Антикоррозийные материалы
Металлические конструкции, которые применяются в машиностроении и строительстве необходимо надежно защищать от различных воздействий окружающей среды и от коррозии. Антикоррозийное покрытие защищает металл от физико-химической реакции, которая происходит в результате воздействия окружающей среды на материал, от которого основные свойства металла изменяются. Именно такие воздействия приводят к коррозии металла.
Наиболее доступным способом, который способен защитить металл от коррозии является применения специализированных эмалей и красок. Лакокрасочные покрытия с антикоррозийными свойствами отличаются своими значительными преимуществами:
- высокие защитные свойства от коррозии;
- существенная простота нанесения;
- возможность обрабатывать металлические конструкции самых различных габаритов;
- антикоррозийное покрытие такого типа отличается своей дешевизной в отличие от других видов покрытий.
При выборе антикоррозийного покрытия для защиты металла необходимо учитывать толщину покрытия, количество всех наносимых слоев, среду, в которой будет эксплуатироваться металлическая конструкция.
Самые эффективные антикоррозийные материалы, обладающие отличными эксплуатационными свойствами, производятся на акриловой основе и содержат в своем составе цинк. При нанесении такого покрытия на металлическую поверхность образовывается специальная защитная пленка с высоким содержанием цинка, которая обеспечивает весьма эффективную и надежную защиту металла от коррозии. Такое покрытие отличается длительным сроком службы, который составляет 10-15 лет. Новые антикоррозионные материалы обладают значительной устойчивостью, которая позволяет сохранять гомогенные свойства металла. Физико-химические свойства и состав новых защитных материалов способен обеспечивать им отличное сцепление с металлом конструкции, которая требует антикоррозийной защиты.
Антикоррозийное покрытие нового поколения обладает отличными механическими и эксплуатационными свойствами. Во-первых, они отличаются высокой стойкостью к различному химическому воздействию и водостойкостью. Во-вторых, они эластичны, что позволяет им хорошо держаться на поверхности металла даже при незначительных изгибах. Помимо этого такие покрытия отличаются своими основными техническими свойствами при температурах от -50 до +150.
Основные преимущества использования новых антикоррозийных материалов заключается в их простоте использования, не требующей дополнительных трудоемких сложных операций по термической подготовке металла. Новое антикоррозийное покрытие, содержащее цинк служит эффективной защитой для самых различных металлоконструкций.
Антикоррозийные свойства цинковых покрытий, химические реакции, защита от коррозии с помощью оцинкования
Коррозия стали и антикоррозийные свойства цинковых покрытий
Коррозией называют самопроизвольное разрушение металлических материалов вследствие физико-химического взаимодействия их с окружающей средой. Коррозионный процесс протекает на границе двух фаз, т. е. является гетерогенным процессом взаимодействия жидкой или газообразной среды с металлом.
Ниже будет рассмотрена коррозия электрохимического типа в условиях естественной атмосферы воздуха. В этих условиях на металлах в большинстве случаев образуются электролиты, т. с. проводящие электрический ток жидкие среды.
У границы раздела двух взаимодействующих фаз — металла и электролита (воды, водного раствора солей, кислот и др.) возникает разность электрических потенциалов. Электродвижущую силу элемента, составленного из исследуемого электрода (например, металла в электролите) в сопоставлении с э. д. с. электрода, потенциал которого условно принят за 0 (стандартный водородный потенциал), называют электродным потенциалом металла. Так, обратимый электродный потенциал железа V(Fe) = -0,440 В, а цинка V(Zn) = -0,761 В.
Электрохимическое растворение металла — сложный процесс, состоящий из трех основных частей:
a) анодного процесса — образования гидратированных ионов корродирующего металла Me в электролите и некомпенсированных электронов е на анодных А участках по реакции
б) катодного процесса — ассимиляции электронов какими-либо ионами или молекулами электролита (D-деполяризаторами), способными к восстановлению на катодных участках по реакции
D + пе= [D . ne]
в) процесса протекания электронов по металлу от анодных участков к катодным в соответствующего перемещения анионов (А(-)) и катионов (K(+)) в растворе.
По границе раздела двух фаз, на которой возникает разность электрических потенциалов, наблюдается локализация анодных и катодных участков. Основными причинами возникновения электрохимической неоднородности поверхности раздела металл—электролит являются наличие разнородных атомов в твердом растворе металла, выход дислокаций на поверхность его, микровключения, макро- и микропоры в окисной пленке на поверхности металла, неравномерное распределение на его поверхности вторичных продуктов коррозии, неоднородность электролита и др.
Механические воздействия часто приводят к сдвигу электродного потенциала в сторону отрицательных значений и в связи с этим к усилению коррозии металла. Сдвиг потенциала может быть вызван как процессом деформации, так и деформированным состоянием металла.
Степень неоднородности (гетерогенности) этой поверхности характеризуется разностью электродных потенциалов анодных (с более отрицательным потенциалом V(A)) и катодных (с более положительным электродным потенциалом V(K)) участков
Вторая особенность электрохимического коррозионного процесса — реализация материального эффекта на анодных участках поверхности корродирующего металла.
Таким образом, электрохимическая коррозия металлов представляет собой результат работы большого числа коррозионных гальванических элементов на корродирующей поверхности металла, соприкасающейся с электролитом. Это приводит к неравномерному или местному коррозионному разрушению.
Наиболее распространенные виды электрохимической коррозии — мокрая и влажная атмосферная коррозия. Коррозия первого типа протекает при наличии на поверхности металла видимой пленки влаги; коррозия второго типа — в случае тончайшей, невидимой пленки влаги, которая образуется в результате капиллярной, адсорбционной или химической ее конденсации.
На скорость атмосферной коррозии металлов оказывает влияние ряд факторов. Влажность воздуха — один из главных. По достижении некоторой влажности воздуха скорость коррозии резко увеличивается. Так, критическая влажность для чистой поверхности железа в чистом воздухе составляет 100%, а для поверхности, слегка предварительно прокорродировавшей в воде,— 65%.
Очень сильно влияют на скорость атмосферной коррозии металла примеси, находящиеся в воздухе: газы (SO2, h3S и др.), твердые частицы солей, угля, песка.
Скорость атмосферной коррозии увеличивается с увеличением продолжительности пребывания влажной пленки на поверхности металла и уменьшается с повышением температуры окружающего воздуха.
Для защиты поверхности тонких стальных полос от коррозии применяют металлические покрытия. Их можно разделить на два вида: катодные и анодные. Для катодных покрытий используют металлы с более положительным потенциалом, чем сталь (например, Cu, Ni, Cr). В этом случае в местах обнажения основного металла создается такое направление гидратированных ионов, при котором усиливается его коррозия (рис. 3,а). Следовательно, необходимо, чтобы в катодных покрытиях было минимальное количество пор и чтобы эти поры, если они все-таки имеются, обладали возможно меньшими размерами. Это затрудняло бы проникновение воды к основному металлу.
В случае анодных покрытий (к ним, в частности, относятся цинковые) происходит электрохимическая защита стали. Процесс развивается следующим образом.
Анодная реакция ионизации цинка
Zn + mН2О = Zn(3+) x mh4O + 2е
и катодная реакция ассимиляции электронов
О2 + 4е + 2Н2О = 4ОН(-)
являются первичными процессами электрохимической коррозии, а их продукты (Zn(2+) x mh3O и ОН(-)) — первичными продуктами коррозии. Эти продукты коррозии при определенных значениях среды (например, в водном растворе NaCl) образуют трудно растворимый гидрат окисла
Zn(2+) x тН2О + 2ОН(-) = тh3О + Zn(ОН)2 (осадок)
— вторичный продукт коррозии.
Пленка вторичных трудно растворимых продуктов коррозии перекрывает оголенный от покрытия участок (в результате — царапин, образование сквозного отверстия, после пайки и др.), защищая поверхность стали.
Для определения степени протекторной защиты на стальной пруток, покрытый цинком, и без него навивали стальную проволоку без покрытия. Продолжительность испытания составляла 1 месяц. Условия — крыша городского дома (лето А и зима Б) и железнодорожный тоннель (лето В):
Испытания позволили установить, что защитный эффект цинка обнаруживается на расстоянии нескольких миллиметров; в холодное время года этот эффект проявляется слабее, чем в теплое время.
Аналогичный результат получен и при более продолжительных испытаниях тем же методом. Установлено, в частности, что потери массы стальной не защищенной проволоки диаметром 0,5 мм, навитой на оцинкованный цилиндр, составили за 6 месяцев 8-11 мг, а навитой на неоцинкованный цилиндр (в обоих случаях диаметром 18 мм) достигли за тот же период 351—378 мг. Расчет показал, что 1 г цинка предотвращает потери из-за коррозии 10 г стали в год. Полная защита оголенных кромок оцинкованных листов благодаря анодному характеру покрытия поверхности обеспечивается при толщине до 1,6 мм.
Цинковое покрытие анодно по отношению к стали практически во всех коррозионных средах. Характерно, что скорость коррозии цинковых покрытий практически не меняется за весь срок их службы. Это позволяет довольно точно рассчитывать время до их разрушения.
Скорость коррозии цинка в 10-30 раз меньше, чем скорость коррозии стали.
На поверхности горячеоцинкованной стали в процессе экспозиции в открытой агрессивной атмосфере (промышленная атмосфера, содержащая двуокись серы) образуется сетка кристаллов. Рентгенографический анализ этих кристаллов показал, что они на 98% состоят из сульфата цинка. Во влажной атмосфере, содержащей SO3, пассивирующий воздушноокисный слой на цинке разрушается и скорость саморастворения возрастает на два порядка по сравнению с чистой атмосферой.Коррозия оцинкованных листов в зимний период заметно больше, чем летом. Объясняется это главным образом тем, что зимой в воздухе относительно больше СО2, SO2, чем летом, а также большей влажностью зимнего воздуха.
Такое специфическое влияние температуры воды, под воздействием которой находится цинковое покрытие, на процесс его коррозии объясняется тем, что при 50—60° С гидроокись цинка и карбонат цинка, возникающие на поверхности оцинкованного листа, преобразуются в стабильную окись цинка, которая по потенциалу благороднее железа, т.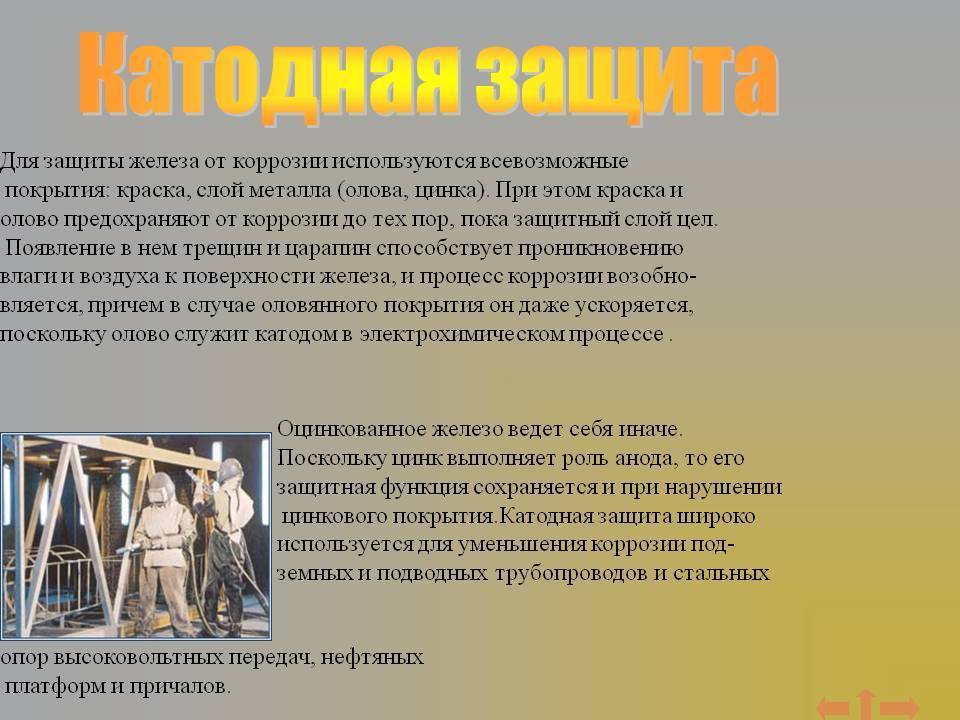
Минимальная скорость коррозии цинка наблюдается в слабощелочных средах: если рН ниже 5 или выше 12, наступает сильная коррозия.
Наибольшей стойкостью к коррозии обладают промежуточные слои цинкового покрытия, т. е. Fe—Zn слой, обогащенный железом, и слой, обогащенный цинком.
Исследованием, выполненным в течение 80 дней на образцах оцинкованной листовой стали, подвергавшейся коррозии в атмосфере городской местности, установлено следующее. Наибольшей коррозионной стойкостью обладает сталь, оцинкованная электролитным цинком, не содержащим примесей. При повышенном содержании в цинке алюминия, свинца (более 0,25—0,35%) и олова коррозионная стойкость цинкового покрытия понижается.
Рекомендуем посетить http://www.newmet.ru/
Время последней модификации 1271980337
Сталь Антикоррозийные свойства — Энциклопедия по машиностроению XXL
Хромирование — процесс поверхностного насыщения стали хромом. Хромирование применяется для придания стали антикоррозийных свойств, а также для повышения износоустойчивости и улучшения внешнего вида изделий (декоративное хромирование). [c.20]При сварке стали 18-8 участки основного металла, расположенные по обе стороны от шва, подвергаются нагреву. В участках, длительное время находящихся под воздействием критических температур (450—850″), может развиться межкристаллитная коррозия, заключающаяся в том, что пограничные слои зерен под действием агрессивной среды теряют свои антикоррозийные свойства. Это явление есть результат обеднения пограничных слоев зерен аустенита хромом вследствие выпадения сложных карбидов железа и хрома по границам кристаллов аустенита. С целью уменьшения склонности стали к межкристаллит-ной коррозии уменьшают содержание в ней С или сокращают время пребывания металла в интервале критических температур.
[c.82]
Каждая топливная таблетка должна быть изолирована от охлаждающей воды. Реактивность и тепловые напряжения вызывают значительную деформацию и изменения плотности топлива. В топливе также содержатся побочные продукты деления. Оболочки, используемые для этой цели, обычно изготавливаются из циркониевых сплавов, однако используются также оболочки из нержавеющей стали. Циркониевые сплавы обладают хорошей механической прочностью и необходимыми антикоррозийными свойствами, а также превосходными ядерными свойствами. Например, сечение захвата нейтронов у него значительно меньше, чем у нержавеющей стали. [c.171]
Азотирование неответственных деталей, изготовленных из низкоуглеродистой стали, не несущих нагрузки в эксплоатации, к которым предъявляются требования только в части устойчивости против коррозии, может проводиться при температурах 500—850 С. Глубина азотированного слоя, обеспечивающая антикоррозийные свойства, получается при выдержках 2—3 часа при температуре 600° С, 20—60 мин. при 600—750° С и 10 — 20 мин. при 800-850° С.
[c.521]
Механические и антикоррозийные свойства низколегированных сталей [c.645]
Большой интерес в этом отношении представляет процесс диффузионного хромирования, позволяющий довести содержание хрома в поверхностном слое до 50″/о [2, 4]. Насыщенная хромом поверхность стали обладает очень высокими антикоррозийными свойствами, очень высокой твердостью (808 ед. Бринеля для углеродистых сталей) и износоустойчивостью. [c.364]
При хромировании высокоуглеродистой стали диффузионная зона представляет собой карбидный слой и небольшую прослойку тройного эвтектоида. Дальше идет уже основной металл. Образующийся карбидный слой обладает очень высокой твердостью, высоким сопротивлением против истирания и высокими антикоррозийными свойствами, особенно при высоких температурах. Карбидный слой отличается несколько меньшей вязкостью в сравнении со слоем твердых растворов, но не настолько, чтобы могло происходить отслаивание или появление трещин.
[c.366]
Для стали типа 18-8 с 0,07% С и 0,4% Ti, закаленной с 900—1300° С, экспериментом было установлено, что при последующем нагреве при 600° С выделяется главным образом карбид хрома и лишь немного карбида титана. При 700° С выделяются одновременно карбиды хрома и карбиды титана, а при 800° С количество карбидов хрома становится меньше, а карбидов титана — больше. При стабилизирующей обработке при 850—900° С в аустенитной основной м>ассе должны быть только карбиды титана, вследствие чего сталь не должна быть склонна к межкристаллитной коррозии после нагрева в опасном интервале температур. Однако присадка этих элементов отрицательно сказывается на качестве поверхности слитков, снижает общие антикоррозийные свойства металла, ухудшает его пластичность. В присутствии титана несколько снижается химическая стойкость стали в кипящей азотной кислоте. Кроме того, титан, как легко окисляющийся элемент, выгорает во время сварки, что, в свою очередь, может привести к по-
[c.153]
Азотирование — насыщение поверхностного слоя стали азотом при нагревании в газообразном аммиаке (температура не ниже 450° С), выдержка при этой температуре и последующее охлаждение.Повышается твердость, износоустойчивость и антикоррозийные свойства. [c.29]
В течение определенного времени и в последующем охлаждении в минеральном масле. Химический способ воронения стали состоит в обработке изделия в концентрированном растворе щелочи и азотнокислых солей при температуре 120— 150° С. Антикоррозийные свойства этой обработки невысоки, поэтому изделия дополнительно смазывают маслом. Применяется для изделий, работающих в закрытых помещениях в сухом воздухе. [c.74]
Кислород, попадая в зону сварки из воздуха, электродного покрытия или флюса, взаимодействуете жидкой ванной металла, окисляет железо и элементы, содержащиеся в стали. Кислород является наиболее вредной примесью, так как он образует растворимые в стали окислы, наличие которых в металле шва снижает пределы прочности и текучести, относительное удлинение и ударную вязкость сварного соединения. Повышенное содержание кислорода в сварном шве приводит к снижению антикоррозийных свойств и увеличивает склонность металла к образованию горячих и холодных трещин.
[c.28]
Опыт предприятий показывает, что контактная сварка нержавеющих сталей должна выполняться на жестких режимах. Это объясняется, во-первых, тем, что при медленном нагреве и охлаждении нержавеющие стали теряют свои антикоррозийные свойства и, во-вторых, при нагреве они имеют большой коэффициент линейного расширения, в силу чего могут возникнуть значительные коробления в крупногабаритных деталях и узлах. [c.108]
Фосфатирование — образование пленки фосфорно-кислых солей на деталях из малоуглеродистых сталей. Фосфатная пленка имеет невысокую механическую прочность. Антикоррозийные свойства ее повышаются после лакировки.
[c.49]
При осаждении черного никеля непосредственно на сталь, прочность сцепления, пластичность и антикоррозийные свойства покрытия являются весьма низкими. Поэтому при осаждении черного никеля рекомендуется применять подслой меди или обычного матового никеля, а толщину покрытия черным никелем ограничивать величиной около 0,5 мк. [c.100]
Многослойные вкладыши представляют возможность одновременного использования нескольких металлов или сплавов, которые раздельно — по-разному (или только частично), а в сочетании — почти полностью удовлетворяют требования, предъявляемые К подшипниковому материалу, повышая надёжность подшипника. Например, слой металла с высокими механическими и антифрикционными свойствами, но с пониженной устойчивостью коррозии, покрывается антикоррозийным металлом. Так, практикуется электролитическое покрытие рабочей поверхности слоем индия, предохраняющего от коррозии и улучшающего антифрикционные свойства. Выполняются комбинации 1) сталь (основа вкладыша) — серебро — свинец — индий
[c.634]
Фосфатирование широко применяется как метод подготовки поверхности под окраску углеродистых сталей и цинка. Оно заключается в обработке хорошо очищенных поверхностей растворами первичных фосфорнокислых солей цинка, марганца и железа в присутствии свободной фосфорной кислоты. Получаемая на поверхности металла фосфатная пленка толщиной около 3 мк имеет кристаллическое пористое строение. Лакокрасочное покрытие имеет отличное сцепление с фосфати-рованной поверхностью и обладает повышенными антикоррозийными свойствами. [c.264]
Сталь нержавеющая хромоникельмарганцовая 3 — 486, 490 Сталь низколегированная — Свойства 3 — 374 —низколегированная МСт. 3 — Антикоррозийные свойства 13 — 645 — Механические свойства 13—645 [c.282]
VII Малоуглеродистый легированный ковкгй чугун Группа 3 или 2, тип д 1,1-1,77 С 0,8 1,3″/ 51 2,0—3,0 / Сг 0,6—Мп 52—61 46-52 7. 1—2.5 220—280 Высокая прочность и циклическая вязкость, антифрикционные и антикоррозийные свойства [11] То же Заменитель поковок из легированных сталей Коленчатые и кулачковые валы, поршни, тормоз-н)>1в барабаны
[c.83]
При сварке хромоникелевых нержавеющих и жароупорных сталей необходимо учесть следующие их особенности а) хром интенсивно соединяется с кислородом, образуя тугоплавкий окисел Сг20 , б) хром образует устойчивые карбиды СГ3С2 и СгцС. сильно снижающие антикоррозийные свойства металла выделение карбидов из аустенита проходит в интервале температур 600—800° С, и чем больше содержание углерода в металле, тем благоприятнее условия их выделения. Наличие в металле титана и ниобия предохраняет его от выпадения карбидов хрома в) теплопроводность нержавеющих и жароупорных сталей в 3—4 раза меньше, чем малоуглеродистых, а коэфициент линейного расширения значительно выше, что вызывает местные перегревы и повышает внутренние напряжения. [c.428]
Припои4, 5и6-с высоким содержанием серебра, белого цвета, являются наиболее распространёнными применяются для пайки стали, меди, медных и никелевых сплавов.

Для придания стали специальных физических и химических свойств (жаростойкости, антикоррозийных свойств и др.) применяют диффузионную металлизацию. Она заключается в нагревании стальной поверхности, контактирующей с металлосодержащей средой, до высокой температуры, насыщении поверхности алюминием (алити-рование), хромом (диффузионное хромирование), кремнием (сили-цирование) и другими металлами, выдержке и последующем охлаждении. [c.30]
Охлаждающие жидкости должны обладать высокой теплоемкостью, смазыва1ющими и антикоррозийными свойствами, устойчивостью и высокой температурой вспышки. При обработке стали в качестве такой смазочно-охлаждающей жидкости применяется эмульсия из соды, зеленого мыла, минерального масла и воды. Для резьбонарезания и зубофрезерования используется сульфо-фрезол, состоящий из минерального масла), серы и смолистых веществ. Чистовое точение, фрезерование и сверление стали ведутся с применением растворов из 0,5—1% мыла, 0,5—0,75% соды и 0,25% нитрита натрия или же с применением эмульсии, содержащей 3—4% эмульсола и 0,2— 0,3% соды или жидкого стекла. Входящий в состав упомянутой эмульсии эмульсол состоит из 7% олеиновой кислоты, 10% канифоли, 4% каустической соды,
[c.127]
При сварке стали 1Х18Н9Т применяется сварочная проволока 0Х18Н9Т без ниобия. Сварной шов, заваренный такой проволокой, не гарантирует стойкость против межкристаллитной коррозии. Повышения антикоррозийных свойств можно добиться, применяя иммунизационную термическую обработку, которая заключается в нагреве сварного изделия или только сварного шва до температуры 750—900° и выдержке при этой температуре в течение нескольких часов. При таком режиме происходит диффузия хрома, и его содержание выравнивается по всему объему зерна. При последующем воздействии более низких температур выпадение карбидов не наблюдается.
[c.87]
Оксидирование стали — воронение, синение, чернение — получается при обработке сталей щелочными растворами. Оно придает поверхности антикоррозийные свойства, красивый внешний вид, применяется для покрытия мелких деталей, винтов и др. [c.49]
Для снижения уровня шума зубчатые колеса изготовляют из чугуна и пластмассы. Эти материалы по сравнению со сталью имеют меньшую стоимость, лучшую обрабатываемость, но колеса из этих материалов передают меньший крутящий момент, чем стальные колеса. Зубчатые венцы червячных колес чаще всего изготовляют из бронзы, которая обладает высокими антифрикционными и антикоррозийными свойствами. Зубч атые колеса насосов экономично изготовлять из металлического порошка. [c.16]
Основное затруднение при сварке хромоникелевых сталей, не содержащих титана или ниобия, сосгоит в том, что при нагревании до 500—700° они теряют свои антикоррозийные свойства и становятся хрупкими вследствие выделения карбидов хрома по границам зерен. Свойства стали можно снова восстановить нагреванием до температуры 850° (при которой карбиды хрома вновь растворяются в сплаве) и последующим быстрым охлаждением в воде, а для малых толщин — на воздухе. Такой вид термообработки называется стабилизирующим отжигом.
[c.150]
Нужны были более совершенные металличеокие сплавы. Б последние десятилетия минувшего века появились стали, в состав которых вошли легирующие элементы — вольфрам, хром, марганец, никель и другие, значительно новы-сившие механические и иные свойства (жаростойкость, антикоррозийность, кислотоупорность и т. д.) стальных сплавов. [c.151]
Антикоррозийное азотирование стали 7 — 521 Антипараллелограм шарнирный 2 — 75 Антисептики для древесины 4 — 278 Антифрикционная кривая — см. Трактрисса Антифрикционные материалы металлокерамические — Физико-механические свойства 4 — 257 [c.13]
Медь — металл красноватого цвета. Благодаря своему внешнему виду и свойству легко коваться при сравнительно низких температурах медь одним из первых металлов стала применяться для изготовления предметов домашнего обихода и сельскохозяйственных орудий. А 1едь отличается высокой электропроводностью, теплопроводностью, пластичностью и антикоррозийной устойчивостью.
[c.59]
Нержавеющая сталь типа Х18Н9 благодаря своим высоким антикоррозийным, механическим и технологическим свойствам широко применяется во всех отраслях промышленности. В целях экономии этой дорогой и дефицитной стали изучено электроосаждение сплавов Ре—Сг на обычную углеродистую сталь [1— [c.28]
Легированные стали и сплавы на железной основе с особыми свойствами содержат в своем составе большое количество легирующие компоненты, сочетание которых придает сталям жаропрочность, антикоррозийность, большое электрическое сопротивление и другие ценные свойства. Так, например, сталь марки 1Х18Н9Т — хромоникелевая нержавеющая сталь с содержанием около 0,1% углерода, 18% хрома, 9% никеля, около 1% гитана отличается высокой кислотоупорностью и применяется для изготовления аппаратов на заводах химического машиностроения марганцовистая сталь марки Г13, называемая сталью Гадфильда, содержащая от 11 до 14% марганца, хорошо работает на истирание и применяется для изготовления зубьев ковшей экскаваторов и железнодорожных стрелок. .
[c.16]
Ковкий чугун но сравнению со сталью более дешевый материал, обладает хорошими механическими (противоударными) свойствами и высокой антикоррозийной стойкостью. Из него изготовляют изделия, работающие в условиях значительных напряжений, повторно переменных нагрузок, ударов, а также высокого давления воды, пара, газов и пр. детали сельскохо- [c.30]
Высоколегированные стали и сплавы более склонны к образованию трещин, чем низкоуглеродистые. Горячие трещины появляются большей частью в аустенитных сталях, холодные — в закаливающихся сталях мартенситного и мартенситно-ферритного классов. Кроме этого, коррозионностойкие стали, не содержащие титана или ниобия или легированные ванадием, при нагревании выше 500°С теряют антикоррозионные свойства по причине выпадения из твердого раствора карбидов хрома и железа, которые становятся центрами коррозии и коррозионного растрескивания. Термической обработкой (чаще всего закалкой) можно восстановить антикоррозионные свойства сварных изделий.

Как выбрать антикоррозийное средство для обработки металла?
- Главная
- Статьи
- Антикоррозийные средства для металлических конструкций: советы по выбору
Покраска металлоконструкций – один из этапов антикоррозийной обработки, качество которой зависит не только от мастерства и опыта специалиста, но и от выбора антикоррозийного средства для металла.
Выполнив десятки заказов по антикоррозийной обработке металлических конструкций, мы с уверенностью можем сказать, что правильный выбор антикоррозийного состава для металла – это 50% успеха.
Дело в том, что антикоррозийная обработка конструкций на промышленных объектах должна соответствовать принятым нормам и требованиям, так как на каждом предприятии имеются свои конструкции и оборудование, трубы, вентиляционная система, каркасы строений и зданий – и все это может состоять из разных сплавов металлов.
Таким образом, в промышленном плане невозможно подобрать какое-то одно универсальное средство антикоррозийной обработки, это всегда будет система антикоррозийных покрытий.
Пример № 1. В одном из заказов клиенту требовалась антикоррозийная обработка и окрашивание металлических конструкций. Важной особенностью было то, что при эксплуатации конструкции возникал риск механических повреждений и даже деформации, поэтому антикоррозийная система должна была придать конструкции устойчивости к механическим повреждениям и повысить уровень прочности.
В этом случае лучшие антикоррозийные средства – те, что обладают высокой эластичностью и прочностью, а также низкой степенью изнашиваемости.
Пример № 2. Руководство предприятия, на котором требовалась антикоррозийная защита определенного рода металлоконструкций, предупредило нас, что эти самые конструкции будут подвергаться воздействию резкого перепада температур, а также частому воздействию воды. В этом случае мы подобрали средство с высокой степенью устойчивости к влаге, высоким и низким температурам.
Критерии выбора антикоррозийного состава
Исходя из собственного опыта, мы делимся с вами критериями, которые обязательно следует учитывать при выборе того или иного антикоррозийного покрытия для конструкций из металла.
- Состав металла. Подбирать средство нужно так, чтобы оно подходило для конкретного металла или сплава металлов. К примеру, для разных марок стали подходят разные покрытия, не говоря уже о конструкциях из чугуна, алюминия, оцинкованной стали и т.
д. Для черных металлов выбирайте грунтовку и краску с повышенными антикоррозийными свойствами. При этом крайне желательно, чтобы грунтовка, краска и растворитель были одной фирмы и представляли собой целую антикоррозийную систему.
- Поверхность покрытия. В идеале она должна быть чистой и сухой, без грязи и ржавчины, но такое бывает редко. В большинстве случаев можно провести чистку металлоконструкций, обеспыливание балок и ферм и т.д. перед покраской. Но в ряде случаев нет возможности тщательно очистить поверхность от окиси, ржавчины, соли, масел и старых покрытий. Это стоит учитывать при выборе средства, и отдавать предпочтение тому, что отличается отличной адгезией, даже если наносить его на мокрую или ржавую поверхность.
- Условия эксплуатации. Важно учитывать, при каких условиях будут эксплуатироваться конструкции. Перепады температур, воздействие агрессивных сред, атмосферных осадков, химических веществ и т.д. – все это является показателем к подбору антикоррозийного средства, способного нивелировать или минимизировать негативное воздействие.
Виды грунтовок по металлу
В зависимости от состава металла и назначения конструкции при антикоррозийной обработке требуется использование того или иного вида грунтовок. В данном случае соблюдение технологии на 100% крайне обязательно!
Все виды грунтовок можно разделить на следующие группы:
- Для черных металлов (чугун, железо), сплавов из железа и стали. Правильно подобранная грунтовка замедлит процесс окисления и появления ржавчины.
- Для алюминия, латуни, меди и прочих цветных металлов и их сплавов, а также для оцинкованной стали.
- Для оцинкованной стали лучше использовать грунтовку на органических растворителях.
- Для черных металлов, затронутых коррозией, нужно использовать грунтовочные составы – преобразователи ржавчины, восстанавливающие поврежденную поверхность металлической конструкции.
- Грунтовки для загрязненных металлов блокируют следы копоти, жира и несмываемой грязи, позволяя лакокрасочному покрытию лечь ровно и не отслаиваться со временем.
Можно ли сэкономить при выборе состава для антикоррозийной обработки металлических конструкций?
В ряде случаев при выборе антикоррозийного средства у заказчиков возникает резонный вопрос – почему выбрано то или иное средство, и можно ли взять дешевле. Конечно, стоимость средств в данном случае – важный фактор при выборе, но далеко не основополагающий.
Если металлоконструкции эксплуатируются в неблагоприятных, жестких условиях, в контакте с химикатами, водой, подвержены механическим воздействиям, перепадам температур, то экономия на антикоррозийной системе обернется дополнительными расходами на ту же самую процедуру в ближайшее время.
Если же конструкции эксплуатируются в благоприятных условиях, а сплавы не отличаются высокой коррозией, то здесь нет смысла переплачивать за антикоррозийное покрытие с дополнительной стойкостью.
ТОП-3 популярных и надежных производителей антикоррозийных грунтовок и красок
- Tikkurila – это всемирно известный производитель, ассортимент которого включает широкий выбор грунтовок и красок как для внутреннего, так и для наружного применения.
Грунтовки и краски быстро сохнут, ровно ложатся, очень экономичны в расходе, образуют ровную и плотную поверхность, устойчивы к выгоранию, истиранию , служат очень долго (при условии грамотного нанесения и соблюдения технологии).
- Компания «Эмлак» производит грунтовку, являющуюся, по совместительству, преобразователем ржавчины. Грунтовки отлично защищают металлические конструкции от коррозии, что очень важно в условиях длительной нружной эксплуатации.
- Компания «Радуга» — известный производитель акриловых грунтовок, обладающих отличным антикоррозийным эффектом, доступной стоимостью, быстротой высыхания и обширной цветовой гаммой – и все это по доступной стоимости.
В дополнение хочется отметить, что помимо качественного средства важна технология нанесения, поэтому стоит доверить антикоррозийную обработку металлических конструкций профессионалам, особенно, если планируются работы на высоте.
Специалисты компании «Высотные Работы» выполнят работы по антикоррозийному покрытию и окрашиванию промышленных конструкций на любой высоте ив любых объемах. Заказать услуги можно по телефонам +7 (495) 991-55-21, +7 (916) 903-33-84, либо оставив заявку на сайте.
Рейтинг: 5/5 — 3 голосов
Для чего нужна антикоррозийная защита металла
Использование металла при возведении зданий и сооружений в своё время перевернуло деятельность человека, стало отправной точкой развития промышленной и строительной сферы. Только среди очевидных плюсов металла – гибкости и прочности, возможности надёжного соединения, небольшого веса и так далее, присутствует недостаток – коррозия. Известно, что длительное воздействие кислорода, воды, газа или кислот способно нанести вред металлоконструкции. Она утратит изначальную прочность и начнёт разрушаться.
Антикоррозийная защита в Екатеринбурге от профессионалов компании Штурм позволит предотвратить негативные процессы. Существует немало различных способов, как сохранить целостность металла и уберечь его от коррозийного разрушения. В промышленности и строительстве популярностью пользуется барьерная защита, предполагающая создание особой плёнки на поверхности металла, выступающей преградой внешней среде. Часто для этого используются лакокрасочные покрытия.
Плюсы защитной обработки металла
Коррозией является процесс разрушения металлов и сплавов, который активно протекает при взаимодействии изделия с атмосферой. Разрушение часто носят химический или электрохимический характер, при этом оказывает особое влияние на эксплуатационные показатели конструкции.
Достоинства защитной обработки следующие:
- существенное продление срока эксплуатации конструкции;
- нанесение обрабатывающего материала не требует много времени;
- ценовая доступность наносимых составов;
- снижение риска возникновения аварийных ситуаций при эксплуатации изделия.
Материалы для проведения защитной обработки
По той причине, что работы выполняются за несколько стадий, предполагая использование определённых материалов. Подбор составов зависит от существующих эксплуатационных условий. У стандартного покрытия обычно три слоя:
- Грунтовый. Материалы применяются для подготовки или повышения уровня защиты изделия;
- Барьерный. Часто состоит из краски с включением металлических элементов;
- Финишный. Обеспечивает внешние показатели и защиту от ультрафиолета.
Используемые вещества могут оказывать влияние на свойства и параметры покрытия. К примеру, их эксплуатационные показатели часто зависят от толщины наносимой краски.
На правах рекламы
Влияние химических элементов на свойства стали.
Условные обозначения химических элементов:
хром ( Cr ) — Х никель ( Ni ) — Н молибден ( Mo ) — М титан ( Ti ) — Т медь ( Cu ) — Д ванадий ( V ) — Ф вольфрам ( W ) — В | азот ( N ) — А алюминий ( Аl ) — Ю бериллий ( Be ) — Л бор ( B ) — Р висмут ( Вi ) — Ви галлий ( Ga ) — Гл | иридий ( Ir ) — И кадмий ( Cd ) — Кд кобальт ( Co ) — К кремний ( Si ) — C магний ( Mg ) — Ш марганец ( Mn ) — Г | свинец ( Pb ) — АС ниобий ( Nb) — Б селен ( Se ) — Е углерод ( C ) — У фосфор ( P ) — П цирконий ( Zr ) — Ц |
ВЛИЯНИЕ ПРИМЕСЕЙ НА СТАЛЬ И ЕЕ СВОЙСТВА
Углерод — находится в стали обычно в виде химического соединения Fe3C, называемого цементитом. С увеличением содержания углерода до 1,2% твердость, прочность и упругость стали увеличиваются, но пластичность и сопротивление удару понижаются, а обрабатываемость ухудшается, ухудшается и свариваемость.
Кремний — если он содержится в стали в небольшом количестве, особого влияния на ее свойства не оказывает.(Полезная примесь; вводят в качестве активного раскислителя и остается в стали в кол-ве 0,4%)
Марганец — как и кремний, содержится в обыкновенной углеродистой стали в небольшом количестве и особого влияния на ее свойства также не оказывает. (Полезная примесь; вводят в сталь для раскисления и остается в ней в кол-ве 0,3-0,8%. Марганец уменьшает вредное влияние кислорода и серы.
Сера — является вредной примесью. Она находится в стали главным образом в виде FeS. Это соединение сообщает стали хрупкость при высоких температурах, например при ковке, — свойство, которое называется красноломкостью. Сера увеличивает истираемость стали, понижает сопротивление усталости и уменьшает коррозионную стойкость. В углеродистой стали допускается серы не более 0,06-0,07%. ( От красноломкости сталь предохраняет марганец, который связывает серу в сульфиды MnS).
Фосфор — также является вредной примесью. Снижает вязкость при пониженных температурах, то есть вызывает хладноломкость. Обрабатываемость стали фосфор несколько улучшает, так как способствует отделению стружки.
ЛЕГИРУЮЩИЕ ЭЛЕМЕНТЫ И ИХ ВЛИЯНИЕ НА СВОЙСТВА СТАЛИ
Хром (Х) — наиболее дешевый и распространенный элемент. Он повышает твердость и прочность, незначительно уменьшая пластичность, увеличивает коррозионную стойкость; содержание больших количеств хрома делает сталь нержавеющей и обеспечивает устойчивость магнитных сил.
Никель (Н) — сообщает стали коррозионную стойкость, высокую прочность и пластичность, увеличивает прокаливаемость, оказывает влияние на изменение коэффициента теплового расширения. Никель – дорогой металл, его стараются заменить более дешевым.
Вольфрам (В) — образует в стали очень твердые химические соединения – карбиды, резко увеличивающие твердость и красностойкость. Вольфрам препятствует росту зерен при нагреве, способствует устранению хрупкости при отпуске. Это дорогой и дефицитный металл.
Ванадий (Ф) — повышает твердость и прочность, измельчает зерно. Увеличивает плотность стали, так как является хорошим раскислителем, он дорог и дефицитен.
Кремний (С)- в количестве свыше 1% оказывает особое влияние на свойства стали: содержание 1-1,5% Si увеличивает прочность, при этом вязкость сохраняется. При большем содержании кремния увеличивается электросопротивление и магнитопроницаемость. Кремний увеличивает также упругость, кислостойкость, окалиностойкость.
Марганец (Г) — при содержании свыше 1% увеличивает твердость, износоустойчивость, стойкость против ударных нагрузок, не уменьшая пластичности.
Кобальт (К) — повышает жаропрочность, магнитные свойства, увеличивает сопротивление удару.
Молибден (М) — увеличивает красностойкость, упругость, предел прочности на растяжение, антикоррозионные свойства и сопротивление окислению при высоких температурах.
Титан (Т) — повышает прочность и плотность стали, способствует измельчению зерна, является хорошим раскислителем, улучшает обрабатываемость и сопротивление коррозии.
Ниобий (Б) — улучшает кислостойкость и способствует уменьшению коррозии в сварных конструкциях.
Алюминий (Ю) — повышает жаростойкость и окалиностойкость.
Медь (Д) — увеличивает антикоррозионные свойства, она вводится главным образом в строительную сталь.
Церий — повышает прочность и особенно пластичность.
Цирконий (Ц) — оказывает особое влияние на величину и рост зерна в стали, измельчает зерно и позволяет получать сталь с заранее заданной зернистостью.
Лантан, цезий, неодим — уменьшают пористость, способствуют уменьшению содержания серы в стали, улучшают качество поверхности, измельчают зерно.
из чего состоит, где применяется
Автор: iforget • Дата публикации: 21.01.2022Металлические конструкции широко используется в строительстве. Они выносят большую нагрузку, им можно придавать любую форму. Но у них есть важный недостаток – способность окисляться, покрываться ржавчиной. Избавиться от этого неприятного свойства позволяет антикоррозийная защита металла. На сайте https://shturm.pro/info/news/antikorrozionnaya-zashchita/ можно заказать работы по обработке металлоконструкций, приданию им устойчивости к появлению ржавчины.
Степени защиты
Различают два вида антикоррозийной защиты:
- Первичную – проводится еще на этапе изготовления металлоизделий путем ввода в состав сплава различных добавок. Используется для защиты от атмосферной коррозии, возникающей при контакте металлов с воздухом.
- Вторичную – это покрытие поверхностей металлических изделий, подвергаемых в дальнейшем эксплуатационным воздействиям, лакокрасочными покрытиями.
Чем обрабатывают металлы от коррозии
Антикоррозийное покрытие используют для трубопроводов и металлических конструкций. Ее осуществляют путем нанесения на поверхность изделий специальных обмазок, эмульсий, суспензий, паст и покрытий. Для производства работ по защите металлоконструкций и сооружений от коррозии используют:
- краски;
- грунтовки;
- химическое, электрохимическое и комбинированное покрытия.
Выбор того или иного материала для антикоррозионной защиты зависит от условий эксплуатации металлоконструкций, свойств и состава защищаемой поверхности, а также от финансовых возможностей заказчика.
Антикоррозийный грунт содержит в себе ингибиторы коррозии и пассивирующие вещества. Благодаря им создается защитная пленка, которая предотвращает дальнейшее развитие ржавчины. Грунтовку наносят на поверхность металла для повышения адгезии между металлом и лакокрасочным материалом, а также для предохранения ее от коррозии. При нанесении грунтовки происходит пассивирование – образование на поверхности плотной защитной пленки, которая предохраняет металл от дальнейшего окисления.
Почему появляется ржавчина
Антикоррозийная обработка металлов проводится с целью защиты его от воздействия окружающей среды. В процессе эксплуатации металлоизделий происходит окисление поверхностей и образуется ржавчина. Особенно активно коррозия развивается на стыках между деталями. Необработанный металл вступает в реакцию с кислородом, водой и другими веществами, которые содержатся в воздухе. В состав антикора включают специальные добавки, которые уменьшают риск возникновения очагов коррозии. Защитные составы наносят на предварительно очищенную и обезжиренную поверхность. Для очистки обычно используют пескоструйный метод.
Оставьте первый комментарий
Ждем ваш первый комментарий
Похожие материалы
[06. Подшипники скольжения и каченияПодшипник представляет собой промежуточный узел, обеспечивающий вращение двух сопрягаемых деталей. Это относительно простое изделие является незаменимым во всех отраслях народного хозяйства и без него не может обойтись практически никакая конструкция. Классификация подшипников Все существующие подшипники разделяются на две большие категории. Скольжения. Состоят из двух колец, между которыми н… |
[06.02.2022] Назначение строительных касокРабота в определенных сферах промышленности, например, в горной добыче, строительстве, металлургии, энергетике и прочих нередко сопровождается вероятностью получить травму головы или после падения предмета, или столкновения с определенным объектом. Специфика деятельности бывает такой, что не во всех случаях можно предотвратить данную вероятность иначе, как использованием индивидуальных средств за.![]() |
[06.02.2022] Изготовление металлоконструкций на заказВсем известно, что изделия из металла обладают качествами, позволяющими использовать их во многих сферах. Особенно часто с металлическими конструкциями работают специалисты строительной отрасли. И это вполне понятно, ведь металлические элементы делают строительные объекты максимально прочными и надёжными. Однако для того чтобы применить в работе ту или иную металлическую конструкцию, её необходимо… |
[03.02.2022] Требования к стоматологической установкеПри посещении клиники человек в первую очередь обращает внимание на оснащение стоматологического кабинета. Технологичное современное оборудование в первую очередь повышает имидж медицинского центра, а также при условии высокого качества повышает эффективность, скорость терапии.![]() |
Anti-Corrosion — обзор | ScienceDirect Topics
3.1 Введение
Полимерные нанокомпозиты с различными типами нанонаполнителей привлекли внимание благодаря своим ценным проводящим, магнитным, оптическим, тепловым, механическим, антикоррозионным, биомедицинским и другим свойствам [1–3]. Полимерные нанокомпозиты с наноуглеродными нанонаполнителями разработаны с использованием углеродных нанотрубок [4–6], графена [7–9], оксида графена [10–12], фуллеренов [13–18], наноалмазов [19–24], графита [25– 27], сажа [28–30] и др.[31–34]. Точно так же полимерные нанокомпозиты были разработаны путем включения неорганических нанонаполнителей, таких как наноглины [35–37], галлуазит [38–40], полиэдрический олигомерный силсесквиоксан [41–43], наночастицы металлов [44, 45], оксиды металлов [46]. –48] и другие неорганические наночастицы и нанонаполнители в полимерах [49–51]. Следовательно, полимер/наноуглерод и полимер/неорганические материалы нашли применение в оборонной [52–54], аэрокосмической [55–57], автомобильной [58–60], мембранах [61–64], покрытиях [65–67], фотогальванике [58–60]. 68–70], сенсоры [71–73], устройства накопления энергии [74–76], устройства производства энергии [77–79], доставка лекарств [80–82], биовизуализация [83–85], тканевая инженерия [86– 90] и др.Для наполнения полимеров этими нанонаполнителями были приняты различные методы [91–93]. Соответственно, различные исследователи сосредоточились на однородной дисперсии нанонаполнителя [94–96]. Однако добиться однородной дисперсии и морфологии нанокомпозитов непросто и не просто [97–99]. Было обнаружено несколько попыток равномерного диспергирования нанонаполнителя в матрицах [99–101]. Для улучшения дисперсии нанонаполнителя и совместимости матрицы с нанонаполнителем рассматривалась модификация поверхности нанонаполнителя [102–105].Для создания высокоэффективных нанокомпозитов необходимы простые методы и оптимизированные условия для разработки высокотехнологичных наноматериалов [106–108].
В этой главе оценивается важность различных типов нанонаполнителей, дисперсий нанонаполнителей и модификаций нанонаполнителей для получения нанокомпозитов. Необходимость диспергирования наночастиц в сопряженных полимерах очень похожа на диспергирование нанонаполнителей в термопластах или других полимерах. Здесь мелкодисперсная дисперсия нанонаполнителя в полимерах требует модификации наночастицами для повышения производительности.
Границы | Получение и свойства антикоррозионных покрытий из эпоксидной эмульсии, модифицированной полиуретаном на водной основе
Введение
Коррозия — это процесс, при котором материалы, особенно металлы (например, углеродистая сталь, оцинкованная сталь и чугун), изнашиваются под действием электрохимических и химических воздействий. Металлы имеют анодную и катодную области, а коррозия возникает в присутствии кислорода, воды и проводящей среды. Влияние коррозии металла на безопасность эксплуатации и надежность продукции может привести к потере ценных продуктов, крупным авариям, гибели персонала и остановке производства, поэтому последствия коррозии металлических конструкций огромны. Нанесение покрытий является наиболее широко используемым методом защиты от коррозии из-за желаемого преимущества замедления проникновения воды, ионов и других агрессивных сред через органическую пленку, а также простоты нанесения.
Большинство современных антикоррозионных покрытий представляют собой покрытия на основе растворителей. В последнее десятилетие водоразбавляемые покрытия привлекли внимание для защиты металлов, потому что требования экологических стандартов устанавливают ограничения на удаление или контроль летучих органических соединений до минимально возможных уровней (Wang et al., 2013; Абдолахи и др., 2014; Йылмаз и др., 2014; Лю и др., 2016; Чжан и др., 2017).
Однако антикоррозионные свойства покрытий на водной основе значительно уступают покрытиям на основе растворителя, поскольку гидрофильные группы часто сохраняются в покрытии в процессе формирования пленки, что снижает способность щита к диффузии пара и влагостойкость (Ai et al., 2014; Wang З. и др. , 2014; Рахман и др., 2015). Таким образом, добавление ингибиторов коррозии или наполнителей необходимо для повышения коррозионной стойкости покрытий на водной основе, а также микро/нано неорганических частиц (т.например, неорганические добавки) часто применяются в качестве ингибиторов коррозии или наполнителей (Hao et al., 2012; Ma et al., 2012b; Cheek et al., 2013; Liang et al., 2013; Suleiman et al., 2014; Дас и др., 2017).
Многие неорганические частицы, включающие графен (Mittal, 2014; Kausar et al., 2016; Qiu et al., 2017; Shahabadi et al., 2017; Zhu et al., 2017), Ni-Fe(Ti,W)C нанокомпозит (Khorsand et al., 2018), нано-ZnO (Dhoke and Khanna, 2009; Rasool et al., 2018), SiO 2 (Khademian et al., 2015; Wang N.et al., 2016), TiO 2 (Montesinos et al., 2015; Wang N. et al., 2016), Al (Deflorian et al., 2011), Al 2 O 3 (Chen et al. al., 2014), Ag (Rahman, 2017), слюдистый оксид железа (Kakaei et al., 2013) и углеродные нанотрубки (Zhuo et al. , 2016) были исследованы исследователями, и результаты показывают, что коррозионная стойкость композитных покрытий значительно улучшилось.
Композитное покрытие состоит из органических полимеров и неорганических добавок.Полимеры действуют как матрица и удерживают неорганические добавки. Полимеры на водной основе используются из-за их популярности в составах покрытий, включая акрил (Singh et al., 2017), полиуретан (PU) (Alagi et al., 2017), алкид (Pathan and Ahmad, 2013), эпоксидная смола (Cao et al., 2015), полиэстер (Kumar et al., 2017) и их комбинации из-за их дополнительных характеристик.
Водоразбавляемые органо-неорганические гибридные покрытия станут тенденцией развития в будущем (Boubakri et al., 2010; Хуанг и др., 2012). Однако из-за добавления неорганических добавок некоторые свойства (например, прозрачность и т. д.) композиционных покрытий явно снижаются, а применение покрытий ограничивается в некоторых специальных областях, требующих высокой прозрачности и демонстрирующих естественные цвета подложка, покрытая покрытиями. Поэтому необходимы исследования и разработка антикоррозионного покрытия без неорганических добавок.
Среди различных полимеров на водной основе, используемых в покрытиях, полиуретан известен своей превосходной долговечностью и устойчивостью, главным образом, к химическому и термическому разложению, ультрафиолетовому (УФ) излучению, царапинам и гидрофобности (Boubakri et al., 2010; Хуанг и др., 2012 г.; Ма и др., 2013; Мохаммад и Хан, 2015 г.; Каусар, 2016).
Эпоксидные смолы, благодаря своим превосходным химическим свойствам, коррозионной стойкости, выдающимся адгезионным свойствам, низкой усадке и низкой цене, широко используются в различных покрытиях. Кроме того, свойства отвержденного эпоксидного покрытия зависят от отвердителя и процесса отверждения, и эти свойства можно широко регулировать (Muhammad et al., 2014; Pradhan et al., 2016; Kumar et al., 2017). Однако из-за низкой стойкости эпоксидных смол на открытом воздухе все более широкое применение находят акриловые и полиуретановые гибриды.
При воздействии агрессивных сред стабильность металла или сплава зависит от защитных свойств образующихся покрытий поверхности. Химический состав, электропроводность, адгезия, растворимость, гигроскопичность и морфологические характеристики определяют способность пленки работать в качестве антикоррозионного барьера (Stratmant et al., 1983). Если полиуретановые и эпоксидные сегменты синтезированы в молекуле полимера, свойства (то есть химический состав, адгезия, гигроскопичность и морфологические характеристики) смолы могут регулироваться в широких пределах.Следовательно, коррозионная стойкость полимера может быть улучшена.
В ходе этого исследования была приготовлена и охарактеризована водоразбавляемая эмульсия эпоксидной смолы, модифицированной полиуретаном (WPUME), которая показала хорошие свойства коррозионной стойкости.
Материалы и методы
Материалы
Эпоксидная смола (E-44) была приобретена у компании Lanxing Advanced Material Co. (Уси, Китай). Изофорондиизоцианат (IPDI), диметилолмасляная кислота (DMBA), триэтиламин (TEA), ацетон, бутанон и полиэтиленгликоль 2000 (PEG-2000) были приобретены у Kelong Co.(Чэнду, Китай). Катализатор с оловоорганическим (т.е. дилаурат дибутилолова) в качестве основного активного ингредиента, названный DY-20, был продуктом Deyin Chemical Co. (Шанхай, Китай). Отвердитель на водной основе с модифицированным первичным амином в качестве основного активного ингредиента, названный GCA 02, был приобретен у BASF Co. Активный водородный эквивалент GC 02 составляет 320. Все материалы были аналитической чистоты, кроме эпоксидной смолы, отвердителя и ДЯ-20. ИФДИ, ДМБА и ПЭГ-2000 высушивали в вакуумной печи (100°С) не менее 5 ч перед экспериментом, а остальные материалы наносили без дополнительной обработки.
Приготовление модифицированной полиуретаном эпоксидной эмульсии
Эмульсия эпоксидной смолы, модифицированная полиуретаном, была синтезирована реакцией с использованием ИФДИ, ПЭГ, ДМБА, эпоксидной смолы и ТЭА. В четырехгорлой круглодонной колбе растворяли 5 г ДМБА в 10 г ацетона, колбу снабжали термометром, мешалкой, вводом сухого азота, холодильником и нагревательной рубашкой. Затем медленно добавляли 15 г ИФДИ и 5 г ацетона при умеренном перемешивании (300 об/мин) и смеси давали реагировать при 70°С до тех пор, пока не было достигнуто теоретическое содержание NCO.Изменение содержания NCO в ходе реакции определяли стандартным методом обратного титрования дибутиламина (David and Staley, 1969). После получения теоретического значения NCO реагент нагревали до 90°С, добавляли раствор (т.е. 41,8 г эпоксидной смолы, 37,1 г ПЭГ-2000, 0,3 г DY-20 и 40 г ацетона) и перемешивали при 300 об/мин в течение 2,5 ч при поддержании температуры 90°С. Затем реагент охлаждали до 40°С, медленно добавляли 3,5 г ТЭА и перемешивали в течение 30 мин, поддерживая температуру на уровне 40°С.По окончании реакции в колбу добавляли 120 г деионизированной воды при быстром перемешивании (800 об/мин) при комнатной температуре в течение 15 мин.
Наконец, ацетон удаляли в вакууме, чтобы получить эмульсию смолы WPUME. Молекула WPUME содержала гидрофильные группы (т. е. карбоксилатную группу и эфирную связь) и эпоксидную группу, поэтому она могла самоэмульгироваться (т. е. в зависимости от карбоксильной группы и эфирной связи) в воде с образованием стабильной эмульсии. Эмульсия отверждалась до стабильной пленки в зависимости от реакции между эпоксидной группой и аминогруппой в GC 02.Схема процесса приготовления ВЭУМЭ показана на схеме 1, а основные функциональные группы обведены кружком.
Схема 1 . Процесс приготовления молекулы WPUME. (A) Реакция между IPDI и DMBA. (B) Реакция между форполимером, эпоксидной смолой и ПЭГ-2000. (C) Взаимодействие карбоновой кислоты и ТЭА.
Подготовка отвержденной и нетронутой пленки WPUME
Около 100 г эмульсии WPUME хорошо смешали с 7.5 г отвердителя (например, GCA 02), и смесь была отлита на несколько листов белой жести размером 8 × 15 см. Процесс отверждения осуществляли при 120°С в течение 15 минут, а затем при 140°С в течение 15 минут для формирования пленки. Другая поверхность листа белой жести была отлита для формирования дополнительной литой пленки. Спиральным микрометром измеряли толщину полученных пленок 15–25 мкм. Реакция отверждения произошла между эпоксидной группой в молекуле WPUME и аминогруппой в GC 02, и реакция показана на схеме 2.
Схема 2 .Реакция на отверждение между WPUME и отвердителем GC 02.
При приготовлении исходной пленки в эмульсию не добавлялся отвердитель, а все остальные процедуры были такими же, как и при приготовлении отвержденной пленки.
Водонепроницаемость
Испытание на водостойкость характеризовалось скоростью водопоглощения и определялось методом взвешивания следующим образом (Ma et al., 2012a). Образцы отвержденной пленки WPUME были разрезаны на кусочки размером 3 см × 3 см и высушены в вакуумной печи при 60°C в течение 24 часов для определения их сухой массы (W d ). Затем пленку погружали в дистиллированную воду на 72 ч, после чего стирали с поверхности воду кусочком фильтровальной бумаги для определения ее массы (W t ). Затем по формуле (1) рассчитывали степень водопоглощения (вес.%).
Стабильность эмульсии
Стабильность при хранении
Образец эмульсии заливали в закрытую стеклянную бутылку объемом 50 мл и помещали в печь на 20 ч при 50 ± 2°С. Затем бутылку достали из печи и поместили при комнатной температуре (т.е., 23 ± 2°С) в течение 3 ч. Если эмульсия не расслаивалась, стабильность была хорошей.
Устойчивость к замораживанию и оттаиванию
Образец эмульсии замерзал при -10°C и помещался при комнатной температуре (т.е. 23 ± 2°C) на некоторое время до оттаивания замороженной эмульсии. Если образец не расслаивался, процесс циклов замораживания-оттаивания продолжался до тех пор, пока не было проведено пять циклов для завершения теста на устойчивость к замораживанию-оттаиванию.
Стабильность при центрифугировании
Образец эмульсии центрифугировали при 5000 об/мин в течение 5 мин на центрифуге (TGK-16, Xiangyi Co., Китай). Если эмульсия не расслаивалась, стабильность была хорошей.
Характеристика
FTIR
Инфракрасные спектры с преобразованием Фурье (FTIR) исходного и отвержденного образца пленки были записаны соответственно в диапазоне 400–4000 см -1 с использованием FTIR-спектрометра (VERTEX 70, BRUKER Co., Германия) на диске KBr при температуре разрешение 4 см -1 для 32 сканирований.
Твердое содержимое
Образец эмульсии весом 2 г был точно взвешен, чтобы получить вес W 1 , а затем эмульсия была высушена до постоянного веса, чтобы получить вес W 2 , и содержание твердого вещества (sc %) было вычисляется по формуле (2).
sc(%)=W1-W2W1×100 (2)Размер частиц и дисперсия эмульсии
Для определения размера и дисперсии частиц использовали оборудование для лазерного рассеяния (Autosizer, Melvern Co. , UK). Образец сначала разбавляли дистиллированной водой до 0,5%, а затем обрабатывали ультразвуковой волной для гомогенизации эмульсии.
Микроскопическое наблюдение
Микроскопическое исследование проводили на просвечивающем электронном микроскопе (TEM, JEM-200CX, Japan Electronics Co., Япония) работающих на 120 кВ. Чтобы увидеть морфологию, первоначальную пленку смывали со слюдяных подложек в дистиллированную воду и собирали на сетках ПЭМ.
Термогравиметрический анализ
Термогравиметрический анализ (ТГА) проводили на термоанализаторе (STA 449 F3, NETZSCH Co., Германия). Прибор ТГА калибровали оксалатом кальция от 30 до 500°С при скорости нагрева 10°С/мин в статической атмосфере азота.
Электрохимические измерения
Электрохимические измерения отвержденных и исходных пленок WPUME на жести (покрытие было отполировано наждачной бумагой перед нанесением пленки) проводили с использованием потенциостата ParStat 2273 (Ametec, Berwyn, PA, USA). Применялась классическая трехэлектродная система. Образцы, насыщенный каломельный электрод (НКЭ) и платиновая пластина, использовались в качестве рабочего электрода, электрода сравнения и вспомогательного электрода соответственно. Кривые поляризации были получены на площади 1 см 2 при постоянной скорости сканирования напряжения 0,5 мВ с -1 после начальной задержки 300 с. Испытание на погружение проводили согласно GB 10124-88 Китая (GB 10124-88, 2008). Электрохимические измерения проводились в растворе NaCl 3.5%.
Испытание соляным туманом
Испытание на коррозию в соляном тумане YW/R-150 (Тяньцзинь, Китай) проводили на листах белой жести с отвержденным образцом WPUME для моделирования коррозии в окружающей среде в соответствии со стандартом ASTM B117-09 (испытание на воздействие естественного солевого тумана).
Тест на гибкость
Эмульсию WPUME отверждали на белой жести, а гибкость образцов тестировали в соответствии со стандартом ASTM 4145-2010 (гибкость покрытия).
Результаты и обсуждение
Химическая характеристика
Исследование с помощью ИК-Фурье-спектроскопии было проведено для структурного сравнения между отвержденными и исходными пленками, которые были приготовлены с помощью эмульсии WPUME (рис. 1).В целом, не было существенной структурной разницы между спектрами отвержденной и исходной пленки.
Рисунок 1 . Инфракрасные спектры с преобразованием Фурье исходной и отвержденной пленки, приготовленной с помощью эмульсии WPUME.
Спектр FTIR для исходной пленки показал полосу поглощения при 3406 см -1 и пики поглощения при 1718 и 1250 см -1 , соответствующие характеристическому поглощению NH, C = O и CO в -NH- COO- соответственно.Не было обнаружено пика поглощения при 2270 см -1 (т.е. пик поглощения -NCO), что означает, что -NCO почти полностью реагирует с -ОН в реагенте. Анализ этих спектров показывает пики поглощения при 1400 и 1107 см -1 , которые можно отнести к характерному поглощению -ОН в первичной спиртовой и эфирной связи соответственно. Это означает, что ПЭГ индуцируется в сегменте полимерной цепи, и остается некоторое количество первичного спирта. Результаты характеристического пика при 955 см -1 относятся к поглощению -СООН, что означает, что ДМБА реагирует с другими материалами, и -СООН индуцируется в сегменте полимерной цепи.Гидрофильные группы (например, эфирная связь и карбоксильная группа) в молекуле WPUME обеспечивают хорошую устойчивость к эмульсии. Характерные пики поглощения эпоксидной группы при 913 и 830 см -1 легко обнаруживаются в исходном образце пленки, что означает, что эпоксидная группа сохраняется и позже может привести к реакции отверждения. Эти спектры ИК-Фурье показывают, что реакция синтеза ДМБА, ИФДИ, ПЭГ и эпоксидной смолы для синтеза ВПМЭ может происходить в соответствии со схемой 1.
Что касается спектра отвержденного образца пленки на рис. 1, пик поглощения эпоксидной группы, первичного гидроксила и -COOH при 913, 1400 и 955 см -1 соответственно исчезает, и появляется новое поглощение банка третичной аминогруппы на 1,125 см найдено -1 , что означает отвердитель (т. например, модифицированный амин) может реагировать с кислородной группой, а эпоксидная группа может реагировать с активным амином, так что может образовываться аминогруппа. Исчезновение эпоксидной группы, первичного гидроксила и -COOH означает, что реакция отверждения проходит тщательно, и отвержденная пленка может обладать хорошими свойствами коррозионной стойкости, низкой скоростью водопоглощения и хорошей термостойкостью; поэтому свойства хорошо согласуются с результатами более поздних исследований.
Твердое содержимое
Содержание твердого вещества в эмульсии, приготовленной обычным способом, составляло 44.5%, что хорошо соответствует теоретическому значению (т.е. 46%). Разница может быть связана с улетучиванием материалов в реакции.
Водонепроницаемость
Все прозрачные образцы исходных и отвержденных пленок были погружены в дистиллированную воду для определения их водонепроницаемости. Прозрачная нетронутая пленка WPUME становилась белой, а затем непрозрачной после того, как ее погружали в дистиллированную воду примерно на 30 минут при комнатной температуре, и она постепенно распадалась на мелкие кусочки в течение примерно 2 часов. Однако отвержденная пленка ВПМЭ не претерпела видимых изменений даже после погружения ее в дистиллированную воду на 72 ч при комнатной температуре. Средняя скорость водопоглощения составила 2,8%, что было рассчитано по формуле (1). Низкий показатель водопоглощения свидетельствует о том, что отвержденная пленка не чувствительна к воде и обладает хорошей водостойкостью.
Размер частиц и дисперсность эмульсии
На рис. 2 показаны размер частиц и дисперсия WPUME. Видно, что средний размер частиц эмульсии составляет 102.82 нм, и это хорошо согласуется с ПЭМ. Небольшой размер частиц эмульсии приводит к хорошей стабильности эмульсии.
Рисунок 2 . Размер частиц и дисперсность образца эмульсии.
Стабильность
Эмульсия WPUME демонстрирует хорошую стабильность (т.е. стабильность при хранении, стабильность при замораживании и оттаивании, стабильность при центрифугировании). Стабильность можно объяснить введением гидрофильных групп в полимерную цепь ВПМЭ и малым размером частиц эмульсии.
Микроскопическое наблюдение
Типичные ПЭМ-изображения частиц эмульсии ВЭМЭ представлены на рис. 3. Установлено, что частицы имеют правильную сферическую форму диаметром 100–200 нм и имеют некоторые регулярные границы. Морфология частиц представляет собой приблизительную структуру ядро-оболочка, в которой гидрофильные группы (т.е. карбоксильная группа и эфирная связь) составляют оболочку, а гидрофобный компонент составляет ядро. Инкапсулированный гидрофильной группой исходный гидрофобный сегмент полимерной цепи диспергирован в воде.Структура ядро-оболочка становится более заметной, когда частицы увеличиваются до больших размеров, как показано на рисунке 3b.
Рисунок 3 . ПЭМ-изображения образцов эмульсии с разным увеличением (т.е. 2500× в a и 5000× в b ).
Термогравиметрический анализ
Результаты ТГА исходных и отвержденных образцов пленки WPUME показаны на рисунке 4. Температуры соответствуют потере веса 5, 10, 20, 50 и 80%, которые перечислены в таблице 1.
Рисунок 4 . ТГА отвердевает исходные и отвержденные пленки WPUME.
Таблица 1 . Данные о тепловых потерях для образцов WPUME.
Основная потеря массы образцов обусловлена термическим разложением сегмента молекулы полимера. При добавлении отвердителя отвержденный образец пленки WPUME демонстрирует лучшую термостойкость, чем нетронутый образец. Для типичных образцов температура, соответствующая 5%-ной потере веса исходной и отвержденной пленки, составляет 270 и 335°С соответственно, что на 65°С выше для образца отвержденной пленки, чем исходного.Отверждение и образование поперечных связей между полимерными цепями ограничивают свободное движение полимеров (Charles and Carraher, 2007), поэтому отвержденная пленка WPUME демонстрирует лучшую термостойкость. Лучшее термическое сопротивление указывает на то, что полимерные цепи образца WPUME сшиты и эффективно отверждены. Отвержденная пленка WPUME может обеспечить относительно более высокие свойства коррозионной стойкости, что подтверждается в следующем разделе.
Электрохимические измерения
Кривые поляризации отвержденных и исходных пленок на полированной белой жести показаны на рисунке 5.На рисунке 5 видно, что скорость выделения водорода на катодной стороне и скорость растворения металла на анодной стороне значительно уменьшаются, когда отвержденная пленка наносится на подложку по сравнению с исходной пленкой. Кроме того, анодные стороны двух кривых также различны. Анодная сторона образца с нетронутой пленкой гораздо более гладкая, чем у отвержденного. На кривой отвержденного пленочного образца плотность тока коррозии (J) увеличивается значительно медленнее с ростом анодного потенциала в области пассивной тенденции.Плотность тока коррозии образца, покрытого отвержденной пленкой, составляет 0,002551 мкА·см -2 , что значительно ниже, чем у образца, покрытого исходной пленкой (1,905 мкА·см -2 ). Результат показывает, что белая жесть с отвержденной пленкой на ней может значительно улучшить коррозионную стойкость подложки по сравнению с исходной.
Рисунок 5 . Поляризационные кривые отвержденных и исходных пленок, нанесенных на полированные белые жести.
Испытание соляным туманом
На рис. 6 показаны фотографии образца WPUME, отвержденного на листах белой жести после разного времени выдержки (0, 30, 60 и 65 дней) в камере с нейтральным солевым туманом соответственно.
Рисунок 6 . Образцы подвергали испытанию на коррозию в солевом тумане через 0, 30, 60 и 65 дней.
До испытаний в солевом тумане коррозии не наблюдается. Изображения на рисунке 6 после 30, 60 и 65 дней воздействия показывают наличие коррозионной активности. Вблизи царапин на образцах наблюдается желтая ржавчина и вздутие покрытия, что свидетельствует о коррозионном поражении. Однако на изображении образца после 30 дней воздействия не видно образования пузырей, и нет признаков очевидной локализованной коррозии.Вблизи царапин образца после 60 и 65 сут выдержки наблюдаются блистеры покрытия диаметром около 1 мм и более 1 мм, что свидетельствует о хороших антикоррозионных характеристиках ВЭМЭ покрытия, полученного в ходе исследования. Тем не менее, некоторые предыдущие покрытия на водной основе могут выдерживать испытание в нейтральном солевом тумане около 480 часов (Wang et al., 2014), 720 часов (Li et al., 2018), 600 часов (Wang N. et al., 2016) и 288 ч (Zhang et al., 2019) и т. д. до появления локальной коррозии, что намного короче, чем у образцов, приготовленных в этом исследовании.
Тест на гибкость
Гибкость подготовленного покрытия изгибается до диаметра 2 мм, что является наивысшей гибкостью по ASTM 4145-2010.
Выводы
Эмульсия WPUME была успешно приготовлена с помощью реакции эпоксидной смолы (E-44), IPDI, DMBA, оловоорганического катализатора и PEG-2000, и отвердитель для образования коррозионно-стойкого покрытия смог отвердить эмульсию. Покрытие обладает хорошей гибкостью (т.е. может изгибаться при диаметре 2 мм) и свойствами коррозионной стойкости (т.е., может выдержать испытание на коррозию в солевом тумане в течение примерно 60 дней на листах белой жести). Покрытие имеет множество потенциальных применений в некоторых специальных областях, требующих высокой гибкости и коррозионной стойкости.
Доступность данных
Необработанные данные, подтверждающие выводы этой рукописи, будут предоставлены авторами без неоправданных оговорок любому квалифицированному исследователю.
Вклад авторов
Все перечисленные авторы внесли существенный, непосредственный и интеллектуальный вклад в работу и одобрили ее для публикации.
Финансирование
Работа выполнена при финансовой поддержке Сычуаньской научно-технической программы (№ 2019JDTD0024 и № 2019ZHCG0048), военного и гражданского проекта интеграции провинции Сычуань (№ zyf-2018-089), Ибиньской научно-технической программы (№ 2018YG05 и № 2017YG02), проект Chunhui Министерства образования Китая (№ Z2017066), Научно-исследовательский фонд Департамента образования провинции Сычуань, Китай (№ 18ZA0445) и программа ученых Сихуа Университета Сихуа.
Заявление о конфликте интересов
JM работал в компании North Sichuan Nitrocellular Co., Ltd.
Остальные авторы заявляют, что исследование проводилось при отсутствии каких-либо коммерческих или финансовых отношений, которые могли бы быть истолкованы как потенциальный конфликт интересов.
Каталожные номера
Абдолахи, Э., Ибрагим, З., и Хашим, С. (2014). Применение экологически чистых покрытий для подавления микробной коррозии (MIC) стали: обзор. Полим. Ред. 54, 702–745. дои: 10.1080/15583724.2014.946188
Полнотекстовая перекрестная ссылка | Академия Google
Ай, Л., Лю, Ю., Чжан, X., Оуян, X., и Ге, З. (2014). Упрощенный и безтемплатный метод получения политиофеновых микросфер и их диспергирования для водоразбавляемых антикоррозионных покрытий. Синтез. Встретились. 191, 41–46. doi: 10.1016/j.synthmet.2014.02.004
Полнотекстовая перекрестная ссылка | Академия Google
Алаги П., Горпаде Р., Choi, Y., Patil, U., Kim, I., Baik, J., et al. (2017). Полиолы на основе диоксида углерода как устойчивое сырье термопластичного полиуретана для антикоррозионного покрытия металлов. ACS Sustain. хим. англ. 5, 3871–3881. doi: 10.1021/acssuschemeng.6b03046
Полнотекстовая перекрестная ссылка | Академия Google
Бубакри, А. , Гермази, Н., Эллеуч, К., и Айеди, Х. (2010). Исследование УФ-старения термопластичного полиуретанового материала. Мат. науч. англ. А 527, 1649–1654.doi: 10.1016/j.msea.2010.01.014
Полнотекстовая перекрестная ссылка | Академия Google
Цао, М., Ван, Х., Цай, Р., Ге, К., Цзян, С., Чжай, Л., и др. (2015). Приготовление и свойства эпоксидно-модифицированного тунгового масла изоляционного лака на водной основе. Дж. Заявл. Полим. науч. 132:42755. doi: 10.1002/прил.42755
Полнотекстовая перекрестная ссылка | Академия Google
Чарльз, Э., и Карраер, Дж. (2007). Seymour/Carraher’s Polymer Chemistry . 7-е изд. Нью-Йорк, штат Нью-Йорк: Марсель Деккер Пресс.
Академия Google
Чик, Дж., Стил, А., Байер, И., и Лот, Э. (2013). Устойчивость к подводному насыщению и электролитическая функциональность для супергидрофобных нанокомпозитов. Коллоидный полимер. науч. 291, 2013–2016 гг. doi: 10.1007/s00396-013-2933-x
Полнотекстовая перекрестная ссылка | Академия Google
Chen, X. , Yuan, J., Huang, J., Ren, K., Liu, Y., Lu, S., et al. (2014). Крупномасштабное производство супергидрофобных покрытий из полиуретана/нано-Al2O3 методом суспензионного газопламенного напыления для защиты от коррозии. Заяв. Серф. науч. 311, 864–869. doi: 10.1016/j.apsusc.2014.05.186
Полнотекстовая перекрестная ссылка | Академия Google
Дас С., Пандей П., Моханти С. и Наяк С. (2017). Взгляд на полиуретан и нанокомпозиты на основе касторового масла: последние тенденции и развитие. Полим. Пласт. Технол. 56, 1556–1585. дои: 10.1080/03602559.2017.1280685
Полнотекстовая перекрестная ссылка | Академия Google
Дэвид, Д. Дж., и Стейли, Х. Б. (1969). «High Polymer Series», в Analytical Chemistry of Polyurethans , Vol.16 (Нью-Йорк, штат Нью-Йорк: Wiley Interscience Press, 45–46.
). Дефлориан Ф., Росси С. и Федель М. (2011). Алюминиевые компоненты для морского применения защищены от коррозии циклами нанесения органических покрытий с низким воздействием на окружающую среду. Коррос. англ. науч. Технол. 46, 237–244. дои: 10.1179/147842209X12489567719545
Полнотекстовая перекрестная ссылка | Академия Google
Дхок, С., и Ханна, А. (2009). Изучение электрохимического поведения алкидных покрытий на водной основе, модифицированных нано-ZnO. Дж. Заявл. Полим. науч. 113, 2232–2237. doi: 10.1002/прил.30276
Полнотекстовая перекрестная ссылка | Академия Google
ГБ 10124-88 (2008 г.). Стандартная практика лабораторных испытаний металлов на иммерсионную коррозию. Пекин: Управление стандартизации Китайской Народной Республики.
Хао Ю., Лю Ф. и Хан Э. (2012). Механические и барьерные свойства композиционных покрытий на основе эпоксидной смолы/ультракоротких стеклянных волокон. Дж. Матер. науч. Технол. 28, 1077–1084.doi: 10.1016/S1005-0302(12)60176-5
Полнотекстовая перекрестная ссылка | Академия Google
Хуанг, Т., Ван, Ю., Се, К., и Лин, Дж. (2012). Дисперсия гибридов фосфазен-глина на молекулярном уровне в полиуретане и синергетическое влияние на термостойкость и устойчивость к ультрафиолетовому излучению. Полимер 53, 4060–4068. doi: 10.1016/j.polymer.2012.07.049
Полнотекстовая перекрестная ссылка | Академия Google
Какаи, М., Данаи, И., и Заарей, Д. (2013). Исследование защиты от коррозии неорганическими антикоррозионными покрытиями, содержащими слюдистый оксид железа и цинковую пыль. Коррос. англ. науч. Технол. 48, 194–198. дои: 10.1179/1743278212Y.0000000060
Полнотекстовая перекрестная ссылка | Академия Google
Каусар, А. (2016). Композитные пленки полиамид/фуллерен с полиуретановым покрытием на водной основе: механические, термические и воспламеняемые свойства. Междунар. Дж. Полим. Анальный. Характер. 21, 275–285. дои: 10.1080/1023666X.2016.1147729
Полнотекстовая перекрестная ссылка | Академия Google
Каусар А., Рафик И., Анвар З. и Мухаммед Б.(2016). Перспективы композита эпоксид/оксид графена: важные особенности и технические применения. Полим. Пласт. Технол. 55, 704–722. дои: 10.1080/03602559. 2015.1098700
Полнотекстовая перекрестная ссылка | Академия Google
Хадемян М., Эйсазаде Х., Шакери А. и Горбани М. (2015). Влияние эмульсионного нанокомпозита HPC-PANI/SiO 2 в поливинилацетате на антикоррозионные покрытия. Полим. Пласт. Технол. 54, 1051–1056. дои: 10.1080/03602559.2014.986801
Полнотекстовая перекрестная ссылка | Академия Google
Хорсанд С., Карбаси М., Сайедан Ф., Эшагян М. и Разави М. (2018). Разработка электроосаждаемых нанокомпозитных покрытий Ni-Fe (Ti, W) C. Прибой. англ. 34, 433–439. дои: 10.1080/02670844.2017.1370880
Полнотекстовая перекрестная ссылка | Академия Google
Кумар С., Кришнан С., Самал С., Моханти С. и Наяк С. (2017). Итаконовая кислота, используемая в качестве универсального строительного блока для синтеза смол и полиэфиров на основе возобновляемых ресурсов для будущих перспектив: обзор. Полим. Междунар. 66, 1349–1363. doi: 10.1002/pi.5399
Полнотекстовая перекрестная ссылка | Академия Google
Ли, Дж. , Ли, X., Чжу, К., Ван, Х., и Фей, Г. (2018). Влияние фосфорилированного оксида графена на антикоррозионные свойства водоразбавляемых акрилатно-эпоксидных покрытий. Дж. Макромоль. науч. А 55, 649–657. дои: 10.1080/10601325.2018.1504611
Полнотекстовая перекрестная ссылка | Академия Google
Лян Ю., Лю Ф., Не М., Чжао С., Линь Дж.и Хан, Э. (2013). Влияние концентратов нано-Al на коррозионную стойкость эпоксидных покрытий. Дж. Матер. науч. Технол. 29, 353–358. doi: 10.1016/j.jmst.2013.01.014
Полнотекстовая перекрестная ссылка | Академия Google
Лю, С., Гу, Л., Чжао, Х., Чен, Дж., и Ю, Х. (2016). Коррозионная стойкость эпоксидных покрытий на водной основе, армированных графеном. Дж. Матер. науч. Технол. 32, 425–431. doi: 10.1016/j.jmst.2015.12.017
Полнотекстовая перекрестная ссылка | Академия Google
млн лет назад, с., Сюй Л., Сюй В. и Чжан Г. (2013). Разлагаемый полиуретан для защиты от биологического обрастания на море. Дж. Матер. хим. Б 1, 3099–3106. дои: 10.1039/c3tb20454e
Полнотекстовая перекрестная ссылка | Академия Google
Ма С., Сонг Г. и Фэн Н. (2012a). Получение и характеристика самоэмульгированной нитроцеллюлозы на водной основе. Углевод. Полим. 89, 36–40. doi: 10.1016/j.carbpol.2012.02.029
Реферат PubMed | Полный текст перекрестной ссылки | Академия Google
Ма, С., Сонг Г., Фэн Н. и Чжао П. (2012b). Защита от коррозии низкоуглеродистой стали нановолокнистыми покрытиями на основе полианилина. Дж. Заявл. Полим. науч. 125, 1601–1605. doi: 10.1002/прил.35643
Полнотекстовая перекрестная ссылка | Академия Google
Миттал, В. (2014). Функциональные полимерные нанокомпозиты с графеном: обзор. Макромоль. Матер. англ. 299, 906–931. doi: 10.1002/mame.201300394
Полнотекстовая перекрестная ссылка | Академия Google
Мохаммад М. и Хан Д.(2015). Композит на водной основе полиуретан/масляная летучая зола: новый экологически безопасный материал покрытия. J. Прилипатели. науч. Технол. 29, 2709–2718. дои: 10.1080/01694243.2015.1087252
Полнотекстовая перекрестная ссылка | Академия Google
Монтесинос, Р., Рейносо, Р., Альварес, Ф., и Васкес, К. (2015). Оценка новых водоразбавляемых покрытий, полученных из композитных латексных частиц и армированных нанотрубками TiO 2 . Полим. Пласт. Технол. 54, 730–740.дои: 10.1080/03602559.2014.974273
Полнотекстовая перекрестная ссылка | Академия Google
Мухаммед, Р., Мохаммад, Д., и Саидатул, С. (2014). Разработка полимеров на основе растительных масел. Дж. Заявл. Полим. науч. 131, 1–13. doi: 10.1002/прил.40787
Полнотекстовая перекрестная ссылка | Академия Google
Патан С. и Ахмад С. (2013 г.). Алкид на водной основе, модифицированный s-триазиновым кольцом: синтез, характеристика, антибактериальные и электрохимические исследования коррозии. ACS Sustain.хим. англ. 1, 1246–1257. doi: 10.1021/sc4001077
Полнотекстовая перекрестная ссылка | Академия Google
Прадхан С. , Пандей П., Моханти С. и Наяк С. (2016). Взгляд на химию эпоксидной смолы и ее отверждение для нанесения покрытий: подробное исследование и перспективы на будущее. Полим. Пласт. Технол. 55, 862–877. дои: 10.1080/03602559.2015.1103269
Полнотекстовая перекрестная ссылка | Академия Google
Цю С., Ли В., Чжэн В., Чжао Х. и Ван Л.(2017). Синергический эффект интеркалированного полипирролом графена для усиления защиты от коррозии водного покрытия в 3,5% растворе NaCl. Приложение ACS Матер. Интерфейсы 9, 34294–34304. doi: 10.1021/acsami.7b08325
Реферат PubMed | Полный текст перекрестной ссылки | Академия Google
Рахман, М. (2017). Улучшение антимикробных и барьерных свойств водоразбавляемых полиуретанов, содержащих наночастицы гидроксиапатит-серебро. J. Прилипатели. науч. Технол. 31, 613–626.дои: 10.1080/01694243.2016.1228744
Полнотекстовая перекрестная ссылка | Академия Google
Рахман, О., Кашиф, М., и Ахмад, С. (2015). Наноферритные дисперсные эпоксидно-акрилатные покрытия на водной основе: антикоррозионные нанокомпозитные покрытия. Прог. Орг. Пальто. 80, 77–86. doi: 10.1016/j.porgcoat.2014.11.023
Полнотекстовая перекрестная ссылка | Академия Google
Расул К., Насралла Г., Юнес Н., Панди Р., Рашид П. и Махмуд К. (2018). «Зеленые» наночастицы хитозана, связанные ZnO, для эффективного ингибирования сульфатредуцирующих бактерий в закачиваемой морской воде. ACS Sustain. хим. англ. 6, 3896–3906. doi: 10.1021/acssuschemeng.7b04248
Полнотекстовая перекрестная ссылка | Академия Google
Шахабади, С., Конг, Дж., и Лу, X. (2017). Только водный, зеленый путь к самовосстанавливающимся, устойчивым к ультрафиолетовому излучению и электропроводящим нанокомпозитным покрытиям из полиуретана/графена/лигнина. ACS Sustain. хим. англ. 5, 3148–3157. doi: 10.1021/acssuschemeng.6b02941
Полнотекстовая перекрестная ссылка | Академия Google
Сингх, А. , Алам С. и Рани Н. (2017). Приготовление и характеристика водоразбавляемого акрило-полиуретанового покрытия на оцинкованной стали. Пер. Инст. Встретились. Заканчивать. 95, 165–172. дои: 10.1080/00202967.2017.1237759
Полнотекстовая перекрестная ссылка | Академия Google
Stratmant, M., Bohnenkamp, K., and Engel, HJ (1983). Электрохимическое исследование фазовых переходов в слоях ржавчины. Коррос. науч. 23, 969–985. дои: 10.1016/0010-938X(83)-0
Полнотекстовая перекрестная ссылка | Академия Google
Сулейман Р., Khaled, M., Wang, H., Smith, T., Gittens, J., Akid, R., et al. (2014). Сравнение выбранных систем золь-гелевых покрытий, легированных ингибиторами, для защиты низкоуглеродистой стали. Коррос. англ. науч. Технол. 49, 189–196. дои: 10.1179/1743278213Y.0000000113
Полнотекстовая перекрестная ссылка | Академия Google
Ван Н., Фу В., Сунь М., Чжан Дж. и Фанг К. (2016). Влияние разноструктурных частиц TiO 2 на антикоррозионные свойства водоразбавляемых эпоксидных покрытий. Коррос.англ. науч. Технол. 51, 365–372. дои: 10.1080/1478422X.2015.1117267
Полнотекстовая перекрестная ссылка | Академия Google
Ван, Н., Ву, Ю., Ченг, К., и Чжан, Дж. (2014). Исследование антикоррозионных свойств полианилин-мезопористого композита МС-41 в новом эпоксидном покрытии на водной основе. Матер. Коррос. 65, 968–976. doi: 10.1002/maco.201307458
Полнотекстовая перекрестная ссылка | Академия Google
Ван, X., Ван, Дж., Ли, К., и Ли, С. (2013). Синтез и характеристика водоразбавляемых эпоксидно-акриловых антикоррозионных покрытий. Дж. Макромоль. науч. В 52, 751–761. дои: 10.1080/00222348.2012.730351
Полнотекстовая перекрестная ссылка | Академия Google
Ван З., Хань Э., Лю Ф., Цянь З. и Чжу Л. (2014). Эпоксидные нанопокрытия на водной основе, модифицированные наноэмульсиями и наночастицами. Дж. Матер. науч. Технол. 30, 1036–1042. doi: 10.1016/j.jmst.2014.01.004
Полнотекстовая перекрестная ссылка | Академия Google
Йылмаз О. , Каресоджа М., Адигузель К., Зенгин Г. и Тенху Х. (2014).Нанокомпозиты на основе сшитого полиакрилового латекса/наночастиц серебра для водоразбавляемых высокоэффективных антибактериальных покрытий. Дж. Заявл. Полим. науч. А 52, 1435–1447. doi: 10.1002/pol.27130
Полнотекстовая перекрестная ссылка | Академия Google
Чжан, Дж., Ли, Ю., Ху, К., Хуанг, В., и Су, Л. (2019). Антикоррозионные свойства покрытий полиуретан/поли(о-толуидин)–ZnO на водной основе в растворе NaCl. J. Прилипатели. науч. Технол. 33, 1047–1065. дои: 10.1080/01694243.2018.1529881
Полнотекстовая перекрестная ссылка | Академия Google
Чжан К., Хуанг К., Фанг К. и Лу К. (2017). Синтез самоэмульгируемого эпоксидного отвердителя на водной основе на основе глицидилтретного эфира карбоновой кислоты и характеристики его отверждения. Дж. Заявл. Полим. науч. 134:44246. doi: 10.1002/прил.44246
Полнотекстовая перекрестная ссылка | Академия Google
Чжу, К. , Ли, X., Ван, Х., Ли, Дж., и Фей, Г. (2017). Электрохимические и антикоррозионные свойства латексных композитов на основе алкидной смолы, модифицированной графеном/акриловой смолой, углеродистой стали. Дж. Заявл. Полим. науч. 134:44445. doi: 10.1002/прил.44445
Полнотекстовая перекрестная ссылка | Академия Google
Чжо, Ю., Лю, Дж., Ли, К., Цю, Б., и Син, Г. (2016). Получение и характеристика нанокомпозитов WPU/CNT/GO. Интегр. Ферроэлектр. 171, 52–58. дои: 10.1080/10584587.2016.1171662
Полнотекстовая перекрестная ссылка | Академия Google
Как выбрать правильный коррозионностойкий материал
Как выбрать правильный коррозионностойкий материал
Выбор материала является важной частью любого производственного процесса.Выбор правильного материала очень важен, потому что материал определяет химические и механические свойства изготавливаемого компонента, может существенно повлиять на его долговечность и обеспечить правильное функционирование детали. Коррозионно-стойкие материалы играют важную роль в производстве из-за их свойств материала и отсутствия реакции на суровые условия окружающей среды и химические вещества.
Например, многие аэрокосмические компоненты изготавливаются с использованием титана, вольфрама и углеродного волокна, поскольку эти материалы очень прочные, но при этом легкие и гибкие.К сожалению, эти материалы могут реагировать друг с другом и со временем вызывать гальваническую коррозию, локальную коррозию, когда происходит обмен ионами между материалами. Здесь коррозионно-стойкие материалы сохраняют целостность деталей в одной из самых строго регулируемых отраслей промышленности в мире.
С экологической точки зрения, экологически чистые солнечные и ветряные источники энергии уязвимы для суровых условий, а коррозионно-стойкие материалы помогают защитить их важные компоненты от повреждений с течением времени.Это помогает производителям безопасно создавать компоненты для альтернативных источников энергии и способствовать более устойчивой экономике. Для инженеров, стремящихся защитить свои детали от коррозионно-активных сред, таких как кислоты и соли, или от ультрафиолетового излучения, вот лучшие коррозионно-стойкие материалы.
Примеры коррозионностойких материалов
1. Нержавеющая сталь
Сплавы из нержавеющей сталиизвестны своей коррозионной стойкостью, пластичностью и высокой прочностью.Коррозионностойкие свойства нержавеющих сталей напрямую связаны с содержанием в них хрома и никеля — большее количество этих элементов коррелирует с повышенной стойкостью.
Большинство сплавов нержавеющей стали, представленных сегодня на рынке, содержат не менее 18% хрома. Когда хром окисляется, он образует защитный слой оксида хрома на поверхности металлической детали, который одновременно предотвращает коррозию и предотвращает попадание кислорода в нижележащую сталь.
Нержавеющая сталь имеет широкий спектр применения: от кухонных приборов, таких как кастрюли и сковородки, до деталей автомобилей и хирургических имплантатов.
Поскольку этот материал имеет высокую температуру плавления и может выдерживать высокое давление, он также хорошо подходит для строительства, машиностроения и производства контейнеров для хранения. Нержавеющие стали 304, 430 и 316 являются наиболее часто используемыми марками нержавеющей стали, а марка 316 используется в суровых морских условиях.
Однако долговечность и высокая коррозионная стойкость нержавеющей стали связаны с высокой ценой, что делает их непомерно дорогими для некоторых производителей.Кроме того, со сплавами нержавеющей стали может быть трудно работать, особенно при сварке, из-за их высокой температуры плавления.
2. Алюминий
Алюминиевые сплавы нетоксичны, на 100% пригодны для вторичной переработки, имеют высокое отношение прочности к весу, обладают высокой тепло- и электропроводностью и легко поддаются механической обработке. Кроме того, алюминий уникален, потому что это один из немногих материалов, которые обладают естественной коррозионной стойкостью.
Этот материал практически не содержит железа, поэтому не ржавеет, хотя и может окисляться.Когда алюминиевый сплав подвергается воздействию воды и окисляется, процесс, называемый самопассивацией, на поверхности детали образуется пленка оксида алюминия, которая защищает ее от коррозии. Алюминий 5052-х42 более устойчив к коррозии, чем другие разновидности алюминия, и образует яркую гладкую поверхность.
Этот процесс окисления также можно точно контролировать с помощью процесса, называемого анодированием. Кроме того, алюминий уникален тем, что это один из немногих инновационных материалов для аддитивного производства, обладающих естественной коррозионной стойкостью.Анодирование – это недорогая контролируемая отделка, которая широко используется. Этот процесс также позволяет добавлять к детали цвет, что позволяет выполнять дальнейшую настройку для различных вариантов использования.
Алюминий часто используется в аэрокосмической промышленности, автомобильных кузовных панелях, приложениях, чувствительных к соленой воде, и в других ситуациях, когда требуется материал с высокими эксплуатационными характеристиками. Производителям следует рассмотреть возможность использования алюминия, если им нужен доступный по цене устойчивый к коррозии материал, помня при этом, что изготовление алюминия может быть грязным и хлопотным в работе.
3. Мягкие металлы
Мягкие металлы или красные металлы включают устойчивые к коррозии материалы, такие как медь и ее сплавы, латунь и бронза. Медь пластична, пластична и является отличным проводником тепла и электричества. Эти металлы могут обеспечить коррозионную стойкость на протяжении всего жизненного цикла данного компонента. . Медь не подвергается коррозии со временем; когда он окисляется, он образует зеленый внешний слой, называемый патиной, который защищает деталь от дальнейшей коррозии.
Медь часто является предпочтительным коррозионно-стойким материалом для производителей полупроводниковой промышленности, и она чаще всего встречается в проводах и кабелях. Он используется для изготовления печатных плат, электромагнитов, теплообменников и электродвигателей.
Медь также играет ключевую роль в производстве деталей для систем возобновляемой энергии. Поскольку медь является отличным проводником тепла и электричества, системы, работающие на основе меди, передают энергию более эффективно и с меньшим воздействием на окружающую среду.
4. Полипропилен
Металлы — не единственные доступные коррозионно-стойкие материалы. Полипропилен, один из самых популярных пластиков в обрабатывающей промышленности и особенно распространенный пластик для производства автомобильных деталей. Это также один из самых коррозионностойких пластиков.
Эта термопластичная полимерная смола получила прозвище «сталь пластмассовой промышленности» за ее прочность, способность выдерживать высокие уровни физического давления и устойчивость к широкому спектру агрессивных элементов, таких как масло, растворители, вода, бактерии и т. д. .Полипропилен высокой плотности (HDPE) обладает более высокой прочностью на растяжение и повышенным диапазоном рабочих температур.
Однако высокая воспламеняемость и высокий тепловой коэффициент этого материала ограничивают его пригодность для применения при высоких температурах. Кроме того, важно отметить, что полипропилен подвержен окислению, УФ-разложению и воздействию некоторых хлорированных растворителей.
5. Политетрафторэтилен (ПТФЭ)
PTFE, обычно известный под торговой маркой Teflon, представляет собой химико- и коррозионно-стойкий технический термопласт с самым низким коэффициентом трения среди всех известных твердых материалов. ПТФЭ является гидрофобным, то есть он не впитывает воду и обладает хорошей электроизоляционной способностью как в жаркой, так и во влажной среде.
ПТФЭ наиболее известен своими коммерческими и медицинскими применениями — созданием антипригарных покрытий для кастрюль и сковородок и обеспечением антифрикционного покрытия для медицинских и промышленных применений. Благодаря низкому трению этот материал используется для изготовления подшипников, шестерен, пластин скольжения, уплотнений и других мелких деталей, имеющих решающее значение для промышленного применения. ПТФЭ также часто используется в композитах из углеродного волокна и стекловолокна.
Тем не менее, PTFE имеет свои ограничения. Этот материал трудно соединять, он чувствителен к ползучести, истиранию и излучению. Кроме того, пары, выделяемые ПТФЭ, могут быть токсичными в закрытых помещениях. Прежде чем принимать какие-либо важные решения о материалах, лучше проконсультироваться с опытным партнером-производителем.
Получить консультацию специалиста по выбору материала
Коррозионная стойкость является чрезвычайно желательным свойством, особенно в полупроводниковой, энергетической, аэрокосмической и автомобильной промышленности. Существует широкий выбор коррозионно-стойких материалов, в том числе пять вышеупомянутых, и группы разработчиков должны проявлять должную осмотрительность при выборе материалов, чтобы убедиться, что они соответствуют уникальным требованиям проекта.
Опытный партнер по цифровому производству, такой как Fast Radius, может помочь командам разработчиков ответить на самые сложные вопросы в процессе разработки продукта. Вы должны использовать металл или пластик? Полипропилен так же хорош, как нержавеющая сталь? Наша команда имеет многолетний опыт в области аддитивного и традиционного производства, и мы поможем каждому клиенту выбрать устойчивый к коррозии материал, который защитит его детали в течение длительного времени. Свяжитесь с нами сегодня чтобы начать.
Для получения дополнительной информации о материалах в аддитивном производстве и о том, как выбрать лучший материал для вашего следующего проекта, ознакомьтесь с соответствующими статьями блога в учебном центре Fast Radius.
Как драгоценные металлы могут предотвратить коррозию
Драгоценные металлы хорошо известны своей эстетической привлекательностью, но это гораздо больше, чем их внешний вид. Драгоценные металлы, к которым относятся золото, серебро и платина, широко используются в технике и промышленности. В то время как драгоценные металлы обладают привлекательным блеском, который делает их визуально привлекательными, они также обладают большой практической ценностью — лишь некоторые из свойств семейства драгоценных металлов — это химическая стабильность, электропроводность и пластичность. Однако одной из наиболее примечательных особенностей драгоценных металлов является их способность противостоять коррозии.
В компании Sharretts Plating Company мы можем порекомендовать вам правильные драгоценные металлы, которые помогут предотвратить коррозию в вашем следующем проекте. Читайте дальше, чтобы узнать больше о коррозии во всех ее формах и использовании драгоценных металлов для создания устойчивых к коррозии продуктов.
Что такое драгоценные металлы? Драгоценные металлы чаще всего определяются как встречающиеся в природе металлы, которые относительно редки и менее химически активны, чем другие металлы. Пластичные и блестящие драгоценные металлы часто используются в эстетических целях и обычно используются в качестве слитков. Однако драгоценные металлы также высоко ценятся за их химическую стабильность, электропроводность и коррозионную стойкость.
Семейство драгоценных металлов состоит из трех основных подгрупп:
- Золото и сплавы золота: Золото является чрезвычайно инертным драгоценным металлом и не окисляется в обычных условиях окружающей среды.Чрезвычайно мягкий и пластичный металл, чистое золото часто используется в качестве футеровки или гальванического покрытия в электронике. Золото также может быть сплавлено с другими металлами для повышения его прочности, что позволяет использовать его в отдельно стоящих компонентах в аэрокосмической и электронной промышленности.
- Серебро и сплавы серебра: Серебро имеет самую высокую тепло- и электропроводность среди всех металлов, а также легко сплавляется с другими металлами, создавая термостабильные сплавы для промышленного применения.Поскольку оно дешевле других драгоценных металлов, серебро является популярной альтернативой для тех, кто стремится снизить затраты.
Серебряное покрытие чаще всего встречается в автомобильной, электронной и электротехнической промышленности.
- Металлы и сплавы платины: Металлы платиновой группы чрезвычайно редки и включают платину, палладий, родий, рутений, иридий и осмий, которые встречаются в природе в одной и той же руде. Эти серебристо-белые металлы чрезвычайно инертны и стабильны, с некоторыми различиями в пластичности и прочности.Все они сохраняют свою стабильность при высоких температурах, что делает их идеальными для различных применений в автомобильной и аэрокосмической промышленности.
Любой из этих металлов может быть нанесен гальванопокрытием на поверхность, чтобы придать изделию некоторые из их свойств. В SPC мы предлагаем гальванопокрытие для стоек и бочек для драгоценных металлов.
Что вызывает коррозию? Коррозия, образованная от латинского слова «corrodere», означающего «разгрызать на куски», в общих чертах определяется как ухудшение качества материала с течением времени. Применительно к металлам коррозия определяется как электрохимическая реакция между металлом и окружающей средой, в результате которой металл переходит из высокоэнергетического состояния в низкоэнергетическое. Обычно это происходит в результате атмосферной коррозии в результате процесса, называемого окислением, когда металл вступает в реакцию с кислородом и водой в атмосфере. Например, железо естественным образом соединяется с кислородом и водой с образованием гидратированных оксидов железа или «ржавчины». Воздействие кислоты или высоких уровней электролитов также может привести к химическим реакциям, ведущим к коррозии, но атмосферное окисление является наиболее распространенной формой коррозии.На защиту от атмосферной коррозии приходится примерно 50 % всех затрат на защиту от коррозии.
Дополнительные факторы, влияющие на скорость коррозии, в том числе:
- Температура: Скорость химических реакций имеет тенденцию увеличиваться с ростом температуры, а это означает, что высокотемпературные материалы в коррозионных средах имеют тенденцию к более быстрой коррозии.
- Обработка поверхности: Обработка поверхности материала определяет серьезность коррозии — шероховатые или грязные поверхности, а также небольшие щели могут задерживать коррозионные вещества, вызывая их более быстрое и агрессивное действие.
- Электричество: Воздействие электрического тока может привести к более быстрой коррозии материала с течением времени из-за потери электронов из материала.
Покрытие соответствующими материалами, включая драгоценные металлы, может помочь уменьшить влияние вышеуказанных факторов на скорость коррозии, эффективно защищая материал от коррозии.
Как появляется коррозия?В зависимости от конкретной причины коррозии в сочетании с перечисленными выше факторами коррозия может проявляться в одной из восьми основных форм:
- Равномерное воздействие: Наиболее распространенная форма коррозии, равномерное воздействие характеризуется равномерным распространением коррозии по поверхности материала.
Хотя на эту форму коррозии приходится наибольшее объемное разрушение металла, это одна из самых простых форм коррозии, с которой можно справиться с помощью соответствующих покрытий.
- Гальваническая коррозия: Когда два разнородных металла находятся в физическом или электрическом контакте, их близость может создавать поток электронов, в результате чего менее устойчивый к коррозии металл подвергается коррозии с большей скоростью, а более устойчивый к коррозии металл испытывает более низкую скорость коррозии.
- Щелевая коррозия: Коррозия часто возникает быстрее в щелях в материале, где коррозионное вещество задерживается в течение длительного периода времени.Щелевая коррозия обычно возникает в местах соединений, отверстий и точек заклепок.
- Точечная коррозия: Точечная коррозия — это локальная форма коррозии, которая приводит к образованию отверстий в материале, и является одной из наиболее разрушительных форм коррозии, снижающей целостность конструкции при незначительной потере веса конструкции.
Это одна из самых сложных форм коррозии, и она сравнительно непредсказуема.
- Межкристаллитная коррозия: Плохолегированные материалы могут при определенных условиях образовывать межкристаллитную коррозию, что приводит к коррозионным воздействиям на границы зерен, снижающим прочность сплава.
- Селективное выщелачивание: В этой форме коррозии коррозия функционально удаляет один элемент из твердого сплава, чаще всего цинк из латунных сплавов.
- Эрозионная коррозия: Эрозионная коррозия — это увеличение скорости коррозии, вызванное движением между поверхностью и агрессивной жидкостью. Это движение приводит к образованию канавок, волн и отверстий на поверхности материала, обычно появляющихся в направлении движения.
- Коррозионное растрескивание под напряжением: Растягивающее напряжение снижает количество энергии, необходимой для того, чтобы коррозия закрепилась в материале, а при наличии растягивающего напряжения и коррозионной среды могут образовываться коррозионные трещины под напряжением.
Обычно они выглядят как мелкие трещины на неповрежденной металлической поверхности.
Изменения конструкции изделия, включая добавление антикоррозионного покрытия, могут эффективно предотвращать большинство видов коррозии, перечисленных выше.
Влияние коррозии и почему важно ее предотвращатьКоррозия может иметь серьезные последствия для функциональности и безопасности продуктов и со временем может привести к увеличению затрат. Некоторые из наиболее частых последствий коррозии включают:
- Потеря эффективности: Коррозия может снизить эффективность продукта, уменьшая количество функционального материала до такой степени, что продукт больше не может обеспечивать стандартную функциональность.Кроме того, машины с проржавевшим оборудованием, возможно, придется останавливать для ремонта, что снижает общую эффективность компании.
- Соображения безопасности: Коррозия может снизить структурную или функциональную целостность материала до такой степени, что он разрушается или выходит из строя, травмируя операторов и пользователей.
Кроме того, отверстия, вызванные коррозией, могут привести к утечке токсичных материалов в окружающую среду, что может нанести вред здоровью или окружающей среде.
- Внешний вид: Ржавчина и коррозия непривлекательны с эстетической точки зрения и могут заставить зрителей меньше думать о продукте или выразить обеспокоенность по поводу его безопасности.
- Затраты на ремонт: Проржавевшее оборудование и материалы необходимо модифицировать, отремонтировать или заменить, но это не единственные детали, на которые может повлиять коррозия. Части и оборудование, прилегающие к корродированному материалу, могут быть повреждены в результате косвенной коррозии, что еще больше увеличивает затраты на ремонт и сокращает расчетный срок службы.
Все вышеперечисленные факторы могут снизить прибыль компании за счет увеличения затрат и сокращения продаж. Покрытие может помочь предотвратить коррозию, тем самым снижая эти затраты — в то время как дополнительные затраты, связанные с антикоррозионным покрытием, могут привести к увеличению первоначальных затрат, они меркнут по сравнению с затратами, понесенными коррозионным повреждением.
Почти все металлы подвержены коррозии в обычных условиях окружающей среды. Исключение составляют драгоценные металлы.
Драгоценные металлы отличаются не только своей высокой ценностью — драгоценные металлы также известны своей стабильностью. В гальваническом ряду металлы сортируются по иерархической шкале от благородных до активных. Активные металлы имеют тенденцию больше взаимодействовать с окружающей средой, тогда как благородные металлы более стабильны.Металлы в семействе драгоценных металлов находятся на благородном конце этой шкалы, а это означает, что они более устойчивы к взаимодействию с другими химическими веществами и, следовательно, более устойчивы к коррозии.
Хотя драгоценные металлы относятся к благородным, термины «драгоценный металл» и «благородный металл» не являются синонимами. Определение благородного металла зависит от области исследования — например, в атомной физике к благородным металлам относятся только медь, серебро и золото, поскольку они имеют полностью заполненные d-подоболочки, что делает их более стабильными. Однако в самом широком определении обе группы включают золото, серебро, платину, палладий, родий, рутений, иридий и осмий, а благородные металлы также включают ртуть, рений и медь. Эти последние три элемента не обладают коррозионной стойкостью, поэтому важно четко различать драгоценные и благородные металлы.
Одним из лучших способов предотвращения коррозии является покрытие драгоценными металлами и их сплавами.Тем не менее, важно выбрать правильный тип драгоценного металла для вашего применения и выбрать метод гальванического покрытия и толщину, соответствующие вашим целям. При принятии решения важно учитывать качества, которые вы ищете для своего покрытия, а также применение.
Ниже приведены наиболее важные факторы, которые следует учитывать при выборе антикоррозионного покрытия:
1. Материал покрытия Покрытия из драгоценных металлов изолируют подложку от окружающей среды, создавая гладкую защитную поверхность, предотвращающую попадание воды и кислорода на основной материал. Поскольку драгоценные металлы немного различаются по своим электрохимическим и физическим свойствам, некоторые из них лучше подходят для определенных применений, чем другие. В этом списке драгоценных металлов представлены сильные стороны каждого элемента, а также его наиболее распространенные области применения:
- Золото: Золото обладает тепло- и электропроводностью и обладает высокой стабильностью в качестве коррозионностойкого покрытия. Он часто используется в электронике, но имеет тенденцию быть более дорогим, чем другие антикоррозионные покрытия.
- Серебро: Серебро является менее дорогим материалом для покрытия по сравнению с другими драгоценными металлами и обладает превосходной электротермической проводимостью. Он используется в производстве электроэнергии и автомобильных приложениях.
- Платина: Платина имеет высокую температуру плавления, но термически стабильна, что делает ее идеальной для применения при высоких температурах.
Типичные области применения включают электронику, электроэнергетику и аэрокосмическую промышленность.
- Родий: Родий является наиболее электротермически проводящим из платиновой группы и сохраняет высокую отражательную способность, что делает его идеальным материалом для зеркал в высокотемпературных применениях.Родий чаще всего используется в аэрокосмической и электронной промышленности.
- Рутений: Рутений часто используется в качестве легирующего агента, особенно из-за его кислотостойких свойств. Электронная промышленность в основном использует рутений для производства электрических контактов.
- Палладий: Палладий — популярная альтернатива золоту. В сплаве с никелем он менее хрупкий и лучше поддается пайке. В сплаве с кобальтом он более прочен и электропроводен.В целом этот металл и его сплавы часто используются в электронной промышленности для изготовления контактов на печатных платах.
Компания Sharretts Plating может помочь вам оценить ваш проект и определить лучший материал для покрытия для вашего применения.
Эффективность любого типа покрытия сильно зависит от того, насколько хорошо подложка подготовлена для покрытия. Если подложка покрыта ямками, кратерами, загрязнена или иным образом повреждена, покрытие либо образует поверхностные дефекты, либо не будет должным образом сцепляться с поверхностью подложки.SPC может помочь вам оценить качество вашего субстрата и внести предложения по его улучшению. Мы также используем тщательный процесс подготовки к гальваническому покрытию, чтобы гарантировать, что конечный продукт имеет максимально возможное качество.
3. Толщина покрытия Толщина покрытия из драгоценного металла оказывает значительное влияние на прочность и долговечность конечного продукта. Более тонкие отложения могут не полностью покрывать подложку, позволяя коррозионным молекулам пробить поверхность и атаковать подложку под ней.С другой стороны, слишком толстые покрытия могут быть неоправданно дорогими и негативно влиять на функциональность продукта. Специалисты SPC могут обсудить наилучший диапазон толщины покрытия для вашего применения и даже могут предложить дополнительные слои неблагородных материалов для повышения эффективности конечного продукта.
Если вы рассматриваете покрытие драгоценными металлами в качестве варианта для вашего следующего проекта, чтобы предотвратить коррозию и снизить затраты на ремонт, компания Sharretts Plating может помочь вам начать работу.Обладая более чем восьмидесятилетним опытом работы в отрасли, мы знаем отрасль вдоль и поперек и усовершенствовали наши методы покрытия драгоценными металлами, чтобы каждый раз обеспечивать высочайшее качество.
Наши специалисты по металлизации могут встретиться с представителями вашего бизнеса, чтобы определить ваши потребности и предложить вам наилучшие варианты покрытия. Мы можем встретиться с вами для консультации на месте, чтобы обсудить ваш проект от начала до конца, ответить на любые ваши вопросы и помочь вам изучить все ваши варианты.
Готовы начать? Получите бесплатное предложение без обязательств сегодня! Пожалуйста, заполните эту форму запроса расценок или позвоните нам по телефону (717) 767-6702, чтобы узнать больше о покрытии драгоценными металлами и о том, какую пользу оно может принести вашему бизнесу.
Свойства металла: коррозионная стойкость
Коррозия является распространенной проблемой, поражающей поверхность большинства металлических деталей. В то время как коррозия часто влияет только на внешний вид металлической детали, сильная коррозия может повлиять на производительность и даже привести к отказу оборудования. Коррозия является настолько широко распространенной проблемой, что глобальные затраты на коррозию оцениваются в 2,5 триллиона долларов в год, согласно исследованию, проведенному Национальной ассоциацией инженеров-коррозионистов (NACE).
Здесь мы рассмотрим многие способы проявления коррозии в материале, а также методы, которые производители используют для предотвращения воздействия коррозии на рабочие характеристики деталей.
Коррозия и коррозионная стойкость
Коррозия — это естественный процесс, который происходит, когда химическая реакция с окружающей средой постепенно разрушает поверхность материала. Если не остановить коррозию, она будет распространяться глубже в материал, пока не повлияет на целостность самой детали. Коррозионная стойкость , с другой стороны, это способность материала противостоять коррозионным силам. Различные материалы способны противостоять коррозии с разной скоростью
Формы коррозии
По данным Национальной ассоциации инженеров по коррозии (NACE), коррозия любого металла проявляется одним из восьми способов.
1. Равномерное воздействие
Равномерное воздействие является наиболее распространенным типом коррозии. Это происходит посредством электрохимической реакции и распределяется равномерно по всей поверхности металла.В результате корродированный материал становится тоньше и со временем может выйти из строя.
2. Гальваническая коррозия, или коррозия двух металлов
Гальваническая коррозия, или коррозия двух металлов, относится к коррозионным повреждениям, возникающим при соединении двух разнородных материалов и их контакте с электрическим током в проводящем растворе. Типичным примером являются подводные трубопроводы, изготовленные путем сварки стальных и медных труб. Что запускает эту реакцию, так это несходство электродных потенциалов между двумя разными металлами, что в конечном итоге приводит к тому, что один металл корродирует заметно быстрее, чем другой
3.Межкристаллитная коррозия
Межкристаллитная коррозия включает в себя локальную коррозию исключительно по границам пораженного металла, а не внутри. Этот тип коррозии может затронуть даже аустенитные нержавеющие стали , которые, как правило, устойчивы к коррозии, если они не обработаны должным образом и подвергаются воздействию агрессивных сред.
4. Щелевая коррозия
Как следует из названия, щелевая коррозия чаще всего возникает в щелях, а также под полимерными покрытиями и клеями.Механизм этого типа коррозионного воздействия основан на разнице между концентрациями кислорода внутри и снаружи щели или области покрытия.
5. Селективное выщелачивание
Селективное выщелачивание представляет собой удаление одного из металлов, входящих в состав твердого сплава, в результате процессов коррозии. Децинкификация (селективное удаление цинка из латунных сплавов) и деникелирование (селективное удаление никеля из труб из медно-никелевого сплава) являются примерами селективного выщелачивания. Однако этот процесс может происходить и со сплавами, содержащими алюминий, железо, хром или другие металлы.
6. Эрозионная коррозия
Эрозионная коррозия возникает, когда оксиды и гидроксиды металлов с корродированной металлической поверхности удаляются жидкостями, обнажая и воздействуя на свежий некорродированный металл. Этот тип коррозии обычно наблюдается в металлических трубах, где движущиеся жидкости переносят коррозию на не подвергшийся воздействию металл.
7. Коррозионное растрескивание под напряжением
Коррозионное растрескивание под напряжением относится к растрескиванию, вызванному напряжением и воздействием агрессивной среды.В этих ситуациях напряжения или условий окружающей среды самих по себе недостаточно, чтобы вызвать коррозию, но они работают вместе, вызывая растрескивание.
8. Точечная коррозия
Точечная коррозия – это еще одна разрушительная форма коррозии, которая приводит к образованию локальных отверстий в металле. Небольшие отверстия бывает трудно обнаружить, даже если они становятся глубже и угрожают целостности детали.
Предотвращение коррозии металлических деталей
Коррозия является серьезной проблемой для клиентов, занимающихся литьем, поэтому предприятия по литью металлов (и другие производители металлов) используют различные методы для производства деталей, устойчивых к коррозии.
- Правильное планирование
Хотя ни один металл не является полностью устойчивым к коррозии во всех средах, тщательное планирование на этапе проектирования продукта обеспечивает максимальную коррозионную стойкость каждой детали в условиях эксплуатации. Помимо используемого материала, конструкции изделий могут также включать дренажные каналы и элементы, улучшающие поток воздуха. Дизайнеры также знают, что щели, зазоры и глухие отверстия могут привести к коррозии. - Легирование
Легирование включает смешивание металлических элементов вместе, часто для улучшения таких качеств, как прочность, пластичность и коррозионная стойкость.Например, сочетание железа с не менее чем 12-13% хрома позволяет получить нержавеющую сталь, широко используемый коррозионно-стойкий сплав. - Анодирование
Анодирование означает окисление поверхности металла с целью получения защитного оксидного слоя. Анодирование может добавить цвет и улучшить эстетику и обычно используется для алюминиевых изделий. - Термическая обработка
Надлежащая термическая обработка отливок играет большую роль в том, как материал будет вести себя в определенных условиях, включая его коррозионную стойкость.Для большинства аустенитных сплавов нержавеющей стали требуется этап отжига на твердый раствор для растворения любых присутствующих карбидов и предотвращения межкристаллитной коррозии. Термическая обработка после сварки также очень важна для предотвращения аналогичной десенсибилизации нержавеющих сплавов и межкристаллитного разрушения во время эксплуатации. - Азотирование и карбидирование
Азотирование и карбидирование представляют собой виды специальной термической обработки, при которой поверхность металла подвергается воздействию химической среды, образующей защитный слой на поверхности детали.Оба метода в основном используются для упрочнения компонентов, а дополнительным преимуществом является небольшое повышение коррозионной стойкости. - Регулярное техническое обслуживание
Визуальный осмотр является ключом к предотвращению влияния коррозии на работу деталей. Регулярное техническое обслуживание для удаления видимой коррозии может значительно увеличить срок службы деталей в агрессивных средах. - Гальванизация
Гальванизация включает в себя покрытие поверхности металлического предмета слоем цинка. Этот слой цинка действует как расходуемый анод , чтобы помочь предотвратить окислительную коррозию от повреждения исходного металла. - Окраска и порошковое покрытие
Окраска часто является наиболее экономичным способом защиты от коррозии. Краски и порошковые покрытия, часто на основе акрила, нейлона, винила или уретана, образуют защитный барьер между металлом и агрессивными элементами, такими как вода и кислород.
Стойкость металлов к естественной коррозии
Поскольку различные металлические элементы и сплавы подвергаются воздействию агрессивных сред, их внешний вид часто меняется. Красновато-коричневая ржавчина (оксид железа) является одним из наиболее распространенных видимых типов коррозии в материалах на основе железа.Ржавчина также является очень разрушительным типом коррозии и может легко привести к поломке детали, если ее не обслуживать должным образом.
Другие изменения поверхности, хотя и тесно связанные с коррозией, на самом деле служат для защиты некоторых металлов от разрушительной коррозии. Например, потускнение , которое образуется на светлых металлах, таких как серебро, представляет собой самоограничивающийся коррозионный слой. Патина , представляющая собой зеленый слой, покрывающий многие медные предметы, состоит из карбоната меди и защищает эти предметы от дальнейшей коррозии.Точно так же ряд металлов естественным образом образуют оксидные слои при воздействии воздуха или воды. Эти слои включают оксид меди, оксид алюминия и оксид хрома.
Коррозия является неизбежным фактом жизни на протяжении всего производства. При заказе, сборке или производстве литых металлических деталей производители должны учитывать коррозию. Во многих случаях металлурги на литейных предприятиях, таких как Eagle Group, дают рекомендации по идеальному сплаву для каждой детали с учетом функциональной среды детали.
Как предотвратить коррозию | Металлические супермаркеты
Что такое коррозия?
Коррозия – это повреждение материала, вызванное взаимодействием с окружающей средой. Это естественное явление, требующее трех условий: влаги, металлической поверхности и окислителя, известного как акцептор электронов. Процесс коррозии переводит поверхность реактивного металла в более устойчивую форму, а именно в его оксид, гидроксид или сульфид. Распространенной формой коррозии является ржавчина.
Коррозия может иметь различные негативные последствия для металла. Когда металлические конструкции страдают от коррозии, они становятся небезопасными, что может привести к несчастным случаям, например, к обрушению. Даже незначительная коррозия требует ремонта и обслуживания. Фактически, ежегодные прямые затраты на металлическую коррозию во всем мире составляют примерно 2,2 триллиона долларов США!
Хотя все металлы подвержены коррозии, считается, что 25-30% коррозии можно предотвратить с помощью подходящих методов защиты.
Как предотвратить коррозию
Вы можете предотвратить коррозию, правильно выбрав:
- Металл Тип
- Защитное покрытие
- Экологические меры
- Жертвенные покрытия
- Ингибиторы коррозии
- Модификация конструкции
Металл Тип
Одним из простых способов предотвращения коррозии является использование устойчивого к коррозии металла, такого как алюминий или нержавеющая сталь.В зависимости от области применения эти металлы могут использоваться для снижения потребности в дополнительной защите от коррозии.
Защитные покрытия
Нанесение лакокрасочного покрытия является экономичным способом предотвращения коррозии. Лакокрасочные покрытия действуют как барьер, предотвращающий передачу электрохимического заряда от коррозионно-активного раствора металлу под ним.
Другой возможностью является нанесение порошкового покрытия. В этом процессе на чистую металлическую поверхность наносится сухой порошок.Затем металл нагревают, в результате чего порошок плавится в гладкую сплошную пленку. Можно использовать ряд различных порошковых композиций, включая акрил, полиэстер, эпоксидную смолу, нейлон и уретан.
Экологические меры
Коррозия вызывается химической реакцией между металлом и газами в окружающей среде. Принимая меры по контролю за окружающей средой, эти нежелательные реакции можно свести к минимуму. Это может быть как простое сокращение воздействия дождя или морской воды, так и более сложные меры, такие как контроль количества серы, хлора или кислорода в окружающей среде.Примером этого может быть обработка воды в водогрейных котлах с помощью умягчителей для регулирования жесткости, щелочности или содержания кислорода.
Жертвенные покрытия
Временное покрытие включает покрытие металла дополнительным типом металла, который с большей вероятностью окисляется; отсюда и термин «жертвенное покрытие».
Существует два основных метода получения расходуемого покрытия: катодная защита и анодная защита.
Катодная защита
Наиболее распространенным примером катодной защиты является покрытие стали из сплава железа цинком, процесс, известный как цинкование.Цинк является более активным металлом, чем сталь, и когда он начинает корродировать, он окисляется, что замедляет коррозию стали. Этот метод известен как катодная защита, потому что он работает, превращая сталь в катод электрохимической ячейки. Катодная защита используется для стальных трубопроводов, несущих воду или топливо, баков водонагревателей, корпусов кораблей и морских нефтяных платформ.
Анодная защита
Анодная защита включает в себя покрытие стали, легированной железом, менее активным металлом, например оловом. Олово не подвергается коррозии, поэтому сталь будет защищена, пока есть оловянное покрытие. Этот метод известен как анодная защита, потому что он делает сталь анодом электрохимической ячейки.
Анодная защита часто применяется к резервуарам для хранения из углеродистой стали, используемым для хранения серной кислоты и 50% каустической соды. В этих условиях катодная защита не подходит из-за очень высоких требований к току.
Ингибиторы коррозии
Ингибиторы коррозии — это химические вещества, которые вступают в реакцию с поверхностью металла или окружающими газами для подавления электрохимических реакций, ведущих к коррозии.Они работают путем нанесения на поверхность металла, где они образуют защитную пленку. Ингибиторы можно наносить в виде раствора или в виде защитного покрытия с использованием методов диспергирования. Ингибиторы коррозии обычно применяются с помощью процесса, известного как пассивация.
Пассивация
При пассивации тонкий слой защитного материала, такого как оксид металла, создает на металле защитный слой, который действует как барьер против коррозии. На формирование этого слоя влияют рН, температура и химический состав окружающей среды.Ярким примером пассивации является Статуя Свободы, где образовалась сине-зеленая патина, которая фактически защищает медь под ней. Ингибиторы коррозии применяются в нефтепереработке, химическом производстве, водоподготовке.
Модификация конструкции
Модификации конструкции могут помочь уменьшить коррозию и повысить долговечность любых существующих защитных антикоррозионных покрытий. В идеале конструкции не должны улавливать пыль и воду, способствовать движению воздуха и избегать открытых щелей.Обеспечение доступности металла для регулярного технического обслуживания также увеличит срок службы.
Металлические супермаркеты
Metal Supermarkets — крупнейший в мире поставщик мелких партий металла с более чем 100 обычными магазинами в США, Канаде и Великобритании. Мы являемся экспертами в области металлов и предоставляем качественное обслуживание клиентов и продукцию с 1985 года.
В супермаркетах металлов мы поставляем широкий ассортимент металлов для различных областей применения.Наш склад включает в себя: мягкую сталь, нержавеющую сталь, алюминий, инструментальную сталь, легированную сталь, латунь, бронзу и медь.
У нас есть широкий ассортимент форм, включая стержни, трубы, листы, пластины и многое другое. И мы можем порезать металл по вашим точным спецификациям.
Посетите один из наших 100+ офисов по всей Северной Америке сегодня.
(PDF) Исследование антикоррозионных свойств различных составов на образцах стандартных металлов
86 Пол.Дж. Хим. Тех., Том. 19, № 4, 2017
11. Чжао Ф., Урбанс М. и Скерлос С.Дж. (2004). Mechanistic
Модель коаксиальной микрофильтрации для полусинтетических
жидких микроэмульсий металлообработки. Дж. Производство. науч. Инженер. 126(3),
435. http://doi.org/10.1115/1.1763187.
12. Шуцзюнь, Гао, Пэн, Джин, Брюс, Браун и др. (2017).
Коррозионное поведение мягкой стали в кислых средах при повышенных температурах.Коррозия. Том. 73. No. 8. pp. 915–926 https://
doi.org/10.5006/2366
13. Айад И., Рия М.А., Тауфик С.М. & Abousehly,
A.M. (2016). Защита углеродистой стали от коррозии
в растворе соляной кислоты некоторыми синтезированными катионными ПАВ
. 52: 339. https://doi.org/10.1134/S2070205116020027
14. Скерлос, С.Дж., Раджагопалан, Н., ДеВор, Р.Э., Капур, С.Г. (2001). Микрофильтрация полиоксиалкиленовых
смазочных присадок к жидкостям для металлообработки с использованием мембран из оксида алюминия
.Дж. Производство. науч. Инженер. 123(4), 692. http://doi.
орг/10.1115/1.1392993.
15. Томас Норрби. (2003). Экологически адаптированные смазочные материалы
– где возможности? Инд Любр. Трибол. 5(6),
268–274. https://doi.org/10.1108/003687
496400.
16. Скерлос С.Дж. (2011). Смазочно-охлаждающие жидкости и их воздействие на окружающую среду. Глава. Энциклоп. Трибол. Спрингер. http://дои.
орг/10.1007/978-0-387-92897-5.
17.Маклин Д., Хейс К., Барнард Т., Халл Т., Парк Ю.Е.
и Скерлос, С.Дж. (2009). Влияние сверхкритического диоксида углерода
на стойкость инструмента при точении спеченной стали
и фрезеровании чугуна с уплотненным графитом. Продолжить. ASME
Интер. Производство. науч. Инженер. Конференция 2009 г. MSEC2009,
, 4–7 октября 2009 г. Уэст-Лафайет. Индиана. США. стр. 43–48.
18. Сингх Б.П., Наяк С., Нанда. К., Бикаш К.Дж., Бхат-
Тачарджи С.и Бесра, Л. (2013). Изготовление коррозионностойкого
армированного графеном композитного покрытия на меди методом электрофоретического осаждения
. Углерод 61, 47–56. DOI: 10.1016/j.
карбон.2013.04.063.
19. Кайюэ Ли., Гуодин Чен, Дэн Лю. (2016). Исследование
влияния параметров смазки на свойства и эффективность смазки зубчатых передач. Инд Любр. Трибол. 68(6). 647–657. https://
doi.org/10.1108/ILT-06-2015-0089
20.Chang, S.C., Rihana, A., Bahrman, S., Gruden, C.L.,
Hijniak, A.I., Skerlos, S.J. и Адрианс, П. (2004). Flow
цитометрическое обнаружение и количественный анализ микобактерий в
жидкостях для металлообработки. Интер. Биодеградация и биоразложение-
54(2–3), 105–112. http://doi.org/10.1016/j.ibiod.2004.03.019
21. Hernández Gayosso, M.J. Nava, N. & Zavala, G. Oli-
vares. (2016). Характеристика и сравнение продуктов коррозии
, возникших в стальных трубопроводах, транспортирующих высокосернистый газ и
сырую нефть.Интер. Дж. Корр. Процесс. Корр. Контроль 51(8), 626–634.
http://dx.doi.org/10.1080/1478422X.2016.1173421.
22. Бханудас Даттатрая Баччхав, Гита, С. Латкар.
Хариджан Багчи. (2014). Трибология волочения смазок для низкоуглеродистой стали
. Инд Любр. Трибол. 66(6), 640–644. https://дои.
орг/10.1108/ИЛТ-10-2012-0105.
23. Насиров Ф.А. (1983). Исследование и разработка процесса
получения низкомолекулярного полибутадия в присутствии
каталитических систем на основе органических дитиопроизводных
никеля (кобальта).Дисс… канд. хим. наук.. Баку. ИПП НАНА 202 с.
24. ASTM C 613-14: «Стандартный метод определения содержания компонентов
композитного препрега методом экстракции по Сокслету».
25. Ван де Воорт, Ф.Р., Седман, Дж. и Пинчук, Д. (2011).
Обзор прогресса и новых разработок в методологии мониторинга состояния смазочных материалов
FTIR. Дж. ASTM междунар. 8(5).
ID: JAI103344Google Scholar.
26. Циммерман, Дж.Б., Хейс, К.Ф. и Скерлос, С.Дж. (2004).
Влияние накопления ионов на стабильность эмульсии и
Характеристики полусинтетических смазочно-охлаждающих жидкостей. Enviro-
чел. науч. Технол, 38(8), 2482–2490. http://doi.org/10.1021/
es0340477
27. Ли Мин Чу, Джав-Рен Лин, Юх-Пин Чанг.