ΠΠ΅Ρ Π°Π½ΠΈΠ·ΠΌ Ρ ΠΈΠΌΠΈΡΠ΅ΡΠΊΠΎΠ³ΠΎ Π½ΠΈΠΊΠ΅Π»ΠΈΡΠΎΠ²Π°Π½ΠΈΡ ΡΠΏΠ»Π°Π²ΠΎΠΌ Π½ΠΈΠΊΠ΅Π»Ρ-ΡΠΎΡΡΠΎΡ
ΠΠ»Π°Π²Π½Π°Ρ β ΠΠ΅Ρ Π°Π½ΠΈΠ·ΠΌ Ρ ΠΈΠΌΠΈΡΠ΅ΡΠΊΠΎΠ³ΠΎ Π½ΠΈΠΊΠ΅Π»ΠΈΡΠΎΠ²Π°Π½ΠΈΡΒ
Β
ΠΠ°ΠΊΠ°Π·Π°ΡΡ Π₯ΠΠΠΠ§ΠΠ‘ΠΠΠ ΠΠΠΠΠΠΠ ΠΠΠΠΠΠ (ΡΠΏΠ»Π°Π² Π½ΠΈΠΊΠ΅Π»Ρ-ΡΠΎΡΡΠΎΡ) ΡΡΠ°Π»ΠΈ
ΠΠ°ΠΊΠ°Π·Π°ΡΡ Π₯ΠΠΠΠ§ΠΠ‘ΠΠΠ ΠΠΠΠΠΠΠ ΠΠΠΠΠΠ (ΡΠΏΠ»Π°Π² Π½ΠΈΠΊΠ΅Π»Ρ-ΡΠΎΡΡΠΎΡ) Π°Π»ΡΠΌΠΈΠ½ΠΈΡ
Β
1. ΠΠ±ΡΠΈΠ΅ ΡΠ²Π΅Π΄Π΅Π½ΠΈΡ ΠΎ Ρ ΠΈΠΌΠΈΡΠ΅ΡΠΊΠΎΠΌ Π½ΠΈΠΊΠ΅Π»ΠΈΡΠΎΠ²Π°Π½ΠΈΠΈ.
ΠΡΠΎΡΠ΅ΡΡ Ρ ΠΈΠΌΠΈΡΠ΅ΡΠΊΠΎΠ³ΠΎ Π½ΠΈΠΊΠ΅Π»ΠΈΡΠΎΠ²Π°Π½ΠΈΡ ΠΏΠΎΠ·Π²ΠΎΠ»ΡΠ΅Ρ ΠΎΡΠ°ΠΆΠ΄Π°ΡΡ ΠΏΠΎΠΊΡΡΡΠΈΡ ΡΠ°Π²Π½ΠΎΠΌΠ΅ΡΠ½ΠΎΠΉ ΡΠΎΠ»ΡΠΈΠ½Ρ Ρ ΠΎΡΠΊΠ»ΠΎΠ½Π΅Π½ΠΈΡΠΌΠΈ Π½Π΅ Π±ΠΎΠ»Π΅Π΅ 10% Π½Π° Π΄Π΅ΡΠ°Π»ΡΡ ΡΠ»ΠΎΠΆΠ½ΠΎΠΉ ΠΊΠΎΠ½ΡΠΈΠ³ΡΡΠ°ΡΠΈΠΈ. ΠΠΎ ΡΡΠ°Π²Π½Π΅Π½ΠΈΡ Ρ Π½ΠΈΠΊΠ΅Π»Π΅Π²ΡΠΌΠΈ ΠΏΠΎΠΊΡΡΡΠΈΡΠΌΠΈ, ΠΏΠΎΠ»ΡΡΠ΅Π½Π½ΡΠΌΠΈ Π³Π°Π»ΡΠ²Π°Π½ΠΈΡΠ΅ΡΠΊΠΈΠΌ ΡΠΏΠΎΡΠΎΠ±ΠΎΠΌ ΠΎΠ½ΠΈ ΠΎΠ±Π»Π°Π΄Π°ΡΡ Π±ΠΎΠ»Π΅Π΅ Π²ΡΡΠΎΠΊΠΎΠΉ ΡΠ²Π΅ΡΠ΄ΠΎΡΡΡΡ ΠΈ ΠΈΠ·Π½ΠΎΡΠΎΡΡΠΎΠΉΠΊΠΎΡΡΡΡ, ΠΏΠΎΡΡΠΎΠΌΡ ΠΌΠΎΠ³ΡΡ ΠΏΡΠΈΠΌΠ΅Π½ΡΡΡΡΡ Π΄Π»Ρ Π΄Π΅ΡΠ°Π»Π΅ΠΉ, ΡΠ°Π±ΠΎΡΠ°ΡΡΠΈΡ Π² ΡΡΠ»ΠΎΠ²ΠΈΡΡ ΡΡΠ΅Π½ΠΈΡ, ΠΎΡΠΎΠ±Π΅Π½Π½ΠΎ ΠΏΡΠΈ ΠΎΡΡΡΡΡΡΠ²ΠΈΠΈ ΡΠΌΠ°Π·ΠΊΠΈ.
ΠΠΎΠΊΡΡΡΠΈΡ ΠΈΠΌΠ΅ΡΡ ΠΌΠΈΠ½ΠΈΠΌΠ°Π»ΡΠ½ΡΡ ΠΏΠΎΡΠΈΡΡΠΎΡΡΡ ΠΈ Π²ΡΡΠΎΠΊΠΈΠ΅ Π΄Π΅ΠΊΠΎΡΠ°ΡΠΈΠ²Π½ΡΠ΅ ΡΠ²ΠΎΠΉΡΡΠ²Π° (ΠΎΡΠΎΠ±Π΅Π½Π½ΠΎ ΠΏΡΠΈ ΠΎΡΠ°ΠΆΠ΄Π΅Π½ΠΈΠΈ ΠΈΠ· ΡΠ²Π΅ΠΆΠ΅ΠΏΡΠΈΠ³ΠΎΡΠΎΠ²Π»Π΅Π½Π½ΠΎΠ³ΠΎ ΡΠ°ΡΡΠ²ΠΎΡΠ°), ΠΏΠΎΡΡΠΎΠΌΡ ΠΏΡΠΈΠΌΠ΅Π½ΡΡΡΡΡ Π² ΠΊΠ°ΡΠ΅ΡΡΠ²Π΅ Π·Π°ΡΠΈΡΠ½ΠΎ-Π΄Π΅ΠΊΠΎΡΠ°ΡΠΈΠ²Π½ΡΡ .
Π₯ΠΈΠΌΠΈΡΠ΅ΡΠΊΠΎΠ΅ Π½ΠΈΠΊΠ΅Π»ΠΈΡΠΎΠ²Π°Π½ΠΈΠ΅ ΠΎΠ±ΡΠ·Π°ΡΠ΅Π»ΡΠ½ΠΎ Π²ΡΠΏΠΎΠ»Π½ΡΠ΅ΡΡΡ Π² ΠΏΡΠΈΡΡΡΡΡΠ²ΠΈΠΈ ΠΎΠ΄Π½ΠΎΠ³ΠΎ ΠΈΠ· ΡΠΈΠ»ΡΠ½ΡΡ Π²ΠΎΡΡΡΠ°Π½ΠΎΠ²ΠΈΡΠ΅Π»Π΅ΠΉ. Π‘Π°ΠΌΡΠΌ ΡΠ°ΡΠΏΡΠΎΡΡΡΠ°Π½Π΅Π½Π½ΡΠΌ ΡΠ²Π»ΡΠ΅ΡΡΡ Π³ΠΈΠΏΠΎΡΠΎΡΡΠΈΡ Π½Π°ΡΡΠΈΡ. Π ΠΎΡΠ½ΠΎΠ²Π΅ ΠΏΡΠΎΡΠ΅ΡΡΠ° Π»Π΅ΠΆΠΈΡ ΡΠ΅Π°ΠΊΡΠΈΡ Π²Π·Π°ΠΈΠΌΠΎΠ΄Π΅ΠΉΡΡΠ²ΠΈΡ Π³ΠΈΠΏΠΎΡΠΎΡΡΠΈΡΠ° Π½Π°ΡΡΠΈΡ Ρ ΠΈΠΎΠ½Π°ΠΌΠΈ Π½ΠΈΠΊΠ΅Π»Ρ. ΠΠΈΠΏΠΎΡΠΎΡΡΠΈΡ Π½Π°ΡΡΠΈΡ Π³ΠΈΠ΄ΡΠΎΠ»ΠΈΠ·ΡΠ΅ΡΡΡ Π² Π²ΠΎΠ΄Π΅ Ρ ΠΎΠ±ΡΠ°Π·ΠΎΠ²Π°Π½ΠΈΠ΅ΠΌ ΡΠΎΡΡΠΈΡΠ° Π½Π°ΡΡΠΈΡ ΠΈ Π°ΡΠΎΠΌΠ°ΡΠ½ΠΎΠ³ΠΎ Π²ΠΎΠ΄ΠΎΡΠΎΠ΄Π° ΠΏΠΎ Ρ ΠΈΠΌΠΈΡΠ΅ΡΠΊΠΎΠΉ ΡΠ΅Π°ΠΊΡΠΈΠΈ:
NaH2PO2 + Π2Π = NaH2PO3 + 2ΠΠ°Ρ.
ΠΡΠΎΠΌΠ°ΡΠ½ΡΠΉ Π²ΠΎΠ΄ΠΎΡΠΎΠ΄, Π°Π΄ΡΠΎΡΠ±ΠΈΡΠΎΠ²Π°Π½Π½ΡΠΉ Π½Π° ΠΏΠΎΠ²Π΅ΡΡ Π½ΠΎΡΡΠΈ ΠΏΠΎΠΊΡΡΠ²Π°Π΅ΠΌΠΎΠΉ Π΄Π΅ΡΠ°Π»ΠΈ, Π²ΠΎΡΡΡΠ°Π½Π°Π²Π»ΠΈΠ²Π°Π΅Ρ ΠΈΠΎΠ½Ρ Π½ΠΈΠΊΠ΅Π»Ρ ΠΏΠΎ Ρ ΠΈΠΌΠΈΡΠ΅ΡΠΊΠΎΠΉ ΡΠ΅Π°ΠΊΡΠΈΠΈ:
Ni2+ + 2ΠΠ°ΡΒ β Ni + 2Π+
ΠΠ΄Π½ΠΎΠ²ΡΠ΅ΠΌΠ΅Π½Π½ΠΎ Π°ΡΠΎΠΌΠ°ΡΠ½ΡΠΉ Π²ΠΎΠ΄ΠΎΡΠΎΠ΄ Π²Π·Π°ΠΈΠΌΠΎΠ΄Π΅ΠΉΡΡΠ²ΡΠ΅Ρ Ρ Π°Π½ΠΈΠΎΠ½Π°ΠΌΠΈ Π2Π Π2-1 ΠΈ Π2Π Π3-1, Π²ΠΎΡΡΡΠ°Π½Π°Π²Π»ΠΈΠ²Π°Ρ ΡΠΎΡΡΠΎΡ Π΄ΠΎ ΡΠ»Π΅ΠΌΠ΅Π½ΡΠ°ΡΠ½ΠΎΠ³ΠΎ ΡΠΎΡΡΠΎΡΠ½ΠΈΡ, ΠΊΠΎΡΠΎΡΡΠΉ Π² ΠΏΠΎΡΠ»Π΅Π΄ΡΡΠ²ΠΈΠΈ Π²Ρ ΠΎΠ΄ΠΈΡ Π² ΡΠΎΡΡΠ°Π² ΠΏΠΎΠΊΡΡΡΠΈΡ.
ΠΡΠΈ Ρ ΠΈΠΌΠΈΡΠ΅ΡΠΊΠΎΠΌ Π½ΠΈΠΊΠ΅Π»ΠΈΡΠΎΠ²Π°Π½ΠΈΠΈ Π²ΡΠ΅Π³Π΄Π° Π²ΡΠ΄Π΅Π»ΡΠ΅ΡΡΡ Π²ΠΎΠ΄ΠΎΡΠΎΠ΄:
2ΠΠ°ΡΒ β H2
ΠΠ° ΡΡΡ ΡΠ΅Π°ΠΊΡΠΈΡ ΡΠ°ΡΡ
ΠΎΠ΄ΡΠ΅ΡΡΡ Π±ΠΎΠ»Π΅Π΅ 60 % Π²ΡΠ΄Π΅Π»ΡΡΡΠ΅Π³ΠΎΡΡ ΠΏΠΎ ΡΠ΅Π°ΠΊΡΠΈΠΈ Π²ΠΎΠ΄ΠΎΡΠΎΠ΄Π°.
Β
Π Π΅Π°ΠΊΡΠΈΡ Π²ΠΎΡΡΡΠ°Π½ΠΎΠ²Π»Π΅Π½ΠΈΡ Π½ΠΈΠΊΠ΅Π»Ρ ΡΠ²Π»ΡΠ΅ΡΡΡ Π°Π²ΡΠΎΠΊΠ°ΡΠ°Π»ΠΈΡΠΈΡΠ΅ΡΠΊΠΎΠΉ, Ρ.Π΅. Π΄Π»Ρ Π΅Π΅ Π½Π°ΡΠ°Π»Π° Π½Π΅ΠΎΠ±Ρ ΠΎΠ΄ΠΈΠΌΠΎ Π½Π°Π»ΠΈΡΠΈΠ΅ ΠΊΠ°ΡΠ°Π»ΠΈΠ·Π°ΡΠΎΡΠ°. ΠΠ°ΡΠ°Π»ΠΈΡΠΈΡΠ΅ΡΠΊΠΈΠΌΠΈ ΡΠ²ΠΎΠΉΡΡΠ²Π°ΠΌΠΈ ΠΎΠ±ΡΡΠ½ΠΎ ΠΎΠ±Π»Π°Π΄Π°Π΅Ρ ΠΌΠ΅ΡΠ°Π»Π» Π΄Π΅ΡΠ°Π»ΠΈ, Π½Π°ΠΏΡΠΈΠΌΠ΅Ρ ΠΆΠ΅Π»Π΅Π·ΠΎ, ΡΠΈΡΠ°Π½, Π°Π»ΡΠΌΠΈΠ½ΠΈΠΉ, Π° Π² Π΄Π°Π»ΡΠ½Π΅ΠΉΡΠ΅ΠΌ — Π½ΠΈΠΊΠ΅Π»Ρ (ΠΎΡΡΡΠ΄Π° ΠΈ Π½Π°Π·Π²Π°Π½ΠΈΠ΅ ΠΌΠ΅Ρ Π°Π½ΠΈΠ·ΠΌΠ° — Π°Π²ΡΠΎΠΊΠ°ΡΠ°Π»ΠΈΡΠΈΡΠ΅ΡΠΊΠΈΠΉ Ρ.Π΅. Π½ΠΈΠΊΠ΅Π»Ρ ΡΠ°ΠΌ ΠΏΡΠΎΠ²ΠΎΡΠΈΡΡΠ΅Ρ ΡΠ²ΠΎΠΉ ΡΠΎΡΡ Π½Π° ΠΏΠΎΠΊΡΡΠ²Π°Π΅ΠΌΠΎΠΉ Π΄Π΅ΡΠ°Π»ΠΈ).
ΠΠ°Π½ΠΎΡΠΈΡΡ Ρ
ΠΈΠΌΠΈΡΠ΅ΡΠΊΠΈΠΉ Π½ΠΈΠΊΠ΅Π»Ρ ΠΌΠΎΠΆΠ½ΠΎ ΠΈ Π½Π° ΠΌΠ΅ΡΠ°Π»Π»Ρ, ΠΊΠΎΡΠΎΡΡΠ΅ Π½Π΅ ΡΠ²Π»ΡΡΡΡΡ ΠΊΠ°ΡΠ°Π»ΠΈΠ·Π°ΡΠΎΡΠ°ΠΌΠΈ Π΄Π°Π½Π½ΠΎΠΉ ΡΠ΅Π°ΠΊΡΠΈΠΈ: ΠΌΠ΅Π΄Ρ, ΡΠ΅ΡΠ΅Π±ΡΠΎ ΠΈ Π΄Ρ. Π ΡΡΠΎΠΌ ΡΠ»ΡΡΠ°Π΅ Π½Π΅ΠΎΠ±Ρ
ΠΎΠ΄ΠΈΠΌΡ ΠΏΡΠ΅Π΄Π²Π°ΡΠΈΡΠ΅Π»ΡΠ½ΡΠΉ ΠΊΠΎΠ½ΡΠ°ΠΊΡ Π΄Π΅ΡΠ°Π»ΠΈ Ρ Π±ΠΎΠ»Π΅Π΅ ΠΎΡΡΠΈΡΠ°ΡΠ΅Π»ΡΠ½ΡΠΌ ΠΌΠ΅ΡΠ°Π»Π»ΠΎΠΌ, Π½Π°ΠΏΡΠΈΠΌΠ΅Ρ Ρ Π°Π»ΡΠΌΠΈΠ½ΠΈΠ΅ΠΌ, ΠΈΠ»ΠΈ ΠΏΠΎΠ΄Π°ΡΠ° ΠΊΠΎΡΠΎΡΠΊΠΎΠ³ΠΎ ΠΈΠΌΠΏΡΠ»ΡΡΠ° ΡΠΎΠΊΠ°. ΠΠ° ΡΠ°ΠΊΠΈΡ
ΠΌΠ΅ΡΠ°Π»Π»Π°Ρ
, ΠΊΠ°ΠΊ ΡΠ²ΠΈΠ½Π΅Ρ, ΠΊΠ°Π΄ΠΌΠΈΠΉ, ΠΎΠ»ΠΎΠ²ΠΎ ΠΈ Π΄Ρ., ΠΏΠΎΠΊΡΡΡΠΈΠ΅ ΠΏΠΎΠ»ΡΡΠΈΡΡ Π½Π΅Π²ΠΎΠ·ΠΌΠΎΠΆΠ½ΠΎ. Π₯ΠΈΠΌΠΈΡΠ΅ΡΠΊΠΈΠΉ Π½ΠΈΠΊΠ΅Π»Ρ Π½Π°Π½ΠΎΡΡΡ ΠΈ Π½Π° Π½Π΅ΠΌΠ΅ΡΠ°Π»Π»ΠΈΡΠ΅ΡΠΊΠΈΠ΅ ΠΌΠ°ΡΠ΅ΡΠΈΠ°Π»Ρ: ΡΡΠ΅ΠΊΠ»ΠΎ, ΠΊΠ΅ΡΠ°ΠΌΠΈΠΊΡ ΠΈ ΠΏΠ»Π°ΡΡΠΌΠ°ΡΡΡ. ΠΠ΅ΡΠ΅Π΄ Π½Π°Π½Π΅ΡΠ΅Π½ΠΈΠ΅ΠΌ ΠΏΠΎΠΊΡΡΡΠΈΡ ΠΏΠΎΠ²Π΅ΡΡ
Π½ΠΎΡΡΡ ΠΏΠΎΠ΄Π²Π΅ΡΠ³Π°ΡΡ Π°ΠΊΡΠΈΠ²ΠΈΡΠΎΠ²Π°Π½ΠΈΡ ΠΈΠ·Π²Π΅ΡΡΠ½ΡΠΌΠΈ ΠΌΠ΅ΡΠΎΠ΄Π°ΠΌΠΈ.
Π‘ΠΎΠ΄Π΅ΡΠΆΠ°Π½ΠΈΠ΅ ΡΠΎΡΡΠΎΡΠ° Π² ΠΏΠΎΠΊΡΡΡΠΈΠΈ ΠΊΠΎΠ»Π΅Π±Π»Π΅ΡΡΡ Π² ΠΏΡΠ΅Π΄Π΅Π»Π°Ρ
ΠΎΡ 3 Π΄ΠΎ 12 % ΠΈ Π·Π°Π²ΠΈΡΠΈΡ ΠΎΡ ΠΊΠΈΡΠ»ΠΎΡΠ½ΠΎΡΡΠΈ ΡΠ°ΡΡΠ²ΠΎΡΠ°, ΡΠ½ΠΈΠΆΠ°ΡΡΡ Ρ ΠΏΠΎΠ½ΠΈΠΆΠ΅Π½ΠΈΠ΅ΠΌ ΡΠ. ΠΠΎΠ·ΠΌΠΎΠΆΠ½ΠΎ, ΡΡΠΎ ΡΠ²ΡΠ·Π°Π½ΠΎ Ρ ΡΠ΅ΠΌ, ΡΡΠΎ ΡΠΊΠΎΡΠΎΡΡΡ Π²ΠΎΡΡΡΠ°Π½ΠΎΠ²Π»Π΅Π½ΠΈΡ ΠΈΠΎΠ½ΠΎΠ² Π½ΠΈΠΊΠ΅Π»Ρ Ρ ΡΠΎΡΡΠΎΠΌ ΡΠ ΡΠ²Π΅Π»ΠΈΡΠΈΠ²Π°Π΅ΡΡΡ Π±ΡΡΡΡΠ΅Π΅, ΡΠ΅ΠΌ ΡΠΊΠΎΡΠΎΡΡΡ Π²ΠΎΡΡΡΠ°Π½ΠΎΠ²Π»Π΅Π½ΠΈΡ ΡΠΎΡΡΠΎΡΠ°.
ΠΠ° ΡΠΊΠΎΡΠΎΡΡΡ Ρ ΠΈΠΌΠΈΡΠ΅ΡΠΊΠΎΠ³ΠΎ Π½ΠΈΠΊΠ΅Π»ΠΈΡΠΎΠ²Π°Π½ΠΈΡ ΠΎΠΊΠ°Π·ΡΠ²Π°ΡΡ Π²Π»ΠΈΡΠ½ΠΈΠ΅ ΠΈ ΡΠ°ΠΊΠΈΠ΅ ΡΠ°ΠΊΡΠΎΡΡ, ΠΊΠ°ΠΊ ΡΠ΅ΠΌΠΏΠ΅ΡΠ°ΡΡΡΠ°, ΠΊΠΎΠ½ΡΠ΅Π½ΡΡΠ°ΡΠΈΡ ΠΈ ΡΠΎΠΎΡΠ½ΠΎΡΠ΅Π½ΠΈΠ΅ Π³ΠΈΠΏΠΎΡΠΎΡΡΠΈΡΠ° Π½Π°ΡΡΠΈΡ ΠΈ ΠΈΠΎΠ½ΠΎΠ² Π½ΠΈΠΊΠ΅Π»Ρ, ΠΏΡΠΈΡΠΎΠ΄Π° ΠΈ ΠΊΠΎΠ»ΠΈΡΠ΅ΡΡΠ²ΠΎ ΠΎΡΠ³Π°Π½ΠΈΡΠ΅ΡΠΊΠΈΡ Π΄ΠΎΠ±Π°Π²ΠΎΠΊ.
Π’Π΅ΠΌΠΏΠ΅ΡΠ°ΡΡΡΡ ΡΠ°Π±ΠΎΡΠ΅Π³ΠΎ ΡΠ°ΡΡΠ²ΠΎΡΠ° ΠΏΠΎΠ΄Π΄Π΅ΡΠΆΠΈΠ²Π°ΡΡ ΡΠ°Π²Π½ΠΎΠΉ 80-97 Β°Π‘. ΠΡΠΈ ΠΏΠΎΠ²ΡΡΠ΅Π½ΠΈΠΈ ΡΠ΅ΠΌΠΏΠ΅ΡΠ°ΡΡΡΡ Ρ 80 Π΄ΠΎ 90 Β°Π‘ ΡΠΊΠΎΡΠΎΡΡΡ ΠΎΡΠ°ΠΆΠ΄Π΅Π½ΠΈΡ ΡΠ²Π΅Π»ΠΈΡΠΈΠ²Π°Π΅ΡΡΡ Π² 1,5 ΡΠ°Π·Π°, Π° ΠΏΡΠΈ ΡΠ½ΠΈΠΆΠ΅Π½ΠΈΠΈ Π΅Π΅ Π½ΠΈΠΆΠ΅ 70 Β°Π‘ ΠΏΡΠΎΡΠ΅ΡΡ ΠΎΡΠ°ΠΆΠ΄Π΅Π½ΠΈΡ ΠΏΠΎΠ»Π½ΠΎΡΡΡΡ ΠΏΡΠ΅ΠΊΡΠ°ΡΠ°Π΅ΡΡΡ.
Π₯ΠΈΠΌΠΈΡΠ΅ΡΠΊΠΎΠ΅ Π½ΠΈΠΊΠ΅Π»ΠΈΡΠΎΠ²Π°Π½ΠΈΠ΅ ΠΏΡΠΎΡΠ΅ΠΊΠ°Π΅Ρ ΠΏΡΠΈ ΡΠ 4-4,5 ΠΈ ΠΏΡΠΈ ΡΠ 8-10, ΠΏΠΎΡΡΠΎΠΌΡ ΡΠ°ΡΡΠ²ΠΎΡΡ, Π² ΠΊΠΎΡΠΎΡΡΡ
ΠΏΡΠΎΠΈΡΡ
ΠΎΠ΄ΠΈΡ ΠΎΡΠ°ΠΆΠ΄Π΅Π½ΠΈΠ΅ ΠΏΠΎΠΊΡΡΡΠΈΡ, Π΄Π΅Π»ΡΡΡΡ Π½Π° ΠΊΠΈΡΠ»ΡΠ΅ ΠΈ ΡΠ΅Π»ΠΎΡΠ½ΡΠ΅. ΠΡΠΈ ΡΠ<4 ΠΏΡΠΎΡΠ΅ΡΡ ΠΎΡΠ°ΠΆΠ΄Π΅Π½ΠΈΡ ΠΏΡΠ΅ΠΊΡΠ°ΡΠ°Π΅ΡΡΡ. ΠΡΠΈ ΡΠ>5,5 Π½Π°ΡΠΈΠ½Π°Π΅ΡΡΡ Π³ΠΈΠ΄ΡΠΎΠ»ΠΈΠ· ΡΠΎΠ»Π΅ΠΉ Π½ΠΈΠΊΠ΅Π»Ρ, ΠΏΡΠΈ ΡΡΠΎΠΌ ΡΠ°ΡΡΠΈΡΡ Π³ΠΈΠ΄ΡΠΎΠΊΡΠΈΠ΄Π° Π½ΠΈΠΊΠ΅Π»Ρ ΡΡΠ°Π½ΠΎΠ²ΡΡΡΡ ΡΠ΅Π½ΡΡΠ°ΠΌΠΈ ΡΠ°Π·Π»ΠΎΠΆΠ΅Π½ΠΈΡ ΡΠ°Π±ΠΎΡΠ΅Π³ΠΎ ΡΠ°ΡΡΠ²ΠΎΡΠ° ΠΈ ΠΌΠΎΠΆΠ΅Ρ ΠΏΡΠΎΠΈΠ·ΠΎΠΉΡΠΈ Β«ΡΠ°ΠΌΠΎΡΠ°Π·ΡΡΠ΄Β» Π²Π°Π½Π½Ρ — Π²ΡΠ΄Π΅Π»Π΅Π½ΠΈΠ΅ ΠΌΠ΅ΡΠ°Π»Π»ΠΈΡΠ΅ΡΠΊΠΎΠ³ΠΎ Π½ΠΈΠΊΠ΅Π»Ρ Π²ΠΎ Π²ΡΠ΅ΠΌ ΠΎΠ±ΡΠ΅ΠΌΠ΅ ΡΠ°ΡΡΠ²ΠΎΡΠ°.
Π’Π°ΠΊ ΠΊΠ°ΠΊ Π²ΠΎ Π²ΡΠ΅ΠΌΡ Ρ
ΠΈΠΌΠΈΡΠ΅ΡΠΊΠΎΠ³ΠΎ Π½ΠΈΠΊΠ΅Π»ΠΈΡΠΎΠ²Π°Π½ΠΈΡ Π²ΡΠ΅ Π²ΡΠ΅ΠΌΡ Π²ΡΠ΄Π΅Π»ΡΠ΅ΡΡΡ ΠΊΠΈΡΠ»ΠΎΡΠ°, Π½Π΅ΠΎΠ±Ρ
ΠΎΠ΄ΠΈΠΌΠΎ Π²Π²ΠΎΠ΄ΠΈΡΡ ΡΠ°Π·Π»ΠΈΡΠ½ΡΠ΅ Π±ΡΡΠ΅ΡΠ½ΡΠ΅ Π΄ΠΎΠ±Π°Π²ΠΊΠΈ: ΡΠΊΡΡΡΠ½ΡΡ ΠΊΠΈΡΠ»ΠΎΡΡ, ΡΠ½ΡΠ°ΡΠ½ΡΡ ΠΊΠΈΡΠ»ΠΎΡΡ ΠΈ Ρ. ΠΏ. ΠΠ²Π΅Π΄Π΅Π½ΠΈΠ΅ Π² ΡΠ°ΡΡΠ²ΠΎΡ ΠΊΠΎΠΌΠΏΠ»Π΅ΠΊΡΠΎΠΎΠ±ΡΠ°Π·ΠΎΠ²Π°ΡΠ΅Π»Π΅ΠΉ ΠΏΡΠ΅ΠΏΡΡΡΡΠ²ΡΠ΅Ρ ΠΎΠ±ΡΠ°Π·ΠΎΠ²Π°Π½ΠΈΡ ΡΠΎΡΡΠΈΡΠ° Π½ΠΈΠΊΠ΅Π»Ρ, ΠΊΠΎΡΠΎΡΡΠΉ, Π²ΡΠΏΠ°Π΄Π°Ρ Π² ΠΎΡΠ°Π΄ΠΎΠΊ, Π΄Π΅Π»Π°Π΅Ρ Π΅Π³ΠΎ Π½Π΅ΠΏΡΠΈΠ³ΠΎΠ΄Π½ΡΠΌ Π΄Π»Ρ Π΄Π°Π»ΡΠ½Π΅ΠΉΡΠ΅Π³ΠΎ ΠΈΡΠΏΠΎΠ»ΡΠ·ΠΎΠ²Π°Π½ΠΈΡ.
ΠΠ±ΡΡΠ½ΠΎ ΡΠ°ΡΡΠ²ΠΎΡ ΠΈΡΠΏΠΎΠ»ΡΠ·ΡΡΡ ΠΎΠ΄ΠΈΠ½ ΡΠ°Π·, ΠΏΡΠΈ ΡΡΠΎΠΌ 10-15 % ΠΈΡΡ
ΠΎΠ΄Π½ΡΡ
ΠΊΠΎΠΌΠΏΠΎΠ½Π΅Π½ΡΠΎΠ² ΠΏΡΠΎΠΏΠ°Π΄Π°Π΅Ρ, Π° Π±ΡΡΠ΅ΡΠ½ΡΠ΅ Π΄ΠΎΠ±Π°Π²ΠΊΠΈ ΠΏΡΠΎΠΏΠ°Π΄Π°ΡΡ ΠΏΠΎΠ»Π½ΠΎΡΡΡΡ. ΠΠ΄Π½Π°ΠΊΠΎ ΠΈΠ·-Π·Π° ΡΠ²ΠΎΠ΅ΠΉ ΠΏΡΠΎΡΡΠΎΡΡ ΡΡΠΎΡ ΡΠΏΠΎΡΠΎΠ± ΡΠΈΡΠΎΠΊΠΎ ΠΏΡΠΈΠΌΠ΅Π½ΡΠ΅ΡΡΡ Π² ΠΏΡΠΎΠΌΡΡΠ»Π΅Π½Π½ΠΎΡΡΠΈ, Ρ
ΠΎΡΡ Π΅Π³ΠΎ ΠΈ Π½Π΅Π»ΡΠ·Ρ Π½Π°Π·Π²Π°ΡΡ ΡΠΊΠΎΠ»ΠΎΠ³ΠΈΡΠ½ΡΠΌ.
ΠΡΠΎΠΌΠ΅ Π±ΡΡΠ΅ΡΠ½ΡΡ
Π΄ΠΎΠ±Π°Π²ΠΎΠΊ ΠΈ ΠΊΠΎΠΌΠΏΠ»Π΅ΠΊΡΠΎΠΎΠ±ΡΠ°Π·ΠΎΠ²Π°ΡΠ΅Π»Π΅ΠΉ Π² ΡΠ°ΡΡΠ²ΠΎΡΡ Π²Π²ΠΎΠ΄ΡΡ Π² ΠΎΡΠ΅Π½Ρ ΠΌΠ°Π»ΡΡ
ΠΊΠΎΠ»ΠΈΡΠ΅ΡΡΠ²Π°Ρ
ΡΠΏΠ΅ΡΠΈΠ°Π»ΡΠ½ΡΠ΅ Π΄ΠΎΠ±Π°Π²ΠΊΠΈ-ΡΡΠ°Π±ΠΈΠ»ΠΈΠ·Π°ΡΠΎΡΡ, Π½Π°ΠΏΡΠΈΠΌΠ΅Ρ ΠΊΠ°ΡΠΈΠΎΠ½Ρ ΡΡΡΡΠΌΡ, Π²ΠΈΡΠΌΡΡΠ° ΠΈ ΠΌΡΡΡΡΠΊΠ°.
Π ΠΊΠΈΡΠ»ΡΡ
ΡΠ°ΡΡΠ²ΠΎΡΠ°Ρ
ΠΎΠΏΡΠΈΠΌΠ°Π»ΡΠ½ΡΠΌ ΠΎΡΠ½ΠΎΡΠ΅Π½ΠΈΠ΅ΠΌ ΡΠΎΠ»ΠΈ Π½ΠΈΠΊΠ΅Π»Ρ ΠΊ Π³ΠΈΠΏΠΎΡΠΎΡΡΠΈΡΡ Π½Π°ΡΡΠΈΡ, Π²ΡΡΠ°ΠΆΠ΅Π½Π½ΡΠΌ Π² ΠΌΠΎΠ»ΡΡ
, ΡΠ²Π»ΡΠ΅ΡΡΡ 0,4. ΠΠ°ΠΊΠΎΠΏΠ»Π΅Π½ΠΈΠ΅ ΡΠΎΡΡΠΈΡΠΎΠ² Π½ΠΈΠΊΠ΅Π»Ρ ΠΎΠΊΠ°Π·ΡΠ²Π°Π΅Ρ Π²ΡΠ΅Π΄Π½ΠΎΠ΅ Π²Π»ΠΈΡΠ½ΠΈΠ΅ Π½Π° ΠΏΡΠΎΡΠ΅ΡΡ ΠΎΡΠ°ΠΆΠ΄Π΅Π½ΠΈΡ: Π²Π·Π²Π΅ΡΠ΅Π½Π½ΡΠ΅ ΡΠ°ΡΡΠΈΡΡ ΡΡΡΠ΄Π½ΠΎΡΠ°ΡΡΠ²ΠΎΡΠΈΠΌΡΡ
ΡΠΎΡΡΠΈΡΠΎΠ² ΠΎΡΠ΅Π΄Π°ΡΡ Π½Π° Π΄Π΅ΡΠ°Π»ΡΡ
, Π΄Π΅Π»Π°Ρ ΠΏΠΎΠ²Π΅ΡΡ
Π½ΠΎΡΡΡ ΡΠ΅ΡΠΎΡ
ΠΎΠ²Π°ΡΠΎΠΉ.
ΠΡΠΎΡΠ΅ΡΡ ΠΏΡΠΎΡΠ΅ΠΊΠ°Π΅Ρ ΠΏΡΠΈ ΡΠ΅ΠΌΠΏΠ΅ΡΠ°ΡΡΡΠ΅ 80-100 Β°Π‘. Π’Π°ΠΊ ΠΊΠ°ΠΊ ΠΊΠΈΡΠ»ΠΎΡΠ½ΠΎΡΡΡ ΡΠ°ΡΡΠ²ΠΎΡΠ° Π²ΡΠ΅ Π²ΡΠ΅ΠΌΡ ΡΠ²Π΅Π»ΠΈΡΠΈΠ²Π°Π΅ΡΡΡ ΠΈΠ·-Π·Π° ΠΎΠ±ΡΠ°Π·ΠΎΠ²Π°Π½ΠΈΡ ΡΠΎΡΡΠΎΡΠΈΡΡΠΎΠΉ ΠΊΠΈΡΠ»ΠΎΡΡ, Π΄ΠΎΠ±Π°Π²Π»ΡΡΡ 1-2 %-Π½ΡΠΉ ΡΠ°ΡΡΠ²ΠΎΡ NaOH ΠΈΠ»ΠΈ 25 %-Π½ΡΠΉ ΡΠ°ΡΡΠ²ΠΎΡ Nh5OH (1:10).
ΠΠΈΡΠ»ΡΠ΅ ΡΠ°ΡΡΠ²ΠΎΡΡ ΠΏΠΎ ΡΡΠ°Π²Π½Π΅Π½ΠΈΡ ΡΠΎ ΡΠ΅Π»ΠΎΡΠ½ΡΠΌΠΈ ΠΈΠΌΠ΅ΡΡ ΡΡΠ΄ ΠΏΡΠ΅ΠΈΠΌΡΡΠ΅ΡΡΠ²: ΠΎΠ½ΠΈ Π±ΠΎΠ»Π΅Π΅ ΡΡΠ°Π±ΠΈΠ»ΡΠ½Ρ, ΠΈΠΌΠ΅ΡΡ Π±ΠΎΠ»Π΅Π΅ Π²ΡΡΠΎΠΊΡΡ ΡΠΊΠΎΡΠΎΡΡΡ ΠΎΡΠ°ΠΆΠ΄Π΅Π½ΠΈΡ ΠΈ ΠΎΠ±Π»Π°Π΄Π°ΡΡ Π±ΠΎΠ»Π΅Π΅ Π²ΡΡΠΎΠΊΠΈΠΌΠΈ Π·Π°ΡΠΈΡΠ½ΡΠΌΠΈ ΡΠ²ΠΎΠΉΡΡΠ²Π°ΠΌΠΈ.
Π©Π΅Π»ΠΎΡΠ½ΡΠ΅ ΡΠ°ΡΡΠ²ΠΎΡΡ ΠΊΡΠΎΠΌΠ΅ ΡΠΎΠ»Π΅ΠΉ Π½ΠΈΠΊΠ΅Π»Ρ ΠΈ Π³ΠΈΠΏΠΎΡΠΎΡΡΠΈΡΠ° Π½Π°ΡΡΠΈΡ ΡΠΎΠ΄Π΅ΡΠΆΠ°Ρ ΠΊΠΎΠΌΠΏΠ»Π΅ΠΊΡΠΎΠΎΠ±ΡΠ°Π·ΠΎΠ²Π°ΡΠ΅Π»ΠΈ — Π°ΠΌΠΌΠΈΠ°ΠΊ ΠΈ Π»ΠΈΠΌΠΎΠ½Π½ΡΡ ΠΊΠΈΡΠ»ΠΎΡΡ, ΡΡΠΎ ΠΏΠΎΠ·Π²ΠΎΠ»ΡΠ΅Ρ Π²Π΅ΡΡΠΈ ΠΏΡΠΎΡΠ΅ΡΡ ΠΎΡΠ°ΠΆΠ΄Π΅Π½ΠΈΡ Π΄Π»ΠΈΡΠ΅Π»ΡΠ½ΠΎΠ΅ Π²ΡΠ΅ΠΌΡ. Π Π°ΡΡΠ²ΠΎΡΠΈΠΌΠΎΡΡΡ ΡΠΎΡΡΠΈΡΠΎΠ² Π² ΡΠ΅Π»ΠΎΡΠ½ΡΡ
ΡΠ°ΡΡΠ²ΠΎΡΠ°Ρ
Π·Π½Π°ΡΠΈΡΠ΅Π»ΡΠ½ΠΎ Π²ΡΡΠ΅, ΡΠ΅ΠΌ Π² ΠΊΠΈΡΠ»ΡΡ
. ΠΠ°ΠΊΠ°ΠΏΠ»ΠΈΠ²Π°ΡΡΠΈΠΉΡΡ ΡΠΎΡΡΠΈΡ Π½Π΅ ΠΎΠΊΠ°Π·ΡΠ²Π°Π΅Ρ Π²ΡΠ΅Π΄Π½ΠΎΠ³ΠΎ Π²Π»ΠΈΡΠ½ΠΈΡ ΠΏΡΠΈ ΠΊΠΎΠ½ΡΠ΅Π½ΡΡΠ°ΡΠΈΠΈ ΠΌΠ΅Π½Π΅Π΅ 340 Π³/Π». Π ΡΠ΅Π»ΠΎΡΠ½ΡΡ
ΡΠ°ΡΡΠ²ΠΎΡΠ°Ρ
ΠΌΠΎΠΆΠ½ΠΎ Π½Π°Π½ΠΎΡΠΈΡΡ ΠΏΠΎΠΊΡΡΡΠΈΠ΅ Π½Π° ΠΊΠΎΡΡΠΎΠ·ΠΈΠΎΠ½Π½ΠΎ-ΡΡΠΎΠΉΠΊΡΡ ΡΡΠ°Π»Ρ, Π°Π»ΡΠΌΠΈΠ½ΠΈΠΉ, ΡΠΈΡΠ°Π½ ΠΈ Ρ. ΠΏ.
ΠΠΎΠΊΡΡΡΠΈΡ, ΠΏΠΎΠ»ΡΡΠ΅Π½Π½ΡΠ΅ ΠΏΡΠΈ Ρ
ΠΈΠΌΠΈΡΠ΅ΡΠΊΠΎΠΌ Π½ΠΈΠΊΠ΅Π»ΠΈΡΠΎΠ²Π°Π½ΠΈΠΈ, ΠΈΠΌΠ΅ΡΡ ΡΠ»ΠΎΠΈΡΡΡΡ Π°ΠΌΠΎΡΡΠ½ΡΡ ΡΡΡΡΠΊΡΡΡΡ. ΠΠ΅Π΄ΠΎΡΡΠ°ΡΠΊΠΎΠΌ ΠΏΠΎΠΊΡΡΡΠΈΡ ΡΠ²Π»ΡΠ΅ΡΡΡ Π΅Π³ΠΎ Ρ
ΡΡΠΏΠΊΠΎΡΡΡ, ΠΊΠΎΡΠΎΡΠ°Ρ Π½Π°ΡΠΈΠ½Π°Π΅Ρ ΠΏΡΠΎΡΠ²Π»ΡΡΡΡΡ ΠΏΡΠΈ ΡΠΎΠ»ΡΠΈΠ½Π΅ ΡΠ»ΠΎΡ ΠΎΠΊΠΎΠ»ΠΎ 10 ΠΌΠΊΠΌ ΠΈ Π²ΡΡΠ΅. ΠΠΎΡΠ»Π΅ ΡΠ΅ΡΠΌΠΈΡΠ΅ΡΠΊΠΎΠΉ ΠΎΠ±ΡΠ°Π±ΠΎΡΠΊΠΈ ΠΏΠΎΠΊΡΡΡΠΈΠ΅ ΡΡΠ°Π½ΠΎΠ²ΠΈΡΡΡ ΠΊΡΠΈΡΡΠ°Π»Π»ΠΈΡΠ΅ΡΠΊΠΈΠΌ ΠΈ ΠΏΡΠ΅Π΄ΡΡΠ°Π²Π»ΡΠ΅Ρ ΡΠΎΠ±ΠΎΠΉ ΡΠ²Π΅ΡΠ΄ΡΠΉ ΡΠ°ΡΡΠ²ΠΎΡ Π½ΠΈΠΊΠ΅Π»Ρ Ρ Π½Π΅Π±ΠΎΠ»ΡΡΠΈΠΌ ΡΠΎΠ΄Π΅ΡΠΆΠ°Π½ΠΈΠ΅ΠΌ ΡΠΎΡΡΠΎΡΠ° ΠΈ ΠΈΠ½ΡΠ΅ΡΠΌΠ΅ΡΠ°Π»Π»ΠΈΡΠ΅ΡΠΊΠΎΠ΅ ΡΠΎΠ΅Π΄ΠΈΠ½Π΅Π½ΠΈΠ΅ Ni3P. Π‘ΠΎΠ΄Π΅ΡΠΆΠ°Π½ΠΈΠ΅ ΡΠΎΡΡΠΎΡΠ° 4-8 % Π΄Π»Ρ ΡΠ΅Π»ΠΎΡΠ½ΡΡ
ΠΈ 8-10 % Π΄Π»Ρ ΠΊΠΈΡΠ»ΡΡ
ΡΠ°ΡΡΠ²ΠΎΡΠΎΠ².
Π’Π΅ΡΠΌΠΈΡΠ΅ΡΠΊΠ°Ρ ΠΎΠ±ΡΠ°Π±ΠΎΡΠΊΠ° ΠΏΠΎΠ·Π²ΠΎΠ»ΡΠ΅Ρ ΠΏΠΎΠ²ΡΡΠΈΡΡ ΠΌΠΈΠΊΡΠΎΡΠ²Π΅ΡΠ΄ΠΎΡΡΡ ΠΏΠΎΠΊΡΡΡΠΈΠΉ Π΄ΠΎ 8400-11 800 ΠΠΠ°. Π’Π΅ΡΠΌΠΈΡΠ΅ΡΠΊΠ°Ρ ΠΎΠ±ΡΠ°Π±ΠΎΡΠΊΠ° ΡΡΠ°Π»ΡΠ½ΡΡ
Π΄Π΅ΡΠ°Π»Π΅ΠΉ ΠΏΡΠΎΠΈΠ·Π²ΠΎΠ΄ΠΈΡΡΡ ΠΏΡΠΈ ΡΠ΅ΠΌΠΏΠ΅ΡΠ°ΡΡΡΠ΅ 300-400 Β°Π‘, Π°Π»ΡΠΌΠΈΠ½ΠΈΠ΅Π²ΡΡ
— ΠΏΡΠΈ 275-280 Β°Π‘, Π° Π΄Π΅ΡΠ°Π»Π΅ΠΉ ΠΈΠ· Π΄ΡΡΠ°Π»Ρ — ΠΏΡΠΈ 375-385 Β°Π‘. ΠΡΠ΅ΠΌΡ Π²ΡΠ΄Π΅ΡΠΆΠΊΠΈ 1 Ρ. Π‘ΡΡΡΠΊΡΡΡΠ½ΡΠ΅ ΠΏΡΠ΅Π²ΡΠ°ΡΠ΅Π½ΠΈΡ Π² ΠΏΠΎΠΊΡΡΡΠΈΡΡ
ΡΠΎΠΏΡΠΎΠ²ΠΎΠΆΠ΄Π°ΡΡΡΡ Π²ΡΠ΄Π΅Π»Π΅Π½ΠΈΠ΅ΠΌ ΡΠ΅ΠΏΠ»Π° ΠΈ ΠΈΠ·ΠΌΠ΅Π½Π΅Π½ΠΈΠ΅ΠΌ ΠΎΠ±ΡΠ΅ΠΌΠ°, ΠΏΠΎΡΡΠΎΠΌΡ ΠΏΡΠΈ ΠΎΡΠ΅Π½Ρ Π±ΡΡΡΡΠΎΠΌ Π½Π°Π³ΡΠ΅Π²Π΅ Π²ΠΎΠ·ΠΌΠΎΠΆΠ½ΠΎ ΡΠ°Π·ΡΡΡΠ΅Π½ΠΈΠ΅ ΠΏΠΎΠΊΡΡΡΠΈΠΉ.
Π‘ΡΠ΅ΠΏΠ»Π΅Π½ΠΈΠ΅ Π½ΠΈΠΊΠ΅Π»Ρ-ΡΠΎΡΡΠΎΡΠ½ΡΡ
ΠΏΠΎΠΊΡΡΡΠΈΠΉ ΡΠΈΠ»ΡΠ½Π΅Π΅ ΡΡΠ΅ΠΏΠ»Π΅Π½ΠΈΡ ΡΠ»Π΅ΠΊΡΡΠΎΠ»ΠΈΡΠΈΡΠ΅ΡΠΊΠΎΠ³ΠΎ Π½ΠΈΠΊΠ΅Π»Ρ, ΡΠ°ΠΊ ΠΊΠ°ΠΊ ΠΎΡΠ°ΠΆΠ΄Π΅Π½ΠΈΠ΅ ΠΏΡΠΎΠΈΡΡ
ΠΎΠ΄ΠΈΡ ΡΠ°Π²Π½ΠΎΠΌΠ΅ΡΠ½ΠΎ ΠΊΠ°ΠΊ Π²Π½ΡΡΡΠΈ, ΡΠ°ΠΊ ΠΈ ΡΠ½Π°ΡΡΠΆΠΈ Π΄Π΅ΡΠ°Π»ΠΈ, Π·Π°ΠΏΠΎΠ»Π½ΡΡ Π²ΡΠ΅ ΠΌΠΈΠΊΡΠΎΡΠ³Π»ΡΠ±Π»Π΅Π½ΠΈΡ ΠΈ Π½Π΅ΡΠΎΠ²Π½ΠΎΡΡΠΈ. ΠΡΠΊΠ»ΠΎΠ½Π΅Π½ΠΈΡ ΡΠΎΠ»ΡΠΈΠ½ Π½Π΅ ΠΏΡΠ΅Π²ΡΡΠ°ΡΡ 10%, ΠΏΠΎΡΡΠΎΠΌΡ Ρ
ΠΈΠΌΠΈΡΠ΅ΡΠΊΠΈΠΉ Π½ΠΈΠΊΠ΅Π»Ρ Π½Π°Π½ΠΎΡΡΡ Π½Π° ΠΏΡΠ΅ΡΠΈΠ·ΠΈΠΎΠ½Π½ΡΠ΅ Π΄Π΅ΡΠ°Π»ΠΈ, Π½Π°ΠΏΡΠΈΠΌΠ΅Ρ Π½Π° ΠΏΠ»ΡΠ½ΠΆΠ΅ΡΠ½ΡΠ΅ ΠΏΠ°ΡΡ ΡΠΎΠΏΠ»ΠΈΠ²Π½ΡΡ
Π½Π°ΡΠΎΡΠΎΠ² Π΄Π²ΠΈΠ³Π°ΡΠ΅Π»Π΅ΠΉ, ΠΌΠ΅Π»ΠΊΠΈΠ΅ Π΄Π΅ΡΠ°Π»ΠΈ Π² ΡΠ°ΡΠΎΠ²ΠΎΠΉ ΠΈ ΠΎΠΏΡΠΈΡΠ΅ΡΠΊΠΎΠΉ ΠΏΡΠΎΠΌΡΡΠ»Π΅Π½Π½ΠΎΡΡΠΈ ΠΈ Ρ. ΠΏ.
ΠΡΡΠΎΠΊΠΈΠ΅ Π·Π°ΡΠΈΡΠ½ΡΠ΅ ΡΠ²ΠΎΠΉΡΡΠ²Π° Π½Π°ΡΡΠ΄Ρ Ρ Π½Π΅Π±ΠΎΠ»ΡΡΠΎΠΉ ΠΏΠΎΡΠΈΡΡΠΎΡΡΡΡ ΠΏΠΎΠ·Π²ΠΎΠ»ΡΡΡ ΠΏΡΠΈΠΌΠ΅Π½ΡΡΡ Π½ΠΈΠΊΠ΅Π»Ρ-ΡΠΎΡΡΠΎΡΠ½ΡΠ΅ ΠΏΠΎΠΊΡΡΡΠΈΡ Π² ΠΊΠ°ΡΠ΅ΡΡΠ²Π΅ Π·Π°ΡΠΈΡΠ½ΡΡ
, Π² ΡΠΎΠΌ ΡΠΈΡΠ»Π΅ Π² ΡΡΠ»ΠΎΠ²ΠΈΡΡ
ΠΏΠ΅ΡΠ΅Π³ΡΠ΅ΡΠΎΠ³ΠΎ ΠΏΠ°ΡΠ° ΠΈ Π²ΠΎΠ·Π΄ΡΡ
Π°, Π²ΠΏΠ»ΠΎΡΡ Π΄ΠΎ 700 Β°Π‘. ΠΠ»Ρ ΡΠ²Π΅Π»ΠΈΡΠ΅Π½ΠΈΡ ΠΈΠ·Π½ΠΎΡΠΎΡΡΡΠΎΠΉΡΠΈΠ²ΠΎΡΡΠΈ ΠΈ ΡΠ½ΠΈΠΆΠ΅Π½ΠΈΡ ΠΊΠΎΡΡΡΠΈΡΠΈΠ΅Π½ΡΠ° ΡΡΠ΅Π½ΠΈΡ Π½ΠΈΠΊΠ΅Π»Ρ-ΡΠΎΡΡΠΎΡΠ½ΠΎΠ΅ ΠΏΠΎΠΊΡΡΡΠΈΠ΅ Π½Π°Π½ΠΎΡΡΡ Π½Π° ΡΡΡΡΠΈΠ΅ΡΡ ΠΏΠΎΠ²Π΅ΡΡ
Π½ΠΎΡΡΠΈ. ΠΠ΅Π·Π°ΠΌΠ΅Π½ΠΈΠΌΠΎ ΠΏΠΎΠΊΡΡΡΠΈΠ΅ Π² ΠΏΠΎΠ»Π΅Π²ΡΡ
ΡΡΠ»ΠΎΠ²ΠΈΡΡ
ΠΈ Π² Π½Π΅Π±ΠΎΠ»ΡΡΠΈΡ
ΠΌΠ°ΡΡΠ΅ΡΡΠΊΠΈΡ
Π΄Π»Ρ Π²ΠΎΡΡΡΠ°Π½ΠΎΠ²Π»Π΅Π½ΠΈΡ ΡΠ°Π·ΠΌΠ΅ΡΠΎΠ² ΠΈΠ·Π½ΠΎΡΠ΅Π½Π½ΡΡ
Π΄Π΅ΡΠ°Π»Π΅ΠΉ. Π¦Π΅Π»Π΅ΡΠΎΠΎΠ±ΡΠ°Π·Π½ΠΎ Π½Π°Π½Π΅ΡΠ΅Π½ΠΈΠ΅ ΠΏΠΎΠΊΡΡΡΠΈΡ Π½Π° ΠΊΡΡΠΏΠ½ΠΎΠ³Π°Π±Π°ΡΠΈΡΠ½ΡΠ΅ Π΄Π΅ΡΠ°Π»ΠΈ.
Π‘ΠΊΠΎΡΠΎΡΡΡ ΠΎΡΠ°ΠΆΠ΄Π΅Π½ΠΈΡ ΠΏΡΠΈ Ρ
ΠΈΠΌΠΈΡΠ΅ΡΠΊΠΎΠΌ Π½ΠΈΠΊΠ΅Π»ΠΈΡΠΎΠ²Π°Π½ΠΈΠΈ ΠΊΠΎΠ»Π΅Π±Π»Π΅ΡΡΡ Π² Π·Π°Π²ΠΈΡΠΈΠΌΠΎΡΡΠΈ ΠΎΡ ΡΠΎΡΡΠ°Π²Π° ΡΠ»Π΅ΠΊΡΡΠΎΠ»ΠΈΡΠ° ΠΎΡ 10 Π΄ΠΎ 25 ΠΌΠΊΠΌ/Ρ. Π₯ΠΈΠΌΠΈΡΠ΅ΡΠΊΠΎΠ΅ Π½ΠΈΠΊΠ΅Π»ΠΈΡΠΎΠ²Π°Π½ΠΈΠ΅ ΠΏΡΠΎΠ²ΠΎΠ΄ΡΡ Π² ΠΏΡΠΎΡΠΎΡΠ½ΡΡ
ΠΈ Π½Π΅ΠΏΡΠΎΡΠΎΡΠ½ΡΡ
ΡΠ°ΡΡΠ²ΠΎΡΠ°Ρ
. Π ΠΏΡΠΎΡΠΎΡΠ½ΡΡ
ΡΠ°ΡΡΠ²ΠΎΡΠ°Ρ
ΠΏΠΎΡΡΠΎΡΠ½ΡΡΠ²ΠΎ ΡΠΎΡΡΠ°Π²Π° ΠΏΠΎΠ΄Π΄Π΅ΡΠΆΠΈΠ²Π°Π΅ΡΡΡ ΠΏΡΠΈ ΠΏΠΎΠΌΠΎΡΠΈ ΡΠΈΡΠΊΡΠ»ΡΡΠΈΠΈ ΡΠ°ΡΡΠ²ΠΎΡΠ° ΠΏΠΎ Π·Π°ΠΌΠΊΠ½ΡΡΠΎΠΌΡ ΡΠΈΠΊΠ»Ρ: ΠΈΠ· ΡΠ΅Π°ΠΊΡΠΎΡΠ°, Π² ΠΊΠΎΡΠΎΡΠΎΠΌ ΠΏΡΠΎΠΈΡΡ
ΠΎΠ΄ΠΈΡ ΠΎΡΠ°ΠΆΠ΄Π΅Π½ΠΈΠ΅, Π² ΡΠ΅ΠΏΠ»ΠΎΠΎΠ±ΠΌΠ΅Π½Π½ΠΈΠΊ, Π³Π΄Π΅ ΡΠ°ΡΡΠ²ΠΎΡ ΠΎΡ
Π»Π°ΠΆΠ΄Π°Π΅ΡΡΡ Π΄ΠΎ 55 Β°Π‘, Π·Π°ΡΠ΅ΠΌ Π½Π°ΡΠΎΡΠΎΠΌ ΠΏΠ΅ΡΠ΅ΠΊΠ°ΡΠΈΠ²Π°Π΅ΡΡΡ ΡΠ΅ΡΠ΅Π· ΡΠΈΠ»ΡΡΡ, ΠΎΡΡΡΠ΄Π° ΡΠ°ΠΌΠΎΡΠ΅ΠΊΠΎΠΌ ΡΡΠ΅ΠΊΠ°Π΅Ρ Π² ΠΊΠΎΡΡΠ΅ΠΊΡΠΈΡΠΎΠ²ΠΎΡΠ½ΡΠΉ Π±Π°ΠΊ ΠΈ ΠΏΠΎΡΡΡΠΏΠ°Π΅Ρ Π² ΡΠ΅Π°ΠΊΡΠΎΡ. Π£ΡΡΠ°Π½ΠΎΠ²ΠΊΠ° ΡΠ½Π°Π±ΠΆΠ΅Π½Π° ΠΏΡΠΈΠ±ΠΎΡΠ°ΠΌΠΈ Π°Π²ΡΠΎΠΌΠ°ΡΠΈΡΠ΅ΡΠΊΠΎΠ³ΠΎ ΡΠ΅Π³ΡΠ»ΠΈΡΠΎΠ²Π°Π½ΠΈΡ ΡΠ ΠΈ ΡΠ΅ΠΌΠΏΠ΅ΡΠ°ΡΡΡΡ.
Β
2. ΠΠΈΠ½Π΅ΡΠΈΠΊΠ° ΠΏΡΠΎΡΠ΅ΡΡΠ° Ρ ΠΈΠΌΠΈΡΠ΅ΡΠΊΠΎΠ³ΠΎ Π½ΠΈΠΊΠ΅Π»ΠΈΡΠΎΠ²Π°Π½ΠΈΡ.
ΠΠ° ΡΠΈΡΡΠ½ΠΊΠ΅ 1 (Π° ΠΈ Π±) ΠΏΡΠΈΠ²Π΅Π΄Π΅Π½Π° Π΄ΠΈΠ°Π³ΡΠ°ΠΌΠΌΠ° Π-ΡΠ (Π — ΠΎΠΊΠΈΡΠ»ΠΈΡΠ΅Π»ΡΠ½ΠΎ-Π²ΠΎΡΡΡΠ°Π½ΠΎΠ²ΠΈΡΠ΅Π»ΡΠ½ΡΠΉ ΠΏΠΎΡΠ΅Π½ΡΠΈΠ°Π» ΡΠΈΡΡΠ΅ΠΌΡ). ΠΠΈΠ½ΠΈΠΈ Π½Π° Π΄ΠΈΠ°Π³ΡΠ°ΠΌΠΌΠ΅ ΠΎΡΡΠ°ΠΆΠ°ΡΡ ΡΠ°Π²Π½ΠΎΠ²Π΅ΡΠΈΡ ΠΎΠΏΡΠ΅Π΄Π΅Π»Π΅Π½Π½ΡΡ ΠΠ ΡΠ΅Π°ΠΊΡΠΈΠΉ Π² Π·Π°Π²ΠΈΡΠΈΠΌΠΎΡΡΠΈ ΠΎΡ ΡΠ ΡΠ°ΡΡΠ²ΠΎΡΠ°. ΠΠ° Π΄ΠΈΠ°Π³ΡΠ°ΠΌΠΌΡ Π½Π°Π½Π΅ΡΠ΅Π½Ρ ΡΠΎΡΡΠΎΡΠ½ΠΈΡ Π½ΠΈΠΊΠ΅Π»Ρ (ΡΠΈΡΡΠ½ΠΎΠΊ 1Π°), ΡΠΈΡΡΠ°ΡΠ½ΠΎΠ³ΠΎ ΠΊΠΎΠΌΠΏΠ»Π΅ΠΊΡΠ° Π½ΠΈΠΊΠ΅Π»Ρ (ΡΠΈΡΡΠ½ΠΎΠΊ 1Π±) ΠΈ Π³ΠΈΠΏΠΎΡΠΎΡΡΠΈΡΠ°, ΠΎΡΠ²Π΅ΡΠ°ΡΡΠΈΠ΅ ΡΠ°Π²Π½ΠΎΠ²Π΅ΡΠ½ΡΠΌ ΡΠ΅Π°ΠΊΡΠΈΡΠΌ, ΠΏΡΠΈΠ²Π΅Π΄Π΅Π½Π½ΡΠΌ Π² ΡΠ°Π±Π»ΠΈΡΠ΅ 2.
ΠΠ° ΡΠΈΡΡΠ½ΠΊΠ°Ρ
1Π° ΠΈ
1Π± Π·Π°ΡΡΡΠΈΡ
ΠΎΠ²Π°Π½Π° ΠΎΠ±Π»Π°ΡΡΡ, Π² ΠΊΠΎΡΠΎΡΠΎΠΉ Π½ΠΈΠΊΠ΅Π»Ρ Π½Π°Ρ
ΠΎΠ΄ΠΈΡΡΡ Π² Π²ΠΎΡΡΡΠ°Π½ΠΎΠ²Π»Π΅Π½Π½ΠΎΠΌ
(ΠΌΠ΅ΡΠ°Π»Π»ΠΈΡΠ΅ΡΠΊΠΎΠΌ) ΡΠΎΡΡΠΎΡΠ½ΠΈΠΈ, Π² Π³ΠΈΠΏΠΎΡΠΎΡΡΠΈΡ — Π² ΠΎΠΊΠΈΡΠ»Π΅Π½Π½ΠΎΠΌ, Ρ. Π΅. ΠΎΠ±Π»Π°ΡΡΡ
Π²ΠΎΠ·ΠΌΠΎΠΆΠ½ΠΎΠ³ΠΎ ΠΏΡΠΎΡΠ΅ΠΊΠ°Π½ΠΈΡ ΡΠ΅Π°ΠΊΡΠΈΠΉ Π₯ΠΠ. Π‘ΡΠ°Π²Π½Π΅Π½ΠΈΠ΅ ΡΠΈΡΡΠ½ΠΊΠΎΠ² ΠΏΠΎΠΊΠ°Π·ΡΠ²Π°Π΅Ρ, ΡΡΠΎ Π²
ΠΏΡΠΈΡΡΡΡΡΠ²ΠΈΠΈ Π»ΠΈΠ³Π°Π½Π΄Π° (ΡΠΈΡΡΠ°Ρ-ΠΈΠΎΠ½Π°) ΠΈΡΡΠ΅Π·Π°ΡΡ ΠΎΠΊΡΠΈΠ΄Π½ΡΠ΅ ΡΠΎΠ΅Π΄ΠΈΠ½Π΅Π½ΠΈΡ Π½ΠΈΠΊΠ΅Π»Ρ, Π°
ΠΎΠ±Π»Π°ΡΡΡ ΠΏΡΠΎΡΠ΅ΠΊΠ°Π½ΠΈΡ ΡΠ΅Π°ΠΊΡΠΈΠΈ Π·Π°ΠΌΠ΅ΡΠ½ΠΎ ΡΠ°ΡΡΠΈΡΡΠ΅ΡΡΡ ΠΊΠ°ΠΊ ΠΏΠΎ ΠΏΠΎΡΠ΅Π½ΡΠΈΠ°Π»Π°ΠΌ, ΡΠ°ΠΊ ΠΈ
ΠΏΠΎ ΠΈΠ½ΡΠ΅ΡΠ²Π°Π»Π°ΠΌ ΡΠ.
aΒ Β Β Β Β Β Β Β Β Β Β Β Β Β Β Β Β Β Β Β Β Β Β Β Β Β Β Β Β Β Β Β Β Β Β Β Β Β Β Β Β Β Β Β Β Β Β Β Β Β Β Β Β Β Β Β Β Β Β Β Β Β Β Β Β Β Β Β Β Β Β Β Β Π±
Π ΠΈΡΡΠ½ΠΎΠΊ 1 — ΠΠΈΠ°Π³ΡΠ°ΠΌΠΌΠ° Π-ΡΠ: Π° — Π΄Π»Ρ ΡΠΈΡΡΠ΅ΠΌΡ Π½ΠΈΠΊΠ΅Π»Ρ — Π²ΠΎΠ΄Π°,Β Π³ΠΈΠΏΠΎΡΠΎΡΡΠΈΡ-Π²ΠΎΠ΄Π°, Π± - Π΄Π»Ρ ΡΠΈΡΡΠ΅ΠΌΡ Π½ΠΈΠΊΠ΅Π»Ρ — Π²ΠΎΠ΄Π°, ΡΠΈΡΡΠ°ΡΠ½ΡΠΉ ΠΊΠΎΠΌΠΏΠ»Π΅ΠΊΡ Π½ΠΈΠΊΠ΅Π»Ρ — Π²ΠΎΠ΄Π°,Β Π³ΠΈΠΏΠΎΡΠΎΡΡΠΈΡ-Π²ΠΎΠ΄Π°. ΠΠΎΠΌΠ΅ΡΠ° ΠΊΡΠΈΠ²ΡΡ Π½Π° Π΄ΠΈΠ°Π³ΡΠ°ΠΌΠΌΠ΅ ΡΠΎΠΎΡΠ²Π΅ΡΡΡΠ²ΡΡΡΒ Π½ΠΎΠΌΠ΅ΡΠ°ΠΌΒ ΡΠ°Π²Π½ΠΎΠ²Π΅ΡΠΈΠΉ Π² ΡΠ°Π±Π». 2 ΡΠΎΡΡΠΎΡΠ½ΠΈΡ Π½ΠΈΠΊΠ΅Π»Ρ (1 — 9) ΠΈ ΡΠΎΡΡΠΎΡΠ½ΠΈΡ Π³ΠΈΠΏΠΎΡΠΎΡΡΠΈΡΠ° (10-14).
Π’Π°ΠΊΠΈΠΌ ΠΎΠ±ΡΠ°Π·ΠΎΠΌ, Π΄Π»Ρ ΠΎΡΠ³Π°Π½ΠΈΠ·Π°ΡΠΈΠΈ ΠΏΡΠΎΡΠ΅ΡΡΠ° Π₯ΠΠ ΡΡΠ΅Π±ΡΠ΅ΡΡΡ ΠΊΠ°ΠΊ ΠΌΠΈΠ½ΠΈΠΌΡΠΌ ΡΠΎΠ»Ρ ΠΎΡΠ°ΠΆΠ΄Π°Π΅ΠΌΠΎΠ³ΠΎ ΠΌΠ΅ΡΠ°Π»Π»Π°, Π»ΠΈΠ³Π°Π½Π΄, Π²ΠΎΡΡΡΠ°Π½ΠΎΠ²ΠΈΡΠ΅Π»Ρ ΠΈ ΡΠ΅Π»ΠΎΡΡ.
Π
ΡΠ²ΡΠ·ΠΈ Ρ ΡΠ΅ΠΌ, ΡΡΠΎ Π²Π΅Π»ΠΈΡΠΈΠ½Π° ΡΠ ΡΡΡΠ΅ΡΡΠ²Π΅Π½Π½ΠΎ Π²Π»ΠΈΡΠ΅Ρ ΠΊΠ°ΠΊ Π½Π° ΡΠ΅ΡΠΌΠΎΠ΄ΠΈΠ½Π°ΠΌΠΈΠΊΡ,
ΡΠ°ΠΊ ΠΈ Π½Π° ΠΊΠΈΠ½Π΅ΡΠΈΠΊΡ ΠΏΡΠΎΡΠ΅ΡΡΠ°, Π² ΡΠΎΡΡΠ°Π² ΡΠ°ΡΡΠ²ΠΎΡΠ° Π₯ΠΠ, ΠΊΠ°ΠΊ ΠΏΡΠ°Π²ΠΈΠ»ΠΎ, Π²Π²ΠΎΠ΄ΠΈΡΡΡ
Π±ΡΡΠ΅ΡΠ½Π°Ρ Π΄ΠΎΠ±Π°Π²ΠΊΠ°.
Π Π΅Π°ΠΊΡΠΈΠΈ Π₯ΠΠ ΠΈΠΌΠ΅ΡΡ ΡΠΎΠΏΠΎΡ
ΠΈΠΌΠΈΡΠ΅ΡΠΊΠΈΠΉ Ρ
Π°ΡΠ°ΠΊΡΠ΅Ρ,
Ρ.Π΅. ΠΏΡΠΎΡΠ΅ΠΊΠ°ΡΡ Π½Π° Π³ΡΠ°Π½ΠΈΡΠ΅ ΡΠ°Π·Π΄Π΅Π»Π° ΡΠ°Π·: ΠΏΡΠΎΠ΄ΡΠΊΡ ΡΠ΅Π°ΠΊΡΠΈΠΈ (ΠΌΠ΅ΡΠ°Π»Π»ΠΎΠΏΠΎΠΊΡΡΡΠΈΠ΅)
— ΡΠ΅Π°ΠΊΡΠΈΠΎΠ½Π½Π°Ρ ΡΡΠ΅Π΄Π°.
Β
ΠΡΠ΅ ΠΎΠ΄Π½Π° Π²Π°ΠΆΠ½Π°Ρ ΠΎΡΠΎΠ±Π΅Π½Π½ΠΎΡΡΡ, Π±Π΅Π· ΠΊΠΎΡΠΎΡΠΎΠΉ Π½Π΅Π²ΠΎΠ·ΠΌΠΎΠΆΠ½ΠΎ Π΄Π»ΠΈΡΠ΅Π»ΡΠ½ΠΎΠ΅ ΠΏΡΠΎΡΠ΅ΠΊΠ°Π½ΠΈΠ΅ ΡΠ΅Π°ΠΊΡΠΈΠΈ Π₯ΠΠ β Π°Π²ΡΠΎΠΊΠ°ΡΠ°Π»ΠΈΡΠΈΡΠ΅ΡΠΊΠΈΠΉ Ρ Π°ΡΠ°ΠΊΡΠ΅Ρ ΠΏΡΠΎΡΠ΅ΡΡΠ°, Ρ. Π΅. ΡΠΏΠΎΡΠΎΠ±Π½ΠΎΡΡΡ ΠΎΡΠ°ΠΆΠ΄Π°Π΅ΠΌΠΎΠ³ΠΎ ΠΌΠ΅ΡΠ°Π»Π»Π° ΠΊΠ°ΡΠ°Π»ΠΈΠ·ΠΈΡΠΎΠ²Π°ΡΡ ΠΏΡΠΎΡΠ΅ΡΡ Π²ΠΎΡΡΡΠ°Π½ΠΎΠ²Π»Π΅Π½ΠΈΡ.
Π’Π°Π±Π»ΠΈΡΠ° 2 — Π£ΡΠ°Π²Π½Π΅Π½ΠΈΡ, ΠΎΠΏΠΈΡΡΠ²Π°ΡΡΠΈΠ΅ ΡΠ°Π²Π½ΠΎΠ²Π΅ΡΠΈΡ Π² ΡΠΈΡΡΠ΅ΠΌΠ°Ρ Π½ΠΈΠΊΠ΅Π»Ρ — Π²ΠΎΠ΄Π° ΠΈ Π³ΠΈΠΏΠΎΡΠΎΡΡΠΈΡ-Π²ΠΎΠ΄Π°.
β |
Π Π°Π²Π½ΠΎΠ²Π΅ΡΠΈΠ΅ |
Π£ΡΠ°Π²Π½Π΅Π½ΠΈΠ΅, ΠΎΠΏΠΈΡΡΠ²Π°ΡΡΠ΅Π΅ ΡΠ°Π²Π½ΠΎΠ²Π΅ΡΠΈΠ΅ |
1 |
Ni2++2e + Ni |
E=-0,250+0,0295lg[Ni2+] |
2 |
Ni(OH)2+2H++2e =Ni+2H2O |
E=0,110-0,059lgpH |
3 |
Ni3O4+2H2O+2H++2e=3Ni(OH)2 |
E=0,897-0,059lgpH |
4 |
Ni3O4+H++2e=3Ni2++4H2O |
E=1,977-0,264pH-0,08861lg[Ni2+] |
5 |
2Ni2O3+2H++2e=2Ni3O4+H2O |
E=1,305 — 0,059 pH |
6 |
2NiO2+2H++2e=Ni2O3+H2O |
E=1,434 — 0,059 pH |
7 |
Ni(OH)2+2H+=Ni2++2H2O |
lg[Ni2+] = 12,18 — 2 pH |
8 |
NiO2+4H++2e=Ni2++2H2O |
E=1,593-0,118pH-0,0295lg[Ni2+] |
9 |
[NiCit]—+2e=Ni+Cit3- |
E=-0,37+0,295lg [NiCit—/Cit3-] |
10 |
H2PO3—+2H++2e=H2PO2—+H2O |
E=-0,31 — 0,059 pH |
11 |
HPO32-+3H++2e=H2PO3—+H2O |
E=-0,276 — 0,87 pH |
12 |
H2PO4—+2H++2e=H2PO3—+H2O |
E=-0,26-0,059pH+0,0295lg [H2PO4—]/[H2PO3—] |
13 |
HPO42-+2H++2e=HPO32-+H2O |
E=0,234-0,059pH+0,0295lg [HPO42-]/[HPO32-] |
14 |
PO43-+2H2O+2e=HPO32-+3OH— |
E=0,14 — 0,087 pH |
Π Ρ ΠΎΠ΄Π΅ Π₯ΠΠ Π·Π°Π²ΠΈΡΠΈΠΌΠΎΡΡΡ ΠΌΠ΅ΠΆΠ΄Ρ ΠΌΠ°ΡΡΠΎΠΉ ΠΏΠΎΠ»ΡΡΠ°Π΅ΠΌΠΎΠ³ΠΎ ΠΌΠ΅ΡΠ°Π»Π»Π° ΠΈ Π²ΡΠ΅ΠΌΠ΅Π½Π΅ΠΌ ΠΎΡΠ°ΠΆΠ΄Π΅Π½ΠΈΡ ΠΈΠΌΠ΅Π΅Ρ ΡΠ»ΠΎΠΆΠ½ΡΠΉ Π²ΠΈΠ΄ (ΡΠΈΡΡΠ½ΠΎΠΊ 2). ΠΠΎΡΠ»Π΅ ΠΏΠΎΠ³ΡΡΠΆΠ΅Π½ΠΈΡ Π΄Π΅ΡΠ°Π»ΠΈ Π² ΡΠ°ΡΡΠ²ΠΎΡ Π² ΡΠ΅ΡΠ΅Π½ΠΈΠ΅ Π½Π΅ΠΊΠΎΡΠΎΡΠΎΠ³ΠΎ Π²ΡΠ΅ΠΌΠ΅Π½ΠΈ ΠΎΡΡΡΡΡΡΠ²ΡΡΡ Π²Π½Π΅ΡΠ½ΠΈΠ΅ ΠΏΡΠΈΠ·Π½Π°ΠΊΠΈ ΠΏΡΠΎΡΠ΅ΠΊΠ°Π½ΠΈΡ ΡΠ΅Π°ΠΊΡΠΈΠΈ (ΡΡΠ°ΡΡΠΎΠΊ 1). ΠΠΈΠ΄ΠΈΠΌΠΎΠ΅ ΠΏΡΠΎΡΠ΅ΠΊΠ°Π½ΠΈΠ΅ ΡΠ΅Π°ΠΊΡΠΈΠΈ Π₯ΠΠ Π½Π°ΡΠΈΠ½Π°Π΅ΡΡΡ Ρ Π½Π΅ΠΊΠΎΡΠΎΡΠΎΠ³ΠΎ ΠΌΠΎΠΌΠ΅Π½ΡΠ° Ξ€0.
Π ΠΈΡΡΠ½ΠΎΠΊ 2. ΠΠ°Π²ΠΈΡΠΈΠΌΠΎΡΡΡ ΠΌΠ°ΡΡΡ ΠΎΡΠ°ΠΆΠ΄Π°Π΅ΠΌΠΎΠ³ΠΎ ΠΌΠ΅ΡΠ°Π»Π»Π° ΠΎΡ Π²ΡΠ΅ΠΌΠ΅Π½ΠΈ (ΠΏΠΎΡΡΠ½Π΅Π½ΠΈΡ Π² ΡΠ΅ΠΊΡΡΠ΅).
ΠΡΡΠ΅Π·ΠΎΠΊ Π²ΡΠ΅ΠΌΠ΅Π½ΠΈ ΠΌΠ΅ΠΆΠ΄Ρ 0 ΠΈ Ξ€0 Π½ΠΎΡΠΈΡ Π½Π°Π·Π²Π°Π½ΠΈΠ΅ ΠΈΠ½Π΄ΡΠΊΡΠΈΠΎΠ½Π½ΠΎΠ³ΠΎ ΠΏΠ΅ΡΠΈΠΎΠ΄Π°. ΠΡΠΎ Π²ΡΠ΅ΠΌΡ, Π½Π΅ΠΎΠ±Ρ ΠΎΠ΄ΠΈΠΌΠΎΠ΅ Π΄Π»Ρ ΡΠΎΠ³ΠΎ, ΡΡΠΎΠ±Ρ ΠΎΠ±ΡΠ°Π·ΠΎΠ²Π°Π»ΠΈΡΡ ΡΡΡΠΎΠΉΡΠΈΠ²ΡΠ΅ ΠΌΠ°Π»ΡΠ΅ ΡΠ°ΡΡΠΈΡΡ ΡΠ²Π΅ΡΠ΄ΠΎΠ³ΠΎ ΠΏΡΠΎΠ΄ΡΠΊΡΠ°, ΠΎΠ±Π»Π°Π΄Π°ΡΡΠΈΠ΅ ΠΊΠ°ΡΠ°Π»ΠΈΡΠΈΡΠ΅ΡΠΊΠΎΠΉ Π°ΠΊΡΠΈΠ²Π½ΠΎΡΡΡΡ. ΠΠΎΡΠ»Π΅ Π΅Π³ΠΎ ΠΎΠ±ΡΠ°Π·ΠΎΠ²Π°Π½ΠΈΡ ΡΠΊΠΎΡΠΎΡΡΡ ΠΎΡΠ°ΠΆΠ΄Π΅Π½ΠΈΡ Π±ΡΡΡΡΠΎ Π²ΠΎΠ·ΡΠ°ΡΡΠ°Π΅Ρ (ΡΡΠ°ΡΡΠΎΠΊ II). Π’ΠΎΡΠΌΠΎΠΆΠ΅Π½ΠΈΠ΅ ΠΏΡΠΎΡΠ΅ΡΡΠ° (ΡΡΠ°ΡΡΠΎΠΊ III) ΠΎΠ±ΡΡΡΠ½ΡΠ΅ΡΡΡ Π²ΡΡΠ°Π±ΠΎΡΠΊΠΎΠΉ ΡΠ΅Π°Π³Π΅Π½ΡΠΎΠ² Π² ΠΎΠ³ΡΠ°Π½ΠΈΡΠ΅Π½Π½ΠΎΠΌ ΠΎΠ±ΡΡΠΌΠ΅ ΡΠ°ΡΡΠ²ΠΎΡΠ°. ΠΡΠ»ΠΈ ΠΏΡΠΎΠ²ΠΎΠ΄ΠΈΡΡΡ ΠΊΠΎΡΡΠ΅ΠΊΡΠΈΡΠΎΠ²ΠΊΠ° ΡΠ°ΡΡΠ²ΠΎΡΠ°, ΡΠΎΡΠΌΠΎΠΆΠ΅Π½ΠΈΡ ΠΌΠΎΠΆΠ΅Ρ ΠΈ Π½Π΅ Π±ΡΡΡ.
ΠΡΠΎΡΠ΅ΡΡ Π₯ΠΠ ΠΌΠΎΠΆΠ΅Ρ Π±ΡΡΡ ΠΎΡΠ³Π°Π½ΠΈΠ·ΠΎΠ²Π°Π½
ΠΊΠ°ΠΊ ΠΎΠ΄Π½ΠΎΠΊΡΠ°ΡΠ½ΡΠΉ ΠΈΠ»ΠΈ ΠΊΠ°ΠΊ Π½Π΅ΠΏΡΠ΅ΡΡΠ²Π½ΡΠΉ. Π ΠΏΠ΅ΡΠ²ΠΎΠΌ ΡΠ»ΡΡΠ°Π΅ ΠΏΡΠΎΡΠ΅ΡΡ Π²Π΅Π΄Π΅ΡΡΡ Π²
ΠΎΠ³ΡΠ°Π½ΠΈΡΠ΅Π½Π½ΠΎΠΌ ΠΎΠ±ΡΠ΅ΠΌΠ΅ ΡΠ°ΡΡΠ²ΠΎΡΠ° Π±Π΅Π· ΠΊΠΎΡΡΠ΅ΠΊΡΠΈΡΠΎΠ²ΠΊΠΈ ΠΏΠΎ ΠΎΡΠ½ΠΎΠ²Π½ΡΠΌ ΠΊΠΎΠΌΠΏΠΎΠ½Π΅Π½ΡΠ°ΠΌ; Π²
ΡΠ΅Π·ΡΠ»ΡΡΠ°ΡΠ΅ ΠΈΡ
Π²ΡΡΠ°Π±ΠΎΡΠΊΠΈ ΡΠΊΠΎΡΠΎΡΡΡ ΡΠ΅Π°ΠΊΡΠΈΠΈ ΠΏΠΎΡΡΠ΅ΠΏΠ΅Π½Π½ΠΎ ΠΏΠ°Π΄Π°Π΅Ρ, ΡΠ°ΡΡΠ²ΠΎΡ
ΠΏΡΠΈΡ
ΠΎΠ΄ΠΈΡ Π² Π½Π΅Π³ΠΎΠ΄Π½ΠΎΡΡΡ. Π ΡΡΠΎΠΌ ΡΠ»ΡΡΠ°Π΅ Π΄Π»Ρ Ρ
Π°ΡΠ°ΠΊΡΠ΅ΡΠΈΡΡΠΈΠΊΠΈ ΡΠ°ΡΡΠ²ΠΎΡΠΎΠ² Π²Π²ΠΎΠ΄ΡΡ
ΡΠ΅ΡΠΌΠΈΠ½ βΠΊΠΎΡΡΡΠΈΡΠΈΠ΅Π½Ρ ΠΈΡΠΏΠΎΠ»ΡΠ·ΠΎΠ²Π°Π½ΠΈΡβ, Ρ. Π΅. ΠΎΡΠ½ΠΎΡΠ΅Π½ΠΈΠ΅ ΡΠΎΠ³ΠΎ ΠΊΠΎΠ»ΠΈΡΠ΅ΡΡΠ²Π°
ΠΌΠ΅ΡΠ°Π»Π»Π°, ΠΊΠΎΡΠΎΡΠΎΠ΅ ΡΠ΅Π°Π»ΡΠ½ΠΎ ΠΎΡΠ°Π΄ΠΈΠ»ΠΎΡΡ ΠΈΠ· Π΄Π°Π½Π½ΠΎΠ³ΠΎ ΡΠ°ΡΡΠ²ΠΎΡΠ°, ΠΊΠΎ Π²ΡΠ΅ΠΌΡ
ΠΊΠΎΠ»ΠΈΡΠ΅ΡΡΠ²Ρ ΠΌΠ΅ΡΠ°Π»Π»Π°, ΡΠΎΠ΄Π΅ΡΠΆΠ°ΡΠ΅ΠΌΡΡΡ Π² ΡΠ°ΡΡΠ²ΠΎΡΠ΅. ΠΠΎ Π½Π΅Π΄Π°Π²Π½Π΅Π³ΠΎ Π²ΡΠ΅ΠΌΠ΅Π½ΠΈ
ΠΎΠ΄Π½ΠΎΠΊΡΠ°ΡΠ½Π°Ρ ΠΎΡΠ³Π°Π½ΠΈΠ·Π°ΡΠΈΡ ΠΏΡΠΎΡΠ΅ΡΡΠ° ΠΈΡΠΏΠΎΠ»ΡΠ·ΠΎΠ²Π°Π»Π°ΡΡ ΠΏΠΎΠ²ΡΠ΅ΠΌΠ΅ΡΡΠ½ΠΎ. ΠΠΎΠ»Π΅Π΅
ΠΏΡΠΎΠ³ΡΠ΅ΡΡΠΈΠ²Π½ΡΠΌ ΡΠ²Π»ΡΠ΅ΡΡΡΒ Π½Π΅ΠΏΡΠ΅ΡΡΠ²Π½ΡΠΉ ΠΏΡΠΎΡΠ΅ΡΡ, ΠΊΠΎΠ³Π΄Π° ΠΏΡΠΎΠ²ΠΎΠ΄ΠΈΡΡΡ
ΠΏΠ΅ΡΠΈΠΎΠ΄ΠΈΡΠ΅ΡΠΊΠ°Ρ ΠΈΠ»ΠΈ Π½Π΅ΠΏΡΠ΅ΡΡΠ²Π½Π°ΡΒ ΠΊΠΎΡΡΠ΅ΠΊΡΠΈΡΠΎΠ²ΠΊΠ° ΡΠ°ΡΡΠ²ΠΎΡΠ° ΠΏΠΎ ΡΠ°ΡΡ
ΠΎΠ΄ΡΠ΅ΠΌΡΠΌ
ΡΠ΅Π°Π³Π΅Π½ΡΠ°ΠΌ. Π ΡΡΠΎΠΌ ΡΠ»ΡΡΠ°Π΅ ΡΡΠΎΠΊ ΡΠ»ΡΠΆΠ±Ρ ΡΠ°ΡΡΠ²ΠΎΡΠ° ΠΌΠΎΠΆΠ΅Ρ Π±ΡΡΡ ΠΏΡΠΎΠ΄Π»Π΅Π½ Π΄ΠΎ
Π½Π΅ΡΠΊΠΎΠ»ΡΠΊΠΈΡ
Π½Π΅Π΄Π΅Π»Ρ, Π° Π² ΠΈΠ΄Π΅Π°Π»Π΅ — ΠΈ ΠΌΠ΅ΡΡΡΠ΅Π². ΠΠ΅ΠΏΡΠ΅ΠΌΠ΅Π½Π½ΡΠΌ ΡΡΠ»ΠΎΠ²ΠΈΠ΅ΠΌ
ΡΡΡΠ΅ΡΡΠ²ΠΎΠ²Π°Π½ΠΈΡ ΡΠ°ΠΊΠΈΡ
ΡΠ°ΡΡΠ²ΠΎΡΠΎΠ² ΡΠ²Π»ΡΠ΅ΡΡΡ ΠΏΡΠΈΡΡΡΡΡΠ²ΠΈΠ΅ Π΅ΡΠ΅ ΠΎΠ΄Π½ΠΎΠ³ΠΎ ΠΊΠ»Π°ΡΡΠ°
ΠΊΠΎΠΌΠΏΠΎΠ½Π΅Π½ΡΠΎΠ² ΡΠ°ΡΡΠ²ΠΎΡΠ° — ΡΡΠ°Π±ΠΈΠ»ΠΈΠ·Π°ΡΠΎΡΠΎΠ².
Β
Π‘ΡΠ°Π±ΠΈΠ»ΠΈΠ·Π°ΡΠΎΡΡ — ΡΡΠΎ Π²Π΅ΡΠ΅ΡΡΠ²Π°, ΠΏΡΠ΅Π΄ΠΎΡΠ²ΡΠ°ΡΠ°ΡΡΠΈΠ΅ ΡΠΏΠΎΠ½ΡΠ°Π½Π½ΠΎΠ΅ ΠΏΡΠΎΡΠ΅ΠΊΠ°Π½ΠΈΠ΅ ΡΠ΅Π°ΠΊΡΠΈΠΈ Π² ΠΎΠ±ΡΠ΅ΠΌΠ΅ ΡΠ°ΡΡΠ²ΠΎΡΠ°, Π±Π»Π°Π³ΠΎΠ΄Π°ΡΡ ΡΠ΅ΠΌΡ ΡΠ΄Π»ΠΈΠ½ΡΠ΅ΡΡΡ ΡΡΠΎΠΊ ΡΠ»ΡΠΆΠ±Ρ ΡΠ°ΡΡΠ²ΠΎΡΠ°. ΠΠ½ΠΈ Π²Π²ΠΎΠ΄ΡΡΡΡ Π² ΡΠ°ΡΡΠ²ΠΎΡ, ΠΊΠ°ΠΊ ΠΏΡΠ°Π²ΠΈΠ»ΠΎ, Π² Π²Π΅ΡΡΠΌΠ° ΠΌΠ°Π»ΡΡ ΠΊΠΎΠ½ΡΠ΅Π½ΡΡΠ°ΡΠΈΡΡ . ΠΡΠΎΠ±Π΅Π½Π½ΠΎΡΡΡΡ Π΄Π΅ΠΉΡΡΠ²ΠΈΡ ΡΡΠ°Π±ΠΈΠ»ΠΈΠ·ΠΈΡΡΡΡΠΈΡ Π΄ΠΎΠ±Π°Π²ΠΎΠΊ ΡΠ²Π»ΡΠ΅ΡΡΡ ΡΠΎ, ΡΡΠΎ ΠΎΠ½ΠΈ ΡΠΎΡΠΌΠΎΠ·ΡΡ ΠΎΠ±ΡΠ°Π·ΠΎΠ²Π°Π½ΠΈΠ΅ Π·Π°ΡΠΎΠ΄ΡΡΠ΅ΠΉ ΠΌΠ΅ΡΠ°Π»Π»ΠΈΡΠ΅ΡΠΊΠΎΠΉ ΡΠ°Π·Ρ Π½Π° Π½Π°ΡΠ°Π»ΡΠ½ΠΎΠΉ ΡΡΠ°Π΄ΠΈΠΈ ΠΈΡ ΠΎΠ±ΡΠ°Π·ΠΎΠ²Π°Π½ΠΈΡ, Π² ΠΎΡΠΎΠ±Π΅Π½Π½ΠΎΡΡΠΈ Π² ΠΎΠ±ΡΠ΅ΠΌΠ΅ ΡΠ°ΡΡΠ²ΠΎΡΠ°. Π‘ΡΠ°Π±ΠΈΠ»ΠΈΠ·Π°ΡΠΎΡΠ°ΠΌΠΈ ΠΌΠΎΠ³ΡΡ ΡΠ²Π»ΡΡΡΡΡ Π²Π΅ΡΠ΅ΡΡΠ²Π° ΡΠ°ΠΌΠΎΠΉ ΡΠ°Π·Π½ΠΎΠΉ ΠΏΡΠΈΡΠΎΠ΄Ρ: ΠΠΠ, ΡΠ΅ΡΠΎ- ΠΈ ΡΠ΅Π»Π΅Π½ΡΠΎΠ΄Π΅ΡΠΆΠ°ΡΠΈΠ΅ ΡΠΎΠ΅Π΄ΠΈΠ½Π΅Π½ΠΈΡ, ΡΠΎΠ»ΠΈ ΡΡΠΆΠ΅Π»ΡΡ ΠΌΠ΅ΡΠ°Π»Π»ΠΎΠ², ΡΠ»Π°Π±ΡΠ΅ ΠΎΠΊΠΈΡΠ»ΠΈΡΠ΅Π»ΠΈ, ΠΊΠΎΠΌΠΏΠ»Π΅ΠΊΡΠΎΠΎΠ±ΡΠ°Π·ΠΎΠ²Π°ΡΠ΅Π»ΠΈ ΠΈ Π΄Ρ. Π‘ΠΎΠΎΡΠ²Π΅ΡΡΡΠ²Π΅Π½Π½ΠΎ ΠΈ ΠΌΠ΅Ρ Π°Π½ΠΈΠ·ΠΌ ΠΈΡ Π΄Π΅ΠΉΡΡΠ²ΠΈΡ ΠΌΠΎΠΆΠ΅Ρ Π±ΡΡΡ ΡΠ°Π·Π»ΠΈΡΠ½ΡΠΌ, Π½Π°ΠΏΡΠΈΠΌΠ΅Ρ, ΡΠ²ΡΠ·ΡΠ²Π°Π½ΠΈΠ΅ Π² ΠΊΠΎΠΌΠΏΠ»Π΅ΠΊΡ ΠΈΠ»ΠΈ ΠΎΠΊΠΈΡΠ»Π΅Π½ΠΈΠ΅ ΠΏΡΠΎΠ΄ΡΠΊΡΠΎΠ², Π²ΡΠΏΠ°Π΄Π°ΡΡΠΈΡ Π² ΠΎΡΠ°Π΄ΠΎΠΊ. Π§Π°ΡΠ΅ Π²ΡΠ΅Π³ΠΎ Π΄Π΅ΠΉΡΡΠ²ΠΈΠ΅ ΡΡΠ°Π±ΠΈΠ»ΠΈΠ·Π°ΡΠΎΡΠΎΠ² ΠΎΠ±ΡΡΡΠ½ΡΡΡ ΠΈΡ Π°Π΄ΡΠΎΡΠ±ΡΠΈΠ΅ΠΉ Π½Π° ΠΏΠΎΠ²Π΅ΡΡ Π½ΠΎΡΡΠΈ ΡΠ°ΡΡΠΈΡ Π² ΠΎΠ±ΡΡΠΌΠ΅ ΡΠ°ΡΡΠ²ΠΎΡΠ° ΠΈ Π½Π° ΠΏΠΎΠΊΡΡΠ²Π°Π΅ΠΌΠΎΠΉ ΠΏΠΎΠ²Π΅ΡΡ Π½ΠΎΡΡΠΈ. ΠΡΠΈ ΡΠ΄Π°ΡΠ½ΠΎΠΌ ΠΏΠΎΠ΄Π±ΠΎΡΠ΅ ΡΡΠ°Π±ΠΈΠ»ΠΈΠ·Π°ΡΠΎΡΠΎΠ² ΠΎΠ½ΠΈ ΠΏΠΎΠ»Π½ΠΎΡΡΡΡ ΡΠΎΡΠΌΠΎΠ·ΡΡ ΡΠ΅Π°ΠΊΡΠΈΡ Π² ΠΎΠ±ΡΡΠΌΠ΅ ΠΈ Π»ΠΈΡΡ ΡΠ°ΡΡΠΈΡΠ½ΠΎ ΡΠ½ΠΈΠΆΠ°ΡΡ ΡΠΊΠΎΡΠΎΡΡΡ ΡΠ΅Π°ΠΊΡΠΈΠΈ Π½Π° ΡΠ°Π±ΠΎΡΠ΅ΠΉ ΠΏΠΎΠ²Π΅ΡΡ Π½ΠΎΡΡΠΈ. ΠΠ°ΠΈΠ±ΠΎΠ»ΡΡΠ΅Π³ΠΎ ΡΡΡΠ΅ΠΊΡΠ° Π΄ΠΎΠ±ΠΈΠ²Π°ΡΡΡΡ ΠΏΡΠΈ ΠΎΠ΄Π½ΠΎΠ²ΡΠ΅ΠΌΠ΅Π½Π½ΠΎΠΌ ΠΈΡΠΏΠΎΠ»ΡΠ·ΠΎΠ²Π°Π½ΠΈΠΈ Π½Π΅ΡΠΊΠΎΠ»ΡΠΊΠΈΡ ΡΡΠ°Π±ΠΈΠ»ΠΈΠ·Π°ΡΠΎΡΠΎΠ² ΡΠ°Π·Π½ΠΎΠ³ΠΎ ΡΠΈΠΏΠ°.
Β
Β
Π Π½Π°ΡΡΠΎΡΡΠ΅Π΅ Π²ΡΠ΅ΠΌΡ Π΄Π»Ρ ΠΎΠΏΠΈΡΠ°Π½ΠΈΡ ΠΏΡΠΎΡΠ΅ΡΡΠ° Π₯ΠΠ ΠΏΡΠ΅Π΄Π»ΠΎΠΆΠ΅Π½Ρ Π΄Π²Π° ΠΎΡΠ½ΠΎΠ²Π½ΡΡ ΠΌΠ΅Ρ Π°Π½ΠΈΠ·ΠΌΠ°: Ρ ΠΈΠΌΠΈΡΠ΅ΡΠΊΠΈΠΉ ΠΈ ΡΠ»Π΅ΠΊΡΡΠΎΡ ΠΈΠΌΠΈΡΠ΅ΡΠΊΠΈΠΉ. ΠΠ΅ΡΠ²ΡΠΉΒ Π·Π°ΠΊΠ»ΡΡΠ°Π΅ΡΡΡ Π² Ρ ΠΈΠΌΠΈΡΠ΅ΡΠΊΠΎΠΌ Π²Π·Π°ΠΈΠΌΠΎΠ΄Π΅ΠΉΡΡΠ²ΠΈΠΈ Π²ΠΎΡΡΡΠ°Π½ΠΎΠ²ΠΈΡΠ΅Π»Ρ Ρ Π²ΠΎΡΡΡΠ°Π½Π°Π²Π»ΠΈΠ²Π°Π΅ΠΌΡΠΌ ΠΈΠΎΠ½ΠΎΠΌ, ΠΏΡΠΈ ΠΊΠΎΡΠΎΡΠΎΠΌ ΠΏΡΠΎΠΈΡΡ ΠΎΠ΄ΠΈΡ Π½Π΅ΠΏΠΎΡΡΠ΅Π΄ΡΡΠ²Π΅Π½Π½ΡΠΉ ΠΏΠ΅ΡΠ΅Ρ ΠΎΠ΄ ΡΠ»Π΅ΠΊΡΡΠΎΠ½ΠΎΠ² ΠΎΡ ΠΏΠ΅ΡΠ²ΠΎΠ³ΠΎ ΠΊΠΎ Π²ΡΠΎΡΠΎΠΌΡ. ΠΠ»Π΅ΠΊΡΡΠΎΡ ΠΈΠΌΠΈΡΠ΅ΡΠΊΠΈΠΉ ΠΌΠ΅Ρ Π°Π½ΠΈΠ·ΠΌ ΠΏΡΠ΅Π΄ΠΏΠΎΠ»Π°Π³Π°Π΅Ρ ΠΏΡΠΎΡΠ΅ΠΊΠ°Π½ΠΈΠ΅ Π½Π° ΠΊΠ°ΡΠ°Π»ΠΈΡΠΈΡΠ΅ΡΠΊΠΎΠΉ ΠΏΠΎΠ²Π΅ΡΡ Π½ΠΎΡΡΠΈ ΠΎΡΠ΄Π΅Π»ΡΠ½ΡΡ ΡΠ»Π΅ΠΊΡΡΠΎΡ ΠΈΠΌΠΈΡΠ΅ΡΠΊΠΈΡ ΡΠ΅Π°ΠΊΡΠΈΠΉ (Π°Π½ΠΎΠ΄Π½ΠΎΠ³ΠΎ ΠΎΠΊΠΈΡΠ»Π΅Π½ΠΈΡ Π²ΠΎΡΡΡΠ°Π½ΠΎΠ²ΠΈΡΠ΅Π»Ρ ΠΈ ΠΊΠ°ΡΠΎΠ΄Π½ΠΎΠ³ΠΎ Π²ΠΎΡΡΡΠ°Π½ΠΎΠ²Π»Π΅Π½ΠΈΡ ΠΈΠΎΠ½ΠΎΠ² ΠΌΠ΅ΡΠ°Π»Π»Π°) ΠΏΡΡΠ΅ΠΌ ΠΈΡ ΡΠΎΠΏΡΡΠΆΠ΅Π½ΠΈΡ (ΡΠΈΡΡΠ½ΠΎΠΊ 3)
Π ΠΈΡΡΠ½ΠΎΠΊ 3. Π‘ΠΎΠΏΡΡΠΆΠ΅Π½ΠΈΠ΅ ΠΊΠ°ΡΠΎΠ΄Π½ΠΎΠ³ΠΎ ΠΈ Π°Π½ΠΎΠ΄Π½ΠΎΠ³ΠΎ ΠΏΡΠΎΡΠ΅ΡΡΠΎΠ² Π² Ρ ΠΎΠ΄Π΅ Π₯ΠΠ: 1 β ΠΊΠ°ΡΠΎΠ΄Π½ΠΎΠ΅ Π²ΠΎΡΡΡΠ°Π½ΠΎΠ²Π»Π΅Π½ΠΈΠ΅ ΠΌΠ΅ΡΠ°Π»Π»Π°; 2 β Π°Π½ΠΎΠ΄Π½ΠΎΠ΅ ΠΎΠΊΠΈΡΠ»Π΅Π½ΠΈΠ΅ Π²ΠΎΡΡΡΠ°Π½ΠΎΠ²ΠΈΡΠ΅Π»Ρ; ΠΡΠΌ β ΡΠΌΠ΅ΡΠ°Π½Π½ΡΠΉ ΠΏΠΎΡΠ΅Π½ΡΠΈΠ°Π» (|ik|=|ia|).
ΠΠ΅ΡΠ΅Π΄Π°ΡΠ° ΡΠ»Π΅ΠΊΡΡΠΎΠ½ΠΎΠ² ΠΎΡΡΡΠ΅ΡΡΠ²Π»ΡΠ΅ΡΡΡ Ρ ΠΎΠ±ΡΠ·Π°ΡΠ΅Π»ΡΠ½ΡΠΌ ΡΡΠ°ΡΡΠΈΠ΅ΠΌ ΠΏΠΎΠ²Π΅ΡΡ
Π½ΠΎΡΡΠΈ. ΠΠ²ΠΈΠΆΡΡΠ΅ΠΉ ΡΠΈΠ»ΠΎΠΉ ΠΏΡΠΎΡΠ΅ΡΡΠ° ΡΠ²Π»ΡΠ΅ΡΡΡ Π°Π½ΠΎΠ΄Π½ΠΎΠ΅ ΠΎΠΊΠΈΡΠ»Π΅Π½ΠΈΠ΅ Π²ΠΎΡΡΡΠ°Π½ΠΎΠ²ΠΈΡΠ΅Π»Ρ, ΡΠΎΠ·Π΄Π°ΡΡΠ΅Π΅ ΠΎΡΡΠΈΡΠ°ΡΠ΅Π»ΡΠ½ΡΠΉ ΠΏΠΎΡΠ΅Π½ΡΠΈΠ°Π» Π΄Π»Ρ Π²ΠΎΡΡΡΠ°Π½ΠΎΠ²Π»Π΅Π½ΠΈΡ ΠΈΠΎΠ½ΠΎΠ² ΠΌΠ΅ΡΠ°Π»Π»Π°. Π‘ΠΊΠΎΡΠΎΡΡΡ Π²ΡΠ΅Π³ΠΎ ΠΏΡΠΎΡΠ΅ΡΡΠ° ΠΎΠΏΡΠ΅Π΄Π΅Π»ΡΠ΅ΡΡΡ ΡΠΏΠΎΡΠΎΠ±Π½ΠΎΡΡΡΡ Π΄Π°Π½Π½ΠΎΠ³ΠΎ ΠΌΠ΅ΡΠ°Π»Π»Π° ΠΊΠ°ΡΠ°Π»ΠΈΠ·ΠΈΡΠΎΠ²Π°ΡΡ ΠΏΡΠΎΡΠ΅ΡΡ Π°Π½ΠΎΠ΄Π½ΠΎΠ³ΠΎ ΠΎΠΊΠΈΡΠ»Π΅Π½ΠΈΡ Π²ΠΎΡΡΡΠ°Π½ΠΎΠ²ΠΈΡΠ΅Π»Ρ.
Β
ΠΡΠΈ ΡΠΎΠΏΡΡΠΆΠ΅Π½ΠΈΠΈ ΠΊΠ°ΡΠΎΠ΄Π½ΠΎΠ³ΠΎ ΠΈ Π°Π½ΠΎΠ΄Π½ΠΎΠ³ΠΎ ΠΏΡΠΎΡΠ΅ΡΡΠΎΠ² Π² ΠΎΡΡΡΡΡΡΠ²ΠΈΠ΅ Π²Π½Π΅ΡΠ½Π΅Π³ΠΎ ΡΠΎΠΊΠ° Π² ΡΠΈΡΡΠ΅ΠΌΠ΅ ΡΡΡΠ°Π½Π°Π²Π»ΠΈΠ²Π°Π΅ΡΡΡ ΡΡΠ°ΡΠΈΠΎΠ½Π°ΡΠ½ΠΎΠ΅ ΡΠΎΡΡΠΎΡΠ½ΠΈΠ΅, ΠΏΡΠΈ ΠΊΠΎΡΠΎΡΠΎΠΌ Π°Π±ΡΠΎΠ»ΡΡΠ½ΡΠ΅ Π·Π½Π°ΡΠ΅Π½ΠΈΡ ΠΊΠ°ΡΠΎΠ΄Π½ΠΎΠΉ ΠΈ Π°Π½ΠΎΠ΄Π½ΠΎΠΉ ΠΏΠ»ΠΎΡΠ½ΠΎΡΡΠΈ ΡΠΎΠΊΠ° ΡΠ°Π²Π½Ρ:
|ik | = |ia |, Β
ik + ia = 0,
Π° ΠΌΠ΅ΡΠ°Π»Π» ΠΏΡΠΈΠΎΠ±ΡΠ΅ΡΠ°Π΅Ρ ΡΠΌΠ΅ΡΠ°Π½Π½ΡΠΉ ΠΏΠΎΡΠ΅Π½ΡΠΈΠ°Π» ΠΡΠΌ. ΠΡΠ° ΠΏΠ»ΠΎΡΠ½ΠΎΡΡΡ ΡΠΎΠΊΠ° ΠΈ ΠΎΠΏΡΠ΅Π΄Π΅Π»ΡΠ΅Ρ ΡΠΊΠΎΡΠΎΡΡΡ ΡΠ΅Π°ΠΊΡΠΈΠΈ Π₯ΠΠ. ΠΡΠ»ΠΈ ΡΠΊΠΎΡΠΎΡΡΡ ΠΏΡΠΎΡΠ΅ΡΡΠ°, Π½Π°ΠΉΠ΄Π΅Π½Π½Π°Ρ ΠΏΡΠΈ ΡΠΎΠΏΡΡΠΆΠ΅Π½ΠΈΠΈ ΠΏΠΎΠ»ΡΡΠΈΠ·Π°ΡΠΈΠΎΠ½Π½ΡΡ ΠΊΡΠΈΠ²ΡΡ , ΡΠ°Π²Π½Π° ΡΠ΅Π°Π»ΡΠ½ΠΎΠΉ ΡΠΊΠΎΡΠΎΡΡΠΈ ΠΌΠ΅ΡΠ°Π»Π»ΠΈΠ·Π°ΡΠΈΠΈ, ΡΡΠΎ ΡΠ»ΡΠΆΠΈΡ ΠΏΠΎΠ΄ΡΠ²Π΅ΡΠΆΠ΄Π΅Π½ΠΈΠ΅ΠΌ ΡΠ»Π΅ΠΊΡΡΠΎΡ ΠΈΠΌΠΈΡΠ΅ΡΠΊΠΎΠ³ΠΎ ΠΌΠ΅Ρ Π°Π½ΠΈΠ·ΠΌΠ° ΠΏΡΠΎΡΠ΅ΡΡΠ°. ΠΠ΄Π½Π°ΠΊΠΎ Π² ΡΡΠ΄Π΅ ΡΠ»ΡΡΠ°Π΅Π² ΡΠΊΠΎΡΠΎΡΡΡ ΠΎΡΠ°ΠΆΠ΄Π΅Π½ΠΈΡ ΠΌΠ΅ΡΠ°Π»Π»Π° Π² ΠΌΠΎΠ΄Π΅Π»ΡΠ½ΡΡ ΡΠΈΡΡΠ΅ΠΌΠ°Ρ Π·Π°ΠΌΠ΅ΡΠ½ΠΎ ΠΎΡΠ»ΠΈΡΠ°Π΅ΡΡΡ ΠΎΡ ΡΠ΅Π°Π»ΡΠ½ΠΎΠΉ, ΡΡΠΎ ΡΠ²ΠΈΠ΄Π΅ΡΠ΅Π»ΡΡΡΠ²ΡΠ΅Ρ ΠΎ ΡΠ°ΡΡΠΈΡΠ½ΠΎΠΌ ΠΈΠ»ΠΈ ΠΏΠΎΠ»Π½ΠΎΠΌ ΠΏΡΠΎΡΠ΅ΠΊΠ°Π½ΠΈΠΈ ΠΏΡΠΎΡΠ΅ΡΡΠ° Π₯ΠΠ ΠΏΠΎ ΠΈΠ½ΠΎΠΌΡ ΠΌΠ΅Ρ Π°Π½ΠΈΠ·ΠΌΡ.
ΠΠΎΠ΄ Ρ ΠΈΠΌΠΈΡΠ΅ΡΠΊΠΈΠΌ Π½ΠΈΠΊΠ΅Π»ΠΈΡΠΎΠ²Π°Π½ΠΈΠ΅ΠΌ (Π₯Π) ΠΏΠΎΠ½ΠΈΠΌΠ°ΡΡ ΠΏΡΠΎΡΠ΅ΡΡ Π½ΠΈΠΊΠ΅Π»ΠΈΡΠΎΠ²Π°Π½ΠΈΡ ΠΈΠ·Π΄Π΅Π»ΠΈΠΉ ΠΏΡΡΠ΅ΠΌ Π²ΠΎΡΡΡΠ°Π½ΠΎΠ²Π»Π΅Π½ΠΈΡ Π½ΠΈΠΊΠ΅Π»Ρ ΠΈΠ· ΡΠ°ΡΡΠ²ΠΎΡΠ° Ρ ΠΏΠΎΠΌΠΎΡΡΡ ΡΠΎΠ΄Π΅ΡΠΆΠ°ΡΠ΅Π³ΠΎΡΡ Π² ΡΠ°ΡΡΠ²ΠΎΡΠ΅ Π²ΠΎΡΡΡΠ°Π½ΠΎΠ²ΠΈΡΠ΅Π»Ρ.
Π ΠΏΠΎΡΠ»Π΅Π΄Π½Π΅Π΅ Π²ΡΠ΅ΠΌΡ ΠΏΡΠΎΡΠ΅ΡΡΡ Π₯Π ΠΏΡΠΈΠΏΠΈΡΡΠ²Π°ΡΡ ΡΠ»Π΅ΠΊΡΡΠΎΡ
ΠΈΠΌΠΈΡΠ΅ΡΠΊΡΡ ΠΏΡΠΈΡΠΎΠ΄Ρ. Π‘ΠΎΠ³Π»Π°ΡΠ½ΠΎ ΡΡΠΎΠΌΡ ΠΌΠ΅Ρ
Π°Π½ΠΈΠ·ΠΌΡ Π²Π΅ΡΡ ΠΏΡΠΎΡΠ΅ΡΡ Π²ΠΎΡΡΡΠ°Π½ΠΎΠ²Π»Π΅Π½ΠΈΡ Ni(II) Π³ΠΈΠΏΠΎΡΠΎΡΡΠΈΡΠΎΠΌ ΠΌΠΎΠΆΠ΅Ρ Π±ΡΡΡ ΠΏΡΠ΅Π΄ΡΡΠ°Π²Π»Π΅Π½ Π΄Π²ΡΠΌΡ ΡΠΎΠΏΡΡΠΆΠ΅Π½Π½ΡΠΌΠΈ ΡΠ΅Π°ΠΊΡΠΈΡΠΌΠΈ.
zctc.ru
ΠΠΠΠΠΠΠ«Π Π‘Π‘Π«ΠΠΠ: ΠΠΠΠ£Π‘Π« ΠΠΠΠΠΠΠ ΠΠ!: ΠΠ« Π Π‘ΠΠ¦.Π‘ΠΠ’Π―Π₯: | ΠΠ°Π²ΠΈΠ³Π°ΡΠΈΡ ΠΏΠΎ ΡΠΏΡΠ°Π²ΠΎΡΠ½ΠΈΠΊΡ TehTab.ru:Β Β Π³Π»Π°Π²Π½Π°Ρ ΡΡΡΠ°Π½ΠΈΡΠ°Β /Β /Β Π’Π΅Ρ
Π½ΠΈΡΠ΅ΡΠΊΠ°Ρ ΠΈΠ½ΡΠΎΡΠΌΠ°ΡΠΈΡ /Β /Β Π₯ΠΈΠΌΠΈΡΠ΅ΡΠΊΠΈΠΉ ΡΠΏΡΠ°Π²ΠΎΡΠ½ΠΈΠΊ /Β /Β ΠΠΎΠ΄Π½ΡΠ΅ ΡΠ°ΡΡΠ²ΠΎΡΡ ΠΈ ΡΠΌΠ΅ΡΠΈ Π΄Π»Ρ ΠΎΠ±ΡΠ°Π±ΠΎΡΠΊΠΈ ΠΌΠ΅ΡΠ°Π»Π»ΠΎΠ². /Β /Β ΠΠΎΠ΄Π½ΡΠ΅ ΡΠ°ΡΡΠ²ΠΎΡΡ Π΄Π»Ρ Π½Π°Π½Π΅ΡΠ΅Π½ΠΈΡ ΠΈ ΡΠ΄Π°Π»Π΅Π½ΠΈΡ ΠΌΠ΅ΡΠ°Π»Π»ΠΈΡΠ΅ΡΠΊΠΈΡ
ΠΏΠΎΠΊΡΡΡΠΈΠΉ Β /Β /Β ΠΠΎΠ΄Π½ΡΠ΅ ΡΠ°ΡΡΠ²ΠΎΡΡ Π΄Π»Ρ Ρ
ΠΈΠΌΠΈΡΠ΅ΡΠΊΠΎΠ³ΠΎ Π½ΠΈΠΊΠ΅Π»ΠΈΡΠΎΠ²Π°Π½ΠΈΡ.
|
tehtab.ru
ΠΠΈΠΊΠ΅Π»ΠΈΡΠΎΠ²Π°Π½ΠΈΠ΅, ΡΠ΅ΡΠ΅Π±ΡΠ΅Π½ΠΈΠ΅ ΠΈ Π·ΠΎΠ»ΠΎΡΠ΅Π½ΠΈΠ΅ | Π’Π°ΠΊ Π΄Π΅Π»Π°ΡΡ
Π£ΡΡΠ°Π½ΠΎΠ²ΠΈΡΡ Π² Π³Π°ΡΠ°ΠΆΠ΅ Π°ΠΏΠΏΠ°ΡΠ°ΡΡΡΡ Π΄Π»Ρ ΡΠ»Π΅ΠΊΡΡΠΎΡ ΠΈΠΌΠΈΡΠ΅ΡΠΊΠΎΠ³ΠΎ ΠΏΠΎΠΊΡΡΡΠΈΡ ΠΌΠ΅ΡΠ°Π»Π»Π°ΠΌΠΈ Π΄ΡΡΠ³ΠΈΡ ΠΌΠ΅ΡΠ°Π»Π»ΠΎΠ² ΠΈ Π΄ΠΈΡΠ»Π΅ΠΊΡΡΠΈΠΊΠΎΠ² (ΡΡΠ°Π½ΡΡΠΎΡΠΌΠ°ΡΠΎΡ, Π²ΡΠΏΡΡΠΌΠΈΡΠ΅Π»Ρ, ΠΈΠ·ΠΌΠ΅ΡΠΈΡΠ΅Π»ΡΠ½ΡΠ΅ ΠΏΡΠΈΠ±ΠΎΡΡ, Π²Π°Π½Π½Π° ΠΈ Ρ. ΠΏ.) Π΄ΠΎΠ²ΠΎΠ»ΡΠ½ΠΎ ΠΏΡΠΎΠ±Π»Π΅ΠΌΠ°ΡΠΈΡΠ½ΠΎ.
Π‘Π΅ΠΉΡΠ°Ρ ΠΏΡΠΈΠΌΠ΅Π½ΡΠ΅ΡΡΡ ΠΌΠ΅ΡΠΎΠ΄ Ρ ΠΈΠΌΠΈΡΠ΅ΡΠΊΠΎΠ³ΠΎ ΠΏΠΎΠΊΡΡΡΠΈΡ ΠΌΠ΅ΡΠ°Π»Π»ΠΎΠ² ΠΈ Π΄ΠΈΡΠ»Π΅ΠΊΡΡΠΈΠΊΠΎΠ² (ΠΏΠ»Π°ΡΡΠΌΠ°ΡΡ, ΡΡΠ΅ΠΊΠ»Π°, ΡΠ°ΡΡΠΎΡΠ° ΠΈ Ρ. ΠΏ.) Π΄ΡΡΠ³ΠΈΠΌΠΈ ΠΌΠ΅ΡΠ°Π»Π»Π°ΠΌΠΈ.
ΠΡΠΎΡΠ΅ΡΡ Ρ ΠΈΠΌΠΈΡΠ΅ΡΠΊΠΎΠ³ΠΎ ΠΏΠΎΠΊΡΡΡΠΈΡ ΠΎΡΠ»ΠΈΡΠ°Π΅ΡΡΡ ΡΠ²ΠΎΠ΅ΠΉ ΠΏΡΠΎΡΡΠΎΡΠΎΠΉ. ΠΠ΅ΠΉΡΡΠ²ΠΈΡΠ΅Π»ΡΠ½ΠΎ, Π΄Π»Ρ ΡΠΎΠ³ΠΎ ΡΡΠΎΠ±Ρ ΠΏΠΎΠΊΡΡΡΡ ΠΌΠ΅ΡΠ°Π»Π»ΠΈΡΠ΅ΡΠΊΡΡ Π΄Π΅ΡΠ°Π»Ρ, Π½Π°ΠΏΡΠΈΠΌΠ΅Ρ, Π½ΠΈΠΊΠ΅Π»Π΅ΠΌ, Π½Π΅ Π½ΡΠΆΠ½ΠΎ Π³ΠΎΡΠΎΠ΄ΠΈΡΡ ΡΠ»ΠΎΠΆΠ½ΡΡ ΡΡΡΠ°Π½ΠΎΠ²ΠΊΡ. ΠΠΎΡΡΠ°ΡΠΎΡΠ½ΠΎ ΡΠ°ΡΠΏΠΎΠ»Π°Π³Π°ΡΡ ΠΈΡΡΠΎΡΠ½ΠΈΠΊΠΎΠΌ ΠΎΠ³Π½Ρ (Π³Π°Π·, ΠΏΡΠΈΠΌΡΡ ΠΈ Ρ.ΠΏ.), ΡΠΌΠ°Π»ΠΈΡΠΎΠ²Π°Π½Π½ΠΎΠΉ ΠΏΠΎΡΡΠ΄ΠΎΠΉ ΠΈ ΠΏΠΎΠ΄Ρ ΠΎΠ΄ΡΡΠΈΠΌΠΈ Ρ ΠΈΠΌΠΈΠΊΠ°ΡΠ°ΠΌΠΈ. Π§Π°Ρ, Π΄Π²Π°- ΠΈ Π΄Π΅ΡΠ°Π»ΠΈ ΠΏΠΎΠΊΡΡΡΡ ΠΏΠ»ΠΎΡΠ½ΡΠΌ ΠΈ Π±Π»Π΅ΡΡΡΡΠΈΠΌ ΡΠ»ΠΎΠ΅ΠΌ Π½ΠΈΠΊΠ΅Π»Ρ.
Π ΡΡΠΎΠΉ ΡΡΠ°ΡΡΠ΅ ΠΌΡ ΡΠ°ΡΡΠΌΠΎΡΡΠΈΠΌ ΡΠΎΠ»ΡΠΊΠΎ: Π½ΠΈΠΊΠ΅Π»ΠΈΡΠΎΠ²Π°Π½ΠΈΠ΅, ΡΠ΅ΡΠ΅Π±ΡΠ΅Π½ΠΈΠ΅ ΠΈ Π·ΠΎΠ»ΠΎΡΠ΅Π½ΠΈΠ΅ ΠΌΠ΅ΡΠ°Π»Π»ΠΎΠ². ΠΠ΄Π½Π°ΠΊΠΎ ΡΡΡΠ΅ΡΡΠ²ΡΠ΅Ρ ΠΌΠ½ΠΎΠ³ΠΎ ΡΠ΅ΡΠ΅ΠΏΡΠΎΠ² Ρ ΠΈΠΌΠΈΡΠ΅ΡΠΊΠΎΠ³ΠΎ ΠΏΠΎΠΊΡΡΡΠΈΡ ΠΌΠ΅ΡΠ°Π»Π»ΠΎΠ² ΠΈ Π΄ΠΈΡΠ»Π΅ΠΊΡΡΠΈΠΊΠΎΠ² ΠΌΠ΅Π΄ΡΡ, ΠΊΠ°Π΄ΠΌΠΈΠ΅ΠΌ, ΠΎΠ»ΠΎΠ²ΠΎΠΌ, ΠΊΠΎΠ±Π°Π»ΡΡΠΎΠΌ, Π±ΠΎΡΠΎΠΌ, Π΄Π²ΠΎΠΉΠ½ΡΠΌΠΈ ΠΈ ΡΡΠΎΠΉΠ½ΡΠΌΠΈ ΡΠΏΠ»Π°Π²Π°ΠΌΠΈ.
ΠΠΈΠΊΠ΅Π»ΠΈΡΠΎΠ²Π°Π½ΠΈΠ΅
Π ΠΎΡΠ½ΠΎΠ²Ρ ΠΏΡΠΎΡΠ΅ΡΡΠ° Ρ ΠΈΠΌΠΈΡΠ΅ΡΠΊΠΎΠ³ΠΎ Π½ΠΈΠΊΠ΅Π»ΠΈΡΠΎΠ²Π°Π½ΠΈΡ ΠΏΠΎΠ»ΠΎΠΆΠ΅Π½Π° ΡΠ΅Π°ΠΊΡΠΈΡ Π²ΠΎΡΡΡΠ°Π½ΠΎΠ²Π»Π΅Π½ΠΈΡ Π½ΠΈΠΊΠ΅Π»Ρ ΠΈΠ· Π²ΠΎΠ΄Π½ΡΡ ΡΠ°ΡΡΠ²ΠΎΡΠΎΠ² Π΅Π³ΠΎ ΡΠΎΠ»Π΅ΠΉ Π³ΠΈΠΏΠΎΡΠΎΡΡΠΈΡΠΎΠΌ Π½Π°ΡΡΠΈΡ.
ΠΠ»ΡΠ½ΠΊΠ° Π½ΠΈΠΊΠ΅Π»Π΅Π²ΠΎΠ³ΠΎ ΠΏΠΎΠΊΡΡΡΠΈΡ ΠΏΠΎΠ»ΡΡΠ°Π΅ΡΡΡ Π±Π»Π΅ΡΡΡΡΠ°Ρ ΠΈΠ»ΠΈ ΠΏΠΎΠ»ΡΠ±Π»Π΅ΡΡΡΡΠ°Ρ. Π‘ΡΡΡΠΊΡΡΡΠ° ΠΏΠΎΠΊΡΡΡΠΈΡ β Π°ΠΌΠΎΡΡΠ½Π°Ρ, ΠΈΠ· ΡΠΏΠ»Π°Π²Π° Π½ΠΈΠΊΠ΅Π»Ρ ΠΈ ΡΠΎΡΡΠΎΡΠ°. ΠΠ»ΡΠ½ΠΊΠ° Π½ΠΈΠΊΠ΅Π»Ρ Π±Π΅Π· ΡΠ΅ΡΠΌΠΎΠΎΠ±ΡΠ°Π±ΠΎΡΠΊΠΈ ΡΠ»Π°Π±ΠΎ Π΄Π΅ΡΠΆΠΈΡΡΡ Π½Π° ΠΏΠΎΠ²Π΅ΡΡ Π½ΠΎΡΡΠΈ ΠΎΡΠ½ΠΎΠ²Π½ΠΎΠ³ΠΎ ΠΌΠ΅ΡΠ°Π»Π»Π°, Ρ ΠΎΡΡ Π΅Π΅ ΡΠ²Π΅ΡΠ΄ΠΎΡΡΡ Π±Π»ΠΈΠ·ΠΊΠ° ΠΊ ΡΠ²Π΅ΡΠ΄ΠΎΡΡΠΈ Ρ ΡΠΎΠΌΠΎΠ²ΠΎΠ³ΠΎ ΠΏΠΎΠΊΡΡΡΠΈΡ.
Π’Π΅ΡΠΌΠΈΡΠ΅ΡΠΊΠ°Ρ ΠΎΠ±ΡΠ°Π±ΠΎΡΠΊΠ° Π΄Π΅ΡΠ°Π»ΠΈ Ρ Π½ΠΈΠΊΠ΅Π»Π΅Π²ΡΠΌ ΠΏΠΎΠΊΡΡΡΠΈΠ΅ΠΌ, ΠΏΠΎΠ»ΡΡΠ΅Π½Π½ΡΠΌ Ρ ΠΈΠΌΠΈΡΠ΅ΡΠΊΠΈΠΌ ΠΏΡΡΠ΅ΠΌ, Π² Π·Π½Π°ΡΠΈΡΠ΅Π»ΡΠ½ΠΎΠΉ ΡΡΠ΅ΠΏΠ΅Π½ΠΈ ΡΠ²Π΅Π»ΠΈΡΠΈΠ²Π°Π΅Ρ ΡΡΠ΅ΠΏΠ»Π΅Π½ΠΈΠ΅ ΠΏΠ»Π΅Π½ΠΊΠΈ Π½ΠΈΠΊΠ΅Π»Ρ Ρ ΠΎΡΠ½ΠΎΠ²Π½ΡΠΌ ΠΌΠ΅ΡΠ°Π»Π»ΠΎΠΌ. ΠΠ΄Π½ΠΎΠ²ΡΠ΅ΠΌΠ΅Π½Π½ΠΎ ΡΠ°ΡΡΠ΅Ρ ΠΈ ΡΠ²Π΅ΡΠ΄ΠΎΡΡΡ Π½ΠΈΠΊΠ΅Π»Ρ, Π΄ΠΎΡΡΠΈΠ³Π°ΡΡΠ°Ρ ΡΠ²Π΅ΡΠ΄ΠΎΡΡΠΈ Ρ ΡΠΎΠΌΠ°.
Π’Π΅ΡΠΌΠΈΡΠ΅ΡΠΊΠ°Ρ ΠΎΠ±ΡΠ°Π±ΠΎΡΠΊΠ° Π΄Π΅ΡΠ°Π»ΠΈ Ρ Π½ΠΈΠΊΠ΅Π»Π΅Π²ΡΠΌ ΠΏΠΎΠΊΡΡΡΠΈΠ΅ΠΌ ΠΏΡΠΎΠΈΠ·Π²ΠΎΠ΄ΠΈΡΡΡ ΠΏΡΠΈ ΡΠ΅ΠΌΠΏΠ΅ΡΠ°ΡΡΡΠ΅ ΠΎΠΊΠΎΠ»ΠΎ 400Β°Π‘ Π² ΡΠ΅ΡΠ΅Π½ΠΈΠ΅ ΡΠ°ΡΠ°. ΠΡΠΈ ΡΠ΅ΡΠΌΠΈΡΠ΅ΡΠΊΠΎΠΉ ΠΎΠ±ΡΠ°Π±ΠΎΡΠΊΠ΅ Π·Π°ΠΊΠ°Π»Π΅Π½Π½ΡΡ ΡΡΠ°Π»ΡΠ½ΡΡ Π΄Π΅ΡΠ°Π»Π΅ΠΉ Ρ Π½ΠΈΠΊΠ΅Π»Π΅Π²ΡΠΌ ΠΏΠΎΠΊΡΡΡΠΈΠ΅ΠΌ Π½Π΅ΠΎΠ±Ρ ΠΎΠ΄ΠΈΠΌΠΎ ΡΡΠΈΡΡΠ²Π°ΡΡ, ΠΏΡΠΈ ΠΊΠ°ΠΊΠΎΠΉ ΡΠ΅ΠΌΠΏΠ΅ΡΠ°ΡΡΡΠ΅ ΡΡΠΈ Π΄Π΅ΡΠ°Π»ΠΈ ΠΎΡΠΏΡΡΠΊΠ°Π»ΠΈΡΡ, ΠΈ Π½Π΅ ΠΏΡΠ΅Π²ΡΡΠ°ΡΡ Π΅Π΅. Π ΡΡΠΎΠΌ ΡΠ»ΡΡΠ°Π΅ ΡΠ΅ΡΠΌΠΈΡΠ΅ΡΠΊΡΡ ΠΎΠ±ΡΠ°Π±ΠΎΡΠΊΡ ΠΏΡΠΎΠΈΠ·Π²ΠΎΠ΄ΡΡ ΠΏΡΠΈ ΡΠ΅ΠΌΠΏΠ΅ΡΠ°ΡΡΡΠ΅ 270- 300 Β°Π‘ Ρ Π²ΡΠ΄Π΅ΡΠΆΠΊΠΎΠΉ Π΄ΠΎ 3 Ρ.
Π Π°ΡΡΠ²ΠΎΡΡ Π΄Π»Ρ Ρ ΠΈΠΌΠΈΡΠ΅ΡΠΊΠΎΠ³ΠΎ Π½ΠΈΠΊΠ΅Π»ΠΈΡΠΎΠ²Π°Π½ΠΈΡ ΠΌΠΎΠ³ΡΡ Π±ΡΡΡ ΡΠ΅Π»ΠΎΡΠ½ΡΠΌΠΈ (ΡΠ- Π²ΡΡΠ΅ 6,5) ΠΈ ΠΊΠΈΡΠ»ΡΠΌΠΈ (ΡΠ- ΠΎΡ 4 Π΄ΠΎ 6,5).
Π©Π΅Π»ΠΎΡΠ½ΡΠ΅ ΡΠ°ΡΡΠ²ΠΎΡΡ. ΠΡ ΠΏΡΠΈΠΌΠ΅Π½ΡΡΡ ΠΏΡΠΈ Π½Π°Π½Π΅ΡΠ΅Π½ΠΈΠΈ ΠΏΠΎΠΊΡΡΡΠΈΠΉ Π½Π° ΠΊΠΎΡΡΠΎΠ·ΠΈΠΎΠ½Π½ΠΎΡΡΠΎΠΉΠΊΡΡ ΡΡΠ°Π»Ρ, Π°Π»ΡΠΌΠΈΠ½ΠΈΠΉ, ΠΌΠ°Π³Π½ΠΈΠΉ ΠΈ Π΄ΠΈΡΠ»Π΅ΠΊΡΡΠΈΠΊΠΈ. ΠΠΎΠΊΡΡΡΠΈΡ, ΠΎΡΠ°ΠΆΠ΄Π°Π΅ΠΌΡΠ΅ ΠΈΠ· ΡΠ΅Π»ΠΎΡΠ½ΡΡ ΡΠ°ΡΡΠ²ΠΎΡΠΎΠ², ΠΈΠΌΠ΅ΡΡ ΠΌΠ΅Π½Π΅Π΅ Π±Π»Π΅ΡΡΡΡΡΡ ΠΏΠΎΠ²Π΅ΡΡ Π½ΠΎΡΡΡ, ΡΠ΅ΠΌ ΠΏΠΎΠ»ΡΡΠ΅Π½Π½ΡΠ΅ ΠΈΠ· ΠΊΠΈΡΠ»ΡΡ ΡΠ°ΡΡΠ²ΠΎΡΠΎΠ². ΠΠΎ Π·Π°ΡΠΎ ΠΏΠΎΠΊΡΡΡΠΈΡ ΠΈΠ· ΡΠ΅Π»ΠΎΡΠ½ΡΡ ΡΠ°ΡΡΠ²ΠΎΡΠΎΠ² Π±ΠΎΠ»Π΅Π΅ ΠΏΡΠΎΡΠ½ΠΎ ΡΠ²ΡΠ·Π°Π½Ρ Ρ ΠΎΡΠ½ΠΎΠ²ΠΎΠΉ, ΡΠ΅ΠΌ ΠΈΠ· ΠΊΠΈΡΠ»ΠΎΠ³ΠΎ.
Π£ ΡΠ΅Π»ΠΎΡΠ½ΡΡ ΡΠ°ΡΡΠ²ΠΎΡΠΎΠ² Π΅ΡΡΡ Π΅ΡΠ΅ ΠΎΠ΄ΠΈΠ½ ΡΡΡΠ΅ΡΡΠ²Π΅Π½Π½ΡΠΉ Π½Π΅Π΄ΠΎΡΡΠ°ΡΠΎΠΊ- ΡΠ²Π»Π΅Π½ΠΈΠ΅ ΡΠ°ΠΌΠΎΡΠ°Π·ΡΡΠ΄Π°. ΠΠ½ΠΎ Π½Π°ΡΡΡΠΏΠ°Π΅Ρ ΠΏΡΠΈ ΠΏΠ΅ΡΠ΅Π³ΡΠ΅Π²Π΅ ΡΠ°ΡΡΠ²ΠΎΡΠ°. ΠΡΠΎ ΠΌΠ³Π½ΠΎΠ²Π΅Π½Π½ΠΎΠ΅ Π²ΡΠΏΠ°Π΄Π΅Π½ΠΈΠ΅ Π³ΡΠ±ΡΠ°ΡΠΎΠΉ ΠΌΠ°ΡΡΡ Π½ΠΈΠΊΠ΅Π»Ρ ΠΈΠ· ΡΠ°ΡΡΠ²ΠΎΡΠ°, ΡΠΎΠΏΡΠΎΠ²ΠΎΠΆΠ΄Π°ΡΡΠ΅Π΅ΡΡ Π²ΡΠ±ΡΠΎΡΠΎΠΌ ΠΊΠΈΠΏΡΡΠ΅Π³ΠΎ ΡΠ°ΡΡΠ²ΠΎΡΠ° ΠΈΠ· Π²Π°Π½Π½Ρ!
Π Π΅Π³ΡΠ»ΠΈΡΠΎΠ²ΠΊΡ ΡΠ΅ΠΌΠΏΠ΅ΡΠ°ΡΡΡΡ ΠΏΡΠΈ ΠΎΡΡΡΡΡΡΠ²ΠΈΠΈ ΡΠ΅ΡΠΌΠΎΠΌΠ΅ΡΡΠ° ΠΌΠΎΠΆΠ½ΠΎ Π²Π΅ΡΡΠΈ ΠΏΠΎ ΠΈΠ½ΡΠ΅Π½ΡΠΈΠ²Π½ΠΎΡΡΠΈ Π³Π°Π·ΠΎΠ²ΡΠ΄Π΅Π»Π΅Π½ΠΈΡ. ΠΡΠ»ΠΈ Π³Π°Π· Π²ΡΠ΄Π΅Π»ΡΠ΅ΡΡΡ Π½Π΅ ΠΈΠ½ΡΠ΅Π½ΡΠΈΠ²Π½ΠΎ, ΡΠΎ ΠΌΠΎΠΆΠ½ΠΎ Π±ΡΡΡ ΡΠ²Π΅ΡΠ΅Π½Π½ΡΠΌ, ΡΡΠΎ ΡΠ°ΠΌΠΎΡΠ°Π·ΡΡΠ΄Π° Π½Π΅ Π±ΡΠ΄Π΅Ρ.
ΠΠΈΡΠ»ΡΠ΅ ΡΠ°ΡΡΠ²ΠΎΡΡ
ΠΠ½ΠΈ Π½Π°Ρ ΠΎΠ΄ΡΡ ΠΏΡΠΈΠΌΠ΅Π½Π΅Π½ΠΈΠ΅ ΠΏΡΠΈ Π½Π°Π½Π΅ΡΠ΅Π½ΠΈΠΈ ΠΏΠΎΠΊΡΡΡΠΈΠΉ Π½Π° Π΄Π΅ΡΠ°Π»ΠΈ ΠΈΠ· ΡΠ΅ΡΠ½ΡΡ ΠΌΠ΅ΡΠ°Π»Π»ΠΎΠ², ΠΌΠ΅Π΄ΠΈ, Π»Π°ΡΡΠ½ΠΈ, ΠΎΡΠΎΠ±Π΅Π½Π½ΠΎ ΠΊΠΎΠ³Π΄Π° ΡΡΠ΅Π±ΡΠ΅ΡΡΡ Π²ΡΡΠΎΠΊΠ°Ρ ΡΠ²Π΅ΡΠ΄ΠΎΡΡΡ, ΠΈΠ·Π½ΠΎΡΠΎΡΡΠΎΠΉΠΊΠΎΡΡΡ ΠΈ ΠΊΠΎΡΡΠΎΠ·ΠΈΠΎΠ½Π½ΠΎ Π·Π°ΡΠΈΡΠ½ΡΠ΅ ΡΠ²ΠΎΠΉΡΡΠ²Π° ΠΏΠΎΠ²Π΅ΡΡ Π½ΠΎΡΡΠΈ, ΠΏΠΎΠΊΡΡΡΠΎΠΉ Π½ΠΈΠΊΠ΅Π»Π΅ΠΌ.
ΠΠ»Ρ ΡΠΏΡΠ°Π²ΠΊΠΈ. ΠΠΎΠ΄Ρ Π΄Π»Ρ Π½ΠΈΠΊΠ΅Π»ΠΈΡΠΎΠ²Π°Π½ΠΈΡ (ΠΈ ΠΏΡΠΈ Π½Π°Π½Π΅ΡΠ΅Π½ΠΈΠΈ Π΄ΡΡΠ³ΠΈΡ ΠΏΠΎΠΊΡΡΡΠΈΠΉ) Π±Π΅ΡΡΡ Π΄ΠΈΡΡΠΈΠ»Π»ΠΈΡΠΎΠ²Π°Π½Π½ΡΡ (ΠΌΠΎΠΆΠ½ΠΎ ΠΈΡΠΏΠΎΠ»ΡΠ·ΠΎΠ²Π°ΡΡ ΠΊΠΎΠ½Π΄Π΅Π½ΡΠ°Ρ ΠΈΠ· Π±ΡΡΠΎΠ²ΡΡ Ρ ΠΎΠ»ΠΎΠ΄ΠΈΠ»ΡΠ½ΠΈΠΊΠΎΠ²). Π₯ΠΈΠΌΡΠ΅Π°ΠΊΡΠΈΠ²Ρ Π΄ΠΎΠ»ΠΆΠ½Ρ ΠΏΡΠΈΠΌΠ΅Π½ΡΡΡΡΡ ΠΊΠ°ΠΊ ΠΌΠΈΠ½ΠΈΠΌΡΠΌ ΡΠΈΡΡΡΠ΅ (ΠΎΠ±ΠΎΠ·Π½Π°ΡΠ΅Π½ΠΈΠ΅ Π½Π° ΡΡΠΈΠΊΠ΅ΡΠΊΠ΅ β Π§).
ΠΠΎΠ΄Π³ΠΎΡΠΎΠ²ΠΊΠ° Π΄Π΅ΡΠ°Π»ΠΈ. ΠΠ΅ΡΠ΅Π΄ Π½Π°Π½Π΅ΡΠ΅Π½ΠΈΠ΅ΠΌ Π½Π° ΠΎΡΠ½ΠΎΠ²Π½ΠΎΠΉ ΠΌΠ΅ΡΠ°Π»Π» ΠΊΠ°ΠΊΠΈΡ -Π»ΠΈΠ±ΠΎ ΠΌΠ΅ΡΠ°Π»Π»ΠΈΡΠ΅ΡΠΊΠΈΡ ΠΏΠ»Π΅Π½ΠΎΠΊ Π½Π΅ΠΎΠ±Ρ ΠΎΠ΄ΠΈΠΌΠΎ ΠΎΡΡΡΠ΅ΡΡΠ²ΠΈΡΡ ΡΡΠ΄ ΠΏΠΎΠ΄Π³ΠΎΡΠΎΠ²ΠΈΡΠ΅Π»ΡΠ½ΡΡ ΠΎΠΏΠ΅ΡΠ°ΡΠΈΠΉ. ΠΡΠΏΠΎΠ»ΠΈΡΠΎΠ²Π°Π½Π½ΡΡ Π΄Π΅ΡΠ°Π»Ρ ΠΎΠ±Π΅Π·ΠΆΠΈΡΠΈΠ²Π°ΡΡ, ΡΡΠ°Π²ΡΡ ΠΈ Π΄Π΅ΠΊΠ°ΠΏΠΈΡΡΡΡ.
ΠΠ±Π΅Π·ΠΆΠΈΡΠΈΠ²Π°Π½ΠΈΠ΅. ΠΡΠΎΡΠ΅ΡΡ ΠΎΠ±Π΅Π·ΠΆΠΈΡΠΈΠ²Π°Π½ΠΈΡ ΠΌΠ΅ΡΠ°Π»Π»ΠΈΡΠ΅ΡΠΊΠΈΡ Π΄Π΅ΡΠ°Π»Π΅ΠΉ ΠΏΡΠΎΠ²ΠΎΠ΄ΡΡ, ΠΊΠ°ΠΊ ΠΏΡΠ°Π²ΠΈΠ»ΠΎ, ΠΊΠΎΠ³Π΄Π° ΡΡΠΈ Π΄Π΅ΡΠ°Π»ΠΈ ΡΠΎΠ»ΡΠΊΠΎ ΡΡΠΎ ΠΎΠ±ΡΠ°Π±ΠΎΡΠ°Π½Ρ (ΠΎΡΡΠ»ΠΈΡΠΎΠ²Π°Π½Ρ ΠΈΠ»ΠΈ ΠΎΡΠΏΠΎΠ»ΠΈΡΠΎΠ²Π°Π½Ρ) ΠΈ Π½Π° ΠΈΡ ΠΏΠΎΠ²Π΅ΡΡ Π½ΠΎΡΡΠΈ Π½Π΅Ρ ΡΠΆΠ°Π²ΡΠΈΠ½Ρ, ΠΎΠΊΠ°Π»ΠΈΠ½Ρ ΠΈ Π΄ΡΡΠ³ΠΈΡ ΠΏΠΎΡΡΠΎΡΠΎΠ½Π½ΠΈΡ ΠΏΡΠΎΠ΄ΡΠΊΡΠΎΠ².
Π‘ ΠΏΠΎΠΌΠΎΡΡΡ ΠΎΠ±Π΅Π·ΠΆΠΈΡΠΈΠ²Π°Π½ΠΈΡ Ρ ΠΏΠΎΠ²Π΅ΡΡ Π½ΠΎΡΡΠΈ Π΄Π΅ΡΠ°Π»Π΅ΠΉ ΡΠ΄Π°Π»ΡΡΡ ΠΌΠ°ΡΠ»ΡΠ½ΡΠ΅ ΠΈ ΠΆΠΈΡΠΎΠ²ΡΠ΅ ΠΏΠ»Π΅Π½ΠΊΠΈ. ΠΠ»Ρ ΡΡΠΎΠ³ΠΎ ΠΏΡΠΈΠΌΠ΅Π½ΡΡΡ Π²ΠΎΠ΄Π½ΡΠ΅ ΡΠ°ΡΡΠ²ΠΎΡΡ Π½Π΅ΠΊΠΎΡΠΎΡΡΡ Ρ ΠΈΠΌΡΠ΅Π°ΠΊΡΠΈΠ²ΠΎΠ², Ρ ΠΎΡΡ Π΄Π»Ρ ΡΡΠΎΠ³ΠΎ ΠΌΠΎΠΆΠ½ΠΎ ΠΈΡΠΏΠΎΠ»ΡΠ·ΠΎΠ²Π°ΡΡ ΠΈ ΠΎΡΠ³Π°Π½ΠΈΡΠ΅ΡΠΊΠΈΠ΅ ΡΠ°ΡΡΠ²ΠΎΡΠΈΡΠ΅Π»ΠΈ (ΡΡΠΈΡ Π»ΠΎΡΡΡΠΈΠ»Π΅Π½, ΠΏΠ΅Π½ΡΠ°Ρ Π»ΠΎΡΡΡΠ°Π½, ΡΠ°ΡΡΠ²ΠΎΡΠΈΡΠ΅Π»ΠΈ β 646 ΠΈ β 648 ΠΈ Π΄Ρ.).
ΠΠ±Π΅Π·ΠΆΠΈΡΠΈΠ²Π°Π½ΠΈΠ΅ Π² Π²ΠΎΠ΄Π½ΡΡ ΡΠ°ΡΡΠ²ΠΎΡΠ°Ρ ΠΏΡΠΎΠ²ΠΎΠ΄ΡΡ Π² ΡΠΌΠ°Π»ΠΈΡΠΎΠ²Π°Π½Π½ΠΎΠΉ ΠΏΠΎΡΡΠ΄Π΅. ΠΠ°Π»ΠΈΠ²Π°ΡΡ Π²ΠΎΠ΄Ρ, ΡΠ°ΡΡΠ²ΠΎΡΡΡΡ Π² Π½Π΅ΠΉ Ρ ΠΈΠΌΡΠ΅Π°ΠΊΡΠΈΠ²Ρ ΠΈ ΡΡΠ°Π²ΡΡ Π½Π° ΠΌΠ°Π»ΡΠΉ ΠΎΠ³ΠΎΠ½Ρ. ΠΡΠΈ Π΄ΠΎΡΡΠΈΠΆΠ΅Π½ΠΈΠΈ Π½ΡΠΆΠ½ΠΎΠΉ ΡΠ΅ΠΌΠΏΠ΅ΡΠ°ΡΡΡΡ Π·Π°Π³ΡΡΠΆΠ°ΡΡ Π² ΡΠ°ΡΡΠ²ΠΎΡ Π΄Π΅ΡΠ°Π»ΠΈ. Π ΠΏΡΠΎΡΠ΅ΡΡΠ΅ ΠΎΠ±ΡΠ°Π±ΠΎΡΠΊΠΈ ΡΠ°ΡΡΠ²ΠΎΡ ΠΏΠ΅ΡΠ΅ΠΌΠ΅ΡΠΈΠ²Π°ΡΡ. ΠΠΈΠΆΠ΅ ΠΏΡΠΈΠ²ΠΎΠ΄ΡΡΡΡ ΡΠΎΡΡΠ°Π²Ρ Π΄Π»Ρ ΠΎΠ±Π΅Π·ΠΆΠΈΡΠΈΠ²Π°Π½ΠΈΡ (Π²ΡΠ΅ Π΄Π°Π½ΠΎ Π² Π³ΡΠ°ΠΌΠΌΠ°Ρ Π½Π° Π»ΠΈΡΡ Π²ΠΎΠ΄Ρ β Π³/Π»), Π° ΡΠ°ΠΊΠΆΠ΅ ΡΠ°Π±ΠΎΡΠΈΠ΅ ΡΠ΅ΠΌΠΏΠ΅ΡΠ°ΡΡΡΡ ΡΠ°ΡΡΠ²ΠΎΡΠΎΠ² ΠΈ Π²ΡΠ΅ΠΌΡ ΠΎΠ±ΡΠ°Π±ΠΎΡΠΊΠΈ Π΄Π΅ΡΠ°Π»Π΅ΠΉ.
ΠΠ½ΠΈΠΌΠ°Π½ΠΈΠ΅! ΠΡ ΠΊΠ°ΡΠ΅ΡΡΠ²Π° ΠΏΡΠΎΠ²Π΅Π΄Π΅Π½ΠΈΡ ΠΏΠΎΠ΄Π³ΠΎΡΠΎΠ²ΠΈΡΠ΅Π»ΡΠ½ΡΡ ΠΎΠΏΠ΅ΡΠ°ΡΠΈΠΉ Π² ΡΠΈΠ»ΡΠ½ΠΎΠΉ ΡΡΠ΅ΠΏΠ΅Π½ΠΈ Π·Π°Π²ΠΈΡΠΈΡ ΠΊΠΎΠ½Π΅ΡΠ½ΡΠΉ ΡΠ΅Π·ΡΠ»ΡΡΠ°Ρ Π²ΡΠ΅Ρ ΡΠ°Π±ΠΎΡ.
Π§Π΅ΡΠ½ΡΠ΅ ΠΌΠ΅ΡΠ°Π»Π»Ρ ΠΎΠ±Π΅Π·ΠΆΠΈΡΠΈΠ²Π°ΡΡ Π² ΠΎΠ΄Π½ΠΎΠΌ ΠΈΠ· ΡΠ°ΡΡΠ²ΠΎΡΠΎΠ²:
- ΠΠΈΠ΄ΠΊΠΎΠ΅ ΡΡΠ΅ΠΊΠ»ΠΎ (ΠΊΠ°Π½ΡΠ΅Π»ΡΡΡΠΊΠΈΠΉ ΡΠΈΠ»ΠΈΠΊΠ°ΡΠ½ΡΠΉ ΠΊΠ»Π΅ΠΉ) β 3β10, Π΅Π΄ΠΊΠΈΠΉ Π½Π°ΡΡ (ΠΊΠ°Π»ΠΈΠΉ) β 20- 30, ΡΡΠΈΠ½Π°ΡΡΠΈΠΉΡΠΎΡΡΠ°Ρ β 25β30. Π’Π΅ΠΌΠΏΠ΅ΡΠ°ΡΡΡΠ° ΡΠ°ΡΡΠ²ΠΎΡΠ° β 70β90 Β°Π‘, Π²ΡΠ΅ΠΌΡ ΠΎΠ±ΡΠ°Π±ΠΎΡΠΊΠΈ β 10β30 ΠΌΠΈΠ½.
- ΠΠ°Π»ΡΡΠΈΠ½ΠΈΡΠΎΠ²Π°Π½Π½Π°Ρ ΡΠΎΠ΄Π° β 20, ΠΊΠ°Π»ΠΈΠ΅Π²ΡΠΉ Ρ ΡΠΎΠΌΠΏΠΈΠΊ β 1. Π’Π΅ΠΌΠΏΠ΅ΡΠ°ΡΡΡΠ° ΡΠ°ΡΡΠ²ΠΎΡΠ° β 80β90Β°Π‘, Π²ΡΠ΅ΠΌΡ ΠΎΠ±ΡΠ°Π±ΠΎΡΠΊΠΈ β 10β20 ΠΌΠΈΠ½.
ΠΠ΅Π΄Ρ ΠΈ Π΅Π΅ ΡΠΏΠ»Π°Π²Ρ ΠΎΠ±Π΅Π·ΠΆΠΈΡΠΈΠ²Π°ΡΡ Π² ΠΎΠ΄Π½ΠΎΠΌ ΠΈΠ· ΡΠ°ΡΡΠ²ΠΎΡΠΎΠ²:
- ΠΠ΄ΠΊΠΈΠΉ Π½Π°ΡΡ β 35, ΠΊΠ°Π»ΡΡΠΈΠ½ΠΈΡΠΎΠ²Π°Π½Π½Π°Ρ ΡΠΎΠ΄Π° β 60, ΡΡΠΈΠ½Π°ΡΡΠΈΠΉΡΠΎΡΡΠ°Ρ β 15, ΠΏΡΠ΅ΠΏΠ°ΡΠ°Ρ ΠΠ-7 (ΠΈΠ»ΠΈ ΠΠ-10). Π’Π΅ΠΌΠΏΠ΅ΡΠ°ΡΡΡΠ° ΡΠ°ΡΡΠ²ΠΎΡΠ° β 60β70 Β°Π‘, Π²ΡΠ΅ΠΌΡ ΠΎΠ±ΡΠ°Π±ΠΎΡΠΊΠΈ 10β20 ΠΌΠΈΠ½.
- ΠΠ΄ΠΊΠΈΠΉ Π½Π°ΡΡ (ΠΊΠ°Π»ΠΈΠΉ) β 75, ΠΆΠΈΠ΄ΠΊΠΎΠ΅ ΡΡΠ΅ΠΊΠ»ΠΎ β 20. Π’Π΅ΠΌΠΏΠ΅ΡΠ°ΡΡΡΠ° ΡΠ°ΡΡΠ²ΠΎΡΠ° β 80β90 Β°Π‘, Π²ΡΠ΅ΠΌΡ ΠΎΠ±ΡΠ°Π±ΠΎΡΠΊΠΈ β 40β60 ΠΌΠΈΠ½.
ΠΠ»ΡΠΌΠΈΠ½ΠΈΠΉ ΠΈ Π΅Π³ΠΎ ΡΠΏΠ»Π°Π²Ρ ΠΎΠ±Π΅Π·ΠΆΠΈΡΠΈΠ²Π°ΡΡ Π² ΡΠ»Π΅Π΄ΡΡΡΠΈΡ ΡΠ°ΡΡΠ²ΠΎΡΠ°Ρ :
- ΠΠΈΠ΄ΠΊΠΎΠ΅ ΡΡΠ΅ΠΊΠ»ΠΎ β 20β30, ΠΊΠ°Π»ΡΡΠΈΠ½ΠΈΡΠΎΠ²Π°Π½Π½Π°Ρ ΡΠΎΠ΄Π° β 50β60, ΡΡΠΈΠ½Π°ΡΡΠΈΠΉΡΠΎΡΡΠ°Ρ βΒ 50β60. Π’Π΅ΠΌΠΏΠ΅ΡΠ°ΡΡΡΠ° ΡΠ°ΡΡΠ²ΠΎΡΠ° β 50β 60 Β°Π‘, Π²ΡΠ΅ΠΌΡ ΠΎΠ±ΡΠ°Π±ΠΎΡΠΊΠΈ β 3β5 ΠΌΠΈΠ½.
- ΠΠ°Π»ΡΡΠΈΠ½ΠΈΡΠΎΠ²Π°Π½Π½Π°Ρ ΡΠΎΠ΄Π° β 20β25, ΡΡΠΈΠ½Π°ΡΡΠΈΠΉΡΠΎΡΡΠ°Ρ β 20β25, ΠΏΡΠ΅ΠΏΠ°ΡΠ°Ρ ΠΠ-7 (ΠΈΠ»ΠΈ ΠΠ-10) β 5β7. Π’Π΅ΠΌΠΏΠ΅ΡΠ°ΡΡΡΠ° ΡΠ°ΡΡΠ²ΠΎΡΠ° β 70β80 Β°Π‘, Π²ΡΠ΅ΠΌΡ ΠΎΠ±ΡΠ°Π±ΠΎΡΠΊΠΈ β 10β 20 ΠΌΠΈΠ½.
Π‘Π΅ΡΠ΅Π±ΡΠΎ, Π½ΠΈΠΊΠ΅Π»Ρ ΠΈ ΠΈΡ ΡΠΏΠ»Π°Π²Ρ ΠΎΠ±Π΅Π·ΠΆΠΈΡΠΈΠ²Π°ΡΡ Π² ΡΠ°ΡΡΠ²ΠΎΡΠ°Ρ :
- ΠΠΈΠ΄ΠΊΠΎΠ΅ ΡΡΠ΅ΠΊΠ»ΠΎ β 50, ΠΊΠ°Π»ΡΡΠΈΠ½ΠΈΡΠΎΠ²Π°Π½Π½Π°Ρ ΡΠΎΠ΄Π° β 20, ΡΡΠΈΠ½Π°ΡΡΠΈΠΉΡΠΎΡΡΠ°Ρ β 20, ΠΏΡΠ΅ΠΏΠ°ΡΠ°Ρ ΠΠ-7 (ΠΈΠ»ΠΈ ΠΠ-10) β 2. Π’Π΅ΠΌΠΏΠ΅ΡΠ°ΡΡΡΠ° ΡΠ°ΡΡΠ²ΠΎΡΠ° β 70β80 Β°Π‘, Π²ΡΠ΅ΠΌΡ ΠΎΠ±ΡΠ°Π±ΠΎΡΠΊΠΈ β 5-10 ΠΌΠΈΠ½.
- ΠΠΈΠ΄ΠΊΠΎΠ΅ ΡΡΠ΅ΠΊΠ»ΠΎ β 25, ΠΊΠ°Π»ΡΡΠΈΠ½ΠΈΡΠΎΠ²Π°Π½Π½Π°Ρ ΡΠΎΠ΄Π° β 5, ΡΡΠΈΠ½Π°ΡΡΠΈΠΉΡΠΎΡΡΠ°Ρ β 10. Π’Π΅ΠΌΠΏΠ΅ΡΠ°ΡΡΡΠ° ΡΠ°ΡΡΠ²ΠΎΡΠ° β 75β80 Β°Π‘, Π²ΡΠ΅ΠΌΡ ΠΎΠ±ΡΠ°Π±ΠΎΡΠΊΠΈ β 15β20 ΠΌΠΈΠ½.
Π’ΡΠ°Π²Π»Π΅Π½ΠΈΠ΅. Π‘ΡΠ°Π½Π΄Π°ΡΡΠ½Π°Ρ ΠΏΠΎΠ΄Π³ΠΎΡΠΎΠ²ΠΊΠ° Π΄Π΅ΡΠ°Π»Π΅ΠΉ ΠΏΠΎΠ΄ ΠΏΠΎΠΊΡΡΡΠΈΠ΅, ΠΎΠ±ΡΡΠ½ΠΎ ΡΠΎΡΡΠΎΡΡΠ°Ρ Π² ΠΎΠ±Π΅Π·ΠΆΠΈΡΠΈΠ²Π°Π½ΠΈΠΈ ΠΈ Π΄Π΅ΠΊΠ°ΠΏΠΈΡΠΎΠ²Π°Π½ΠΈΠΈ, Π²ΠΏΠΎΠ»Π½Π΅ Π΄ΠΎΡΡΠ°ΡΠΎΡΠ½Π° Π΄Π»Ρ Π±ΠΎΠ»ΡΡΠΈΠ½ΡΡΠ²Π° ΡΠ»ΡΡΠ°Π΅Π². ΠΠ΄Π½Π°ΠΊΠΎ Π΄Π»Ρ Π΄Π΅ΡΠ°Π»Π΅ΠΉ, ΠΈΠΌΠ΅ΡΡΠΈΡ Π³Π»ΡΡ ΠΈΠ΅ ΠΎΡΠ²Π΅ΡΡΡΠΈΡ, ΠΏΠ°Π·ΡΡ ΠΈ ΠΈ Ρ.ΠΏ., Π½Π΅ΠΎΠ±Ρ ΠΎΠ΄ΠΈΠΌΠΎ ΠΏΡΠΎΠ²ΠΎΠ΄ΠΈΡΡ ΠΏΡΠΎΡΠ΅ΡΡ ΡΡΠ°Π²Π»Π΅Π½ΠΈΡ.
Π§Π΅ΡΠ½ΡΠ΅ ΠΌΠ΅ΡΠ°Π»Π»Ρ ΡΡΠ°Π²ΡΡ Π² ΡΠ°ΡΡΠ²ΠΎΡΠ°Ρ :
- Π‘Π΅ΡΠ½Π°Ρ ΠΊΠΈΡΠ»ΠΎΡΠ° β 90β130, ΡΠΎΠ»ΡΠ½Π°Ρ ΠΊΠΈΡΠ»ΠΎΡΠ° β 80β100, ΡΡΠΎΡΡΠΎΠΏΠΈΠ½ β 0,5. Π’Π΅ΠΌΠΏΠ΅ΡΠ°ΡΡΡΠ° ΡΠ°ΡΡΠ²ΠΎΡΠ° β 30β40 Β°Π‘, Π²ΡΠ΅ΠΌΡ ΠΎΠ±ΡΠ°Π±ΠΎΡΠΊΠΈ β Π΄ΠΎ 1 Ρ.
- Π‘ΠΎΠ»ΡΠ½Π°Ρ ΠΊΠΈΡΠ»ΠΎΡΠ° β 200, ΡΡΠΎΡΡΠΎΠΏΠΈΠ½ βΒ 0,5. Π’Π΅ΠΌΠΏΠ΅ΡΠ°ΡΡΡΠ° ΡΠ°ΡΡΠ²ΠΎΡΠ° β 30β35 Β°Π‘, Π²ΡΠ΅ΠΌΡ ΠΎΠ±ΡΠ°Π±ΠΎΡΠΊΠΈ β 15β20 ΠΌΠΈΠ½.
ΠΠ΅Π΄Ρ ΠΈ Π΅Π΅ ΡΠΏΠ»Π°Π²Ρ ΡΡΠ°Π²ΡΡ Π² ΡΠ°ΡΡΠ²ΠΎΡΠ°Ρ :
- Π‘Π΅ΡΠ½Π°Ρ ΠΊΠΈΡΠ»ΠΎΡΠ° β 25β40, Ρ ΡΠΎΠΌΠΎΠ²ΡΠΉ Π°Π½Π³ΠΈΠ΄ΡΠΈΠ΄ β 150β200. Π’Π΅ΠΌΠΏΠ΅ΡΠ°ΡΡΡΠ° ΡΠ°ΡΡΠ²ΠΎΡΠ° βΒ 25 Β°Π‘, Π²ΡΠ΅ΠΌΡ ΠΎΠ±ΡΠ°Π±ΠΎΡΠΊΠΈ β 5β10 ΠΌΠΈΠ½.Β
- Π₯ΡΠΎΠΌΠΎΠ²ΡΠΉ Π°Π½Π³ΠΈΠ΄ΡΠΈΠ΄ β 350, Ρ Π»ΠΎΡΠΈΡΡΡΠΉ Π½Π°ΡΡΠΈΠΉ β 50. Π’Π΅ΠΌΠΏΠ΅ΡΠ°ΡΡΡΠ° ΡΠ°ΡΡΠ²ΠΎΡΠ° β 18β 25 Β°Π‘, Π²ΡΠ΅ΠΌΡ ΠΎΠ±ΡΠ°Π±ΠΎΡΠΊΠΈ β 5β15 ΠΌΠΈΠ½.
ΠΠ»ΡΠΌΠΈΠ½ΠΈΠΉ ΠΈ Π΅Π³ΠΎ ΡΠΏΠ»Π°Π²Ρ ΡΡΠ°Π²ΡΡ Π² ΡΠ°ΡΡΠ²ΠΎΡΠ°Ρ :
- ΠΠ΄ΠΊΠΈΠΉ Π½Π°ΡΡ β 50β100. Π’Π΅ΠΌΠΏΠ΅ΡΠ°ΡΡΡΠ° ΡΠ°ΡΡΠ²ΠΎΡΠ° β 40β60 Β°Π‘, Π²ΡΠ΅ΠΌΡ ΠΎΠ±ΡΠ°Π±ΠΎΡΠΊΠΈ β 5-10 Ρ.
- ΠΠ·ΠΎΡΠ½Π°Ρ ΠΊΠΈΡΠ»ΠΎΡΠ° β 35β40. Π’Π΅ΠΌΠΏΠ΅ΡΠ°ΡΡΡΠ° ΡΠ°ΡΡΠ²ΠΎΡΠ° β 18β25 Β°Π‘ , Π²ΡΠ΅ΠΌΡ ΠΎΠ±ΡΠ°Π±ΠΎΡΠΊΠΈ β 3β5 Ρ.
ΠΠ΅ΠΊΠ°ΠΏΠΈΡΠΎΠ²Π°Π½ΠΈΠ΅. ΠΡΠΎΡ ΠΏΡΠΎΡΠ΅ΡΡ ΠΏΡΠ΅Π΄ΡΡΠ°Π²Π»ΡΠ΅Ρ ΡΠΎΠ±ΠΎΠΉ ΡΠ΄Π°Π»Π΅Π½ΠΈΠ΅ Ρ ΠΏΠΎΠ²Π΅ΡΡ Π½ΠΎΡΡΠΈ ΠΌΠ΅ΡΠ°Π»Π»Π° ΡΠ°Π·Π»ΠΈΡΠ½ΡΡ ΠΏΠ»Π΅Π½ΠΎΠΊ, ΠΌΠ΅ΡΠ°ΡΡΠΈΡ ΠΎΡΠ°ΠΆΠ΄Π΅Π½ΠΈΡ ΠΌΠ΅ΡΠ°Π»Π»ΠΎΠ². ΠΠ΅ΠΊΠ°ΠΏΠΈΡΠΎΠ²Π°Π½ΠΈΠ΅ ΠΏΡΠΎΠ²ΠΎΠ΄ΡΡ Π½Π΅ΠΏΠΎΡΡΠ΅Π΄ΡΡΠ²Π΅Π½Π½ΠΎ ΠΏΠ΅ΡΠ΅Π΄ ΠΏΠΎΠΊΡΡΡΠΈΠ΅ΠΌ ΠΎΡΠ½ΠΎΠ²Π½ΠΎΠ³ΠΎ ΠΌΠ΅ΡΠ°Π»Π»Π° ΡΠΎΠΎΡΠ²Π΅ΡΡΡΠ²ΡΡΡΠ΅ΠΉ ΠΏΠ»Π΅Π½ΠΊΠΎΠΉ Π΄ΡΡΠ³ΠΎΠ³ΠΎ ΠΌΠ΅ΡΠ°Π»Π»Π°.
Π§Π΅ΡΠ½ΡΠ΅ ΠΌΠ΅ΡΠ°Π»Π»Ρ Π΄Π΅ΠΊΠ°ΠΏΠΈΡΡΡΡ Π² ΡΠ»Π΅Π΄ΡΡΡΠΈΡ ΡΠ°ΡΡΠ²ΠΎΡΠ°Ρ :
- Π‘Π΅ΡΠ½Π°Ρ ΠΊΠΈΡΠ»ΠΎΡΠ° β 30β50. Π’Π΅ΠΌΠΏΠ΅ΡΠ°ΡΡΡΠ° ΡΠ°ΡΡΠ²ΠΎΡΠ° β 20 Β°Π‘, Π²ΡΠ΅ΠΌΡ ΠΎΠ±ΡΠ°Π±ΠΎΡΠΊΠΈ β 20β60 Ρ.
- Π‘ΠΎΠ»ΡΠ½Π°Ρ ΠΊΠΈΡΠ»ΠΎΡΠ° β 25β45. Π’Π΅ΠΌΠΏΠ΅ΡΠ°ΡΡΡΠ° ΡΠ°ΡΡΠ²ΠΎΡΠ° β 20 Β°Π‘, Π²ΡΠ΅ΠΌΡ ΠΎΠ±ΡΠ°Π±ΠΎΡΠΊΠΈ 15β 40 Ρ.
ΠΠ΅Π΄Ρ ΠΈ Π΅Π΅ ΡΠΏΠ»Π°Π²Ρ Π΄Π΅ΠΊΠ°ΠΏΠΈΡΡΡΡ Π² ΡΠ°ΡΡΠ²ΠΎΡΠ°Ρ :
- Π‘Π΅ΡΠ½Π°Ρ ΠΊΠΈΡΠ»ΠΎΡΠ° β 5. Π’Π΅ΠΌΠΏΠ΅ΡΠ°ΡΡΡΠ° ΡΠ°ΡΡΠ²ΠΎΡΠ° β 18β20 Β°Π‘, Π²ΡΠ΅ΠΌΡ ΠΎΠ±ΡΠ°Π±ΠΎΡΠΊΠΈ β 20 Ρ.
- Π‘ΠΎΠ»ΡΠ½Π°Ρ ΠΊΠΈΡΠ»ΠΎΡΠ° β 10. Π’Π΅ΠΌΠΏΠ΅ΡΠ°ΡΡΡΠ° ΡΠ°ΡΡΠ²ΠΎΡΠ° β 20β25 Β°Π‘, Π²ΡΠ΅ΠΌΡ ΠΎΠ±ΡΠ°Π±ΠΎΡΠΊΠΈ β 10-15 Ρ.
ΠΠ»ΡΠΌΠΈΠ½ΠΈΠΉ ΠΈ Π΅Π³ΠΎ ΡΠΏΠ»Π°Π²Ρ Π΄Π΅ΠΊΠ°ΠΏΠΈΡΡΡΡ Π² ΡΠ°ΡΡΠ²ΠΎΡΠ°Ρ :
- ΠΠ·ΠΎΡΠ½Π°Ρ ΠΊΠΈΡΠ»ΠΎΡΠ° β 10β15. Π’Π΅ΠΌΠΏΠ΅ΡΠ°ΡΡΡΠ° ΡΠ°ΡΡΠ²ΠΎΡΠ° β 20 Β°Π‘, Π²ΡΠ΅ΠΌΡ ΠΎΠ±ΡΠ°Π±ΠΎΡΠΊΠΈ β 5-15 Ρ.
- ΠΠ΄ΠΊΠΈΠΉ Π½Π°ΡΡ β 150, Ρ Π»ΠΎΡΠΈΡΡΡΠΉ Π½Π°ΡΡΠΈΠΉ β 30. Π’Π΅ΠΌΠΏΠ΅ΡΠ°ΡΡΡΠ° ΡΠ°ΡΡΠ²ΠΎΡΠ° β 30β40 Β°Π‘, Π²ΡΠ΅ΠΌΡ ΠΎΠ±ΡΠ°Π±ΠΎΡΠΊΠΈ β 5β10 Ρ.
ΠΠΎΡΠ»Π΅ ΠΊΠ°ΠΆΠ΄ΠΎΠ³ΠΎ ΠΏΡΠΎΡΠ΅ΡΡΠ° ΠΏΠΎΠ΄Π³ΠΎΡΠΎΠ²ΠΊΠΈ Π΄Π΅ΡΠ°Π»Ρ ΠΏΡΠΎΠΌΡΠ²Π°ΡΡ Π² Π³ΠΎΡΡΡΠ΅ΠΉ, Π° Π·Π°ΡΠ΅ΠΌ Π² Ρ ΠΎΠ»ΠΎΠ΄Π½ΠΎΠΉ Π²ΠΎΠ΄Π΅.
ΠΠΈΠΊΠ΅Π»ΠΈΡΠΎΠ²Π°Π½ΠΈΠ΅ ΠΌΠ΅Π΄ΠΈ ΠΈ Π΅Π΅ ΡΠΏΠ»Π°Π²ΠΎΠ²
ΠΠΎΠ΄Π³ΠΎΡΠΎΠ²Π»Π΅Π½Π½ΡΡ (ΠΎΠ±Π΅Π·ΠΆΠΈΡΠ΅Π½Π½ΡΡ, ΠΏΡΠΎΡΡΠ°Π²Π»Π΅Π½Π½ΡΡ ΠΈ Π΄Π΅ΠΊΠ°ΠΏΠΈΡΠΎΠ²Π°Π½Π½ΡΡ) Π΄Π΅ΡΠ°Π»Ρ ΠΏΠΎΠ΄Π²Π΅ΡΠΈΠ²Π°ΡΡ Π² ΡΠ°ΡΡΠ²ΠΎΡ Π΄Π»Ρ Π½ΠΈΠΊΠ΅Π»ΠΈΡΠΎΠ²Π°Π½ΠΈΡ. ΠΠ΄Π΅ΡΡ Π΅ΡΡΡ ΠΎΠ΄Π½Π° ΡΠΎΠ½ΠΊΠΎΡΡΡ, ΠΈ Π΅ΡΠ»ΠΈ Π΅Ρ ΠΏΡΠ΅Π½Π΅Π±ΡΠ΅ΡΡ, ΡΠΎ ΠΏΡΠΎΡΠ΅ΡΡ ΠΎΡΠ°ΠΆΠ΄Π΅Π½ΠΈΡ Π½ΠΈΠΊΠ΅Π»Ρ Π½Π΅ ΠΏΠΎΠΉΠ΄Π΅Ρ. ΠΠ΅ΡΠ°Π»Ρ Π΄ΠΎΠ»ΠΆΠ½Π° Π±ΡΡΡ ΠΏΠΎΠ΄Π²Π΅ΡΠ΅Π½Π° Π² ΡΠ°ΡΡΠ²ΠΎΡ Π½Π° Π°Π»ΡΠΌΠΈΠ½ΠΈΠ΅Π²ΠΎΠΉ ΠΈΠ»ΠΈ ΠΆΠ΅Π»Π΅Π·Π½ΠΎΠΉ (ΡΡΠ°Π»ΡΠ½ΠΎΠΉ) ΠΏΡΠΎΠ²ΠΎΠ»ΠΎΠΊΠ΅. Π ΠΊΡΠ°ΠΉΠ½Π΅ΠΌ ΡΠ»ΡΡΠ°Π΅ ΠΏΡΠΈ ΠΎΠΏΡΡΠΊΠ°Π½ΠΈΠΈ Π΄Π΅ΡΠ°Π»ΠΈ Π² ΡΠ°ΡΡΠ²ΠΎΡ Π΅Π΅ Π½Π΅ΠΎΠ±Ρ ΠΎΠ΄ΠΈΠΌΠΎ ΠΊΠΎΡΠ½ΡΡΡΡΡ ΠΆΠ΅Π»Π΅Π·Π½ΡΠΌ ΠΈΠ»ΠΈ Π°Π»ΡΠΌΠΈΠ½ΠΈΠ΅Π²ΡΠΌ ΠΏΡΠ΅Π΄ΠΌΠ΅ΡΠΎΠΌ.
ΠΡΠΈ Β«ΡΠ²ΡΡΠ΅Π½Π½ΠΎΠ΄Π΅ΠΉΡΡΠ²ΠΈΡΒ» Π½ΡΠΆΠ½Ρ Π΄Π»Ρ ΡΠΎΠ³ΠΎ, ΡΡΠΎΠ±Ρ Π΄Π°ΡΡ ΡΡΠ°ΡΡ ΠΏΡΠΎΡΠ΅ΡΡΡ Π½ΠΈΠΊΠ΅Π»ΠΈΡΠΎΠ²Π°Π½ΠΈΡ, ΡΠ°ΠΊ ΠΊΠ°ΠΊ Ρ ΠΌΠ΅Π΄ΠΈ ΠΌΠ΅Π½ΡΡΠΈΠΉ ΡΠ»Π΅ΠΊΡΡΠΎΠΎΡΡΠΈΡΠ°ΡΠ΅Π»ΡΠ½ΡΠΉ ΠΏΠΎΡΠ΅Π½ΡΠΈΠ°Π» ΠΏΠΎ ΠΎΡΠ½ΠΎΡΠ΅Π½ΠΈΡ ΠΊ Π½ΠΈΠΊΠ΅Π»Ρ. Π’ΠΎΠ»ΡΠΊΠΎ ΠΏΡΠΈΡΠΎΠ΅Π΄ΠΈΠ½Π΅Π½ΠΈΠ΅ ΠΈΠ»ΠΈ ΠΊΠ°ΡΠ°Π½ΠΈΠ΅ Π΄Π΅ΡΠ°Π»ΠΈ Π±ΠΎΠ»Π΅Π΅ ΡΠ»Π΅ΠΊΡΡΠΎΠΎΡΡΠΈΡΠ°ΡΠ΅Π»ΡΠ½ΡΠΌ ΠΌΠ΅ΡΠ°Π»Π»ΠΎΠΌ Π΄Π°Π΅Ρ ΡΡΠ°ΡΡ ΠΏΡΠΎΡΠ΅ΡΡΡ.
ΠΡΠΈΠ²ΠΎΠ΄ΠΈΠΌ ΡΠΎΡΡΠ°Π² Π½Π΅ΠΊΠΎΡΠΎΡΡΡ ΠΈΠ·Π²Π΅ΡΡΠ½ΡΡ ΡΠ°ΡΡΠ²ΠΎΡΠΎΠ² Π΄Π»Ρ Ρ ΠΈΠΌΠΈΡΠ΅ΡΠΊΠΎΠ³ΠΎ Π½ΠΈΠΊΠ΅Π»ΠΈΡΠΎΠ²Π°Π½ΠΈΡ ΠΌΠ΅Π΄ΠΈ ΠΈ Π΅Π΅ ΡΠΏΠ»Π°Π²ΠΎΠ² (Π²ΡΠ΅ Π΄Π°Π½ΠΎ Π² Π³/Π»):
- Π₯Π»ΠΎΡΠΈΡΡΡΠΉ Π½ΠΈΠΊΠ΅Π»Ρ β 21, Π³ΠΈΠΏΠΎΡΠΎΡΡΠΈΡ Π½Π°ΡΡΠΈΡ β 24, ΡΠΊΡΡΡΠ½ΠΎΠΊΠΈΡΠ»ΡΠΉ Π½Π°ΡΡΠΈΠΉ β 10, ΡΡΠ»ΡΡΠΈΠ΄ ΡΠ²ΠΈΠ½ΡΠ° β 15 ΠΌΠ³/Π». Π’Π΅ΠΌΠΏΠ΅ΡΠ°ΡΡΡΠ° ΡΠ°ΡΡΠ²ΠΎΡΠ° β 97 Β°Π‘, ΡΠ β 5,2, ΡΠΊΠΎΡΠΎΡΡΡ Π½Π°ΡΠ°ΡΠΈΠ²Π°Π½ΠΈΡ ΠΏΠ»Π΅Π½ΠΊΠΈ β 15 ΠΌΠΊΠΌ/Ρ.
- Π₯Π»ΠΎΡΠΈΡΡΡΠΉ Π½ΠΈΠΊΠ΅Π»Ρ β 20, Π³ΠΈΠΏΠΎΡΠΎΡΡΠΈΡ Π½Π°ΡΡΠΈΡ β 27, ΡΠ½ΡΠ°ΡΠ½ΠΎΠΊΠΈΡΠ»ΡΠΉ Π½Π°ΡΡΠΈΠΉ β 16. Π’Π΅ΠΌΠΏΠ΅ΡΠ°ΡΡΡΠ° ΡΠ°ΡΡΠ²ΠΎΡΠ° β 95 Β°Π‘, ΡΠ β 5, ΡΠΊΠΎΡΠΎΡΡΡ Π½Π°ΡΠ°ΡΠΈΠ²Π°Π½ΠΈΡ β 35 ΠΌΠΊΠΌ/Ρ.
- Π‘Π΅ΡΠ½ΠΎΠΊΠΈΡΠ»ΡΠΉ Π½ΠΈΠΊΠ΅Π»Ρ β 21, Π³ΠΈΠΏΠΎΡΠΎΡΡΠΈΡ Π½Π°ΡΡΠΈΡ β 24, ΡΠΊΡΡΡΠ½ΠΎΠΊΠΈΡΠ»ΡΠΉ Π½Π°ΡΡΠΈΠΉ β 10, ΠΌΠ°Π»Π΅ΠΈΠ½ΠΎΠ²ΡΠΉ Π°Π½Π³ΠΈΠ΄ΡΠΈΠ΄ β 1,5. Π’Π΅ΠΌΠΏΠ΅ΡΠ°ΡΡΡΠ° ΡΠ°ΡΡΠ²ΠΎΡΠ° β 83 Β°Π‘, ΡΠ β 5,2, ΡΠΊΠΎΡΠΎΡΡΡ Π½Π°ΡΠ°ΡΠΈΠ²Π°Π½ΠΈΡ β 10 ΠΌΠΊΠΌ/Ρ.
- Π‘Π΅ΡΠ½ΠΎΠΊΠΈΡΠ»ΡΠΉ Π½ΠΈΠΊΠ΅Π»Ρ β 23, Π³ΠΈΠΏΠΎΡΠΎΡΡΠΈΡ Π½Π°ΡΡΠΈΡ β 27, ΠΌΠ°Π»Π΅ΠΈΠ½ΠΎΠ²ΡΠΉ Π°Π½Π³ΠΈΠ΄ΡΠΈΠ΄ β 1,5, ΡΠ΅ΡΠ½ΠΎΠΊΠΈΡΠ»ΡΠΉ Π°ΠΌΠΌΠΎΠ½ΠΈΠΉ β 50, ΡΠΊΡΡΡΠ½Π°Ρ ΠΊΠΈΡΠ»ΠΎΡΠ° β 20 ΠΌΠ»/Π». Π’Π΅ΠΌΠΏΠ΅ΡΠ°ΡΡΡΠ° ΡΠ°ΡΡΠ²ΠΎΡΠ° β 93 Β°Π‘, ΡΠ β 5,5, ΡΠΊΠΎΡΠΎΡΡΡ Π½Π°ΡΠ°ΡΠΈΠ²Π°Π½ΠΈΡ β 20 ΠΌΠΊΠΌ/Ρ.
ΠΠ΄Π΅ΡΡ (ΠΈ Π΄Π°Π»Π΅Π΅) ΡΠ΅ΡΠ½ΠΎΠΊΠΈΡΠ»ΡΠΉ Π½ΠΈΠΊΠ΅Π»Ρ, Ρ Π»ΠΎΡΠΈΡΡΡΠΉ Π½ΠΈΠΊΠ΅Π»Ρ ΠΈ Π³ΠΈΠΏΠΎΡΠΎΡΡΠΈΡ Π½Π°ΡΡΠΈΡ β ΠΊΡΠΈΡΡΠ°Π»Π»ΠΎΠ³ΠΈΠ΄ΡΠ°ΡΡ.
ΠΠ»Ρ ΠΏΡΠΈΠ³ΠΎΡΠΎΠ²Π»Π΅Π½ΠΈΡ ΡΠ°ΡΡΠ²ΠΎΡΠ° Π΄Π»Ρ Π½ΠΈΠΊΠ΅Π»ΠΈΡΠΎΠ²Π°Π½ΠΈΡ Π½ΡΠΆΠ½ΠΎ ΡΠ°ΡΡΠ²ΠΎΡΠΈΡΡ Π²ΡΠ΅ ΠΊΠΎΠΌΠΏΠΎΠ½Π΅Π½ΡΡ, ΠΊΡΠΎΠΌΠ΅ Π³ΠΈΠΏΠΎΡΠΎΡΡΠΈΡΠ° Π½Π°ΡΡΠΈΡ, ΠΈ Π½Π°Π³ΡΠ΅ΡΡ Π΅Π³ΠΎ Π΄ΠΎ Π½ΡΠΆΠ½ΠΎΠΉ ΡΠ΅ΠΌΠΏΠ΅ΡΠ°ΡΡΡΡ. ΠΠΈΠΏΠΎΡΠΎΡΡΠΈΡ Π½Π°ΡΡΠΈΡ Π²Π²ΠΎΠ΄ΠΈΡΡΡ Π² ΡΠ°ΡΡΠ²ΠΎΡ Π½Π΅ΠΏΠΎΡΡΠ΅Π΄ΡΡΠ²Π΅Π½Π½ΠΎ ΠΏΠ΅ΡΠ΅Π΄ Π·Π°Π²Π΅ΡΠΈΠ²Π°Π½ΠΈΠ΅ΠΌ Π΄Π΅ΡΠ°Π»ΠΈ Π΄Π»Ρ Π½ΠΈΠΊΠ΅Π»ΠΈΡΠΎΠ²Π°Π½ΠΈΡ. ΠΡΠΎΡ ΠΏΠΎΡΡΠ΄ΠΎΠΊ ΠΊΠ°ΡΠ°Π΅ΡΡΡ Π²ΡΠ΅Ρ ΡΠ΅ΡΠ΅ΠΏΡΠΎΡΠΎΠ², Π³Π΄Π΅ ΠΈΠΌΠ΅Π΅ΡΡΡ Π³ΠΈΠΏΠΎΡΠΎΡΡΠΈΡ Π½Π°ΡΡΠΈΡ.
Π Π°ΡΡΠ²ΠΎΡ Π΄Π»Ρ Π½ΠΈΠΊΠ΅Π»ΠΈΡΠΎΠ²Π°Π½ΠΈΡ ΡΠ°Π·Π²ΠΎΠ΄ΡΡ Π² Π»ΡΠ±ΠΎΠΉ ΡΠΌΠ°Π»ΠΈΡΠΎΠ²Π°Π½Π½ΠΎΠΉ ΠΏΠΎΡΡΠ΄Π΅ (ΠΌΠΈΡΠΊΠ°, Π³Π»ΡΠ±ΠΎΠΊΠ°Ρ ΡΠΊΠΎΠ²ΠΎΡΠΎΠ΄Π°, ΠΊΠ°ΡΡΡΡΠ»ΡΠΊΠ° ΠΈ Ρ.ΠΏ.) Π±Π΅Π· ΠΏΠΎΠ²ΡΠ΅ΠΆΠ΄Π΅Π½ΠΈΠΉ Π½Π° ΠΏΠΎΠ²Π΅ΡΡ Π½ΠΎΡΡΠΈ ΡΠΌΠ°Π»ΠΈ. ΠΠΎΠ·ΠΌΠΎΠΆΠ½ΡΠΉ ΠΎΡΠ°Π΄ΠΎΠΊ Π½ΠΈΠΊΠ΅Π»Ρ Π½Π° ΡΡΠ΅Π½ΠΊΠ°Ρ ΠΏΠΎΡΡΠ΄Ρ Π»Π΅Π³ΠΊΠΎ ΡΠ΄Π°Π»ΡΠ΅ΡΡΡ Π°Π·ΠΎΡΠ½ΠΎΠΉ ΠΊΠΈΡΠ»ΠΎΡΠΎΠΉ (50%-Π½ΡΠΉ ΡΠ°ΡΡΠ²ΠΎΡ).
ΠΠΎΠΏΡΡΡΠΈΠΌΠ°Ρ ΠΏΠ»ΠΎΡΠ½ΠΎΡΡΡ Π·Π°Π³ΡΡΠ·ΠΊΠΈ Π²Π°Π½Π½Ρ β Π΄ΠΎ 2 Π΄ΠΌ2/Π».
ΠΠΈΠΊΠ΅Π»ΠΈΡΠΎΠ²Π°Π½ΠΈΠ΅ Π°Π»ΡΠΌΠΈΠ½ΠΈΡ ΠΈ Π΅Π³ΠΎ ΡΠΏΠ»Π°Π²ΠΎΠ²
Π£ΡΡΠΈΡΠ΅, ΡΡΠΎ Π΄Π»Ρ Π°Π»ΡΠΌΠΈΠ½ΠΈΡ ΠΈ Π΅Π³ΠΎ ΡΠΏΠ»Π°Π²ΠΎΠ² ΠΏΠ΅ΡΠ΅Π΄ Ρ ΠΈΠΌΠΈΡΠ΅ΡΠΊΠΈΠΌ Π½ΠΈΠΊΠ΅Π»ΠΈΡΠΎΠ²Π°Π½ΠΈΠ΅ΠΌ ΠΏΡΠΎΠ²ΠΎΠ΄ΡΡ Π΅ΡΠ΅ ΠΎΠ΄Π½Ρ ΠΎΠ±ΡΠ°Π±ΠΎΡΠΊΡ (ΠΏΠΎΡΠ»Π΅ Π²ΡΠ΅Ρ ΠΏΠΎΠ΄Π³ΠΎΡΠΎΠ²ΠΈΡΠ΅Π»ΡΠ½ΡΡ ΠΎΠΏΠ΅ΡΠ°ΡΠΈΠΉ) β ΡΠ°ΠΊ Π½Π°Π·ΡΠ²Π°Π΅ΠΌΡΡ ΡΠΈΠ½ΠΊΠ°ΡΠ½ΡΡ.
ΠΠΈΠΆΠ΅ ΠΏΡΠΈΠ²Π΅Π΄Π΅Π½Ρ ΡΠ΅ΡΠ΅ΠΏΡΡ ΡΠ°ΡΡΠ²ΠΎΡΠΎΠ² Π΄Π»Ρ ΡΠΈΠ½ΠΊΠ°ΡΠ½ΠΎΠΉ ΠΎΠ±ΡΠ°Π±ΠΎΡΠΊΠΈ.
ΠΠ»Ρ Π°Π»ΡΠΌΠΈΠ½ΠΈΡ:
- ΠΠ΄ΠΊΠΈΠΉ Π½Π°ΡΡ β 250, ΠΎΠΊΠΈΡΡ ΡΠΈΠ½ΠΊΠ° β 55. Π’Π΅ΠΌΠΏΠ΅ΡΠ°ΡΡΡΠ° ΡΠ°ΡΡΠ²ΠΎΡΠ° β 20 Β°Π‘, Π²ΡΠ΅ΠΌΡ ΠΎΠ±ΡΠ°Π±ΠΎΡΠΊΠΈ β 3β5 Ρ.
- ΠΠ΄ΠΊΠΈΠΉ Π½Π°ΡΡ β 120, ΡΠ΅ΡΠ½ΠΎΠΊΠΈΡΠ»ΡΠΉ ΡΠΈΠ½ΠΊ 40. Π’Π΅ΠΌΠΏΠ΅ΡΠ°ΡΡΡΠ° ΡΠ°ΡΡΠ²ΠΎΡΠ° β 20 Β°Π‘, Π²ΡΠ΅ΠΌΡ ΠΎΠ±ΡΠ°Π±ΠΎΡΠΊΠΈ β 1,2 ΠΌΠΈΠ½.
ΠΠ»Ρ Π»ΠΈΡΠ΅ΠΉΠ½ΡΡ Π°Π»ΡΠΌΠΈΠ½ΠΈΠ΅Π²ΡΡ ΡΠΏΠ»Π°Π²ΠΎΠ² (ΡΠΈΠ»ΡΠΌΠΈΠ½ΠΎΠ²):
- ΠΠ΄ΠΊΠΈΠΉ Π½Π°ΡΡ β 10, ΠΎΠΊΠΈΡΡ ΡΠΈΠ½ΠΊΠ° β 5, ΡΠ΅Π³Π½Π΅ΡΠΎΠ²Π° ΡΠΎΠ»Ρ (ΠΊΡΠΈΡΡΠ°Π»Π»ΠΎΠ³ΠΈΠ΄ΡΠ°Ρ) β 10. Π’Π΅ΠΌΠΏΠ΅ΡΠ°ΡΡΡΠ° ΡΠ°ΡΡΠ²ΠΎΡΠ° β 20 Β°Π‘, Π²ΡΠ΅ΠΌΡ ΠΎΠ±ΡΠ°Π±ΠΎΡΠΊΠΈ β 2 ΠΌΠΈΠ½.
ΠΠ»Ρ Π΄Π΅ΡΠΎΡΠΌΠΈΡΡΠ΅ΠΌΡΡ Π°Π»ΡΠΌΠΈΠ½ΠΈΠ΅Π²ΡΡ ΡΠΏΠ»Π°Π²ΠΎΠ² (Π΄ΡΡΠ°Π»Π΅ΠΉ):
- Π₯Π»ΠΎΡΠ½ΠΎΠ΅ ΠΆΠ΅Π»Π΅Π·ΠΎ (ΠΊΡΠΈΡΡΠ°Π»Π»ΠΎΠ³ΠΈΠ΄ΡΠ°Ρ) β 1, Π΅Π΄ΠΊΠΈΠΉ Π½Π°ΡΡ β 525, ΠΎΠΊΠΈΡΡ ΡΠΈΠ½ΠΊΠ° β 100, ΡΠ΅Π³Π½Π΅ΡΠΎΠ²Π° ΡΠΎΠ»Ρ β 10. Π’Π΅ΠΌΠΏΠ΅ΡΠ°ΡΡΡΠ° ΡΠ°ΡΡΠ²ΠΎΡΠ° β 25 Β°Π‘, Π²ΡΠ΅ΠΌΡ ΠΎΠ±ΡΠ°Π±ΠΎΡΠΊΠΈ β 30β60 Ρ.
ΠΡΠΈ ΠΏΠΎΠ΄Π³ΠΎΡΠΎΠ²ΠΊΠ΅ ΡΠ°ΡΡΠ²ΠΎΡΠΎΠ² Π΄Π»Ρ ΡΠΈΠ½ΠΊΠ°ΡΠ½ΠΎΠΉ ΠΎΠ±ΡΠ°Π±ΠΎΡΠΊΠΈ ΠΏΠΎΡΡΡΠΏΠ°ΡΡ ΡΠ»Π΅Π΄ΡΡΡΠΈΠΌ ΠΎΠ±ΡΠ°Π·ΠΎΠΌ. ΠΡΠ΄Π΅Π»ΡΠ½ΠΎ Π² ΠΏΠΎΠ»ΠΎΠ²ΠΈΠ½Π΅ Π²ΠΎΠ΄Ρ ΡΠ°ΡΡΠ²ΠΎΡΡΡΡ Π΅Π΄ΠΊΠΈΠΉ Π½Π°ΡΡ, Π² Π΄ΡΡΠ³ΠΎΠΉ ΠΏΠΎΠ»ΠΎΠ²ΠΈΠ½Π΅ β ΠΎΡΡΠ°Π»ΡΠ½ΡΠ΅ Ρ ΠΈΠΌΡΠ΅Π°ΠΊΡΠΈΠ²Ρ. ΠΠ°ΡΠ΅ΠΌ ΠΎΠ±Π° ΡΠ°ΡΡΠ²ΠΎΡΠ° ΡΠ»ΠΈΠ²Π°ΡΡ Π²ΠΌΠ΅ΡΡΠ΅.
ΠΠΎΡΠ»Π΅ ΡΠΈΠ½ΠΊΠ°ΡΠ½ΠΎΠΉ ΠΎΠ±ΡΠ°Π±ΠΎΡΠΊΠΈ Π΄Π΅ΡΠ°Π»Ρ ΠΏΡΠΎΠΌΡΠ²Π°ΡΡ Π² Π³ΠΎΡΡΡΠ΅ΠΉ, Π° Π·Π°ΡΠ΅ΠΌ Π² Ρ ΠΎΠ»ΠΎΠ΄Π½ΠΎΠΉ Π²ΠΎΠ΄Π΅ ΠΈ Π·Π°Π²Π΅ΡΠΈΠ²Π°ΡΡ Π² ΡΠ°ΡΡΠ²ΠΎΡ Π΄Π»Ρ Π½ΠΈΠΊΠ΅Π»ΠΈΡΠΎΠ²Π°Π½ΠΈΡ.
ΠΠΈΠΆΠ΅ ΠΏΡΠΈΠ²Π΅Π΄Π΅Π½Ρ ΡΠ΅ΡΡΡΠ΅ ΡΠ°ΡΡΠ²ΠΎΡΠ° Π΄Π»Ρ Ρ ΠΈΠΌΠΈΡΠ΅ΡΠΊΠΎΠ³ΠΎ Π½ΠΈΠΊΠ΅Π»ΠΈΡΠΎΠ²Π°Π½ΠΈΡ Π°Π»ΡΠΌΠΈΠ½ΠΈΡ ΠΈ Π΅Π³ΠΎ ΡΠΏΠ»Π°Π²ΠΎΠ²:
- Π₯Π»ΠΎΡΠΈΡΡΡΠΉ Π½ΠΈΠΊΠ΅Π»Ρ β 45, Π³ΠΈΠΏΠΎΡΠΎΡΡΠΈΡ Π½Π°ΡΡΠΈΡ β 20, Ρ Π»ΠΎΡΠΈΡΡΡΠΉ Π°ΠΌΠΌΠΎΠ½ΠΈΠΉ β 45, Π»ΠΈΠΌΠΎΠ½Π½ΠΎΠΊΠΈΡΠ»ΡΠΉ Π½Π°ΡΡΠΈΠΉ β 45. Π’Π΅ΠΌΠΏΠ΅ΡΠ°ΡΡΡΠ° ΡΠ°ΡΡΠ²ΠΎΡΠ° 90 Β°Π‘, ΡΠ β 8,5, ΡΠΊΠΎΡΠΎΡΡΡ Π½Π°ΡΠ°ΡΠΈΠ²Π°Π½ΠΈΡ β 20 ΠΌΠΊΠΌ/Ρ.
- Π₯Π»ΠΎΡΠΈΡΡΡΠΉ Π½ΠΈΠΊΠ΅Π»Ρ β 35, Π³ΠΈΠΏΠΎΡΠΎΡΡΠΈΡ Π½Π°ΡΡΠΈΡ β 17, Ρ Π»ΠΎΡΠΈΡΡΡΠΉ Π°ΠΌΠΌΠΎΠ½ΠΈΠΉ β 40, Π»ΠΈΠΌΠΎΠ½Π½ΠΎΠΊΠΈΡΠ»ΡΠΉ Π½Π°ΡΡΠΈΠΉ β 40. Π’Π΅ΠΌΠΏΠ΅ΡΠ°ΡΡΡΠ° ΡΠ°ΡΡΠ²ΠΎΡΠ° β 80 Β°Π‘, ΡΠ β 8, ΡΠΊΠΎΡΠΎΡΡΡ Π½Π°ΡΠ°ΡΠΈΠ²Π°Π½ΠΈΡ β 12 ΠΌΠΊΠΌ/Ρ.
- Π‘Π΅ΡΠ½ΠΎΠΊΠΈΡΠ»ΡΠΉ Π½ΠΈΠΊΠ΅Π»Ρ β 20, Π³ΠΈΠΏΠΎΡΠΎΡΡΠΈΡ Π½Π°ΡΡΠΈΡ β 25, ΡΠΊΡΡΡΠ½ΠΎΠΊΠΈΡΠ»ΡΠΉ Π½Π°ΡΡΠΈΠΉ β 40, ΡΠ΅ΡΠ½ΠΎΠΊΠΈΡΠ»ΡΠΉ Π°ΠΌΠΌΠΎΠ½ΠΈΠΉ β 30. Π’Π΅ΠΌΠΏΠ΅ΡΠ°ΡΡΡΠ° ΡΠ°ΡΡΠ²ΠΎΡΠ° β 93 Β°Π‘, ΡΠ β 9, ΡΠΊΠΎΡΠΎΡΡΡ Π½Π°ΡΠ°ΡΠΈΠ²Π°Π½ΠΈΡ β 25 ΠΌΠΊΠΌ/Ρ.
- Π‘Π΅ΡΠ½ΠΎΠΊΠΈΡΠ»ΡΠΉ Π½ΠΈΠΊΠ΅Π»Ρ β 27, Π³ΠΈΠΏΠΎΡΠΎΡΡΠΈΡ Π½Π°ΡΡΠΈΡ β 27, ΠΏΠΈΡΠΎΡΠΎΡΡΠ°Ρ Π½Π°ΡΡΠΈΡ β 30, ΠΊΠ°ΡΠ±ΠΎΠ½Π°Ρ Π½Π°ΡΡΠΈΡ β 42. Π’Π΅ΠΌΠΏΠ΅ΡΠ°ΡΡΡΠ° ΡΠ°ΡΡΠ²ΠΎΡΠ° β 50 Β°Π‘, ΡΠ β 9,5, ΡΠΊΠΎΡΠΎΡΡΡ Π½Π°ΡΠ°ΡΠΈΠ²Π°Π½ΠΈΡ β 15 ΠΌΠΊΠΌ/Ρ.
ΠΠΎΠ²ΠΎΡΡ ΠΎ Ρ ΠΈΠΌΠΈΡΠ΅ΡΠΊΠΎΠΌ Π½ΠΈΠΊΠ΅Π»ΠΈΡΠΎΠ²Π°Π½ΠΈΠΈ, Π½Π΅Π»ΡΠ·Ρ Π½Π΅ ΠΎΡΠΌΠ΅ΡΠΈΡΡ ΡΠ»Π΅Π΄ΡΡΡΠ΅Π΅. ΠΠΈΠΊΠ΅Π»Π΅Π²ΠΎΠ΅ ΠΏΠΎΠΊΡΡΡΠΈΠ΅ ΠΈΠΌΠ΅Π΅Ρ Ρ ΠΎΡΠΎΡΡΡ ΡΠΌΠ°ΡΠΈΠ²Π°Π΅ΠΌΠΎΡΡΡ ΠΏΡΠΈΠΏΠΎΡΠΌΠΈ, ΡΡΠΎ ΠΏΠΎΠ·Π²ΠΎΠ»ΡΠ΅Ρ ΠΏΠΎΠ»ΡΡΠΈΡΡ Π΄ΠΎΠ±ΡΠΎΠΊΠ°ΡΠ΅ΡΡΠ²Π΅Π½Π½ΡΡ ΠΏΠ°ΠΉΠΊΡ Ρ ΠΏΠΎΠΌΠΎΡΡΡ ΠΌΡΠ³ΠΊΠΈΡ ΠΏΡΠΈΠΏΠΎΠ΅Π². ΠΠ±Π»Π°Π΄Π°Ρ Π²ΡΡΠΎΠΊΠΈΠΌΠΈ Π·Π°ΡΠΈΡΠ½ΡΠΌΠΈ ΡΠ²ΠΎΠΉΡΡΠ²Π°ΠΌΠΈ, ΠΎΠ½ΠΈ ΠΏΠΎΠ·Π²ΠΎΠ»ΡΡΡ ΠΏΠΎΠ»ΡΡΠ°ΡΡ ΡΡΠΎΠΉΠΊΠΈΠ΅ ΠΊ ΠΊΠΎΡΡΠΎΠ·ΠΈΠΈ ΠΏΠ°ΡΠ½ΡΠ΅ ΡΠΎΠ΅Π΄ΠΈΠ½Π΅Π½ΠΈΡ.
ΠΠΈΠΊΠ΅Π»ΠΈΡΠΎΠ²Π°Π½ΠΈΠ΅ ΡΡΠ°Π»ΠΈ
ΠΠ»Ρ Π½ΠΈΠΊΠ΅Π»ΠΈΡΠΎΠ²Π°Π½ΠΈΡ ΡΡΠ°Π»ΠΈ ΠΌΠΎΠΆΠ½ΠΎ ΠΈΡΠΏΠΎΠ»ΡΠ·ΠΎΠ²Π°ΡΡ ΠΎΠ΄ΠΈΠ½ ΠΈΠ· ΡΠ»Π΅Π΄ΡΡΡΠΈΡ ΡΠ΅ΡΠ΅ΠΏΡΠΎΠ²:
- Π₯Π»ΠΎΡΠΈΡΡΡΠΉ Π½ΠΈΠΊΠ΅Π»Ρ β 45, Π³ΠΈΠΏΠΎΡΠΎΡΡΠΈΡ Π½Π°ΡΡΠΈΡ β 20, Ρ Π»ΠΎΡΠΈΡΡΡΠΉ Π°ΠΌΠΌΠΎΠ½ΠΈΠΉ β 45, ΡΠΊΡΡΡΠ½ΠΎΠΊΠΈΡΠ»ΡΠΉ Π½Π°ΡΡΠΈΠΉ β 45. Π’Π΅ΠΌΠΏΠ΅ΡΠ°ΡΡΡΠ° ΡΠ°ΡΡΠ²ΠΎΡΠ° β 90 Β°Π‘, ΡΠ β 8.5, ΡΠΊΠΎΡΠΎΡΡΡ Π½Π°ΡΠ°ΡΠΈΠ²Π°Π½ΠΈΡ β 18 ΠΌΠΊΠΌ/Ρ.
- Π₯Π»ΠΎΡΠΈΡΡΡΠΉ Π½ΠΈΠΊΠ΅Π»Ρ β 30, Π³ΠΈΠΏΠΎΡΠΎΡΡΠΈΡ Π½Π°ΡΡΠΈΡ β 10, Ρ Π»ΠΎΡΠΈΡΡΡΠΉ Π°ΠΌΠΌΠΎΠ½ΠΈΠΉ β 50, Π»ΠΈΠΌΠΎΠ½Π½ΠΎΠΊΠΈΡΠ»ΡΠΉ Π½Π°ΡΡΠΈΠΉ β 100 Π’
takdelayut.ru
Π₯ΠΈΠΌΠΈΡΠ΅ΡΠΊΠΎΠ΅ Π½ΠΈΠΊΠ΅Π»ΠΈΡΠΎΠ²Π°Π½ΠΈΠ΅ Π΄Π΅ΡΠ°Π»Π΅ΠΉ β Π²ΡΡ ΠΎ ΠΏΡΠΎΡΠ΅ΡΡΠ΅ ΠΈ ΠΎΡΠΎΠ±Π΅Π½Π½ΠΎΡΡΡΡ + ΠΠΈΠ΄Π΅ΠΎ
ΠΠΈΠΊΠ΅Π»ΠΈΡΠΎΠ²Π°Π½ΠΈΠ΅ Ρ ΠΈΠΌΠΈΡΠ΅ΡΠΊΠΎΠ΅ — ΡΡΠΎ ΡΠ»ΠΎΠΆΠ½ΡΠΉ ΠΏΡΠΎΡΠ΅ΡΡ, ΠΏΠΎΠ·Π²ΠΎΠ»ΡΡΡΠΈΠΉ ΠΏΠΎΠΊΡΡΡΡ ΠΈΠ·Π΄Π΅Π»ΠΈΡ ΠΈΠ· ΠΏΡΠ°ΠΊΡΠΈΡΠ΅ΡΠΊΠΈ Π»ΡΠ±ΠΎΠ³ΠΎ ΠΌΠ΅ΡΠ°Π»Π»Π° ΡΠΎΠ½ΠΊΠΈΠΌ Π·Π°ΡΠΈΡΠ½ΡΠΌ ΡΠ»ΠΎΠ΅ΠΌ Π½ΠΈΠΊΠ΅Π»Ρ, ΠΏΠΎΠ²ΡΡΠΈΡΡ ΠΏΡΠΈ ΡΡΠΎΠΌ ΠΊΠΎΡΡΠΎΠ·ΠΈΠΎΠ½Π½ΡΡ ΡΡΠΎΠΉΠΊΠΎΡΡΡ ΠΈ ΠΏΡΠΈΠ΄Π°ΡΡ ΠΏΠΎΠ²Π΅ΡΡ Π½ΠΎΡΡΠΈ Π±Π»Π΅ΡΡΡΡΠΈΠΉ Π²ΠΈΠ΄ ΠΈ ΡΠ²Π΅ΡΠ΄ΠΎΡΡΡ.
1 ΠΡΠΎΡΠ΅ΡΡ Ρ ΠΈΠΌΠΈΡΠ΅ΡΠΊΠΎΠ³ΠΎ Π½ΠΈΠΊΠ΅Π»ΠΈΡΠΎΠ²Π°Π½ΠΈΡ Π΄Π΅ΡΠ°Π»Π΅ΠΉ
Π‘Π²ΠΎΠΉΡΡΠ²ΠΎ Π½ΠΈΠΊΠ΅Π»Ρ ΡΠΎΠ·Π΄Π°Π²Π°ΡΡ Π½Π° ΡΠ²ΠΎΠ΅ΠΉ ΠΏΠΎΠ²Π΅ΡΡ Π½ΠΎΡΡΠΈ ΡΠΎΠ½ΠΊΡΡ ΠΎΠΊΡΠΈΠ΄Π½ΡΡ ΠΏΠ»Π΅Π½ΠΊΡ, ΡΡΡΠΎΠΉΡΠΈΠ²ΡΡ ΠΊ Π΄Π΅ΠΉΡΡΠ²ΠΈΡ ΠΊΠΈΡΠ»ΠΎΡ ΠΈ ΡΠ΅Π»ΠΎΡΠ΅ΠΉ, ΠΏΠΎΠ·Π²ΠΎΠ»ΡΠ΅Ρ ΠΈΡΠΏΠΎΠ»ΡΠ·ΠΎΠ²Π°ΡΡ Π΅Π³ΠΎ Π΄Π»Ρ Π°Π½ΡΠΈΠΊΠΎΡΡΠΎΠ·ΠΈΠΎΠ½Π½ΠΎΠΉ Π·Π°ΡΠΈΡΡ ΠΌΠ΅ΡΠ°Π»Π»ΠΎΠ².
ΠΡΠ½ΠΎΠ²Π½ΠΎΠΉ ΠΌΠ΅ΡΠΎΠ΄, ΠΏΡΠΈΠΌΠ΅Π½ΡΡΡΠΈΠΉΡΡ Π² ΠΏΡΠΎΠΌΡΡΠ»Π΅Π½Π½ΠΎΡΡΠΈ — Π³Π°Π»ΡΠ²Π°Π½ΠΈΡΠ΅ΡΠΊΠΎΠ΅ Π½ΠΈΠΊΠ΅Π»ΠΈΡΠΎΠ²Π°Π½ΠΈΠ΅, Π½ΠΎ ΠΎΠ½ΠΎ ΡΡΠ΅Π±ΡΠ΅Ρ Π½Π°Π»ΠΈΡΠΈΡ Π΄ΠΎΡΡΠ°ΡΠΎΡΠ½ΠΎ ΡΠ»ΠΎΠΆΠ½ΠΎΠ³ΠΎ ΠΎΠ±ΠΎΡΡΠ΄ΠΎΠ²Π°Π½ΠΈΡ ΠΈ ΠΏΠΎΠ΄ΡΠ°Π·ΡΠΌΠ΅Π²Π°Π΅Ρ ΡΠ°Π±ΠΎΡΡ Ρ ΠΊΠΈΡΠ»ΠΎΡΠ°ΠΌΠΈ ΠΈ ΡΠ΅Π»ΠΎΡΠ°ΠΌΠΈ, ΠΏΠ°ΡΡ ΠΊΠΎΡΠΎΡΡΡ Π²ΡΠ΄Π΅Π»ΡΡΡΡΡ Π²ΠΎ Π²ΡΠ΅ΠΌΡ ΡΠ°Π±ΠΎΡΡ ΠΈ ΠΌΠΎΠ³ΡΡ ΡΠΈΠ»ΡΠ½ΠΎ Π½Π°Π²ΡΠ΅Π΄ΠΈΡΡ Π·Π΄ΠΎΡΠΎΠ²ΡΡ ΡΠ΅Π»ΠΎΠ²Π΅ΠΊΠ°. ΠΠ»Ρ ΠΏΠΎΠΊΡΡΡΠΈΡ ΡΡΠ°Π»ΠΈ, Π°Π»ΡΠΌΠΈΠ½ΠΈΡ, Π»Π°ΡΡΠ½ΠΈ, Π±ΡΠΎΠ½Π·Ρ ΠΈ Π΄ΡΡΠ³ΠΈΡ ΠΌΠ΅ΡΠ°Π»Π»ΠΎΠ² ΠΌΠΎΠΆΠ΅Ρ Π±ΡΡΡ ΠΏΡΠΈΠΌΠ΅Π½Π΅Π½ Ρ ΠΈΠΌΠΈΡΠ΅ΡΠΊΠΈΠΉ ΡΠΏΠΎΡΠΎΠ±, ΡΠ°ΠΊ ΠΊΠ°ΠΊ ΠΎΠ½ ΠΏΡΠΎΡΡ Π² ΠΈΡΠΏΠΎΠ»ΡΠ·ΠΎΠ²Π°Π½ΠΈΠΈ, ΠΈ ΡΡΠΎΡ ΠΏΡΠΎΡΠ΅ΡΡ ΠΌΠΎΠΆΠ½ΠΎ ΠΏΡΠΎΠ²ΠΎΠ΄ΠΈΡΡ Π² Π΄ΠΎΠΌΠ°ΡΠ½ΠΈΡ ΡΡΠ»ΠΎΠ²ΠΈΡΡ .
ΠΠ° ΡΠ΅Π³ΠΎΠ΄Π½ΡΡΠ½ΠΈΠΉ Π΄Π΅Π½Ρ ΡΡΡΠ΅ΡΡΠ²ΡΠ΅Ρ Π΄Π²Π° ΠΎΡΠ½ΠΎΠ²Π½ΡΡ ΠΌΠ΅ΡΠΎΠ΄Π° ΠΏΠΎΠΊΡΡΡΠΈΡ ΠΌΠ΅ΡΠ°Π»Π»ΠΈΡΠ΅ΡΠΊΠΈΡ Π΄Π΅ΡΠ°Π»Π΅ΠΉ Π½ΠΈΠΊΠ΅Π»Π΅ΠΌ: Π³Π°Π»ΡΠ²Π°Π½ΠΈΡΠ΅ΡΠΊΠΎΠ΅ ΠΈ Ρ ΠΈΠΌΠΈΡΠ΅ΡΠΊΠΎΠ΅. ΠΠ΅ΡΠ²ΡΠΉ ΠΌΠ΅ΡΠΎΠ΄ ΡΡΠ΅Π±ΡΠ΅Ρ Π½Π°Π»ΠΈΡΠΈΡ ΠΈΡΡΠΎΡΠ½ΠΈΠΊΠ° ΠΏΠΎΡΡΠΎΡΠ½Π½ΠΎΠ³ΠΎ ΡΠΎΠΊΠ° — ΡΠ»Π΅ΠΊΡΡΠΎΠ»ΠΈΡΠΈΡΠ΅ΡΠΊΠΎΠΉ Π²Π°Π½Π½Ρ Ρ ΡΠ»Π΅ΠΊΡΡΠΎΠ΄Π°ΠΌΠΈ ΠΈ Π±ΠΎΠ»ΡΡΠΎΠ³ΠΎ ΠΊΠΎΠ»ΠΈΡΠ΅ΡΡΠ²Π° Ρ ΠΈΠΌΠΈΡΠ΅ΡΠΊΠΈΡ ΡΠ΅Π°ΠΊΡΠΈΠ²ΠΎΠ². ΠΡΠΎΡΠΎΠΉ ΡΠΏΠΎΡΠΎΠ± Π½Π°ΠΌΠ½ΠΎΠ³ΠΎ ΠΏΡΠΎΡΠ΅. ΠΠ»Ρ Π΅Π³ΠΎ ΠΏΡΠΎΠ²Π΅Π΄Π΅Π½ΠΈΡ ΡΡΠ΅Π±ΡΠ΅ΡΡΡ Π½Π°Π»ΠΈΡΠΈΠ΅ ΠΌΠ΅ΡΠ½ΠΎΠΉ ΠΏΠΎΡΡΠ΄Ρ ΠΈ ΡΠΌΠ°Π»ΠΈΡΠΎΠ²Π°Π½Π½ΠΎΠΉ Π΅ΠΌΠΊΠΎΡΡΠΈ Π΄Π»Ρ Π½Π°Π³ΡΠ΅Π²Π° ΡΠ΅Π°ΠΊΡΠΈΠ²ΠΎΠ². ΠΠ΅ΡΠΌΠΎΡΡΡ Π½Π° Π²ΡΡ ΠΊΠ°ΠΆΡΡΡΡΡΡ ΠΏΡΠΎΡΡΠΎΡΡ, ΡΡΠΎ Π΄ΠΎΠ²ΠΎΠ»ΡΠ½ΠΎ ΡΠ»ΠΎΠΆΠ½ΡΠΉ ΠΏΡΠΎΡΠ΅ΡΡ, ΠΊΠΎΡΠΎΡΡΠΉ ΡΡΠ΅Π±ΡΠ΅Ρ Π±ΠΎΠ»ΡΡΠΎΠ³ΠΎ Π²Π½ΠΈΠΌΠ°Π½ΠΈΡ ΠΈ ΡΠΎΠ±Π»ΡΠ΄Π΅Π½ΠΈΡ ΠΏΡΠ°Π²ΠΈΠ» Π±Π΅Π·ΠΎΠΏΠ°ΡΠ½ΠΎΡΡΠΈ. ΠΠΎ Π²ΠΎΠ·ΠΌΠΎΠΆΠ½ΠΎΡΡΠΈ ΠΏΡΠΎΠ²ΠΎΠ΄ΠΈΡΠ΅ ΡΠ΅Π°ΠΊΡΠΈΠΈ Π² Ρ ΠΎΡΠΎΡΠΎ ΠΏΡΠΎΠ²Π΅ΡΡΠΈΠ²Π°Π΅ΠΌΠΎΠΌ ΠΏΠΎΠΌΠ΅ΡΠ΅Π½ΠΈΠΈ. ΠΠ΄Π΅Π°Π»ΡΠ½ΡΠΌ Π²Π°ΡΠΈΠ°Π½ΡΠΎΠΌ Π±ΡΠ΄Π΅Ρ ΠΎΠ±ΠΎΡΡΠ΄ΠΎΠ²Π°Π½ΠΈΠ΅ ΡΠ°Π±ΠΎΡΠ΅Π³ΠΎ ΠΌΠ΅ΡΡΠ° Π²ΡΡΡΠΆΠΊΠΎΠΉ, Π½ΠΈ Π² ΠΊΠΎΠ΅ΠΌ ΡΠ»ΡΡΠ°Π΅ Π½Π΅ ΡΠΎΠ΅Π΄ΠΈΠ½Π΅Π½Π½ΠΎΠΉ Ρ ΠΎΠ±ΡΠ΅Π΄ΠΎΠΌΠΎΠ²ΠΎΠΉ Π²Π΅Π½ΡΠΈΠ»ΡΡΠΈΠ΅ΠΉ. ΠΡΠΈ ΡΠ°Π±ΠΎΡΠ΅ ΠΏΠΎΠ»ΡΠ·ΡΠΉΡΠ΅ΡΡ Π·Π°ΡΠΈΡΠ½ΡΠΌΠΈ ΠΎΡΠΊΠ°ΠΌΠΈ, Π½Π΅ ΠΎΡΡΠ°Π²Π»ΡΠΉΡΠ΅ Π΅ΠΌΠΊΠΎΡΡΡ Ρ ΡΠ΅Π°ΠΊΡΠΈΠ²Π°ΠΌΠΈ Π±Π΅Π· ΠΏΡΠΈΡΠΌΠΎΡΡΠ°.
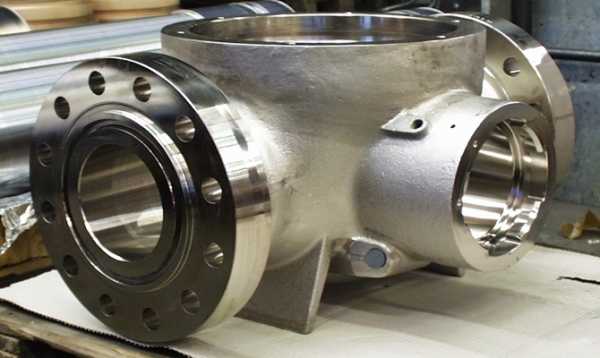
ΠΠΎΠΊΡΡΡΠΈΠ΅ ΠΌΠ΅ΡΠ°Π»Π»ΠΈΡΠ΅ΡΠΊΠΈΡ Π΄Π΅ΡΠ°Π»Π΅ΠΉ Π½ΠΈΠΊΠ΅Π»Π΅ΠΌ
Π Π΅ΠΊΠΎΠΌΠ΅Π½Π΄ΡΠ΅ΠΌ ΠΎΠ·Π½Π°ΠΊΠΎΠΌΠΈΡΡΡΡ
ΠΡΠ½ΠΎΠ²Π½ΡΠ΅ ΡΡΠ°Π΄ΠΈΠΈ Π΄Π»Ρ ΠΏΡΠΎΠΈΠ·Π²Π΅Π΄Π΅Π½ΠΈΡ Ρ ΠΈΠΌΠΈΡΠ΅ΡΠΊΠΎΠ³ΠΎ Π½ΠΈΠΊΠ΅Π»ΠΈΡΠΎΠ²Π°Π½ΠΈΡ ΡΠ»Π΅Π΄ΡΡΡΠΈΠ΅:
- ΠΠ»Ρ ΡΠΎΠ³ΠΎ ΡΡΠΎΠ±Ρ Π½ΠΈΠΊΠ΅Π»Ρ ΠΏΠΎΠΊΡΡΠ» ΠΏΠΎΠ²Π΅ΡΡ Π½ΠΎΡΡΡ ΡΠΎΠ½ΠΊΠΈΠΌ ΠΈ ΡΠ°Π²Π½ΠΎΠΌΠ΅ΡΠ½ΡΠΌ ΡΠ»ΠΎΠ΅ΠΌ, ΠΈΠ·Π΄Π΅Π»ΠΈΠ΅ ΠΏΡΠ΅Π΄Π²Π°ΡΠΈΡΠ΅Π»ΡΠ½ΠΎ ΡΠ»ΠΈΡΡΡΡ ΠΈ ΠΏΠΎΠ»ΠΈΡΡΡΡ.
- ΠΠ±Π΅Π·ΠΆΠΈΡΠΈΠ²Π°Π½ΠΈΠ΅. ΠΠΎΡΠΊΠΎΠ»ΡΠΊΡ Π΄Π°ΠΆΠ΅ ΡΠΎΠ½ΡΠ°ΠΉΡΠ°Ρ ΠΏΠ»Π΅Π½ΠΊΠ° ΠΆΠΈΡΠ° Π½Π° ΠΏΠΎΠ²Π΅ΡΡ Π½ΠΎΡΡΠΈ ΠΎΠ±ΡΠ°Π±Π°ΡΡΠ²Π°Π΅ΠΌΠΎΠ³ΠΎ ΠΈΠ·Π΄Π΅Π»ΠΈΡ ΠΌΠΎΠΆΠ΅Ρ Π²ΡΠ·Π²Π°ΡΡ Π½Π΅ΡΠ°Π²Π½ΠΎΠΌΠ΅ΡΠ½ΠΎΠ΅ ΡΠ°ΡΠΏΡΠ΅Π΄Π΅Π»Π΅Π½ΠΈΠ΅ Π½ΠΈΠΊΠ΅Π»Ρ ΠΏΠΎ ΠΏΠ»ΠΎΡΠ°Π΄ΠΈ Π΄Π΅ΡΠ°Π»ΠΈ, ΠΏΠΎΡΠ»Π΅Π΄Π½ΡΡ ΠΎΠ±Π΅Π·ΠΆΠΈΡΠΈΠ²Π°ΡΡ Π² ΡΠΏΠ΅ΡΠΈΠ°Π»ΡΠ½ΠΎΠΌ ΡΠ°ΡΡΠ²ΠΎΡΠ΅, ΡΠΎΡΡΠΎΡΡΠ΅ΠΌ ΠΈΠ· 25-35 Π³/Π» NaOH ΠΈΠ»ΠΈ KOH, 30-60 Π³ ΠΊΠ°Π»ΡΡΠΈΠ½ΠΈΡΠΎΠ²Π°Π½Π½ΠΎΠΉ ΡΠΎΠ΄Ρ ΠΈ 5-10 Π³ ΠΆΠΈΠ΄ΠΊΠΎΠ³ΠΎ ΡΡΠ΅ΠΊΠ»Π°.
- ΠΠ΅ΡΠ°Π»Ρ ΠΈΠ»ΠΈ ΠΈΠ·Π΄Π΅Π»ΠΈΠ΅, ΠΊΠΎΡΠΎΡΠΎΠ΅ Π½Π΅ΠΎΠ±Ρ ΠΎΠ΄ΠΈΠΌΠΎ ΠΏΠΎΠΊΡΡΡΡ Π½ΠΈΠΊΠ΅Π»Π΅ΠΌ, ΠΏΡΠΎΠΌΡΠ²Π°ΡΡ Π² Π²ΠΎΠ΄Π΅, ΠΏΠΎΡΠ»Π΅ ΡΠ΅Π³ΠΎ Π½Π° 0,5-1 ΠΌΠΈΠ½ΡΡΡ ΠΏΠΎΠ³ΡΡΠΆΠ°ΡΡ Π² 5% ΡΠ°ΡΡΠ²ΠΎΡ HCl. ΠΠ°Π½Π½ΡΠΉ ΡΠ°Π³ ΠΏΡΠ΅Π΄ΠΏΡΠΈΠ½ΠΈΠΌΠ°Π΅ΡΡΡ Π΄Π»Ρ ΡΠΎΠ³ΠΎ, ΡΡΠΎΠ±Ρ ΡΠ΄Π°Π»ΠΈΡΡ Ρ ΠΏΠΎΠ²Π΅ΡΡ Π½ΠΎΡΡΠΈ ΠΌΠ΅ΡΠ°Π»Π»Π° ΡΠΎΠ½ΠΊΠΈΠΉ ΡΠ»ΠΎΠΉ ΠΎΠΊΠΈΡΠ»ΠΎΠ², ΠΊΠΎΡΠΎΡΡΠΉ Π±ΡΠ΄Π΅Ρ Π·Π½Π°ΡΠΈΡΠ΅Π»ΡΠ½ΠΎ ΡΠ½ΠΈΠΆΠ°ΡΡ Π°Π΄Π³Π΅Π·ΠΈΡ ΠΌΠ΅ΠΆΠ΄Ρ ΠΌΠ°ΡΠ΅ΡΠΈΠ°Π»Π°ΠΌΠΈ. ΠΠΎΡΠ»Π΅ ΠΏΡΠΎΡΡΠ°Π²ΠΊΠΈ Π΄Π΅ΡΠ°Π»Ρ ΡΠ½ΠΎΠ²Π° ΠΏΡΠΎΠΌΡΠ²Π°ΡΡ Π² Π²ΠΎΠ΄Π΅, Π·Π°ΡΠ΅ΠΌ Π½Π΅ΠΌΠ΅Π΄Π»Π΅Π½Π½ΠΎ ΠΏΠ΅ΡΠ΅Π½ΠΎΡΡΡ Π² Π΅ΠΌΠΊΠΎΡΡΡ Ρ ΡΠ°ΡΡΠ²ΠΎΡΠΎΠΌ Π΄Π»Ρ ΠΏΠΎΠΊΡΡΡΠΈΡ Π½ΠΈΠΊΠ΅Π»Π΅ΠΌ.
Π‘ΠΎΠ±ΡΡΠ²Π΅Π½Π½ΠΎ Π½ΠΈΠΊΠ΅Π»ΠΈΡΠΎΠ²Π°Π½ΠΈΠ΅ ΠΏΡΠΎΠΈΠ·Π²ΠΎΠ΄ΡΡ ΠΏΡΠΈ ΠΏΠΎΠΌΠΎΡΠΈ ΠΊΠΈΠΏΡΡΠ΅Π½ΠΈΡ ΠΌΠ΅ΡΠ°Π»Π»ΠΈΡΠ΅ΡΠΊΠΎΠ³ΠΎ ΠΈΠ·Π΄Π΅Π»ΠΈΡ Π² ΡΠΏΠ΅ΡΠΈΠ°Π»ΡΠ½ΠΎΠΌ ΡΠ°ΡΡΠ²ΠΎΡΠ΅, ΠΊΠΎΡΠΎΡΡΠΉ Π³ΠΎΡΠΎΠ²ΡΡ ΡΠ»Π΅Π΄ΡΡΡΠΈΠΌ ΠΎΠ±ΡΠ°Π·ΠΎΠΌ:
- Π±Π΅ΡΡΡ Π²ΠΎΠ΄Ρ (ΠΆΠ΅Π»Π°ΡΠ΅Π»ΡΠ½ΠΎ — Π΄ΠΈΡΡΠΈΠ»Π»ΠΈΡΠΎΠ²Π°Π½Π½ΡΡ) ΠΈΠ· ΡΠ°ΡΡΠ΅ΡΠ° 300 ΠΌΠ»/Π΄ΠΌ2 ΠΏΠ»ΠΎΡΠ°Π΄ΠΈ ΠΏΠΎΠ²Π΅ΡΡ Π½ΠΎΡΡΠΈ Π΄Π΅ΡΠ°Π»ΠΈ, Π²ΠΊΠ»ΡΡΠ°Ρ ΠΊΠ°ΠΊ Π²Π½ΡΡΡΠ΅Π½Π½ΡΡ, ΡΠ°ΠΊ ΠΈ Π²Π½Π΅ΡΠ½ΡΡ;
- Π²ΠΎΠ΄Ρ Π½Π°Π³ΡΠ΅Π²Π°ΡΡ Π΄ΠΎ 60Β°Π‘, ΠΏΠΎΡΠ»Π΅ ΡΠ΅Π³ΠΎ ΡΠ°ΡΡΠ²ΠΎΡΡΡΡ Π² Π½Π΅ΠΉ 30 Π³ Ρ Π»ΠΎΡΠΈΡΡΠΎΠ³ΠΎ Π½ΠΈΠΊΠ΅Π»Ρ (NiCl2) ΠΈ 10 Π³ ΡΠΊΡΡΡΠ½ΠΎΠΊΠΈΡΠ»ΠΎΠ³ΠΎ Π½Π°ΡΡΠΈΡ (CH3COONa) Π½Π° 1 Π» Π²ΠΎΠ΄Ρ;
- ΡΠ΅ΠΌΠΏΠ΅ΡΠ°ΡΡΡΡ ΠΏΠΎΠ΄Π½ΠΈΠΌΠ°ΡΡ Π΄ΠΎ 80Β°Π‘ ΠΈ Π΄ΠΎΠ±Π°Π²Π»ΡΡΡ 15 Π³ Π³ΠΈΠΏΠΎΡΡΠ»ΡΡΠΈΡΠ° Π½Π°ΡΡΠΈΡ, Π·Π°ΡΠ΅ΠΌ Π² Π΅ΠΌΠΊΠΎΡΡΡ Ρ ΡΠ°ΡΡΠ²ΠΎΡΠΎΠΌ ΠΏΠΎΠ³ΡΡΠΆΠ°ΡΡ ΠΎΠ±ΡΠ°Π±Π°ΡΡΠ²Π°Π΅ΠΌΡΡ Π΄Π΅ΡΠ°Π»Ρ.
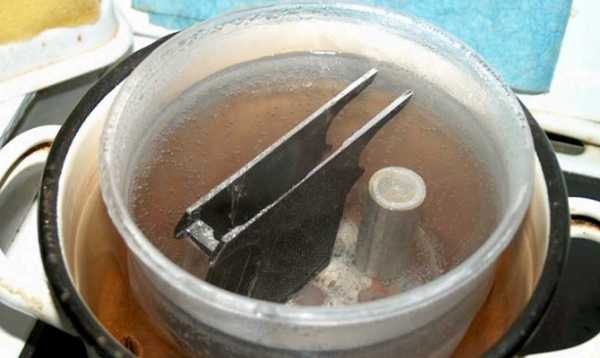
ΠΠΈΠΏΡΡΠ΅Π½ΠΈΠ΅ ΠΌΠ΅ΡΠ°Π»Π»ΠΈΡΠ΅ΡΠΊΠΎΠ³ΠΎ ΠΈΠ·Π΄Π΅Π»ΠΈΡ
ΠΠΎΡΠ»Π΅ ΠΏΠΎΠ³ΡΡΠΆΠ΅Π½ΠΈΡ Π΄Π΅ΡΠ°Π»ΠΈ, ΡΠ°ΡΡΠ²ΠΎΡ Π½Π°Π³ΡΠ΅Π²Π°ΡΡ Π΄ΠΎ 90-95Β°Π‘ ΠΈ ΠΏΠΎΠ΄Π΄Π΅ΡΠΆΠΈΠ²Π°ΡΡ ΡΠ΅ΠΌΠΏΠ΅ΡΠ°ΡΡΡΡ Π½Π° ΡΠ°ΠΊΠΎΠΌ ΡΡΠΎΠ²Π½Π΅ Π² ΡΠ΅ΡΠ΅Π½ΠΈΠ΅ Π²ΡΠ΅Π³ΠΎ ΠΏΡΠΎΡΠ΅ΡΡΠ° Π½ΠΈΠΊΠ΅Π»ΠΈΡΠΎΠ²Π°Π½ΠΈΡ. ΠΡΠ»ΠΈ Π²Ρ ΡΠ²ΠΈΠ΄Π΅Π»ΠΈ, ΡΡΠΎ ΠΊΠΎΠ»ΠΈΡΠ΅ΡΡΠ²ΠΎ ΡΠ°ΡΡΠ²ΠΎΡΠ° ΡΠΈΠ»ΡΠ½ΠΎ ΡΠΌΠ΅Π½ΡΡΠΈΠ»ΠΎΡΡ, ΠΌΠΎΠΆΠ½ΠΎ Π΄ΠΎΠ±Π°Π²ΠΈΡΡ Π² Π½Π΅Π³ΠΎ ΠΏΡΠ΅Π΄Π²Π°ΡΠΈΡΠ΅Π»ΡΠ½ΠΎ Π½Π°Π³ΡΠ΅ΡΡΡ Π΄ΠΈΡΡΠΈΠ»Π»ΠΈΡΠΎΠ²Π°Π½Π½ΡΡ Π²ΠΎΠ΄Ρ. ΠΠΈΠΏΡΡΠ΅Π½ΠΈΠ΅ Π΄ΠΎΠ»ΠΆΠ½ΠΎ ΠΏΡΠΎΡ ΠΎΠ΄ΠΈΡΡ Π½Π΅ ΠΌΠ΅Π½Π΅Π΅ 1-2 ΡΠ°ΡΠΎΠ². ΠΠ½ΠΎΠ³Π΄Π° Π΄Π»Ρ ΠΏΠΎΠ»ΡΡΠ΅Π½ΠΈΡ ΠΌΠ½ΠΎΠ³ΠΎΡΠ»ΠΎΠΉΠ½ΠΎΠ³ΠΎ ΠΏΠΎΠΊΡΡΡΠΈΡ, ΠΈΠ·Π΄Π΅Π»ΠΈΡ ΠΈΠ· ΠΌΠ΅ΡΠ°Π»Π»Π° ΠΏΠΎΠ΄Π²Π΅ΡΠ³Π°ΡΡ ΡΠ΅ΡΠΈΠΈ ΠΊΠΎΡΠΎΡΠΊΠΈΡ (20-30 ΠΌΠΈΠ½ΡΡ) ΠΊΠΈΠΏΡΡΠ΅Π½ΠΈΠΉ, ΠΏΠΎΡΠ»Π΅ ΠΊΠ°ΠΆΠ΄ΠΎΠ³ΠΎ ΠΈΠ· ΠΊΠΎΡΠΎΡΡΡ Π΄Π΅ΡΠ°Π»Ρ Π΄ΠΎΡΡΠ°ΡΡ ΠΈΠ· ΡΠ°ΡΡΠ²ΠΎΡΠ°, ΠΏΡΠΎΠΌΡΠ²Π°ΡΡ ΠΈ Π²ΡΡΡΡΠΈΠ²Π°ΡΡ. ΠΡΠΎ Π΄Π°Π΅Ρ Π²ΠΎΠ·ΠΌΠΎΠΆΠ½ΠΎΡΡΡ ΠΏΠΎΠ»ΡΡΠΈΡΡ ΡΠ»ΠΎΠΉ Π½ΠΈΠΊΠ΅Π»Ρ ΠΈΠ· 3-4 ΠΏΡΠΎΡΠ»ΠΎΠ΅Π², ΠΊΠΎΡΠΎΡΡΠ΅ ΡΡΠΌΠΌΠ°ΡΠ½ΠΎ ΠΈΠΌΠ΅ΡΡ Π±ΠΎΠ»ΡΡΡΡ ΠΏΠ»ΠΎΡΠ½ΠΎΡΡΡ ΠΈ ΠΊΠ°ΡΠ΅ΡΡΠ²ΠΎ, ΡΠ΅ΠΌ ΠΎΠ΄ΠΈΠ½Π°ΡΠ½ΡΠΉ ΡΠ»ΠΎΠΉ ΡΠΎΠΉ ΠΆΠ΅ ΠΌΠΎΡΠ½ΠΎΡΡΠΈ.
ΠΡΠΎΠ±Π΅Π½Π½ΠΎΡΡΡ ΠΏΠΎΠΊΡΡΡΠΈΡ ΡΡΠ°Π»ΡΠ½ΡΡ ΠΈΠ·Π΄Π΅Π»ΠΈΠΉ Π² ΡΠΎΠΌ, ΡΡΠΎ Π½ΠΈΠΊΠ΅Π»Ρ ΠΎΡΠ°ΠΆΠ΄Π°Π΅ΡΡΡ ΡΠ°ΠΌΠΎΠΏΡΠΎΠΈΠ·Π²ΠΎΠ»ΡΠ½ΠΎ Π²ΡΠ»Π΅Π΄ΡΡΠ²ΠΈΠ΅ ΠΊΠ°ΡΠ°Π»ΠΈΡΠΈΡΠ΅ΡΠΊΠΎΠ³ΠΎ Π²ΠΎΠ·Π΄Π΅ΠΉΡΡΠ²ΠΈΡ ΠΆΠ΅Π»Π΅Π·Π°. ΠΠ»Ρ ΠΎΡΠ°ΠΆΠ΄Π΅Π½ΠΈΡ Π·Π°ΡΠΈΡΠ½ΠΎΠ³ΠΎ ΡΠ»ΠΎΡ Π½Π° ΡΠ²Π΅ΡΠ½ΡΡ ΠΌΠ΅ΡΠ°Π»Π»Π°Ρ ΠΈΡΠΏΠΎΠ»ΡΠ·ΡΠ΅ΡΡΡ Π΄ΡΡΠ³ΠΎΠΉ ΡΠΎΡΡΠ°Π².
2 ΠΠΈΠΊΠ΅Π»ΠΈΡΠΎΠ²Π°Π½ΠΈΠ΅ ΡΠ²Π΅ΡΠ½ΡΡ ΠΌΠ΅ΡΠ°Π»Π»ΠΎΠ² ΠΈ ΡΠΏΠ»Π°Π²ΠΎΠ²
Π₯ΠΈΠΌΠΈΡΠ΅ΡΠΊΠΎΠ΅ Π½ΠΈΠΊΠ΅Π»ΠΈΡΠΎΠ²Π°Π½ΠΈΠ΅ ΡΠ²Π΅ΡΠ½ΡΡ ΠΌΠ΅ΡΠ°Π»Π»ΠΎΠ² ΠΏΠΎΠ·Π²ΠΎΠ»ΡΠ΅Ρ ΡΠΎΠ·Π΄Π°Π²Π°ΡΡ Π·Π°ΡΠΈΡΠ½ΡΡ ΠΏΠ»Π΅Π½ΠΊΡ Π½Π° ΠΏΠΎΠ²Π΅ΡΡ Π½ΠΎΡΡΠΈ Π»Π°ΡΡΠ½ΠΈ, ΠΌΠ΅Π΄ΠΈ ΠΈ Π±ΡΠΎΠ½Π·Ρ. ΠΠ»Ρ ΡΡΠΎΠ³ΠΎ Π΄Π΅ΡΠ°Π»Ρ ΡΠ½Π°ΡΠ°Π»Π° ΠΎΠ±Π΅Π·ΠΆΠΈΡΠΈΠ²Π°ΡΡ ΡΠ°ΡΡΠ²ΠΎΡΠΎΠΌ, ΡΠΎΡΡΠ°Π² ΠΊΠΎΡΠΎΡΠΎΠ³ΠΎ ΡΠΊΠ°Π·Π°Π½ Π² ΠΏΠ΅ΡΠ²ΠΎΠΌ ΡΠΏΠΎΡΠΎΠ±Π΅, ΠΏΡΠΈΡΠ΅ΠΌ ΡΠ½ΠΈΠΌΠ°ΡΡ ΠΎΠΊΡΠΈΠ΄Π½ΡΡ ΠΏΠ»Π΅Π½ΠΊΡ Ρ ΠΌΠ΅ΡΠ°Π»Π»Π° Π½Π΅ ΠΎΠ±ΡΠ·Π°ΡΠ΅Π»ΡΠ½ΠΎ. Π Π°ΡΡΠ²ΠΎΡ Π΄Π»Ρ Π½ΠΈΠΊΠ΅Π»ΠΈΡΠΎΠ²Π°Π½ΠΈΡ Π³ΠΎΡΠΎΠ²ΡΡ ΡΠ»Π΅Π΄ΡΡΡΠΈΠΌ ΠΎΠ±ΡΠ°Π·ΠΎΠΌ: Π² ΡΠΌΠ°Π»ΠΈΡΠΎΠ²Π°Π½Π½ΡΡ Π΅ΠΌΠΊΠΎΡΡΡ Π½Π°Π»ΠΈΠ²Π°ΡΡ 10% ΡΠ°ΡΡΠ²ΠΎΡ Ρ Π»ΠΎΡΠΈΡΡΠΎΠ³ΠΎ ΡΠΈΠ½ΠΊΠ° (ZnCl2), ΠΊΠΎΡΠΎΡΡΠΉ Π±ΠΎΠ»Π΅Π΅ ΠΈΠ·Π²Π΅ΡΡΠ΅Π½ ΠΏΠΎΠ΄ Π½Π°Π·Π²Π°Π½ΠΈΠ΅ΠΌ Β«ΠΏΠ°ΡΠ»ΡΠ½Π°Ρ ΠΊΠΈΡΠ»ΠΎΡΠ°Β». Π Π½Π΅ΠΌΡ ΠΏΠΎΠ½Π΅ΠΌΠ½ΠΎΠ³Ρ Π΄ΠΎΠ±Π°Π²Π»ΡΡΡ ΡΠ΅ΡΠ½ΠΎΠΊΠΈΡΠ»ΡΠΉ Π½ΠΈΠΊΠ΅Π»Ρ (NiSO4) Π΄ΠΎ ΡΠ°ΠΊΠΎΠΉ ΠΊΠΎΠ½ΡΠ΅Π½ΡΡΠ°ΡΠΈΠΈ, ΠΏΡΠΈ ΠΊΠΎΡΠΎΡΠΎΠΉ ΡΠ°ΡΡΠ²ΠΎΡ ΠΎΠΊΡΠ°ΡΠΈΠ²Π°Π΅ΡΡΡ Π² Π·Π΅Π»Π΅Π½ΡΠΉ ΡΠ²Π΅Ρ. Π‘ΠΎΡΡΠ°Π² Π΄ΠΎΠ²ΠΎΠ΄ΡΡ Π΄ΠΎ ΠΊΠΈΠΏΠ΅Π½ΠΈΡ, ΠΏΠΎΡΠ»Π΅ ΡΠ΅Π³ΠΎ ΠΏΠΎΠ³ΡΡΠΆΠ°ΡΡ Π΄Π΅ΡΠ°Π»Ρ Π² Π½Π΅Π³ΠΎ Π½Π° 1,5-2 ΡΠ°ΡΠ°. ΠΠΎΡΠ»Π΅ ΡΠΎΠ³ΠΎ ΠΊΠ°ΠΊ ΡΠ΅Π°ΠΊΡΠΈΡ Π·Π°ΠΊΠΎΠ½ΡΠΈΡΡΡ, ΠΈΠ·Π΄Π΅Π»ΠΈΠ΅ Π΄ΠΎΡΡΠ°ΡΡ ΠΈΠ· ΡΠ°ΡΡΠ²ΠΎΡΠ° ΠΈ ΠΏΠΎΠΌΠ΅ΡΠ°ΡΡ Π² Π΅ΠΌΠΊΠΎΡΡΡ Ρ ΠΌΠ΅Π»ΠΎΠ²ΠΎΠΉ Π²ΠΎΠ΄ΠΎΠΉ (Π³ΠΎΡΠΎΠ²ΠΈΡΡΡ ΡΠΏΠΎΡΠΎΠ±ΠΎΠΌ Π΄ΠΎΠ±Π°Π²Π»Π΅Π½ΠΈΡ 50-70 Π³ ΠΌΠ΅Π»Π° Π² ΠΏΠΎΡΠΎΡΠΊΠ΅ Π½Π° 1 Π»ΠΈΡΡ Π²ΠΎΠ΄Ρ), Π° Π·Π°ΡΠ΅ΠΌ ΠΏΡΠΎΠΌΡΠ²Π°Π΅ΡΡΡ.

Π Π°ΡΡΠ²ΠΎΡ ΡΠ΅ΡΠ½ΠΎΠΊΠΈΡΠ»ΠΎΠ³ΠΎ Π½ΠΈΠΊΠ΅Π»Ρ
ΠΠΈΠΊΠ΅Π»ΠΈΡΠΎΠ²Π°Π½ΠΈΠ΅ Π°Π»ΡΠΌΠΈΠ½ΠΈΡ ΠΏΡΠΎΡ ΠΎΠ΄ΠΈΡ ΠΏΠΎ ΡΡ ΠΎΠΆΠ΅ΠΉ ΡΠ΅Ρ Π½ΠΎΠ»ΠΎΠ³ΠΈΠΈ, Π½ΠΎ ΡΠΎΡΡΠ°Π² ΡΠ°ΡΡΠ²ΠΎΡΠ° Π½Π΅ΠΌΠ½ΠΎΠ³ΠΎ Π΄ΡΡΠ³ΠΎΠΉ:
- 20 Π³ ΡΠ΅ΡΠ½ΠΎΠΊΠΈΡΠ»ΠΎΠ³ΠΎ Π½ΠΈΠΊΠ΅Π»Ρ;
- 10 Π³ Π½Π°ΡΡΠΈΡ ΡΠΊΡΡΡΠ½ΠΎΠΊΠΈΡΠ»ΠΎΠ³ΠΎ;
- 25 Π³ Π½Π°ΡΡΠΈΡ ΡΠΎΡΡΠΎΡΠ½ΠΎΠ²Π°ΡΠΈΡΡΠΎΠΊΠΈΡΠ»ΠΎΠ³ΠΎ;
- 3 ΠΌΠ» ΡΠΈΠΎΠΌΠΎΡΠ΅Π²ΠΈΠ½Ρ ΠΊΠΎΠ½ΡΠ΅Π½ΡΡΠ°ΡΠΈΠ΅ΠΉ 1 Π³/Π»;
- 0,4 Π³ ΡΡΠΎΡΠΈΡΡΠΎΠ³ΠΎ Π½Π°ΡΡΠΈΡ;
- 9 ΠΌΠ» ΡΠΊΡΡΡΠ½ΠΎΠΉ ΠΊΠΈΡΠ»ΠΎΡΡ.

ΠΠ±ΡΠ°Π±ΠΎΡΠΊΠ° Π΄Π΅ΡΠ°Π»Π΅ΠΉ ΠΈΠ· Π°Π»ΡΠΌΠΈΠ½ΠΈΡ
ΠΠ΅ΡΠ΅Π΄ ΠΎΠ±ΡΠ°Π±ΠΎΡΠΊΠΎΠΉ ΠΈΠ·Π΄Π΅Π»ΠΈΡ ΠΈΠ· Π°Π»ΡΠΌΠΈΠ½ΠΈΡ ΠΏΠΎΠ³ΡΡΠΆΠ°ΡΡ Π² ΡΠ°ΡΡΠ²ΠΎΡ ΠΊΠ°ΡΡΡΠΈΡΠ΅ΡΠΊΠΎΠΉ ΡΠΎΠ΄Ρ, ΠΊΠΎΠ½ΡΠ΅Π½ΡΡΠ°ΡΠΈΠ΅ΠΉ 10-15%, ΠΈ Π½Π°Π³ΡΠ΅ΡΠΎΠΌ Π΄ΠΎ ΡΠ΅ΠΌΠΏΠ΅ΡΠ°ΡΡΡΡ 60-70Β°Π‘. ΠΡΠΈ ΡΡΠΎΠΌ ΠΏΡΠΎΠΈΡΡ ΠΎΠ΄ΠΈΡ Π±ΡΡΠ½Π°Ρ ΡΠ΅Π°ΠΊΡΠΈΡ Ρ Π²ΡΠ΄Π΅Π»Π΅Π½ΠΈΠ΅ΠΌ Π²ΠΎΠ΄ΠΎΡΠΎΠ΄Π°, ΠΏΡΠ·ΡΡΡΠΊΠΈ ΠΊΠΎΡΠΎΡΠΎΠ³ΠΎ ΠΎΡΠΈΡΠ°ΡΡ ΠΏΠΎΠ²Π΅ΡΡ Π½ΠΎΡΡΡ ΠΎΡ ΠΎΠΊΠΈΡΠ»ΠΎΠ² ΠΈ Π·Π°Π³ΡΡΠ·Π½Π΅Π½ΠΈΡ. Π Π·Π°Π²ΠΈΡΠΈΠΌΠΎΡΡΠΈ ΠΎΡ ΡΡΠ΅ΠΏΠ΅Π½ΠΈ Π·Π°Π³ΡΡΠ·Π½Π΅Π½Π½ΠΎΡΡΠΈ, Π΄Π΅ΡΠ°Π»ΠΈ Π²ΡΠ΄Π΅ΡΠΆΠΈΠ²Π°ΡΡ Π² ΠΎΡΠΈΡΠ°ΡΡΠ΅ΠΌ ΡΠ°ΡΡΠ²ΠΎΡΠ΅ ΠΎΡ 15-20 ΡΠ΅ΠΊΡΠ½Π΄ Π΄ΠΎ 1-2 ΠΌΠΈΠ½ΡΡ, ΠΏΠΎΡΠ»Π΅ ΡΠ΅Π³ΠΎ ΠΏΡΠΎΠΌΡΠ²Π°ΡΡ Π² ΠΏΡΠΎΡΠΎΡΠ½ΠΎΠΉ Π²ΠΎΠ΄Π΅ ΠΈ ΠΏΠΎΠ³ΡΡΠΆΠ°ΡΡ Π² Π½ΠΈΠΊΠ΅Π»ΠΈΡΡΡΡΠΈΠΉ ΡΠ°ΡΡΠ²ΠΎΡ.
3 ΠΡΠΈΠΌΠ΅Π½Π΅Π½ΠΈΠ΅ Π½ΠΈΠΊΠ΅Π»ΠΈΡΠΎΠ²Π°Π½Π½ΡΡ ΠΈΠ·Π΄Π΅Π»ΠΈΠΉ
ΠΡΠ»Π΅Π΄ΡΡΠ²ΠΈΠ΅ Π½ΠΈΠΊΠ΅Π»ΠΈΡΠΎΠ²Π°Π½ΠΈΡ Π·Π½Π°ΡΠΈΡΠ΅Π»ΡΠ½ΠΎ ΠΏΠΎΠ²ΡΡΠ°ΡΡΡΡ ΡΠΈΠ·ΠΈΠΊΠΎ-ΠΌΠ΅Ρ Π°Π½ΠΈΡΠ΅ΡΠΊΠΈΠ΅ ΠΈ Π΄Π΅ΠΊΠΎΡΠ°ΡΠΈΠ²Π½ΡΠ΅ ΡΠ²ΠΎΠΉΡΡΠ²Π° ΠΌΠ΅ΡΠ°Π»Π»ΠΈΡΠ΅ΡΠΊΠΈΡ ΠΈΠ·Π΄Π΅Π»ΠΈΠΉ. ΠΠΈΠΊΠ΅Π»Ρ ΠΈΠΌΠ΅Π΅Ρ ΡΠ΅ΡΠ΅Π±ΡΠΈΡΡΠΎ-Π±Π΅Π»ΡΠΉ ΡΠ²Π΅Ρ, Π½Π° Π²ΠΎΠ·Π΄ΡΡ Π΅ Π±ΡΡΡΡΠΎ ΠΏΠΎΠΊΡΡΠ²Π°Π΅ΡΡΡ Π½Π΅Π·Π°ΠΌΠ΅ΡΠ½ΠΎΠΉ ΡΠ΅Π»ΠΎΠ²Π΅ΡΠ΅ΡΠΊΠΎΠΌΡ Π³Π»Π°Π·Ρ ΠΏΠ»Π΅Π½ΠΊΠΎΠΉ ΠΎΠΊΠΈΡΠ»ΠΎΠ², ΠΊΠΎΡΠΎΡΡΠ΅ ΠΏΡΠ°ΠΊΡΠΈΡΠ΅ΡΠΊΠΈ Π½Π΅ ΠΌΠ΅Π½ΡΡΡ Π΅Π³ΠΎ Π²Π½Π΅ΡΠ½Π΅Π³ΠΎ Π²ΠΈΠ΄Π°, Π½ΠΎ ΠΏΡΠΈ ΡΡΠΎΠΌ Π½Π°Π΄Π΅ΠΆΠ½ΠΎ Π·Π°ΡΠΈΡΠ°ΡΡ ΠΎΡ Π΄Π°Π»ΡΠ½Π΅ΠΉΡΠ΅Π³ΠΎ ΠΎΠΊΠΈΡΠ»Π΅Π½ΠΈΡ ΠΈ ΡΠ΅Π°ΠΊΡΠΈΠΉ Ρ Π°Π³ΡΠ΅ΡΡΠΈΠ²Π½ΠΎΠΉ ΡΡΠ΅Π΄ΠΎΠΉ. ΠΠΈΠΊΠ΅Π»ΠΈΡΠΎΠ²Π°Π½ΠΈΠ΅ ΠΈΡΠΏΠΎΠ»ΡΠ·ΡΠ΅ΡΡΡ Π΄Π»Ρ Π·Π°ΡΠΈΡΡ ΡΡΠ°Π»Π΅ΠΉ, Π±ΡΠΎΠ½Π·Ρ, Π»Π°ΡΡΠ½ΠΈ, Π°Π»ΡΠΌΠΈΠ½ΠΈΡ, ΠΌΠ΅Π΄ΠΈ ΠΈ Π΄ΡΡΠ³ΠΈΡ ΠΌΠ°ΡΠ΅ΡΠΈΠ°Π»ΠΎΠ².

ΠΠ°ΡΠΈΡΠ° ΠΌΠ΅ΡΠ°Π»Π»ΠΈΡΠ΅ΡΠΊΠΈΡ ΠΈΠ·Π΄Π΅Π»ΠΈΠΉ ΠΎΡ ΠΎΠΊΠΈΡΠ»Π΅Π½ΠΈΡ
Π―Π²Π»ΡΠ΅ΡΡΡ ΠΊΠ°ΡΠΎΠ΄Π½ΠΎΠΉ Π·Π°ΡΠΈΡΠΎΠΉ. ΠΡΠΎ Π·Π½Π°ΡΠΈΡ, ΡΡΠΎ ΠΏΡΠΈ ΠΏΠΎΠ²ΡΠ΅ΠΆΠ΄Π΅Π½ΠΈΠΈ ΡΠ΅Π»ΠΎΡΡΠ½ΠΎΡΡΠΈ ΠΏΠΎΠΊΡΡΡΠΈΡ, ΠΌΠ΅ΡΠ°Π»Π» Π½Π°ΡΠΈΠ½Π°Π΅Ρ ΡΠ΅Π°Π³ΠΈΡΠΎΠ²Π°ΡΡ Ρ Π²Π½Π΅ΡΠ½Π΅ΠΉ ΡΡΠ΅Π΄ΠΎΠΉ. ΠΠ»Ρ ΠΏΠΎΠ²ΡΡΠ΅Π½ΠΈΡ ΠΌΠ΅Ρ Π°Π½ΠΈΡΠ΅ΡΠΊΠΈΡ ΡΠ²ΠΎΠΉΡΡΠ² Π·Π°ΡΠΈΡΠ½ΠΎΠ³ΠΎ ΡΠ»ΠΎΡ, Π½ΡΠΆΠ½ΠΎ Π½Π°Π½ΠΎΡΠΈΡΡ Π΅Π³ΠΎ, ΡΠΎΡΠ½ΠΎ ΠΏΡΠΈΠ΄Π΅ΡΠΆΠΈΠ²Π°ΡΡΡ ΡΠ΅Ρ Π½ΠΎΠ»ΠΎΠ³ΠΈΠΈ ΠΈ ΠΏΠΎΡΠ»Π΅Π΄ΠΎΠ²Π°ΡΠ΅Π»ΡΠ½ΠΎΡΡΠΈ Π΄Π΅ΠΉΡΡΠ²ΠΈΠΉ. ΠΠΈΠΊΠ΅Π»Ρ, Π½Π°Π½Π΅ΡΠ΅Π½Π½ΡΠΉ Π½Π° ΠΏΠΎΠ²Π΅ΡΡ Π½ΠΎΡΡΡ ΡΠΎ ΡΠ»Π΅Π΄Π°ΠΌΠΈ Π·Π°Π³ΡΡΠ·Π½Π΅Π½ΠΈΡ ΠΈ ΡΠΆΠ°Π²ΡΠΈΠ½Ρ, Ρ Π±ΠΎΠ»ΡΡΠΈΠΌ ΠΊΠΎΠ»ΠΈΡΠ΅ΡΡΠ²ΠΎΠΌ Π½Π΅ΡΠΎΠ²Π½ΠΎΡΡΠ΅ΠΉ, ΠΌΠΎΠΆΠ΅Ρ Π½Π°ΡΠ°ΡΡ Π²ΡΠΏΡΡΠΈΠ²Π°ΡΡΡΡ ΠΈ ΠΎΡΡΠ»Π°ΠΈΠ²Π°ΡΡΡΡ Π² ΠΏΡΠΎΡΠ΅ΡΡΠ΅ ΡΠΊΡΠΏΠ»ΡΠ°ΡΠ°ΡΠΈΠΈ.
ΠΠ·Π΄Π΅Π»ΠΈΡ, ΠΏΠΎΠΊΡΡΡΡΠ΅ Π½ΠΈΠΊΠ΅Π»Π΅ΠΌ, ΠΏΠΎΡΡΠΈ Π½ΠΈ Π² ΡΠ΅ΠΌ Π½Π΅ ΡΡΡΡΠΏΠ°ΡΡ Ρ ΡΠΎΠΌΠΈΡΠΎΠ²Π°Π½Π½ΡΠΌ — ΠΈΠΌΠ΅ΡΡ ΠΏΠΎΡ ΠΎΠΆΠΈΠΉ Π±Π»Π΅ΡΠΊ ΠΈ ΡΠ²Π΅ΡΠ΄ΠΎΡΡΡ. ΠΡΠΈ Π±ΠΎΠ»ΡΡΠΈΡ ΡΠ°Π·ΠΌΠ΅ΡΠ°Ρ Π΅ΠΌΠΊΠΎΡΡΠ΅ΠΉ Π΄Π»Ρ Ρ ΠΈΠΌΠΈΡΠ΅ΡΠΊΠΎΠΉ ΡΠ΅Π°ΠΊΡΠΈΠΈ Π½ΠΈΠΊΠ΅Π»Π΅ΠΌ ΠΌΠΎΠΆΠ½ΠΎ ΠΏΠΎΠΊΡΡΠ²Π°ΡΡ Π΄ΠΎΠ²ΠΎΠ»ΡΠ½ΠΎ Π±ΠΎΠ»ΡΡΠΈΠ΅ Π΄Π΅ΡΠ°Π»ΠΈ, Π½Π°ΠΏΡΠΈΠΌΠ΅Ρ, Π°Π²ΡΠΎΠΌΠΎΠ±ΠΈΠ»ΡΠ½ΡΠ΅ Π΄ΠΈΡΠΊΠΈ.
4 ΠΡΠ½ΠΎΠ²Π½ΡΠ΅ Π²ΡΠ²ΠΎΠ΄Ρ ΠΏΠΎ ΡΠ΅ΠΌΠ΅
ΠΠΈΠΊΠ΅Π»ΠΈΡΠΎΠ²Π°Π½ΠΈΠ΅ ΠΏΡΠΈΠ΄Π°Π΅Ρ ΠΌΠ΅ΡΠ°Π»Π»Ρ ΠΊΡΠ°ΡΠΈΠ²ΡΠΉ Π±Π»Π΅ΡΡΡΡΠΈΠΉ Π²ΠΈΠ΄, Π²ΡΡΠΎΠΊΡΡ ΠΊΠΎΡΡΠΎΠ·ΠΈΠΎΠ½Π½ΡΡ ΡΡΠΎΠΉΠΊΠΎΡΡΡ ΠΈ ΠΏΠΎΠ²ΡΡΠ°Π΅Ρ ΡΠ²Π΅ΡΠ΄ΠΎΡΡΡ ΠΏΠΎΠ²Π΅ΡΡ Π½ΠΎΡΡΠΈ. ΠΠ΅ΡΠ°Π»ΠΈ, ΠΏΠΎΠΊΡΡΡΡΠ΅ Π½ΠΈΠΊΠ΅Π»Π΅ΠΌ, ΠΌΠΎΠΆΠ½ΠΎ ΠΈΡΠΏΠΎΠ»ΡΠ·ΠΎΠ²Π°ΡΡ Π΄Π»Ρ ΡΠΊΡΠ°ΡΠ΅Π½ΠΈΡ ΡΡΠΎΠ»Π±ΠΎΠ² ΠΎΠ³ΡΠ°Π΄Ρ, Π΅ΡΠ»ΠΈ ΡΠ°ΠΊΡΡ ΠΏΡΠ΅Π΄ΡΡΠΌΠ°ΡΡΠΈΠ²Π°Π΅Ρ ΠΏΡΠΎΠ΅ΠΊΡ ΡΡΠ°ΡΡΠΊΠ°. ΠΡΠ°ΡΠΈΠ²ΠΎ Π²ΡΠ³Π»ΡΠ΄ΡΡ ΠΈ ΠΈΠΌΠ΅ΡΡ Π΄Π»ΠΈΡΠ΅Π»ΡΠ½ΡΠΉ ΡΡΠΎΠΊ ΡΠΊΡΠΏΠ»ΡΠ°ΡΠ°ΡΠΈΠΈ ΡΠ°Π·Π»ΠΈΡΠ½ΡΠ΅ ΠΌΠ΅ΡΠΈΠ·Ρ — ΠΊΡΠ΅ΠΏΠ΅ΠΆΠ½ΡΠ΅ Π±ΠΎΠ»ΡΡ, ΡΠΊΠΎΠ±Ρ, ΡΠ»Π΅ΠΌΠ΅Π½ΡΡ ΠΌΠ΅Π±Π΅Π»ΡΠ½ΠΎΠΉ ΡΡΡΠ½ΠΈΡΡΡΡ. ΠΠ½ΠΈ ΠΌΠΎΠ³ΡΡ Π±ΡΡΡ ΠΈΡΠΏΠΎΠ»ΡΠ·ΠΎΠ²Π°Π½Ρ Π² ΡΡΠ»ΠΎΠ²ΠΈΡΡ ΠΏΠΎΠ²ΡΡΠ΅Π½Π½ΠΎΠΉ Π²Π»Π°ΠΆΠ½ΠΎΡΡΠΈ, ΡΠ΅ΠΌΠΏΠ΅ΡΠ°ΡΡΡΡ ΠΈ Π½Π°Π³ΡΡΠ·ΠΊΠΈ — Π² ΠΌΠ΅ΡΡΠ°Ρ , Π³Π΄Π΅ ΡΡΠ°Π»Ρ Π±ΡΡΡΡΠΎ ΡΠΆΠ°Π²Π΅Π΅Ρ ΠΈ ΡΠ΅ΡΡΠ΅Ρ ΡΠ²ΠΎΠΉΡΡΠ²Π°.
Π₯ΠΈΠΌΠΈΡΠ΅ΡΠΊΠΎΠ΅ Π½ΠΈΠΊΠ΅Π»ΠΈΡΠΎΠ²Π°Π½ΠΈΠ΅ ΠΌΠΎΠΆΠ½ΠΎ ΠΏΡΠΎΠΈΠ·Π²Π΅ΡΡΠΈ ΡΠΎΠ±ΡΡΠ²Π΅Π½Π½ΠΎΡΡΡΠ½ΠΎ, Π² ΡΡΠ»ΠΎΠ²ΠΈΡΡ Ρ ΠΎΡΠΎΡΠΎ ΠΏΡΠΎΠ²Π΅ΡΡΠΈΠ²Π°Π΅ΠΌΠΎΠ³ΠΎ Π³Π°ΡΠ°ΠΆΠ° ΠΈΠ»ΠΈ ΠΌΠ°ΡΡΠ΅ΡΡΠΊΠΎΠΉ.

ΠΡΠ°ΡΠΈΠ²ΡΠΉ Π±Π»Π΅ΡΡΡΡΠΈΠΉ Π²ΠΈΠ΄ ΠΏΠΎΠ²Π΅ΡΡ Π½ΠΎΡΡΠΈ
ΠΠ΅ΠΆΠ΅Π»Π°ΡΠ΅Π»ΡΠ½ΠΎ Π΄Π΅Π»Π°ΡΡ ΠΎΠΏΠΈΡΠ°Π½Π½ΡΠ΅ ΡΠ΅Ρ Π½ΠΎΠ»ΠΎΠ³ΠΈΡΠ΅ΡΠΊΠΈΠ΅ ΠΎΠΏΠ΅ΡΠ°ΡΠΈΠΈ Π½Π° ΠΊΡΡ Π½Π΅, ΡΠ°ΠΊ ΠΊΠ°ΠΊ ΠΈΡΠΏΠ°ΡΠ΅Π½ΠΈΡ Π»ΡΠ±ΡΡ Ρ ΠΈΠΌΠΈΡΠ΅ΡΠΊΠΈΡ Π²Π΅ΡΠ΅ΡΡΠ² ΠΌΠΎΠ³ΡΡ Π±ΡΡΡ ΠΎΠΏΠ°ΡΠ½ΡΠΌΠΈ Π΄Π»Ρ Π·Π΄ΠΎΡΠΎΠ²ΡΡ.
ΠΠΎΠΊΡΡΡΠΈΠ΅ Π½ΠΈΠΊΠ΅Π»Π΅ΠΌ Ρ ΠΏΠΎΠΌΠΎΡΡΡ Ρ ΠΈΠΌΠΈΡΠ΅ΡΠΊΠΈΡ ΡΠ΅Π°ΠΊΡΠΈΠ²ΠΎΠ² Π½Π΅ ΡΡΠ΅Π±ΡΠ΅Ρ Π²ΡΡΠΎΠΊΠΈΡ ΡΠ½Π΅ΡΠ³ΠΎΠ·Π°ΡΡΠ°Ρ, Π² ΠΎΡΠ»ΠΈΡΠΈΠ΅ ΠΎΡ Π³Π°Π»ΡΠ²Π°Π½ΠΈΡΠ΅ΡΠΊΠΎΠ³ΠΎ, Π½ΠΎ ΠΏΠΎΠ·Π²ΠΎΠ»ΡΠ΅Ρ ΠΏΠΎΠ»ΡΡΠΈΡΡ Π΄ΠΎΡΡΠ°ΡΠΎΡΠ½ΠΎ ΠΊΠ°ΡΠ΅ΡΡΠ²Π΅Π½Π½ΠΎΠ΅, Π±Π»Π΅ΡΡΡΡΠ΅Π΅ ΠΈ ΡΠ²Π΅ΡΠ΄ΠΎΠ΅ ΠΏΠΎΠΊΡΡΡΠΈΠ΅.
tutmet.ru
ΠΠΈΠΊΠ΅Π»ΠΈΡΠΎΠ²Π°Π½ΠΈΠ΅ Π² Π΄ΠΎΠΌΠ°ΡΠ½ΠΈΡ ΡΡΠ»ΠΎΠ²ΠΈΡΡ : Ρ ΠΈΠΌΠΈΡΠ΅ΡΠΊΠΎΠ΅, Π³Π°Π»ΡΠ²Π°Π½ΠΈΡΠ΅ΡΠΊΠΎΠ΅
ΠΠΈΠΊΠ΅Π»ΠΈΡΠΎΠ²Π°Π½ΠΈΠ΅ ΠΈΠ·Π΄Π΅Π»ΠΈΠΉ ΠΈΠ· ΠΌΠ΅ΡΠ°Π»Π»ΠΎΠ² ΠΏΠΎΠ·Π²ΠΎΠ»ΡΠ΅Ρ Π½Π΅ ΡΠΎΠ»ΡΠΊΠΎ Π·Π°ΡΠΈΡΠΈΡΡ ΠΈΡ ΠΏΠΎΠ²Π΅ΡΡ Π½ΠΎΡΡΠΈ ΠΎΡ ΠΊΠΎΡΡΠΎΠ·ΠΈΠΈ, Π½ΠΎ ΠΈ ΡΠΎΠ·Π΄Π°ΡΡ Π½Π° Π½ΠΈΡ Π±Π»Π΅ΡΡΡΡΠ΅Π΅ ΠΏΠΎΠΊΡΡΡΠΈΠ΅. Π’Π°ΠΊΠΈΠ΅ ΠΈΠ·Π΄Π΅Π»ΠΈΡ ΡΠΈΡΠΎΠΊΠΎ ΠΏΡΠΈΠΌΠ΅Π½ΡΡΡΡΡ ΠΏΡΠΈ ΠΈΠ·Π³ΠΎΡΠΎΠ²Π»Π΅Π½ΠΈΠΈ ΡΠ°Π½ΡΠ΅Ρ Π½ΠΈΠΊΠΈ, Π°Π²ΡΠΎΠΌΠΎΠ±ΠΈΠ»ΡΠ½ΡΡ Π·Π°ΠΏΡΠ°ΡΡΠ΅ΠΉ, ΠΌΠ΅Π΄ΠΈΡΠΈΠ½ΡΠΊΠΈΡ ΠΈΠ½ΡΡΡΡΠΌΠ΅Π½ΡΠΎΠ² ΠΈ Ρ. Π΄. Π ΡΠ²ΡΠ·ΠΈ Ρ ΡΡΠΈΠΌ ΠΌΠ½ΠΎΠ³ΠΈΠ΅ Π»ΡΠ΄ΠΈ Π·Π°Π΄Π°ΡΡΡΡ Π²ΠΎΠΏΡΠΎΡΠΎΠΌ, ΠΌΠΎΠΆΠ½ΠΎ Π»ΠΈ Π²ΡΠΏΠΎΠ»Π½ΠΈΡΡ Π½ΠΈΠΊΠ΅Π»ΠΈΡΠΎΠ²Π°Π½ΠΈΠ΅ ΡΡΠ°Π»ΠΈ Π² Π΄ΠΎΠΌΠ°ΡΠ½ΠΈΡ ΡΡΠ»ΠΎΠ²ΠΈΡΡ ?
Π’Π΅Ρ Π½ΠΎΠ»ΠΎΠ³ΠΈΡ Π½ΠΈΠΊΠ΅Π»ΠΈΡΠΎΠ²Π°Π½ΠΈΡ ΠΌΠ΅ΡΠ°Π»Π»ΠΎΠ²
ΠΠΈΠΊΠ΅Π»ΠΈΡΠΎΠ²Π°Π½ΠΈΠ΅ ΠΎΡΡΡΠ΅ΡΡΠ²Π»ΡΠ΅ΡΡΡ ΠΏΡΡΠ΅ΠΌ Π½Π°Π½Π΅ΡΠ΅Π½ΠΈΡ Π½Π° ΠΌΠ΅ΡΠ°Π»Π»ΠΈΡΠ΅ΡΠΊΠΈΠΉ ΠΏΡΠ΅Π΄ΠΌΠ΅Ρ ΡΠΎΠ½ΠΊΠΎΠ³ΠΎ ΡΠ»ΠΎΡ Π½ΠΈΠΊΠ΅Π»Π΅Π²ΠΎΠ³ΠΎ ΠΏΠΎΠΊΡΡΡΠΈΡ. ΠΠΎΠΊΡΡΡΡ Π½ΠΈΠΊΠ΅Π»Π΅ΠΌ ΠΌΠΎΠΆΠ½ΠΎ ΠΈΠ·Π΄Π΅Π»ΠΈΡ ΠΈΠ· ΡΠ°Π·Π»ΠΈΡΠ½ΡΡ ΠΌΠ΅ΡΠ°Π»Π»ΠΎΠ², ΡΠ°ΠΊΠΈΡ ΠΊΠ°ΠΊ:
- ΡΡΠ°Π»Ρ;
- ΠΌΠ΅Π΄Ρ;
- ΡΠΈΡΠ°Π½;
- Π°Π»ΡΠΌΠΈΠ½ΠΈΠΉ.
Π‘ΡΡΠ΅ΡΡΠ²ΡΡΡ ΠΌΠ΅ΡΠ°Π»Π»Ρ, ΠΊΠΎΡΠΎΡΡΠ΅ Π½Π΅Π»ΡΠ·Ρ Π½ΠΈΠΊΠ΅Π»ΠΈΡΠΎΠ²Π°ΡΡ:
- ΠΎΠ»ΠΎΠ²ΠΎ;
- ΡΠ²ΠΈΠ½Π΅Ρ;
- ΠΊΠ°Π΄ΠΌΠΈΠΉ;
- ΡΡΡΡΠΌΠ°.
ΠΠΈΠΊΠ΅Π»Π΅Π²ΠΎΠ΅ ΠΏΠΎΠΊΡΡΡΠΈΠ΅ ΠΎΠ±Π΅ΡΠΏΠ΅ΡΠΈΠ²Π°Π΅Ρ Π·Π°ΡΠΈΡΡ ΠΈΠ·Π΄Π΅Π»ΠΈΡ ΠΎΡ Π²ΠΎΠ·Π΄Π΅ΠΉΡΡΠ²ΠΈΡ Π²Π»Π°Π³ΠΈ ΠΈ ΡΠ°Π·Π»ΠΈΡΠ½ΡΡ Π°Π³ΡΠ΅ΡΡΠΈΠ²Π½ΡΡ Π²Π΅ΡΠ΅ΡΡΠ². Π§Π°ΡΡΠΎ Π΅Π³ΠΎ Π½Π°Π½ΠΎΡΡΡ Π² ΠΊΠ°ΡΠ΅ΡΡΠ²Π΅ ΡΠ»ΠΎΡ-ΠΎΡΠ½ΠΎΠ²Ρ ΠΏΠ΅ΡΠ΅Π΄ Ρ ΡΠΎΠΌΠΈΡΠΎΠ²Π°Π½ΠΈΠ΅ΠΌ Π΄Π΅ΡΠ°Π»Π΅ΠΉ. ΠΠΎΡΠ»Π΅ Π½Π°Π½Π΅ΡΠ΅Π½ΠΈΡ ΡΠΎΠ½ΠΊΠΎΠΉ ΠΏΠ»Π΅Π½ΠΊΠΈ Π½ΠΈΠΊΠ΅Π»Ρ, Π½Π°ΠΏΡΠ»Π΅Π½ΠΈΡ ΠΈΠ· ΡΠ΅ΡΠ΅Π±ΡΠ°, Π·ΠΎΠ»ΠΎΡΠ° ΠΈ Π΄ΡΡΠ³ΠΈΡ ΠΌΠ΅ΡΠ°Π»Π»ΠΎΠ² Π΄Π΅ΡΠΆΠ°ΡΡΡ Π±ΠΎΠ»Π΅Π΅ ΠΏΡΠΎΡΠ½ΠΎ.
Π Π΄ΠΎΠΌΠ°ΡΠ½ΠΈΡ ΡΡΠ»ΠΎΠ²ΠΈΡΡ ΠΏΡΠΈΠΌΠ΅Π½ΡΡΡΡΡ ΡΠΏΠΎΡΠΎΠ±Ρ, Π½Π΅ ΡΡΠ΅Π±ΡΡΡΠΈΠ΅ ΠΈΡΠΏΠΎΠ»ΡΠ·ΠΎΠ²Π°Π½ΠΈΡ ΡΠΏΠ΅ΡΠΈΠ°Π»ΠΈΠ·ΠΈΡΠΎΠ²Π°Π½Π½ΠΎΠ³ΠΎ ΠΎΠ±ΠΎΡΡΠ΄ΠΎΠ²Π°Π½ΠΈΡ. ΠΠ»Π°Π³ΠΎΠ΄Π°ΡΡ ΡΡΠΎΠΌΡ, Π½ΠΈΠΊΠ΅Π»ΠΈΡΠΎΠ²Π°Π½ΠΈΠ΅ ΡΡΠ°Π»ΠΈ, ΠΌΠ΅Π΄ΠΈ, Π°Π»ΡΠΌΠΈΠ½ΠΈΡ Π² Π±ΡΡΠΎΠ²ΡΡ ΡΡΠ»ΠΎΠ²ΠΈΡΡ Π΄ΠΎΡΡΡΠΏΠ½ΠΎ ΠΏΡΠ°ΠΊΡΠΈΡΠ΅ΡΠΊΠΈ ΠΊΠ°ΠΆΠ΄ΠΎΠΌΡ ΡΠ΅Π»ΠΎΠ²Π΅ΠΊΡ. Π§ΡΠΎΠ±Ρ ΠΏΠΎΠ»ΡΡΠΈΡΡ ΡΠ°Π²Π½ΠΎΠΌΠ΅ΡΠ½ΠΎΠ΅ ΠΏΠΎΠΊΡΡΡΠΈΠ΅, Π½Π΅ΠΎΠ±Ρ ΠΎΠ΄ΠΈΠΌΠΎ ΠΏΡΠ΅Π΄Π²Π°ΡΠΈΡΠ΅Π»ΡΠ½ΠΎ ΠΏΠΎΠ΄Π³ΠΎΡΠΎΠ²ΠΈΡΡ Π΄Π΅ΡΠ°Π»Ρ.
ΠΡΠ΅ΠΈΠΌΡΡΠ΅ΡΡΠ²ΠΎ Π½ΠΈΠΊΠ΅Π»ΠΈΡΠΎΠ²Π°Π½ΠΈΡ
ΠΠ°ΠΊ ΠΏΠΎΠ΄Π³ΠΎΡΠΎΠ²ΠΈΡΡ ΠΈΠ·Π΄Π΅Π»ΠΈΠ΅ ΠΊ Π½ΠΈΠΊΠ΅Π»ΠΈΡΠΎΠ²Π°Π½ΠΈΡ?
ΠΠΎΠ΄Π³ΠΎΡΠΎΠ²ΠΊΠ° ΠΈΠ·Π΄Π΅Π»ΠΈΡ Π΄ΠΎΠ²ΠΎΠ»ΡΠ½ΠΎ ΡΡΡΠ΄ΠΎΠ΅ΠΌΠΊΠΈΠΉ ΠΏΡΠΎΡΠ΅ΡΡ. Π‘Π»Π΅Π΄ΡΠ΅Ρ ΠΏΠΎΠ»Π½ΠΎΡΡΡΡ ΠΈΡΠΊΠ»ΡΡΠΈΡΡ Π½Π°Π»ΠΈΡΠΈΠ΅ ΠΊΠΎΡΡΠΎΠ·ΠΈΠΈ, ΠΎΠΊΠΈΡΠ»Π΅Π½ΠΈΠΉ ΠΈ Ρ. ΠΏ. ΠΠΎΠ΄Π³ΠΎΡΠΎΠ²ΠΊΠ° ΠΏΡΠΎΠ²ΠΎΠ΄ΠΈΡΡΡ Π² Π½Π΅ΡΠΊΠΎΠ»ΡΠΊΠΎ ΡΡΠ°ΠΏΠΎΠ².
ΠΠ±ΡΠ°Π±ΠΎΡΠΊΠ° ΠΏΠ΅ΡΠΊΠΎΡΡΡΡΠΉΠ½ΡΠΌ Π°ΠΏΠΏΠ°ΡΠ°ΡΠΎΠΌ
ΠΠ°Π½Π½ΡΠΉ Π²ΠΈΠ΄ ΠΎΠ±ΡΠ°Π±ΠΎΡΠΊΠΈ ΠΌΠΎΠΆΠ½ΠΎ Π²ΡΠΏΠΎΠ»Π½ΡΡΡ ΠΊΠ°ΠΊ ΡΠΏΠ΅ΡΠΈΠ°Π»ΠΈΠ·ΠΈΡΠΎΠ²Π°Π½Π½ΡΠΌ ΠΏΠ΅ΡΠΊΠΎΡΡΡΡΠΉΠ½ΡΠΌ Π°ΠΏΠΏΠ°ΡΠ°ΡΠΎΠΌ, ΡΠ°ΠΊ ΠΈ ΡΠ°ΠΌΠΎΠ΄Π΅Π»ΡΠ½ΡΠΌ. ΠΠΎ Π²ΡΠ΅ΠΌΡ ΠΎΠ±ΡΠ°Π±ΠΎΡΠΊΠΈ Π½ΡΠΆΠ½ΠΎ ΠΏΠΎΡΡΠ°ΡΠ°ΡΡΡΡ ΡΠ±ΡΠ°ΡΡ ΠΊΠ°ΠΊ ΠΌΠΎΠΆΠ½ΠΎ Π±ΠΎΠ»ΡΡΠ΅ ΠΏΠΎΡΡΠΎΡΠΎΠ½Π½ΠΈΡ Π½Π°ΡΠ»ΠΎΠ΅Π½ΠΈΠΉ Ρ ΠΏΠΎΠ²Π΅ΡΡ Π½ΠΎΡΡΠΈ Π·Π°Π³ΠΎΡΠΎΠ²ΠΊΠΈ. ΠΡΠΎΠ±ΠΎΠ΅ Π²Π½ΠΈΠΌΠ°Π½ΠΈΠ΅ ΡΠ»Π΅Π΄ΡΠ΅Ρ ΠΎΠ±ΡΠ°ΡΠΈΡΡ Π½Π° ΡΡΡΠ΄Π½ΠΎΠ΄ΠΎΡΡΡΠΏΠ½ΡΠ΅ ΠΌΠ΅ΡΡΠ°. ΠΠ½ΠΈ Π΄ΠΎΠ»ΠΆΠ½Ρ Π±ΡΡΡ ΠΎΡΠΈΡΠ΅Π½Ρ ΡΠ°ΠΊ ΠΆΠ΅, ΠΊΠ°ΠΊ ΠΈ Π΄ΡΡΠ³ΠΈΠ΅ ΡΡΠ°ΡΡΠΊΠΈ ΠΏΠΎΠ²Π΅ΡΡ Π½ΠΎΡΡΠΈ.
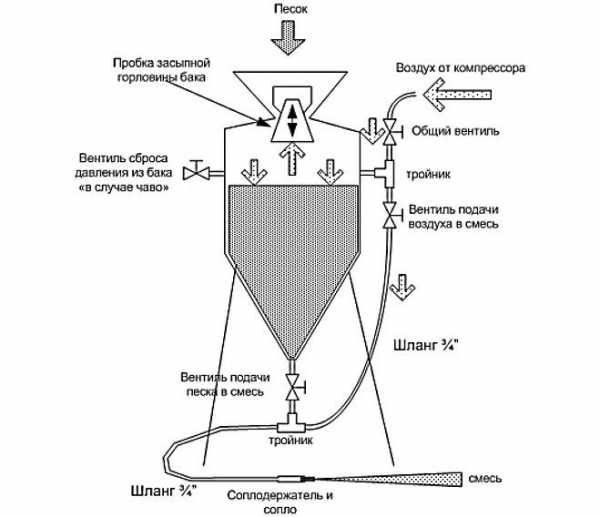
ΠΠ±ΡΠ°Ρ ΡΡ Π΅ΠΌΠ° ΠΏΠ΅ΡΠΊΠΎΡΡΡΡΠΉΠ½ΠΎΠ³ΠΎ Π°ΠΏΠΏΠ°ΡΠ°ΡΠ°
Π¨Π»ΠΈΡΠΎΠ²ΠΊΠ°
Π§ΡΠΎΠ±Ρ Π½ΠΈΠΊΠ΅Π»Π΅Π²ΠΎΠ΅ ΠΏΠΎΠΊΡΡΡΠΈΠ΅ ΠΏΠΎΠ»ΡΡΠΈΠ»ΠΎΡΡ ΡΠ°Π²Π½ΠΎΠΌΠ΅ΡΠ½ΡΠΌ, Π½ΡΠΆΠ½ΠΎ ΠΌΠ°ΠΊΡΠΈΠΌΠ°Π»ΡΠ½ΠΎ Π²ΡΡΠΎΠ²Π½ΡΡΡ ΠΏΠΎΠ²Π΅ΡΡ Π½ΠΎΡΡΡ. Π¨Π»ΠΈΡΠΎΠ²ΠΊΠ° Π΄Π°Π΅Ρ Π²ΠΎΠ·ΠΌΠΎΠΆΠ½ΠΎΡΡΡ ΠΎΡΠΈΡΡΠΈΡΡ ΠΏΡΠ΅Π΄ΠΌΠ΅Ρ ΠΎΡ ΠΎΠΊΡΠΈΠ΄Π½ΠΎΠΉ ΠΏΠ»Π΅Π½ΠΊΠΈ. ΠΠ»Ρ Π²ΡΠΏΠΎΠ»Π½Π΅Π½ΠΈΡ ΡΡΠΎΠ³ΠΎ ΡΡΠ°ΠΏΠ° ΠΈΡΠΏΠΎΠ»ΡΠ·ΡΠ΅ΡΡΡ Π½Π°ΠΆΠ΄Π°ΡΠ½Π°Ρ Π±ΡΠΌΠ°Π³Π°, Π° ΡΠ°ΠΊΠΆΠ΅ ΡΠ°Π·Π»ΠΈΡΠ½ΡΠ΅ ΠΈΠ½ΡΡΡΡΠΌΠ΅Π½ΡΡ ΠΈ ΠΏΡΠΈΡΠΏΠΎΡΠΎΠ±Π»Π΅Π½ΠΈΡ, ΠΏΡΠ΅Π΄Π½Π°Π·Π½Π°ΡΠ΅Π½Π½ΡΠ΅ Π΄Π»Ρ ΡΠ»ΠΈΡΠΎΠ²ΠΊΠΈ.

ΠΠΎ ΠΈ ΠΏΠΎΡΠ»Π΅ ΠΏΠ΅ΡΠΊΠΎΡΡΡΡΠΉΠ½ΠΎΠΉ ΠΎΠ±ΡΠ°Π±ΠΎΡΠΊΠΈ
Π‘ΠΎΠ²Π΅Ρ: Π½Π΅ ΡΡΠΎΠΈΡ ΠΏΡΠ΅Π½Π΅Π±ΡΠ΅Π³Π°ΡΡ ΡΠ»ΠΈΡΠΎΠ²ΠΊΠΎΠΉ Π·Π°Π³ΠΎΡΠΎΠ²ΠΎΠΊ, Π½Π΅ΠΏΡΠ°Π²ΠΈΠ»ΡΠ½Π°Ρ ΠΏΠΎΠ΄Π³ΠΎΡΠΎΠ²ΠΊΠ° ΠΌΠΎΠΆΠ΅Ρ ΠΏΡΠΈΠ²Π΅ΡΡΠΈ ΠΊ ΠΎΡΡΠ»ΠΎΠ΅Π½ΠΈΡ ΠΏΠΎΠΊΡΡΡΠΈΡ.
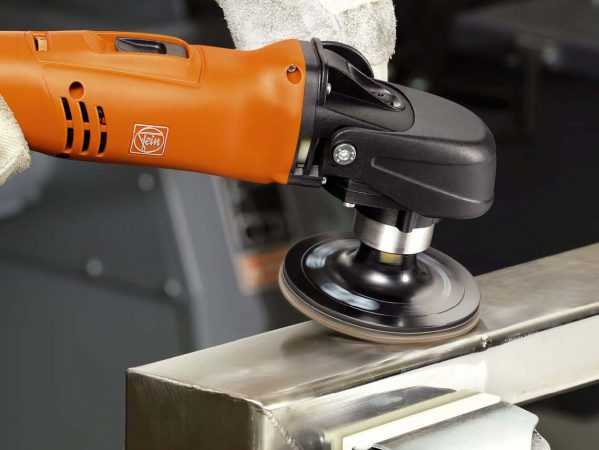
Π‘Π»Π΅Π΄ΡΡΡΠΈΠΉ ΡΡΠ°ΠΏ ΠΏΠΎΠ΄Π³ΠΎΡΠΎΠ²ΠΊΠΈ ΠΌΠ΅ΡΠ°Π»Π»Π° β ΡΠ»ΠΈΡΠΎΠ²ΠΊΠ°
Π£ΡΡΡΠ°Π½Π΅Π½ΠΈΠ΅ ΠΆΠΈΡΠΎΠ²ΡΡ Π·Π°Π³ΡΡΠ·Π½Π΅Π½ΠΈΠΉ
ΠΠΎΡΠ»Π΅ ΡΠΎΠ³ΠΎ, ΠΊΠ°ΠΊ ΠΏΡΠΎΡΠ΅ΡΡ ΡΠ»ΠΈΡΠΎΠ²ΠΊΠΈ ΠΎΠΊΠΎΠ½ΡΠ΅Π½, ΡΠ»Π΅Π΄ΡΠ΅Ρ ΡΠΌΡΡΡ ΠΎΠ±ΡΠ°Π·ΠΎΠ²Π°Π²ΡΠΈΠ΅ΡΡ Π·Π°Π³ΡΡΠ·Π½Π΅Π½ΠΈΡ ΠΏΠΎΠ΄ ΠΏΡΠΎΡΠΎΡΠ½ΠΎΠΉ Π²ΠΎΠ΄ΠΎΠΉ. ΠΠ°ΡΠ΅ΠΌ ΠΏΠΎΡΡΠ΅Π±ΡΠ΅ΡΡΡ ΠΏΡΠΎΠ²Π΅ΡΡΠΈ ΠΎΠ±Π΅Π·ΠΆΠΈΡΠΈΠ²Π°Π½ΠΈΠ΅ Π·Π°Π³ΠΎΡΠΎΠ²ΠΊΠΈ. ΠΠ»Ρ ΡΡΠΎΠ³ΠΎ ΠΌΠΎΠΆΠ½ΠΎ ΠΈΡΠΏΠΎΠ»ΡΠ·ΠΎΠ²Π°ΡΡ ΠΊΠ°ΠΊ Π³ΠΎΡΠΎΠ²ΡΠ΅, ΡΠ°ΠΊ ΠΈ ΡΠ°ΠΌΠΎΠ΄Π΅Π»ΡΠ½ΡΠ΅ ΡΠ°ΡΡΠ²ΠΎΡΠΈΡΠ΅Π»ΠΈ. ΠΠΎΡΠ»Π΅ Π½Π°Π½Π΅ΡΠ΅Π½ΠΈΡ ΡΠ°ΡΡΠ²ΠΎΡΠΈΡΠ΅Π»Ρ Π΄Π΅ΡΠ°Π»Ρ Π½ΡΠΆΠ½ΠΎ Π΅ΡΠ΅ ΡΠ°Π· ΠΏΡΠΎΠΌΡΡΡ Π²ΠΎΠ΄ΠΎΠΉ ΠΈ ΡΡΠ°ΡΠ΅Π»ΡΠ½ΠΎ ΠΏΡΠΎΡΡΡΠΈΡΡ.
ΠΠ½ΠΈΠΌΠ°Π½ΠΈΠ΅: ΠΏΡΠΈ Π²ΡΠ±ΠΎΡΠ΅ ΡΠ°ΡΡΠ²ΠΎΡΠΈΡΠ΅Π»Ρ Π½Π΅ΠΎΠ±Ρ ΠΎΠ΄ΠΈΠΌΠΎ ΡΡΠΈΡΡΠ²Π°ΡΡ ΡΡΠ΅ΠΏΠ΅Π½Ρ Π΅Π³ΠΎ Π²ΠΎΠ·Π΄Π΅ΠΉΡΡΠ²ΠΈΡ Π½Π° ΠΌΠ΅ΡΠ°Π»Π», ΠΈΠ· ΠΊΠΎΡΠΎΡΠΎΠ³ΠΎ Π²ΡΠΏΠΎΠ»Π½Π΅Π½ΠΎ ΠΈΠ·Π΄Π΅Π»ΠΈΠ΅. ΠΠ°ΠΏΡΠ΅ΡΠ°Π΅ΡΡΡ ΠΏΡΠΈΠΌΠ΅Π½ΡΡΡ ΠΎΠ±Π΅Π·ΠΆΠΈΡΠΈΠ²Π°ΡΡΠΈΠ΅ ΡΠ°ΡΡΠ²ΠΎΡΡ, Π²ΡΡΡΠΏΠ°ΡΡΠΈΠ΅ Π² Ρ ΠΈΠΌΠΈΡΠ΅ΡΠΊΡΡ ΡΠ΅Π°ΠΊΡΠΈΡ Ρ ΠΏΠΎΠ²Π΅ΡΡ Π½ΠΎΡΡΡΡ.
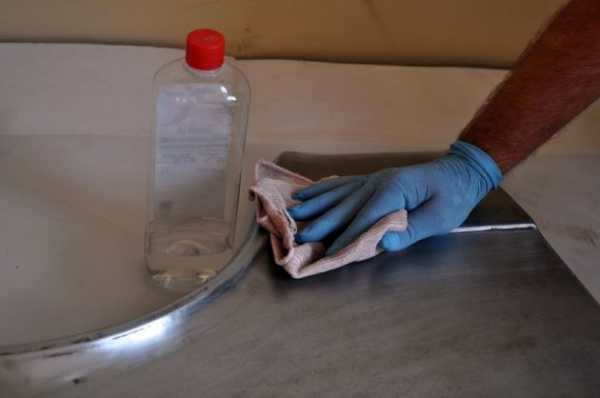
ΠΠ±Π΅Π·ΠΆΠΈΡΠΈΠ²Π°Π½ΠΈΠ΅ ΠΌΠ΅ΡΠ°Π»Π»Π°
ΠΠΌΠ΅Π΄Π½Π΅Π½ΠΈΠ΅
ΠΠΈΠΊΠ΅Π»ΠΈΡΠΎΠ²Π°Π½ΠΈΠ΅ ΠΈΠ·Π΄Π΅Π»ΠΈΡ Π»ΡΡΡΠ΅ ΠΏΡΠΎΠ²ΠΎΠ΄ΠΈΡΡ Ρ ΠΏΡΠ΅Π΄Π²Π°ΡΠΈΡΠ΅Π»ΡΠ½ΡΠΌ ΠΎΠΌΠ΅Π΄Π½Π΅Π½ΠΈΠ΅ΠΌ Π·Π°Π³ΠΎΡΠΎΠ²ΠΊΠΈ. ΠΡΠΎΡ ΡΡΠ°ΠΏ Π½Π΅ ΡΠ²Π»ΡΠ΅ΡΡΡ ΠΎΠ±ΡΠ·Π°ΡΠ΅Π»ΡΠ½ΡΠΌ, Π½ΠΎ Π½ΠΈΠΊΠ΅Π»ΠΈΡΠΎΠ²Π°Π½ΠΈΠ΅ ΡΡΠ°Π»ΠΈ ΠΈ Π΄ΡΡΠ³ΠΈΡ ΠΌΠ΅ΡΠ°Π»Π»ΠΎΠ² Π±ΡΠ΄Π΅Ρ Π±ΠΎΠ»Π΅Π΅ ΠΊΠ°ΡΠ΅ΡΡΠ²Π΅Π½Π½ΡΠΌ, Π΅ΡΠ»ΠΈ ΠΏΠΎΠΊΡΡΡΠΈΠ΅ Π½Π°Π½ΠΎΡΠΈΡΡΡ Π½Π° ΡΠΎΠ½ΠΊΠΈΠΉ ΡΠ»ΠΎΠΉ ΠΌΠ΅Π΄ΠΈ.

ΠΠΌΠ΅Π΄Π½Π΅Π½ΠΈΠ΅ Π² Π΄ΠΎΠΌΠ°ΡΠ½ΠΈΡ ΡΡΠ»ΠΎΠ²ΠΈΡΡ
ΠΠ»Ρ ΠΎΠΌΠ΅Π΄Π½Π΅Π½ΠΈΡ Π΄Π΅ΡΠ°Π»ΠΈ Π½Π΅ΠΎΠ±Ρ ΠΎΠ΄ΠΈΠΌΠΎ ΠΏΠΎΠΌΠ΅ΡΡΠΈΡΡ Π΅Π΅ Π² ΡΡΠ΅ΠΊΠ»ΡΠ½Π½ΡΡ Π΅ΠΌΠΊΠΎΡΡΡ Ρ Π²ΠΎΠ΄Π½ΡΠΌ ΡΠ»Π΅ΠΊΡΡΠΎΠ»ΠΈΡΠΎΠΌ, ΡΠΎΡΡΠΎΡΡΠΈΠΌ ΠΈΠ· ΠΌΠ΅Π΄Π½ΠΎΠ³ΠΎ ΠΊΡΠΏΠΎΡΠΎΡΠ° ΠΈ ΡΠ΅ΡΠ½ΠΎΠΉ ΠΊΠΈΡΠ»ΠΎΡΡ. ΠΡΠ΅Π΄ΠΌΠ΅Ρ ΠΏΠΎΠ΄Π²Π΅ΡΠΈΠ²Π°Π΅ΡΡΡ Π½Π° ΠΏΡΠΎΠ²ΠΎΠ΄Π΅ ΡΠ°ΠΊΠΈΠΌ ΠΎΠ±ΡΠ°Π·ΠΎΠΌ, ΡΡΠΎΠ±Ρ ΠΎΠ½ Π½Π΅ ΠΊΠ°ΡΠ°Π»ΡΡ ΡΡΠ΅Π½ΠΎΠΊ ΠΈ Π΄Π½Π° Π΅ΠΌΠΊΠΎΡΡΠΈ. ΠΠΎ ΠΎΠ±Π΅ ΡΡΠΎΡΠΎΠ½Ρ ΠΎΡ Π·Π°Π³ΠΎΡΠΎΠ²ΠΊΠΈ ΡΠ°Π·ΠΌΠ΅ΡΠ°ΡΡΡΡ ΠΌΠ΅Π΄Π½ΡΠ΅ ΠΏΠ»Π°ΡΡΠΈΠ½Ρ, ΡΠ²Π»ΡΡΡΠΈΠ΅ΡΡ ΡΠ»Π΅ΠΊΡΡΠΎΠ΄Π°ΠΌΠΈ. ΠΠΎΡΠ»Π΅ ΡΡΠΎΠ³ΠΎ ΠΊ ΡΠ»Π΅ΠΊΡΡΠΎΠ΄Π°ΠΌ ΠΈ Π·Π°Π³ΠΎΡΠΎΠ²ΠΊΠ΅ ΠΏΠΎΠ΄ΠΊΠ»ΡΡΠ°Π΅ΡΡΡ ΠΈΡΡΠΎΡΠ½ΠΈΠΊ ΠΏΠΎΡΡΠΎΡΠ½Π½ΠΎΠ³ΠΎ ΡΠΎΠΊΠ°. Π‘ΡΠ΅ΠΏΠ΅Π½Ρ ΠΎΠΌΠ΅Π΄Π½Π΅Π½ΠΈΡ ΠΏΡΡΠΌΠΎ Π·Π°Π²ΠΈΡΠΈΡ ΠΎΡ Π²ΡΠ΅ΠΌΠ΅Π½ΠΈ ΠΏΡΠΎΠ²Π΅Π΄Π΅Π½ΠΈΡ ΠΏΡΠΎΡΠ΅ΡΡΠ°.
Π‘ΠΏΠΎΡΠΎΠ±Ρ Π½Π°Π½Π΅ΡΠ΅Π½ΠΈΡ Π½ΠΈΠΊΠ΅Π»Π΅Π²ΠΎΠ³ΠΎ ΠΏΠΎΠΊΡΡΡΠΈΡ
ΠΠΈΠΊΠ΅Π»ΠΈΡΠΎΠ²Π°Π½ΠΈΠ΅ ΠΈΠ·Π΄Π΅Π»ΠΈΡ Π² Π΄ΠΎΠΌΠ°ΡΠ½ΠΈΡ ΡΡΠ»ΠΎΠ²ΠΈΡΡ ΠΌΠΎΠΆΠ½ΠΎ Π²ΡΠΏΠΎΠ»Π½ΠΈΡΡ Π΄Π²ΡΠΌΡ ΡΠΏΠΎΡΠΎΠ±Π°ΠΌΠΈ: Ρ ΠΈΠΌΠΈΡΠ΅ΡΠΊΠΈΠΌ ΠΈ ΡΠ»Π΅ΠΊΡΡΠΎΠ»ΠΈΡΠΈΡΠ΅ΡΠΊΠΈΠΌ.
ΠΠ»Π΅ΠΊΡΡΠΎΠ»ΠΈΡΠΈΡΠ΅ΡΠΊΠΈΠΉ ΠΌΠ΅ΡΠΎΠ΄
ΠΠ°Π½Π΅ΡΠ΅Π½ΠΈΠ΅ ΠΏΠΎΠΊΡΡΡΠΈΡ Ρ ΠΈΡΠΏΠΎΠ»ΡΠ·ΠΎΠ²Π°Π½ΠΈΠ΅ΠΌ ΡΠ»Π΅ΠΊΡΡΠΎΠ»ΠΈΡΠ° Π½Π°Π·ΡΠ²Π°Π΅ΡΡΡ Π³Π°Π»ΡΠ²Π°Π½ΠΈΡΠ΅ΡΠΊΠΈΠΌ Π½ΠΈΠΊΠ΅Π»ΠΈΡΠΎΠ²Π°Π½ΠΈΠ΅ΠΌ. Π‘Π½Π°ΡΠ°Π»Π° ΠΏΠΎΡΡΠ΅Π±ΡΠ΅ΡΡΡ ΠΏΠΎΠ΄Π³ΠΎΡΠΎΠ²ΠΈΡΡ Π²ΠΎΠ΄Π½ΡΠΉ ΡΠ°ΡΡΠ²ΠΎΡ (ΡΠ»Π΅ΠΊΡΡΠΎΠ»ΠΈΡ). ΠΠ»Ρ ΡΡΠΎΠ³ΠΎ Π½Π΅ΠΎΠ±Ρ ΠΎΠ΄ΠΈΠΌΡ ΡΠ»Π΅Π΄ΡΡΡΠΈΠ΅ ΠΊΠΎΠΌΠΏΠΎΠ½Π΅Π½ΡΡ:
- ΡΠ΅ΡΠ½ΠΎΠΊΠΈΡΠ»ΡΠΉ Π½ΠΈΠΊΠ΅Π»Ρ β 70 Π³;
- ΡΠ΅ΡΠ½ΠΎΠΊΠΈΡΠ»ΡΠΉ ΠΌΠ°Π³Π½ΠΈΠΉ β 15 Π³;
- ΠΏΠΎΠ²Π°ΡΠ΅Π½Π½Π°Ρ ΡΠΎΠ»Ρ β 2.5 Π³;
- ΡΠ΅ΡΠ½ΠΎΠΊΠΈΡΠ»ΡΠΉ Π½Π°ΡΡΠΈΠΉ β 25 Π³;
- Π±ΠΎΡΠ½Π°Ρ ΠΊΠΈΡΠ»ΠΎΡΠ° β 10Π³;
- Π²ΠΎΠ΄Π° β 500Π³.
ΠΠ°ΠΆΠ΄ΡΠΉ ΠΈΠ· ΠΊΠΎΠΌΠΏΠΎΠ½Π΅Π½ΡΠΎΠ² Π½ΡΠΆΠ½ΠΎ ΠΎΡΠ΄Π΅Π»ΡΠ½ΠΎ ΡΠ°ΡΡΠ²ΠΎΡΠΈΡΡ Π² Π²ΠΎΠ΄Π΅ ΠΈ ΠΏΡΠΎΡΠΈΠ»ΡΡΡΠΎΠ²Π°ΡΡ. ΠΠΎΠ»ΡΡΠ΅Π½Π½ΡΠ΅ ΡΠ°ΡΡΠ²ΠΎΡΡ ΡΠΌΠ΅ΡΠΈΠ²Π°ΡΡ ΠΈ Π·Π°Π»ΠΈΠ²Π°ΡΡ Π² ΡΡΠ΅ΠΊΠ»ΡΠ½Π½ΡΡ Π΅ΠΌΠΊΠΎΡΡΡ. ΠΠ»Ρ Π³Π°Π»ΡΠ²Π°Π½ΠΈΡΠ΅ΡΠΊΠΎΠ³ΠΎ Π½ΠΈΠΊΠ΅Π»ΠΈΡΠΎΠ²Π°Π½ΠΈΡ Π² ΡΠΎΡΡΠ΄ Ρ ΡΠ»Π΅ΠΊΡΡΠΎΠ»ΠΈΡΠΎΠΌ ΠΏΠΎΠΌΠ΅ΡΠ°ΡΡ Π½ΠΈΠΊΠ΅Π»Π΅Π²ΡΠ΅ ΡΠ»Π΅ΠΊΡΡΠΎΠ΄Ρ. Π§ΡΠΎΠ±Ρ ΠΏΠΎΠΊΡΡΡΠΈΠ΅ Π½Π° Π·Π°Π³ΠΎΡΠΎΠ²ΠΊΠ΅ Π±ΡΠ»ΠΎ ΡΠ°Π²Π½ΠΎΠΌΠ΅ΡΠ½ΡΠΌ, ΡΠΎ Π²ΡΠ΅Ρ ΡΡΠΎΡΠΎΠ½ ΡΡΡΠ°Π½Π°Π²Π»ΠΈΠ²Π°ΡΡ Π½Π΅ ΠΌΠ΅Π½Π΅Π΅ Π΄Π²ΡΡ ΡΠ»Π΅ΠΊΡΡΠΎΠ΄ΠΎΠ².
ΠΠΎΠ΄Π³ΠΎΡΠΎΠ²Π»Π΅Π½Π½ΡΡ Π·Π°Π³ΠΎΡΠΎΠ²ΠΊΡ ΠΏΠΎΠΌΠ΅ΡΠ°ΡΡ Π² ΡΠΎΡΡΠ΄ ΠΌΠ΅ΠΆΠ΄Ρ ΡΠ»Π΅ΠΊΡΡΠΎΠ΄Π°ΠΌΠΈ ΡΠ°ΠΊΠΈΠΌ ΠΎΠ±ΡΠ°Π·ΠΎΠΌ, ΡΡΠΎΠ±Ρ ΠΎΠ½Π° Π½Π΅ ΠΊΠ°ΡΠ°Π»Π°ΡΡ ΡΡΠ΅Π½ ΠΈ Π΄Π½Π° Π΅ΠΌΠΊΠΎΡΡΠΈ. ΠΠ»Π΅ΠΊΡΡΠΎΠ΄Ρ ΡΠΎΠ΅Π΄ΠΈΠ½ΡΡΡ ΠΌΠ΅ΠΆΠ΄Ρ ΡΠΎΠ±ΠΎΠΉ ΠΌΠ΅Π΄Π½ΡΠΌΠΈ ΠΏΡΠΎΠ²ΠΎΠ΄Π½ΠΈΠΊΠ°ΠΌΠΈ, ΠΈ ΠΏΠΎΠ΄ΠΊΠ»ΡΡΠ°ΡΡ ΠΊ ΠΏΠ»ΡΡΠΎΠ²ΠΎΠΌΡ ΠΊΠΎΠ½ΡΠ°ΠΊΡΡ ΠΈΡΡΠΎΡΠ½ΠΈΠΊΠ° ΠΏΠΎΡΡΠΎΡΠ½Π½ΠΎΠ³ΠΎ ΡΠΎΠΊΠ°. Π’ΠΎΠΊΠΎΠΏΡΠΎΠ²ΠΎΠ΄ΡΡΠΈΠΉ ΠΏΡΠΎΠ²ΠΎΠ΄ ΠΏΠΎΠ΄ΠΊΠ»ΡΡΠ°ΡΡ ΠΊ ΠΌΠΈΠ½ΡΡΠΎΠ²ΠΎΠΌΡ Π²ΡΠ²ΠΎΠ΄Ρ.
Π‘Ρ Π΅ΠΌΠ° ΡΡΡΠ°Π½ΠΎΠ²ΠΊΠΈ Π΄Π»Ρ ΡΠ»Π΅ΠΊΡΡΠΎΠ»ΠΈΡΠΈΡΠ΅ΡΠΊΠΎΠ³ΠΎ Π½ΠΈΠΊΠ΅Π»ΠΈΡΠΎΠ²Π°Π½ΠΈΡ
Π ΠΏΡΠΎΡΠ΅ΡΡΠ΅ Π½ΠΈΠΊΠ΅Π»ΠΈΡΠΎΠ²Π°Π½ΠΈΡ ΡΡΠ°Π»ΠΈ Π½Π°ΠΏΡΡΠΆΠ΅Π½ΠΈΠ΅ ΠΏΠΈΡΠ°Π½ΠΈΡ Π½Π΅ Π΄ΠΎΠ»ΠΆΠ½ΠΎ ΠΏΡΠ΅Π²ΡΡΠ°ΡΡ 6 ΠΠΎΠ»ΡΡ. Π‘Π»Π΅Π΄ΡΠ΅Ρ ΠΊΠΎΠ½ΡΡΠΎΠ»ΠΈΡΠΎΠ²Π°ΡΡ ΠΏΠ»ΠΎΡΠ½ΠΎΡΡΡ ΡΠΎΠΊΠ°, ΠΎΠ½Π° Π½Π΅ Π΄ΠΎΠ»ΠΆΠ½Π° ΠΏΡΠ΅Π²ΡΡΠ°ΡΡ 1,2 Π. ΠΡΠΎΡΠ΅ΡΡ Π·Π°Π½ΠΈΠΌΠ°Π΅Ρ ΠΎΠΊΠΎΠ»ΠΎ 30β40 ΠΌΠΈΠ½ΡΡ. ΠΠΎ Π΅Π³ΠΎ ΠΎΠΊΠΎΠ½ΡΠ°Π½ΠΈΠΈ, ΠΏΡΠ΅Π΄ΠΌΠ΅Ρ Π½ΡΠΆΠ½ΠΎ ΠΏΡΠΎΠΌΡΡΡ ΠΏΡΠΎΡΠΎΡΠ½ΠΎΠΉ Π²ΠΎΠ΄ΠΎΠΉ ΠΈ ΡΡΠ°ΡΠ΅Π»ΡΠ½ΠΎ ΠΏΡΠΎΡΡΡΠΈΡΡ. ΠΠ°Π½Π΅ΡΠ΅Π½Π½ΠΎΠ΅ ΠΏΠΎΠΊΡΡΡΠΈΠ΅ Π΄ΠΎΠ»ΠΆΠ½ΠΎ ΠΏΠΎΠ»ΡΡΠΈΡΡΡΡ ΠΌΠ°ΡΠΎΠ²ΡΠΌ ΠΈ Π³Π»Π°Π΄ΠΊΠΈΠΌ. Π§ΡΠΎΠ±Ρ ΠΏΠΎΠ²Π΅ΡΡ Π½ΠΎΡΡΡ ΠΈΠ·Π΄Π΅Π»ΠΈΡ ΠΏΡΠΈΠΎΠ±ΡΠ΅Π»Π° Π±Π»Π΅ΡΠΊ, ΠΏΠΎΡΡΠ΅Π±ΡΠ΅ΡΡΡ Π²ΡΠΏΠΎΠ»Π½ΠΈΡΡ Π΅Π΅ ΠΏΠΎΠ»ΠΈΡΠΎΠ²ΠΊΡ.
Π₯ΠΈΠΌΠΈΡΠ΅ΡΠΊΠΈΠΉ ΠΌΠ΅ΡΠΎΠ΄
ΠΠΈΠΊΠ΅Π»ΠΈΡΠΎΠ²Π°Π½ΠΈΠ΅ ΡΡΠ°Π»ΠΈ ΠΈ Π΄ΡΡΠ³ΠΈΡ ΠΌΠ΅ΡΠ°Π»Π»ΠΎΠ² Ρ ΠΈΠΌΠΈΡΠ΅ΡΠΊΠΈΠΌ ΡΠΏΠΎΡΠΎΠ±ΠΎΠΌ ΠΎΡΠ»ΠΈΡΠ°Π΅ΡΡΡ ΠΎΡ Π³Π°Π»ΡΠ²Π°Π½ΠΈΡΠ΅ΡΠΊΠΎΠ³ΠΎ ΠΏΡΠΎΡΠ½ΠΎΡΡΡΡ ΠΏΠΎΠΊΡΡΡΠΈΡ. ΠΡΠΈ ΠΏΠΎΠΌΠΎΡΠΈ Ρ ΠΈΠΌΠΈΡΠ΅ΡΠΊΠΎΠ³ΠΎ Π½ΠΈΠΊΠ΅Π»ΠΈΡΠΎΠ²Π°Π½ΠΈΡ ΠΌΠΎΠΆΠ½ΠΎ Π»Π΅Π³ΠΊΠΎ Π½Π°Π½Π΅ΡΡΠΈ Π²Π΅ΡΠ΅ΡΡΠ²ΠΎ Π΄Π°ΠΆΠ΅ Π½Π° ΡΠ°ΠΌΡΠ΅ ΡΡΡΠ΄Π½ΠΎΠ΄ΠΎΡΡΡΠΏΠ½ΡΠ΅ ΠΌΠ΅ΡΡΠ°.
ΠΠ»Ρ Π²ΡΠΏΠΎΠ»Π½Π΅Π½ΠΈΡ ΠΏΡΠΎΡΠ΅ΡΡΠ° ΠΏΠΎΡΡΠ΅Π±ΡΠ΅ΡΡΡ:
- ΡΠ½ΡΠ°ΡΠ½ΠΎ-ΠΊΠΈΡΠ»ΡΠΉ Π½Π°ΡΡΠΈΠΉ β 7.5 Π³;
- Ρ Π»ΠΎΡΠΈΡΡΡΠΉ Π½ΠΈΠΊΠ΅Π»Ρ β 12.5 Π³;
- Π³ΠΈΠΏΠΎΡΠΎΡΡΠΈΡ Π½Π°ΡΡΠΈΡ β 15 Π³;
- Π²ΠΎΠ΄Π° β 500 ΠΌΠ».
Π ΡΠΌΠ°Π»ΠΈΡΠΎΠ²Π°Π½Π½ΡΡ ΠΏΠΎΡΡΠ΄Ρ Π½Π°Π»ΠΈΠ²Π°ΡΡ Π²ΠΎΠ΄Ρ ΠΈ ΡΠ°ΡΡΠ²ΠΎΡΡΡΡ Π² Π½Π΅ΠΉ ΡΠ½ΡΠ°ΡΠ½ΠΎ-ΠΊΠΈΡΠ»ΡΠΉ Π½Π°ΡΡΠΈΠΉ ΠΈ Ρ Π»ΠΎΡΠΈΡΡΡΠΉ Π½ΠΈΠΊΠ΅Π»Ρ. ΠΠ°ΡΠ΅ΠΌ ΡΠ°ΡΡΠ²ΠΎΡ Π½Π°Π³ΡΠ΅Π²Π°ΡΡ Π΄ΠΎ ΡΠ΅ΠΌΠΏΠ΅ΡΠ°ΡΡΡΡ 90 Π³ΡΠ°Π΄ΡΡΠΎΠ². ΠΠΎ Π΄ΠΎΡΡΠΈΠΆΠ΅Π½ΠΈΡ ΡΡΠ΅Π±ΡΠ΅ΠΌΠΎΠΉ ΡΠ΅ΠΌΠΏΠ΅ΡΠ°ΡΡΡΡ Π΄ΠΎΠ±Π°Π²Π»ΡΠ΅ΡΡΡ Π³ΠΈΠΏΠΎΡΠΎΡΡΠΈΡ Π½Π°ΡΡΠΈΡ. ΠΠ·Π΄Π΅Π»ΠΈΠ΅ Π°ΠΊΠΊΡΡΠ°ΡΠ½ΠΎ ΠΏΠΎΠ΄Π²Π΅ΡΠΈΠ²Π°Π΅ΡΡΡ Π½Π°Π΄ Π΅ΠΌΠΊΠΎΡΡΡΡ Ρ ΡΠ°ΡΡΠ²ΠΎΡΠΎΠΌ. ΠΠΎΠ»ΠΈΡΠ΅ΡΡΠ²ΠΎ ΠΆΠΈΠ΄ΠΊΠΎΡΡΠΈ ΡΠ°ΡΡΡΠΈΡΡΠ²Π°Π΅ΡΡΡ ΠΈΡΡ ΠΎΠ΄Ρ ΠΈΠ· ΡΠΎΠ³ΠΎ, ΡΡΠΎ Π² 1 Π»ΠΈΡΡΠ΅ ΡΠ°ΡΡΠ²ΠΎΡΠ° ΠΌΠΎΠΆΠ½ΠΎ ΠΏΠΎΠΊΡΡΡΡ ΠΏΠΎΠ²Π΅ΡΡ Π½ΠΎΡΡΡ ΠΏΠ»ΠΎΡΠ°Π΄ΡΡ 2Π΄ΠΌ2.
ΠΠΈΠΊΠ΅Π»ΠΈΡΠΎΠ²Π°Π½ΠΈΠ΅ ΠΊΠΎΠ½ΡΡΠΎΠ»ΠΈΡΡΠ΅ΡΡΡ Π²ΠΈΠ·ΡΠ°Π»ΡΠ½ΠΎ: ΠΊΠΎΠ³Π΄Π° Π΄Π΅ΡΠ°Π»Ρ ΡΠ°Π²Π½ΠΎΠΌΠ΅ΡΠ½ΠΎ ΠΏΠΎΠΊΡΠΎΠ΅ΡΡΡ ΠΏΠ»Π΅Π½ΠΊΠΎΠΉ, ΠΏΡΠΎΡΠ΅ΡΡ Π·Π°Π²Π΅ΡΡΠ°Π΅ΡΡΡ. ΠΠΎ ΠΎΠΊΠΎΠ½ΡΠ°Π½ΠΈΠΈ, Π΄Π΅ΡΠ°Π»Ρ Π½ΡΠΆΠ½ΠΎ ΠΏΡΠΎΠΌΡΡΡ Π² ΡΠ°ΡΡΠ²ΠΎΡΠ΅, ΠΈΠ·Π³ΠΎΡΠΎΠ²Π»Π΅Π½Π½ΠΎΠΌ ΠΈΠ· Π²ΠΎΠ΄Ρ ΠΈ Π½Π΅Π±ΠΎΠ»ΡΡΠΎΠ³ΠΎ ΠΊΠΎΠ»ΠΈΡΠ΅ΡΡΠ²Π° ΠΌΠ΅Π»Π°. ΠΠΎΡΠ»Π΅ ΡΡΠΎΠ³ΠΎ ΠΎΡΡΡΠ΅ΡΡΠ²Π»ΡΡΡ ΡΡΡΠΊΡ ΠΈ ΠΏΠΎΠ»ΠΈΡΠΎΠ²ΠΊΡ Π΄Π΅ΡΠ°Π»ΠΈ.
ΠΠ°ΠΊ ΡΠ²Π΅Π»ΠΈΡΠΈΡΡ ΡΡΠΎΠΊ ΡΠ»ΡΠΆΠ±Ρ ΠΏΠΎΠΊΡΡΡΠΈΡ?
ΠΠΎΠ»ΡΡΠ΅Π½Π½ΠΎΠ΅ ΠΏΠΎΠΊΡΡΡΠΈΠ΅ ΠΈΠΌΠ΅Π΅Ρ ΠΏΠΎΡΠΈΡΡΡΡ ΡΡΡΡΠΊΡΡΡΡ. ΠΠΎΡΡΠΎΠΌΡ ΠΌΠ΅ΡΠ°Π»Π» ΠΈΠ·Π΄Π΅Π»ΠΈΡ ΠΏΠΎΠ΄Π²Π΅ΡΠΆΠ΅Π½ ΠΊΠΎΡΡΠΎΠ·ΠΈΠΈ. Π§ΡΠΎΠ±Ρ ΡΠ½ΠΈΠ·ΠΈΡΡ ΡΠΈΡΠΊ Π΅Π΅ Π²ΠΎΠ·Π½ΠΈΠΊΠ½ΠΎΠ²Π΅Π½ΠΈΡ, ΡΠ»ΠΎΠΉ Π½ΠΈΠΊΠ΅Π»Ρ ΠΏΠΎΠΊΡΡΠ²Π°ΡΡ ΡΠΌΠ°Π·ΠΎΡΠ½ΡΠΌΠΈ ΡΠΎΡΡΠ°Π²Π°ΠΌΠΈ. ΠΠΎΡΠ»Π΅ ΠΈΡ Π½Π°Π½Π΅ΡΠ΅Π½ΠΈΡ ΠΏΡΠ΅Π΄ΠΌΠ΅Ρ ΠΏΠΎΠ³ΡΡΠΆΠ°ΡΡ Π² Π΅ΠΌΠΊΠΎΡΡΡ Ρ ΡΡΠ±ΡΠΈΠΌ ΠΆΠΈΡΠΎΠΌ. Π‘ΠΏΡΡΡΡ 24 ΡΠ°ΡΠ°, Π΅Π³ΠΎ ΠΈΠ·Π»ΠΈΡΠΊΠΈ ΡΠ±ΠΈΡΠ°ΡΡ ΠΏΡΠΈ ΠΏΠΎΠΌΠΎΡΠΈ ΡΠ°ΡΡΠ²ΠΎΡΠΈΡΠ΅Π»Ρ.
ΠΡΠ»ΠΈ ΠΈΠ·Π΄Π΅Π»ΠΈΠ΅ ΠΈΠΌΠ΅Π΅Ρ ΠΊΡΡΠΏΠ½ΡΠ΅ Π³Π°Π±Π°ΡΠΈΡΡ, ΠΈ ΠΏΠΎΠ³ΡΡΠ·ΠΈΡΡ Π΅Π³ΠΎ Π² Π΅ΠΌΠΊΠΎΡΡΡ Π½Π΅Π²ΠΎΠ·ΠΌΠΎΠΆΠ½ΠΎ, ΡΠΎ Π΅Π³ΠΎ ΠΏΠΎΠ²Π΅ΡΡ Π½ΠΎΡΡΡ ΠΏΡΠΎΡΡΠΎ Π½Π°ΡΠΈΡΠ°ΡΡ ΡΡΠ±ΡΠΈΠΌ ΠΆΠΈΡΠΎΠΌ. ΠΠ°Π½Π½ΡΡ ΠΏΡΠΎΡΠ΅Π΄ΡΡΡ ΠΏΠΎΡΡΠ΅Π±ΡΠ΅ΡΡΡ ΠΏΡΠΎΠ²ΠΎΠ΄ΠΈΡΡ Π΄Π²Π°ΠΆΠ΄Ρ, Ρ ΠΏΡΠΎΠΌΠ΅ΠΆΡΡΠΊΠΎΠΌ Π²ΡΠ΅ΠΌΠ΅Π½ΠΈ ΠΎΠΊΠΎΠ»ΠΎ 12 ΡΠ°ΡΠΎΠ². Π§Π΅ΡΠ΅Π· 48 ΡΠ°ΡΠΎΠ² ΠΏΠΎΡΠ»Π΅ ΠΎΠ±ΡΠ°Π±ΠΎΡΠΊΠΈ ΠΎΡΡΠ°ΡΠΊΠΈ ΠΆΠΈΡΠ° Π½ΡΠΆΠ½ΠΎ ΡΠ΄Π°Π»ΠΈΡΡ.
ΠΠΈΠΊΠ΅Π»ΠΈΡΠΎΠ²Π°Π½ΠΈΠ΅ Π·Π°ΡΠΈΡΠ°Π΅Ρ ΠΌΠ΅ΡΠ°Π»Π» ΠΎΡ ΠΊΠΎΡΡΠΎΠ·ΠΈΠΈ
ΠΡΠΏΠΎΠ»Π½ΠΈΡΡ Π½ΠΈΠΊΠ΅Π»ΠΈΡΠΎΠ²Π°Π½ΠΈΠ΅ ΡΡΠ°Π»ΠΈ Π² Π΄ΠΎΠΌΠ°ΡΠ½ΠΈΡ ΡΡΠ»ΠΎΠ²ΠΈΡΡ ΠΌΠΎΠΆΠ½ΠΎ Π΄Π²ΡΠΌΡ ΡΠΏΠΎΡΠΎΠ±Π°ΠΌΠΈ. ΠΠ°Π½Π½ΡΠΉ ΠΏΡΠΎΡΠ΅ΡΡ ΡΠ²Π»ΡΠ΅ΡΡΡ Π½Π΅ΡΠ»ΠΎΠΆΠ½ΡΠΌ, Π½ΠΎ ΡΡΠ΅Π±ΡΠ΅Ρ ΡΡΠ°ΡΠ΅Π»ΡΠ½ΠΎΠΉ ΠΏΠΎΠ΄Π³ΠΎΡΠΎΠ²ΠΊΠΈ ΠΈ ΠΏΡΠ΅Π΄Π΅Π»ΡΠ½ΠΎΠΉ Π°ΠΊΠΊΡΡΠ°ΡΠ½ΠΎΡΡΠΈ ΠΏΡΠΈ Π²ΡΠΏΠΎΠ»Π½Π΅Π½ΠΈΠΈ. ΠΠ΅ΠΎΠ±Ρ ΠΎΠ΄ΠΈΠΌΠΎ ΠΏΡΠΈΠΎΠ±ΡΠ΅ΡΡΠΈ ΠΊΠ°ΡΠ΅ΡΡΠ²Π΅Π½Π½ΡΠ΅ ΠΊΠΎΠΌΠΏΠΎΠ½Π΅Π½ΡΡ Π΄Π»Ρ ΠΏΡΠΈΠ³ΠΎΡΠΎΠ²Π»Π΅Π½ΠΈΡ ΡΠ°ΡΡΠ²ΠΎΡΠ°, Π·Π°ΡΠ°Π½Π΅Π΅ ΠΏΠΎΠ΄Π³ΠΎΡΠΎΠ²ΠΈΡΡ ΡΠ°Π±ΠΎΡΡΡ Π·ΠΎΠ½Ρ, Π΅ΠΌΠΊΠΎΡΡΠΈ, ΠΈΠ½ΡΡΡΡΠΌΠ΅Π½ΡΡ ΠΈ ΡΡΡΡΠΎΠΉΡΡΠ²Π°.
Π ΠΏΡΠΎΡΠ΅ΡΡΠ΅ ΡΠ°Π±ΠΎΡΡ Π²Π°ΠΆΠ½ΠΎ ΡΠΎΠ±Π»ΡΠ΄Π°ΡΡ ΠΌΠ΅ΡΡ Π±Π΅Π·ΠΎΠΏΠ°ΡΠ½ΠΎΡΡΠΈ: Π·Π°ΡΠΈΡΠΈΡΡ Π³Π»Π°Π·Π° ΠΈ ΠΊΠΎΠΆΠ½ΡΠ΅ ΠΏΠΎΠΊΡΠΎΠ²Ρ ΠΎΡ ΠΏΠΎΠΏΠ°Π΄Π°Π½ΠΈΡ Ρ ΠΈΠΌΠΈΡΠ΅ΡΠΊΠΈΡ Π²Π΅ΡΠ΅ΡΡΠ², ΠΎΠ±Π΅ΡΠΏΠ΅ΡΠΈΡΡ Π΄ΠΎΡΡΠ°ΡΠΎΡΠ½ΡΡ Π²Π΅Π½ΡΠΈΠ»ΡΡΠΈΡ ΠΏΠΎΠΌΠ΅ΡΠ΅Π½ΠΈΡ, ΠΏΡΠ΅Π΄ΠΎΡΠ²ΡΠ°ΡΠΈΡΡ Π²ΠΎΠ·ΠΌΠΎΠΆΠ½ΠΎΡΡΡ Π²ΠΎΡΠΏΠ»Π°ΠΌΠ΅Π½Π΅Π½ΠΈΡ ΡΠΌΠ΅ΡΠΈ ΠΈ ΡΠ»Π΅ΠΊΡΡΠΈΡΠ΅ΡΠΊΠΎΠΉ ΡΡΡΠ°Π½ΠΎΠ²ΠΊΠΈ.
ΠΠΈΠ΄Π΅ΠΎ ΠΏΠΎ ΡΠ΅ΠΌΠ΅:Β Π₯ΠΈΠΌΠΈΡΠ΅ΡΠΊΠ°Ρ ΠΌΠ΅ΡΠ°Π»Π»ΠΈΠ·Π°ΡΠΈΡ β Π½ΠΈΠΊΠ΅Π»ΠΈΡΠΎΠ²Π°Π½ΠΈΠ΅
vtorexpo.ru
Π₯ΠΈΠΌΠΈΡΠ΅ΡΠΊΠΎΠ΅ Π½ΠΈΠΊΠ΅Π»ΠΈΡΠΎΠ²Π°Π½ΠΈΠ΅ — ΠΠ»Π΅ΠΊΡΡΠΎΠ₯ΠΈΠΌΠΈΡ
ΠΠ»Π°Π²Π½Π°Ρ Β» ΠΡΡ ΠΈΠ² Π±ΠΈΠ±Π»ΠΈΠΎΡΠ΅ΠΊΠ° Β» ΠΡΠΎΡΠ΅Π΅ Β» Π₯ΠΈΠΌΠΈΡΠ΅ΡΠΊΠΎΠ΅ Π½ΠΈΠΊΠ΅Π»ΠΈΡΠΎΠ²Π°Π½ΠΈΠ΅ΠΏΠΎ ΠΌΠ°ΡΠ΅ΡΠΈΠ°Π»Π°ΠΌ «ΠΠ°Π»ΡΠ²Π°Π½ΠΎΡΠ΅Ρ Π½ΠΈΠΊΠ° Π΄Π»Ρ ΠΌΠ°ΡΡΠ΅ΡΠΎΠ²», ΠΠΈΡΠ±ΠΈΠ»ΠΈΡ
ΠΡΠΎΡ ΠΏΡΠΎΡΠ΅ΡΡ Π±ΡΠ» Π² ΡΠ²ΠΎΠ΅ Π²ΡΠ΅ΠΌΡ ΠΎΠ΄Π½ΠΈΠΌ ΠΈΠ· Π³Π»Π°Π²Π½ΡΡ Π² ΡΠ΅Ρ Π½ΠΈΡΠ΅ΡΠΊΠΎΠΉ ΡΠΏΠ΅ΡΠΈΠ°Π»ΡΠ½ΠΎΠΉ Π»ΠΈΡΠ΅ΡΠ°ΡΡΡΠ΅, ΠΈ ΠΊΠ°Π·Π°Π»ΠΎΡΡ, ΡΡΠΎ ΠΎΠ½ ΡΠΎΠ·Π΄Π°Π΅Ρ ΡΠΈΠ»ΡΠ½ΡΡ ΠΊΠΎΠ½ΠΊΡΡΠ΅Π½ΡΠΈΡ Π΄Π»Ρ ΡΡΠ°Π΄ΠΈΡΠΈΠΎΠ½Π½ΠΎΠ³ΠΎ ΡΠ»Π΅ΠΊΡΡΠΎΠ»ΠΈΡΠΈΡΠ΅ΡΠΊΠΎΠ³ΠΎ Π½ΠΈΠΊΠ΅Π»ΠΈΡΠΎΠ²Π°Π½ΠΈΡ. Π Π½Π°ΡΡΠΎΡΡΠ΅Π΅ Π²ΡΠ΅ΠΌΡ Π΅Π³ΠΎ ΠΎΡΠ΅Π½ΠΈΠ²Π°ΡΡ Π±ΠΎΠ»Π΅Π΅ ΡΠΏΠΎΠΊΠΎΠΉΠ½ΠΎ ΠΈ ΠΏΡΠΈΠΌΠ΅Π½ΡΡΡ, ΠΊΠΎΠ³Π΄Π° Π΄Π»Ρ ΡΡΠΎΠ³ΠΎ Π΅ΡΡΡ ΡΠ΅Ρ Π½ΠΈΡΠ΅ΡΠΊΠΎΠ΅ ΠΈ ΠΌΠ°ΡΠ΅ΡΠΈΠ°Π»ΡΠ½ΠΎΠ΅ ΠΎΠ±Π΅ΡΠΏΠ΅ΡΠ΅Π½ΠΈΠ΅. ΠΡΠ½ΠΎΠ²Π½ΡΠΌ ΠΏΡΠ΅ΠΈΠΌΡΡΠ΅ΡΡΠ²ΠΎΠΌ Π½ΠΈΠΊΠ΅Π»Π΅Π²ΡΡ ΠΏΠΎΠΊΡΡΡΠΈΠΉ, Π½Π°Π½Π΅ΡΠ΅Π½Π½ΡΡ Ρ ΠΈΠΌΠΈΡΠ΅ΡΠΊΠΈΠΌ ΠΏΡΡΠ΅ΠΌ, ΡΠ²Π»ΡΠ΅ΡΡΡ ΠΎΠ΄Π½ΠΎΡΠΎΠ΄Π½Π°Ρ ΡΠΎΠ»ΡΠΈΠ½Π° Π½Π΅Π·Π°Π²ΠΈΡΠΈΠΌΠΎ ΠΎΡ ΡΠΎΡΠΌΡ ΠΈΠ·Π΄Π΅Π»ΠΈΡ. ΠΡΠΎ Ρ Π°ΡΠ°ΠΊΡΠ΅ΡΠ½ΠΎ Π΄Π»Ρ Π²ΡΠ΅Ρ ΠΏΡΠΎΡΠ΅ΡΡΠΎΠ² ΠΎΡΠ°ΠΆΠ΄Π΅Π½ΠΈΡ ΠΌΠ΅ΡΠ°Π»Π»Π° Π±Π΅Π· ΠΏΡΠΈΠΌΠ΅Π½Π΅Π½ΠΈΡ ΡΠΎΠΊΠ°. ΠΡΠΎΠ±Π΅Π½Π½ΠΎΡΡΡΡ Ρ ΠΈΠΌΠΈΡΠ΅ΡΠΊΠΎΠ³ΠΎ Π½ΠΈΠΊΠ΅Π»ΠΈΡΠΎΠ²Π°Π½ΠΈΡ ΡΠ²Π»ΡΠ΅ΡΡΡ Π½Π΅ΠΏΡΠ΅ΡΡΠ²Π½ΠΎΠ΅ ΠΎΡΠ°ΠΆΠ΄Π΅Π½ΠΈΠ΅ ΡΠ»ΠΎΡ, ΡΡΠΎ ΡΠΎΠ·Π΄Π°Π΅Ρ Π²ΠΎΠ·ΠΌΠΎΠΆΠ½ΠΎΡΡΡ ΠΎΠ±ΡΠ°Π·ΠΎΠ²Π°Π½ΠΈΡ ΠΏΠΎΠΊΡΡΡΠΈΠΉ Π»ΡΠ±ΠΎΠΉ ΡΠΎΠ»ΡΠΈΠ½Ρ. ΠΠ°Π½Π½Ρ Π΄Π»Ρ Ρ ΠΈΠΌΠΈΡΠ΅ΡΠΊΠΎΠ³ΠΎ Π½ΠΈΠΊΠ΅Π»ΠΈΡΠΎΠ²Π°Π½ΠΈΡ ΡΠΎΡΡΠΎΡΡ ΠΈΠ· ΡΠΎΠ»ΠΈ Π½ΠΈΠΊΠ΅Π»Ρ, Π³ΠΈΠΏΠΎΡΠΎΡΡΠΈΡΠ° Π½Π°ΡΡΠΈΡ ΠΈ Π΄ΠΎΠ±Π°Π²ΠΎΠΊ. ΠΡΠ½ΠΎΠ²ΠΎΠΉ ΡΠ²Π»ΡΡΡΡΡ ΡΠΎΠ»ΠΈ Π½ΠΈΠΊΠ΅Π»Ρ ΠΈ Π³ΠΈΠΏΠΎΡΠΎΡΡΠΈΡ Π½Π°ΡΡΠΈΡ. Π‘ΡΡΠ΅ΡΡΠ²ΡΡΡ Π΄Π²Π΅ ΡΠ°Π·Π½ΠΎΠ²ΠΈΠ΄Π½ΠΎΡΡΠΈ Π²Π°Π½Π½ Π΄Π»Ρ Ρ ΠΈΠΌΠΈΡΠ΅ΡΠΊΠΎΠ³ΠΎ Π½ΠΈΠΊΠ΅Π»ΠΈΡΠΎΠ²Π°Π½ΠΈΡ β ΠΊΠΈΡΠ»Π°Ρ ΠΈ ΡΠ΅Π»ΠΎΡΠ½Π°Ρ. Π ΠΊΠ°ΡΠ΅ΡΡΠ²Π΅ ΡΠΎΠ»Π΅ΠΉ Π½ΠΈΠΊΠ΅Π»Ρ, Π² ΠΎΡΠ½ΠΎΠ²Π½ΠΎΠΌ, ΠΏΡΠΈΠΌΠ΅Π½ΡΡΡ ΡΡΠ»ΡΡΠ°Ρ ΠΈΠ»ΠΈ Ρ Π»ΠΎΡΠΈΠ΄ Π½ΠΈΠΊΠ΅Π»Ρ ΠΎΡΠ½ΠΎΡΠΈΡΠ΅Π»ΡΠ½ΠΎ Π½Π΅Π±ΠΎΠ»ΡΡΠΎΠΉ (~5 Π³/Π») ΠΊΠΎΠ½ΡΠ΅Π½ΡΡΠ°ΡΠΈΠΈ. Π‘ΠΎΠ΄Π΅ΡΠΆΠ°Π½ΠΈΠ΅ Π³ΠΈΠΏΠΎΡΠΎΡΡΠΈΡΠ° Π΄ΠΎΡΡΠΈΠ³Π°Π΅Ρ 10β30 Π³/Π». ΠΠΎΠ±Π°Π²ΠΊΠΈ Π²Π²ΠΎΠ΄ΡΡΡΡ Π² Π²ΠΈΠ΄Π΅ ΠΊΠΎΠΌΠΏΠ»Π΅ΠΊΡΠΎΠΎΠ±ΡΠ°Π·ΡΡΡΠΈΡ ΡΠΎΠ΅Π΄ΠΈΠ½Π΅Π½ΠΈΠΉ, ΡΡΠΊΠΎΡΡΡΡΠΈΡ ΠΎΡΠ°ΠΆΠ΄Π΅Π½ΠΈΠ΅ Π½ΠΈΠΊΠ΅Π»Ρ, ΠΈ ΡΡΠ°Π±ΠΈΠ»ΠΈΠ·Π°ΡΠΎΡΠΎΠ², ΠΏΡΠ΅ΠΏΡΡΡΡΠ²ΡΡΡΠΈΡ ΡΠ°Π·Π»ΠΎΠΆΠ΅Π½ΠΈΡ ΡΠ»Π΅ΠΊΡΡΠΎΠ»ΠΈΡΠ°. Π ΠΊΠ°ΡΠ΅ΡΡΠ²Π΅ ΠΊΠΎΠΌΠΏΠ»Π΅ΠΊΡΠΎΠΎΠ±ΡΠ°Π·ΡΡΡΠΈΡ ΡΠΎΠ΅Π΄ΠΈΠ½Π΅Π½ΠΈΠΉ Π² ΡΠΏΠ΅ΡΠΈΠ°Π»ΡΠ½ΠΎΠΉ Π»ΠΈΡΠ΅ΡΠ°ΡΡΡΠ΅ ΡΠΏΠΎΠΌΠΈΠ½Π°ΡΡΡΡ Π³Π»ΠΈΠΊΠΎΠ»Π΅Π²Π°Ρ, ΠΌΠΎΠ»ΠΎΡΠ½Π°Ρ, Π»ΠΈΠΌΠΎΠ½Π½Π°Ρ ΠΈ Π°ΠΌΠΈΠ½ΠΎΡΠΊΡΡΡΠ½Π°Ρ ΠΊΠΈΡΠ»ΠΎΡΡ. Π£ΡΠΊΠΎΡΡΡΡΠΈΠΌΠΈ ΡΠ²Π»ΡΡΡΡΡ ΡΠ½ΡΠ°ΡΠ½Π°Ρ, ΠΌΠ°Π»ΠΎΠ½ΠΎΠ²Π°Ρ, ΠΏΡΠΎΠΏΠΈΠΎΠ½ΠΎΠ²Π°Ρ, ΠΌΠ°ΡΠ»ΡΠ½Π°Ρ, Π²Π°Π»Π΅ΡΠΈΠ°Π½ΠΎΠ²Π°Ρ ΠΈ Π΄ΡΡΠ³ΠΈΠ΅ ΠΊΠΈΡΠ»ΠΎΡΡ. ΠΠ»Ρ ΡΡΠ°Π±ΠΈΠ»ΠΈΠ·Π°ΡΠΈΠΈ ΡΠ»ΡΠΆΠ°Ρ Π² ΠΎΡΠ½ΠΎΠ²Π½ΠΎΠΌ ΡΠΎΠ΅Π΄ΠΈΠ½Π΅Π½ΠΈΡ ΡΠ²ΠΈΠ½ΡΠ°, ΡΠΈΠΎΡΡΠ»ΡΡΠ°Ρ, ΡΠΈΠΎΠΌΠΎΡΠ΅Π²ΠΈΠ½Π° ΠΈ Ρ.Π΄. ΠΠΈΠΆΠ΅ ΠΏΡΠΈΠ²Π΅Π΄Π΅Π½Ρ ΠΏΡΠΈΠΌΠ΅ΡΡ Π΄Π²ΡΡ Π²Π°Π½Π½ Π΄Π»Ρ Ρ ΠΈΠΌΠΈΡΠ΅ΡΠΊΠΎΠ³ΠΎ Π½ΠΈΠΊΠ΅Π»ΠΈΡΠΎΠ²Π°Π½ΠΈΡ, Π³/Π»:
ΠΠ°Π½Π½Π°Β Β Β Β |
1 |
2 |
Π‘ΡΠ»ΡΡΠ°Ρ Π½ΠΈΠΊΠ΅Π»Ρ (NiS04β’7Π2Π) |
20β30 |
— |
ΠΡΠ΅ΡΠ°Ρ Π½Π°ΡΡΠΈΡ (CH3β’COONaβ’3H2O) |
10β15 |
— |
ΠΠΎΠ»ΠΎΡΠ½Π°Ρ ΠΊΠΈΡΠ»ΠΎΡΠ° (CH3CHOHCOOH)Β |
25β30 |
— |
Π’ΠΈΠΎΠΌΠΎΡΠ΅Π²ΠΈΠ½Π° (H2NCSNH2) |
0,0005β0,001 |
— |
ΠΠΈΠΏΠΎΡΠΎΡΡΠΈΡ Π½Π°ΡΡΠΈΡ (Na2HPO2β’H2O) |
15β20 |
15β25 |
Π₯Π»ΠΎΡΠΈΠ΄ Π°ΠΌΠΌΠΎΠ½ΠΈΡ (NH4Cl) |
— |
30β40 |
Π¦ΠΈΡΡΠ°Ρ Π½Π°ΡΡΠΈΡ (Na3C6H5O7β’5,5H20) |
Β |
30β50 |
ΠΠΌΠΌΠΈΠ°ΠΊ (NH4OH)Β Β |
Β |
70-100 |
Π₯Π»ΠΎΡΠΈΠ΄ Π½ΠΈΠΊΠ΅Π»Ρ (NiCl2β’6H2O) |
Β |
20β30 |
Β
ΠΠ°Π½Π½Π° 1 ΠΊΠΈΡΠ»Π°Ρ, Π»ΡΡΡΠ΅ Π²ΡΠ΅Π³ΠΎ ΡΠ°Π±ΠΎΡΠ°Π΅Ρ ΠΏΡΠΈ ΡΠ = 4,3β4,8. Π Π°Π±ΠΎΡΠ°Ρ ΡΠ΅ΠΌΠΏΠ΅ΡΠ°ΡΡΡΠ° Π²Π°Π½Π½Ρ 85β90 Β°Π‘ Π΄ΠΎΠ»ΠΆΠ½Π° ΠΏΠΎΠ΄Π΄Π΅ΡΠΆΠΈΠ²Π°ΡΡΡΡ Π²ΠΎ Π²ΡΠ΅ΠΌΡ Π²ΡΠ΅Π³ΠΎ ΠΏΡΠΎΡΠ΅ΡΡΠ° Π½ΠΈΠΊΠ΅Π»ΠΈΡΠΎΠ²Π°Π½ΠΈΡ. ΠΠ»Ρ ΡΠ΅Π³ΡΠ»ΠΈΡΠΎΠ²Π°Π½ΠΈΡ ΡΠ ΡΠ»ΡΠΆΠΈΡ ΡΠ°Π·Π±Π°Π²Π»Π΅Π½Π½ΡΠΉ (Π½Π°ΠΏΡΠΈΠΌΠ΅Ρ, 5 %-Π½ΡΠΉ) ΡΠ°ΡΡΠ²ΠΎΡ Π΅Π΄ΠΊΠΎΠ³ΠΎ Π½Π°ΡΡΠ°. ΠΠΎΡΠΎΠ²ΡΡ Π²Π°Π½Π½Ρ 1 ΡΠ»Π΅Π΄ΡΡΡΠΈΠΌ ΠΎΠ±ΡΠ°Π·ΠΎΠΌ: Π² Π΄ΠΈΡΡΠΈΠ»Π»ΠΈΡΠΎΠ²Π°Π½Π½ΠΎΠΉ Π²ΠΎΠ΄Π΅, Π½Π°Π³ΡΠ΅ΡΠΎΠΉ Π΄ΠΎ ΡΠ΅ΠΌΠΏΠ΅ΡΠ°ΡΡΡΡ 60 Β°Π‘, ΡΠ½Π°ΡΠ°Π»Π° ΡΠ°ΡΡΠ²ΠΎΡΡΡΡ Π°ΡΠ΅ΡΠ°Ρ Π½Π°ΡΡΠΈΡ, Π·Π°ΡΠ΅ΠΌ ΡΡΠ»ΡΡΠ°Ρ Π½ΠΈΠΊΠ΅Π»Ρ ΠΈ Π΄ΠΎΠ±Π°Π²Π»ΡΡΡ ΠΌΠΎΠ»ΠΎΡΠ½ΡΡ ΠΊΠΈΡΠ»ΠΎΡΡ, ΠΏΡΠ΅Π΄Π²Π°ΡΠΈΡΠ΅Π»ΡΠ½ΠΎ Π½Π΅ΠΉΡΡΠ°Π»ΠΈΠ·ΠΎΠ²Π°Π½Π½ΡΡ Π΅Π΄ΠΊΠΈΠΌ Π½Π°ΡΡΠΎΠΌ Π΄ΠΎ ΡΠ = 3,5β4,0. ΠΠ°Π³ΡΠ΅Π² Π²Π°Π½Π½Ρ Π΄ΠΎ 85 Β°Π‘, Π΄ΠΎΠ±Π°Π²Π»ΡΡΡ Π³ΠΈΠΏΠΎΡΠΎΡΡΠΈΡ Π½Π°ΡΡΠΈΡ. ΠΠΎΡΠ»Π΅ ΡΡΠΎΠ³ΠΎ ΠΌΠΎΠΆΠ½ΠΎ ΠΏΡΠΈΡΡΡΠΏΠΈΡΡ ΠΊ Π½ΠΈΠΊΠ΅Π»ΠΈΡΠΎΠ²Π°Π½ΠΈΡ. ΠΠΎΠ½ΡΠ΅Π½ΡΡΠ°ΡΠΈΡ ΡΠΈΠΎΠΌΠΎΡΠ΅Π²ΠΈΠ½Ρ ΠΎΡΠ΅Π½Ρ ΠΌΠ°Π»Π° ΠΈ Π² ΡΡΠ»ΠΎΠ²ΠΈΡΡ ΠΌΠ°ΡΡΠ΅ΡΡΠΊΠΎΠΉ Π½Π΅Ρ Π²ΠΎΠ·ΠΌΠΎΠΆΠ½ΠΎΡΡΠΈ Π²Π·Π²Π΅ΡΠΈΠ²Π°Π½ΠΈΡ Ρ ΡΠΎΡΠ½ΠΎΡΡΡΡ Π΄ΠΎ Π΄ΠΎΠ»Π΅ΠΉ Π³ΡΠ°ΠΌΠΌΠ°. Π’Π°ΠΊ ΠΊΠ°ΠΊ ΠΈΠ·Π±ΡΡΠΎΠΊ ΡΠΈΠΎΠΌΠΎΡΠ΅Π²ΠΈΠ½Ρ ΠΌΠΎΠΆΠ΅Ρ ΠΏΡΠΈΠ²Π΅ΡΡΠΈ ΠΊ ΠΏΠΎΠ»Π½ΠΎΠΉ Π·Π°Π΄Π΅ΡΠΆΠΊΠ΅ ΠΏΡΠΎΡΠ΅ΡΡΠ° Π½ΠΈΠΊΠ΅Π»ΠΈΡΠΎΠ²Π°Π½ΠΈΡ, Π»ΡΡΡΠ΅ ΠΏΠΎΠ»Π½ΠΎΡΡΡΡ ΠΎΡΠΊΠ°Π·Π°ΡΡΡΡ ΠΎΡ ΡΡΠΎΠ³ΠΎ ΡΡΠ°Π±ΠΈΠ»ΠΈΠ·Π°ΡΠΎΡΠ° ΠΈ Π²ΠΎΡΠΏΠΎΠ»ΡΠ·ΠΎΠ²Π°ΡΡΡΡ Π²Π°Π½Π½ΠΎΠΉ Π±Π΅Π· ΡΠΈΠΎΠΌΠΎΡΠ΅Π²ΠΈΠ½Ρ. ΠΠ°Π½Π½Π° 2 ΡΠ΅Π»ΠΎΡΠ½Π°Ρ. Π Π΄ΠΈΡΡΠΈΠ»Π»ΠΈΡΠΎΠ²Π°Π½Π½ΠΎΠΉ Π²ΠΎΠ΄Π΅, Π½Π°Π³ΡΠ΅ΡΠΎΠΉ Π΄ΠΎ 60 Β°Π‘, ΡΠ°ΡΡΠ²ΠΎΡΡΡΡ ΡΠΈΡΡΠ°Ρ Π½Π°ΡΡΠΈΡ, Ρ Π»ΠΎΡΠΈΠ΄Ρ Π°ΠΌΠΌΠΎΠ½ΠΈΡ ΠΈ Π½ΠΈΠΊΠ΅Π»Ρ, Π΄ΠΎΠ±Π°Π²Π»ΡΡΡ ΠΏΠΎΡΡΠΈΡΠΌΠΈ ΠΏΡΠΈ ΠΏΠΎΡΡΠΎΡΠ½Π½ΠΎΠΌ ΠΏΠ΅ΡΠ΅ΠΌΠ΅ΡΠΈΠ²Π°Π½ΠΈΠΈ ΡΠ°ΡΡΠ²ΠΎΡ Π°ΠΌΠΌΠΈΠ°ΠΊΠ° Ρ ΡΠ΅Π»ΡΡ Π΄ΠΎΡΡΠΈΠΆΠ΅Π½ΠΈΡ ΡΠ = 8β9.ΒΠΡΠΈ ΡΡΠΎΠΌ ΠΏΡΠΎΠΈΡΡ ΠΎΠ΄ΠΈΡ Π·Π°ΠΌΠ΅ΡΠ½ΠΎΠ΅ ΠΈΠ·ΠΌΠ΅Π½Π΅Π½ΠΈΠ΅ ΡΠ²Π΅ΡΠ° ΡΠ°ΡΡΠ²ΠΎΡΠ° Ρ Π·Π΅Π»Π΅Π½ΠΎΠ²Π°ΡΠΎΠ³ΠΎ Π½Π° Π³ΠΎΠ»ΡΠ±ΠΎΠΉ. ΠΠΎΡΠ»Π΅ ΠΏΠΎΠ΄ΠΎΠ³ΡΠ΅Π²Π° Π΄ΠΎ 80 Β°Π‘ Π΄ΠΎΠ±Π°Π²Π»ΡΡΡ Π³ΠΈΠΏΠΎΡΠΎΡΡΠΈΡ ΠΈ Π²Π°Π½Π½Π° Π³ΠΎΡΠΎΠ²Π° ΠΊ ΡΠΊΡΠΏΠ»ΡΠ°ΡΠ°ΡΠΈΠΈ.
ΠΡΠΈΠ²Π΅Π΄Π΅Π½Π½Π°Ρ ΠΈΠ½ΡΠΎΡΠΌΠ°ΡΠΈΡ ΠΎΡΠ΅Π½Ρ ΠΎΠ±ΡΠ°Ρ ΠΈ ΠΌΠ°Π»ΠΎ ΠΎΡΡΠ°ΠΆΠ°Π΅Ρ ΠΏΡΠ°ΠΊΡΠΈΡΠ΅ΡΠΊΡΡ ΡΡΠΎΡΠΎΠ½Ρ Π½ΠΈΠΊΠ΅Π»ΠΈΡΠΎΠ²Π°Π½ΠΈΡ. ΠΡΠΈ ΠΌΠ΅Π½Π΅Π΅ 80 Β°Π‘ ΡΡΡΠ΅ΠΊΡΠΈΠ²Π½ΠΎΡΡΡ Π²Π°Π½Π½Ρ ΠΎΡΠ΅Π½Ρ Π½ΠΈΠ·ΠΊΠ°. ΠΡΠΈ 90 Β°Π‘ ΠΏΠΎΠ»ΡΡΠ°ΡΡ Π² ΡΠ΅ΡΠ΅Π½ΠΈΠ΅ 1 Ρ ΡΠ»ΠΎΠΉ Π½ΠΈΠΊΠ΅Π»Ρ ΡΠΎΠ»ΡΠΈΠ½ΠΎΠΉ 10β20 ΠΌΠΊΠΌ. ΠΡΠΈ Π΄Π°Π»ΡΠ½Π΅ΠΉΡΠ΅ΠΌ ΠΏΠΎΠ²ΡΡΠ΅Π½ΠΈΠΈ ΡΠ΅ΠΌΠΏΠ΅ΡΠ°ΡΡΡΡ, Π½Π°ΠΏΡΠΈΠΌΠ΅Ρ, Π΄ΠΎ 95Β°Π‘ ΠΏΠΎΠ»ΡΡΠ°ΡΡ Π±ΠΎΠ»Π΅Π΅ ΡΠΎΠ»ΡΡΡΠ΅ ΡΠ»ΠΎΠΈ, Π½ΠΎ ΡΡΠ°Π±ΠΈΠ»ΡΠ½ΠΎΡΡΡ Π²Π°Π½Π½Ρ ΡΠ½ΠΈΠΆΠ°Π΅ΡΡΡ. Π ΠΎΠΏΡΠ΅Π΄Π΅Π»Π΅Π½Π½ΡΠΉ ΠΌΠΎΠΌΠ΅Π½Ρ ΠΌΠΎΠΆΠ΅Ρ Π½Π°ΡΡΡΠΏΠΈΡΡ Π²Π½Π΅Π·Π°ΠΏΠ½ΠΎΠ΅ ΡΠ°Π·Π»ΠΎΠΆΠ΅Π½ΠΈΠ΅ Π²Π°Π½Π½Ρ, ΡΡΠΎ ΡΠΎΠΏΡΠΎΠ²ΠΎΠΆΠ΄Π°Π΅ΡΡΡ ΠΏΠΎΡΠ²Π»Π΅Π½ΠΈΠ΅ΠΌ ΡΠ΅ΡΠ½ΠΎΠ³ΠΎ ΠΏΠΎΡΠΎΡΠΊΠ° Π½Π° Π΄Π½Π΅ ΠΈ ΡΡΠ΅Π½ΠΊΠ°Ρ Π²Π°Π½Π½Ρ. Π’Π°ΠΊΠ°Ρ Π²Π°Π½Π½Π° Π½Π΅ΠΏΡΠΈΠ³ΠΎΠ΄Π½Π° Π΄Π»Ρ Π΄Π°Π»ΡΠ½Π΅ΠΉΡΠ΅Π³ΠΎ ΠΈΡΠΏΠΎΠ»ΡΠ·ΠΎΠ²Π°Π½ΠΈΡ. Π‘Π΅ΡΡΠ΅Π·Π½ΠΎΠΉ ΠΏΡΠΎΠ±Π»Π΅ΠΌΠΎΠΉ ΡΠ²Π»ΡΠ΅ΡΡΡ Π²ΡΠ±ΠΎΡ ΡΠΎΠΎΡΠ²Π΅ΡΡΡΠ²ΡΡΡΠΈΡ ΡΠ°Π±ΠΎΡΠΈΡ Π΅ΠΌΠΊΠΎΡΡΠ΅ΠΉ. Π ΠΏΡΠΎΠΌΡΡΠ»Π΅Π½Π½ΡΡ ΡΡΠ»ΠΎΠ²ΠΈΡΡ ΠΏΡΠΈΠΌΠ΅Π½ΡΡΡ ΡΠ»ΠΎΠΆΠ½ΡΠ΅ ΡΡΡΠ°Π½ΠΎΠ²ΠΊΠΈ ΠΈΠ· ΠΊΠΎΡΡΠΎΠ·ΠΈΠΎΠ½Π½ΠΎΡΡΠΎΠΉΠΊΠΎΠΉ ΡΡΠ°Π»ΠΈ, ΡΠΎΠ³Π΄Π° ΠΊΠ°ΠΊ Π΄Π»Ρ Π½ΠΈΠΊΠ΅Π»ΠΈΡΠΎΠ²Π°Π½ΠΈΡ Π² ΠΌΠ°Π»ΠΎΠΌ ΠΎΠ±ΡΠ΅ΠΌΠ΅ Π² ΠΎΡΠ½ΠΎΠ²Π½ΠΎΠΌ ΡΠ»ΡΠΆΠ°Ρ ΡΡΠ΅ΠΊΠ»ΡΠ½Π½ΡΠ΅, ΡΠ°ΡΡΠΎΡΠΎΠ²ΡΠ΅ ΠΈΠ»ΠΈ ΡΠΌΠ°Π»ΠΈΡΠΎΠ²Π°Π½Π½ΡΠ΅ Π΅ΠΌΠΊΠΎΡΡΠΈ. ΠΠ°ΠΈΠ»ΡΡΡΠΈΠΌ ΡΠΏΠΎΡΠΎΠ±ΠΎΠΌ Π½Π°Π³ΡΠ΅Π²Π° ΠΌΠ°Π»ΡΡ ΠΈ ΡΡΠ΅Π΄Π½ΠΈΡ Π΅ΠΌΠΊΠΎΡΡΠ΅ΠΉ ΡΠ²Π»ΡΠ΅ΡΡΡ Π²ΠΎΠ΄ΡΠ½Π°Ρ ΡΡΠ±Π°ΡΠΊΠ°. ΠΠΏΡΡΡΠΈΠΌ 5 Π» ΡΡΠ΅ΠΊΠ»ΡΠ½Π½ΡΠΉ ΡΠΎΡΡΠ΄ Π² ΡΠΌΠ°Π»ΠΈΡΠΎΠ²Π°Π½Π½ΡΠΉ 10 Π» Π±Π°ΠΊ Ρ Π²ΠΎΠ΄ΠΎΠΉ, ΠΌΡ ΠΌΠΎΠΆΠ΅ΠΌ ΠΏΠΎΠ»ΡΡΠΈΡΡ Π²ΠΎΠ΄ΡΠ½ΡΡ ΡΡΠ±Π°ΡΠΊΡ, ΠΏΡΠΈΠ³ΠΎΠ΄Π½ΡΡ Π΄Π»Ρ Π³Π°Π·ΠΎ- ΠΈΠ»ΠΈ ΡΠ»Π΅ΠΊΡΡΠΎΠ½Π°Π³ΡΠ΅Π²Π° Π΅Π΅ Π΄ΠΎ ΡΠ΅ΠΌΠΏΠ΅ΡΠ°ΡΡΡΡ ΠΊΠΈΠΏΠ΅Π½ΠΈΡ. Π ΡΡΠ΅ΠΊΠ»ΡΠ½Π½ΠΎΠΌ ΡΠΎΡΡΠ΄Π΅ ΠΌΠΎΠΆΠ½ΠΎ Π΄ΠΎΡΡΠΈΡΡ ΡΠ΅ΠΌΠΏΠ΅ΡΠ°ΡΡΡΡ 83β85 Β°Π‘, Π΄ΠΎΡΡΠ°ΡΠΎΡΠ½ΠΎΠΉ Π΄Π»Ρ ΠΏΡΠΎΠ²Π΅Π΄Π΅Π½ΠΈΡ ΠΏΡΠΎΡΠ΅ΡΡΠ°. ΠΡΡΠΎΠΊΠ°Ρ ΡΠ΅ΠΌΠΏΠ΅ΡΠ°ΡΡΡΠ° ΠΈ ΡΠΈΠ»ΡΠ½ΠΎΠ΅ Π³Π°Π·ΠΎΠ²ΡΠ΄Π΅Π»Π΅Π½ΠΈΠ΅ Π½Π° ΠΏΠΎΠ²Π΅ΡΡ Π½ΠΎΡΡΠΈ ΠΈΠ·Π΄Π΅Π»ΠΈΠΉ ΡΠΈΠΊΡΠΈΡΡΠ΅ΡΡΡ ΠΎΠ±ΡΠ»ΡΠΆΠΈΠ²Π°ΡΡΠΈΠΌ ΠΏΠ΅ΡΡΠΎΠ½Π°Π»ΠΎΠΌ ΠΏΠΎ ΡΠΈΠ»ΡΠ½ΠΎΠΌΡ Π½Π΅ΠΏΡΠΈΡΡΠ½ΠΎΠΌΡ Π·Π°ΠΏΠ°Ρ Ρ. ΠΡΠ΅Π²ΠΈΠ΄Π½ΠΎ, ΡΡΠΎ Π²ΡΡ ΡΡΡΠ°Π½ΠΎΠ²ΠΊΠ° Π΄ΠΎΠ»ΠΆΠ½Π° Π½Π°Ρ ΠΎΠ΄ΠΈΡΡΡΡ ΠΏΠΎΠ΄ Π²ΡΡΡΠΆΠΊΠΎΠΉ. ΠΠ°ΠΊ Π²ΠΈΠ΄Π½ΠΎ, Π²ΡΡ ΠΏΡΠΎΡΠ΅Π΄ΡΡΠ° Π½Π΅ΠΏΡΠΎΡΡΠ°, Π²ΡΠ»Π΅Π΄ΡΡΠ²ΠΈΠ΅ ΡΠ΅Π³ΠΎ ΠΏΡΠΈΠΌΠ΅Π½Π΅Π½ΠΈΠ΅ Ρ ΠΈΠΌΠΈΡΠ΅ΡΠΊΠΎΠ³ΠΎ Π½ΠΈΠΊΠ΅Π»ΠΈΡΠΎΠ²Π°Π½ΠΈΡ ΠΎΠ³ΡΠ°Π½ΠΈΡΠ΅Π½ΠΎ ΡΠ΅ΠΌΠΈ ΡΠ»ΡΡΠ°ΡΠΌΠΈ, ΠΊΠΎΠ³Π΄Π° Π½Π΅ΠΏΡΠΈΠΌΠ΅Π½ΠΈΠΌΡ ΡΠ»Π΅ΠΊΡΡΠΎΠ»ΠΈΡΠΈΡΠ΅ΡΠΊΠΈΠ΅ ΠΌΠ΅ΡΠΎΠ΄Ρ. ΠΠ°ΠΏΡΠΈΠΌΠ΅Ρ, ΠΌΠ΅ΡΠ°Π»Π»ΠΈΡΠ΅ΡΠΊΠΈΠ΅ ΡΠΈΠ»ΡΡΠΎΠ½Ρ Π² Π²ΠΈΠ΄Π΅ ΡΠΈΠ»ΠΈΠ½Π΄ΡΠΈΡΠ΅ΡΠΊΠΎΠΉ Π³Π°ΡΠΌΠΎΡΠΊΠΈ, ΠΏΡΠΈΠΌΠ΅Π½ΡΠ΅ΠΌΡΠ΅ Π΄Π»Ρ ΠΈΠ·ΠΌΠ΅ΡΠ΅Π½ΠΈΡ Π΄Π°Π²Π»Π΅Π½ΠΈΡ ΠΏΡΠΈ ΠΏΠ½Π΅Π²ΠΌΠΎΡΠ΅Π³ΡΠ»ΠΈΡΠΎΠ²ΠΊΠ΅, Π½Π΅Π²ΠΎΠ·ΠΌΠΎΠΆΠ½ΠΎ Π½ΠΈΠΊΠ΅Π»ΠΈΡΠΎΠ²Π°ΡΡ ΡΠ»Π΅ΠΊΡΡΠΎΠ»ΠΈΡΠΈΡΠ΅ΡΠΊΠΈ ΠΈΠ·-Π·Π° ΡΠ»ΠΎΠΆΠ½ΠΎΠΉ Π³Π΅ΠΎΠΌΠ΅ΡΡΠΈΡΠ΅ΡΠΊΠΎΠΉ ΡΠΎΡΠΌΡ. Π₯ΠΈΠΌΠΈΡΠ΅ΡΠΊΠΎΠ΅ Π½ΠΈΠΊΠ΅Π»ΠΈΡΠΎΠ²Π°Π½ΠΈΠ΅ ΡΠ²Π»ΡΠ΅ΡΡΡ ΠΏΡΠ΅ΠΊΡΠ°ΡΠ½ΡΠΌ ΡΠ΅ΡΠ΅Π½ΠΈΠ΅ΠΌ ΡΡΠΎΠΉ ΠΏΡΠΎΠ±Π»Π΅ΠΌΡ. Π‘ΡΠ°Π»ΡΠ½ΡΠ΅ ΠΈΠ·Π΄Π΅Π»ΠΈΡ ΠΌΠΎΠΆΠ½ΠΎ Π½ΠΈΠΊΠ΅Π»ΠΈΡΠΎΠ²Π°ΡΡ Ρ ΠΈΠΌΠΈΡΠ΅ΡΠΊΠΈ Π±Π΅Π· Π·Π°ΡΡΡΠ΄Π½Π΅Π½ΠΈΠΉ. ΠΠ° ΠΌΠ΅Π΄ΠΈ ΠΈ Π»Π°ΡΡΠ½ΠΈ ΠΎΡΠ°ΠΆΠ΄Π΅Π½ΠΈΠ΅ Π½ΠΈΠΊΠ΅Π»Ρ Π½Π°ΡΠΈΠ½Π°Π΅ΡΡΡ ΠΏΠΎΡΠ»Π΅ ΠΊΡΠ°ΡΠΊΠΎΠ²ΡΠ΅ΠΌΠ΅Π½Π½ΠΎΠ³ΠΎ ΠΊΠΎΠ½ΡΠ°ΠΊΡΠ° Ρ ΠΌΠ΅Π½Π΅Π΅ Π±Π»Π°Π³ΠΎΡΠΎΠ΄Π½ΡΠΌ ΠΌΠ΅ΡΠ°Π»Π»ΠΎΠΌ, Π½Π°ΠΏΡΠΈΠΌΠ΅Ρ, ΠΆΠ΅Π»Π΅Π·ΠΎΠΌ ΠΈΠ»ΠΈ Π°Π»ΡΠΌΠΈΠ½ΠΈΠ΅ΠΌ. ΠΠ»Ρ Π½ΠΈΠΊΠ΅Π»ΠΈΡΠΎΠ²Π°Π½ΠΈΡ Π°Π»ΡΠΌΠΈΠ½ΠΈΠ΅Π²ΡΡ ΡΠΏΠ»Π°Π²ΠΎΠ² ΠΎΠ±ΡΡΠ½ΠΎ ΠΏΡΠΈΠΌΠ΅Π½ΡΡΡ ΡΠ΅Π»ΠΎΡΠ½ΡΠ΅ Π²Π°Π½Π½Ρ (Π½Π°ΠΏΡΠΈΠΌΠ΅Ρ Π²Π°Π½Π½Ρ 2).ΠΠ° ΡΡΠ΅Π½ΠΊΠ°Ρ ΠΈ Π΄Π½Π΅ ΡΠΎΡΡΠ΄Π°, ΠΏΡΠΈΠΌΠ΅Π½ΡΠ΅ΠΌΠΎΠ³ΠΎ Π΄Π»Ρ Ρ ΠΈΠΌΠΈΡΠ΅ΡΠΊΠΎΠ³ΠΎ Π½ΠΈΠΊΠ΅Π»ΠΈΡΠΎΠ²Π°Π½ΠΈΡ, ΠΌΠΎΠ³ΡΡ ΠΎΡΠ΅Π΄Π°ΡΡ ΠΌΠ΅Π»ΠΊΠΈΠ΅ ΡΠ°ΡΡΠΈΡΠΊΠΈ Π½ΠΈΠΊΠ΅Π»Ρ, Π² ΠΎΡΠΎΠ±Π΅Π½Π½ΠΎΡΡΠΈ, Π΅ΡΠ»ΠΈ ΠΏΠΎΠ²Π΅ΡΡ Π½ΠΎΡΡΡ ΡΠΎΡΡΠ΄Π° Π½Π΅ ΠΎΡΠ΅Π½Ρ Π³Π»Π°Π΄ΠΊΠ°, ΠΈΠΌΠ΅Π΅Ρ ΡΠ°ΡΠ°ΠΏΠΈΠ½Ρ. ΠΠ΅ΡΠ΅Π΄ Π΄Π°Π»ΡΠ½Π΅ΠΉΡΠΈΠΌ ΠΈΡΠΏΠΎΠ»ΡΠ·ΠΎΠ²Π°Π½ΠΈΠ΅ΠΌ ΡΠ°ΠΊΠΎΠ³ΠΎ ΡΠΎΡΡΠ΄Π° Π½Π΅ΠΎΠ±Ρ ΠΎΠ΄ΠΈΠΌΠΎ ΡΡΡΡΠ°Π½ΠΈΡΡ ΠΎΡΠ΅Π²ΡΠΈΠ΅ ΡΠ°ΡΡΠΈΡΠΊΠΈ Π½ΠΈΠΊΠ΅Π»Ρ, ΡΠ°ΡΡΠ²ΠΎΡΡΡ ΠΈΡ Π² Π°Π·ΠΎΡΠ½ΠΎΠΉ ΠΊΠΈΡΠ»ΠΎΡΠ΅.
echemistry.ru
Π₯ΠΈΠΌΠΈΡΠ΅ΡΠΊΠΎΠ΅ ΠΎΡΠ°ΠΆΠ΄Π΅Π½ΠΈΠ΅ Π½ΠΈΠΊΠ΅Π»Ρ. Π’Π΅Ρ Π½ΠΎΠ»ΠΎΠ³ΠΈΡ Π½ΠΈΠΊΠ΅Π»ΠΈΡΠΎΠ²Π°Π½ΠΈΡ Π² Π΄ΠΎΠΌΠ°ΡΠ½ΠΈΡ ΡΡΠ»ΠΎΠ²ΠΈΡΡ .
Π‘ ΡΠ΅Π½Π°ΠΌΠΈ Π½Π° ΡΠ°Π±ΠΎΡΡ ΠΏΠΎ Π½ΠΈΠΊΠ΅Π»ΠΈΡΠΎΠ²Π°Π½ΠΈΡ, ΠΡ ΠΌΠΎΠΆΠ΅ΡΠ΅ ΠΎΠ·Π½Π°ΠΊΠΎΠΌΠΈΡΡΡΡ Π² .
ΠΠ°Π½Π΅ΡΠ΅Π½ΠΈΠ΅ Π½ΠΈΠΊΠ΅Π»Ρ, ΡΠ°ΠΊΠΆΠ΅ ΠΊΠ°ΠΊ ΠΈ ΠΌΠ΅Π΄ΠΈ, ΡΠ²Π»ΡΠ΅ΡΡΡ ΠΎΠ΄Π½ΠΈΠΌ ΠΈΠ· ΠΎΠ±ΡΠ·Π°ΡΠ΅Π»ΡΠ½ΡΡ
ΠΏΡΠΎΡΠ΅Π΄ΡΡ ΠΏΡΠΈ ΠΏΠΎΠ΄Π³ΠΎΡΠΎΠ²ΠΊΠ΅ ΠΈΠ·Π΄Π΅Π»ΠΈΡ ΠΏΠΎΠ΄ ΡΠ΅Π»Π΅Π²ΠΎΠ΅ ΡΠΈΠ½ΠΈΡΠ½ΠΎΠ΅ ΠΏΠΎΠΊΡΡΡΠΈΠ΅. ΠΠ»Π΅ΠΊΡΡΠΎΠ»ΠΈΡΠΎΠ² Π΄Π»Ρ Π½Π°Π½Π΅ΡΠ΅Π½ΠΈΡ Π½ΠΈΠΊΠ΅Π»Ρ ΡΡΡΠ΅ΡΡΠ²ΡΠ΅Ρ ΠΌΠ½ΠΎΠΆΠ΅ΡΡΠ²ΠΎ. ΠΠ½ ΡΠ°Π·Π½ΡΡΡΡ ΠΏΠΎ ΡΠΏΠΎΡΠΎΠ±Π°ΠΌ ΠΏΡΠΈΠΌΠ΅Π½Π΅Π½ΠΈΡ, ΡΠ΅ΠΆΠΈΠΌΠ°ΠΌ, ΠΊΠ°ΡΠ΅ΡΡΠ²Ρ ΠΏΠΎΠΊΡΡΡΠΈΡ ΠΈ ΡΠΎΡΡΠ°Π²Π°ΠΌ. ΠΡΠ»ΠΈ ΠΡ ΡΠ΅ΡΠΈΠ»ΠΈ Π·Π°Π½ΠΈΠΌΠ°ΡΡΡΡ Π³Π°Π»ΡΠ²Π°Π½ΠΈΠΊΠΎΠΉ, Π±Π΅Π· Π½ΠΈΠΊΠ΅Π»ΠΈΡΠΎΠ²Π°Π½ΠΈΡ ΠΠ°ΠΌ Π½Π΅ ΠΎΠ±ΠΎΠΉΡΠΈΡΡ.
Π‘Π°ΠΌ ΠΏΠΎ ΡΠ΅Π±Π΅ Π½ΠΈΠΊΠ΅Π»Ρ Π½Π΅ ΡΠ°ΡΡΠΎ ΡΠ²Π»ΡΠ΅ΡΡΡ ΡΠ΅Π»Π΅Π²ΡΠΌ ΠΏΠΎΠΊΡΡΡΠΈΠ΅ΠΌ. Π ΠΊΠ°ΡΠ΅ΡΡΠ²Π΅ Π°Π½ΡΠΈΠΊΠΎΡΡΠΎΠ·ΠΈΠΎΠ½Π½ΠΎΠ³ΠΎ ΠΏΠΎΠΊΡΡΡΠΈΡ ΠΎΠ½ Π½Π΅ ΡΠ²Π»ΡΠ΅ΡΡΡ Π»ΡΡΡΠΈΠΌ ΠΊΠ°Π½Π΄ΠΈΠ΄Π°ΡΠΎΠΌ, Π² ΡΡΠΎ ΡΠ»ΡΡΠ°Π΅ Π±ΠΎΠ»ΡΡΠ΅ ΠΏΠΎΠ΄ΠΎΠΉΠ΄ΡΡ ΡΠΈΠ½ΠΊ ΠΈ Ρ
ΡΠΎΠΌ, Π²Π²ΠΈΠ΄Ρ ΠΈΡ
Ρ
ΠΈΠΌΠΈΡΠ΅ΡΠΊΠΈΡ
ΡΠ²ΠΎΠΉΡΡΠ² ΠΈ ΡΠΏΠΎΡΠΎΠ±Π½ΠΎΡΡΠΈ Β«ΠΎΡΡΡΠ³ΠΈΠ²Π°ΡΡΒ» ΠΎΠΊΠΈΡΠ»Π΅Π½ΠΈΠ΅ ΠΆΠ΅Π»Π΅Π·Π°, ΡΠΊΠ»ΠΎΠ½Π½ΠΎΠ³ΠΎ ΠΊ ΡΠΆΠ°Π²ΡΠΈΠ½Π΅, Π½Π° ΡΠ΅Π±Ρ. ΠΠ°ΠΊ Π΄Π΅ΠΊΠΎΡΠ°ΡΠΈΠ²Π½ΠΎΠ΅ ΠΏΠΎΠΊΡΡΡΠΈΠ΅ Π½ΠΈΠΊΠ΅Π»ΠΈΡΠΎΠ²Π°Π½ΠΈΠ΅ ΠΈΡΠΏΠΎΠ»ΡΠ·ΡΠ΅ΡΡΡ ΡΠ°ΡΠ΅, Π½ΠΎ Π² Π²Π²ΠΈΠ΄Ρ Π΅Π³ΠΎ Ρ
ΠΈΠΌΠΈΡΠ΅ΡΠΊΠΎΠΉ Π½Π΅ΡΡΠΎΠΉΠΊΠΎΡΡΠΈ, ΠΏΡΠΈ Π½Π΅ΠΎΠ±Ρ
ΠΎΠ΄ΠΈΠΌΠΎΡΡΠΈ Π½Π°Π½ΠΎΡΠΈΡΡ ΡΠ²Π΅Ρ Β«Π±Π΅Π»ΠΎΠ³ΠΎΒ» ΠΌΠ΅ΡΠ°Π»Π»Π°, ΡΠ°ΡΠ΅ Π²ΡΠ±ΠΈΡΠ°ΡΡ ΠΏΠΎΠΊΡΡΡΠΈΠ΅ ΠΏΠ°Π»Π»Π°Π΄ΠΈΠ΅ΠΌ ΠΈΠ»ΠΈ ΡΠΎΠ΄ΠΈΠ΅ΠΌ.
ΠΠ° Π½Π°ΡΠ΅ΠΌ ΠΏΡΠ΅Π΄ΠΏΡΠΈΡΡΠΈΠΈ ΠΈΡΠΏΠΎΠ»ΡΠ·ΡΡΡΡΡ Π³Π°Π»ΡΠ²Π°Π½ΠΈΡΠ΅ΡΠΊΠΈΠΉ Π½ΠΈΠΊΠ΅Π»Ρ ΠΈ Ρ
ΠΈΠΌΠΈΡΠ΅ΡΠΊΠΈΠΉ (ΠΈΠΌΠΌΠ΅ΡΡΠΈΠΎΠ½Π½ΡΠΉ) Π½ΠΈΠΊΠ΅Π»Ρ.
ΠΠ°ΠΈΠ±ΠΎΠ»Π΅Π΅ ΠΏΡΠΎΡΡΠΎΠΉ ΡΠ°ΡΡΠ²ΠΎΡ Π΄Π»Ρ Π½ΠΈΠΊΠ΅Π»ΠΈΡΠΎΠ²Π°Π½ΠΈΡ β
Π Π°ΡΡΠ²ΠΎΡ ΠΊΠΈΡΠ»ΠΎΠ³ΠΎ (ΠΏΠΎΠ΄ΡΠ»ΠΎΠΉΠ½ΠΎΠ³ΠΎ) Π½ΠΈΠΊΠ΅Π»ΠΈΡΠΎΠ²Π°Π½ΠΈΡ.
ΠΠ»Π΅ΠΊΡΡΠΎΠ»ΠΈΡ ΠΊΠΈΡΠ»ΠΎΠ³ΠΎ Π½ΠΈΠΊΠ΅Π»ΠΈΡΠΎΠ²Π°Π½ΠΈΡ ΠΏΡΠΈΠΌΠ΅Π½ΡΠ΅ΡΡΡ Π² ΠΊΠ°ΡΠ΅ΡΡΠ²Π΅ ΠΏΠ΅ΡΠ²ΠΎΠ³ΠΎ ΠΌΠ΅ΡΠ°Π»Π»ΠΈΡΠ΅ΡΠΊΠΎΠ³ΠΎ ΠΏΠΎΠΊΡΡΡΠΈΡ ΠΏΠΎΡΠ»Π΅ ΠΎΡΠΈΡΡΠΊΠΈ ΠΈ ΠΏΠΎΠ»ΠΈΡΠΎΠ²ΠΊΠΈ ΠΈΠ·Π΄Π΅Π»ΠΈΡ. ΠΠ³ΠΎ ΠΌΠΎΠΆΠ½ΠΎ ΡΡΠΈΡΠ°ΡΡ Β«ΠΊΠ»Π΅Π΅ΠΌΒ» ΠΈΠ»ΠΈ ΠΎΡΠ½ΠΎΠ²ΠΎΠΉ, Π½Π° ΠΊΠΎΡΠΎΡΡΡ ΠΏΠΎΡΠΎΠΌ ΠΏΠΎΠ»ΠΎΠΆΠΈΠΌ Π²ΡΠ΅ ΠΎΡΡΠ°Π»ΡΠ½ΡΠ΅ ΠΌΠ΅ΡΠ°Π»Π»Ρ. Π’ΠΎΠ»ΡΠΈΠ½Π° ΠΏΠΎΠΊΡΡΡΠΈΡ ΠΈΠ· ΡΠ°ΠΊΠΎΠ³ΠΎ ΡΠ°ΡΡΠ²ΠΎΡΠ° Π½Π΅ ΠΏΡΠ΅Π²ΡΡΠ°Π΅Ρ 1 ΠΌΠΊΠΌ, Π° ΡΠΊΠΎΡΠΎΡΡΡ ΠΎΡΠ°ΠΆΠ΄Π΅Π½ΠΈΡ 1-2 ΠΌΠΊΠΌ/ΠΌΠΈΠ½. ΠΠ»ΠΈΡΠ΅Π»ΡΠ½ΠΎΡΡΡ Π²ΡΠ΄Π΅ΡΠΆΠΊΠΈ Π² Π²Π°Π½Π½Π΅ ΠΊΠΈΡΠ»ΠΎΠ³ΠΎ Π½ΠΈΠΊΠ΅Π»ΠΈΡΠΎΠ²Π°Π½ΠΈΡ Π½Π΅ Π±ΠΎΠ»ΡΡΠ΅ 1 ΠΌΠΈΠ½ΡΡΡ. ΠΡΠΎ ΡΠ²ΡΠ·Π°Π½ΠΎ Ρ ΡΠ΅ΠΌ, ΡΡΠΎ ΠΊΠΈΡΠ»ΡΠΉ Π½ΠΈΠΊΠ΅Π»Ρ Π΄Π°Π΅Ρ Ρ ΡΡΠΏΠΊΠΈΠ΅ ΠΈ ΡΠ΅ΠΌΠ½ΡΠ΅ ΠΎΡΠ°Π΄ΠΊΠΈ Π½Π° Π±ΠΎΠ»ΡΡΠΈΡ ΡΠΎΠ»ΡΠΈΠ½Π°Ρ . ΠΠΎ, ΡΠ΅ΠΌ Π½Π΅ ΠΌΠ΅Π½Π΅Π΅, ΠΏΠΎΠ»ΠΎΠΆΠΈΡΡ ΡΠΎΠ½ΠΊΠΈΠΉ ΡΠ»ΠΎΠΉ ΠΊΠΈΡΠ»ΠΎΠ³ΠΎ Π½ΠΈΠΊΠ΅Π»Ρ Π½Π΅ΠΎΠ±Ρ ΠΎΠ΄ΠΈΠΌΠΎ. ΠΠ΅ΠΊΠΎΡΠΎΡΡΠ΅ ΠΊΠΎΠΌΠΏΠΎΠ½Π΅Π½ΡΡ Π΅Π³ΠΎ ΡΠΎΡΡΠ°Π²Π° ΠΎΠ±Π΅ΡΠΏΠ΅ΡΠΈΠ²Π°Π΅Ρ ΠΌΠΈΠΊΡΠΎΡΠ°Π·ΡΡΡΠ΅Π½ΠΈΡ ΠΏΠΎΠ²Π΅ΡΡ Π½ΠΎΡΡΠΈ Π΄Π»Ρ ΠΊΠ°ΡΠ΅ΡΡΠ²Π΅Π½Π½ΠΎΠΉ Π°Π΄Π³Π΅Π·ΠΈΠΈ ΠΏΠΎΠΊΡΡΡΠΈΡ, Π²ΠΌΠ΅ΡΡΠ΅ Ρ ΡΠ΅ΠΌ, Π½Π°Π½ΠΎΡΡ ΡΠΎΠ½ΠΊΠΈΠΉ ΡΠ»ΠΎΠΉ ΡΠ²Π΅ΠΆΠ΅Π³ΠΎ Π½ΠΈΠΊΠ΅Π»Ρ, ΠΌΡ ΠΎΠ±Π΅ΡΠΏΠ΅ΡΠΈΠ²Π°Π΅ΠΌ Ρ ΠΎΡΠΎΡΠ΅Π΅ ΠΊΠ°ΡΠ΅ΡΡΠ²ΠΎ Π°Π΄Π³Π΅Π·ΠΈΠΈ Π΄Π»Ρ ΡΠ»Π΅Π΄ΡΡΡΠ΅Π³ΠΎ ΠΏΠΎΠΊΡΡΡΠΈΡ ΠΌΠ΅Π΄ΡΡ ΠΈΠ»ΠΈ Π±Π»Π΅ΡΡΡΡΠΈΠΌ Π½ΠΈΠΊΠ΅Π»Π΅ΠΌ. ΠΠ»Π΅ΠΊΡΡΠΎΠ»ΠΈΡ ΠΊΠΈΡΠ»ΠΎΠ³ΠΎ Π½ΠΈΠΊΠ΅Π»ΠΈΡΠΎΠ²Π°Π½ΠΈΡ ΠΎΡΠ΅Π½Ρ ΡΡΠ°Π±ΠΈΠ»Π΅Π½ Π²ΠΎ Π²ΡΠ΅ΠΌΠ΅Π½ΠΈ ΠΈ ΡΡΠΎΠ΅ΠΊ ΠΊ Π·Π°Π³ΡΡΠ·Π½Π΅Π½ΠΈΡΠΌ.
ΠΠ»Π΅ΠΊΡΡΠΎΠ»ΠΈΡ Π±Π»Π΅ΡΡΡΡΠ΅Π³ΠΎ Π½ΠΈΠΊΠ΅Π»ΠΈΡΠΎΠ²Π°Π½ΠΈΡ.
ΠΠ»Π΅ΠΊΡΡΠΎΠ»ΠΈΡ Π±Π»Π΅ΡΡΡΡΠ΅Π³ΠΎ Π½ΠΈΠΊΠ΅Π»ΠΈΡΠΎΠ²Π°Π½ΠΈΡ ΠΏΡΠΈΠΌΠ΅Π½ΡΡΡ Π΄Π»Ρ ΠΌΠΈΠΊΡΠΎΠ²ΡΡΠ°Π²Π½ΠΈΠ²Π°Π½ΠΈΡ ΠΏΠΎΠ²Π΅ΡΡ
Π½ΠΎΡΡΠΈ ΠΈΠ·Π΄Π΅Π»ΠΈΡ. ΠΠΎ ΡΡΠ°Π²Π½Π΅Π½ΠΈΡ Ρ Π±Π»Π΅ΡΡΡΡΠ΅ΠΉ ΠΌΠ΅Π΄ΡΡ, ΠΎΠ½ Π΄Π°Π΅Ρ ΠΌΠ΅Π½Π΅Π΅ Π·Π΅ΡΠΊΠ°Π»ΡΠ½ΡΠ΅ ΠΎΡΠ°Π΄ΠΊΠΈ. Π‘ΠΊΠΎΡΠΎΡΡΡ Π½Π°ΡΠ°ΡΡΠ°Π½ΠΈΡ ΡΠΎΠ»ΡΠΈΠ½Ρ ΠΈ ΡΠ°Π±ΠΎΡΠ°Ρ ΠΏΠ»ΠΎΡΠ½ΠΎΡΡΡ ΡΠΎΠΊΠ° ΡΠ°ΠΊΠΆΠ΅ Π·Π½Π°ΡΠΈΡΠ΅Π»ΡΠ½ΠΎ Π½ΠΈΠΆΠ΅, Π½ΠΎ ΡΡΠΎΡ ΡΠ»Π΅ΠΊΡΡΠΎΠ»ΠΈΡ Π½Π΅ΠΎΠ±Ρ
ΠΎΠ΄ΠΈΠΌ Π΄Π»Ρ ΡΠΈΠ½ΠΈΡΠ½ΠΎΠΉ ΠΎΠ±ΡΠ°Π±ΠΎΡΠΊΠΈ ΠΈΠ·Π΄Π΅Π»ΠΈΠΉ. ΠΠ³ΠΎ ΠΎΠ±ΡΠ·Π°ΡΠ΅Π»ΡΠ½ΠΎ ΠΈΡΠΏΠΎΠ»ΡΠ·ΡΡΡ Π΄Π»Ρ ΠΏΠΎΠ»ΡΡΠ΅Π½ΠΈΡ ΡΠΈΠ½ΠΈΡΠ½ΡΡ
ΠΎΡΠ°Π΄ΠΊΠΎΠ² ΡΠΎΠ»ΡΠΈΠ½ΠΎΠΉ Π΄ΠΎ 15 ΠΌΠΊΠΌ. ΠΠ»ΠΈ, ΠΏΡΠΈ ΡΠΎΠ»ΡΠΈΠ½Π΅ ΠΏΠΎΠΊΡΡΡΠΈΡ 3-6 ΠΌΠΊΠΌ ΠΊΠ°ΠΊ ΠΊΠ°ΡΠ΅ΡΡΠ²Π΅Π½Π½ΡΡ ΠΏΠΎΠ΄Π»ΠΎΠΆΠΊΡ ΠΏΠΎΠ΄ Π³Π°Π»ΡΠ²Π°Π½ΠΈΡΠ΅ΡΠΊΠΎΠ΅ ΠΈΠ»ΠΈ ΠΈΠΌΠΌΠ΅ΡΡΠΈΠΎΠ½Π½ΠΎΠ΅ Π·ΠΎΠ»ΠΎΡΠΎ.
ΠΡΠ΅Π½Ρ Ρ
ΠΎΡΠΎΡΠΈΠ΅ ΡΠ΅Π·ΡΠ»ΡΡΠ°ΡΡ ΡΡΠΎΡ ΡΠ°ΡΡΠ²ΠΎΡ Π΄Π΅ΠΌΠΎΠ½ΡΡΡΠΈΡΡΠ΅Ρ Π² Π±Π°ΡΠ°Π±Π°Π½Π½ΡΡ
ΠΈ ΠΊΠΎΠ»ΠΎΠΊΠΎΠ»ΡΠ½ΡΡ
Π²Π°Π½Π½Π°Ρ
.
ΠΠ»Π΅ΠΊΡΡΠΎΠ»ΠΈΡ Ρ ΠΈΠΌΠΈΡΠ΅ΡΠΊΠΎΠ³ΠΎ (ΠΈΠΌΠΌΠ΅ΡΡΠΈΠΎΠ½Π½ΠΎΠ³ΠΎ) Π½ΠΈΠΊΠ΅Π»ΠΈΡΠΎΠ²Π°Π½ΠΈΡ.
Π₯ΠΈΠΌΠΈΡΠ΅ΡΠΊΠΎΠ΅ Π½ΠΈΠΊΠ΅Π»ΠΈΡΠΎΠ²Π°Π½ΠΈΠ΅ ΠΏΡΠΈΠΌΠ΅Π½ΡΠ΅ΡΡΡ ΠΏΡΠΈ ΠΎΠ±ΡΠ°Π±ΠΎΡΠΊΠ΅ ΡΠ»ΠΎΠΆΠ½ΠΎΠΏΡΠΎΡΠΈΠ»ΡΠ½ΡΡ ΠΈΠ·Π΄Π΅Π»ΠΈΠΉ. Π Π°Π±ΠΎΡΠ°Π΅Ρ Π±Π΅Π· ΠΏΡΠΈΠ»ΠΎΠΆΠ΅Π½ΠΈΡ Π²Π½Π΅ΡΠ½Π΅Π³ΠΎ ΡΠΎΠΊΠ°. Π Π°Π²Π½ΠΎΠΌΠ΅ΡΠ½ΠΎΠ΅ Π½Π°ΡΠ°ΡΠΈΠ²Π°Π½ΠΈΠ΅ Π½Π΅Π½Π°ΠΏΡΡΠΆΠ΅Π½Π½ΠΎΠ³ΠΎ Π½ΠΈΠΊΠ΅Π»Ρ Π²ΠΎ Π²ΡΠ΅Ρ ΡΠΎΡΠΊΠ°Ρ ΠΏΠΎΠ²Π΅ΡΡ Π½ΠΎΡΡΠΈ ΠΈΠ·Π΄Π΅Π»ΠΈΡ, ΠΎΠ±Π΅ΡΠΏΠ΅ΡΠΈΠ²Π°Π΅Ρ ΡΠ²Π΅ΡΠ΄ΠΎΠ΅, ΠΏΠΎΠ»ΡΠ±Π»Π΅ΡΡΡΡΠ΅Π΅ ΠΏΠΎΠΊΡΡΡΠΈΠ΅. Π§Π°ΡΡΠΎ ΡΡΠΎΡ ΡΠ°ΡΡΠ²ΠΎΡ ΠΏΡΠΈΠΌΠ΅Π½ΡΡΡ Π΄Π»Ρ Π·Π°ΡΠΈΡΡ ΠΎΡ ΠΊΠΎΡΡΠΎΠ·ΠΈΠΈ ΠΏΡΡΠ΅ΠΌ Π½Π°ΡΠ°ΡΠΈΠ²Π°Π½ΠΈΡ Π½ΠΈΠΊΠ΅Π»Ρ Π² ΡΠΎΠ»ΡΠΈΠ½Ρ 6-30 ΠΌΠΊΠΌ. ΠΡΠΈΠΌΠ΅Π½Π΅Π½ΠΈΠ΅ Ρ ΠΈΠΌΠΈΡΠ΅ΡΠΊΠΎΠ³ΠΎ Π½ΠΈΠΊΠ΅Π»ΠΈΡΠΎΠ²Π°Π½ΠΈΡ ΠΎΠ³ΡΠ°Π½ΠΈΡΠΈΠ²Π°Π΅ΡΡΡ ΠΈΡΡ ΠΎΠ΄Π½ΡΠΌ ΠΌΠ°ΡΠ΅ΡΠΈΠ°Π»ΠΎΠΌ Π΄Π΅ΡΠ°Π»ΠΈ. Π₯ΠΈΠΌΠΈΡΠ΅ΡΠΊΠΎΠ΅ Π½ΠΈΠΊΠ΅Π»ΠΈΡΠΎΠ²Π°Π½ΠΈΠ΅ β ΡΠ°ΡΡΠ²ΠΎΡ Π³ΠΎΡΡΡΠΈΠΉ, ΡΡΠΎ Π½Π΅ Π²ΡΠ΅Π³Π΄Π° ΠΏΠΎΠ·Π²ΠΎΠ»ΡΠ΅Ρ ΠΈΡΠΏΠΎΠ»ΡΠ·ΠΎΠ²Π°ΡΡ Π΅Π³ΠΎ Π΄Π»Ρ ΠΏΠ»Π°ΡΡΠΈΠΊΠΎΠ². Π’Π°ΠΊΠΆΠ΅, Π² ΠΏΡΠΎΡΠ΅ΡΡΠ΅ ΡΠ°Π±ΠΎΡΡ,
cityshin.ru