Как сделать нож из подшипника
Для того что бы сделать нож из подшипника придется потрудиться. Если самодельный нож из рессоры можно изготовить путем отпуска, механической обработки металла и последующей закалки, то нож из подшипника можно только сковать.
Дело в том, что обойма подшипника круглая, а распрямить ее на полоску металла можно только с помощью ковки.
Для изготовления ножа своими руками можно использовать не только обойму подшипника, но и шарики или ролики из него.
Подшипниковая сталь очень хорошего качества, ведь подшипники работают в очень жестких условиях и под большой нагрузкой, так что лезвие ножа откованного из подшипника получается с хорошими механическими свойствами. Такое лезвие хорошо держит заточку и не ломается.
Посмотрите видео — изготовление ножа из подшипника методом ковки.
Фактически такой нож из подшипника может выковать любой желающий, в ковке ножей нет никаких секретов.
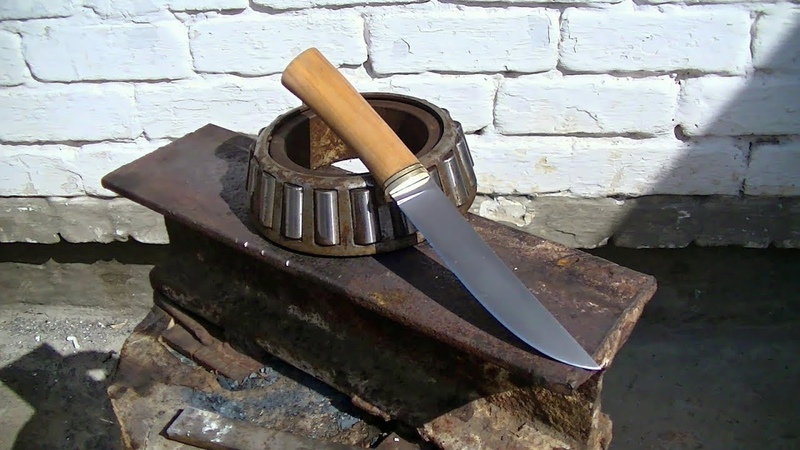
Кстати, хорошо заточенный и правильно закаленный нож из подшипника может резать стекло!
Не верите? Посмотрите видео ниже, в нем рассказывается как отковать самодельную бритву из подшипника. И в конце проводится тест на резку стекла, а так же бритье бороды.
Согласитесь, бритва — это гораздо более «тонкий» инструмент чем обычный самодельный нож. тем не менее — изготовленная с помощью ковки бритва прекрасно бреет и режет стекло!
Особенности изготовления ножа из подшипника
1.Обойма подшипника распиливается болгаркой на заготовки необходимой длины.3. Обдирку делаем перед закалкой на точиле или ленте.
4. Желательно произвести нормализацию — разогрев до 750-770С, затем выдержка 5-7 мин и охлаждение на воздухе. Проводится 2-4 раза.
5. Закалка. Закалка самодельного ножа из подшипника производится при температуре 830С. Определять температуру можно по магниту — прикладываешь к заготовке и как перестало магнититься — пора закаливать.
Можно предварительно ориентироваться по поваренной соли — температура плавления соли 800 градусов. Посыпаем заготовку солью и калим, как соль на клинке начала плавиться, то берется магнит и проверяется достижение температуры закалки.
6. Закалка производится в масле. Температура масла 45-60 градусов. Выдержать в масле надо в течении часа, при этом нельзя болтать заготовку и прислонять ее к стенкам.
7. После закалки надфиль должен скользить по стали. А клинок — царапать стекло.
8. После закалки необходимо произвести отпуск, для этого самодельный нож из подшипника кладется в духовку на 2 часа и греется до температуры 160-200 градусов. Охлаждение производится простым отключением духовки.
Чем толще нож — тем меньше можно ставить температуру. Отпуск уменьшает хрупкость лезвия, но снижает закалку. Более толстый клинок выдерживает нагрузку на излом за счет своих габаритов, так что можно отпускать при меньшей температуре.
9. Заточка самодельного ножа из подшипника производится на алмазных брусках. а шлифовка ведется с помощью алмазной пасты.
Правильно изготовленный нож из подшипника царапает стекло, не тупится и не ломается при изгибающих нагрузках.
Нож из подшипника своими руками. Ковка ножа из подшипника своими руками
Вопрос задает Валерий, Московская область:
Недавно услышал от знакомого, что из подшипника можно изготовить отличный нож. Меня очень заинтересовало это, поскольку люблю все мастерить своими руками. Хотелось бы подробнее узнать об этой технологии.
Предоставляем слово нашему эксперту:
Подшипники изготовляют из стали высокого качества, поскольку они работают в трудных условиях и не теряют своих характеристик при значительных нагрузках. Если выковать из него нож, можно получить отличный инструмент. Он не потеряет остроты в самых трудных условиях эксплуатации.
Для ковки ножа из подшипника необходимо следовать представленной инструкции:
- При помощи болгарки необходимо отрезать заготовку нужной длины, используя обойму подшипника.
Нужно учитывать запас в 1-2 см.
- Полученную заготовку необходимо приварить к прутку арматуры, исполняющей роль рукоятки.
- Ковка осуществляется при достаточно низких температурах, чтобы материал изменился от светло-красного до более темного оттенка.
- Перед закалкой осуществляется обдирка на точиле или при помощи напильника.
- Для улучшения характеристик ножа рекомендуется произвести нормализацию металла. Для этого его разогревают до 750°С, ждут 5 минут и охлаждают на воздухе. Такие манипуляции повторяют 2-4 раза.
- Производится закалка. Чаще всего это осуществляется при температуре 830°С. Для определения подходящего момента для закалки используют магнит. Когда сталь перестала магнититься, можно приступать к данному процессу. Температура плавления поваренной соли составляет 800°С. Поэтому ею посыпают заготовку, чтобы примерно определить момент достижения оптимальных характеристик для закалки.
- Закалка происходит в масле, температура которого достигает 50-60°С.
Заготовку помещают в емкость с подготовленным веществом на 1 час. Все это время ее нельзя шевелить и прислонять к стенкам резервуара. - После закалки проводят отпуск. Нож помещают в духовку при температуре 160-200°С на 2 часа. Для охлаждения просто гасят огонь.
- Для заточки ножа используется алмазные бруски, для шлифовки – алмазная паста. В процессе данной обработки может утратиться до 2 мм толщины заготовки, что вполне нормально.
Если следовать все правильно и в точности следовать инструкции, полученный нож сможет поцарапать стекло. В процессе эксплуатации он не тупится и не разрушается при нагрузках изгибающего характера. Представленным способом легче всего делать нож с накладными рукоятками.
Нож из подшипника делается в достаточно кропотливый способ. Если для изготовления самодельного можно использовать метод отпуска, механическую обработку металла и последующую закалку, то нож из подшипника получится только путем ковки.
Особенность этого процесса состоит в том, что подшипник имеет круглую обойму, а для распрямления ее на металлическую полоску подойдет только лишь один вариант – сковать.
Ковка ножа из подшипника
Распиливать подшипник рекомендуется наискосок – когда будем ковать, носик сможем сформировать в более легкий способ.
Автор использовал сплав Шх15 – это сталь, которая легирована хромом. Перед тем, как приступать к ковке, сплав отжигаем, оставляем в печи или горне, чтобы медленно остыл – примерно 20–60 градусов в час. По отжигу сталь приобретает пластичность, теперь ее ковать удобнее.
Обойму выпрямляем, формируем клинок. Чтобы определить требуемую температуру ковки стали Шх15 – а это в пределах 800…1100°C, стоит использовать пирометр. Но если такового прибора нет, уровень нагрева определяем по цвету каления – где-то от вишнево-красного до темно-желтого.
Когда процесс ковки окончен, делается нормализация, в противном случае в металле останутся напряжения и при лучшем исходе во время закалки клинок поведет, а в худшем – лопнет на морозе, возможно с нанесением травм. Чтобы провести нормализацию, нагреваем клинок до 800…950°C, такую температуру выдерживаем недолго – и на воздух, на ровную поверхность, чтобы остыл.
Дальше можно переходить к слесарной обработке. Черновые спуски делаем путем ковки, остальное – с помощью гриндера или болгарки. Главное – толщину спусков должна быть не меньше 1 мм, в противном случае во время закалки лезвие будет вести.
Теперь – наверное, ключевой момент в изготовлении ножа. Это термическая обработка.
Для закалки медленно нагреваем клинок до 830°C – светло-красного цвета. Для определения нужно температуры можно использовать магнит – если металл больше не магнитится, значит достигнута нижняя температура закалки. После того как при такой температуре соблюдена выдержка 1 минута на каждый мм толщины клинка – охлаждаем в масле. При этом масло должно быть подогрето примерно до 50°C.
Не меньшую важность имеет процесс отпуска металла – можно сделать в духовке, t200°C, продолжительность – полтора часа. Здесь главное, чтобы этого не видела жена =)
Результат – в меру твердый клинок, надфиль можно едва зацепить, при нагрузке пружинит.

Дальше перейдем к рукояти. В качестве материала рукоятки автор взял березовый сувель, отваренный в соленой воде с хвойными опилками.
Сейчас в продаже имеется достаточно большой ассортимент разнообразных ножиков хорошего качества. Однако большой популярностью пользуются ножи ручной ковки. Такие изделия имеют особую энергетику. Ножи своими руками могут изготавливаться по-разному. Самым сложным способом является вариант ручной ковки. Стоит понимать, что ковка дает возможность сделать прочный клинок отменного качества, который сможет прослужить достаточно большое количество времени, не потеряв при этом свои качества.
Нож, выкованный из прочного материала, способен прослужить долгие годы, не сломавшись и не потеряв свои качества.
Для того чтобы ковать нож, понадобится иметь некоторые знания касательно металлов и их свойств. Помимо того, нужно досконально владеть инструментом для ковки. Людям, которые решили сделать данное изделие своими руками впервые, важно ознакомиться с некоторыми рекомендациями.
Как правильно выбирать материал для изготовления ножа?
Рисунок 1. Конструкция кованого ножа.
Чтобы сделать качественный клинок, нужно подобрать подходящую для него сталь. От выбора материала будут зависеть режущие характеристики ножика и его прочность. Для правильного подбора металла важно знать, какие свойства имеет такой материал. Понадобится ориентироваться на 5 главных свойств стали:
- Устойчивость к износу — сопротивление стали изнашиванию при использовании. Данное свойство будет зависеть от твердости материала.
- Твердость — свойство материала, которое указывает на его способность сопротивляться попаданию в нее твердых материалов. Стоит знать, что твердый материал меньше подвергается деформации. Показатель прочности можно измерить по шкале Роквела.
- Прочность — возможность сохранять целостность при воздействии атмосферных сил.
- Пластичность — возможность материала впитывать и распределять кинетическую энергию при ударе и деформации.
- Красностойкость — устойчивость металла к высокой температуре и способность сохранять свойства в процессе нагрева. Минимальная температура ковки стали будет зависеть от устойчивости материала к термической обработке. Рекомендуется выбирать твердые марки, рабочая температура ковки для которых больше 900°С. Стоит знать, что температура плавления данного материала составляет приблизительно 1500°С.
Все данные характеристики связаны между собой. Преобладание одного из них приводит к ухудшению остальных. Каждое свойство материала будет зависеть от содержания в нем легирующих элементов и добавок, к которым можно отнести кремний, вольфрам, молибден и другие.
Рисунок 2. Виды профилей ножа.
Наличие всех легирующих элементов и применение их в необходимой пропорции в процессе изготовления стали, а также знание их свойств позволяет создать сталь для необходимых целей. Каждая из подобных сталей имеет свою маркировку. Стоит отметить, что российские и европейские марки имеют разные обозначения.
К российским производителям, которые достаточно часто применяются в процессе ковки клинков своими руками, можно отнести стали с маркировкой У7-У16, Р6М5, Х12МФ и другие. Из европейских марок можно отметить стали 1095, М-2, А-2 и другие.
Подробное описание марки металла можно найти в «Марочнике стали и сплавов».
Вернуться к оглавлению
Какие инструменты необходимы для ковки ножика своими руками?
Чтобы выполнить ковку клинка, понадобится иметь специальный инструмент кузнеца, однако можно воспользоваться и любительскими инструментами:
- Молот на 4 кг.
- Молоток до 1 кг.
- Тиски.
- Станок для точки.
- Печка.
- Наковальня.
- Аппарат для сварки.
- Болгарка.
- Щипцы кузнеца или обыкновенные пассатижи.
- Разводной ключ.
Инструменты для ковки: молоток, тиски, разводной ключ, щипцы кузнеца, зубило, подбойка.
Следует знать некоторые нюансы касательно печки. Понадобится достичь температуры приблизительно 1000-1200°С, чего сделать в обыкновенной печи не получится. В связи с этим надо будет усовершенствовать печку. Конструкция изготавливается из металла с толстыми стенками, после чего присоединяется труба, в которую будет подаваться воздух из пылесоса. В качестве топлива подойдет уголь.
Перед изготовлением ножа понадобится сделать эскиз. Нож является простым предметом, который состоит из клинка и рукоятки, но данные элементы имеют множество составляющих. На рис. 1 можно увидеть эскиз конструкции со всеми ее составляющими. Существующие виды профилей можно увидеть на рис. 2. После того как будет выбран подходящий профиль, можно будет перейти к созданию эскиза. Профессионалы не всегда используют чертежи, однако новичкам они будут необходимы.
Вернуться к оглавлению
Как сделать кованые ножи из напильника или троса?
Напильник изготавливается из износостойкой стали, в связи с чем достаточно часто из данного инструмента изготавливаются ножики. Такие клинки будут иметь хорошую режущую кромку.
Нож, выкованный из троса, уступает по своим характеристикам другим, но клинок обладает необыкновенно красивым рисунком, напоминающим дамасскую сталь.
Первым делом нужно будет выполнить очистку инструмента от насечек и ржавчины. Данное действие можно сделать, используя болгарку. Если есть необходимость, от напильника надо будет отрезать заготовку нужной длины. После этого изделие приваривается к арматурному пруту и засовывается в печку. Изделие надо нагреть до необходимой температуры, после чего можно будет приступить к раскатке изделия до нужной толщины. Далее делается острие и кромка для резки. Хвостовик ножика из данного инструмента рекомендуется делать под накладную рукоятку.
Трос нужно расколоть до красного цвета, после чего вынуть его из печки и посыпать бурой. После этого трос нужно раскалить до 1000°С, снова вынуть из печки и начать проковывать. Удары наносятся молотком, при этом важно стараться сохранить все волокна вместе.
В конечном итоге может получиться полоса стали, которая состоит из нескольких слоев. Из нее можно будет ковать нож необходимой формы.
Вернуться к оглавлению
Куем нож из сверла сами
Для ковки ножиков достаточно часто используются сверла. Связано это с тем, что данные изделия изготавливаются из стали Р6М5, которая подходит для клинков. Она имеет хороший уровень прочности и проста в заточке.
Следует знать, что сверла больших размеров состоят из рабочей части из стали Р6М5 и хвостовика из обыкновенной стали. Сверла небольших размеров в большинстве случаев изготавливаются из Р6М5.
Нож из напильника обладает отличными режущими свойствами.
Если планируется ковать ножик из сверла больших размеров, нужно сразу определить, где располагается каждый вид стали. Для этого нужно проточить сверло по длине. В местах, где присутствует обыкновенная сталь, будет образовываться большое количество искр. При точке сверла из легированной стали искр будет мало. Данную процедуру понадобится выполнить для того, чтобы определиться, где у ножика будет клинок, а где хвостовик.
Ковка выполняется следующим образом:
Прежде всего разводится огонь в печке, после чего подключается поддув. Далее нужно подождать, когда топливо начнет сильно гореть. После этого сверло помещается в печь. Сделать это нужно при помощи клещей так, чтобы хвостовик располагался вне огня. Если ковка выполняется впервые, достаточно сложно определить с первого раза, нагрелся ли металл до нужной температуры. В связи с этим будет испорчено не одно сверло. Чтобы не испортить большое количество материала, рекомендуется первым делом потренироваться с нагревом и ковкой на арматурных прутьях.
Нужно будет запомнить, какой цвет имел металл и когда его было легко ковать. Стоит учитывать и то, что при солнечном свете даже нагретый до 1000°С металл не будет светлым.
После того как сверло раскалится до температуры больше 1000°С, его понадобится вынуть из печки, после чего закрепить в тисках нижнюю часть хвостовика. После этого надо будет взять разводной ключ, прижать им верхнюю часть сверла и расправить спираль с помощью круговых движений. Все действия понадобится производить быстро, чтобы металл не успевал остывать, иначе сверло сломается. Если выполнить все действия за один подход не получилось, нужно будет повторно нагреть сверло и повторить процесс. В конечном итоге получится сравнительно ровная полоса металла.
На следующем этапе нужно будет выполнить ковку сверла и раскатать металл до нужной толщины. Для этого понадобится нагреть металл до нужной температуры, взять тяжелый молоток, после чего сильными ударами выровнять сталь, придавая необходимую форму. В конечном итоге получится стальная полоса толщиной приблизительно 3-5 мм. В процессе ковки материала надо будет постоянно следить за цветом изделия. Как только появится тусклый цвет, заготовку нужно будет вернуть в горн.
Далее понадобится выковать острие ножика. Стоит знать, что изделию нужно будет придать круглую форму, сохранив при этом нужную толщину конструкции. Ковка должна выполняться так, чтобы в процессе проделывания отверстия слегка оттягивалось лезвие по длине. Бить нужно аккуратно.
Следующим шагом выполняется проковка кромки для резки. Для этого нужно использовать легкий молоток. Металл сдвигается вниз к кромке, при этом начинать нужно со середины лезвия. Режущая кромка должна получиться тонкой, а лезвие должно остаться прямым. Все удары нужно наносить аккуратно. Важно следить за цветом изделия.
Далее выполняется проковка хвостовика. Прежде всего накаливается хвостовик сверла круглой формы, после чего изделие раскатывается сильными ударами молотка. Хвостовик может быть узким или широким. Все будет зависеть от составленного эскиза.
После того как металл остынет, можно будет производить шлифовку. Понадобится снять излишки металла, чтобы сделать ножик ровным и придать ему блеска. После шлифовки изделие может стать на 2 мм тоньше, в результате чего нож будет иметь меньший вес. На данном этапе может быть выполнена заточка и закалка клинка.
Закалка.
Проблема.
Поскольку я делаю ножи в основном из подшипников от автомобилей, по размеру обычно это диаметр сантиметров 10-15, и начинал полным дятлом, после чисто интуитивных попыток возникли следующие проблемы:
После закалки в воде сталь хрупкая настолько, что разлетается как стекло при сильном ударе
Собственно, все. Остальное все меня устраивало. Но мне хотелось, чтобы «не ржавело», «хорошо резало», «держало заточку», «не раскалывалось».
Болометра у меня нет, «все на глазок», и когда я читаю рекомендации «выдержать два часа при температуре 453 градуса» — это не для меня. В конце концов, плюс-минус твердости или вязкости мне фиолетово. Меня вполне устроит «более-менее» приличное качество по перечисленным параметрам.
Поэтому.
Решение проблемы:
1. Отковываю, обязательно соблюдая следующие условия:
При нагреве я лучше недогрею, чем перегрею. Стараюсь не накалять до белого свечения, работаю в диапазоне красного-желтого. Лучше я почаще буду совать-вынимать, чем пережгу.
Внимательно следим за деталью, когда лежит в горне: попытка сэкономить и делать одновременно две детали приводит к тому, что или пережжешь, или что-то испортишь.
Нагрелось до красного яркого с кусками желтого свечения – вынимаем
Периодически пшикаем-брызгаем из бутылочки пластиковой (как на шашлык) – лучше видно температуру, где что нагрето, да и угли экономит
Особенно внимательно, когда есть тонкие детали (лезвие, например) – не пережечь!
2. НИ В КОЕМ СЛУЧАЕ НЕ БИТЬ ПО ХОЛОДНОМУ МЕТАЛЛУ!
Когда куешь, металл пластичен. И по свечению видно, если он начинает остывать. Конечно, хочется за один раз отковать «побольше». Надо бороться с этим искушением.
Как только при ударе молотом (а я все вручную, нет механики) – чувствуешь, что пластичность уменьшается – останавливаемся, греем дальше.
Пояснение: насколько я понял, объясняется все просто. Как только я треснул молотом по подостывшему металлу, возникают микро-трещины, которые плохо «залечиваются» даже хорошим нагревом, и потом по ним все ломается. Вот и все.
3. Собственно, закалка.
Я пробовал в воду. При любых (почти) вариантах – хрупкая сталь получается. Поэтому взял, слил в канистру отработанного машинного (не проблема достать). Читал картинки и про то, какие температуры для каких марок стали… Разбирался в свечениях и цвете металла. Сухой остаток:
Когда форма детали скована – я стараюсь максимально близко к финальной форме, чтобы поменьше точить, — приступаю к закалке
Нагреваю до (в среднем) цвета-свечения между красным и желтым (на глазок) – но для этого есть обоснования теоретические, скажу ниже, — и опускаю ВЕРТИКАЛЬНО ЗА ХВОСТИК кончиком лезвия вниз быстро-быстро в масло. Держу несколько минут, чтобы полностью остыло.
Нагреваю до темно-красного цвета и закаляю еще раз
Если «ведет» нож, что бывает, — просто искривляется он – нагреваю до темно-красного цвета (минимальная пластичность) и подправляю, если надо, закаляю еще раз.
Кладу рядом с углями на поддон, вырубаю горн – пусть остывает все вместе.
Результат – шикарно все, и без заморочек. Могу подвести длинную базу, но такой повтор закалок с понижением верхней температуры нагрева на опыте дает отличный результат в среднем, независимо от взятого подшипника (японских экзотик не пробовал, брать не буду – в основном наш Автоваз, Уралаз, Камаз, Газ, и пр. Совецкие заводы.)
Теперь теория.
Если мы возьмем картинку переходов разных аустентитов в мартенситы и прочие цементиты,
… то обратим внимание, что В СРЕДНЕМ диапазон правильного нагрева выше 850, но ниже 900 градусов. Поэтому нагревать надо примерно до диапазона цветов как на картинке ниже.
Повтор ХУЖЕ не делает, а ЛУЧШЕ делает. Вот и все.
Поскольку подход этот «крестьянский» я его излагаю просто и все.
Русские умельцы ножевого дела, никогда не ищут лёгких путей. Потому что это – для многих хобби и увлечение. Бывает, что из простого занятия, получается настоящий небольшой бизнес. Но в большинстве своём, для людей это всё же, это отдых и отвлечение от повседневной жизни. Каждый человек, определяет свой досуг сам. Любители ковать, довольно часто изготавливают свои изделия из необычных вещей, например: нож из подшипника. Очень интересный и непростой процесс.
Самодельный нож из подшипника.
Плюсы и минусы ножа из подшипника
Многие обыватели скажут, что зачем этим заниматься, когда можно пойти в магазин и прикупить себе парочку замечательных клинков. Но мы же, им не указываем, как проводить своё время. Так что если неинтересно, идём на другой ресурс, а здесь будет статья, содержащая в себе немало полезной информации особенно для новичков. Потому что изложение планируется в пошаговом ракурсе.
Мы уже писали о том, что «идеального ножа» на всё случаи жизни, не существует. И это правда, но стремиться к идеалу нужно всегда. Поэтому попробуем выделить положительные и отрицательные стороны клинка из подшипника. Чтобы знать, что получится в результате правильной обработки металла.
Сталь подшипника изначально предназначена для высоких нагрузок, по этой причине она отличается пластичностью и однородностью при нагреве. А в итоге получается изделие с жёсткостью от 61 до 64 единиц по шкале Роквелла. И главное – высочайшая износостойкость клинка. Единственным минусом можно назвать, хрупкость во время обработки. Очень важно, правильно выполнить закалку, а ковку «на холодную», вообще, исключить.
Как сделать нож из подшипника своими руками
Понятно, что в данном деле без ковки никак не обойтись. Нужно обязательно распрямить обойму изделия. Знатоки таких вещей, разделяются на два лагеря, какую часть лучше выбрать для работы: внутреннюю или внешнюю. Однозначного ответа нет, но многие утверждают, что внутреннее кольцо состоит из лучшей стали. Подкрепляя свои слова, тем, что эта часть несёт на себе большую нагрузку.
Но, как бы там ни было, новичку однозначно без разницы. Для начала нужно, чтобы хоть что-то получилось и не треснуло во время закалки. Для нормальной работы потребуется свой, определённый набор инструментов. Ну и главное – кузница.
Требующиеся материалы и инструменты
У совсем «зелёного» новичка вряд ли есть необходимый инструмент, поэтому им нужно обзавестись. Что-то можно изготовить самостоятельно, а другое только купить. Но опять же, покупной инструмент позволительно заменить аналогичным более простым, но увеличится время изготовления. Если нет в планах, заниматься кузнечным и ножевым делом, покупать что-либо, конечно, бессмысленно, если только мелочи. Материалы потребуются следующие:
- подшипник, желательно в разобранном состоянии;
- деревянный брусок, для изготовления рукояти;
- стержни для заклёпок, лучше из латуни;
- эпоксидный клей или похожий по свойствам заменитель;
- масло или воск для пропитки рукояти;
- малярный скотч, листок бумаги, карандаш, маркер.
Кухонный нож из подшипника.
С материалами не очень сложно и всё доступно. А вот что касаемо инструмента, обратите внимание, как уже говорилось выше, если не найдётся профессионального, пробуйте заменить на более доступные варианты. Их мы также укажем для ясности:
- металлические тиски, зажимы, струбцины;
- УШМ (болгарка) с набором различных дисков;
- горн или муфельную печь, которую можно изготовить самостоятельно;
- сверлильный станок или дрель с набором свёрл;
- бумага наждачная разной зернистости;
- полировальная машина, можно УШМ с полировочным кругом;
- духовой шкаф газовой плиты, для отпуска металла;
- наковальня и два молота разного веса, один – 6 кг, второй – 1,5-2 кг;
- ленточная шлифмашина или опять УШМ с абразивным кругом;
- электролобзик или просто ножовка с мелкими зубцами;
- сварочный аппарат;
- комплект для травления или гравёр (это по желанию).
Большинство этих предметов можно заменить аналогами. Что касается муфельной печи и горна, эти хитрые конструкции можно изготовить своими руками (читайте в статье «Закалка ножа в домашних условиях»).
Подготовка детали к ковке и обработка подшипника
Допустимы к изготовлению ножа из подшипника, любые экземпляры с рабочих машин и двигателей. Если он достался вам в собранном состоянии, самым лучшим способом получить из него заготовку, будет распил «болгаркой». Для этого зажимаем изделие в тиски и при помощи УШМ делаем разрез под углом.
Это делается для одной простой цели, в будущем будет проще ковать остриё и носик клинка. Затем при помощи слесарных инструментов, требуется разогнуть, насколько получится верхнюю обойму. Внимание! Ни в коем случае не стучать молотком, иначе загубите деталь, не начав с ней работать. Вынуть все ненужные части и можно приступать к следующему этапу.
Для полноценной работы, тем более для новичков, обязательно надо сделать эскиз на бумаге будущего клинка. Учесть толщину заготовки и её длину, вернее, то что в результате должно получиться. Чертёж должен содержать в себе всю информацию по размерам, в том числе и рукояти. Для клинков из такого материала лучше использовать накладной метод монтажа рукояти из двух половинок дерева, закреплённых с помощью заклёпок. Чертёж упростит задачу во много раз.
Отжиг и ковка обоймы подшипника
В верхней обойме подшипника чаще всего используется сталь ШХ15, но для точных характеристик, можно воспользоваться справочниками. Маркировка металла иногда присутствует на самих изделиях. Соответственно каждая марка стали ведёт себя по-разному во время ковки и закалки. В наш эксперимент попал экземпляр именно тот, что указан выше.
Подшипник для изготовления ножа.
Такую сталь, нужно подвергать обязательному отжигу, процесс происходит таким образом. В соответствии со справочником, буквы «ШХ», обозначают – подшипниковую сталь с легированием хромом. Отжиг её производится при температуре 800 °С, со снижением её со скоростью 10-20 град/час. Вся эта информация свободно доступна в интернете, пользуйтесь обязательно.
Многим людям, плохо знакомым с ковкой, будет сложно работать с кузнечными клещами. Для упрощения этой задачи к заготовке приваривается пруток. Деталь укладывается в печь и разогревается до 900-1100 °С, выглядеть она будет темно-жёлтой. Но лучше пользоваться лазерным термометром. Если его нет, пробуем сталь магнитом, заготовка не магнитится – значит, разогрев достиг определённой точки Кюри.
При достижении этого значения можно постепенно начинать ковку. Для начала маленьким молотом аккуратно выпрямляем деталь. Всегда контролируйте температуру, лучше подстраховаться и нагреть её, чем на холодную просто разрушить. Следующим приступает к работе большой молот. Проковку нужно выполнять по всем правилам:
- несильными ударами молота, с середины детали «сгоняем» метал в сторону, формируя, таким образом, спуски;
- работа над остриём, немного отличается от общего принципа, носик клинка аккуратно подгоняем к острию;
- обязательна оттяжка заготовки по длине для хвостовика;
- выполнив всё верно, обух будет не более 2 мм.
Вдруг вам вообще не захочется ковать, достаточно просто выпрямить деталь, и остальное можно сточить на шлифовальной машине. Но учтите, потеря в ширине и длине клинка, и сам процесс ковки придаёт металлу дополнительную жёсткость.
По окончании ковочного процесса обязательно требуется провести «нормализацию» стали. Нагреваем заготовку до 900 °С, вынимаем из печи и оставляем на воздухе остывать.
Обдирочные и шлифовальные работы с заготовкой
Всё, что было выполнено в процессе ковки, можно назвать «черновой» работой. Теперь предстоит привести деталь в соответствующий вид. Срежьте при помощи УШМ пруток. На шлифовальном станке, или ленточной машине не сильно прижимая, аккуратно нужно снять весь нагар с металла.
Таким образом, уйдут все неровности и поверхность станет блестящей. Не увлекайтесь этим процессом, дабы не снять лишнего с заготовки. Хотя после этой процедуры, в руках у вас уже будет практически клинок.
Перенос контуров с шаблона на клинок
Дошло дело и до эскиза, который мы выполняли в самом начале. Может случиться так, что чертёж не совпадёт с реальностью. Грустить, тут нет смысла, ведь это черновой вариант. Его надо вырезать и приложить на клинок, а есть смысл, даже приклеить на время любым бумажным клеем.
Чертеж ножа для изготовления из подшипника.
Теперь деталь можно закрепить в тиски, и при помощи «болгарки», абразивным кругом доводим клинок до нужного вам вида, попутно, срезая все задиры и неровности. Единственным минусом может быть, металл нагреется, и бумага сгорит. Поэтому прежде чем её приклеивать, надо процарапать все контуры с эскиза. Задача не из лёгких, но это просто необходимо.
Во время вырезания образа клинка нельзя допускать перегревания детали, даже небольших участков. Поливайте водой заготовку. По окончании работ можно переходить к следующему этапу.
Заточка и шлифовка
В самом начале изготовления ножа вы должны были задуматься: для каких целей он создаётся. Так как заточка для каждого типа изделия абсолютно разная. Но первым делом нужно вывести спуски.
Заострять внимание на них не будем, но запомните: главное в спусках – это симметричность. Только после их выведения, можно приниматься за заточку клинка, но сначала шлифовка. Её можно производить на шлифмашине или при помощи УШМ со специальным кругом. Затем в хвостовике просверливаются два-три несквозных отверстия для крепления рукояти. Во время закалки может случиться неприятность, если просверлить отверстия полностью.
Закалка и отпуск клинка
Очень важный момент, особенно для новичков. Согласно справочнику, температура закалки стали — 830 °С. Разогреть печь, до заданной отметки поможет термометр. Если его нет в наличии, следует воспользоваться одним из способов:
- самый простой и распространённый, проверять магнитом, как только не «прилипает» клинок к нему – цель достигнута;
- следующий очень интересный, посыпать деталь солью, её отметка плавления в 800 °С, значит осталось ещё немного;
- и способ для «прожжённых» профессионалов – цвет заготовки становится светло-красный.
Все способы действенны, но точнее термометра нет ничего. А в данном случае очень важна точность. Нагрев до нужной точки, клинок вынимается и опускается в масло с выдержкой 1 минута на 1 мм толщины изделия. Масло можно использовать практически любое: растительное, минеральное, машинное отработанное или трансформаторное.
Закалка лезвия ножа.
Предварительно его нужно подогреть до 50 °С, это необходимо для хорошего обволакивания погружаемого изделия. Производя такие работы, будьте аккуратны, наденьте защитные очки и перчатки, есть вероятность разбрызгивания масла. Не нужно шевелить клинком, когда он находится в погружении.
После охлаждения заготовки пришёл момент для отпуска стали. Процедура ослабит напряжение в структуре кристаллической решётки металла, возникшее при ковке и закалке. В справочнике указанна температура в 150 °С и время 1,5 часа. Разогрев духовой шкаф кухонной газовой плиты, помещаем туда клин на нужное время.
Очистка клинка
После всех проведённых манипуляций, грубой очистки на гриндере, на клинке останутся тонкие, мелкие царапины. Убирать их надо вручную используя наждачную бумагу. Обрабатывать нужно начиная с зерна 400 перпендикулярно царапинам.
Затем переходим к 600-ому зерну и заканчиваем 800-ым. Добиться зеркального блеска, можно использовав пасту ГОИ или специальные шлифовальные смеси.
Подготовка накладок и сборка ножа
Материалов для изготовления рукояти, довольно широкий выбор: различные металлы, пластмассы, кожа, обмотка бечёвкой и прочие варианты. Но многие мастера любят работать именно с древесиной, она часто подчёркивает уникальность клинка и его красоту.
Подготовка накладок для ножа.
Принцип накладной рукояти довольно прост, и надёжнее, чем другие способы крепления. После отпуска металла можно насверлить отверстия в хвостовике окончательно. А также приготовить брусок:
- Примерить к хвостовику, разметить и придать форму близкую к его размерам.
- Зажав деталь в тиски, разрезать вдоль, строго пополам;
- Для устранения зазоров внутренние части половинок ошкуривают наждачкой.
- Делается разметка в соответствии с отверстиями на хвостовике, и насверливаются в дереве.
- Следующим этапом, можно поступить по-разному, проще всего заклепать ручку клёпками.
- На точильном станке или гриндере обработать рукоять окончательно, под нужную форму вместе с хвостовиком.
- В заключении дерево обрабатывают наждачкой с мелким зерном и пропитывают специальными масляными растворами или покрывают лаком. Зависит от сорта древесины.
Для доведения дела до окончательного варианта можно смастерить ещё и ножны. Но это уже другая и довольно обширная тема. Весь описанный процесс, для новичка может показаться очень сложным. Но люди, занимающиеся этим постоянно, изготавливают такие ножи, словно на конвейере. Так что не расстраиваться при случайных ошибках, продолжать работать, пробовать. И результат не заставит себя долго ждать. Удачи в начинаниях!
Нож из обоймы подшипника своими руками
Сегодня у нас мастер-класс по изготовлению ножа своими руками.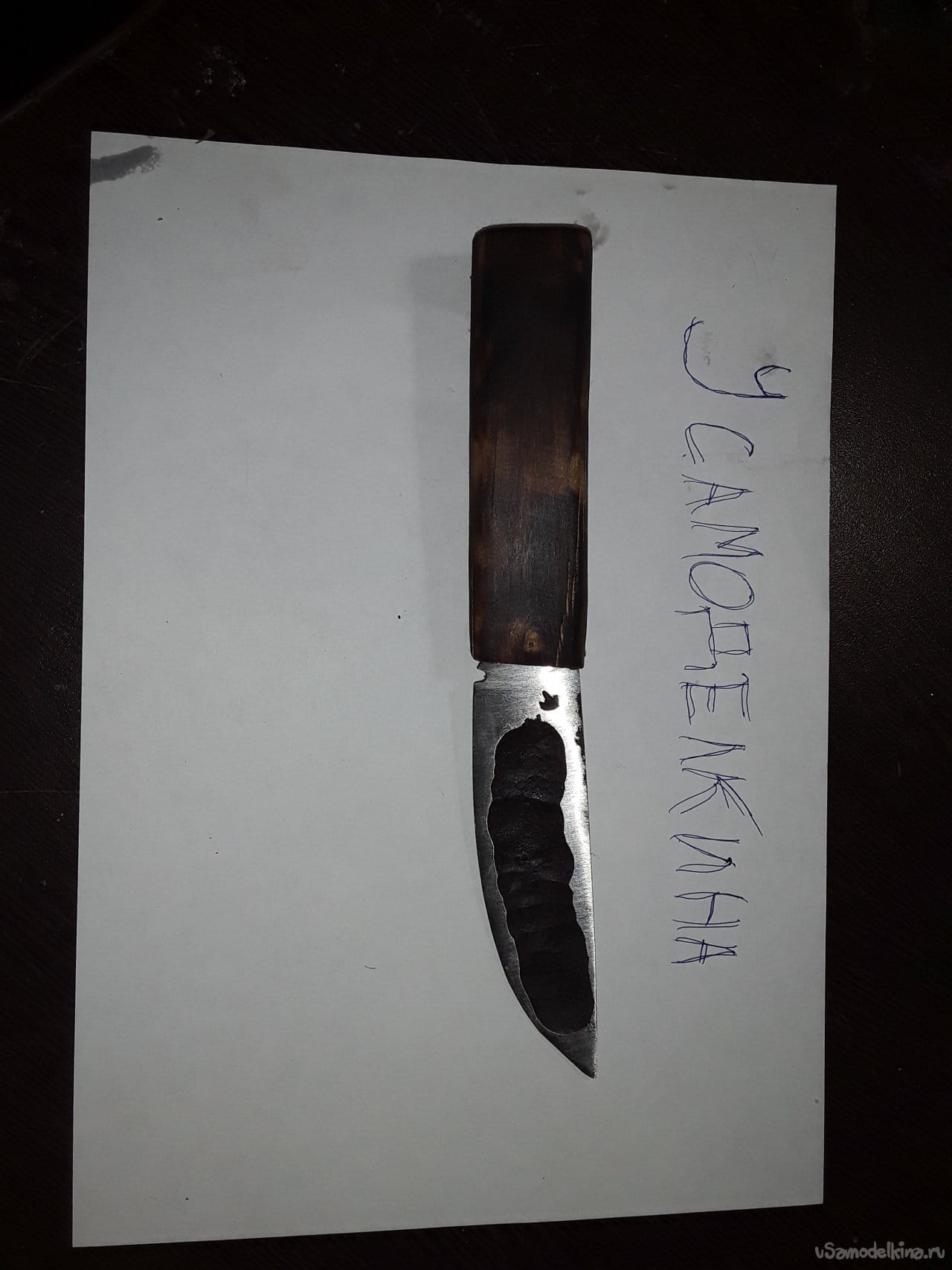
Всем привет! Сегодня мы будем делать нож из обоймы подшипника. Это будет вещь, которую приятно будет иметь при себе.
И так, берем наружную обойму от автомобильного подшипника, разрезаем его вдоль.
Разогнутую заготовку нагреваю и расплескиваю молотком до плоского металла.
Остывшую заготовку пропиливаем по канавкам болгаркой.
Получившийся хвостик вытягиваем в длину, чтобы в конце он сходил в размер 5мм на 5мм.
Нагреваем заготовку и отбиваем молотком так, чтобы ручка у нас была ближе к одной из сторон.
Затем снова нагреваем заготовку и выравниваем ручку. Далее маркером рисуем на заготовке форму ножа и выпиливаем.
Вот что у нас получилось.
Облагораживаем уголочки и делаем более плавную линию.
Теперь будем делать ручку. Для этого еще раз нагреваем заготовку и с помощью тисков и подручных инструментов закругляем ручку.
Вот наш клинок,
берем железную щетку и избавляемся от всей окалины.

Затем делаем режущую кромку.
Остается только подкалить и заворонить.
В итоге у меня получился вот такой нож.
тест
Автор статьи “Нож из обоймы подшипника своими руками” Steel Wood
Смотрите так же:
- самодельный станок для заточки ножей
- самодельное приспособление для заточки сверл малого диаметра
- пила для бетонной тротуарной плитки своими руками
- самодельный токарный станок по дереву
- самодельная наборная ручка ножа из бересты
- Ваша статья будет здесь если Вы ее нам пришлете 🙂 [email protected]
- Об авторе
- Недавние публикации
Друзья, подписывайтесь на мой канал в YouTube
https://www.
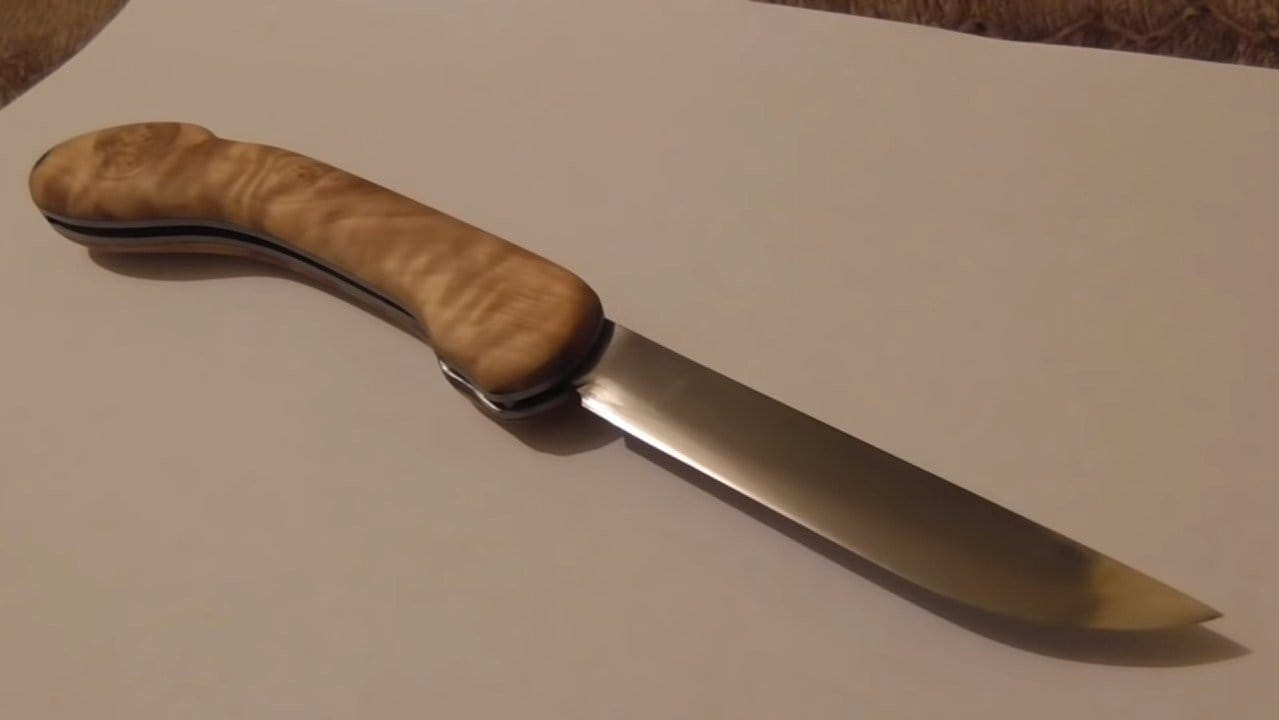
- Подарок для гитариста своими руками — 12 марта 2021
- Зеркало с подсветкой своими руками — 26 января 2021
- Гитара своими руками — 26 декабря 2020
Как сделать нож, автор Виктор Воронин, часть первая. Клинок
Часть первая – изготовление клинка для ножа
(Вторую часть мастер-класса можно почитать здесь)
Всем доброго времени суток. В данном мастер-классе я подробно расскажу как сделать простой рабочий нож.
В качестве материала для клинка было решено использовать подшипник, который сделан из стали ШХ15
Сталь при правильной термообработке выдает очень неплохие прочностные и режущие характеристики, однако её главным минусом является склонность к коррозии. Сначала нужно распилить подшипник с помощью болгарки
Получаются вот такие две половинки
Далее переходим к ковке. Для этого я собрал простенький горн из нескольких кирпичей, трубы и улитки для поддува
Кладем наши половинки в горн, включаем поддув и ждем пока они нагреются до необходимой температуры
Когда металл нагреется до ярко оранжевого цвета, в первую очередь его необходимо выпрямить
После выпрямления половинки подшипника на ней остается желобок
Продолжаем ковать, чтобы избавиться от него и получить ровную полосу
В итоге получаем вот такие поковки
Для того чтобы металл стал мягким и легче обрабатывался делается отжиг. Для этого поковки нагреваются до закалочной температуры (примерно 850 градусов)
и закапываются в угли, оставаясь остывать вместе с горном до полного остывания
На следующий день я достал из горна уже остывшие поковки.
Для этого ножа я не рисовал никаких эскизов, поэтому приблизительную форму будущего клинка я нарисовал сразу на поковке
После вытачивания желаемой формы клинка на гриндере
с помощью напильников я выравниваю плечики клинка
Далее делаются углубления в хвостовике клинка для лучшего сцепления с рукоятью. Получаем такую заготовку
Теперь необходимо разметить границы будущих спусков с помощью штангенциркуля и маркера
Закрепляем клинок в приспособлении для выведения спусков
и делаем черновые спуски
Чтобы клинок не повело при закалке необходимо оставить толщину клинка на месте режущей кромки не менее 1 мм.
Переходим к закалке, но для начала надо сделать несколько циклов нормализации для того, чтобы сталь приобрела мелкозернистую однородную структуру. Чтобы сделать нормализацию, нагреваем клинок до закалочной температуры и даем ему остыть на воздухе
Повторяем данную процедуру 3 раза. В качестве охлаждающей среды при закалке я использую отработанное масло. Чтобы скорость охлаждения была оптимальной масло нужно подогреть примерно до 60 градусов. Для этого нагреваем кусок арматуры
и погружаем его в масло
Чтобы перестраховаться от поводок клинка после закалки я использую тиски с двумя стальными пластинами
Теперь переходим непосредственно к самой закалке. Нагреваем клинок до температуры примерно 850 градусов и быстро погружаем его в масло
Подержав клинок несколько секунд в масле, я зажимаю его между стальными пластинами и жду пока он полностью остынет
Вытаскиваем и смотрим – нет ли поводок
Далее проверяем удалась ли закалка, для этого берем стеклянную бутылку и царапаем ее
Если клинок уверенно царапает стекло, значит закалка удалась, и его твердость более 60 единиц. Чтобы клинок не был хрупким и не рассыпался как стекло при первом же падении необходимо сделать отпуск. Для этого я использую обычную духовку. Выставляем температуру в духовке 180-200 градусов и кладем туда клинок на 1 час. Следующий этап изготовления ножа — чистовое снятие спусков. Закрепляем клинок в приспособлении и приступаем к работе
Сначала обрабатываем грубой лентой
Далее шлифуем спуски более мелкозернистыми лентами, заканчивая лентой Р600. Получаем вот такой готовый клинок
Теперь приступаем к изготовлению больстера. Отпиливаем заготовку от прутка квадратного сечения.
потом распиливаем ее пополам
и обтачиваем на гриндере до необходимого размера
Получаем вот такую заготовку
При помощи штангенциркуля делаем разметку
Далее с помощью керна и молотка намечаем места в которых надо просверлить отверстия
Зажимаем в тиски и сверлим
Берем пробойник, который я сделал специально для этого, и соединяем несколько отверстий, чтобы в них мог пролезть надфиль
Надфилем аккуратно растачиваем отверстие до нужного размера, постоянно проверяя, чтобы не сточить лишнее
Заготовка для больстера готова
Теперь надо ее надеть на клинок. Делаю я это следующим образом: зажимаю в тиски дубовый брусок и втыкаю в него клинок, потом надеваю больстер на сколько это возможно, далее надеваю сверху ещё один больстер, в котором проделано большое отверстие, чтобы он подходил ко всем клинкам, он нужен для того, чтобы принимать все удары на себя и наш больстер не повредился. Потом я надеваю сверху всего этого стальную трубу и набиваю больстер несильными ударами
Получаем такой результат
Кованый нож-тесак из обоймы подшипника
Подшипники, как известно, изготавливаются из стали очень высокого качества, поэтому они идеально подходят для ковки самодельных клинков и ножей. Замечено, что среди мастеров, которые специализируются на изготовлении ножей, особенно ценятся шведские подшипники, однако для данной самоделки вполне подойдут подшипники отечественного производства.
Нужно отметить, что из обоймы подшипника получаются хорошие охотничьи ножи, а также большие кухонные тесаки, которые легко разрезают мясо вместе с костями, при этом они достаточно долго держат заточку — даже при интенсивном использовании точить их можно раз в 6–8 месяцев, иногда даже реже.
Основные этапы работ
1
Читайте также: Как сделать молот Тора из старой кувалдыПервым делом необходимо разрезать наружную и внутреннюю обоймы подшипника, чтобы удалить «внутренности» — зажимаем подшипник в тиски и делаем пропил болгаркой. Затем наружную обойму нужно выпрямить. Для этого нагреваем ее сначала в горне докрасна, а уже потом только разгибаем концы.
Последующее выравнивание заготовки целесообразнее выполнять при помощи пневмомолота, однако можно обойтись и ручной кувалдой, отбивая обойму на наковальне — но в этом случае времени придется потратить больше.
После того, как из круглой обоймы подшипника получилась прямая пластина с рукояткой, обрезаем заготовку по размеру болгаркой и приступаем к механической обработке: зачищаем и шлифуем поверхность, закругляем края, а также делаем режущую кромку.
1
Читайте также: Раскладное кресло из профтрубы и деревянных брусковЗатем сверлим в хвостовой части тесака три отверстия и делаем ручку из фанеры или дерева — в качестве крепежа можно использовать стальные заклепки. Подробный процесс изготовления ножа-тесака из подшипника смотрите в данном видеоролике.
Мне нравитсяНе нравится
Андрей Васильев
Задать вопрос
Закалка ножа из подшипника, «крестьянский» подход / Гостевая / НеПропаду
Закалка.
Проблема.
Поскольку я делаю ножи в основном из подшипников от автомобилей, по размеру обычно это диаметр сантиметров 10-15, и начинал полным дятлом, после чисто интуитивных попыток возникли следующие проблемы:
• После закалки в воде сталь хрупкая настолько, что разлетается как стекло при сильном ударе
Собственно, все. Остальное все меня устраивало. Но мне хотелось, чтобы «не ржавело», «хорошо резало», «держало заточку», «не раскалывалось».
Болометра у меня нет, «все на глазок», и когда я читаю рекомендации «выдержать два часа при температуре 453 градуса» — это не для меня. В конце концов, плюс-минус твердости или вязкости мне фиолетово. Меня вполне устроит «более-менее» приличное качество по перечисленным параметрам.
Поэтому.
Решение проблемы:
1. Отковываю, обязательно соблюдая следующие условия:
• При нагреве я лучше недогрею, чем перегрею. Стараюсь не накалять до белого свечения, работаю в диапазоне красного-желтого. Лучше я почаще буду совать-вынимать, чем пережгу.
• Внимательно следим за деталью, когда лежит в горне: попытка сэкономить и делать одновременно две детали приводит к тому, что или пережжешь, или что-то испортишь.
• Нагрелось до красного яркого с кусками желтого свечения – вынимаем
• Периодически пшикаем-брызгаем из бутылочки пластиковой (как на шашлык) – лучше видно температуру, где что нагрето, да и угли экономит
• Особенно внимательно, когда есть тонкие детали (лезвие, например) – не пережечь!
2. НИ В КОЕМ СЛУЧАЕ НЕ БИТЬ ПО ХОЛОДНОМУ МЕТАЛЛУ!
• Когда куешь, металл пластичен. И по свечению видно, если он начинает остывать. Конечно, хочется за один раз отковать «побольше». Надо бороться с этим искушением.
• Как только при ударе молотом (а я все вручную, нет механики) – чувствуешь, что пластичность уменьшается – останавливаемся, греем дальше.
Пояснение: насколько я понял, объясняется все просто. Как только я треснул молотом по подостывшему металлу, возникают микро-трещины, которые плохо «залечиваются» даже хорошим нагревом, и потом по ним все ломается. Вот и все.
3. Собственно, закалка.
Я пробовал в воду. При любых (почти) вариантах – хрупкая сталь получается. Поэтому взял, слил в канистру отработанного машинного (не проблема достать). Читал картинки и про то, какие температуры для каких марок стали… Разбирался в свечениях и цвете металла. Сухой остаток:
• Когда форма детали скована – я стараюсь максимально близко к финальной форме, чтобы поменьше точить, — приступаю к закалке
• Нагреваю до (в среднем) цвета-свечения между красным и желтым (на глазок) – но для этого есть обоснования теоретические, скажу ниже, — и опускаю ВЕРТИКАЛЬНО ЗА ХВОСТИК кончиком лезвия вниз быстро-быстро в масло. Держу несколько минут, чтобы полностью остыло.
• Нагреваю до темно-красного цвета и закаляю еще раз
• Если «ведет» нож, что бывает, — просто искривляется он – нагреваю до темно-красного цвета (минимальная пластичность) и подправляю, если надо, закаляю еще раз.
• Кладу рядом с углями на поддон, вырубаю горн – пусть остывает все вместе.
Результат – шикарно все, и без заморочек. Могу подвести длинную базу, но такой повтор закалок с понижением верхней температуры нагрева на опыте дает отличный результат в среднем, независимо от взятого подшипника (японских экзотик не пробовал, брать не буду – в основном наш Автоваз, Уралаз, Камаз, Газ, и пр. Совецкие заводы.)
Теперь теория.
Если мы возьмем картинку переходов разных аустентитов в мартенситы и прочие цементиты,
… то обратим внимание, что В СРЕДНЕМ диапазон правильного нагрева выше 850, но ниже 900 градусов. Поэтому нагревать надо примерно до диапазона цветов как на картинке ниже.
Повтор ХУЖЕ не делает, а ЛУЧШЕ делает. Вот и все.
Поскольку подход этот «крестьянский» я его излагаю просто и все.
Что можно сделать из подшипников своими руками
Что можно сделать из подшипника? » Изобретения и самоделки
Крутой станок из Подшипника своими руками!
youtube.com/embed/ss_85-MqtPY» frameborder=»0″ allowfullscreen=»allowfullscreen»>
Я покажу что можно сделать из подшипника и старых металлических обрезков , очередная самоделка превзошла все мои ожидания.
Кондуктор должен быть идеальной формы, как улиточка завитушка., ровный круг с выходом, как спирали от комаров, только меньше колец. А у вас кондуктор с углами и овальный поэтому завитки получились яйцевидной формы. Попробуйте сделать другой кондуктор, из подошвы под жд рельсы, куда гвозди в шпалу забивают. Только кондуктор сделайте в форме капли с изогнутым хвостиком, и вырезать проще, и плавные формы смотрятся лучше, даже если там будет один завитокИсточник
Как сделать сверло из подшипника для сверления каленой стали
Каленую и твердую сталь берет далеко не каждое сверло. В связи с этим при необходимости просверлить обойму подшипника, клинок ножа или другие закаленные изделия возникают трудности. Для их решения можно сделать самодельное сверло, справляющееся со сложными задачами.
Материалы:
- шарик из-под подшипника;
- саморез.
Изготовление сверла
Нужно подобрать шарик соответствующий диаметру требуемого отверстия. Его можно взять из нового или старого отработанного подшипника. Для быстрого извлечения подшипник лучше обмотать в ткань и разбить молотком. Тряпка не позволит шарикам разлететься по мастерской.
В качестве основания сверла будет применяться обычный черный саморез по дереву. Главное, чтобы его длины хватило для нужной глубины сверления. Шляпка самореза обтачивается, чтобы ее диаметр стал немного меньше, чем шарик.
В тисках зажимается небольшая гаечка, на которую выставляется шарик. Гайка используется как временная подставка, поэтому качество ее резьбы и состояние граней не имеет значения.
К шарику приставляется головка самореза и они свариваются вместе.
Выступающую за диаметр шарика сварку нужно сточить на наждаке. При этом саморез важно поворачивать, чтобы получить цилиндр без углов.
Затем шарик перетачивается под спиральное сверло. Если нужно сверлить плитку, то ему придается форма пера.
Получив нужную форму, сверло закаляется. Шарик после сварки и проточки теряет твердость, поэтому ее нужно восстановить. Для этого кончик сверла греется газовой горелкой до оранжевого цвета и погружается в масло на несколько секунд. При этом сам шуруп и сварку охлаждать не нужно, чтобы они не стали хрупкими.
После закалки наконечник сверла окончательно затачивается. Делать это на отпущенном металле до закалки не следует, поскольку тогда качество режущей кромки будет хуже.
Полученное сверло хорошо сверлит практически любой твердый металл, будь то обойма подшипника или напильник. Главное его не переохлаждать. Если нет под рукой масла, то нужно подливать в отверстие хотя бы воду.
При сверлении очень толстых стальных пластин, чтобы не мучатся с постоянным охлаждением, можно положить резиновое кольцо вокруг накерненной точки и подлить в него воды. Жидкость будет удерживаться за счет поверхностного натяжения и постоянно охлаждать сверло.
Смотрите видео
sdelaysam-svoimirukami.ru
Как самому сделать нож из подшипника, который будет не хуже магазинного
Сегодня, я расскажу вам на что способен нож из подшипника и как его сделать-это безумная мысль, которая не давала мне уснуть эту ночь, так как все делают ножи из напильников, потому что они очень прочные.
И сегодня я расскажу вам, кое-что новое и не заезженное, а именно нож из Подшипника.
И так приступим, для начала нам нужен сам подшипник.
А именно та деталь, которую вы видите слева от себя.
После чего мы идем к тискам зажимаем и пилим.
Потом немного ее разгибаем и ложим в печь.
После чего мы выпрямляем деталь с помощью молотка, после того как деталь выпрямлена, мы идем к станку делаем разметку с помощью заранее подготовленного трафарета и начинаем вырезать.
После того как мы все вырезали с помощью болгарки ее нужно отполировать и выполнить термическую обработку в печи +-700-900 градусов.
После чего мы должны поймать температуру в 200 градусов и опустить нож в воду, после чего закинуть в масло.
Потом мы должны зажать заготовку в тисках и обработать нож напильником.
И после этих всех манипуляций проводим отпуск, если его не сделать, то нож будет очень хрупким и разобьется как стекло, если уронишь.
Отпуск нужно проводить в 150 градусах в печи. Ложимся спать и на утро достаем. По сути сам клинок уже готов.
Делаем, какую хотите рукоять. Можно не париться сходить в магазин купить термопластик (он быстро плавится и принимает любое положение). Но мы сделаем из дерева.
Насаживаем клинок на дерево, после чего обрабатываем и придаем форму рукояти.
Ну в принципе все, нож готов. Кому интересно сталь, которая используется в изготовлении подшипников ШХ15-ну что я могу про нее сказать, она долго держит заточку и достаточно прочная.
Если все правильно сделать можно и ветки рубить и разделывать тушки, что хотите в общем. Главное ни где не накосячить.
Такой нож не хуже, того что вы купите в магазине, а наоборот лучше, так как близок к сердцу. HRC будет ниже 60, примерно 56-57.
Источник
Универсальный круглогиб из подшипников своими руками
Давно хотели реализовать приспособление для прокатки металлического профиля, арматуры, полосы и прута в круг. И вот делая внеплановую уборку гаража отрыли подшипники, уголок 40 мм и полумуфты.
Конструкцию решили делать простую, приспособленную под обычные тиски. Первым делом сделали раздвижную станину из уголка на металлических втулках-направляющих. К ней приварили задний ступичный подшипник от Лады-Калины. Это будет основой для ручки прокатного станка.
Чтобы механизм справлялся с широкими пластиками его удлинили в два раза, расхомутав немного трубы от старого домкрата. Далее запрессовав полумуфты в подшипники, наметили места сварки. Приварили и установили подшипники на свои места. Вот и весь станок!
Ручку в итоге все-таки удлинили. На стальном пруте убедились что вся эта штуковина надежна и реально работает. Много полезного можно теперь намудрить… НО! Есть что добавить… Покрасить можно всегда в любой цвет! Но, если серьезно, думаю сделать паз болгаркой по радиусу ступичного подшипника, где-то по середине. Напротив наших сдвоенных. Это для лучшей фиксации прута, арматуры и профильного прута. Как раз прут будет ложиться в насечки с двух сторон и лучше фиксироваться при прокатке.Так же сделаю ребра жесткости на уголке, дабы все было по-мощнее. Все размеры на фото. Все как делали подробно в видео. Может у кого возникнут мысли по доп улучшению данного изделия.
Запись пользователя KAS6russiangarag из сообщества Сделай Сам на DRIVE2
Источник
Сообщества › Сделай Сам › Блог › Универсальный круглогиб из подшипников своими руками.
Полный размер
youtube.com/embed/n_llFC31qxw?wmode=opaque&rel=0″ frameborder=»0″ allowfullscreen=»»/>
Давно хотели реализовать приспособление для прокатки металлического профиля, арматуры, полосы и прута в круг. И вот делая внеплановую уборку гаража отрыли подшипники, уголок 40 мм и полумуфты.
Конструкцию решили делать простую, приспособленную под обычные тиски.
Первым делом сделали раздвижную станину из уголка на металлических втулках-направляющих. К ней приварили задний ступичный подшипник от Лады-Калины. Это будет основой для ручки прокатного станка.
Что бы механизм справлялся с широкими пластиками его удлинили в два раза, расхомутав немного трубы от старого домкрата.
Далее запресовав полумуфты в подшипники, наметили места сварки. Приварили и установили подшипники на свои места. Вот и весь станок!
Ручку в итоге все-таки удлинили. Протестив круглогиб на стальном пруте, убедились что вся эта штуковина надежна и реально работает.
Много полезного можно теперь намудрить…
НО! Есть что добавить… Покрасить можно всегда в любой цвет…)))! Но, если серьезно, думаю сделать паз болгаркой по радиусу ступичного подшипника, где-то по середине.
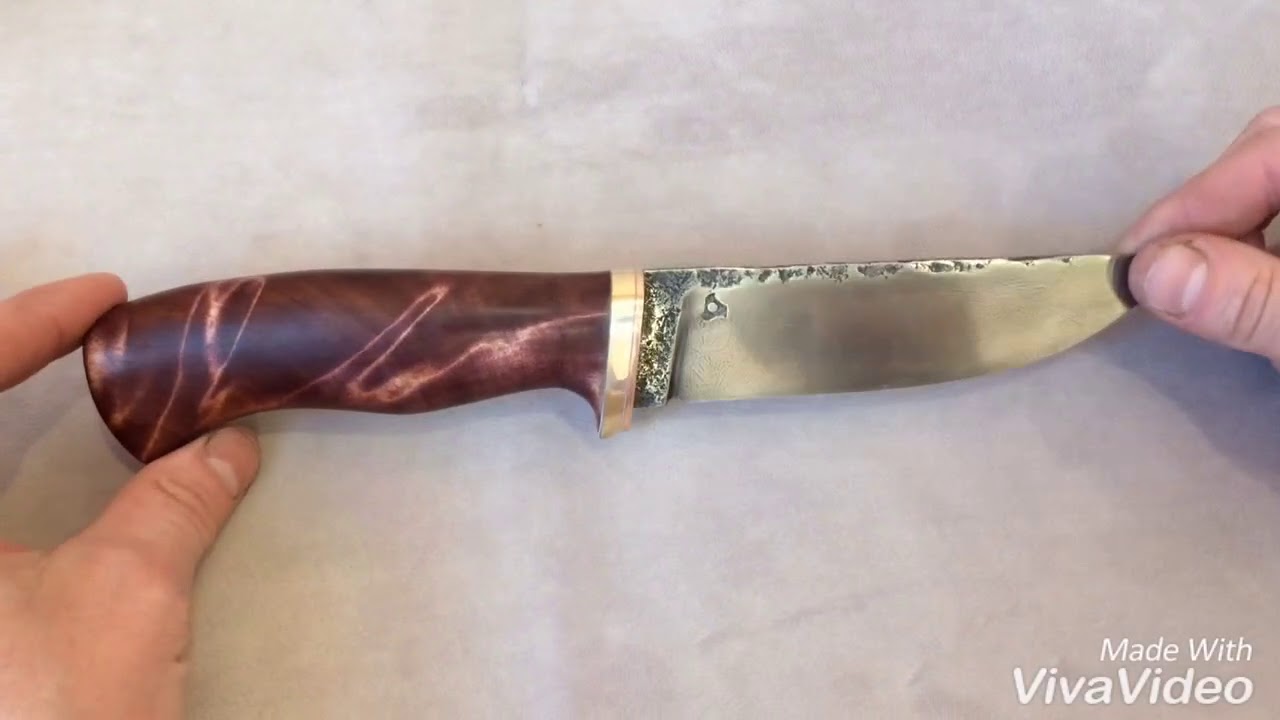
Так же сделаю ребра жесткости на уголке, дабы все было по-мощнее. Все размеры на фото. ВСЕМ СПАСИБО! Все как делали подробно в видео может у кого возникнут мысли по доп улучшению данного изделия.
Полный размер
Полный размер
Полный размер
Полный размер
Полный размер
Полный размер
Полный размер
Полный размер
Полный размер
Полный размер
Полный размер
18 ноября 2019 в 16:32 Метки: кольцегиб, круглогиб, станок своими руками, станок из подшипника, холодная ковка
Что можно сделать из старых подшипников
SAMODELKI.ONLINE
Что можно сделать из старых подшипников
Это нужно иметь в каждом доме/Everyone should have this at home
(2018-02-11 19:49:44)
Смотреть
5 полезных идей и советов / 5 useful life hacks
(2018-02-11 07:00:00)
Смотреть
Железо — Металл, ЗАЩИЩАЮЩИЙ ЗЕМЛЮ
(2018-02-10 14:31:11)
Смотреть
ПЕРЕЗАЛИВ Как сделать РУКИ ИЗ БАЛЛИСТИЧЕСКОГО ГЕЛЯ Изготовление формы и разные составы геля
(2018-02-09 19:49:24)
Смотреть
Самое полезное приспособление для сварки
(2018-02-09 10:43:12)
Смотреть
15 способов УБРАТЬ РЖАВЧИНУ в домашних условиях
(2018-02-07 15:03:37)
Смотреть
5 простых идей и советов которые вам пригодятся / 5 useful life hacks
(2018-02-07 07:00:00)
Смотреть
Супер мощный Power Bank — своими руками
(2018-02-06 19:04:39)
Смотреть
Самодельная Wi-Fi пушка Мощная антенна для ВайФай сигнала своими руками
(2018-02-05 16:58:53)
Смотреть
Самодельная ик паяльная станция из автомобильного прикуривателя
(2018-02-04 12:36:07)
Смотреть
Минералы за МИЛЛИОНЫ ЕВРО Зачем они нужны?
(2018-02-03 14:32:32)
Смотреть
Что можно сделать из старых подшипников
(2018-02-02 17:12:46)
Смотреть
5 простых идей и советов которые вам пригодятся / 5 useful life hacks
(2018-02-02 07:00:01)
Смотреть
Система защиты для LI-ION своими руками.

(2018-02-01 18:05:56)
Смотреть
Плата защиты LI-ION — КАК ЭТО РАБОТАЕТ?
(2018-01-27 20:15:36)
Смотреть
Керамика за 120 Евро? Для чего она нужна?
(2018-01-27 15:58:55)
Смотреть
Нереально крутые самоделки. Сделай и себе эти простые приспособления.
(2018-01-27 09:00:01)
Смотреть
Сделай и себе этот простой и нужный инструмент
(2018-01-26 17:48:07)
Смотреть
СОЛНЕЧНЫЙ РЕЗАК НЕРЕАЛЬНАЯ МОЩЬ ДЛЯ САМОДЕЛЬНОГО КОНЦЕНТРАТОРА Гиперболоид Игорь Белецкий
(2018-01-26 15:25:49)
Смотреть
Как разрезать стеклянную бутылку/банку ВДОЛЬ
(2018-01-26 14:05:33)
Смотреть
Prev12…414243…8081Next
Copyright 2018
Приспособление из большого подшипника
Часто в мастерских лежат без дела старые инструменты и материалы, из которых могут получиться замечательные вещи. Эта публикация как раз об идее использования такого подручного материала для пользы делу.
С помощью большого подшипника можно сделать полезный станок, который нужен любому мастеру.
Для самоделки нужен подшипник значительного размера, весовая шайба, уголок и прутки. В качестве основного инструмента будет использован сварочный аппарат.
Весовая шайба не является базовым элементом, ее можно заменить и другой подходящей деталью. Основная механическая нагрузка в подвижной системе принадлежит нашему подшипнику. В этом самая соль этой полезной модели.
Сначала нужно просверлить два отверстия в детали, которую изготовим из шайбы.
После этого возьмем подшипник и приделаем к нему сваркой два рожка из прутков.
С их помощью будет крепиться элемент из уголка.
К уголку присоединим в указанном порядке шпильки.
Пропустим действия, которые можно посмотреть на видео ниже.
В результате сделали гибочный станок для сложных фигур из полос, прутков, арматуры и др.
Ход работы над изготовлением станка и его испытания в ролике канала TeraFox
youtube.com/embed/ss_85-MqtPY» frameborder=»0″ allowfullscreen=»allowfullscreen»/>
Гибочный станок из подшипника своими руками
При армировании фундаментов или кладки стен требуется заложить арматуру, которую перед этим нужно согнуть. Сделать это быстро и ровно получится только на гибочном станке. Это простое и компактное устройство, которое можно сделать своими руками. Также оно будет полезно для сгибания не толстых прутков для различных поделок.Материалы:
- большой подшипник можно заклинивший;
- длинный болт М12 или толще;
- 3 гайки М12;
- удлиненная гайка М12;
- стальная полоса как минимум 60х10 мм или пластина.
Изготовление гибочного станка
В качестве толкателя и гибочной опоры станка будут использоваться кольца крупного подшипника с наружным диаметром от 100 мм. Его внешняя обойма разрезается пополам.
Одна из ее половин приваривается на стальную полосу, как на фото.
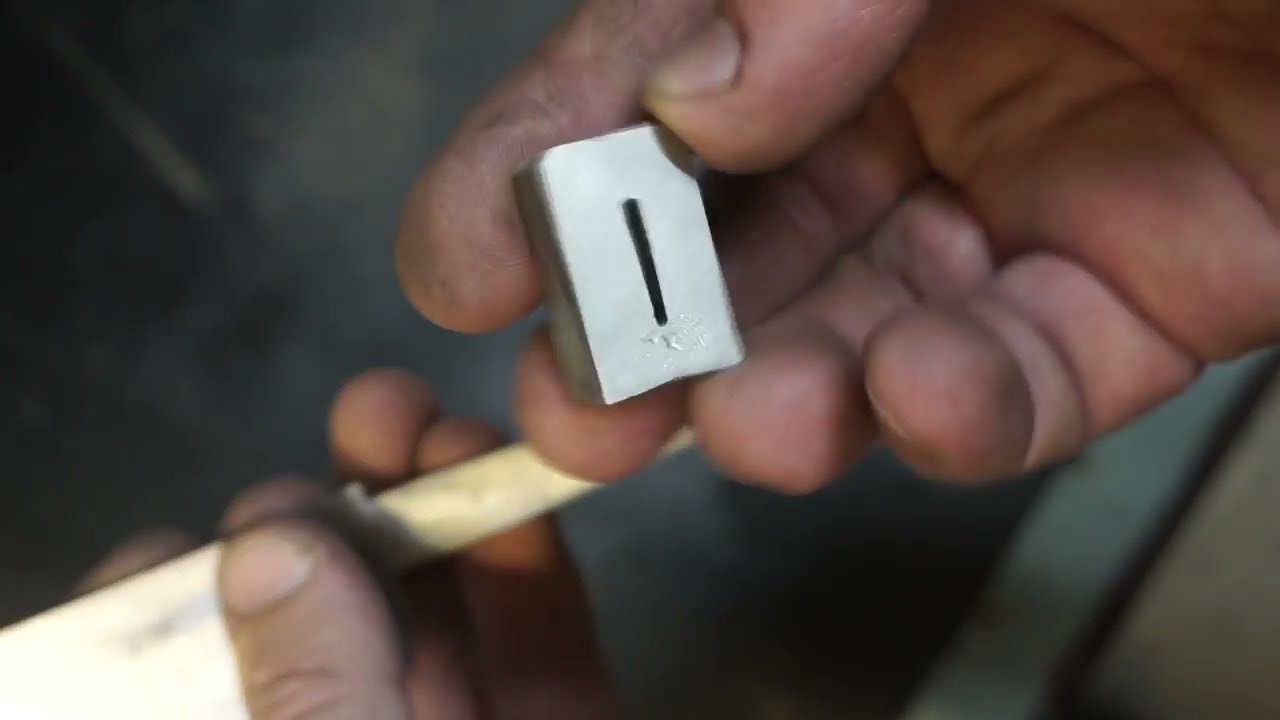
Часть внутреннего кольца вырезается по ширине гайки, которая затем в него уваривается.
Перед этим нужно убрать ее резьбу, прогнав через нее сверло. Нужно, чтобы болт проходил сквозь нее не накручиваясь.
Далее нужно обточить грани еще у 2-х гаек, придав им округлую форму.
На болт накручивается длинная гайка, затем короткая со снятыми гранями. Его конец продевается через расширенную гайку, вваренную во внутреннее кольцо подшипника. Затем на него наворачивается оставшаяся узкая обточенная гайка.
Чтобы гайки без граней не откручивались, их нужно обварить. Перед этим они поджимаются, чтобы кольцо не шаталось относительно болта.
На обратной стороне стальной полосы с полукольцом нужно приварить небольшой флажок. За него в дальнейшем будет удобно зажимать станок в тисках.
Затем полоса переворачивается и к ее противоположному от полукольца краю приваривается механизм с болтом. Сварка делается только на длинной гайке. Таким образом, при вращении болта толкающее кольцо будет двигаться в сторону упорного полукольца.
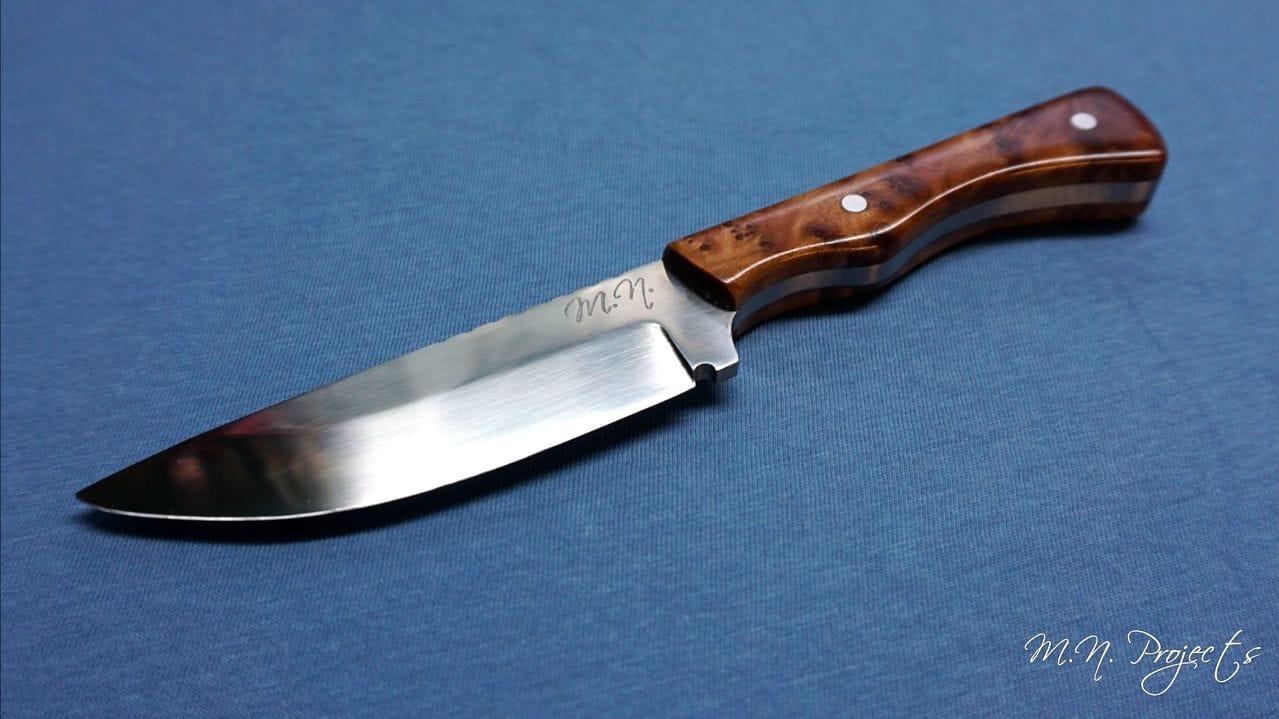
Как пользоваться
Станок зажимается в тисках за сделанный внизу флажок. Между кольцами закладывается арматура. Для движения толкателя на упор, необходимо вращать винт гаечным ключом. Арматура при этом не выскакивает, поскольку удерживается за счет проточки на кольце подшипника. По мере вкручивания болта прут сгибается на необходимый угол.
Несмотря на небольшие размеры станка, его способностей достаточно для легкого сгибания тонких прутков и арматуры диаметром до 6 мм. Более толстый прокат, при качественной сварке станка, также ему не повредит. Для удобства можно приварить к шляпке болта вороток, чтобы не пользоваться гаечным ключом.
Смотрите видео
Как быстро сделать корпус для подшипника
При работе над самодельным устройством в наличии может оказаться подшипник по диаметру меньше уже существующего гнезда или опоры.
Для реализации предстоящей задумки нужно иметь некоторый опыт работы с металлом, совершенно простые, доступные и недорогие материалы, а также вполне стандартное оборудование и инструменты. Конечно, нельзя забывать и об индивидуальных средствах защиты: очках, перчатках и т. д.
Понадобится
Следует не забывать о том, что даже стандартный подшипник – прецизионное изделие. Поэтому так важны точность измерения и аккуратность разметочных операций, чтобы подшипник не оказался слишком зажат или имел бы зазор при монтаже в корпус. В первом случае он быстро выйдет из строя, во втором – не будет держаться на месте.
Для успешной работы мы должны иметь в наличии:
- отрезок трубы необходимого диаметра и толщины стенки;
- угольник и штангенциркуль;
- маркер;
- маятниковую пилу;
- сверлильный станок;
- болгарку;
- сварочное оборудование;
- цилиндрическую стальную оправку;
- тиски, наковальню и молоток.
Порядок изготовления корпуса подшипника из круглой трубы
Тщательно размечаем соответствующую под данный подшипник по диаметру и толщине стенки трубу на два кольца, равные по ширине имеющемуся подшипнику.
На маятниковой пиле по разметке нарезаем кольца.
На одном из них проводим две параллельные линии перпендикулярно торцам, на расстоянии, полученном из предварительного расчета.
На другом кольце наносим четыре точки по центру кольца равномерно по окружности.
Вырезаем участок кольца между двумя линиями разметки и зачищаем места реза болгаркой.
На сверлильном станке выполняем по меткам четыре сквозных отверстия на втором кольце.
Немного сжимаем кольцо с вырезом, слегка ударяя молотком по его концам. Запрессовываем с помощью молотка разрезное кольцо в целое с четырьмя отверстиями на боковой стороне.
Насаживаем на цилиндрическую оправку с входного конца наши запрессованные друг в друга кольца, ударяя по ним молотком по кругу, пока они не окажутся на формирующем участке оправки и разрезное кольцо равномерно без зазоров не примкнет к внутренней поверхности наружного кольца.

Используя ранее просверленные отверстия во внешнем кольце, привариваем его к внутреннему.
Легкими ударами молотка по торцу подшипника устанавливаем его в наш самодельный корпус.
Теперь остается лишь подшипник в корпусе закрепить в гнезде или опоре.
Теперь корпус можно приварить куда угодно и покрасить.
Смотрите видео
Нож из обоймы подшипника, вариант 1
Всем здравствуйте в куче металлического хлама нашел 4 куска от обоймы подшипника и решил сделать из них 4 небольших ножа. Сталь подшипника в основном из ШХ10, ШХ15, а подшипник диаметром от 200 мм из ШХ20. У меня подшипник из ШХ15.
Уже ни один нож делал из подшипников разного диаметра из разных сталей, так что думаю затруднений не будет. Главное правило ковки ножа из подшипника — это температура нагрева заготовки, ведь эта сталь не любит перегрева, и по этому я лучше не до грею чем, перегрею сталь.
Нагреваю до вишневого цвета и начинаю ковать при нанесении удара, если чувствую, что сталь становится упругой, то сразу же немного подогреваю заготовку и продолжаю ковать. Вот и все с теорией, приступаю к ковке ножа из обоймы подшипника.
После обжига заготовки начинаю выпрямлять на наковальне, после выравнивания нагреваю до вишнёвого цвета и начинаю ковать лезвие ножа, нанося скользкие удары, вытягивая от обуха, но лезвия ножа. Нагревать нужно аккуратно, чтобы не перегреть металл, иначе все испортим.
После вытяжки лезвие на обухе 2 мм, а на острие 1 мм я ковал лезвие сразу в готовый вид так, что после ковки буду сразу закаливать нож.
После ковки лезвия приступаю к формировке хвостовика, ручку ножа я решил сделать декоративную кованую ручку. Нагреваю и начинаю ковать хвостовик формой квадрата. После 3 или 4‐х нагревов вытягиваю хвостовик до нужной длины. Нагреваю еще раз, далее зажимаю в тисках, и держав за хвостовик, начинаю закручивать и за два раза закручиваю, как нужно мне. Нагреваю, а затем загибаю ручку под удобный хват, вот и все с ковкой.
Теперь можно и закаливать нож. Нагреваю до того момента пока магнит не перестанет прилипать к ножу, и окунаю в подогретое минеральное автомасло. После закалки оставляю на выключенном горне, пусть остывает будет как отпуск. Вот и все теперь приступаю к слесарке.
Ручку решил оставить как есть, чтобы видно было ковку. На Гриндере, на 120 бумаге, шлифую ручку до малозаметных рисок. Далее на станке формирую форму клинка по шаблону. Металл берется тяжело, но спасает что клинок нужно просто отшлифовать, ведь я сразу отковал нужную толщину. Спустя пол часа я наконец-то закончил шлифовать на станке. Зажимаю нож струбциной и шлифую вручную. К сожалению у меня нет мелкой бумаги, осталось только 60, 100 и 120, а еще 400ка так, что до блеска пока не получится отшлифовать. А травить в кислоте не охота. Вот и все нож готов.
Длина от кончика до конца рукояти 185 мм, длина клинка 103 мм. Нож получился небольшим, но удобным.
Некоторые сейчас будут тролить, типа страшный и из стали го.., а скажу так, что человек от обезьяны отличается тем, что он хотя бы что-то делать старается, а не лежит на диване и строчит некрасивый комментарий, типа я лучше могу, к счастью даже такие комментарии приносят 0.5 монет хоть немного польза.
Сталь ШХ15 — да не спорю не из лучших, но эту марку стали можно найти хоть где даже под диваном, но у нее есть и свои плюсы если не перегревать ее, то она менее поддается ржавчине, но нужно не забывать что любой нож требует ухода.
Вот и все моя статья подошла к концу. Любая вещь, сделанная своими руками, лучше чем фраза я могу лучше. Всем спасибо и до новых Самоделок друзья.
Доставка новых самоделок на почту
Получайте на почту подборку новых самоделок. Никакого спама, только полезные идеи!
*Заполняя форму вы соглашаетесь на обработку персональных данных
Становитесь автором сайта, публикуйте собственные статьи, описания самоделок с оплатой за текст.
Как сделать сверло из подшипника для сверления каленой стали
Каленую и твердую сталь берет далеко не каждое сверло. В связи с этим при необходимости просверлить обойму подшипника, клинок ножа или другие закаленные изделия возникают трудности. Для их решения можно сделать самодельное сверло, справляющееся со сложными задачами.
Материалы:
- шарик из-под подшипника;
- саморез.
Изготовление сверла
Нужно подобрать шарик соответствующий диаметру требуемого отверстия. Его можно взять из нового или старого отработанного подшипника. Для быстрого извлечения подшипник лучше обмотать в ткань и разбить молотком. Тряпка не позволит шарикам разлететься по мастерской.
В качестве основания сверла будет применяться обычный черный саморез по дереву. Главное, чтобы его длины хватило для нужной глубины сверления. Шляпка самореза обтачивается, чтобы ее диаметр стал немного меньше, чем шарик.
В тисках зажимается небольшая гаечка, на которую выставляется шарик.

К шарику приставляется головка самореза и они свариваются вместе.
Выступающую за диаметр шарика сварку нужно сточить на наждаке. При этом саморез важно поворачивать, чтобы получить цилиндр без углов.
Затем шарик перетачивается под спиральное сверло. Если нужно сверлить плитку, то ему придается форма пера.
Получив нужную форму, сверло закаляется. Шарик после сварки и проточки теряет твердость, поэтому ее нужно восстановить. Для этого кончик сверла греется газовой горелкой до оранжевого цвета и погружается в масло на несколько секунд. При этом сам шуруп и сварку охлаждать не нужно, чтобы они не стали хрупкими.
После закалки наконечник сверла окончательно затачивается. Делать это на отпущенном металле до закалки не следует, поскольку тогда качество режущей кромки будет хуже.
Полученное сверло хорошо сверлит практически любой твердый металл, будь то обойма подшипника или напильник.

При сверлении очень толстых стальных пластин, чтобы не мучатся с постоянным охлаждением, можно положить резиновое кольцо вокруг накерненной точки и подлить в него воды. Жидкость будет удерживаться за счет поверхностного натяжения и постоянно охлаждать сверло.
Смотрите видео
пошаговая инструкция по изготовлению своими руками
На чтение 11 мин. Просмотров 447 Опубликовано
Русские умельцы ножевого дела, никогда не ищут лёгких путей. Потому что это – для многих хобби и увлечение. Бывает, что из простого занятия, получается настоящий небольшой бизнес. Но в большинстве своём, для людей это всё же, это отдых и отвлечение от повседневной жизни. Каждый человек, определяет свой досуг сам. Любители ковать, довольно часто изготавливают свои изделия из необычных вещей, например: нож из подшипника. Очень интересный и непростой процесс.
Плюсы и минусы ножа из подшипника
Многие обыватели скажут, что зачем этим заниматься, когда можно пойти в магазин и прикупить себе парочку замечательных клинков. Но мы же, им не указываем, как проводить своё время. Так что если неинтересно, идём на другой ресурс, а здесь будет статья, содержащая в себе немало полезной информации особенно для новичков. Потому что изложение планируется в пошаговом ракурсе.
Мы уже писали о том, что «идеального ножа» на всё случаи жизни, не существует. И это правда, но стремиться к идеалу нужно всегда. Поэтому попробуем выделить положительные и отрицательные стороны клинка из подшипника. Чтобы знать, что получится в результате правильной обработки металла.
Сталь подшипника изначально предназначена для высоких нагрузок, по этой причине она отличается пластичностью и однородностью при нагреве. А в итоге получается изделие с жёсткостью от 61 до 64 единиц по шкале Роквелла. И главное – высочайшая износостойкость клинка. Единственным минусом можно назвать, хрупкость во время обработки. Очень важно, правильно выполнить закалку, а ковку «на холодную», вообще, исключить.
Как сделать нож из подшипника своими руками
Понятно, что в данном деле без ковки никак не обойтись. Нужно обязательно распрямить обойму изделия. Знатоки таких вещей, разделяются на два лагеря, какую часть лучше выбрать для работы: внутреннюю или внешнюю. Однозначного ответа нет, но многие утверждают, что внутреннее кольцо состоит из лучшей стали. Подкрепляя свои слова, тем, что эта часть несёт на себе большую нагрузку.
Но, как бы там ни было, новичку однозначно без разницы. Для начала нужно, чтобы хоть что-то получилось и не треснуло во время закалки. Для нормальной работы потребуется свой, определённый набор инструментов. Ну и главное – кузница.
Требующиеся материалы и инструменты
У совсем «зелёного» новичка вряд ли есть необходимый инструмент, поэтому им нужно обзавестись. Что-то можно изготовить самостоятельно, а другое только купить. Но опять же, покупной инструмент позволительно заменить аналогичным более простым, но увеличится время изготовления. Если нет в планах, заниматься кузнечным и ножевым делом, покупать что-либо, конечно, бессмысленно, если только мелочи. Материалы потребуются следующие:
- подшипник, желательно в разобранном состоянии;
- деревянный брусок, для изготовления рукояти;
- стержни для заклёпок, лучше из латуни;
- эпоксидный клей или похожий по свойствам заменитель;
- масло или воск для пропитки рукояти;
- малярный скотч, листок бумаги, карандаш, маркер.
С материалами не очень сложно и всё доступно. А вот что касаемо инструмента, обратите внимание, как уже говорилось выше, если не найдётся профессионального, пробуйте заменить на более доступные варианты. Их мы также укажем для ясности:
- металлические тиски, зажимы, струбцины;
- УШМ (болгарка) с набором различных дисков;
- горн или муфельную печь, которую можно изготовить самостоятельно;
- сверлильный станок или дрель с набором свёрл;
- бумага наждачная разной зернистости;
- полировальная машина, можно УШМ с полировочным кругом;
- духовой шкаф газовой плиты, для отпуска металла;
- наковальня и два молота разного веса, один – 6 кг, второй – 1,5-2 кг;
- ленточная шлифмашина или опять УШМ с абразивным кругом;
- электролобзик или просто ножовка с мелкими зубцами;
- сварочный аппарат;
- комплект для травления или гравёр (это по желанию).
Большинство этих предметов можно заменить аналогами. Что касается муфельной печи и горна, эти хитрые конструкции можно изготовить своими руками (читайте в статье «Закалка ножа в домашних условиях»).
Подготовка детали к ковке и обработка подшипника
Допустимы к изготовлению ножа из подшипника, любые экземпляры с рабочих машин и двигателей. Если он достался вам в собранном состоянии, самым лучшим способом получить из него заготовку, будет распил «болгаркой». Для этого зажимаем изделие в тиски и при помощи УШМ делаем разрез под углом.
Это делается для одной простой цели, в будущем будет проще ковать остриё и носик клинка. Затем при помощи слесарных инструментов, требуется разогнуть, насколько получится верхнюю обойму. Внимание! Ни в коем случае не стучать молотком, иначе загубите деталь, не начав с ней работать. Вынуть все ненужные части и можно приступать к следующему этапу.
Для полноценной работы, тем более для новичков, обязательно надо сделать эскиз на бумаге будущего клинка. Учесть толщину заготовки и её длину, вернее, то что в результате должно получиться. Чертёж должен содержать в себе всю информацию по размерам, в том числе и рукояти. Для клинков из такого материала лучше использовать накладной метод монтажа рукояти из двух половинок дерева, закреплённых с помощью заклёпок. Чертёж упростит задачу во много раз.
Отжиг и ковка обоймы подшипника
В верхней обойме подшипника чаще всего используется сталь ШХ15, но для точных характеристик, можно воспользоваться справочниками. Маркировка металла иногда присутствует на самих изделиях. Соответственно каждая марка стали ведёт себя по-разному во время ковки и закалки. В наш эксперимент попал экземпляр именно тот, что указан выше.
Такую сталь, нужно подвергать обязательному отжигу, процесс происходит таким образом. В соответствии со справочником, буквы «ШХ», обозначают – подшипниковую сталь с легированием хромом. Отжиг её производится при температуре 800 °С, со снижением её со скоростью 10-20 град/час. Вся эта информация свободно доступна в интернете, пользуйтесь обязательно.
Многим людям, плохо знакомым с ковкой, будет сложно работать с кузнечными клещами. Для упрощения этой задачи к заготовке приваривается пруток. Деталь укладывается в печь и разогревается до 900-1100 °С, выглядеть она будет темно-жёлтой. Но лучше пользоваться лазерным термометром. Если его нет, пробуем сталь магнитом, заготовка не магнитится – значит, разогрев достиг определённой точки Кюри.
При достижении этого значения можно постепенно начинать ковку. Для начала маленьким молотом аккуратно выпрямляем деталь. Всегда контролируйте температуру, лучше подстраховаться и нагреть её, чем на холодную просто разрушить. Следующим приступает к работе большой молот. Проковку нужно выполнять по всем правилам:
- несильными ударами молота, с середины детали «сгоняем» метал в сторону, формируя, таким образом, спуски;
- работа над остриём, немного отличается от общего принципа, носик клинка аккуратно подгоняем к острию;
- обязательна оттяжка заготовки по длине для хвостовика;
- выполнив всё верно, обух будет не более 2 мм.
Вдруг вам вообще не захочется ковать, достаточно просто выпрямить деталь, и остальное можно сточить на шлифовальной машине. Но учтите, потеря в ширине и длине клинка, и сам процесс ковки придаёт металлу дополнительную жёсткость.
По окончании ковочного процесса обязательно требуется провести «нормализацию» стали. Нагреваем заготовку до 900 °С, вынимаем из печи и оставляем на воздухе остывать.
Обдирочные и шлифовальные работы с заготовкой
Всё, что было выполнено в процессе ковки, можно назвать «черновой» работой. Теперь предстоит привести деталь в соответствующий вид. Срежьте при помощи УШМ пруток. На шлифовальном станке, или ленточной машине не сильно прижимая, аккуратно нужно снять весь нагар с металла.
Таким образом, уйдут все неровности и поверхность станет блестящей. Не увлекайтесь этим процессом, дабы не снять лишнего с заготовки. Хотя после этой процедуры, в руках у вас уже будет практически клинок.
Перенос контуров с шаблона на клинок
Дошло дело и до эскиза, который мы выполняли в самом начале. Может случиться так, что чертёж не совпадёт с реальностью. Грустить, тут нет смысла, ведь это черновой вариант. Его надо вырезать и приложить на клинок, а есть смысл, даже приклеить на время любым бумажным клеем.
Чертеж ножа для изготовления из подшипника.Теперь деталь можно закрепить в тиски, и при помощи «болгарки», абразивным кругом доводим клинок до нужного вам вида, попутно, срезая все задиры и неровности. Единственным минусом может быть, металл нагреется, и бумага сгорит. Поэтому прежде чем её приклеивать, надо процарапать все контуры с эскиза. Задача не из лёгких, но это просто необходимо.
Во время вырезания образа клинка нельзя допускать перегревания детали, даже небольших участков. Поливайте водой заготовку. По окончании работ можно переходить к следующему этапу.
Заточка и шлифовка
В самом начале изготовления ножа вы должны были задуматься: для каких целей он создаётся. Так как заточка для каждого типа изделия абсолютно разная. Но первым делом нужно вывести спуски.
Заострять внимание на них не будем, но запомните: главное в спусках – это симметричность. Только после их выведения, можно приниматься за заточку клинка, но сначала шлифовка. Её можно производить на шлифмашине или при помощи УШМ со специальным кругом. Затем в хвостовике просверливаются два-три несквозных отверстия для крепления рукояти. Во время закалки может случиться неприятность, если просверлить отверстия полностью.
Закалка и отпуск клинка
Очень важный момент, особенно для новичков. Согласно справочнику, температура закалки стали – 830 °С. Разогреть печь, до заданной отметки поможет термометр. Если его нет в наличии, следует воспользоваться одним из способов:
- самый простой и распространённый, проверять магнитом, как только не «прилипает» клинок к нему – цель достигнута;
- следующий очень интересный, посыпать деталь солью, её отметка плавления в 800 °С, значит осталось ещё немного;
- и способ для «прожжённых» профессионалов – цвет заготовки становится светло-красный.
Все способы действенны, но точнее термометра нет ничего. А в данном случае очень важна точность. Нагрев до нужной точки, клинок вынимается и опускается в масло с выдержкой 1 минута на 1 мм толщины изделия. Масло можно использовать практически любое: растительное, минеральное, машинное отработанное или трансформаторное.
Закалка лезвия ножа.Предварительно его нужно подогреть до 50 °С, это необходимо для хорошего обволакивания погружаемого изделия. Производя такие работы, будьте аккуратны, наденьте защитные очки и перчатки, есть вероятность разбрызгивания масла. Не нужно шевелить клинком, когда он находится в погружении.
После охлаждения заготовки пришёл момент для отпуска стали. Процедура ослабит напряжение в структуре кристаллической решётки металла, возникшее при ковке и закалке. В справочнике указанна температура в 150 °С и время 1,5 часа. Разогрев духовой шкаф кухонной газовой плиты, помещаем туда клин на нужное время.
Очистка клинка
После всех проведённых манипуляций, грубой очистки на гриндере, на клинке останутся тонкие, мелкие царапины. Убирать их надо вручную используя наждачную бумагу. Обрабатывать нужно начиная с зерна 400 перпендикулярно царапинам.
Затем переходим к 600-ому зерну и заканчиваем 800-ым. Добиться зеркального блеска, можно использовав пасту ГОИ или специальные шлифовальные смеси.
Подготовка накладок и сборка ножа
Материалов для изготовления рукояти, довольно широкий выбор: различные металлы, пластмассы, кожа, обмотка бечёвкой и прочие варианты. Но многие мастера любят работать именно с древесиной, она часто подчёркивает уникальность клинка и его красоту.
Принцип накладной рукояти довольно прост, и надёжнее, чем другие способы крепления. После отпуска металла можно насверлить отверстия в хвостовике окончательно. А также приготовить брусок:
- Примерить к хвостовику, разметить и придать форму близкую к его размерам.
- Зажав деталь в тиски, разрезать вдоль, строго пополам;
- Для устранения зазоров внутренние части половинок ошкуривают наждачкой.
- Делается разметка в соответствии с отверстиями на хвостовике, и насверливаются в дереве.
- Следующим этапом, можно поступить по-разному, проще всего заклепать ручку клёпками.
- На точильном станке или гриндере обработать рукоять окончательно, под нужную форму вместе с хвостовиком.
- В заключении дерево обрабатывают наждачкой с мелким зерном и пропитывают специальными масляными растворами или покрывают лаком. Зависит от сорта древесины.
Для доведения дела до окончательного варианта можно смастерить ещё и ножны. Но это уже другая и довольно обширная тема. Весь описанный процесс, для новичка может показаться очень сложным. Но люди, занимающиеся этим постоянно, изготавливают такие ножи, словно на конвейере. Так что не расстраиваться при случайных ошибках, продолжать работать, пробовать. И результат не заставит себя долго ждать. Удачи в начинаниях!
ИзготовлениеКак сделать нож из косы своими руками
СледующаяИзготовлениеМонтаж рукояти ножа своими руками
Как сделать складной нож Flipper
Готовая авторская папка-флиппер — отшлифована, отполирована и готова к работе! Готовая авторская папка-флиппер — отшлифована, отполирована и готова к работе! Создание папок сильно продвинулось за последние несколько лет. Теперь флиппер-папки — это новая горячая новость.
Ниже приводится обзор этапов изготовления современного флиппера вручную.
Draw It Up
Детали все вырезаны. Отверстия на одной стороне ручки (в центре) перфорированы по центру и готовы к сверлению.Изготовьте детали ножа из прозрачного пластика, чтобы вы могли видеть, где все расположить.Для начала нарисуйте узоры на бумаге и перенесите их на прозрачный пластик. Вырежьте из прозрачного пластика конструкции лезвия и ручки. Перехватите хвостовик лезвия на рукоятке и проденьте иглу через обе части, где будет шарнирный штифт.
Оттуда сложите лезвие на ручку и при необходимости отрегулируйте конструкцию.
Затем обведите пластиковую ручку на титановом листе. Я использую титан размером 1/8 дюйма для верхней части ручки и.070 дюймов для двух нижних частей. Обведите лезвие и вырежьте его.
Знай своего дела
Перед тем, как просверлить их сверлом на 1/16 дюйма, слегка утопите все отверстия.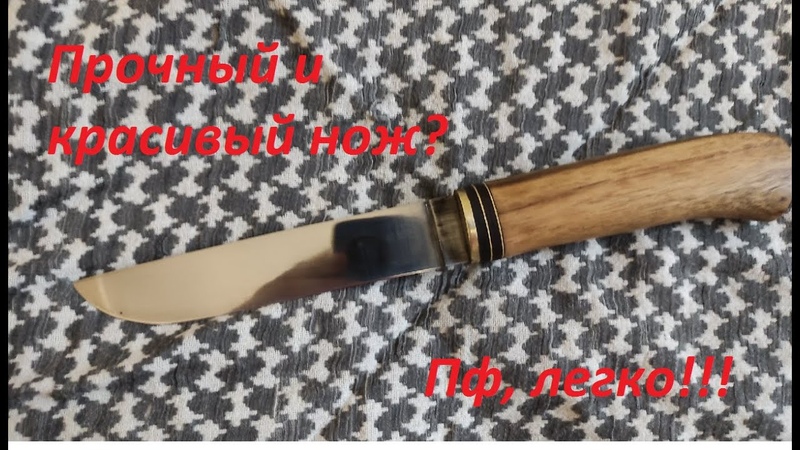
Создание папок — это в основном сверление отверстий. Просверлите одну пластину из титана с отверстиями 1/16 дюйма. Поместите другую пластину из титана под просверленную пластину и скрепите их вместе. Переверните и просверлите вторую пластину.
Начиная с поворотного отверстия, поместите в него закаленный установочный штифт ½x1 / 16 дюйма, чтобы две пластины не двигались.Далее просверлите конец ручки и вставьте в него булавку.
Продолжайте сверлить, зажимать и добавлять штифты в местах, где находятся стойки. Каждый раз, когда вы просверливаете отверстие, разбирайте пластины и снимайте заусенцы. Ручная дрель с зенковкой с четырьмя канавками удобна для удаления заусенцев.
Начните сверлить все отверстия сверлом на 1/16 дюйма. У этого флиппера будет внутренний стопорный штифт, поэтому не просверливайте верхнюю пластину полностью. Однако просверлите нижнюю пластину — 0,070-дюймовую. Отсюда прикрепите пластины с помощью дюбелей 1/16 дюйма.Зажмите, снимите шарнирный штифт, просверлите и разверните до 3/16 дюйма для шарнирного штифта. Удалите заусенцы и снова соберите. Просверлите и разверните стопорный штифт 1/8 дюйма.
ВНИМАНИЕ: Не проходите через верхнюю 1/8-дюймовую пластину полностью! Зенковать внешние пластины под 2-56 головок винтов. Для этого я использую сверло №20.
Поворот, шайбы и пальцы
Фрезеруйте прорезь для стопорного штифта.Теперь пора зенковать два шарнирных винта. На папке можно использовать различные типы распорок и стоек.Для этих ласт я использовала плечи от Knifekits.com. Обычно я использую специальные стойки от Sheffield Knifemakers Supply. Стойки с выступом вниз предотвращают любое нежелательное движение лезвия.
Я проделываю отверстия для стоек, чтобы они поместились с помощью развертки на 1/8 дюйма. На самом деле я использую расширитель на 0,001 дюйма больше, так что это 0,126 дюйма.
Крутая обновка с папками — это шайбы шарнирные с шариковыми опорами. Есть много разных типов, из которых можно выбирать.Майкл Берч порекомендовал мне на BLADE Show стиральные машины от Jantz Supply.
Придется немного утопить шайбы в весы. Для этого я использую 3/8-дюймовую концевую фрезу с четырьмя канавками. Сначала я вставляю концевую фрезу 3/16 дюйма в отверстие на стальной пластине, удерживаемой в тисках. Я блокирую свой стол, вынимаю концевую фрезу 3/16 дюйма и вставляю 3/8 дюйма, используя индикатор с круговой шкалой, чтобы показать, как далеко я сверляю.
Большинство тактических папок довольно толстые с шайбами.От 020 до 0,040 дюйма с каждой стороны лезвия. Я опускаю шайбы так, чтобы они и лезвие были той же толщины, что и стойки. Вы хотите, чтобы расстояние между лезвием и шайбой было равно расстоянию между стойками или прокладочным материалом. Просверлите и просверлите в лезвии поворотное отверстие 3/16 дюйма. Сделайте прорезь в форме полумесяца для стопорного штифта 1/8 дюйма.
Многие производители вставляют штифт в ручку примерно в положение «7 часов» в открытом состоянии. Отшлифуйте ось и стопорные штифты до нужной длины. (Примечание автора: отшлифуйте шарнирный штифт так, чтобы он не выступал за верхнюю часть потайного отверстия шарнирного винта. Отшлифуйте стопорный штифт, чтобы он плавал между двумя шкалами.) Отшлифуйте винты 2-56, чтобы они не закрывались. касаться друг друга, когда они ввинчиваются в стойку.
Профилируйте лезвие и отшлифуйте хвостовик под углом 7 градусов. В качестве ориентира я использую 7-градусный блок Micarta®, который прижимается к моей дисковой шлифовальной машине.
Замок и фиксатор
Отшлифуйте хвостовик, чтобы он соответствовал замку. А теперь пора разрезать замок.Поместите лезвие на нижнюю облицовку так, чтобы шарнир и стопорные штифты были на месте. Откройте лезвие и нанесите ножом X-acto ™ линию за хвостовиком на подкладку. Нарисуйте линию длиной 3 дюйма маркером по шкале. Зажмите мельницу и, используя продольно-резательную пилу, отрежьте кусок длиной 3 дюйма. Используйте ленточную пилу, чтобы отрезать короткую грань, которая будет замком. Используя насадку-отрезное колесо в инструменте Dremel®, очистите конец замка.
На фиксирующем вкладыше или флиппере блокировка выполняется путем загибания язычка титанового вкладыша так, чтобы он вошел в зацепление с концом хвостовика лезвия.Конец этого выступа должен быть покрыт карбидом. Это небольшой ручной аппарат для микросварки, который называется науглероживателем. Просто наденьте стержень на конец титанового фиксатора, и он приваривает карбидное покрытие к титану. Это обеспечивает более плавное действие с папкой.
Вы также можете закрепить замок пламенем, нагревая его до оранжевого цвета. Чтобы стопорная планка изгибалась, протрите вмятину размером 0,020 дюйма с помощью ¾-дюймового колеса на другом конце замка.
Пора просверлить отверстия в замке и лезвии для фиксирующего шарика 1/16 дюйма.Проделайте дыроколом отверстие посередине замка. Просверлите отверстие сверлом №54.
Закройте папку и зажмите ее. Просверлите то же отверстие, что и вкладыш, в лезвие глубиной около 0,060 дюйма. Сверло № 54 имеет диаметр 0,053 дюйма. Вы также можете использовать сверло 0,054 или 0,055 дюйма в зависимости от того, как вы хотите настроить папку. Отшлифовать, термически обработать и отполировать лезвие. Вдавите шариковый подшипник 1/16 дюйма в фиксатор. Оставшаяся высота шарикового подшипника должна равняться толщине шайбы.
Согните фиксатор примерно до середины папки. Теперь отшлифуйте хвостовик под углом 7 градусов на дисковой болгарке, пока фиксатор не начнет заедать. Вы можете собрать папку, поднести ее к свету и отодвинуть фиксатор от ножа, чтобы увидеть, сколько еще вам нужно заточить хвостовик. Двигайтесь медленно и немного потрите, прежде чем проверять замок. Просверлите и постучите по шкале карманного зажима.
Песок и полировка
Наконец, отшлифуйте и отполируйте все. Так же полирую концы шурупов.После сборки папки затяните нижний шарнирный винт и отрегулируйте затяжку действия папки с помощью верхнего винта. Нанесите клей Loctite © на все винты.
А теперь сделай еще один нож из этих книг
Продолжайте читать:
СЛЕДУЮЩИЙ ШАГ: Загрузите бесплатный полный том журнала Vintage
BLADE (4 выпуска) с 1973 года! Загрузите номера журнала BLADE за 1973 год в цифровом формате PDF! Доставляется прямо в ваш почтовый ящик для мгновенной загрузки.
СТАЛИ, ИСПОЛЬЗУЕМЫЕ НОЖНИЦАМИ
СТАЛЬ, ИСПОЛЬЗУЕМЫЕ НОЖЕВОДАМИИнформация и оборудование для заточки ножей
| Главная | | Школы заточки | | Буклеты / DVD / Учебники | | Больше информации | | Карта сайта |
См. также https: // www.osograndeknives.com/catalog/blade-steels.html
СТАЛИ, ИСПОЛЬЗУЕМЫЕ НОЖОМ MAKERS
Боб Энгнант
0-1, пожалуй, самая щадящая сталь из всех ножевых качеств, кроме
очень простые типы сплавов, и производит лезвие отличного качества для
наиболее нормальное использование. Он очень легко поддается термической обработке. Дополнительные ссылки?
Что ж, старый хозяин, Купер, использовал его много лет, и люди его обожают. его лезвия, потому что они крепкие. Некоторое время назад один из лучших
кузнецы клинков сказали, что при хорошем обращении 0: 1 превзойдет любой дамаск, и никакие
один спорил с ним.Удержание края исключительное. 0-1 — точная шлифовка
если только вам не повезет наткнуться на какой-нибудь мельничный стержень. Лох вверх
термообработка и 0-1 позволит вам пробовать снова так часто, как вы хотите, до тех пор, пока
вы не перегреваете металл. Жесткие шлифовальные ленты.
0-6 — это следующий шаг по сравнению с 0-1 легкой термической обработкой, но чистым измельчением. Он значительно более прочный, с более мелкой кристаллической структурой и твердым графитовые частицы, устойчивые к износу. Запас бывает как горячекатаный, так и точная шлифовка.Цены на горячекатаный прокат приемлемые. Очень сложно шлифовать. Края невероятны, служат даже дольше, чем лучший дамаск и даже 0-1. Имеет странную оранжевую искру.
Стали W-1, W-2 и серия 10— с 1045 по 1095 являются
максимальная простота и очень мелкое отверждение, поэтому их можно использовать для
сделайте выборочно закаленное лезвие, как на старых японских мечах. Превосходная ударная вязкость, эти сплавы используются для изготовления ножей грейдеров.
кромки, грузовые пружины и напильники.Использует шлифовальные ленты довольно быстро.
ставка. Края приемлемы для 1045, хороши для 1060, хороши для 1084 и
отлично с 1095, W-1 или W-2. Последние два часто упоминаются как
О-Ф, старый файл. Получить более высокий углеродный конец этой серии очень легко.
слишком сложно сделать хороший нож.
5160 — обычная пружинная сталь, в основном 1060 с одним процентом
хром добавлен для его глубокого затвердевания. (Это может быть выборочно
при желании нарисовать более мягкую спинку.) Отличная сталь для мечей, или
любой другой клинок, которому придется немного побить. Выбор Джима
Хрисулас, который делает одни из лучших рабочих мечей в своем деле.
Длинные лезвия лучше всего подходят к середине 50-х годов по шкале Роквелла, в то время как
небольшие рабочие лезвия могут быть введены в эксплуатацию при полном 60 RC. Кованые
лезвия с хорошо утрамбованной кромкой режут вечно! Черновая шлифовка
ремни. В шутку назывался O-C-S, Old Chevy Spring.
52100 — это сталь для шарикоподшипников, обычно не используемая при шлифовании. размеры, но потрясающие по удержанию кромки и прочности.52100 — это 5160 с отношение, больше сплава и больше углерода, что делает его все труднее и жестче. Подобно 5160, бросает блестящую желтую искру. Эд Фаулер разработал превосходная технология термической обработки этой стали.
L-6 — это сталь для ленточных или дисковых пил, используемых на большинстве лесопильных и
совершенно сложно найти в какой-либо другой форме. Затвердевает в масле до RC 57.
и берет острую кромку для большинства стрижек, особенно там, где кромка может
вернуться в форму.Отлично там, где требуется гибкость
но легко ржавеет, как практически все простые углеродистые стали. L-7 — это
то же самое с чуть большим количеством углерода.
A-2 — это сталь исключительного качества, обладающая прекрасными износостойкими качествами плюс отличная устойчивость к отжигу и короблению. Заметно шлифование сложнее, чем 0-1, но не очень сложно. Пиление сложнее и связывает до пяти процентов хрома в химическом составе этих сталей. Действительно мило закончить шлифовальной машиной, и при полировке появляется очень мало зерна.Отличная гибкость. Фил Хартсфилд получил невероятные режущие способности из этой стали. Несколько других из серии A также сделают прекрасные лезвия.
D-2 предлагает другую инструментальную сталь для закалки на воздухе, но с 12% хрома и
отличная, если не превосходная, износостойкость. Сопротивление также верно
как при распиловке, так и при шлифовании, даже когда сталь полностью отожжена. Пока
использовать ремни быстрее, чем в среднем, D-2 не
особенно трудно шлифовать свежими ремнями.Использование старых ремней вызывает достаточно
нагрейте до закалки стали. D-2 отжигает при несколько более высокой температуре
чем А-2 и правда не возьму, зеркально отполировать. Определенно сталь для
передовой мастер. Главный недостаток — апельсиновая корка.
внешний вид поверхности после доведения до блеска. Один производитель ножей
часто цитируют, говоря, что D-2 берет паршивое преимущество и держит его
навсегда. Часто встречается в виде излишков деревянных лезвий. D-4 и D-7 также
хорошие сплавы для столовых приборов, но чертовски трудно найти подходящие размеры.Воздуха
закалочные стали могут затвердеть во время шлифования, если вы получите
сток слишком горячий. На кофемолке это мало что значит, но когда вы пытаетесь
сделайте защитную выемку, файл будет просто скользить.
М-2 — жаропрочная сталь для токарного режущего инструмента, имеющая
чертовски мало общего с ножами, но позволяет действительно приготовить лезвие в
отделка после термообработки без отжига. М-2, пожалуй, немного
лучше держит ребро, чем D-2. К тому же он довольно хрупкий и не
рекомендуется для больших ножей.
440C был первым общепризнанным производителем ножей из нержавеющей стали и остается
довольно популярны, особенно потому, что процесс отрицательной температуры был разработан для
добавить жесткости. На кофемолке он липкий и быстро нагревается, но режет
намного быстрее и проще, чем любая углеродистая сталь. Ваши ремни будут
сократить примерно в 2–3 раза больше 440-C, чем 0-1. Используя ручные ножовки по нему
в спешке изнашивает множество лезвий.Но при должном уходе хорошо
термообработка и финишная обработка, 440C производит отличные, исправные и
прочный нож, даже для нового производителя ножей. Отжигает при очень низкой
температура. Обратите внимание, что 440A и 440B — похожие сплавы, часто
путают с 440C, но не стоит использовать нож. Коммерческий
производители ножей часто маркируют лезвия 440, когда они
желательные версии, дающие плохую репутацию реальным материалам. 440C также
доступны в большем количестве размеров и в большем количестве мест, чем любая нержавеющая сталь
сплав подходит для ножей.Также важно помнить, что
коллекционеры ненавидят, когда один из их призов становится коричневым в ножнах, и
440C очень хорошо справляется с коррозионной стойкостью. Пока вариация,
440-V кажется не таким сложным, но держит преимущество намного дольше
и шлифовать его гораздо труднее.
154 CM многие считали суперстальными, если удастся найти
старый производственный инвентарь. Новые партии не производятся в
стандарты, которые мы привыкли ожидать от ножевой стали.Хотя отлично в
154 CM съедает лучшие полотна ножовки за один поперечный разрез
1-1 / 2 «. Его обрабатывающие и шлифовальные качества аналогичны 440C и
не получит никаких наград за легкость в работе. Однако при использовании этот сплав имеет
Несомненное преимущество как в твердости, так и в ударной вязкости по сравнению с 440 ° C. 154 CM не является общепринятым стандартным обозначением степени, а скорее
торговое наименование производителя.
АТС-34 японского производства нержавейка считается равной 154 см.Импортировать
ограничения были несколько смягчены, хотя они были вынуждены поднять
цена на 50%. Чище, чем 154 CM. (154 CM больше не используется
в приложениях, определенных правительством, и не является продуктом вакуумной плавки
что мы когда-то ценили.) ATS-34 — практически тот же сплав, что и 154
CM, минус 0,04% одного из менее важных элементов. АТС-34 двухместный
вакуумная расплавленная и очень чистая. Он также имеет твердую черную кожу, которая
сделает вашу шлифовальную ленту сияющей раньше, чем вы это заметите.Мы рекомендуем
сбивание кожи старыми ремнями перед сужением хвостовика или Vee
шлифование. Один парень попытался снять шкуру промышленным мотором
ведомое колесо проволочной щетки. Все, что он сделал, это отполировал. Теперь у нас есть пояс
специально разработан для удаления этого накипи. ATS-34 — торговое наименование. В
три, 154 CM, ATS-34 и 440-C, все имеют небольшую красноватую искру,
отчетливая, но трудно различимая карбоновая вилка. ATS-34 также является
торговое наименование. Эта сверхтвердая черная кожа на некоторых из этих сталей, а также
окалина ковка, можно «протравить», чтобы удалить.Купить галлон недорого
белый уксус и оставьте в нем сталь на ночь. Работает как по волшебству. Если
это не работает, или из-за этого в магазине пахнет салатом, вините Дуга Брэка,
кто дал мне этот намек.
AEBL кажется примерно 440B. Чрезвычайно легко измельчить, на самом деле, я думаю, что
несколько лет назад, возможно, установил мировой рекорд, более ста
лезвия из пруткового материала до зернистости 220 в течение восьми часов. Термическая обработка как
440С. Лучше всего удерживать кромку, когда термообработка включает цикл замораживания. Очень легко полировать и полировать. Очень хороший выбор для миниатюры, кухни.
ножи и т. д. У AEBL есть несколько причудливых привычек в заточке, которые делают его
трудно использовать с более толстыми или большими ножами. Делает хорошие кухонные ножи.
«Хосс» использует это в своем прекрасном дамаске из нержавеющей стали и сообщает, что это
держится очень хорошо.
420 модифицированная нержавеющая сталь, успешно использовалась в некоторых коммерческих производители ножей, но доступность ножей для хобби непрактична производитель, поскольку, черт возьми, немногие из нас заказывают сталь в прокатных валках.
VASCO WEAR довольно дорогая, но очень и очень хорошо держит кромку.
Также очень хорошо сопротивляется шлифованию! Вы поклянетесь, что ваши ремни потускнели
когда вы попробуете. Сделайте все необходимое перед термообработкой, потому что вы
конечно, после этого ничего не получится. По цене как у лобстера
хвосты, когда вы можете их найти. Попробуйте Vasco-Pacific в районе Лос-Анджелеса.
Vasco-Pacific использует свои собственные названия для своих сплавов.
DAMASCUS настолько широко производится, что невозможно
делать слишком много общих заявлений по этому поводу, кроме того, что кажется
коллекционеры лучше любого другого типа.Каждый кузнец делает свое
по-другому, начиная с того, кто выдерживает это, начиная с
три слоя, парню, который сваривает 300-слойный сэндвич из прокладок в
заготовка с одного удара на 40-тонном прессе. Все они хорошенькие. Риз Вейланд
предполагает, что последнее травление дамасского клинка должно быть выполнено фосфорным
кислота, которая как бы паркулирует металл и помогает защитить его. Он сказал
что вам нужно поиграть с концентрацией кислоты и
время погружения немного, в зависимости от используемой стали.Это также
работают на большинстве лезвий из углеродистой стали. Если дамасский клинок закален
с более мягким разделом на позвоночнике или защитном кожухе вы получите гораздо лучшее
если вы сначала используете соляную кислоту, чтобы получить желаемую глубину,
а затем хлорид железа для добавления цвета.
STELLITE 6-K относится к той же категории, что и одежда Vasco Wear. область сопротивления, но не требует термической обработки, так как в ней нет железа это вообще. Хитрость заключается в том, что исключительно твердые частицы помещены в довольно мягкий сплав.Очень гибкий и легко сгибаемый. Практически невозможно довести до зеркальная отделка. Лезвия из стеллита очень востребованы некоторыми коллекционеры. Сплав, который лучше всего подходит для ножей, теперь необходимо заказывать в Канада и стоит около ста баксов за фунт. Часть стеллита Прочность зависит от процесса прокатки, используемого для формирования прутков. Бросать Стеллит далеко не такой прочный.
ТИТАН — металл для лезвия ножа лишь в минимальной степени. Это
не может быть более жестким после середины 40-х по шкале Роквелла С, и
это весна, или территория метательного ножа.Помимо этого, я уверен, что
скоро коллекционные титановые ножи появятся на многих изготовителях по индивидуальному заказу
столы, предназначенные для ловли коллекторов, а не для разделки.
Авторские права 1997 г., Blades ‘N’ Stuff — ВСЕ ПРАВА ЗАЩИЩЕНЫ
Мы ожидаем, что люди будут копировать и распространять эту информацию без
ограничение, пока мы указаны в качестве источника.
| Главная | | Контакты | | О нас | | ССЫЛКИ | | Поставщики | | Фотографии | | Школы заточки |
Авторские права 1996-2021, Стив Ботторфф
История и свойства стали 52100
Спасибо Филу Чжоу за то, что он стал сторонником Knife Steel Nerds Patreon! Я начал публиковать первые результаты испытаний таких вещей, как эксперименты по термообработке, измерения остаточного аустенита и т. Д.на Патреоне. В конечном итоге данные будут размещены на этом веб-сайте, но если вы хотите увидеть их в исходном виде, заходите на Patreon.
52100 История
52100 — относительно простая сталь с 1% углерода и 1,5% хрома и небольшими количествами Mn и Si. Сталь 52100 используется как минимум с 1905 года [1]. Он был разработан для использования в подшипниках. Высокоуглеродистые стали (0,8–1,0% C) в основном использовались до конца 1800-х или начала 1900-х годов [2], после чего стали добавлять хром в подшипниковые стали.Стали с 1% Cr используются в подшипниках по крайней мере с 1903 года [1]. Эти первые легированные хромом подшипниковые стали производились в Германии компаниями Fichtel & Sachs и Deutsche Waffen- und Munitionsfabrik [1]. Хромистые стали французского производства также использовались в подшипниках в тот же период времени [2]. 52100 по-прежнему является наиболее часто используемой подшипниковой сталью [3], поэтому конструкция из стали, безусловно, выдержала испытание временем. Эта сталь имеет много других наименований, таких как 100Cr6, 1.3505, GCr15, En31 и SUJ2.
Обновление 5/8/2019: Ник Данэм опубликовал следующее об истории обозначения SAE 52100 (название появилось позже, чем сталь, конечно):
Похоже, что в 1919 году SAE Iron & Steel Division решили заменить 5295 на 52100 как часть своего седьмого отчета [1].
5295, в свою очередь, было введено как 52-95 в третьем отчете (1912 г.) [2], а дефисы были удалены в пятом отчете (1913-1914 гг.) [3]. С самого начала это была подшипниковая сталь — в третьем отчете о хромистых сталях серий 51 и 52 говорится, что «использование этого типа стали почти полностью ограничивается шариковыми и роликоподшипниками». [2]
Третий отчет также касался введения двузначного префикса ряда [2]; в первом и втором отчетах (1911 г.) использовались только двузначные коды, пронумерованные 1-23 (включая чугунные).Никаких хромистых сталей в списке не было [4]. Это не означает, что хромистых сталей еще не существовало, это просто означает, что еще не существовало спецификаций SAE.
[1] Журнал SAE c1 v4 (1919) https://babel.hathitrust.org/cgi/pt?id=chi.42517057;view=1up;seq=454
[2] Транзакции SAE v7 (1912) https://babel.hathitrust.org/cgi/pt?id=coo.31924058349105;view=1up;seq=75
[3] Бюллетень SAE v5-6 (1913-1914) https://babel.hathitrust. org/cgi/pt?id=umn.31951d00031403a;view=1up;seq=638
[4] Транзакции SAE v6 (1911 г.) https: // babel.hathitrust.org/cgi/pt?id=mdp.3
10782301;view=1up;seq=78
Конец обновления
Эд Фаулер получил определенную заслугу в популяризации 52100 как стали для ножей в наше время. Он произвел много ножей для модели 52100 и много писал о ее достоинствах в колонках Knife Talk в журнале Blade. Эд познакомился с 52100 в виде шарикоподшипников, присланных ему Уэйном Годдардом [5], другим влиятельным производителем ножей, который регулярно писал для журнала Blade. Поскольку подшипники были относительно распространенной формой высокоуглеродистой стали, их использование в ножах, конечно же, имеет гораздо большее значение.Сообщалось о ножах, произведенных еще в 1940-х годах в 52100, включая ножи Уильяма Скагеля [6].
52100 Дизайн
Очевидное отличие 52100 от других высокоуглеродистых сталей, используемых кузнецами, заключается в высоком содержании хрома — 1,5%. Добавление Cr производится по нескольким причинам, которые я описал ниже.
Скорость закалки
Одной из целей добавки Cr является «прокаливаемость», то есть мера того, насколько быстро сталь должна быть закалена от высокой температуры для достижения полной твердости.Простая углеродистая сталь, такая как 1095, требует очень быстрой закалки в воде для полного затвердевания, при этом образуется твердая стальная фаза, называемая мартенситом. 1095 имеет почти 1% углерода, как 52100, но без добавления хрома. Если закалить в медленном масле или дать остыть на воздухе, то образуется некоторое количество «перлита», который снижает твердость стали по сравнению с полным мартенситом. Перлит представляет собой комбинацию 0,02 мас.% Углеродного феррита и 6,67 мас.% Углеродного цементита (Fe 3 C), который образуется чередующимися полосами, поэтому в простой углеродистой стали углерод должен диффундировать на короткое расстояние для полос феррита и цементита. формировать. Хром также обогащен цементитом, поэтому в легированной хромом стали хром также должен диффундировать в цементит с образованием перлита. Хром имеет гораздо больший размер, чем углерод, поэтому он диффундирует медленнее. Таким образом, добавление хрома подавляет образование перлита и повышает прокаливаемость.
Этот эффект закаливаемости можно увидеть на графике время-температура-преобразование (TTT), также называемом графиком изотермического преобразования (IT), где «нос» преобразования (обозначенный как феррит + карбид) выдвигается на более длительное время в 52100 по сравнению с 1095.Это позволяет подшипникам быть полностью закаленными, чтобы они имели достаточную прочность и, следовательно, противостояли деформации во время использования. Сердцевина подшипника во время закалки охлаждается медленнее, чем поверхность, поэтому более высокая закаливаемость позволяет использовать подшипники большего размера. 52100 все еще не является сталью с высокой закалкой и не считается действительно закаленной в масле сталью, такой как O1 (в отличие от закаленной в воде). Для крупных подшипников, требующих более высокой прокаливаемости, были разработаны модифицированные версии 52100. Версия с более высоким содержанием Mn была представлена в середине 1930-х годов, а версия, легированная молибденом, — после Второй мировой войны [7].Однако ни одна из этих версий не нашла значительного применения в ножах.
«Носик» кривой в TTT для 1095 фактически выходит за пределы графика, потому что время очень короткое. Требуется очень быстрая закалка, чтобы избежать мягкого перлита
.«Носик» 52100 TTT составляет примерно 3 секунды, что позволяет менее жесткую закалку для достижения полной твердости
Влияние хрома на размер карбида
Карбиды — это твердые частицы в стали, которые улучшают износостойкость, но снижают ударную вязкость или сопротивление растрескиванию.Следовательно, для применений, требующих высокой износостойкости, желательно большее количество карбидов. Применения, требующие высокой вязкости, обычно требуют, чтобы карбиды были как можно меньше и имели небольшую их объемную долю. Типичная высокоуглеродистая сталь, такая как 1095, образует твердые частицы карбидов железа, называемые цементитом, с тремя атомами железа на каждый атом углерода: Fe 3 C. Высокохромистые стали образуют карбид хрома, например Cr 7 C 3 или Cr 23 С 6 .Некоторые ошибочно полагают, что 52100 образует один из этих типов карбида хрома. Однако в нем недостаточно хрома для образования таких карбидов. Вместо этого часть хрома обогащается цементитом, образуя M 3 C, где M может относиться либо к железу, либо к хрому. Цементит 52100 содержит около 9 мас.% Хрома [8].
Добавление Cr помогает уменьшить размер карбида. Меньшие карбиды означают лучшую вязкость и устойчивость к разрушению. 52100 известен своим очень маленьким размером карбидов и высокой плотностью карбидов, даже по сравнению с другими углеродистыми и легированными сталями, такими как 1095.Размер карбида уменьшается по аналогичному механизму увеличения прокаливаемости. Перед поставкой стали конечному потребителю сталь отжигается, чтобы сделать ее мягкой для механической обработки, и подготовить ее для окончательной термообработки. Одним из методов отжига является медленное охлаждение стали от высокой температуры до образования перлита с последующей промежуточной температурной обработкой, при которой перлитная структура «сфероидизируется» с образованием небольших круглых карбидов [9]:
Поскольку Cr входит в состав карбидов, который диффундирует медленнее, чем углерод, расстояние между цементитом в перлите меньше, и тогда скорость «сфероидизации» и роста круглых карбидов снижается.Вот изображения [10], сравнивающие 52100 (вверху) с 1095 (внизу), где белые частицы являются карбидами. 1095 вполне хорош, но 52100 имеет большую плотность карбидов, а максимальный размер карбидов меньше 1095.
52100
1095
Карбидная фракция и углерод в растворе
При сравнении сталей при такой же высокой температуре закалки, но с увеличением содержания углерода, количество углерода в растворе остается постоянным, но количество карбида увеличивается. Вы можете увидеть это, посмотрев на приведенную ниже фазовую диаграмму железо-углерод; черный кружок на линии представляет углерод в растворе, который не изменяется с увеличением содержания углерода. Однако при более высоком содержании углерода линия распространяется дальше в поле «аустенит + цементит», указывая на присутствие большего количества цементита.
На фазовой диаграмме представлена микроструктура стали при различном содержании углерода и температурах. При температуре 1400 ° F и содержании углерода около 0.55-0,7% сталь находится в «аустенитной» области, где нет карбидов / цементита. При закалке от этой температуры конечная микроструктура представляет собой твердый мартенсит без карбидов. Если содержание углерода увеличивается выше 0,7%, тогда карбиды присутствуют при высокой температуре, что приводит к окончательной микроструктуре мартенсита с карбидами. Карбиды способствуют износостойкости. Чем больше углерода добавлено свыше 0,7%, тем больше присутствует карбид:
Количество углерода «в растворе», вносящее вклад в твердость, остается неизменным при фиксированной температуре, несмотря на увеличение объемного содержания углерода, поскольку углерод способствует образованию карбида. Однако, если температура повышается, углерод в растворе поднимается по линии. Если мы посмотрим на сталь с 1% углерода при температуре 1400 ° F (точка 1), в растворе будет столько же углерода 0,7%, что и в стали с любой другой сталью с содержанием углерода более 0,7%. Пунктирными линиями показано содержание углерода в растворе в зависимости от валового состава стали. При 1450 ° F в растворе содержится 0,8% углерода (точка 2) и 1% углерода в растворе при температуре около 1570 ° F (точка 3). Длина пунктирной линии укорачивается с повышением температуры, указывая на то, что количество карбида уменьшается, до точки 3, где карбид больше не присутствует, и он достигает поля «аустенит»:
Добавление 1.5% Cr сдвигает фазовую диаграмму железо-углерод в сторону более высоких температур и более низкого содержания углерода:
Сдвиг на фазовой диаграмме означает, что при том же объемном содержании углерода в растворе меньше углерода, а объемная доля карбида больше. Вот почему рекомендуемые температуры затвердевания / аустенизации 52100 выше 1095, обычно 1550 ° F, а не 1475 ° F. Уменьшение содержания углерода в растворе по сравнению с 1095 помогает улучшить ударную вязкость, так как содержание углерода выше примерно 0.6% в растворе приводит к образованию пластинчатого мартенсита, который снижает ударную вязкость. Экспериментально 52100 содержит около 0,63% углерода в растворе с закалкой от 1550 ° F [11], что обеспечивает максимальную твердость без образования пластинчатого мартенсита. Более низкие температуры закалки дополнительно уменьшают содержание углерода в растворе для повышения прочности. Подробнее о твердости стали вы можете прочитать в этой статье. Увеличение доли карбида также улучшает износостойкость 52100, где термически обработанный 52100 имеет около 6-10% объема карбида [12], а 1095 — примерно вдвое меньше.
Простота ковки, закалки и термообработки
Благодаря низкому содержанию хрома по сравнению с закаленными на воздухе сталями, такими как A2 или D2, 52100 является хорошим выбором для ковки. В нем нет карбидов, присутствующих при температурах ковки, как в сталях, закаленных на воздухе, что означает, что он легче перемещается под действием молотка. Его средняя или низкая закаливаемость также делает его хорошим выбором. Низкая закаливаемость 1095 означает, что для закалки требуется вода или очень быстрое масло, тогда как 52100 более щадящий при более медленной закалке.Более медленная закалка снижает риск коробления и образования трещин при закалке. Более закаливаемая сталь, такая как O1, или стали, закаливаемые на воздухе, очень просты с этой точки зрения, но это затрудняет их отжиг без печи с контролируемой температурой. Эти стали также трудно или невозможно нормализовать, поскольку они затвердевают при охлаждении на воздухе, а не образуют желаемый перлит. Стали с высокой закаливаемой способностью также более склонны к растрескиванию при ковке при более низких температурах или просто при охлаждении до комнатной температуры после ковки.Следовательно, уровень закаливаемости в 52100 является хорошим компромиссом для гибкости при закалке, в то же время его можно нормализовать и отжиг с помощью простого цикла.
Однако повышенные температура и время, необходимые для аустенизации по сравнению с простой углеродистой сталью, делают аустенизацию более трудной при термообработке в кузнице или с помощью горелки, а не в печи с ПИД-регулированием.
Термическая обработка 52100
Теперь у нас есть отдельная статья о том, как лучше всего термически обрабатывать 52100.
Как обсуждалось выше, повышение температуры закалки / аустенизации до 52100 приводит к увеличению содержания углерода в растворе и уменьшению доли карбида. Это также видно экспериментально, хотя числа несколько отличаются от тех, которые предсказываются на фазовых диаграммах, поскольку эти предсказания относятся к бесконечному времени выдержки при температуре, в отличие от 10-30 минут, используемых при термообработке. По мере увеличения содержания углерода в растворе количество остаточного аустенита после закалки также увеличивается.О том, почему, вы можете прочитать в статье о криогенной обработке стали. Пик твердости происходит при температуре аустенизации около 1650 ° F; выше этого образуется избыточный остаточный аустенит, который снижает твердость. Вот зависимость объема остаточного аустенита и карбида от температуры аустенизации [8]:
При более низких температурах отпуска и более высоких температурах аустенизации твердость увеличивается. Использование 1650 ° F и 300 ° F дает примерно 66 Rc [8], хотя это условие, вероятно, также приводит к относительно низкой ударной вязкости.Типичная термообработка аустенитизации при 1550 ° F и отпуска при 400 ° F дает около 61,5 Rc. Многие производители ножей используют 1475 ° F и 400 ° F, что дает около 59,5 Rc. Я не совсем уверен, почему они используют 1475 ° F, возможно, это происходит из-за копирования рекомендованных термообработок из 1095. Изготовители ножей, как и многие другие люди, любят круглые числа, поэтому температура аустенизации, которая приводит к круглому числу 60 Rc после хорошее круглое число, температура 400 ° F, вероятно, привлекает.
Использование более низких температур аустенизации может привести к повышению ударной вязкости, о чем вы можете прочитать в этой статье об аустенизации.Обычно лучше снизить как температуру аустенизации, так и температуру отпуска, чем поддерживать ту же температуру аустенизации и повышать температуру отпуска. Одна из причин заключается в том, что содержание углерода в растворе уменьшается при более низкой температуре аустенизации, как описано выше. Другой проблемой является диапазон «мартенситного охрупчивания при отпуске» (TME) при слишком высоком отпуске, вы можете увидеть падение ударной вязкости на рисунке ниже при использовании температуры отпуска 230 ° C (450 ° F). Подробнее о TME можно прочитать в Эта статья о добавках кремния, элемента, который минимизирует охрупчивание.Вы можете увидеть улучшенную ударную вязкость 52100 при более низкой температуре аустенизации на этом рисунке [11]:
Повышение температуры аустенизации также увеличивает твердость, но даже когда вязкость отображается в зависимости от твердости, улучшение с более низкой температурой аустенизации все еще сохраняется. Я удалил условия после закалки и отпуска при 230 ° C, потому что в этих условиях была низкая ударная вязкость:
Тройная закалка
Эд Фаулер также популяризировал «тройную закалку» 52100, процесс, при котором сталь подвергается аустенитизации и многократной закалке для измельчения зерна и повышения вязкости.52100 не особенно хорошо подходит для тройной закалки, чем другие низколегированные стали, но 52100 часто присоединяется к нему, поэтому об этом стоит упомянуть. В этой статье я писал о том, как работает многократное тушение, и о его потенциальных преимуществах. Мы также выполнили тройную закалку CruForgeV и проверили его прочность, но не обнаружили улучшений, о которых вы можете прочитать в этой статье.
Аустемперинг и бейнит
52100 относительно хорошо подходит для аустеперирования с образованием бейнита, в отличие от образования мартенсита с помощью термической обработки закалкой и отпуском.Аустперирование включает закалку до промежуточной температуры, такой как 500 ° F, и выдержку в течение нескольких минут или часов, что приводит к образованию бейнита, который представляет собой фазу, аналогичную отпущенному мартенситу, но с несколько другими свойствами. Есть некоторые свидетельства того, что бейнит имеет большую вязкость, чем отпущенный мартенсит. Вы можете узнать больше о бейните и некоторых экспериментах, которые проводились с 52100, в этой статье о закалке. Когда сталь обладает высокой способностью к закаливанию, аустализация занимает слишком много времени, чтобы ее можно было осуществить.Для достижения высоких уровней твердости необходимо относительно высокое содержание углерода при аустемперировании. Таким образом, 52100 имеет хорошее сочетание высокой углеродистой и средней закаливаемости для облегчения закалки.
Прочность 52100
Несмотря на все исследования 52100, довольно сложно найти хорошие сравнения с точки зрения ударной вязкости по сравнению с другими сталями. Многие исследования сосредоточены на самой 52100, так как это отправная точка — наиболее часто используемая подшипниковая сталь.Инструментальная сталь [13] оценивает 52100 как «4» из 10, что похоже на A2, выше, чем у O1, M2 и D2, и ниже, чем у L6 и ударопрочных сталей, согласно книге. Вскоре мы протестируем образец 52100 для сравнения с нашим текущим набором данных по прочности. И если кто-то знает какие-либо опубликованные данные о сравнительной стойкости, пришлите их мне. Используя рейтинг инструментальной стали , мы можем поместить 52100 в ряд других сталей с указанными значениями вязкости из Crucible [14] [15] [16] [17]:
Удержание края 52100
Удержание кромок у 52100 не очень высокое, как у других углеродистых и низколегированных сталей.Относительно небольшой объем карбида в сочетании с низкой твердостью цементита означает, что существуют другие стали с гораздо более высокой износостойкостью и сохранением режущей кромки. В тестах CATRA, проведенных Verhoeven [18], было обнаружено, что 52100 имеет лучшее удержание кромок, чем 1086 и Wootz Damascus, хотя и не так хорошо, как AEB-L, нержавеющая сталь. 1086 — это низкоуглеродистая сталь с меньшим объемом карбидов, а AEB-L имеет более твердые карбиды хрома, поэтому результат имеет смысл. Вы можете узнать больше о том, насколько хорошо 52100 удерживает режущую кромку по сравнению с другими сталями, в статьях по удержанию кромок CATRA: Часть 1 и Часть 2.
В испытаниях на разрезание каната, проведенных Уэйном Годдардом [19], было обнаружено, что 52100 имеет такое же удержание режущей кромки, как и другие стали 60 Rc; в его испытаниях влияние стали было меньше, и твердость была основным фактором, хотя Vascowear (CruWear) был несколько лучше:
Сводка
52100 был разработан в начале 1900-х годов и впервые использован в 1905 году. Он был разработан для использования в подшипниках. Он использовался во многих ножах, отчасти из-за его хороших свойств при ковке, а отчасти потому, что подшипники являются легким источником стального лома.Добавление хрома улучшает прокаливаемость и уменьшает размер карбида для улучшения ударной вязкости. Добавление хрома также означает, что 52100 требует более высоких температур аустенизации и имеет больший объем карбида по сравнению с простой углеродистой сталью для повышения износостойкости. Комбинация уменьшенного размера карбида и увеличенной объемной доли карбида дает 52100 хорошее сочетание ударной вязкости и износостойкости по сравнению с другими углеродистыми и легированными сталями. Более низкие температуры аустенизации приводят к повышению ударной вязкости.Средняя закаливаемость 52100 означает, что он хорошо подходит для ковки, а также является хорошим кандидатом для закалки с образованием бейнита.
[1] Хенгерер Ф., «История SKF3», Ball Bearing Journal 231, вып. 1. С. 2-11.
[2] Стрибек Р. «Шариковые подшипники для различных нагрузок». Пер. ASME 29 (1907): 420-463.
[3] Юки, Хироши, Мию Сато и Чикара Оки. «Влияние условий индукционного нагрева на закаленную структуру стали SUJ2». ISIJ International 58, нет.9 (2018): 1735-1741.
[4] https://www.bladeforums.com/threads/question-about-52100.259561/
[5] Fowler, Ed. Разговор о ножах: искусство и наука изготовления ножей . Иола, Висконсин: Публикации Краузе, 1998.
[6] https://www.bladeforums.com/threads/question-about-52100.259561/
[7] Каппель, Юрген, Матиас Вайнберг и Райнхольд Флендер. «Металлургия роликоподшипниковых сталей». Стальные захваты 2 (2004): 261-268.
[8] Стиклс, К.A. «Термическая обработка карбидного рафинада подшипниковой стали 52100». Металлургический труд 5, вып. 4 (1974): 865-874.
[9] Нуталь, Николя, Седрик Дж. Гоммес, Сильвия Блахер, Филипп Путо, Жан-Поль Пирар, Фредерик Бошини, Карл Трайна и Руди Клус. «Анализ изображений сфероидизации перлита на основе морфологических характеристик частиц цементита». Анализ изображений и стереология 29, вып. 2 (2011): 91-98.
[10] https: // matdata.asminternational.org/mgd/index.aspx
[11] Сантьяго, Рескальво и Хосе Антонио. Разрушение и рост усталостной трещины в подшипниковой стали 52100, М-50 и 18-4-1 . Дисс. Массачусетский технологический институт, 1979 г.
[12] Стиклс, К. А. «Термическая обработка карбидного рафинада подшипниковой стали 52100». Металлургический труд 5, вып. 4 (1974): 865-874.
[13] Робертс Г. А. и Роберт А. Кэри. Инструментальная сталь . Бичвуд, Огайо: Американское общество металлов, 1980.
[14] https://www.crucible.com/eselector/prodbyapp/tooldie/ketos.html
[15] http://www.crucible.com/PDFs/DataSheets2010/ds3Vv1%202015.pdf
[16] https://www.crucible.com/eselector/prodbyapp/tooldie/champloy.html
[17] http://www.crucible.com/PDFs/DataSheets2010/Data%20Sheet%204V.pdf
[18] Верховен, Джон Д., Альфред Х. Пендрей и Ховард Ф. Кларк. «Испытания на износ стальных лезвий ножа». Износ 265, № 7-8 (2008): 1093-1099.
[19] https://sharpeningmadeeasy.com/edge.htm
Нравится:
Нравится Загрузка …
СвязанныеПодшипники шарнира ножа — технология ножей, объясненная на KnifeArt.com
Ларри Коннелли
Во многих складных ножах единственная втулка (или шайба) используется в шарнире, чтобы обеспечить плавное вращательное движение лезвия. Многие производители ножей решили использовать материалы втулки, такие как тефлон, нейлатрон, нейлон и фосборную бронзу, чтобы уменьшить трение металла о металл и возможность истирания.Истирание — это особый металл при трении скольжения по металлу, эта адгезия на атомном уровне вызовет повреждение металлических поверхностей. Некоторые втулки в ножах были улучшены за счет добавления перфораций во втулках, эти перфорации уменьшают площадь поверхности, уменьшают трение и могут удерживать смазку.
Основные втулки или шайбы из нержавеющей стали — размер рядом с шарниром.
Однако в некоторых новых ножах чаще используются опорные шарниры всех типов, чтобы улучшить раскрытие лезвия.Прежде чем мы перейдем к типам подшипников, вот краткое изложение преимуществ и недостатков шарниров подшипников и различий в типах подшипников.
Терминология
Шарикоподшипник — круглый шарик, который предназначен для катания по поверхностям, материалы могут различаться.
Гонка — зона, в которой шарикоподшипники перемещаются и соприкасаются с двумя поверхностями. Кольцо из закаленной стали может использоваться для уменьшения износа незакаленных поверхностей, таких как титан или другие материалы рукоятки, и уменьшения износа от концентрированного давления и трения.
Клетка — дополнительный корпус, в котором подшипники могут перемещаться, удерживая подшипники в фиксированном положении. Могут быть выполнены из различных материалов и конструкций.
Упорный подшипник — цилиндр, а не шарик, который предназначен для катания между двумя поверхностями.
Плюсы и минусы подшипников
Уменьшение трения — шарниры подшипников встроены в шарниры ножей, поскольку они значительно уменьшают трение при открытии и закрытии лезвия. Часто подшипники используются на ножах с открывателями плавников.Подшипники уменьшают контакт металла с металлом, что приводит к быстрому плавному развертыванию лезвия при каждом его открытии или закрытии. Проще говоря, подшипники уменьшают трение.
Техническое обслуживание — к недостаткам подшипников можно отнести необходимость значительного технического обслуживания и ухода. Пользователи ножей должны обязательно смазывать и очищать подшипники, используя крышки, чтобы защитить их от грязи и мусора. Кроме того, подшипники из углеродистой стали могут ржаветь и разрушаться.
Износ — Возможно, подшипники со временем изнашивают подшипник или дорожку качения.В первую очередь изнашивается более мягкий из двух материалов — подшипник или кольцо подшипника. Кроме того, без надлежащей техники и подшипников может не хватать прочности на скручивание.
Толщина — подшипники также могут требовать использования дорожек. Гонки — это поверхность, по которой подшипники движутся для уменьшения износа. Требование наличия дорожек может потребовать более толстого корпуса в рукоятке ножа, чем использование втулки. Однако существует множество различных типов опорных систем для ножей, каждая из которых имеет разную прочность.
Стоимость — качественные подшипниковые системы позволяют увеличить стоимость ножа.
Типы шарниров подшипников
К наиболее распространенным типам шарниров подшипников в ножах относятся:
Шарнирный шарнир (открытый): также известный как шарнирная система с шарикоподшипником без сепаратора, в этом типе подшипников используются открытые шарикоподшипники. на шарнире лезвия. Шарики удерживаются на месте в обработанных рельефах на лезвии или рукоятке. Нож, использующий этот тип подшипника, включает в себя ось подшипника IKBS.Подшипники ослаблены, внутри съемника и, как правило, нет качения.
Шарикоподшипник с сепаратором (шарикоподшипники в корпусе): в этой системе используется меньше шариков, чем в эквивалентном шарнире открытого подшипника, удерживаемом в клетке (конструкции), что упрощает техническое обслуживание.
Подшипники с сепаратором с шариками из нержавеющей стали. Спереди и сзади.
Подшипники с сепаратором и керамическими шариками. Спереди и сзади.
Схема упорного подшипника (Источник: Silberwolf)
Упорные цилиндрические роликоподшипники: используются цилиндры вместо шариков, эти подшипники создают большее трение, но при этом более высокая устойчивость при кручении.
Многорядный подшипник: в этой системе используются многорядные подшипники с сепаратором, обеспечивающие большую устойчивость при кручении. Пример ножа, использующего такой тип поворотной системы, включает некоторые модели Широгорова.
В целом шарниры подшипников могут быстро и плавно раскрыть нож. Хотя они требуют некоторого обслуживания и ремонта. Учтите, что у этой технологии есть свои плюсы и минусы. Если вам нужны низкие эксплуатационные расходы и безотказный шарнир, мы рекомендуем стандартную втулку. Если вы готовы очистить смазку и уберечь нож от мусора, шарнир подшипника может обеспечить чрезвычайно быстрое открытие с уменьшенным трением, что особенно полезно для флипперов.
Товар с добавленной стоимостью, произведенный KnifeArt. com. Если вам понравилась статья, и она поможет вам в ваших знаниях о ножах, мы будем рады видеть вас нашим клиентом. Ссылки и социальные сети также приветствуются.
Авторские права — Все права защищены
Бронзовый подшипник режущей кромки для тонармов SME [английский]
Бронзовый подшипник режущей кромки для тонармов SME
Хороший твик для любителей малого и среднего бизнеса
[Итальянская версия] Продукт: Бронзовый подшипник с режущей кромкой для тонармов SME
Производитель: www.analogtubeaudio.de,
АНАЛОГОВЫЙ ТРУБНЫЙ АУДИО, Am Gitter 2, 27568 Бремерхафен, Германия
Приблизительная стоимость: от 159 евро / доллар в Германии, 2003 г.
Рецензент: Хартмут Кващик — TNT, Германия
Проверено: ноябрь 2002 г. (обновлено в марте 2003 г.)
Некоторое время назад друг обратил мое внимание на статью о настройке тонармов SME старого образца с бронзовым ножевым подшипником. Поскольку я всегда был поклонником старых тонармов SME, я хотел попробовать. Терпеливо ждем несколько недель после заказа — обратите внимание, что эти
подшипники производятся небольшими партиями — наконец-то достался этот шедевр
обработки с ЧПУ.
Я не хотел использовать для тестирования свой SME3012-2, установленный на моем TD124, потому что он работает в гостиной, и моя леди категорически против изменения Hi-Fi в гостиной. Итак, я проверил это в SME3009RM на проигрывателе Solist. Поворотный стол — немецкий специалист небольшая производственная линия подвесной палубы с конца 80-х годов и много рейв, по звучанию это что-то среднее между Linn LP12 и Scheu. Я взял Картридж Ortofon SPU GM / E для тестирования.
Так как запчасти SME у меня уже были от SME3009-ser2
улучшилось, у меня была редкая возможность послушать три разных ножа
краевые подшипники в один вечер: стандартный пластиковый варинт SME, дополнительный
дорогой стальной вариант и новый бронзовый вариант.Я взял запись из
Дженнифер Уорнс «Знаменитый синий плащ», который я не слушала. месяцы.
Делаем модификацию
Замена подшипников режущей кромки 30 минут в первый раз и 10 минут во второй раз (см. Шаг 5, чтобы понять, почему). Он состоит из следующих шагов:
- снимите вилку (ту часть тонарма, где крепится противоскользящая планка) — Примечание: отсюда жизненно важно будьте осторожны: не рвите трубку руки со зверской силой, иначе вы порвете внутренние кабели.
- снимаем винт заднего подшипника, затем берем с задней части тонарма, осторожно нажимая на нее.
- снимите винт переднего подшипника. Сквозь это, ушко заземления, удерживаемое этим винтом, будет освобождено
- поменять подшипники, расположив короткие конец к тылу
- (это действительно немного сложно) вам нужно указать,
но сильный пинцет, который вы вставляете в трубку руки сзади, чтобы держать
проушина заземления в положении, позволяющем завинтить винт переднего подшипника
внутрь через подшипник.ОК, либо тебе нужно четыре руки, либо немного
удача или навыки.
- (6-8) обратны шагам 3-1, поэтому они очевидно, и они не доставляют вам хлопот.
Как это звучит
Оригинальный стальной ножевой подшипник имеет сильный, яркий, но немного искусственный звук (как CD что-то звучит синтезированы), силиланты слишком острые и ярко выраженные, что дает некоторые неудобные чувство. Обнаруживается легкий звон, иногда напоминающий Трубка рычага сделана из стали.Бронзовый подшипник режущей кромки имеет много более изысканные свистящие звуки, более спокойное звучание, в то же время более динамичный, изящный и естественный. Голоса приносят больше всего, получают больше реалистично. Звуковая сцена открывается дальше, чем с другими подшипниками и басами и информация о высоких частотах также лучше определяется. Здесь не обнаруживается звонка, это было большим сюрпризом, так как я не менял стальную трубку, только несущий.
Пластиковый подшипник острия ножа звучит
однородный и очень красивый, но немного убогий и скучный по сравнению с первым
два подшипника. Динамика была немного плоской, а басы хилые. Сибилианц имеют
был представлен хорошо.
Выводы (для МСБ 3009Р)
При использовании с бронзовым подшипником SME 3009R напоминает старого боевого коня SME3009-2 шестидесятых годов по музыкальности, а точнее по плавности и естественности. До сих пор это было решение сердца для владельцев Garrard или Verdier: взять старый SME 3012/2, который звучит такой музыкальный, или новый SME3012RM, который звучит чище, но в то же время «холодно». Большинство людей, знающих различия, выбирают старый тонарм, когда есть возможность получить один в хорошем состоянии.
Рекомендую бронзовый подшипник? Да!
Владельцы SME3009R с пластиковым ножом
краевой подшипник, который всегда думал о переходе на металлический ножевой подшипник,
теперь у них есть опция, которая дешевле (примерно на 30% меньше) и по звуку
больше награды. Но апгрейд подшипников интересен и владельцам.
SME3009RM со стальными подшипниками с режущей кромкой, так как звуковые преимущества
намного превосходят те, которые вы можете купить за те же деньги на картриджи.
Последующее наблюдение (испытание в SME 3012/2)
Тем временем я испытал бронзовый подшипник. в SME3012 / 2 (SME старого образца 60-х годов, с алюминиевой трубкой) и Я был удивлен, обнаружив совершенно разные результаты.SME3012 / 2 был смонтирован в Loricraft-Garrard 401 с 12-дюймовым цоколем, что действительно красиво настраивать. Картридж был таким же, как и в тесте раньше, когда я использовал SME3009R. При замене подшипников со временем порвался внутренний провода и пришлось перемонтировать тонарм, затем ждал несколько дней, чтобы новый проложены кабели. Сменить подшипник гораздо сложнее. серии SME30xx / 2, так как нет доступа сзади в трубку рычага, обычно. Кроме того, есть ранние модели, в которых винт переднего подшипника удерживает проушину для заземляющего кабеля и дополнительную миниатюрную гайку вместо ушко с ниткой.
Я даже несколько раз менял подшипники, чтобы быть уверенным, потому что результаты довольно странные. Короче говоря: бронзовый подшипник улучшил разрешение мелких деталей и
улучшил шипение по сравнению со старым стальным ножевым подшипником, бас
глубина и звуковая сцена уменьшились, и, что еще хуже, тонарм потерял
очарование, или, другими словами, его певческие качества.
Выводы (для SME3012 / 2)
SME3009R имеет нержавеющую сталь толщиной 0,25 мм. стальная трубка рычага, тогда как более старый SME 3012/2 оснащен 0.5 мм алюминий рука трубка. Из-за этого результаты этого теста нельзя просто передать к SME3012 / 2, так как он ведет себя иначе с бронзовым подшипником. Имейте в виду, что старые SME3009 / 2 и SME3012 / 2 уже звучат отлично со стальными подшипниками с режущей кромкой. Подведем итог: модификация рекомендуется для тонармов серии R, но не рекомендуется для старых серий 2 тонарма.
Сравнение модифицированного SME3009R с немодифицированным SME3012 / 2
Мне тогда было любопытно, насколько лучше SME3009R по сравнению с немодифицированным старым тонармом. Для этого сравнения я использовал автономную базу тонарма с отверстием SME и слушал на своем Плутоне.
Поворотный стол на 10А. Я использовал тот же картридж Ortofon SPU GM / E. Измененный
SME3009R победил по расширению басов, высокочастотному разрешению, разрешающей способности
мелких деталей, даже PRAT был лучше. Старый SME3012 / 2 устоял против
это более удобная, очаровательная презентация с соблазнительными средними частотами,
который всегда напоминал мне ламповый усилитель. Хотя ни один тонарм не был
так же хорошо, как мой Шредер
№1 с картриджем Ortofon Rohmann.
Copyright 2003 Hartmut Quaschik — https://www.tnt-audio.com
Создайте скользящий нож для вашего фрезерного или фрезерного станка с ЧПУ
Ножи действительно удобны для резки мягких материалов, таких как винил, картон, матовый картон, поролон, шпон, кожа и многие другие. С плоскими листами вы можете использовать их, например, для создания нестандартной упаковки для некоторого продукта или, по крайней мере, для создания прототипа упаковки. Коммерческие ножи легко изготовить, но они могут быть немного дорогими для любителя.Недавно я наткнулся на отличный пост CNCZone для этого перетягивающего ножа:
Drag Knife от Grunblau…
Здесь он разбит на составные части:
Компоненты Drag Knife…
Как видите, он довольно простой и его довольно легко построить. Главное при его разработке — удерживать лезвие так, чтобы у него был вертикальный тупой край, который находился довольно близко к оси вала, но все же был достаточно отклонен от оси, чтобы иметь небольшой эффект заклинания.Доступны более изящные перетягивающие ножи, которые даже включают сервопривод 4-й оси для управления направлением ножа, но вы можете многое сделать с помощью саморегулирующегося перетягивающего ножа. Иногда более простые решения оказываются лучшими.
Программирование одного из этих перетягивающих ножей может потребовать от вас выполнения так называемого «углового действия». Чтобы получился плотный угол, вы должны поднять лезвие вверх так, чтобы наконечник едва касался материала — ровно настолько, чтобы материал едва мог захватить его, когда он вращается в подшипниках. Теперь запрограммируйте нож так, чтобы он двигался по небольшому кругу вокруг кончика, чтобы переставить его в том направлении, в котором вы хотите двигаться.Опуститесь на глубину резания, и вы готовы к выходу.
Если вы хотите закруглить все углы, нет необходимости в специальных поворотах. Без угловых действий почти любое программное обеспечение CAM даст вам достойный результат с перетаскиванием ножа. Просто используйте траекторию в стиле гравировки, которая следует линии на вашем чертеже.
Завершим красивым видео на YouTube о проекте:
Обратите внимание на то, что он использовал WD-40 при резке алюминия. Хорошая идея!
Совет. Найдите в нашей библиотеке бесплатные файлы DXF, которые можно вырезать перетягивающим ножом.
Нет времени делать перетягивающий нож?
Не беспокойтесь, они коммерчески доступны. «Донек», наверное, самый известный бренд.
В видео-демонстрации показаны довольно удивительно острые разрезы, выполняемые на высоких скоростях, потому что нож сам ориентируется. Подходит для обычных лезвий универсального ножа, бывает 2-х размеров.
ОсновательDonek Шон Мартин изобрел Donek Drag Knife, чтобы вырезать графику для пользовательских сноубордов, которые он делал на своем фрезерном станке с ЧПУ Shopbot.
Нравится то, что вы читаете на CNCCookbook?
Присоединяйтесь к более чем 100 000 ЧПУ! Получайте наши последние сообщения в блоге, которые доставляются прямо на ваш почтовый ящик один раз в неделю бесплатно. Кроме того, мы предоставим вам доступ к отличным справочным материалам по ЧПУ, включая:
- Наш большой список из более чем 200 советов и методов ЧПУ
- Наш бесплатный курс по основам программирования GCode
- И многое другое!
Просто введите свое имя и адрес электронной почты ниже:
100% конфиденциальность: мы никогда не будем спамить вам!Изготовление ножей: как сделать нож из старого гаечного ключа
Это испытание по изготовлению ножей откроет внутри вас кузнеца и позволит превратить старый гаечный ключ в нож!
Повысьте свои навыки изготовления ножей и превратите старый гаечный ключ в оружие
Принадлежности для ковки ножей
Изготовление ножей: Сделайте нож из старого гаечного ключа — Survival Life https: // t.
co / BN7yP0ovNm pic.twitter.com/bxUcw0pmKu
— ASDefense.com (@ASDknife) 13 января 2016 г.
Изготовление ножей — древнее искусство. Однако, как и многие другие навыки, умение делать традиционные ножи кажется утерянным в нашем современном удобном мире.
Вы можете включить изготовление ножей в свои основные примитивные навыки выживания. Каждый нож, будь то из древней дамасской стали или современной углеродистой стали, состоит из набора инструментов.
Изготовителю ножей перед изготовлением лезвия необходимы следующие материалы:
- гаечный ключ старый
- болгарка
- кузнечная кузница
- молоток
- наждачная бумага
Также не забывайте, что изготовителю ножей нужна защитная одежда.Вы же не хотите обжечься искрами от ленточно-шлифовального станка или получить осколок стали в глаза.
Используйте защитные очки, перчатки и даже средства защиты органов дыхания, чтобы изготовление ножей своими руками было безопасным.
Шаг 1. Выбор ножевой стороны гаечного ключа
Сначала выберите конец гаечного ключа для лезвия и рукоятки ножа. Воспользуйтесь портативной кофемолкой, чтобы выпрямить конец, который вы выбрали в качестве лезвия ножа.
Затем с помощью болгарки прорежьте сталь, чтобы придать форму лезвию.
Шаг 2. Подготовка кузнечной кузницы
Между тем, вы можете создать простую кузнечную кузницу дома. Можно использовать старую решетку или любую прочную площадку, на которой можно разместить кусок горящего угля.
Убедитесь, что в вашей кузнице есть выдувной механизм, чтобы было достаточно тепла для ковки стали.
Шаг 3: установка гаечного ключа на горячую кузницу
После использования точильщика на вашем ноже, поместите ножевую сторону гаечного ключа на горящие угли.Держите его там, пока он не станет достаточно горячим, чтобы сталь могла придать форму.
Вы сможете определить, когда сталь достигает температуры ковки. На этом этапе сталь должна стать раскаленной до красного или желтого цвета.
Шаг 4: Удар по стали
Когда сталь сильно нагреется, поместите ее на наковальню или любую металлическую поверхность, достаточно твердую, чтобы она могла поддерживать ее. Теперь вы можете манипулировать сталью.
Забейте его молотком, пока не получите лезвие желаемой формы. При ударе молотка металл может странно двигаться.Примите это как проверку своих кузнечных навыков.
СВЯЗАННЫЙ: Как сделать нож для выживания
Шаг 5: Изготовление лезвия
Вы можете приступить к изготовлению лезвия, как только получите желаемую форму для своего ножа. Ленточный шлифовальный станок или ленточный шлифовальный станок по металлу идеально подходят для этой работы, поскольку они помогают улучшить качество лезвия.
Ленточно-шлифовальный станок также придает лезвиям ровный и гладкий вид нержавеющей стали.
Шаг 6: Термическая обработка стали
После того, как вы обработали острую кромку лезвия, положите его обратно в горячую кузницу. Подождите, пока цвет лезвия не станет светящимся красным.
Выньте нож из кузницы и облейте его моторным маслом, чтобы завершить процесс. Наконец, постарайтесь не давить на лезвие и дайте ему остыть в течение часа.
Шаг 7: Заточка лезвия
Когда лезвие остынет, придайте ему красивый край. Так что держите нож острым, убедившись, что у вас есть эти материалы.
Шаг 8: Цените свою работу
После изготовления ножа цените вашу работу! Лишь немногие люди делают ножи по индивидуальному заказу и сегодня могут называть себя производителями ножей.
Если вам нужны ножны для лезвия, выполните следующие действия. Вскоре вы сможете попробовать делать карманные ножи, охотничьи ножи и другие лезвия, чтобы проверить свои навыки.
Посмотрите этот пост от Trollskyy, чтобы увидеть полное видео по изготовлению ножей:
com/embed/Z2bvHrMSJA4?feature=oembed» frameborder=»0″ allow=»accelerometer; autoplay; encrypted-media; gyroscope; picture-in-picture» allowfullscreen=»»/>
Изготовление ножей — действительно великий первый кузнечный проект. Нам повезло, что в нашем распоряжении есть современные инструменты, упрощающие работу.
Ковка стали и лезвий, должно быть, была действительно сложной задачей столетия назад.К счастью для нас, у нас есть все необходимые инструменты и средства, чтобы превратить любой старый гаечный ключ в нож.
Воспользуйтесь этой возможностью и продолжайте совершенствовать свои навыки изготовления ножей и кузнечного дела!
Что вы можете сказать об этом проекте по изготовлению ножей? Вы когда-нибудь превращали старый гаечный ключ в лезвие? Поделитесь своими мыслями в разделе комментариев ниже!
Наверх Далее: Кузнечное дело: полезное хобби и навык выживания!
Следуйте за нами в Facebook, Instagram, Twitter, Tumblr и Pinterest!
Примечание редактора.