полкилограмма, приблизительный расход 300г на кв.м. Если поверхность горизонтальная, смолу просто наливают на покрытие зигзагообразными линиями и распределяют резиновым шпателем, наклонную поверхность обрабатывают валиком. Для равномерного распределения смолы, прочного сцепления и выдавливания воздушных пузырьков по приклеенной стеклоткани еще раз проходят чистым валиком. Когда покрытие немного затвердеет, излишки стеклоткани обрезают бритвой.
Прочность на века
В последнее время на рынке появилось много новых эпоксидных компаундов, еще более эффективных и безопасных. Эпоксидные составы успешно конкурируют с традиционными материалами: деревом, металлом, керамикой. Эпоксидные смолы более прочные, долговечные, устойчивые к коррозии. У эпоксидных материалов большое будущее и безграничные возможности применения.
Свойства эпоксидной смолы для творчества
В этой статье мы разберём общие свойства эпоксидной смолы, какие бывают разновидности, а также смолу какой вязкости применять для творчества. Для чего предназначена каждый из видов смолы и узнаем её эксплуатационные качества.
Содержание
- Свойства эпоксидной смолы
- Сферы применения эпоксидной смолы
- Состав эпоксидной смолы
- Правила хранения и соотношения
- Повышенная вязкость эпоксидной смолы для творчества
- Средне вязкая смола
- Качества и достоинства низко вязкой эпоксидной смолы
Свойства эпоксидной смолы
Эпоксидная смола — знакомый многим материал обладающий уникальными свойствами. На вид смола представляет собой густую тягучую жидкость прозрачного или немного желтоватого цвета. Одной из главной особенностей «эпоксидки» является ее высокая адгезия к различным материалам, таким как:
- различные металлы
- древесина всевозможных пород
- керамика
- кожа
- резина
- пластик
- стекло и т.д
Это свойство смолы позволяет использовать ее как универсальный клей.
Другой особенностью эпоксидной смолы выделяют ее высокую прочность и стойкость к механическим и иным воздействиям. Эпоксидка не проводит электричество и обладает абсолютной водонепронецаемостью.
В зависимости от вида эпоксидки отличаются и её технические особенности:
- теплостойкость
- плотность
- прозрачность
- время отверждения
- температура для полимеризации
- прочность на сжатие и растяжение
Сферы применения эпоксидной смолы
Преимуществ у эпоксидной смолы огромное множество. Применяется она повсеместно – в творчестве, рисовании, в быту, строительной и промышленной отрасли. Всё благодаря её стойкости и минимальной скорости износа, а также практически полному отсутствию усадки.
Сферы применения смол:
- для сувенирной продукции
- для ювелирных изделий
- прозрачные отливки аксессуаров
- декоративные полы
- панно на стены
- рисование картин
- столешницы под камень
- мебель и столы
- предметы освещения
- дизайнерский декор и т.д
Состав эпоксидной смолы
Любая эпоксидная смола представляет собой двухкомпонентный состав — смола и отвердитель для нее (компонент А и компонент Б). После добавления в неё отвердителя, смола постепенно застывает, и переходит в нерастворимое соединение.
Именно соединения этих составов позволяет запустить процесс полимеризации, доводя запланированные изделия до конца. Всегда обращайте внимание при покупке на полный комплект этих средств.
Правила хранения и соотношения
Соотношение компонентов может отличаться и быть как равным, так и смещаться в разные стороны. От соблюдения правильности пропорций смолы и отвердителя зависит качество готового полимера – избыток или нехватка одного из компонентов несомненно отразится на качестве.
Производитель смолы в инструкции или на самом флаконе приводит правильно подобранные пропорции для состава. Если игнорировать этот факт и смешивать неправильно, снижается его прочность и она попросту не засохнет до конца и останется липкой массой.
На этот же фактор влияет и недостаточное смешивание, оба компонента должны тщательно быть перемешаны. Также на конечный результат эксплуатации влияет хранение материала, температура не должна достигать высоких и слишком низких температур в месте где хранится смола.
Повышенная вязкость эпоксидной смолы для творчества
Существуют разные виды смол, и зависят их назначения от их свойств. Поподробнее остановимся на их различии.
В своём творчестве я часто применяю смолу именно вязкую с ускоренным временем отверждения. При рисовании картин с имитацией камня и натуральных минералов подходит отлично.
А именно медленно растекается сохраняясь на поверхности, и смешение цветов происходит более контролируемо за счёт более густого состава. Для техники Resin Art я предпочитаю её.
Также она применяется в производстве бесцветных, жестких, износостойких декоративных покрытий и заливок. В комплекте с отвердителем представляет собой бесцветный состав без запаха.
Приобрести на нашем сайте такую смолу в различных дозировках и наборах.
Средне вязкая смола
Средне вязкая смола больше подойдёт для бижутерии, гибридной мебели, заливке столешниц, литье сувениров; возможно также применение в качестве заливочного состава для полов.
Внешний вид – прозрачная состав менее густая, имеет увеличенное время жизни
Качества и достоинства низко вязкой эпоксидной смолы
Данную смолу часто применяют для изготовления стеклопластиковых конструкций для лодок, яхт, катеров, различной техники, как склеивающий и антикоррозионный состав.
Купить наборы для рисования эпоксидной смолой
Вдохновиться идеями — Pro Dezign
Полезные статьи
Ваша Алёна
Творческая мастерская ALX STUDIO
Получение и строение эпоксидных смол
Особенности строения эпоксидных смол объясняются наличием в их макромолекулах двух видов функциональных групп эпоксидных и гидроксильных. Свойства эпоксидных смол зависят от применяемых исходных соединений и способов получения.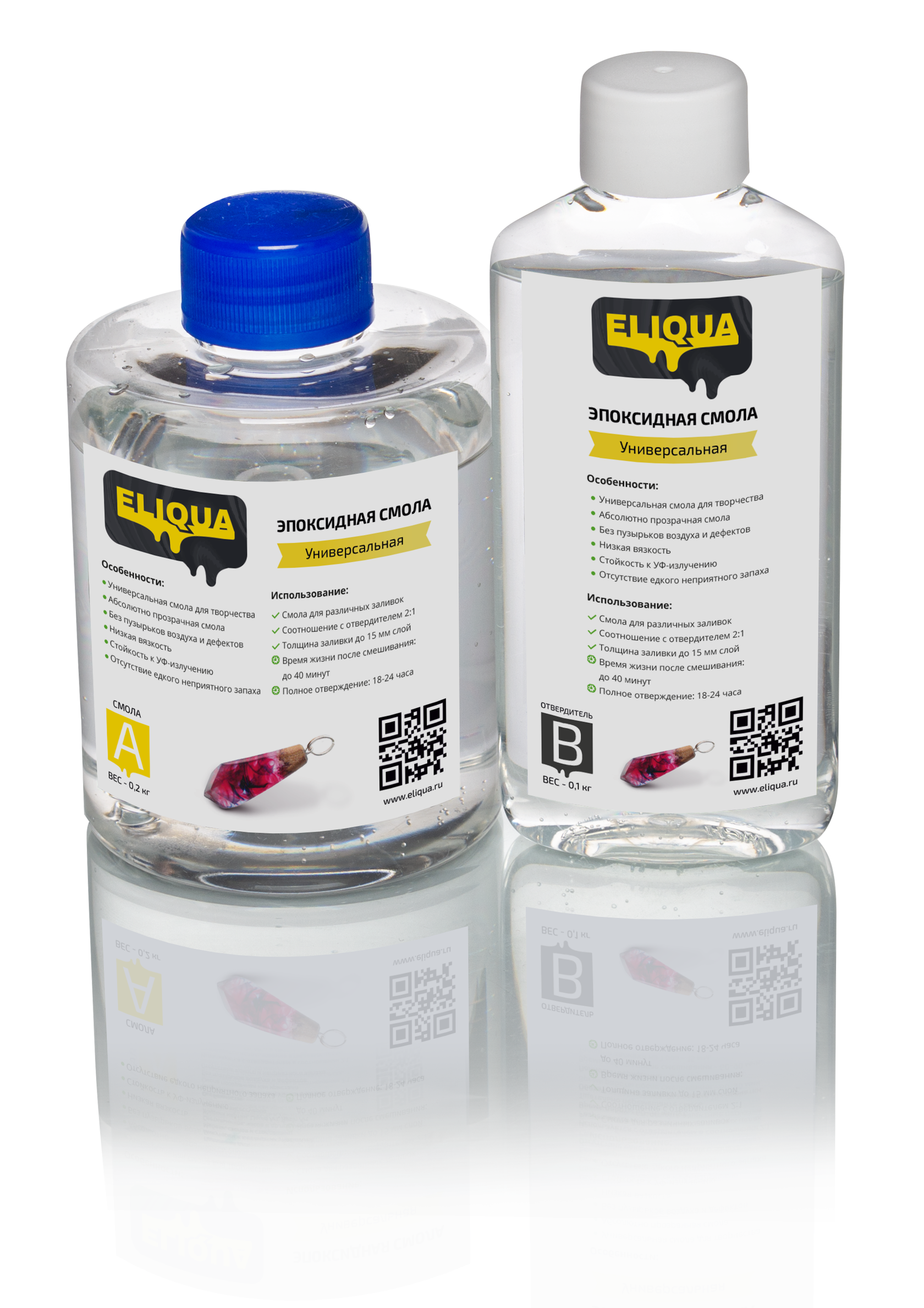
По спектрам ЯМР И и С было установлено строение эпоксидной смолы, полученной действием эпихлоргидрина на фенолфталеин [156]. [c.72]
В зависимости от строения молекул амина и исходной эпоксидной смолы, а также режима формирования полимера, значение его ТТД колеблется в интервале от 60 до 120°С. Полимеры, полученные с помощью алифатических полиаминов, отличаются высокой адгезионной способностью, механической прочностью, стойкостью к воздействию растворов солей и щелочей. [c.36]
В лакокрасочной промышленности применяют многие виды кислот. Ненасыщенные одноосновные жирные кислоты ie—С22 с одной, двумя, тремя и большим числом двойных связей, выделяемые из растительных масел и рыбьих жиров, используют при получении алкидных и эпоксидных смол, олиф, масляных лаков, сиккативов. Насыщенные одноосновные жирные кислоты, выделяемые из растительных масел (главным образом Схг) применяют для синтеза алкидных смол.

Эпоксидные смолы полидисперсны, молекулярный вес их колеблется от нескольких сотен до нескольких тысяч. В зависимости от строения смол и их, молекулярного веса эпоксидные смолы — это либо вязкие жидкости либо твердые тела с различной температурой плавления Такие свойства, как высокая реакционная способность хорошая адгезия к различным материалам, высокая хи мическая стойкость и механическая прочность, присущи в основном, всем эпоксидным смолам. Однако в зависи мости от строения и методов получения смолы в значи тельной степени отличаются по своим свойствам. Так [c.25]
Этерификация одноосновными кислотами. Модификация эпоксидных смол органическими одноосновными кислотами обычно используется для получения связующих веществ воздушной или горячей сушки (в зависи. мости от строения кислот), предназначенных для изготовления лаков и красок, печатных красок по металлу и паст для набивки текстиля. [c.426]
Это иллюстрируется данными, полученными Г. Перри [1801 при испытании адгезии двух эпоксидных смол А и Э (близких по химическому строению) к поверхности алюминия при различных температурах. Адге- [c.206]
Для получения эпоксидных смол наиболее приемлемыми оказались смолы с минимальным молекулярным весом, содержащие 10—13% гидроксильных групп, с температурой каплепадения по Уб
Отвердители для эпоксидных смол — применение, химия и многое другое
По своей сути, установка эпоксидных покрытий для полов включает в себя сочетание эпоксидной смолы с отвердителем, которые затем реагируют друг с другом перед нанесением на подготовленную бетонную основу. В зависимости от конкретной используемой системы смола на основе эпоксидной смолы может быть прозрачной или предварительно окрашенной. Некоторые прозрачные эпоксидные смолы имеют совместимые наборы красок, которые можно добавить для тонирования прозрачной системы на стройплощадке. В других используются специальные агрегатные компоненты для улучшения определенных рабочих характеристик, таких как повышенная ударопрочность, прочность на сжатие или сопротивление скольжению. Разноцветные элементы — например, смешанная виниловая крошка и кварц с керамическим покрытием — являются популярными декоративными дополнениями.
Смешивание нескольких компонентов высокоэффективного декоративного эпоксидного покрытия FloroMica от компании FloorCare USA, Висконсин.
Функция отвердителя эпоксидной смолы
Сами по себе эпоксидные смолы представляют собой очень стабильные жидкости с относительно длительным сроком хранения.Только при смешивании с отвердителем эпоксидной смолы они могут затвердеть должным образом. При нанесении на пол без отвердителя смола будет оставаться почти жидкой на неопределенный срок и не сможет превратиться в прочную систему покрытия пола. В отличие от красок, которые зависят от испарения влаги, чтобы в конечном итоге затвердеть в тонкую пленку, эпоксидное покрытие для пола достигает своих высоких защитных характеристик за счет контролируемой химической реакции, которая происходит между тщательно откалиброванной смолой и компонентами отвердителя.
После того, как различные элементы напольного покрытия смешаны вместе, для некоторых может потребоваться «индукция», при которой их оставляют на 15-30 минут для реакции друг с другом и проведения химического процесса перед укладкой. Тем не менее, другие системы могут иметь очень короткую жизнеспособность, что требует, чтобы смешанная жидкость была немедленно «намотана» на подготовленный бетонный субстрат и распределена, поскольку оставление смешанного продукта в виде массы в ведре еще больше увеличит скорость реакции.Когда это происходит, контейнер и его содержимое могут сильно нагреваться, а в некоторых случаях даже начинают выделять дым в результате экстремальной молекулярной активности. Хотя отдельный компонент может храниться на полке в течение нескольких месяцев или дольше, после смешивания эпоксидного покрытия и отвердителя у подрядчика может быть всего 15 минут на установку комбинированного материала. Может быть нанесено несколько слоев продукта, при этом следующее покрытие наносится в пределах интервала перекрытия, обычно в пределах от 4 до 12 часов. Способ нанесения может варьироваться в зависимости от химического состава, толщины и времени отверждения конкретной формулы. При таком объеме навыков и знаний вполне логично, что многие системы эпоксидных и других смолистых напольных покрытий коммерческого класса лучше всего устанавливаются высококвалифицированными специалистами по укладке полов.
Сверхпрочное напольное покрытие Florock в этой автомастерской намного превосходит характеристики типичных самодельных красок.
Как формула влияет на производительность
Количество и тип необходимого отвердителя зависит от типа используемой эпоксидной смолы.Эпоксидные краски, наносимые своими руками (отличные от настоящих напольных покрытий), часто бывают на водной основе или на основе растворителей и полагаются в основном, если не исключительно, на испарение для затвердевания и высыхания конечного продукта. Эти системы могут требовать небольшого количества отвердителя или совсем без него и часто содержат латексные краски для легких условий эксплуатации с добавлением эпоксидной смолы, а не настоящие эпоксидные покрытия для пола.
Настоящая эпоксидная смола для покрытия полов, хотя и является жидкостью, содержит 100% твердых веществ и использует совместимый каталитический отвердитель для создания прочно сшитых молекулярных структур, которые придают отвержденной пленке невероятную прочность, упругость и виртуальную непроницаемость.Тип и количество используемого отвердителя зависит от конкретного устанавливаемого продукта. Термин «эпоксидная смола» относится не к одному конкретному веществу, а скорее к широкому диапазону форполимерных и полимерных групп, и тип используемой эпоксидной смолы будет влиять на количество и тип необходимого отвердителя. Ученые-производители полимеров используют молекулярную массу формулы эпоксидного покрытия для пола и другие методы, чтобы определить, сколько отвердителя необходимо для эффективного отверждения. Различные составы имеют разные характеристики, при этом некоторые системы способны выдерживать более тяжелые нагрузки, большие колебания температуры, более высокий уровень влажности или повышенную химическую стойкость.
Свяжитесь с Florock, чтобы узнать больше о различных вариантах напольных покрытий для вашего проекта.
Ударная вязкость и твердость обработанных и необработанных композитов из сизалевого волокна и эпоксидной смолы
Влияние комбинированной химической обработки сизалевых волокон посредством последующих процессов мерсеризации (щелочная обработка), затем силановой обработки и, в конечном итоге, кислотного гидролиза на сизалевых волокнах был исследован. Также было изучено влияние обработанных волокон на ударную вязкость и твердость их композитов с эпоксидной смолой.Сканирующая электронная микроскопия поверхностей обработанных и необработанных волокон показала, что процессы химической обработки улучшают удаление поверхностных примесей и, следовательно, увеличивают шероховатость поверхностей волокон. Это дает увеличенную площадь поверхности для сцепления с матрицей и, следовательно, ожидается, что улучшит адгезию двух. Было обнаружено, что обработанные армированные волокном композиты имеют более высокие значения ударной вязкости и твердости, чем необработанные армированные волокном композиты. Эти более высокие значения были отнесены к лучшему межфазному сцеплению из-за лучшего механического сцепления между обработанными волокнами и эпоксидной смолой, возникающего из-за повышенной шероховатости обработанных волокон.
1. Введение
Композитный материал — это физическая смесь двух или более различных материалов, в результате чего получается компонент с превосходными свойствами по сравнению со свойствами любого отдельного компонента [1]. В отличие от металлических сплавов, каждый материал сохраняет свои отдельные химические, физические и механические свойства [1, 2].Основными преимуществами композиционных материалов являются их высокая удельная прочность и жесткость по сравнению с другими материалами, что позволяет снизить вес готовых деталей [3].
Составляющие композитного материала подразделяются на армирование и матрицу. Армирование — это прерывная фаза, а матрица — непрерывная фаза [1–3]. Армирование обычно закладывается в матрицу. Армирование обычно имеет форму волокон, листов или частиц, тогда как матрица представляет собой полимер, керамику или металл [2]. Армирование обеспечивает прочность и жесткость композитного материала [4]. Матрица, с другой стороны, передает и распределяет приложенные нагрузки к волокнам и во многих случаях обеспечивает некоторые необходимые свойства, такие как пластичность, ударная вязкость и электрическая изоляция [1, 3]. Примеры полимерных матриц включают эпоксидные смолы, полиэфирные смолы и фенольные смолы, в то время как металлические матрицы включают алюминиевую смолу, магниевую смолу и титановую смолу [3]. Наиболее распространенными методами, используемыми при производстве композитных материалов, являются прессование, пултрузия, ручная укладка, литье с переносом смолы (RTM), литье под давлением и формование нитями [1].
Композиты могут быть классифицированы как композиты, армированные частицами, или композиты, армированные волокном [3]. Композиты, армированные частицами, состоят из мельчайших частиц толщиной в микрон [5, 6] и наномасштаб [7], внедренных в матрицу. Частицы имеют вид хлопьев или порошка [8]. С другой стороны, композиты, армированные волокном, состоят из непрерывных или прерывистых волокон, которые заключены в матрицу [3].
Область повторного появления композитов, армированных волокном, — это область композитов, армированных натуральными волокнами [9].Натуральные волокна все чаще рассматриваются как экологически чистый заменитель синтетических волокон при армировании композитов на полимерной основе [2, 9]. Использование этих волокон вместо стекла и углерода, например, рассматривается в автомобильной промышленности [10]. Хотя доступно множество различных типов натуральных волокон, сизаль ( Agave sisalana ) является особенно привлекательным вариантом из-за его быстрого роста в широком диапазоне климатических условий [11] и его низкой стоимости [10].Хотя использование натуральных волокон частично удовлетворяет требованиям нормативных документов, предписывающих использование экологически чистых и устойчивых материалов [10], матричная система также должна быть рассмотрена в этом отношении. Очевидно, что предпочтительны полностью биоразлагаемые матрицы, такие как полимолочная кислота (PLA), но текущая высокая стоимость этих матриц является недостатком по сравнению с эпоксидной смолой [10]. Поэтому композиты сизаль / эпоксидная смола представляют значительный коммерческий интерес.
Несмотря на то, что натуральные волокна могут дополнять стекловолокно в полимерных композитах [12], при использовании натуральных волокон возникают ограничения в отношении механических характеристик и поглощения влаги [9].Эти ограничения существуют независимо от того, используются ли термореактивные или термопластичные полимеры в качестве матричного материала. Предыдущие исследования [13–15] показали, что основным фактором, ограничивающим механические свойства композитов из натуральных волокон, является химическая несовместимость между гидрофильными лигноцеллюлозными молекулами натурального волокна и гидрофобной молекулой смолы. Эта несовместимость приводит к трудностям в обеспечении эффективного соединения поверхности раздела волокна и матрицы, что, в свою очередь, вызывает неэффективную передачу нагрузки между армирующим материалом и матрицей [10, 12, 13]. Были предложены различные варианты, включая химическую обработку натуральных волокон и использование агентов совместимости, чтобы достичь необходимой совместимости поверхностных энергий между волокнами и матрицей. Ли и др. [16] представили обзорную статью о различных химических обработках, используемых для улучшения совместимости между натуральными волокнами и полимерными матрицами. Были рассмотрены такие подходы, как мерсеризация (обработка щелочью), обработка силаном, ацетилирование, бензоилирование, использование малеинированных связывающих агентов, обработка пероксидом, обработка перманганатом и обработка изоцианатом.Среди различных представленных методов широко описаны методы мерсеризации и обработки силаном.
Мерсеризация заключается в погружении волокон на некоторое время в щелочной раствор. Он работает за счет увеличения шероховатости поверхности волокна, что улучшает механическое соединение с матрицами [16]. Это также подвергает большее количество целлюлозы на поверхности волокна потенциальному химическому связыванию с матрицами [17]. Обработка силаном включает замачивание волокон в слабом растворе силана, разбавленного в смеси вода / спирт или вода / кетон.В присутствии воды силан распадается на силанол и спирт. Силанол реагирует с ОН-группами целлюлозы в натуральных волокнах, образуя стабильные ковалентные связи на клеточной стенке, которые хемосорбируются на поверхности волокна [16]. Использование силана улучшает степень сшивки в области границы раздела и увеличивает площадь поверхности волокна, обеспечивая более прочную связь между волокном и матрицей [18]. Кислотный гидролиз включает в себя жесткую кислотную обработку натуральных волокон, которая заставляет аморфные области лигнина разрушаться, высвобождая отдельные кристаллиты целлюлозы.Серная кислота и соляная кислота широко используются при проведении кислотного гидролиза [19].
Хотя большинство исследователей использовали либо щелочную обработку, либо обработку силаном, либо кислотный гидролиз по отдельности, необходимо попытаться использовать три метода обработки в комбинации, поскольку механизмы их воздействия на натуральные волокна совершенно разные. Эррера-Франко и Валадес-Гонсалес [20] рассматривали полиэтилен высокой плотности [HDPE], армированный волокнами генекена с объемной долей 20%.Воздействие обработки щелочью и силаном на эти волокна изучалось индивидуально в дополнение к эффекту комбинации двух обработок. Было обнаружено, что обработка щелочью почти не привела к улучшению, тогда как силан привел к улучшению на 19%. Когда рассматривалась комбинация лечения, было улучшение на 30%.
Испытания на ударную нагрузку обычно проводятся на самых ранних стадиях процесса проектирования, чтобы определить целостность материала при ударной нагрузке.Испытания на удар обычно проводятся для определения максимальной ударной нагрузки, которую материал может выдержать при определенной температуре [21]. Ударопрочность композитов, армированных волокном, как и других материалов, измеряется несколькими методами испытаний, а именно: по Шарпи, Изоду, падающим грузом, разрезным стержнем Гопкинсона (SHB), взрывчатым веществом и баллистическим ударом [22]. Результаты испытаний на удар представлены в виде энергии разрушения, накопления повреждений и / или измерения количества падений для достижения определенного уровня повреждения или напряжения.Результаты зависят от многих переменных, таких как размер образца, скорость деформации, тип оборудования и испытательная установка [22].
Wang et al. [23] идентифицировали два различных механизма повреждения композитов, армированных волокном, которые были нагружены системой удара падающим грузом. Для фракций волокна, меньших критического объема волокна, разрушение волокна преобладает в механизмах разрушения, в то время как для более высоких значений, чем критический объем волокна, механизм вытягивания волокна доминирует в отклике.
Рамирес и Фроллини [24] использовали испытание на ударную вязкость без надреза по Изоду для исследования ударных свойств танин-фенольных композитов, армированных сизалевым волокном.Они проводили свои исследования в соответствии со стандартом ASTM D256. Исследователи обнаружили, что улучшение межфазной связи было основной причиной улучшения ударной вязкости. Авторы сообщают, что повышенные кислотные центры на поверхности волокон сизаля улучшают межфазную адгезию. Исследователи также сообщили, что ударная вязкость композитов по Изоду увеличивается с увеличением содержания волокна до максимального содержания волокна 50%. Однако при содержании волокон свыше 50% ударная вязкость по Изоду снижалась из-за неэффективной пропитки смолой волокон.Исследователи пришли к выводу, что использование сизалевых волокон в качестве армирующего материала в танин-фенольной смоле было полезным, поскольку они значительно улучшили ударные свойства композита.
Han-Seung et al. [25] провели исследование влияния различных добавок, улучшающих совместимость, на прочность на разрыв и ударную вязкость по Изоду лигноцеллюлозных материалов. Полиэтилен низкой и высокой плотности использовался в качестве матрицы, в то время как мука из рисовой шелухи и древесная мука использовались в качестве армирования. Малеинированный пропилен и малеинированный полиэтилен использовали в качестве агентов, улучшающих совместимость, для улучшения адгезии волокна к матрице. Исследователи обнаружили, что малеинированный полиэтилен улучшил ударную вязкость по Изоду образцов с надрезом из-за усиления межфазной адгезии между волокном и матрицей. С другой стороны, ударная вязкость по Изоду композитов, изготовленных из малеинированного полипропилена, армированного рисовой шелухой, немного снизилась. Исследователи пришли к выводу, что ударная вязкость по Изоду композитов с малеинированным полиэтиленом немного улучшилась из-за лучшего межфазного связывания между матрицей и волокном.
Твердость означает сопротивление твердого тела локальной деформации. Твердый индентор помещается на поверхность материала и затем вдавливается в материал. Затем измеряют размер образовавшегося постоянного углубления для определения твердости материала. Обычными методами, используемыми для измерения твердости, являются испытание на твердость по Бринеллю, испытание на твердость по Роквеллу, испытание на твердость по Виккерсу и испытание на твердость по Барколу. Хотя обычно используются методы определения твердости по Бринеллю, Роквеллу и Виккерсу, испытание на твердость по Барколу проводится редко.
Kumar et al. [26] изучали твердость обработанных и необработанных образцов, армированных гибридными композитами на основе сизаля и стеклянной эпоксидной смолы, с использованием машины для определения твердости по Роквеллу. В каждом случае были протестированы пять образцов, и среднее значение было сведено в таблицу. Образцы для испытаний были изготовлены в соответствии со стандартом испытаний ASTM D 785. Диаметр использованного шарикового индентора составлял 0,25 дюйма, и все показания были сняты через 10 секунд после того, как индентор прочно соприкоснулся с образцом. Все поверхности образцов были затерты гладкой наждачной бумагой, что обеспечивает точное считывание.Было обнаружено, что композиты с длиной волокна 2 см имели более высокую твердость, чем композиты с длиной волокна 1 см и 3 см.
В этой статье исследуется влияние трех комбинированных химических обработок, а именно мерсеризации, обработки силаном и кислотного гидролиза, на сизальевые волокна. Также изучается влияние этих комбинированных обработок на ударную вязкость и твердость их композитов с эпоксидной смолой. Это контрастирует с другими исследованиями удара и твердости, в которых эти методы лечения использовались индивидуально.Композиты были изготовлены методом вакуумной инфузии изготовления композитов. Этот метод предотвращает попадание воздуха в производимые композиты и образование пустот, и ожидается, что он будет способствовать достижению высокой прочности и жесткости получаемых композитов. Кроме того, этот метод отличается от других технологий изготовления тем, что создание вакуума в полости формы обеспечивает попадание смолы в форму и через уложенные волокна [27] под действием атмосферного давления и, следовательно, обеспечивает надлежащее смачивание армирующих волокон.Пузырьки воздуха все еще могут попадать в систему в процессе смешивания смолы и отвердителя перед загрузкой в форму, а также через утечки из формы. Это, однако, недостатки, которые устраняются в процессе инфузии.
2. Детали эксперимента
2.1. Материалы
Эпоксидная смола Epolam 2015 и отвердитель Epolam 2014 были получены от компании AMT composites в Южной Африке. Соотношение в смеси смолы и отвердителя согласно паспорту, полученному от компании, составляло 100: 32.Пачка сизалевых волокон по 10 кг была получена с фермы Моготио, округ Накуру, Республика Кения. Реагентами, которые использовали в этой работе, были: гидроксид натрия, 3-глицидилоксипропилтриметоксисилан, метанол и соляная кислота (HCL). Гидроксид натрия был предоставлен компанией Minema Chemicals (Pty) limited, в то время как 3-глицидилоксипропилтриметоксисилан, метанол и соляная кислота были предоставлены компанией Sigma Aldrich limited, все из Южной Африки.
2.2. Приготовление обработанных сизалевых волокон
Сизалевые волокна мерсеризовали путем погружения в 5% раствор гидроксида натрия на 20 часов.Затем волокна промывали дистиллированной водой, чтобы удалить из них гидроксид натрия, а затем дополнительно погружали в 1% уксусную кислоту, чтобы нейтрализовать любой оставшийся гидроксид натрия. После этого волокна были погружены в раствор силана, состоящий из 5% 3-глицидилоксипропилтриметоксисилана, разведенного в 95% водном растворе метанола, чтобы затем гидролизовать силан и сделать его активным [16]. . После этой обработки волокна погружали в 67,5% раствор соляной кислоты на 1 час [28].После этого обработанные волокна промывали деионизированной водой и сушили в печи при 45 ° C в течение 24 часов.
2.3. Производство композитов
Для изготовления композитов использовался метод вакуумной инфузии для изготовления композитов, как показано на рисунке 1. Этот метод поддерживает надлежащее смачивание армирующих волокон, что приводит к лучшему и более прочному межфазному соединению волокна и матрицы. Этим методом были изготовлены как обработанные, так и необработанные композиты сизалевое волокно-эпоксидная смола.Волокна сизаля были разрезаны с помощью ножниц и выпрямлены с помощью гребня, чтобы избежать скопления волокон, которое в противном случае минимизировало бы смачивание волокон смолой и, следовательно, снизило бы эффективность армирования. Затем волокна взвешивали с использованием электронных весов с точностью до 0,5 г и группировали по разным массам, соответствующим разным массовым долям волокон. Тонким слоем воска намазывали основание квадратной стеклянной формы размером 50 на 50 см. Воск гарантирует, что композит легко удаляется из стеклянной формы после отверждения.Заданные веса волокон сизаля были распределены продольно в стеклянной форме. Затем волокна одновременно покрывали слоем кожуры и сеткой для инфузии. Отрывной слой изготовлен из полиэфирного материала и используется для удаления небольших излишков смолы. Сетка для инфузии была сделана из пластика, и она помогает смоле эффективно течь по волокнам. Затем около выхода трубки из вакуума кладут ткань для удаления воздуха, чтобы излишки смолы могли всасываться через трубку в ловушку для смолы.Затем были подсоединены обе спиральные трубки: одна к трубке от стакана со смолой, а другая к вакууму. После этого для покрытия всей отливки использовали вакуумный мешок. Затем использовали липкую ленту для прикрепления вакуумного мешка к форме. Электродвигатель вакуумного насоса был включен, и трубка, ведущая к контейнеру для хранения смолы, была временно закрыта с помощью G-зажима, чтобы избежать всасывания воздуха в волокна перед созданием вакуума.
Во время приготовления смолы давали перерыв в один час при работающем вакуумном насосе.Затем смола и отвердитель были измерены в соответствующих соотношениях с использованием электронных весов с точностью ± 0,5 г и затем смешаны с помощью шпателя. Захват воздуха в смоле устраняли путем прокалывания пузырьков воздуха острой иглой. После разрыва всасывающая труба для смолы была помещена в контейнер для смолы, и закрывающий G-образный зажим на трубе был снят, чтобы обеспечить всасывание смолы на волокна. Композиты из эпоксидной смолы, армированные сизалевыми волокнами, были впоследствии отверждены на воздухе в течение 24 часов.После этого отверждения на воздухе композит был дополнительно отвержден в печи при 80 ° C в течение четырех часов, как рекомендовано поставщиком, для получения композитов с превосходными механическими свойствами. Армирование варьировалось от 0 до 50 мас.% Включительно в разных композитах.
2.4. Испытания на ударную вязкость
Для определения вязкости разрушения изготовленных композитов были проведены испытания на ударную вязкость по Шарпи при комнатной температуре с использованием прибора Hounsfield Balanced Impact Tester (Tensometer Ltd. , Кройдон, Англия). Тестер сбалансированного удара Хаунсфилда оказывает трехточечный удар, аналогичный тому, который создается прибором Шарпи, указанным в ASTM D6110-10. Образцы для испытаний с геометрией 50 × 12 × 5 мм в длину, ширину и толщину соответственно были вырезаны из литых композитов на станке с ЧПУ. Для каждого состава делали V-образный надрез 45 ° ± 1 °, радиус основания 0,25 ± 0,05 мм и ширину надреза 2 мм. После этого образцы были отшлифованы наждачной бумагой марки 220, чтобы гарантировать, что на образцах не осталось зазубрин.Испытание на удар по Шарпи, также известное как испытание с V-образным надрезом по Шарпи, представляет собой стандартизированное испытание с высокой скоростью деформации, которое используется для определения количества энергии, поглощаемой материалом во время разрушения. Результаты, полученные при испытании на ударную вязкость по Шарпи, являются мерой ударной вязкости данного материала и могут также использоваться для определения кривой перехода материала из хрупкого в пластичное в зависимости от температуры [3].
При определении вязкости разрушения с использованием рамы для испытания на удар по Шарпи образец образца загружается горизонтально на устройство, и маятниковый молоток для испытания на удар по Шарпи отпускается для удара по образцу с надрезом на задней стороне V-образного надреза.В образцах для испытаний делается надрез, чтобы создать известную точку концентрации напряжений, при которой, как ожидается, возникнут трещины. После удара образец удаляется и исследуются его разрушенные поверхности. Если поверхность разрушения плоская и гладкая, то разрушение классифицируется как хрупкое. Если, наоборот, поверхность разрушения волокнистая, то разрушение классифицируется как пластичное. Объем текущего исследования ограничивался определением ударной вязкости композитов при комнатной температуре.
2,5. Твердость
Испытания на твердость проводились в соответствии со спецификациями стандарта испытаний ASTM D 2583 с использованием импрессора Barber Colman Barcol Impressor. Образцы для испытаний с геометрией 12,7 × 12,7 × 3 мм длиной, шириной и толщиной соответственно были вырезаны из литых композитов с помощью станка с ЧПУ. Испытание на твердость характеризует твердость материалов при вдавливании путем измерения глубины проникновения острия индентора. Barcol Impressor, модель GYZJ-934-1 состоит из усеченного конуса из закаленной стали с углом 26 ° и плоского наконечника 0.Диаметр 157 мм у толкателя пружины, который используется для вмятин на материалах.
2.6. Сканирующая электронная микроскопия
Морфология поверхности композитов с различными весовыми фракциями волокон как для обработанных, так и для необработанных композитов была проанализирована с использованием техники электронной микроскопии. Композитные поверхности анализировали с использованием Zeiss Environmental SEM (ESEM: модель EVO HD 15, работающая при 20 кВ), где образец был покрыт золотым напылением с использованием оборудования для нанесения тонкопленочного покрытия Quorum 150R ES.Покрытие было нанесено таким образом, чтобы образцы были хорошо видны. Обработанные и необработанные волокна сизаля также были сканированы.
3.
Результаты и обсуждение
3.1. Результаты СЭМ необработанных и обработанных сизалевых волокон
Необработанные и обработанные сизалевые волокна были подвергнуты сканирующей электронной микроскопии с полученными изображениями, показанными на рисунках 2 и 3.
Из изображений видно, что поперечный размеры сечения обработанных волокон сизаля (180.3 мкм м) меньше, чем у необработанных сизалевых волокон (286,6 мкм мкм). Уменьшение размера обработанных сизалевых волокон приводит к лучшим механическим свойствам получаемых композитов, чем у необработанных сизалевых волокон, за счет увеличения количества армирующих волокон (и, следовательно, объемной доли армирующих волокон), которые могут быть упакованы в поперечном сечении. матрицы.
3.2. Результаты испытаний на удар
Поверхности излома при ударе наблюдались с помощью сканирующего электронного микроскопа.Для каждого образца было проведено пять сканирований, и репрезентативные микрофотографии показаны на рисунках 4 (a) -4 (j) и 5.
Когда необработанные и обработанные композиты сравнивали по каждой массовой доле и количеству случаев возникновения Подсчитав вытягивание волокна в каждом случае, было обнаружено, что в необработанных композитах сизалевое волокно-эпоксидная смола было больше случаев выдергивания волокон, чем в обработанных композитах сизалевое волокно-эпоксидная смола. Кроме того, поверхность излома эпоксидной смолы при ударе имела гладкую поверхность излома.Более частое выдергивание волокна является четким признаком более низкой адгезии волокна к матрице. Более низкая межфазная адгезия приводит к тому, что матрица поглощает более высокие доли полной энергии, приложенной к композиту, чем в случае, когда существует более высокая межфазная адгезия, и, следовательно, приводит к более низким значениям энергии удара, когда вязкость разрушения матрицы ниже.
Средние значения ударной вязкости как для обработанных композитов сизалевое волокно-эпоксидная смола, так и для необработанных композитов сизалевое волокно-эпоксидная смола, которые были определены с использованием ударной машины по Шарпи, представлены в таблице 1. Также была определена ударная вязкость чистой эпоксидной смолы, которая также занесена в таблицу.
|
Результаты в таблице 1 ясно показывают, что энергия удара армированных композитов была увеличена за счет трех комбинированных методов обработки армирующих волокон. Об увеличении энергии удара из-за улучшенной адгезии волокна к матрице также сообщили Ramires и Frollini [24]. Средняя энергия удара обработанных композитов из сизалевого волокна и эпоксидной смолы, как видно из таблицы, увеличилась на 28,09%, 20,07%, 14,06%, 15.44% и 22,34% для композитов с 5 мас.%, 10 мас.%, 15 мас.%, 30 мас. % И 50 мас.% Соответственно по сравнению со значениями, полученными для необработанных композитов сизалевое волокно-эпоксидная смола. для одинаковых весовых долей. Стандартные отклонения энергии удара как для обработанных, так и для необработанных композитов малы, все они находятся в диапазоне от 0,12 до 0,93, в то время как коэффициент вариации как для обработанных, так и для необработанных композитов сизалевое волокно-эпоксидная смола также невелик и колеблется в пределах с 13,48% до 31.59%. Низкие значения стандартных отклонений и коэффициента вариации указывают на то, что в полученных экспериментальных данных не было большого разброса.
Из значений в приведенной выше таблице видно, что средние значения энергии удара испытанных образцов увеличились со значения 0,84 джоулей для чистой эпоксидной смолы до максимальных 10,34 джоулей и 12,65 джоулей для необработанных 50 мас.% и обработанные композиты сизалевое волокно-эпоксидная смола, соответственно. Это на 1130,95% и 1405,95% увеличения значения энергии удара, соответственно, по сравнению со значениями чистой эпоксидной смолы. Увеличение средней энергии удара для необработанных и обработанных композитов, армированных волокном, по сравнению со значениями для чистой эпоксидной смолы для пяти процентов веса: 5 вес.%, 10 вес.%, 15 вес.%, 30 вес.% И 50 вес.% Были значимыми при 35,73%, 197,62%, 313,10%, 678,57%, 1130,95% и 154,76%, 252,38%, 371,43%, 798,81% и 1405,95%, соответственно, для необработанной и обработанной сизалевой волоконно-эпоксидной смолы. композиты. Более высокие значения энергии удара для композитов из обработанного сизалевого волокна и эпоксидной смолы по сравнению с необработанными композитами из сизалевого волокна и эпоксидной смолы можно объяснить улучшенным механическим сцеплением из-за более грубых поверхностей обработанных сизалевых волокон и улучшенного межфазного сцепления.
Значения ударной вязкости, показанные в таблице 1, показаны на рисунке 6.
Графики кривых на рисунке 6 для обработанных и необработанных композитов сизалевое волокно-эпоксидная смола демонстрируют непрерывное увеличение ударной вязкости с увеличение загрузки волокна. Величина энергии удара построенной кривой для обработанных композитов сизалевое волокно-эпоксидная смола выше, чем для необработанных композитов сизалевое волокно-эпоксидная смола. Эта разница в величине двух кривых объясняется различием в усиливающих эффектах обработанного и необработанного сизалевого волокна.Кроме того, обе кривые не имеют точек минимума. Отсутствие точек минимума на обеих кривых объясняется тем, что диапазон процентных весов, при которых проводились тесты, не включал весов в минимальной точке или около нее. Коэффициент корреляции на обоих графиках очень равен единице, что означает почти идеальное соответствие кривых экспериментальным данным, построенным в обоих случаях.
3.3. Результаты испытаний на твердость
Результаты измерений твердости представлены в таблице 2 для обработанных и необработанных композитов сизалевое волокно-эпоксидная смола.Результаты при 0 мас.% Представляют чистую эпоксидную смолу.
Из таблицы 3 видно, что текущие результаты улучшают ударную нагрузку на 7–56% и твердость на 9%. значения, полученные из предыдущих результатов. Очевидно, что комбинированная химическая обработка мерсеризации, силана и кислотного гидролиза приводит к улучшению механических свойств при ударе и твердости порядка 7–56% для ударной нагрузки и 9% для твердости композита из эпоксидной смолы, армированного сизалевыми волокнами. 4. Выводы Были сделаны следующие выводы: (1) Химическая обработка поверхностей сизалевых волокон приводит к непрерывному увеличению ударной вязкости обработанных композитов из сизалевого волокна и эпоксидной смолы с увеличением массовой доли армирующих волокон (2). ) Химическая обработка поверхностей сизалевого волокна приводит к увеличению твердости композитов сизалевое волокно-эпоксидная смола. (3) Твердость как обработанного, так и необработанного композитного волокна сизалевое волокно-эпоксидная смола постепенно увеличивается с увеличением нагрузки волокна до максимальная массовая доля волокна составляет 10%, а затем снижается до массового содержания волокна 15% в результате группирования волокон, после чего постепенно увеличивается до массовой доли волокна 50% из-за увеличения пространственного распределения армирования. волокна и увеличение жесткости полученного композита.(4) Комбинированная химическая обработка мерсеризации, силана и кислотного гидролиза приводит к улучшению механических свойств при ударе и твердости, которые выше, чем в тех случаях, когда используется только один процесс обработки. Конфликт интересовУ авторов нет конфликта интересов, о котором следует раскрывать в связи с текущим исследованием. БлагодарностиИсследование было поддержано Технологическим университетом Ваала, Южная Африка. Эпоксидные смолы Somnang Rom.Применение эпоксидных смол Это типичные машины для намотки волокна «Основы производства композитов»: Материал,Презентация на тему: «Эпоксидные смолы фирмы Somnang Rom. Применение эпоксидных смол. Это типичные машины для намотки волокон.« Основы производства композитов »: Материал» — стенограмма презентации:1 Эпоксидные смолы Somnang Rom 2
Применение эпоксидных смол Это типичная машина для намотки волокон. 3 Предпосылки Эпоксидные смолы относятся к классу синтетических полимеров. Смола — это жидкая форма эпоксидной смолы до реакции с отвердителем. Химическая структура эпоксидных смол -молекулярная формула эпоксидных смол Эпоксидные смолы образуются из мономерного полимера с длинной цепью молекулярной цепи 4
Что такое эпоксидные смолы Эпоксидные смолы очень жесткие при смешивании и отверждении при любой температуре от 5 o C до 150 o C, это также зависит от отвердителя.Амин используется в качестве отвердителя, он вступает в реакцию с водородом, образующим поперечные связи и цепочки с эпоксидными смолами. 5 Эпоксидная смола Vs. Полиэфирные смолы. Преимущества эпоксидной смолы: превосходная усталостная прочность, по сравнению с полиэфирными смолами: очень низкая усадка, когда она очень жесткая, когда она затвердевает.превосходная химическая стойкость 6 Использование эпоксидной смолы в ЧПУ для намотки волокон. ЧПУ для намотки волокон. Это будет автоматизированный и недорогой метод производства цилиндрических форм. Преимущества намотки волокна — точная ориентация волокна — отрезок волокна — стабильность и повторяемость (рисунок) 7
Эпоксидные смолы и отвердитель В моем дизайне я буду использовать 50% смол и 50% отвердителя (соотношение 1: 1). 8 Вывод: — очень прочный, когда он затвердевает — эпоксидная смола очень прочная, особенно по своему весу. 10 Ссылка: Композитные лонжероны и трубы http://www.compositespars.com Обработка полимеров http://polymerprocessing.com/polymers/PA6.html Gurit Composite Technologies http: // www.spsystems.com Основы производства композитов: материалы, методы и приложения, опубликованные Обществом инженеров-производителей. Авторские права 1989 г., автор: д-р Стронг А. Брент. Механизмы упрочнения разрушения в эпоксидных клеях1. Введение Эпоксидные смолы являются одними из наиболее часто используемых полимерных материалов в конструкционных материалах, таких как клеи и армированные волокном композиты. Несмотря на широкое применение в указанных областях, эпоксидные смолы с высокой степенью сшивки являются жесткими и хрупкими по своей природе и теряют большую часть своей структурной целостности при повреждении, что ограничивает их использование в качестве конструкционных материалов (клеев и композитов). За последние три десятилетия, в том числе благодаря успешной разработке нано- и микрочастиц с различными формами, размерами и химическими характеристиками, нано- / микрочастицы широко изучались как эффективные упрочняющие вещества для преодоления естественной хрупкости эпоксидных смол.Как сообщает Kinloch [3], добавление фракций 15–20 об.% Диспергированных резиноподобных частиц (диаметр ~ 0,5–2 мкм) может приводить к увеличению скорости выделения энергии деформации G IC на фактор 10–15. Рисунок 1.Сравнение когезии и адгезии в клеевом шве. В клее можно выделить две основные силы, то есть силы сцепления и силы сцепления. Первое можно рассматривать как внутреннюю прочность материала, связанную только с химической природой с точки зрения морфологии и химической структуры. Второй определяет сложную систему взаимодействия между клеем и подложкой, поэтому на нее сильно влияет морфология контактной поверхности.Рисунок 1 показывает разницу между силами сцепления и сцепления. Рис. 2.Иллюстрация режима разрушения клеевого шва. Две сцепляющиеся поверхности могут разрушиться в соответствии с различными типами трещин (см. Рисунок 2):
В материаловедении вязкость разрушения описывает способность материала, содержащего трещину, сопротивляться разрушению и является одним из наиболее важных свойств любой системы материалов для многих приложений проектирования.Существует два альтернативных подхода к анализу разрушения: энергетический критерий и подход интенсивности напряжений [8]. Согласно энергетическому подходу, для хрупких материалов трещина распространяется, когда доступная энергия превышает энергию, необходимую для создания двух новых поверхностей разрушения. Для пластичных материалов также следует учитывать другие типы рассеивания энергии (например, пластическую деформацию) в общем энергетическом балансе, чтобы правильно отслеживать возникновение и рост трещины. Рисунок 3.Сквозная трещина в бесконечной пластине, подверженной удаленному растягивающему напряжению. На практике «бесконечность» означает, что ширина пластины >> 2a [8]. , где E — модуль Юнга, σ — дистанционно приложенное напряжение, а a — длина полутрещины. Поскольку, G = G C , когда трещина начинает распространяться, соотношение между напряжением и размером трещины для разрушения может быть выражено как: Рассматривая упругий материал, каждая составляющая напряжения элемента единицу около вершины трещины можно записать, как показано на рисунке 4. Рисунок 4.Напряжения у вершины трещины в упругом материале [8]. Отказ происходит, когда K I = K IC . В этом случае K I является движущей силой разрушения, а K IC является мерой сопротивления материала. Сравнение Ур. (1) и (3) приводят к соотношению между K I и G : Это же соотношение, очевидно, справедливо для G C и K IC . Таким образом, энергетический и напряженно-интенсивный подходы к механике разрушения практически эквивалентны для линейно-упругих материалов [8].Как указывалось ранее, эпоксидные смолы являются хрупкими по своей природе, и для повышения вязкости когезионного разрушения обычно добавляют вторую нано- / микрофазу. Поведение при разрушении упрочненных полимеров может включать несколько механизмов, каждый из которых вносит свой вклад в общую вязкость разрушения материала [9]. Целью данной главы является описание различных механизмов, вызывающих упрочнение разрушения эпоксидного клея, с особым вниманием к корреляции между морфологией поверхности разрушения и механизмами упрочнения разрушения. 2. Эпоксидные смолы и виды разрушения Эпоксидная группа, когда химически связана с другими молекулами, образует большую трехмерную сеть. Процесс, посредством которого достигается химическое связывание, называется отверждением, когда жидкая смола переходит в твердую форму. Среди отвердителей для отверждения эпоксидных смол используются различные амины [10], ангидриды [11] и кислоты Льюиса [12].Свойства полученных эпоксидных смол (рис. 5) зависят от эпоксидной смолы, отвердителя и процесса отверждения. Например, когда отвердители, такие как ароматические амины [13], ангидриды кислот [14] и BF 3 MEA [15], используются с соответствующими эпоксидными смолами и полностью отверждены, эпоксидные смолы достигают высокой температуры стеклования ( T г ) и поэтому подходят для высокотемпературных применений. Рисунок 5.Химическая структура DGEBA, эпоксидной смолы [16]. Процесс отверждения эпоксидной смолы приводит к образованию сети, состоящей из молекул эпоксидной смолы, сшитых с реактивными группами отвердителя, в соответствии с химической стехиометрией соединения. Механические свойства отвержденной смолы строго зависят от уровня сшивки, достигаемого на стадии обработки; Фактически, более низкая плотность поперечных связей будет снижать температуру стеклования и модуль накопления, улучшая вязкость разрушения, обеспечивая большее удлинение до разрушения.В случае полностью сшитой системы более высокая сложность сформированной сетевой структуры приведет к увеличению T g с уменьшением максимальной деформации, допустимой до разрушения. Тема улучшения механических свойств полимеров путем добавления наполнителей второй фазы привлекала большое внимание в научном и промышленном сообществе на протяжении последних нескольких десятилетий [16]. Резина и неорганические частицы — два основных класса наполнителей, используемых для увеличения вязкости разрушения эпоксидных смол.На протяжении десятилетий, начиная с этих двух классов, были разработаны новые типологии наполнителей, и совсем недавно наномодификация стала подходящим инструментом для оптимизации свойств полимеров за счет проектирования их структуры в наномасштабе. Это привело к значительному улучшению механических свойств полимеров, особенно с точки зрения жесткости, прочности и ударной вязкости [17, 18]. Поведение при разрушении упрочненных полимеров может включать несколько механизмов, каждый из которых вносит свой вклад в общую вязкость разрушения материала.Такие возможные механизмы схематически изображены на рисунках 6 и 7 и заключаются в следующем: (1) образование полосы сдвига, (2) разрушение резиновых частиц, (3) растяжение, (4) расслоение и (5) разрыв резиновых частиц, (6) межчастичное разрушение, (7) расслоение твердых частиц, (8) отклонение трещины твердыми частицами, (9) кавитационные или пустые частицы резины, (10) образование трещин, (11) пластическая деформация кончика трещин, (12) диффузный сдвиг уступая, (13) взаимодействие полосы сдвига / крейза и (14) закрепление фронта трещины (рис. 6).6 ) внутричастичное разрушение, (7) разрушение твердых частиц, (8) отклонение трещины твердыми частицами, (9) кавитированные частицы резины, (10) образование трещин, (11) пластическая деформация вершины крейза, (12) податливость при диффузном сдвиге и ( 13) взаимодействие полосы сдвига и крейза [19]. Рисунок 7.Механизм фиксации трещин.Фронт искривленной трещины находится на грани отрыва от закрепления [19]. Механизмы рассеивания энергии могут происходить в упрочненном полимере одновременно, в зависимости от природы частиц и матрицы. Моделирование поглощенной энергии, связанной с каждым механизмом, представляет собой важный вопрос как при проектировании, так и на этапе проверки. Основные взаимосвязи, описанные в современной литературе, представлены ниже. 2.1. Механизмы резиновых частиц: растяжение, разрыв и отслаиваниеKunz-Douglass et al.[20] разработали упрощенную модель для оценки рассеяния энергии (Δ G IC ), связанной с растяжением, разрывом и отслаиванием резиновых частиц. Согласно этому подходу, частицы каучука накапливают упругую энергию, равную Δ G IC , которая необратимо рассеивается (например, в виде тепла), когда частица разрушается либо в результате отсоединения от матрицы, либо в результате разрыва, и по: ΔGIC = 4γVp [1 — 6 (λ2 + λ + 4)] E5, где γ — это либо удельная энергия границы раздела фаз, необходимая для отслаивания резины, либо энергия разрыва резины, объемная доля частиц каучука, а λ — это либо степень удлинения во время разрыва сцепления, либо разрыва резины. 2.2. Трансчастичное излом экватор частицы и σ f — напряжение разрушения. Учитывая, что количество частиц N со средним радиусом r на единицу площади поверхности составляет: | |||||||||||||||||||||||||||||||||||||||||||||||||||||||||||||||||||||||||||||||||||||||||||||||||||||||||||||||||||||||||||||||||||||||||||||||||||||||||||||||||||||||||||||||||||||||||||||||||||||||||||||||||||||
Объемная доля, V p (%) | Средний размер частиц, d (мкм) | K IC 1 МПа МПа 2 ) | E (ГПа) | σ y (МПа) | |||||||||||||||||||||||||||||||||||||||||||||||||||||||||||||||||||||||||||||||||||||||||||||||||||||||||||||||||||||||||||||||||||||||||||||||||||||||||||||||||||||||||||||||||||||||||||||||||||||||||||||||||
---|---|---|---|---|---|---|---|---|---|---|---|---|---|---|---|---|---|---|---|---|---|---|---|---|---|---|---|---|---|---|---|---|---|---|---|---|---|---|---|---|---|---|---|---|---|---|---|---|---|---|---|---|---|---|---|---|---|---|---|---|---|---|---|---|---|---|---|---|---|---|---|---|---|---|---|---|---|---|---|---|---|---|---|---|---|---|---|---|---|---|---|---|---|---|---|---|---|---|---|---|---|---|---|---|---|---|---|---|---|---|---|---|---|---|---|---|---|---|---|---|---|---|---|---|---|---|---|---|---|---|---|---|---|---|---|---|---|---|---|---|---|---|---|---|---|---|---|---|---|---|---|---|---|---|---|---|---|---|---|---|---|---|---|---|---|---|---|---|---|---|---|---|---|---|---|---|---|---|---|---|---|---|---|---|---|---|---|---|---|---|---|---|---|---|---|---|---|---|---|---|---|---|---|---|---|---|---|---|---|---|---|---|---|
40 | 300 | 1.76 | — | — | |||||||||||||||||||||||||||||||||||||||||||||||||||||||||||||||||||||||||||||||||||||||||||||||||||||||||||||||||||||||||||||||||||||||||||||||||||||||||||||||||||||||||||||||||||||||||||||||||||||||||||||||||
160 | 1,74 | — | — | ||||||||||||||||||||||||||||||||||||||||||||||||||||||||||||||||||||||||||||||||||||||||||||||||||||||||||||||||||||||||||||||||||||||||||||||||||||||||||||||||||||||||||||||||||||||||||||||||||||||||||||||||||
100 | 1,87 | — | —
Таблица 1.Эпоксидно-кремнеземный композит с различным содержанием наполнителя и обработкой поверхности [19]. Рисунок 14.Модуль упругости при растяжении в зависимости от содержания стеклянных шариков для различных композиций эпоксидной смолы и CTBN [44]. Простой и эффективный способ улучшить энергию разрушения без потери прочности и модуля упругости — это включение неорганических наполнителей в эпоксидные смолы, упрочненные резиной. Как показано на Фигуре 14, присутствие каучука CTBN снижает механические свойства (модуль упругости при растяжении, E ), но добавление небольшого количества неорганического наполнителя восстанавливает модуль до исходного значения.Значение G IC для гибридной стеклянной эпоксидной смолы, модифицированной каучуком, намного больше, чем для немодифицированной стеклом эпоксидной смолы для данной температуры и объемной доли стекла [49]. Хорошо известно, что присутствие жестких (микро) наполнителей может вызвать несколько механизмов упрочнения эпоксидных матриц, например (1) деформацию трещин [21, 50], (2) пластическую деформацию [26, 51] и 3) передняя закрепка трещины [36, 52]. Первый механизм присутствует всегда, но вносит минимальный вклад в общее повышение вязкости разрушения в эпоксидных смолах с наполнителем из частиц.Подобно эпоксидным смолам с резиновым наполнителем, присутствие неорганических частиц вызывает трехосное напряжение в матрице вокруг нее, способствуя пластической деформации полимерной фазы и затем затуплению вершины трещины. Однако основным источником упрочнения эпоксидных смол с наполнителем из частиц является закрепление трещин. Это утверждение подтверждается работой Moloney et al. [26], в которой изучалось влияние частиц оксида алюминия и кремнезема на вязкость разрушения наполненной эпоксидной смолы. Примечательно, что в случае частиц слабого наполнителя, такого как гидроксид алюминия и доломит [26], закрепление трещин не может полностью объяснить упрочнение разрушения, фактически до определенного содержания наполнителя закрепление трещин применимо, но при более критическом содержании ( ~ 20%) трещина имеет тенденцию распространяться через частицы, способствуя механизму межчастичного разрушения. Как сообщает Kinloch et al. [36], которые исследовали гибридную систему, состоящую из стеклянных шариков и резиновых частиц в эпоксидной матрице, закрепление трещин является основным механизмом вязкости разрушения в системах, работающих при низких температурах. Разрушение можно описать критерием критического смещения раскрытия трещины. При более высоких температурах механизм закрепления трещины затмевается крупными процессами пластического течения в вершине трещины. Рис. 15.Поверхности излома для (а) диоксида циркония-эпоксидной смолы с «хвостами» закрепления трещин (белые стрелки) и (б) диоксида циркония-каучука-эпоксидной смолы, показывающие зарождение и остановку трещин в области, побеленной напряжением [53]. Возникновение закрепления трещин в эпоксидной смоле из диоксида циркония и эпоксидной смолы из диоксида циркония и каучука также было подтверждено в работе Low et al. [52], согласно которой закрепление трещин является основным механизмом упрочнения разрушения в эпоксидной системе на основе диоксида циркония, в то время как в гибридной смоле имеются свидетельства кавитации и сдвигового потока около вершины трещины. На закрепление трещин ясно указывает наличие характерных хвостов (белые стрелки), как показано на Рисунке 15. На Рисунке 15 (b) показана поверхность разрушения гибридной системы, которая очевидна по наличию многих мест зарождения и остановки трещины, с последующее заметное увеличение вязкости разрушения (частицы резины отслаиваются / разрываются в соответствии с каждым участком инициирования, повышая рассеиваемую энергию). Максвелл и др. [53] разработали гибридный стеклонаполненный эпоксидный полимер, содержащий как резиноподобные, так и жесткие частицы. Значения G IC для немодифицированных и модифицированных каучуком эпоксидных материалов в зависимости от объемной доли стеклянных частиц показаны на рисунке 16. Интересно отметить, что в системах без стеклянного шарика ( V f = 0) значение G IC непрерывно увеличивается с температурой, и, в частности, в системе, модифицированной каучуком, это повышение составляет примерно порядок величины.При более высоком содержании стеклянных шариков G IC выравнивается до определенного значения, а затем уменьшается; этот эффект более очевиден для гибридной системы. Оптимальное значение содержания наполнителя для системы стекло-эпоксидная смола составляет около 0,3 с увеличением G IC примерно на 400%. И наоборот, в гибридной системе оптимальное значение зависит от температуры. Рис. 16.Энергия разрушения, GIC, по отношению к объемной доле, Vf, стеклянных частиц для (а) немодифицированной эпоксидной смолы и (б) эпоксидной смолы, модифицированной каучуком [49]. Наблюдение с помощью сканирующего электронного микроскопа может помочь понять механизмы разрушения эпоксидного клея с наполнителем. Типичная микрофотография смолы, наполненной стеклянными частицами, показана на рис. 17 (а), на котором четко видны хвосты за частицами, обычно связанными с механизмом закрепления трещин. Эти хвосты связаны с бифуркацией фронта трещины, когда он встречается с положением закрепления (т. Е. С жесткой частицей), и с последующей встречей снова двух новых фронтов трещины.Рисунок 17 (b) показывает микрофотографию гибридной системы стекло / резина. Интересно отметить наличие множества маленьких отверстий, больших, чем частицы резины, и очень шероховатой поверхности из-за массивного сдвигового потока во время распространения трещины. Наличие нескольких маленьких хвостов за частицами стекла указывает на небольшой вклад закрепления трещины в глобальный механизм упрочнения разрушения. Тем не менее, наличие нескольких характерных хвостов трещин в гибридной системе было предсказуемо, учитывая кривую G IC в зависимости от содержания стеклянных шариков, фактически увеличение G IC содержание неорганического наполнителя очень велико (400%) в системе без резины, но минимально (~ 40%) в системе с упрочненной резиной. Рис. 17.Сканирующие электронные микрофотографии поверхностей излома. (а) Немодифицированная эпоксидная смола, наполненная стеклянными частицами (стрелка указывает направление роста трещины). (б) Гибридный эпоксидный полимер с наполнителем из частиц [19]. 3.3. Эпоксидные смолы, модифицированные термопластомЧастицы термопласта могут использоваться в качестве упрочняющего агента в хрупких эпоксидных смолах, поскольку они способствуют делокализованному микротрещинам и перекрытию трещин [54]. Эта типология частиц широко используется, чтобы избежать снижения модуля матрицы-хозяина. Рис. 18.Схематическая диаграмма механизмов упрочнения, предлагаемых для термопластически модифицированных эпоксидных смол: (1) закрепление трещин, (2) перекрытие частиц, (3) отклонение пути трещины, (4) выход частиц, (5) образование частиц индуцированная полосатость сдвига и (6) микротрещины [57]. Эпоксиды, модифицированные термопластом, упрочняются с помощью механизма, называемого перекрытием трещин (рис. 18) [55, 56]. Увеличение K IC , наблюдаемое в этой упрочненной смоле, связано с эффектом твердых пластиковых частиц, которые перекрывают две поверхности трещины, ограничивая раскрытие вершины трещины.Перекрытие трещин можно также объяснить, учитывая, что энергия рассеивается во время пластической деформации и последующего разрыва пластиковых частиц. Влияние перекрытия трещин на морфологию поверхностей излома легко заметить; Как правило, поверхность разрушенных частиц кажется богатой, деформированной после большой пластической деформации. Микроскопическое свидетельство перекрытия трещин можно увидеть на Рисунке 19, на котором показаны сильно вытянутые частицы полиамида-12 [58] в технологической зоне перед прекрещеной.Видно, что частицы хорошо прилипают к матрице и способны к большим пластическим деформациям перед разрушением. Из больших деформаций также очевидно, что частицы разрушились после того, как трещина прошла через матрицу. Рис. 19.SEM-микрофотография, показывающая деформированные частицы полиамида-12 на поверхности излома эпоксидной смолы, модифицированной полиамидом-12, изнутри технологической зоны (стрелка указывает направление распространения трещины) [54]. Во многих работах [57, 59] также упоминается закрепление трещин как один из механизмов, способствующих усилению разрушения термопластических частиц.Эти частицы ведут себя как непроницаемые объекты, подобно ранее упомянутому неорганическому наполнителю в виде частиц. Действительно, более высокая хрупкость эпоксидной матрицы по сравнению с пластичной термопластичной фазой позволяет рассматривать эти частицы как относительно непроницаемые. Отклонение пути трещины [58] — еще один упоминаемый механизм, ответственный за упрочнение эпоксидных смол с наполнителем из термопластических частиц. Как описано ранее, в этом механизме частицы вызывают отклонение фронта трещины от исходного пути, увеличивая площадь поверхности трещины и, следовательно, рассеивая энергию.Возникновение этого механизма упрочнения можно проверить, наблюдая за поверхностями излома с помощью SEM. Рис. 20.Вязкость разрушения увеличивается с увеличением содержания PPO, в то время как предел текучести остается постоянным [54]. Частицы термопласта также вызывают образование полос сдвига в матрице, как частицы резины. Фактически, во время образования жестких частиц их модуль уменьшается до модуля упругости каучука, и это несоответствие модуля между матрицей и полученными частицами вызывает значительную концентрацию напряжений, вызывая образование полос сдвига в окружающей матрице.Пирсон и др. [54] модифицировали эпоксидную смолу на основе диглицидилового эфира бисфенола A (DGEBA) поли (фениленоксидом) (PPO). Вязкость разрушения эпоксидных смол, модифицированных PPO, увеличивается почти линейно с увеличением содержания PPO. Эти результаты представлены графически на Фигуре 20. Простая линейная зависимость между содержанием PPO и вязкостью разрушения удивительна, поскольку морфология претерпевает резкие изменения от морфологии частиц к морфологии, состоящей из непрерывных доменов. Пирсон и др.заявил, что механизм упрочнения — это не массивные полосы сдвига, которые были обнаружены для эпоксидных смол, модифицированных каучуком; вместо этого эпоксидные смолы, модифицированные PPO, упрочняются за счет механизма микротрещин и разветвлений (рис. 21). Рис. 21.(a) Микротрещины и (b) Механизм разветвления в вершине трещины [54]. По данным Hodgkin et al. [60], критерии для достижения хорошей термопластической ударной прочности могут быть перечислены следующим образом:
3.4. Слоистые эпоксидные смолы, модифицированные нанонаполнителемОдин из наиболее перспективных подходов к синтезу материалов с барьерными свойствами [61, 62], огнестойкостью [44] и повышением механических свойств [10, 44] заключается в диспергировании неорганического глинистого минерала в органический полимер в нанометровом масштабе. Прогиб трещины, вероятно, является основным механизмом рассеивания энергии, который происходит в полимерах с наноглиной, где глиняные пластинки толщиной 1 нм часто имеют тенденцию укладываться в тактоиды микроскопических размеров, легко способные возмущать фронт растущей трещины.Более того, также расслоение наноглины (часто рассматриваемое как расслоение наноглины) и образование полос сдвига матрицы вносят вклад в общее улучшение вязкости разрушения [62]. Рис. 22.Критическая скорость высвобождения энергии деформации, GIC, в зависимости от содержания сепиолита [10]. Доказательства упомянутых механизмов можно увидеть в работе Zotti et al. [10]. В этой работе добавление сепиолитовой глины вызывает увеличение скорости выделения энергии деформации до 30% (Рисунок 22). Эти авторы указали, что частицы сепиолитовой глины могут действовать как места концентрации напряжений, способствуя расслоению глины и матрицы (оранжевая стрелка), что приводит к образованию микро- и нанопастбищ и сдвигу матрицы в областях, близких к вершине трещины (Рисунок 23).Высокая шероховатость поверхности излома свидетельствует о наличии механизма прогиба трещины. Рис. 23.Поверхность излома сепиолита / эпоксидной смолы; (слева) высокое и (справа) малое увеличение [10]. К группе слоистых нанонаполнителей относятся графен и его производные. Этот инновационный материал состоит из одного листа гибридизированных атомов углерода sp 2 и поэтому имеет сотовую структуру. Эта двумерная структура демонстрирует отличную тепло- и электропроводность, как у углеродных нанотрубок (УНТ).Графен также разделяет с УНТ очень высокий модуль упругости [55, 63]. Подобно глинам, графен имеет слоистую структуру, но обладает более высокими механическими свойствами благодаря углеродной основе. Графен способен значительно повысить вязкость разрушения эпоксидной смолы даже с низким содержанием: на самом деле, в работе Raffiee et al. [56] сообщалось о 65% приросте вязкости разрушения для 0,125 мас.% Количества наполнителя. Анализ поверхности разрушения показывает удвоенную площадь поверхности для системы графен / эпоксидная смола по сравнению с чистой эпоксидной смолой.Такое сильное увеличение площади поверхности разрушения указывает на механизм прогиба трещины. Однако вклад этого механизма в вязкость разрушения снижает увеличение содержания наполнителя. Чандрасекаран и др. [64] сообщают о подобных наблюдениях в своей работе, где нанопластинки графита (ЗНЧ) и термически восстановленный оксид графена (TRGO) были диспергированы в эпоксидной матрице. Изломанная поверхность нанокомпозита графен / эпоксидная смола, наблюдаемая с помощью SEM, показывает более высокую шероховатость, чем чистая эпоксидная смола, как показано на Рисунке 24.Это еще раз указывает на то, что прогиб трещин является одним из механизмов упрочнения этих нанокомпозитов. Разница между двумя типами графеновых GNP и TRGO заключается в том, что TRGO образуется путем химического расслоения и, следовательно, содержит некоторые остаточные оксидные функциональные возможности и меньшее количество слоев. Эти факторы улучшают дисперсию графена в эпоксидной матрице по сравнению с системой GNP / эпоксидная смола. Фактически, ЗНЧ получают интеркалированием металла графита и имеют меньшую оксидную функциональность и большее количество слоев по сравнению с TRGO.Лучшая дисперсия объясняет более высокую шероховатость поверхности композита TRGO / эпоксидная смола по сравнению с GNP / эпоксидной смолой (Рисунок 24). Рис. 24.Увеличение шероховатости поверхности излома (b и c) графен / эпоксидный нанокомпозит по сравнению с (a) чистой эпоксидной смолой (белая пунктирная стрелка указывает направление распространения трещины) [65]. Двумерная схема бифуркации и распространения трещины на разной высоте, показывающая взаимодействие фронта трещины с частицей TRGO / GNP, показана на рисунке 25.Во время взаимодействия между распространяющимся фронтом трещины и графеновой нанопластинкой могут произойти две возможные ситуации: (1) фронт трещины отклоняется, принимая извилистый путь, или (2) фронт трещины раздваивается вокруг пластинки (рис. 25a и b) [ 65]. Рис. 25.Схема взаимодействия фронта трещины с частицами GNP / TRGO (белая пунктирная стрелка указывает направление распространения трещины): (a) бифуркация / закрепление трещины, (b) распространение трещины на разной высоте, (c) разделение слоев и (г) проникновение трещины со слоями — ямчатая поверхность излома [64, 65]. На рисунке 26 представлена поверхность излома обеих сторон (для простоты сравнения сторона B была наклонена электронным способом на 180 °) образца. Особенность, которая наблюдалась на поверхностях излома, заключается в том, что есть места, где нет структуры потока, как указано сплошными стрелками на Рисунке 26. Этот факт указывает на то, что эта грань является не поверхностью излома эпоксидной смолы, а поверхностью TRGO. / ВНП частица. В этом случае трещина проходит по поверхности раздела TRGO или GNP / эпоксидная смола.Этот механизм разрушения возникает, когда трещина встречается с краями графеновых листов. Трещина продолжает распространяться между листами графена и, наконец, проходит через разделение слоев. Поскольку сила между листами является вторичной (Ван-дер-Ваальс), разделение листов облегчается за счет легкого распространения трещин (рисунок 25c). Рис. 26.Сканирующая электронная микрофотография обеих сторон поверхности разрушения для 0,1 мас.% TRGO / эпоксидной смолы (a) Сторона A и (b) Сторона B, демонстрирующая разделение между слоями графена, которые ориентированы параллельно и перпендикулярно распространяющаяся трещина [64, 65]. Комбинация изгиба трещины и разделения между слоями графена — еще один механизм, который может происходить в эпоксидных смолах, упрочненных графеном (рис. 24d). Когда фронт трещины отклоняется графеновой пластинкой, она огибает частицу, пока не встретится с краями графена. В некоторых случаях фронт трещины может проходить между листами графена, создавая характерную поверхность излома типа «лунки» [65]. При увеличении содержания графена шероховатость поверхности заметно увеличивается, как показано на рисунке 27.Интересно отметить, что при более низком содержании наполнителя (рис. 25а), бифуркация и вырывание являются основными механизмами разрушения. При увеличении процентного содержания наполнителя, закрепление и прогиб трещин стали преобладающими видами разрушения (рис. 25b и c). Наконец, более высокое содержание наполнителя способствует разделению между листами графена, уменьшая шероховатость поверхности и, следовательно, значение K IC (рисунок 25d). Рис. 27.Вязкость разрушения как функция от массового процента наполнителя и соответствующие микрофотографии поверхности разрушения GNP / эпоксидной смолы, полученные на сканирующем электронном микроскопе: (a) 0.1 мас.%; (б) 0,5 мас.%; (в) 1.0 мас.% и (г) 2.0 мас.% [65]. 3.5. Сверхразветвленные модифицированные эпоксидыСверхразветвленные полимеры характеризуются различными свойствами, которые стимулируют их использование в качестве упрочняющего агента в эпоксидных смолах, такими как низкая вязкость расплава и раствора, большое количество функциональных групп в периферийной области и малые размеры по сравнению с полимером той же молекулярной вес [66, 67]. Сверхразветвленные полимеры также были исследованы как новые, обладающие высоким потенциалом и низкой вязкостью упрочнители эпоксидных смол, которые повышают характеристики вязкости разрушения без вредного воздействия на другие свойства [68]. Наблюдения поверхности трещины с помощью СЭМ, выполненные Fu et al. [69], показали кавитацию в центре и явление текучести волокон на краях, что указывает на то, что кавитация частиц, деформация текучести сдвига и механизм прочности in situ и являются основными механизмами упрочнения. В этой работе Fu et al. синтезировали низковязкую жидкую термореактивную ароматическую полиэфирную сверхразветвленную эпоксидную смолу с концевыми эпоксидными группами (названную HTTE) для модификации эпоксидных смол DGEBA.СЭМ плоскости XY (центральная область образца — рис. 28а) показывает структуры «морского острова», «ямочки» и макроскопически побеленные от напряжения зоны, окружающие трещину, которые обычно являются характеристиками трещины. модифицированные каучуком эпоксидные смолы и называются «ямочками для повышения прочности». Резиновые кавитационные частицы HBP образуют пустоты, которые рассеивают свет и вызывают явление побеления под напряжением. Как сообщалось ранее, кавитация является важным источником рассеивания энергии в эпоксидных смолах, упрочненных резиной, поскольку кавитация поглощает энергию, вызывающую сдвиг, уступающий в окружающей матрице (последний механизм предпочтителен при высоком содержании наполнителя, когда окружение частиц может эффективно взаимодействовать с ним). из остальных). Рис. 28.СЭМ-микрофотографии поверхности излома в плоскостях (а) XY и (б) YZ смесей HTTE / эпоксидной смолы [69]. На рис. 28 (б) представлена микрофотография, полученная с помощью сканирующего электронного микроскопа, относительно плоскости YZ (область, где рост трещины прекратился). На этой микрофотографии очевидна пластическая текучесть и связанная с ней фибрилляция, что указывает на переход между хрупким и пластичным состояниями. Этот переход согласуется с большим увеличением ударной вязкости.Механизм образования фибрилл, вероятно, состоит из следующего: (1) пустоты, возникающие в результате разрыва связи между частицами HBP и матрицей, вызывают образование крейзов; (2) после возникновения трещин и пустот эпоксидная матрица удлиняется под действием высокого напряжения растяжения в области вершины трещины, образуя характерные фибриллы. Также Варлей и др. [70] продемонстрировали, что механизм упрочнения, действующий в системе HBP / эпоксидная смола, основан на процессе кавитации частиц. На рисунке 29 (а) показано существенное улучшение вязкости разрушения (в единицах K IC ) при увеличении добавления HBP. Рис. 29.(a) Повышение вязкости разрушения образцов отвержденной смолы как функция увеличения содержания HBP и (b) SEM системы 20% HBP / эпоксид [70]. Примечательно, что этот результат был получен при некотором уменьшении как T g , так и свойств изгиба. Такое поведение можно объяснить с точки зрения морфологии с разделением фаз, очевидной из снимков, сделанных с помощью сканирующего электронного микроскопа (рис. 29b). Размер частиц HBP (∼1–5 мкм) порядка, подходящего для создания механизмов упрочнения, таких как кавитация частиц.Интересно, что при более высоких уровнях концентрации HBP эпоксидная матрица демонстрирует значительные доказательства пластичного течения в непрерывной эпоксидной сети. Ненасыщенная полиэфирная смола для специального применения1.1.1. Насыщенная полиэфирная смола [9]Это продукты реакции двухосновных кислот или хлоридов двухосновных кислот с диолами и широко используются в текстильной промышленности, например Полиэтилентерефталат. Алкиды — это продукты реакции многоатомных спиртов с жирными кислотами с последующей реакцией с двухосновными кислотами.Они широко используются в лакокрасочной и полиграфической промышленности [10-14]. 1.1.3. Смола на основе сложного винилового эфира [4]Смолы на основе сложного винилового эфира приобретают все большее значение в новых промышленных применениях, таких как покрытия, печатные платы, ламинаты из металлической фольги, строительные материалы, автомобильные детали, жесткие пенопласты и армированные волокном композиты [15-19]. Обычная смола на основе сложного винилового эфира может быть получена путем блокирования концов различных эпоксидных смол ненасыщенной монокарбоновой кислотой [20-22].Они сочетают в себе превосходную механическую, химическую стойкость и устойчивость к растворителям эпоксидных смол со свойствами ненасыщенных полиэфирных смол. Отвержденная смола на основе сложного винилового эфира имеет физические свойства, превосходящие отвержденную обычную смолу на основе сложного полиэфира, в частности устойчивость к коррозии. Смолы на основе сложных виниловых эфиров были разработаны в конце 1950-х — начале 1960-х годов, то есть сразу после II -го года и -й мировой войны. Смолы получали взаимодействием глицидилакрилата и глицидилметакрилата с бисфенолом-A.Эти смолы очень реактивны и имеют очень короткий срок службы. Общая структура сложного винилового эфира, полученного реакцией эпоксидной смолы с акриловой кислотой, показана ниже. 1.1.4. Ненасыщенные полиэфирные смолыНенасыщенные полиэфирные смолы представляют собой продукты конденсации ненасыщенных кислот или ангидридов и диолов с дикислотами или без них. Ненасыщенность, присутствующая в этом типе сложных полиэфиров, обеспечивает сайт для последующего сшивания [23-24]. С 1930 года ненасыщенные полиэфирные смолы широко используются в широком диапазоне применений, что делает их очень важной термореактивной системой [25-26].Эти смолы смешиваются с различными наполнителями, армирующими добавками и отверждаются с использованием свободнорадикальных инициаторов для получения термореактивных изделий, имеющих широкий диапазон химических и механических свойств в зависимости от выбора двухосновных кислот, диолов, сшивающих агентов, инициаторов и других добавок [27]. . Эта универсальность свойств конечного термореактивного продукта, связанная со сравнительно низкой стоимостью, возродила интерес к этим смолам как к важному матричному материалу для широкого спектра применений.В 1929 году Арвин и Каротерс [28] разработали ненасыщенные полиэфирные смолы из малеиновой кислоты и этиленгликоля, прореагировавшего при температуре 175 0 -185 0 C. Ford Motor Co. Ltd. [29] синтезировали ненасыщенную полиэфирную смолу путем взаимодействия малеинового ангидрида и фталевого ангидрида с пропиленгликолем при 100 0 ° C, а затем при 250 0 ° C до тех пор, пока кислотное число не уменьшится до значения менее 50 (мг КОН на грамм образца). Коррадо и его помощники [30] синтезировали ненасыщенные полиэфирные смолы с низкой вязкостью путем взаимодействия малеинового ангидрида, фталевого ангидрида и дипропиленгликоля при 200 0 ° C.Ochsenbein и Olliver [31] синтезировали стабильную при хранении ненасыщенную полиэфирную смолу путем взаимодействия малеинового ангидрида, пропиленгликоля и дипропиленгликоля при 185 0 ° C в инертной атмосфере. Ненасыщенные полиэфирные смолы общего назначения получали с использованием малеинового ангидрида, фталевого ангидрида и пропиленгликоля с молярным соотношением фталевый ангидрид: малеиновый ангидрид в диапазоне от 1: 2 до 2: 1 [32-33]. Для термореактивных продуктов полученную смолу смешивали со стиролом для сшивки и небольшим количеством пероксида в качестве инициатора.Эти типы смол используются для изготовления поддонов, душевых кабин, лодок, бассейнов, резервуаров для воды и т. Д. Смола на основе модифицированного акрилом ненасыщенного полиэфира, обладающая хорошей стойкостью к растрескиванию, гибкостью и тиксотропными свойствами, была синтезирована с использованием 65 частей 0,15: 1,0: 0,3: 0,7 молярное соотношение дициклопентадиен: фумаровая кислота: сополимер этиленгликоль: диэтиленгликоль и 35 частей 2-гидроксиэтилметакрилата [34]. Химически стойкие термореактивные ненасыщенные полиэфирные смолы для ламинатов с низким содержанием летучих органических компонентов получали из изофталевой кислоты, малеинового ангидрида и пропиленгликоля с 35% стирола в качестве реактивных разбавителей [35].Ненасыщенную полиэфирную смолу, полученную из изофталевой кислоты, малеинового ангидрида и неопентилгликоля, смешивали с дициклопентадиеновой смолой и стиролом, чтобы получить диэлектрическую смесь для электрических машин [36]. Влияние содержания стирола на неэкспоненциальное и неаррениусовское поведение α-релаксации отвержденной ненасыщенной полиэфирной смолы исследовали с помощью динамического механического анализа [37]. Обзор последних исследований в области методов модификации ненасыщенной полиэфирной смолы с акцентом на упрочнение и усиление, огнестойкость, повышение термостойкости и устойчивости к окружающей среде, снижение процента усадки отвержденной ненасыщенной полиэфирной смолы и свойств сушки на воздухе. сделано Q.Jun-min et. al. [38]. Результаты исследований ненасыщенных полиэфирных смол в течение 2000-2001 гг. Были рассмотрены со ссылками [39]. Обзор тенденций развития производства ненасыщенных полиэфирных смол был сделан Пенезеком [40]. Обзор литературы показывает, что имеется много сообщений о методах синтеза и модификации ненасыщенных полиэфирных смол [41-49]. Свойства и характеристики эпоксидных смол —Когда два или более объекта должны прилегать друг к другу в течение длительного времени, лучший способ добиться этого — использовать эпоксидную смолу.В комплект поставки входят два шприца, содержащие компоненты, которые вместе реагируют, образуя прочную и долговечную связь. Благодаря характеристикам, которыми обладает эпоксидная смола, предприятия и частные лица используют эпоксидную смолу для широкого спектра применений. Наборы для нанесения эпоксидной смолыимеют длительный срок хранения. Вновь открытые шприцы с эпоксидной смолой после многих лет забвения оказались такими же эффективными, как и эпоксидная смола, купленная в день применения. Свойства эпоксидной смолыОсновная причина популярности эпоксидной смолы — ее превосходная механическая прочность.Часто единственной альтернативой является сварка. Эпоксидная смола почти всегда дешевле и быстрее сварки. Эпоксидная смола также обладает отличной стойкостью к химическим веществам. После схватывания можно не беспокоиться о химической реакции, которая ослабит уплотнение. Он также устойчив к жаре. Такое сопротивление делает его идеальным для электроники, электрических систем и других промышленных приложений. Те, кто использует эпоксидную смолу, знают о превосходной механической прочности и низком усадке при отверждении. Они также знают, что эпоксидные смолы — это хорошо сбалансированные промышленные материалы, которые подходят для широкого спектра применений. Инженерысталкиваются с проблемами рассеивания тепла, электрической изоляции, приклеивания разнородных оснований, легкости, шумопоглощения, вибрации и уменьшения коррозии. Следует учитывать не только внешний вид, но и стоимость сборки. Эпоксидная смола — это клеевой состав, отвечающий всем этим требованиям. Эпоксидная смола известна своими тепловыми и электрическими свойствами, прочностью и долговечностью. Эти свойства наряду с устойчивостью к погружению и агрессивным химическим парам являются причиной, по которой инженеры часто выбирают эпоксидную смолу. Рабочие характеристикиЭксплуатационные характеристики эпоксидной смолы:
Обладает отличными свойствами заполнения зазоров. Эпоксидная смола устойчива к холоду, радиации и пару. Превосходные характеристики эпоксидной смолы сохраняются при воздействии неблагоприятных условий окружающей среды. Почему следует использовать двухкомпонентную эпоксидную смолуПреимущества двухкомпонентной эпоксидной смолы перевешивают недостатки.Двухкомпонентные эпоксидные смолы легко отверждаются при комнатной температуре. Они не требуют никакого тепла. Однокомпонентная эпоксидная смола требует тепла. Двухкомпонентная эпоксидная смола обеспечивает отличную химическую стойкость. Недостатками двухкомпонентной эпоксидной смолы является раздражение рук при контакте с веществами, а также необходимость измерения и смешивания двух веществ. |