расход, пробег, запуск, фильтрация, октановое число газа, влияние на двигатель / СоХабр
После написания первой статьи поступили вопросы от хабросообщества на которые я тут отвечу + добавлю от себя массу интересного. Начнем.1. Сколько кг дров нужно для пробега 100км
Автомобиль жигули — «четверка» объем двигателя 1.5л, 76 лошадиных сил, коэффициент наполнения цилиндров 0.75.
Потребляет на 100 км около 10 литров бензина (старые автомобили) и 20 кг дров в час если ехать со скоростью 100км в час непрерывно. Если ехать с меньшей скоростью и меньшими чем 3000 оборотов — расход меньше.
Автомобиль Волга Газ 24 — «членовоз» объем двигателя 2.4 л, 105 лошадиных сил, коэффициент наполнения цилиндров 0.83.
Потребляет на 100 км около 13-15 литров бензина (старые автомобили) и 36 кг дров в час если ехать со скоростью 100км в час непрерывно и оборотами 3000 двигателя.
Автомобиль ЗИЛ с объемом двигателя 6,0л, 150 лошадиных сил, коэффициент наполнения цилиндров 0,95.
Потребляет на 100 км 36 литров бензина и 103 кг дров в час при оборотах двигателя 3000
Автомобиль ОКА с объемом двигателя 0.75л, 35 лошадиных сил
Потребляет 4.3 литра на 100км и 10 кг дров в час при оборотах двигателя 3000
коэффициент наполнения цилиндров не нашел, посчитал на 0.75
Теперь когда мы знаем расход дров, мы можем смело посчитать размер бункера для загрузки дров.
1 кг дров порубленных на куски 5х5см имеет коэффициент наполняемости 0.5 и занимает объем бункера 5 литров
более мелко порубленное топливо — например щепа имеет коэффициент наполнения 0.35 и занимает объем бункера весом 1 кг на 30% меньший — 3,5 литра. Цифры справедливы для сосны, если применять лучшее топливо: бук, граб, дуб, береза — наполнение бункера еще лучше и в такой же объем войдет больше кг, что значит более долгий пробег, если добавлять еще и пластиковый мусор — пробег еще больше, а расход дров меньше.
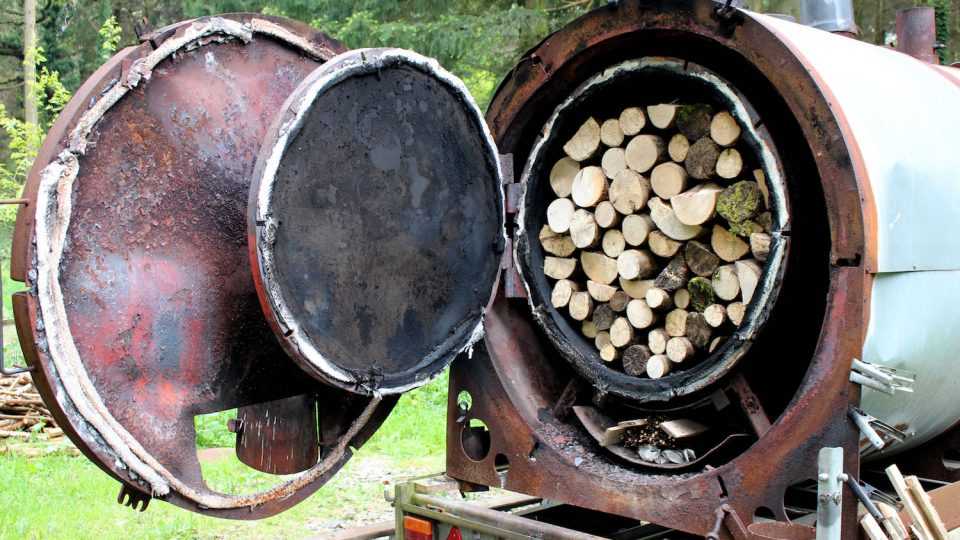
13 — 100%
6 — х
6х100/13 = 46.15%
Какого размера бункер делать?
Некоторые делают объем бункера на 500км пробега, как Веса и его ученик.
Сколько времени нужно на запуск?
Газогенератор на древесном угле — 10-30 секунд
Газогенератор на дровах (и мусоре) — 5-15 минут. Делается это прямо в пути на ходу путем переключения кнопкой топлив. Стоять качегарить и дуть не надо.
Так на сколько же бензин сильнее древесного газа?
Любое топливо ценно двумя элементами: углеродом С и водородом Н2 сжигая которое в единицу времени и объема мы получаем
Теплотворность бензина 10572 ккал/кг
Теплотворность древесного газа 1000 ккал/кг — (цифра колеблется до 1250 ккал/кг)
Казалось бы в 10 раз! Как оно на дровах еще едет? Но нет, забыли о том что топливо должно превратится в газовоздушную и бензовоздушную смесь. Для горения в цилиндрах нужен еще и кислород. Смесь должна поступать смешанная.
Теплотворность бензовоздушной смеси 860 ккал/кг
Теплотворность газовоздушной смеси (древесный газ) 560 ккал/кг — или 64% от бензоводушной.
Цифра 64% на 36% слабее бензовоздушной. Но путем доработок и подключения современных устройств эта цифра снижается вплоть до 0.
Какое октановое число у древесного газа и как эксплуатация его сказывается на моторесурсе двигателя?
У газогенераторного газа октановое число 110-120 что позитивно сказывается на моторесурсе двигателя снижая детонацию, газ не смывает масляную пленку, двигатель работает тише, ровнее. Вот тут подробно описал тем кто хочет углубиться.
Конечно же если не правильно делать газген, а в 1м3 газа содержится 3г пыли и не умело её фильтровать (не правильно делать фильтра) то все это пойдет в двигатель и будет действовать как наждак на поршни, но если все делать правильно то ни пыли ни смол не попадет в двигатель и его моторесурс будет больше чем указанный в паспорте рассчитанном для бензина.
Как часто выгружать золу?
С 1кг дров пропущенном через газогенератор выделяется 1г золы. Сколько кг вы будете жечь в час и посчитайте сколько грамм золы накопиться за час день, месяц эксплуатации при вашем ежедневном пробеге.
Как часто надо менять фильтра?
Раньше забивали в фильтра древесную шерсть, опилки и прочее. Сегодня фильтра делаются безсменные — менять ничего не надо.
Как выгодно ездить на дровах?
Сколько стоит 1 литр бензина?
1 литр бензина = 2-3 кг дров (зависит от влажности, плотности и пр.).
Авто на дровах — Энергознание на портале Энерговектор
Идея газогенераторного автомобиля,
двигатель которого работает на газе, получаемом из твёрдого топлива, не нова,
она возникла ещё в конце XIX — начале XX веков. Первые опыты по газификации
дерева проводились ещё в 1870-х, когда полученный газ использовался для
освещения улиц и приготовления пищи.
Принцип прост
Газификация дерева и других материалов — это процесс, в котором исходное сырьё превращается в горючие газы после нагрева. В транспортное средство устанавливается специальный котёл-газогенератор, по виду напоминающий водонагреватель. Он почти доверху набивается древесиной, которая сжигается при ограниченном доступе воздуха. В котле создаётся очень высокая температура (до 1400 °C), под действием которой твёрдое топливо разлагается с выделением газов — горючих (этилен, метан, угарный газ, водород) и негорючих (азот, углекислый газ). Таким образом, автомобильный газогенератор — это простой, по сути, агрегат, притом громоздкий и конструктивно осложнённый дополнительными системами.
Ford Model A выпуска 1929 г.
Помимо собственно производства газа мобильная газогенераторная установка охлаждает его, очищает и смешивает с воздухом. Поэтому классическая схема включает сам газогенератор, фильтры грубой и тонкой очистки, охладители, электровентилятор для ускорения розжига и трубопроводы. Получаемая смесь газов и подаётся в ДВС в качестве топлива.
Газогенераторный автомобиль (ГГА), быть может, не так элегантно выглядит, как его бензиновые и дизельные собратья, однако экономически эффективнее и экологичнее их. Пробег ГГА от одной заправки примерно такой же, как у электромобилей, но, в отличие от последних, проблем с перезаправкой, по крайней мере, на большей части территории России, нет никаких. После повышения цен на бензин интерес к этой почти забытой технологии возрождается: умельцы переводят свои машины на дровяное топливо.
Немного истории
В 1920-х немецкий инженер Георг Имберт разработал удачный серийный газогенератор.
Эта технология стала общеупотребительной в европейских странах и Советском Союзе во время Второй мировой войны, когда потребление нефтепродуктов нормировалось. В одной лишь Германии к концу войны использовалось почти полмиллиона ГГА. Была построена сеть из примерно 3 тыс. «заправочных станций», где водители могли пополнить запас дров. Газификаторами дров оборудовались не только легковые автомобили, но и грузовики, автобусы, тракторы, мотоциклы, суда и железнодорожные локомотивы. На древесном газе ездили даже танки.
ГАЗ-42
В 1942 г.,
когда эта технология ещё не достигла пика популярности, было около 73 тыс. ГГА — в Швеции, 65 тыс. — во Франции, 10 тыс. — в
Дании, 9 тыс. — в Австрии и Норвегии и почти 8 тыс. — в Швейцарии. В
Финляндии в 1944 г.
эксплуатировались 43 тыс. «дровяных транспортных средств», в том числе 30 тыс.
автобусов и грузовиков, 7 тыс. легковых автомобилей, 4 тыс. тракторов и 600
легкомоторных судов. ГГА использовались в США, Азии и Австралии, где их было 72
тыс. В общей сложности во время Второй мировой
по миру использовалось более миллиона ГГА.
В СССР с 1935 г.
и до самого начала Великой Отечественной войны на предприятиях Министерства
лесной промышленности и ГУЛАГа «полуторки» ГАЗ-АА и «трёхтонки» ЗИС-5, а также
автобусы на их базе переделывались для работы на дровах. Также отдельными
партиями газогенераторные версии грузовиков производились самими автозаводами.
Например, советские автоисторики приводят число 33840 — столько было выпущено
газогенераторных «полуторок» ГАЗ-42. Газогенераторных ЗИСов моделей ЗИС-13 и
ЗИС-21 в Москве было произведено более 16 тыс.
За довоенное время советские инженеры создали более 300 различных вариантов газогенераторных установок, из которых 10 дошли до серийного производства. Во время войны конструкторы серийных заводов подготовили чертежи упрощённых установок, которые могли изготавливаться на местах в автомастерских без применения сложного оборудования. По воспоминаниям жителей северных и северо-восточных регионов СССР, грузовики на дровах можно было встретить в глубинке вплоть до 1970-х.
После войны, когда ограничения на отпуск бензина были сняты, газогенераторные машины начали быстро исчезать. В начале 1950-х в ФРГ осталось всего 20 тыс. ГГА. Единственная на сегодня страна, где массово используются автомобили на дровах, — это Северная Корея. В условиях изоляции от мировой экономики там ощущается дефицит жидкого топлива.
В 1957 г.
шведское правительство инициировало исследовательскую программу подготовки к
быстрому переходу на ГГА в случае внезапного дефицита нефтепродуктов. У Швеции
нет запасов нефти, зато много лесов. Цель исследования — разработать
усовершенствованный стандартизованный газогенератор, который можно было бы
устанавливать на транспортные средства любых типов.
Это исследование, оплаченное компанией Volvo, позволило получить большой объём теоретических сведений и практического опыта эксплуатации различных видов газогенераторных автомобилей и тракторов, общий пробег которых превысил 100 тыс. км. Результаты были обобщены в документе, датированном 1986 г., в котором также обсуждаются некоторые эксперименты в других странах. Шведские и особенно финские инженеры-любители использовали эти данные для дальнейшего развития технологии.
Чем топить?
В основном используются древесина в различных видах (дрова, отходы
лесозаготовки и мебельной промышленности, пеллеты и т. п.) или древесный уголь,
но список этим не ограничивается. Пластик, резина, полиэтилен, тряпичная
ветошь, различный мусор, птичий помёт и многие другие виды отходов могут служить
топливом для газогенераторного котла (конечно, расход топлива и состав газа
меняются в зависимости от сырья). Подсчитывая стоимость дров и древесного угля,
нельзя забывать о различных бесплатных отходах, которые могут быть
использованы, — лузга семечек, скорлупа орехов, стержни кукурузы, отработанный
кофе после кофемашин, сено, торф. Любители ГГА утверждают, что их автомобили
очищают придорожную полосу от мусора.
Реальная экономия
Для автомобиля, расходующего 10 л бензина на 100 км, потребление дров после установки современного газогенератора составляет в среднем около 20 кг. При этом мощность двигателя снижается всего на 4%, показатели максимальной и крейсерской скорости почти не меняются.
Таким образом, килограмм дров заменяет пол-литра бензина. Стоимость килограмма дров примерно втрое меньше стоимости литра бензина, так что экономия очевидна.
ЗИС-13
Один из самых серьёзных недостатков ГГА — большое время выхода
газогенератора на режим. При работе на древесном угле двигатель можно запустить
уже через 10-30 с после розжига котла, на дровах (и мусоре) — через 5-15 мин.
Октановое число газа, получаемого таким способом, доходит до 110-120, так что газ снижает детонацию и в целом щадит двигатель. В отличие от бензина, газ не смывает масляную плёнку со стенок цилиндров, в результате двигатель работает тише и ровнее. Однако при неправильной фильтрации топлива (изначально в 1 м3 газа содержится около 3 г золы и пыли) твёрдые частицы, попадая в двигатель, будут приводить к его преждевременному износу. Поэтому важнейшие элементы газогенератора — это продуманные системы фильтрации и охлаждения (по результатам экспериментов известно, что при увеличении температуры газа с 20 до 70 °C мощность ДВС падает на 25%).
Вопросы экологии
При сжигании веществ органического происхождения вредных выбросов будет немного
— в процессе работы двигателя будут получаться в основном углекислый газ и зола,
из которой можно делать удобрения. По результатам исследований, проводимых в
Европе, автомобили на дровах намного экологичнее традиционных транспортных
средств.
Многих также беспокоит вопрос вырубки лесов. Хочется заметить, что для обеспечения ГГА топливом не обязательно вырубать лес. Приверженцы этой технологии пользуются ветками и дровами от сухих деревьев, которых много в лесополосах вдоль дорог. Кстати, производство нефтепродуктов тоже наносит большой вред окружающей среде.
Кому подходит ГГА?
В первую очередь жителям глубинки, где моторное топливо сложно найти или оно стоит слишком дорого. Однако в последнее время горожане, озабоченные проблемами экологии, нередко переоборудуют свои авто в ГГА.
Например, житель Англии Колин Дэвисон с друзьями проехал по всей стране
(2575 км),
заправляя свой автомобиль отходами кофемашин. Маршрут был проложен между 37
кофейнями, в которых группа брала отработанный кофе, в результате чего её
путешествие было занесено в Книгу рекордов Гиннесса. Максимальная скорость составила
105 км/ч.
Швед Йохан Линель за 20 дней проехал всю Швецию (5420 км) на дровах. Расход древесины
составил 7 м3.
При этом скорость доходила до 150
км/ч.
Украинец Андрей Лагунов пошёл еще дальше — он разработал обучающий курс «Авто на дровах своими руками», а также собрал много информации о газогенераторах и их владельцах. Любой желающий, по словам Андрея, может сделать газогенератор своими руками за несколько дней, потратив менее 50 долл.
Источник: Энерговектор
Авто на дровах работает при помощи газогенератора, производящего газ из дров.
Еще в 30-е годы прошлого века ученые СССР изобрели машины, работающие на дровах, которые назывались газогенераторными. Единственное их отличие заключалось в наличии особой конструкции в виде короба позади машины. В те времени такое устройство было необходимо, ведь в стране был недостаток бензина. Хотя преимуществ у таких машин было немного, их производство было массовым. Тяжелые автомобили на дровах широко использовались во времена Великой Отечественной войны, но только для невоенной техники – бензин уходил на поля боя.
В послевоенный период топлива производилось все больше, и газогенераторный автомобиль постепенно уходил в историю. Тем не менее и сегодня можно встретить людей, которые создают автомобиль на дровах – «машину из прошлого» – самостоятельно либо из-за своего интереса, либо в целях экономии.
Однако нужно ли на самом деле устанавливать газогенератор? Как он работает? Есть ли польза для автомобиля? Постараемся разобраться в этом вопросе.
Принцип работы агрегата
Газогенератор можно сравнить с колонной, имеющей цилиндрическую форму с сужением книзу. От агрегата отходят патрубки для подачи воздуха и выхода горючей смеси. Основным агрегатом, из числа представленных на схеме, является, конечно, газогенератор. Еще имеется люк для доступа в зольник и отверстие, для того чтобы можно было загружать топливо. Дымоход отсутствует.
Для начала следует понять принцип работы газогенератора. Эта информация необходима тем, кто намерен узнать принцип работы газогенератора или «пиролизного газогенератора» – таково его полное название.
Данная установка нужна для выделения смеси газов путем разложения дров, торфа, угля. Затем следует рассмотреть принцип действия газогенератора на дровах. Благодаря пиролизу дерева, выделяются газы, способные гореть. Таким образом, сюда можно включить угарный газ, водород, метан и прочие непредельные углеводороды.
Из чего состоит пиролизный газ?
Порода древесины не влияет на состав смеси при пиролизе. Соответственно, береза, сосна и ель выделяют практически одинаковое количество всех вышеперечисленных газов. После пиролиза 1 куб. м дерева можно получить около 90 м3 неконденсирующегося газа.
Полезная теплота при сгорании 1 м3 неконденсирующегося газа, кДж/м3, вычисляется по формуле.
Для примера возьмем березу и сделаем расчёт калорийности газа:
Qнр=127,5*28,4%+108,1*3,0%+358,8*18,2+604,4*1,4=11 321,62 кДж/м3= 11,3 МДж/м3
Затем делим полученное число на 4,187. Таким образом, Qнр будет равен 2704 кКал/м3. Для сравнения калорийность природного газа составляет 8000 кКал/м3.
Технологический процесс
Один лишь полученный газ непригоден для ДВС, поэтому необходимо соблюдать определенный процесс, который поделен на этапы:
- Дрова не должны сжигаться, а разлагаться термическим образом, ввиду низкой подачи кислорода.
- Следующий этап обуславливается удалением взвешенных частиц при помощи фильтра.
- Затем с помощью воздушного или жидкостного теплообменника смесь охлаждается.
- После этого смесь очищается при помощи тонкой очистки.
- На последнем этапе горючее подходит в смеситель и затем попадет в двигатель.
Мифы о газогенераторных установках
Газогенераторная установка для современного человека является пережитком прошлого, поэтому существуют различные мифы. Но действительно ли им можно верить?
- Миф №1. Утверждается, что установка имеет крайне высокий коэффициент полезного действия.
В действительности, вследствие пиролиза КПД не может превышать 70–80%.
- Миф №2. Утверждается, что установка может проработать и на влажном топливе. Можно сказать, что частично это является правдой. Но влажное топливо уменьшает количество производимой смеси. Иногда падение достигает 25%, так как при испарении пара от воды расходуется больше энергии, чем при выделении газа. Поэтому дрова всё-таки стоит сушить.
- Миф №3. Утверждается, что установка поможет сэкономить расходы по отоплению дома, в сравнении с традиционными устройствами. Однако здесь следует просчитать целесообразность двух установок по их цене и занимаемой площади. Таким образом, это миф.
Как сделать газогенератор самому?
Для того чтобы создать газогенераторную установку, потребуется много сил, так как она не должна занимать много места или быть тяжелой, но при этом быть высокопроизводительной. Нержавеющая сталь будет идеальным материалом для производства корпуса, фильтрующего и охлаждающего устройства. Однако цена такого материала довольно высока, по сравнению со стандартной сталью.
Для наружной емкости можно использовать железную бочку или металлический прокат (толщина не должна быть менее 1 мм), а внутренняя может быть сделана из газового баллона или ресивера от грузовых автомобилей. Стоит предусмотреть отверстия для зольника, чтобы была возможность производить чистку. В камере сгорания должна располагаться горловина (в нижней части) для смольных отложений. Колосниковая решетка отлично получается из арматуры. Патрубки можно купить, благо в продаже они бывают разных размеров и по невысокой стоимости. Крышку можно сделать из металлического листа. Фильтрами могут быть отслужившие огнетушители, а охладителем – «гармошка», применяемая в системе отопления. Кроме того, понадобятся смеситель и вентилятор с реле.
Дровяные машины сегодня
Автомобиль, работающий на дровах, это экологичное средство передвижения. Такое топливо не вредит атмосфере так сильно, как солярка и бензин. Имея ретротранспорт, вопрос наличия заправок становится неактуальным. Но такие автомобили безвозвратно утратили свою популярность. Сегодня газогенераторы интересны только энтузиастам или тем, кто хочет сэкономить на топливе. Не так давно экспериментально, в штучном экземпляре выпускались Москвич-2141, РАФ-2203, работающие на дровах. Конструкторы говорили, что при скорости 85 км/ч можно проехать 120 км, не заправляясь заново.
На данный момент авто на дровах повсеместно используются в Северной Корее, в связи с изоляцией и, как результат, нехваткой топлива.
Итог
Идея использования дров в качестве топлива может быть привлекательной. Однако стоит понимать, что газогенератор на дровах является неконкурентной альтернативой жидкому топливу. Двигатель на газовой смеси не способен раскрыть свой потенциал, так как разогнать автомобиль до 80 км/ч будет недостижимой целью.
‘; blockSettingArray[0][«setting_type»] = 6; blockSettingArray[0][«elementPlace»] = 2; blockSettingArray[1] = []; blockSettingArray[1][«minSymbols»] = 0; blockSettingArray[1][«minHeaders»] = 0; blockSettingArray[1][«text»] = ‘
‘; blockSettingArray[1][«setting_type»] = 6; blockSettingArray[1][«elementPlace»] = 0; blockSettingArray[3] = []; blockSettingArray[3][«minSymbols»] = 1000; blockSettingArray[3][«minHeaders»] = 0; blockSettingArray[3][«text»] = ‘
Расход — 20 кг поленьев на 100 км.
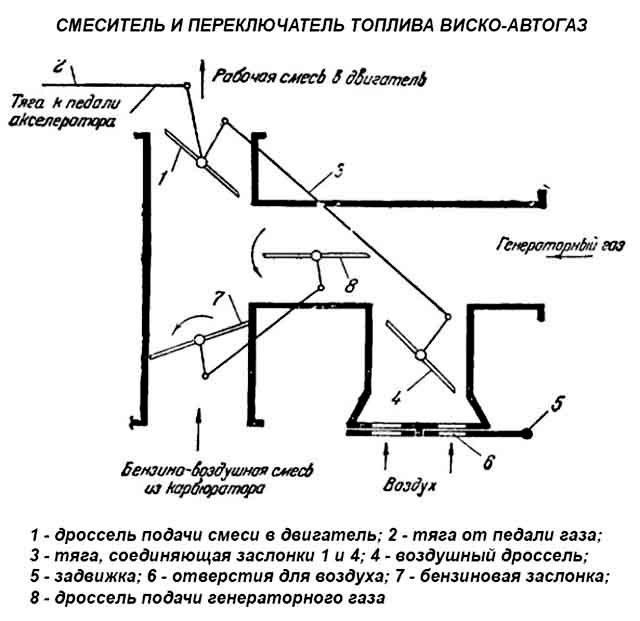
…А вы говорите, экономичный режим, гибриды, электромобили… Тут по Бресту катается УАЗ, работающий на дровах! Для лучшего понимания расхода этой машины стоит процитировать Сергея, автовладельца и, можно сказать, конструктора: «Однажды заехал в лес по грибы и обнаружил, что закончились дрова для растопки. Что делать? Граблями накидал в ведро шишек, забросил их в котел и поехал дальше». Одним словом, УАЗ может ехать «за бесплатно» везде, где есть древесина, где есть то, что горит. Проблемы могут возникнуть разве что в пустыне.
Из истории
Сергей всегда увлекался историей, в частности военной. Потому с ходу рассказывает о временах, когда подобные газогенераторы были на пике технологий: «Угольный газ использовался еще пещерными людьми. Известный факт, что в свое время освещение во всем Санкт-Петербурге обеспечивали именно газогенераторные установки. Современная история этого устройства начинается с 1919 года, когда германско-французский инженер Георг Имберт, вернувшись с Первой мировой, собрал газогенератор на древесном угле. Проходит два года, и изобретатель представляет автомобиль, чей мотор работает по этому же принципу, только с усовершенствованием».
«Камера Имберт обращенного типа» работала так, что пиролиз проходил не в цилиндрах (как у Форда или Порше), а в котле, который устанавливался за кабиной водителя. Пиролиз в нашем случае — это горение древесины при недостатке кислорода с выделением газа, который и крутит поршни двигателя (но об этом чуть позже). Так вот, Имберт достиг таких высот, что здание его компании Imbert Generatoren GmbH стояло рядом с заводом Форда в Кельне, как бы напоминая о конкуренции. В 30-х годах газогенераторы инженера ставили на немецкие грузовики, автомобили Opel и Mercedes. К моменту, когда созрел международный конфликт, вылившийся в итоге во Вторую мировую войну, Имберт придумал, как оборудовать своей установкой танки! И усовершенствованные бронированные машины действительно ездили и даже стояли на вооружении — в основном в «учебках» и частях вспомогательной полиции (по-простому — у полицаев).
Технология получила распространение не только в Германии. В конце 20-х — начале 40-х годов в СССР тоже активно использовали грузовики с газогенераторами. Серийно их устанавливали на АМО, ЗиС-21 (выпущено более 15 тыс. моделей), Урал-ЗиС. В те времена Союз испытывал нехватку нефти, а автомобилизацию останавливать было нельзя. Почему бы не «топить» машины дровами? Во время Великой Отечественной войны такие транспортные средства сильно пригодились благодаря нулевым затратам. Есть свидетельства, что именно на газогенераторных автомобилях прорывали блокаду Ленинграда.
Массовая добыча нефти началась в 50—60-х годах, и в итоге новое топливо понемногу вытеснило разработки ученых образца начала века. Газогенераторы снимали с машин и попросту отправляли в металлолом. Сейчас мы видим обратную тенденцию — отказ от ДВС, использование возобновляемых источников энергии. Например, по данным СМИ, в Швеции владельцев автомобилей, ездящих на дровах, поощряют на государственном уровне субсидиями. Для скептиков стоит пояснить, что газогенератор можно оборудовать на раме прицепа — в таком варианте он наиболее эстетичен.
Проект Сергея
В частном музее, который базируется в Бресте, стоит действующий ЗиС-5. Нескольким любителям автомобильной истории однажды пришла в голову лихая идея: а почему бы не поставить на «дедушку», который выпускался с 1933 года, газогенератор. Должно получиться — ведь в 1939-м подобный эксперимент с 21-й моделью закончился успешно. И Сергей решил повторить. Но почти 90-летний грузовик — раритет, антиквариат, поэтому мужчина не решился переделывать всю топливную систему столь редкого ныне образца советского автомобилестроения. Для пробы, освоения технологии он взялся за преобразование более современной техники — всем известного и довольно простого уазика. Модель была выбрана исходя из увлечений Сергея: трофи, бездорожье, 4×4.
Наверное, большинство читателей, только узнав о способе сборки газогенератора, махнули бы на эту затею рукой. Дело в том, что Сергей не стал покупать готовый образец или собирать его по схемам и чертежам. Он «высчитал» установку по формулам из книг 30-х годов. «В библиотеке, в сети нашел нужную литературу, — вспоминает конструктор. — Пришлось прочесть немало. Среди авторов есть и знаменитые фамилии: Токарев, Панютин. Но готового рецепта по сборке нигде не обнаружил. Есть только формулы. Создать газогенератор по ним — как заново сделать карбюратор. Нужно было высчитать скорость дутья, газификацию, объем нужного газа, материальный баланс — для двигателей разных объемов предусмотрены разные значения. Признаться, до сих пор не помню наизусть таблицу умножения, но эту штуку все же собрал. Ответами на вычисления по формулам стали размеры деталей установки и, собственно, сам чертеж. Ну а сборку производил из того, что было под рукой. На все ушел год».
Как это работает?
Топливом для газогенераторной установки (а в данном случае речь идет о монораторе) служат небольшие деревянные чурки. Причем совсем необязательно, чтобы они были сухими, сгорит и влажная древесина (до 60 процентов влажности) — в этом и отличие моноратора от обычного газогенератора. За задним рядом пассажирских сидений в машине Сергея лежат два мешка таких чурок. Говорит, что одного хватает на 100 километров пути. В пересчете на массу получается, что расход равен 20 кг дров на сотню. Естественно, постоянно подбрасывать дровишки в печь не нужно. Закинул в начале пути — и поехал.
«А это мой заправочный пистолет. Всегда вожу с собой», — шутит мужчина и демонстрирует топор. Судя по его историям, «пистолет» может и не пригодиться — по хвойному лесу можно спокойно ехать на шишках. В любом случае экологичность установки неоспорима. Так как Сергей — человек идейный, экология для него не пустое слово.
Топливо загружается в бак через крышку, расположенную наверху камеры газификации (на фото — черная бочка в центре). Во время работы оттуда непрерывно идет дым. Крышка его не пропускает — таким образом, издалека машина не выглядит как паровоз. Перед запуском двигателя нужно подождать около 5—10 минут, чтобы туда поступил газ.
«Внизу камеры газификации дрова тлеют, — Сергей описывает механику работы установки. — Запуск горения — от спички или факела. Всего в камере протекают три процесса: термическое разложение топлива, окисление, восстановление. При горении топлива с обедненным количеством кислорода (пиролизе) протекают реакции окисления угля и углеводородов: С + О2 = CO2, 2h3 + O2 = 2h3O с выделением тепла. Потом идет реакция восстановления (при прохождении через слой раскаленных углей): С + CO2= 2СО, С + h3O = CO + h3 с потреблением тепла. Топливо в системе обращенного моноратора практически полностью разлагается. Для конденсата предусмотрена отдельная трубка, его можно слить».
Газ попадает в фильтр грубой очистки (на фото — перевернутый конус слева от камеры), который заканчивается банкой, куда оседает сажа, потом проходит через охлаждающую систему труб под днищем УАЗа. Если поджечь газ на этом этапе, пламя будет красным.
Если «грязный» газ запустить в двигатель, его детали быстро покроются налетом, снизится их ресурс. Потому далее топливо поступает в фильтр тонкой очистки (на фото — зеленая бочка справа от камеры). Фильтрующим элементом выступают простые опилки. Их нужно менять через каждые 2 тыс. км пробега. После прохождения через этот фильтр газ горит синим пламенем.
Очищенный газ поступает непосредственно в цилиндры 2,4-литрового мотора, там вспышками сгорает, приводя в движение весь агрегат, а следовательно, и весь автомобиль. Выхлопная система штатная, но выбрасывает она углекислый газ (как и люди при выдохе). То есть никакого тебе токсичного угарного газа, оксидов азота, углеводорода, альдегидов и прочих веществ, против которых выступают экологи. По той же причине масло в двигателе нужно менять только после 30 тыс. км пробега.
В плане комфорта «дровяной» УАЗ не особенно радует — в принципе, как и все машины этой модели (даже те, что работают на бензине). После поездки на одежде остается легкий аромат костра (не раздражающий), «печка» работает жарче обычного. В салоне за подачу газа отвечает рычаг заслонки, спрятавшийся слева от руля.
В УАЗах предусмотрено два топливных бака для бензина: с левой и правой сторон кузова (специально на случай, если один из них будет прострелен). Чтобы развеять сомнения в работоспособности моноратора и показать, что доступ к обоим бакам перекрыт, Сергей демонстрирует рычаг в салоне — он находится в нейтральном положении. При необходимости баки можно заполнить бензином — тогда получится своеобразный гибрид.
Напоследок — о безопасности. В устройстве соседствуют открытый огонь и газ, что настораживает. По словам Сергея, риск пожара или взрыва минимален, потому как газ не находится под большим давлением. «Тот же бензиновый автомобиль легче воспламенить, чем эту машину», — заверяет мужчина.
Проблем с официальной регистрацией транспорта тоже нет — как видно на фото, УАЗ стоит на учете, на нем установлены номера. Техосмотр тоже пройден: по документам газогенератор — навесной груз. Его можно снять и, залив немного бензина, пройти линию ТО.
«Самый волнительный момент был — когда впервые запускали мотор, — вспоминает конструктор-любитель. — Признаться, с первого раза не вышло. Потом сидел и ломал голову, что же не так? В сети нашел несколько таких же российских и украинских фанатов, как и я. К тому моменту уже был создан форум, где ребята обменивались нюансами работы газогенераторов, способами решения проблем. Как видите, в итоге все у меня получилось: УАЗ работает, уверенно едет по болотам и бездорожью, разгоняется на трассе до 70 км/ч. Скажу больше: систему можно спрятать в прицепе и установить на любой автомобиль с ДВС. Это по моим расчетам обойдется примерно в 300 долларов в эквиваленте. Можно сказать, эксперимент удался. Но напомню — это был лишь опытный образец. Основной проект — ЗиС-5 родом из 30-х годов. Сейчас я с командой продолжаю работу над ним. Планируем закончить к 9 мая и выкатить обе машины на парад: проедут по улицам города, как дедушка и внук. Ну а дальше обязательно придумаем что-нибудь этакое к 1000-летию Бреста».
Парковочные радары в каталоге Onliner.by
Читайте также:
Наш канал в Telegram. Присоединяйтесь!
Быстрая связь с редакцией: читайте паблик-чат Onliner и пишите нам в Viber!
Перепечатка текста и фотографий Onliner.by запрещена без разрешения редакции. [email protected]
Автомобиль на дровах принцип действия
Люди изобрели электричество, научились пользоваться солнечной и ветровой энергией, добывать различные полезные ископаемые, например, нефть и газ. Однако большинство из них всё так же продолжает сжигать в топках дерево. Опилками и прочими отходами деревообрабатывающей промышленности можно пользоваться, если своими руками изготовить газогенераторный автомобиль на дровах. Многие мастера сегодня успешно эксплуатируют подобные устройства.
Особенностью газогенератора для автомобиля на дровах является агрегат, в котором происходит добыча газовой смеси. Затем она попадает в ДВС, где осуществляется ее сгорание. В результате этих процессов машина движется. При использовании такого прибора необходимо учитывать, что он занимает немало места и требует использования дополнительного оборудования — фильтра, трубки и радиатора.
Газогенератор — устройство, которое превращает дерево в газ. Всем известно, что именно газ является альтернативным энергетическим источником для автомобилей. Подтверждением этому служит большое количество газовых заправок. Однако добыть топливо самостоятельно не только можно, но и вполне реально. Бортовая конструкция способна вырабатывать столько ресурсов, сколько требуется автомобилю. Однако есть один нюанс: горячее топливо менее эффективно, особенно если в нем присутствуют примеси. Поэтому первым делом его нужно остудить, а затем очистить.
После выхода за пределы агрегата газ движется по трубам к фильтру, а потом к радиатору. Во время движения он очищается от пыли и кислот. Кроме того, снижается его температура. В процессе прохождения по лабиринтам примеси оседают на стенках в виде жидкости или твердых частиц. Через специальный тройник газ соединяется с кислородом и отправляется в двигатель. Затем смесь доходит не только до требуемой кондиции, но и оказывается в двигателе. После этого газ попадает в камеру сгорания и приводит автомобиль в движение.
Подвеска, салон, двигатель и сцепление машины при этом остаются на своих местах. Единственная проблема заключается в том, где поместить газогенератор и как провести трубопровод, чтобы машина была похожа на паровоз. Все эти вопросы следует подробно изучить перед началом работ.
Автомобиль на дровах своими руками вполне можно сделать. Изготовление газогенератора — посильная задача, впрочем, как и его установка. Для начала важно понять особенности агрегата и суть процесса. Сама конструкция представлена в виде зауженного в нижней части цилиндра. Образно можно назвать его бункером, накопителем для дров в котором является цилиндрическая часть. В узкой половине происходит сгорание.
Заготовки сами опускаются под действием собственной массы. Благодаря этому обеспечивается бесперебойная подача топлива к источнику горения. Зола оседает в специальной емкости, которая периодически требует чистки. Дрова загружаются в люк сверху.
Небольшие заготовки плотно размещают от колосников до крышки. Последняя герметично закрывается, чтобы минимизировать утечки. Устройство разжигают, спустя некоторое время машина может отправляться в путь.
Не следует путать конструкцию с открытым костром. Требуемый для горения кислород порциями подается через специальную трубку. На противоположной стороне располагается отверстие для выхода газа. При порционной подаче воздуха не осуществляется активное горение. Деревянные заготовки подвергаются пиролизу — тлеют на слабом огне, активно выделяя горючую смесь.
Основное назначение газогенератора заключается в получении горючего газа, который называется оксидом углерода. Именно это вещество и будет гореть в ДВС. Эту процедуру можно позиционировать как полное и частичное сгорание, во время которого происходит образование оксида углерода. Кроме того, выделяется и углекислый газ. Дрова при сгорании в контакте с влагой образуют смесь, которая состоит из:
- метана;
- непредельных углеводородов;
- оксида углерода;
- водорода.
Кроме того, в процессе горения происходит выделение нескольких негорючих компонентов. К ним относятся:
Существует три вида газогенераторов для автомобиля. Если кислород подается с нижней части, а газ отбирается сверху — это прямоточное изделие. При подобном размещении патрубков газовая смесь высвобождается при горении внизу конуса. В процессе движения газов через уголь и чурки из дерева происходит отдача воздуха и тепла. После того как заготовки пропускают через себя горячую газовую смесь, они просушиваются и готовятся к пиролизу.
Если подача кислорода для поддержки горения осуществляется в начале узкой части бункера, а газовая смесь отбирается снизу, тогда этот вид устройства именуется обратным или опрокинутым. Зажигание дерева осуществляется внутри, выше колосниковой зоны. Трубы для отвода газа располагаются ниже колосников. Подобный принцип работы аналогичен курительной трубке.
Имеется и альтернативный вариант — камера сгорания у обратного газогенератора ограничивается специальной наклонной перегородкой. Напротив трубы подачи кислорода с обратной стороны перегородки имеется ниша, из которой проводится отбор горючего газа. Патрубки кислородной подачи и отвода газа размещаются на одном уровне. Линия подвода труб пересекает бункер поперек, поэтому подобную конструкцию называют горизонтальной.
Прямоточные и горизонтальные газогенераторы хорошо показали себя при использовании торфа, древесного угля или кокса. Опрокинутый вид оборудования широко используется для езды на сухих чурках из дерева.
Характерной чертой всех газогенераторов является перемещение углекислого газа (диоксида углерода) через разлагающийся уголь. При этом газовая смесь отдает излишки воздуха и преобразуется в оксид углерода. Желательно, чтобы между теплообменником и камерой сгорания размещался циклонный фильтр. Это необходимо для того, чтобы газовая смесь очищалась от всевозможных механических примесей. Подобное устройство может задерживать около 90% летучей пыли.
Радиатор выполняет существенную роль. Охлаждаясь, газ становится более концентрированным и уменьшается в объемах. Это способствует подаче в ДВС большего количества топлива. Мощность двигателя в период эксплуатации напрямую зависит от температурных показателей газообразной смеси. Это обусловлено тем, что газ устойчив к детонации, поэтому его нужно охлаждать для усиления сжатия.
Компактным считается фильтрующий элемент тонкой очистки, сделанный из двух канистр. Внутри емкостей располагают минвату и шлак в гранулах. Они и будут хорошо чистить газ. В нижней части фильтра и теплообменника в обязательном порядке нужно установить краны. Это необходимо для стравливания конденсата. После очистки и остывания газовой смеси выпадает роса. Каждые 200 км езды в емкости собирается около 3 л жидкости.
Сварные швы и места соединения обязательно должны быть герметичными, поскольку в случае утечки при постоянном добавлении дров скорость и производительность двигателя авто будут оставаться на минимальном уровне. Собранный агрегат должен быть хорошо закреплен, чтобы он не разрушился от вибрации во время движения.
Газогенераторный двигатель на дровах для автомобиля может быть различных форм и размеров. Для этих показателей не существует каких-либо определенных требований. Однако необходимо учитывать, что прибор должен обязательно быть создан из металла толщиной не менее 3 мм. Где именно установить конструкцию, каждый автолюбитель решает самостоятельно.
При выборе месторасположения важно продумать не только размеры всего агрегата, теплообменника и фильтров, а также длину патрубков. Важно, чтобы загрузка партии топлива происходила через крышку сверху. Во время работы двигателя дозаправка осуществляется с незначительным выделением газа. Если ДВС заглушен, а в устройстве продолжает гореть масса, загрузка новой партии сопровождается появлением обильного облака.
Поместить подобное устройство можно только снаружи автомобиля и обязательно сзади. Это обусловлено тем, что к конструкции должен быть свободный доступ. Чем длиннее планируемые дистанции без дозаправки, тем больше размеры изделия. Составляющие элементы аппарата должны быть сделаны в соответствии с размерами бункера.
Газогенератор на грузовой машине можно разместить между кабиной и бортом с водительской стороны. Трубы, теплообменник и фильтрующий элемент разрешается размещать за кабиной. Фильтр тонкой очистки следует расположить на противоположной части кабины (за дверью пассажира). Для удобного удаления конденсата патрубки и дренажные краны выводят ниже фильтрующего элемента тонкой очистки.
На легковой машине аппарат рекомендуется устанавливать на открытой части. Для этого можно модифицировать багажник, приварить прицеп и т. д. Все зависит от вкусовых предпочтений и фантазий владельца. Не рекомендуется устанавливать оборудование в багажнике под крышкой, так как во время его эксплуатации в салон автомобиля будут попадать дым и угольная пыль.
Газогенератор — агрегат, с помощью которого получается горючий газ. После прогона последнего через очистительные фильтры и охлаждающий радиатор получается чистая и холодная газовая смесь. Оксид углерода может заменить классический вариант топлива, обеспечивая двигателю бесперебойную работу. Бензиновые ДВС функционируют с газогенераторным устройством без существенных потерь производительности.
Производство любого устройства начинается с изготовления чертежа. После изучения подробной информации человек имеет представление о внешней конструкции агрегата. Затем остается воплотить свою идею в жизнь.
Чтобы устройство выглядело эстетично, следует правильно подобрать детали. Для его изготовления понадобятся:
- бочка на 100 л;
- бидон из стали с плотной крышкой на фиксаторах;
- труба с толстыми стенами диаметром 15—16 см и длиной 30 см;
- огнетушитель;
- лист стали толщиной 0,6—1 см;
- часть бытового отопительного радиатора.
Сначала нужно вверху трубы проделать 5—6 отверстий. Она станет верхней частью конструкции. К одному из полученных отверстий следует приварить трубку подачи кислорода. Через остальные будет выходить газ. В нижней части необходимо приварить перфорированное днище из нержавейки. Получится колосниковая часть, на которой разместятся угли. Пыль будет выходить через отверстия.
С внутренней части получившегося стакана приваривается конус из металла для подачи углей. Затем следует приварить металлический лист с отверстием, размер которого совпадает с внутренним диаметром трубы. Конструкция должна размещаться перпендикулярно в верхней части трубки. Лист станет дном бункера. Функции последнего будет выполнять бидон.
Полученную заготовку помещают в бочку и приваривают таким образом, чтобы внизу осталось место для золы, а горлышко бидона размещалось над бочкой. Затем одно из отверстий бидона нужно совместить с камерой сгорания и соединить трубкой подачи кислорода. Далее в верхней части приваривают металлический лист, который перекрывает разницу размеров горловины бидона и бочки. Конструкция готова.
Сделать авто на дровах своими руками не так просто, как может показаться на первый взгляд. Процедура требует больших затрат сил и времени. Однако для умелого мастера, который готов экспериментировать и не боится трудностей, это вполне реальная задача. Очень важно подробно изучить устройство и принцип работы изделия, а также правильно составить его чертеж.
Отгремела Великая Отечественная война. Помимо множества проблем, свалившихся на СССР, была и острая нехватка жидкого топлива. Ситуация требовала экстренного решения. И тогда советский автопром пошел по новому для себя пути – газогенераторному.
Послевоенный кризис
В конце ноября 1941 года из авиабомбового завода №316 было создано предприятие по разработке и производству силовых агрегатов для авто, а также трансмиссий к танкам. Так, благодаря решению Государственного Комитета Обороны появился Миасский завод.
Задачи и сроки их исполнения перед предприятием поставили жесткие. Поэтому уже в начале весны 1942 года заводчане выдали готовое поршневое кольцо для нового двигателя ЗиС-5. А их коллеги еще спустя короткое время продемонстрировали трансмиссию. Вообще, только за тот год предприятие произвело порядка 9 тысяч моторов и примерно 15 тысяч коробок передач. Кроме этого на заводе трудились специалисты конструкторско-экспериментального отдела (с февраля 1942 года) под началом инженера А.С.Айзенберга.
Любопытно, что пока шла война, КЭО занимался лишь подготовкой документации. Его звездный час пришелся на послевоенные годы. Тогда страна начала испытывать сильный бензиновый голод. Образовавшийся дефицит требовалось срочно устранить. И тогда на арену вышел Уральский автомобильный завод (тот самый, расположенный в городе Миасс). Хотя многие советские предприятия пытались решить проблему, разведывая газогенераторное направление, роль ведущей скрипки отдали именно УралАзу.
По решению Наркомата (ноябрь 1946 года) предприятие начало налаживать выпуск грузовиков на базе ЗиС-5, оснащенных газогенераторной установкой.
Надо сказать пару слов о том, что представляла собой газогенераторная установка. Она состояла из самого газогенератора обращенного процесса газификации с центробежным нагнетателем. Кроме этого в состав системы входили: циклонный очиститель для грубой очистки газа (до него – охладитель), фильтры для тонкой очистки, вентилятор розжига, смеситель и предпусковой подогреватель (с начала 50-х годов).
Газогенератор ставили справой стороны. Поэтому пассажирская дверь являлась по совместительству и водительской. А вот фильтры тонкой очистки размещали с противоположной стороны. Газогенератор и центробежный нагнетатель соединялись друг с другом при помощи трубы, подводящей воздух. А крепились они (плюс фильтр) на раме двумя балками. Охладитель ставили под платформой вдоль рамы. Фильтры тонкой очистки, смеситель и вентилятор соединялись специальной составной трубой. Кстати, а вентилятор и подогреватель создатели «прописали»слева, немного выше подножки.
Вся эта «адская машина» в печи перерабатывала дрова, получая энергию, которая и приводила в действие авто.
Первопроходец
Пионером стал ЗиС-21А. Его оснастили деревянной кабиной и выгнутыми крыльями. В движение первопроходца приводил газ, получаемый из сожженных поленьев. А поскольку тогда еще точно не знали, каким аппетитом отличается автомобиль, испытания проходили в лесистых районах с налаженной инфраструктурой. Именно древесина стала единственным источником энергии для всего газогенераторного направления. Надо сказать, что в качестве топлива использовались не только поленья, но и любые отходы лесной промышленности.
Оговоримся сразу: если автомобиль ездит на дровах, это не значит, что он — паровоз без рельсов. Низкий КПД паровой машины с ее отдельной топкой, котлом и цилиндрами двойного-тройного расширения оставил паровые автомобили в числе забытой экзотики. А сегодня мы поговорим о «дровяном» транспорте с привычными нам ДВС, моторами, сжигающими топливо внутри себя.
Разумеется, затолкать дрова (или нечто подобное) в карбюратор вместо бензина пока еще никому не удавалось, а вот идея прямо на борту авто получать из древесины горючий газ и подавать его в цилиндры как топливо прижилась на долгие годы. Речь идет о газогенераторных автомобилях, машинах, чей классический ДВС работает на генераторном газе, который получают из древесины, органических брикетов, или угля. От привычного жидкого топлива, кстати, такие машины тоже не отказываются — они способны работать и на бензине.
Автомобиль с газогенераторной установкой. Фото wikipedia.org
Святая простота
Генераторный газ — это смесь газов, состоящая в основном из окиси углерода СО и водорода Н2. Получить такой газ можно, сжигая размещенную толстым слоем древесину в условиях ограниченного количества воздуха. На этом несложном принципе работает и автомобильный газогенератор, простой по сути агрегат, но громоздкий и конструктивно осложненный дополнительными системами.
Также, помимо собственно производства генераторного газа, автомобильная газогенераторная установка охлаждает его, очищает и смешивает с воздухом. Соответственно, конструктивно классическая установка включает в себя сам газогенератор, фильтры грубой и тонкой очистки, охладители, электровентилятор для ускорения процесса розжига и трубопроводы.
НПЗ вожу с собой
Простейший газогенератор имеет вид вертикального цилиндра, в который почти доверху загружается топливо — дрова, уголь, торф, прессованные пеллеты и т.п. Зона горения расположена внизу, именно здесь, в нижнем слое горящего топлива создается высокая температура (до 1 500 градусов по Цельсию), необходимая для выделения из более верхних слоев будущих компонентов топливной смеси — окиси углерода СО и водорода Н2. Далее горячая смесь этих газов поступает в охладитель, который снижает температуру, повышая таким образом удельную калорийность газа. Этот довольно крупный узел обычно приходилось помещать под кузовом машины. Расположенный следом по ходу газа фильтр-очиститель избавляет будущую топливную смесь от примесей и золы. Далее газ направляется в смеситель, где соединяется с воздухом, и окончательно приготовленная смесь направляется в камеру сгорания двигателя автомобиля.
Схема автомобиля ЗИС-21 с газогенератором
Как видите, система производства топлива прямо на борту грузовика или легковушки занимала довольно много места и немало весила. Но игра стоила свеч. Благодаря собственному — и к тому же дармовому — топливу свой автономный транспорт могли себе позволить предприятия, расположенные за сотни и тысячи километров от баз снабжения ГСМ. Это достоинство долго не могло затмить все недостатки газогенераторных автомобилей, а их было немало:
— существенное сокращение пробега на одной заправке;
— снижение грузоподъемности автомобиля на 150-400 кг;
— уменьшение полезного объема кузова;
— хлопотный процесс «дозаправки» газового генератора;
— дополнительный комплекс регламентных сервисных работ;
— запуск генератора занимает от 10-15 минут;
— существенное снижение мощности двигателя.
ЗиС 150УМ, опытная модель с газогенераторной установкой НАМИ 015УМ
В тайге заправок нет
Древесина всегда являлась основным топливом для газогенераторных автомобилей. В первую очередь, конечно, там, где дров в избытке, — на лесозаготовках, в мебельном и строительном производстве. Традиционные технологии лесопереработки при промышленном использовании древесины в эпоху расцвета «газгенов» около 30% от массы леса отпускали в отходы. Их и использовали как автомобильное топливо. Интересно, что правилами эксплуатации отечественных «газгенов» строжайше запрещалось использование деловой древесины, так как и отходов лесной промышленности было с избытком. Для газогенераторов годились как мягкие, так и твердые породы дерева.
Единственное требование — отсутствие на чурках гнили. Как показали многочисленные исследования, проведенные в 30-е годы в Научном автотракторном институте СССР, лучше всего в качестве топлива подходят дуб, бук, ясень и береза. Чурки, которыми заправлялись котлы газогенераторов, чаще всего имели прямоугольную форму со стороной 5-6 сантиметров. Сельскохозяйственные отходы (солома, лузга, опилки, кора, шишки и пр.) прессовали в специальные брикеты и также «заправляли» ими газогенераторы.
Главным недостатком «газгенов», как мы уже говорили, можно считать малый пробег на одной заправке. Так, одной загрузки древесными чурками советским грузовикам (см. ниже) хватало не более чем на 80-85 км пробега. Учитывая, что «заправляться» руководство по эксплуатации рекомендует при опустошении бака на 50-60%, то и вовсе пробег между заправками сокращается до 40-50 км. Во-вторых, сама установка, вырабатывающая генераторный газ, весит несколько сотен килограммов. К тому же двигатели, работающие на таком газе, выдают на 30-35% меньше мощности, чем их бензиновые аналоги.
Доработка автомобилей под дрова
Для работы на генератором газе автомобили приходилось приспосабливать, но изменения не были серьезными и порой были доступны даже вне заводских условий. Во-первых, в моторах повышали степень сжатия, чтобы не так существенна была потеря мощности. В некоторых случаях для улучшения наполнения цилиндров двигателя применялся даже турбонаддув. На многие «газифицированные» авто устанавливался генератор электрооборудования с повышенной отдачей, поскольку для вдувания воздуха в топку использовался достаточно мощный электровентилятор.
Для сохранения тяговых характеристик, в особенности это касалось грузовиков, при снизившейся мощности двигателя передаточные числа трансмиссии делали более высокими. Скорость движения падала, но для автомобилей, использующихся в лесной глуши и прочих пустынных и отдаленных районах это не имело решающего значения. Чтобы компенсировать изменившуюся из-за тяжелого газогенератора развесовку, в некоторых машинах усиливали подвеску.
Помимо того, из-за громоздкости «газового» оборудования отчасти приходилось перекомпоновывать автомобиль: менять, сдвигать грузовую платформу или урезать кабину грузовика, отказываться от багажника, переносить выхлопную систему.
Золотая эра «газгена» в СССР и за границей
Эра расцвета газогенераторных автомобилей пришлась на 30-40-е года прошлого века. Одновременно в нескольких странах с большими потребностями в автомобилях и малыми разведанными запасами нефти (СССР, Германия, Швеция) инженеры крупных предприятий и научных институтов взялись за разработку автотранспорта на дровах. Советские специалисты больше преуспели в создании грузовых автомобилей.
С 1935 года и до самого начала Великой Отечественной войны на разных предприятиях Министерства лесной промышленности и ГУЛАГа (Главное Управление ЛАГерей, увы, реалии той поры) «полуторки» ГАЗ-АА и «трехтонки» ЗИС-5, а также автобусы на их базе переделывались для работы на дровах. Также отдельными партиями газогенераторные версии грузовиков производились самими заводами-изготовителями машин. Например, советские автоисторики приводят цифру 33 840 — столько было выпущено газогенераторных «полуторок» ГАЗ-42. Газогенераторных ЗИСов моделей ЗИС-13 и ЗИС-21 в Москве выпущено более 16 тыс. единиц.
За довоенное время советскими инженерами было создано более 300 различных вариантов газогенераторных установок, из которых 10 дошли до серийного производства. Во время войны серийными заводами были подготовлены чертежи упрощенных установок, которые могли изготавливаться на местах в автомастерских без применения сложного оборудования. По воспоминаниям жителей северных и северо-восточных регионов СССР, грузовики на дровах можно было встретить в глубинке вплоть до 70-х годов ХХ века.
В Германии во время Второй Мировой войны наблюдался острый дефицит бензина. КБ двух компаний (Volkswagen и Mercedes-Benz) получили задание разработать газогенераторные версии своих популярных компактных машин. Обе фирмы в довольно сжатые сроки справились с поставленной задачей. На конвейер встали Volkswagen Beetle и Mercedes-Benz 230. Интересно, что у серийных авто дополнительное оборудование даже не выступало за стандартные габариты «легковушек». В Volkswagen пошли еще дальше и создали опытный образец «дровяного» армейского Volkswagen Тур 82 («кюбельваген»).
Volkswagen Тур 82
Дровяные машины сегодня
К счастью, главное достоинство газогенераторных автомобилей — независимость от сети АЗС, сегодня стало малоактуальным. Однако в свете современных экологических веяний на первый план вышло другое достоинство автомобилей на дровах — работа на возобновляемом топливе без какой-либо его химической подготовки, без дополнительной траты энергии на производство топлива. Как показывают теоретические расчеты и практические испытания, мотор на дровах меньше вредит атмосфере своими выбросами, чем аналогичных двигатель, но уже работающий на бензине или солярке. Содержание выхлопных газов очень схоже с выбросами ДВС, работающих на природном газе.
И тем не менее тема с автомобилями на дровах утратила свою былую популярность. Забыть о газогенераторах не дают в основном инженеры-энтузиасты, которые ради экономии на топливе или в качестве эксперимента переоборудуют свои личные машины для работы на генераторном газе. На постсоветском пространстве есть удачные примеры «газгенов» на базе легковушек АЗЛК-2141 и ГАЗ-24, грузовика ГАЗ-52, микроавтобуса РАФ-2203 и пр. По словам конструкторов, их творения могут проезжать на одной заправке до 120 км со скоростью 80-90 км/ч.
К примеру, переведенный житомирскими инженерами в 2009 году на дрова ГАЗ-52 расходует около 50 кг древесных чурок на 100 км пробега. По словам конструкторов, подкидывать дровишки нужно каждые 75-80 км. Газогенераторная установка традиционно для грузовиков расположилась между кабиной и кузовом. После розжига топки должно пройти около 20 минут, прежде чем ГАЗ-52 сможет начинать движение (в первые минуты работы генератора выработанный им газ не имеет нужных горючих свойств). По расчетам разработчиков, 1 км на дровах обходится в 3-4 раза дешевле, чем на дизельном топливе или бензине.
Газогенераторная установка ГАЗ-52
Единственная на сегодняшний день страна, в которой массово используются автомобили на дровах, — это Северная Корея. В связи с тотальной мировой изоляцией там наблюдается определенный дефицит жидкого топлива. И дрова снова приходят на выручку тем, кто оказался в нелегком положении.
Может ли машина ездить на дровах: принцип работы газогенератора
Звучит как анекдот. Но людям, работающим на лесозаготовительных предприятиях в далёких 30-х годах прошлого столетия, было не смешно. Заправок в лесу не предусмотрено, а когда заканчивался бензин, ехали на полешках.
Однако стоит заметить, что техника, работающая на древесине — не всё равно, что паровоз, колесящий по дорогам. Первые паровые агрегаты обладали низким КПД, отдельной топкой, двигателем с парой цилиндров и дополнительной системой двойного расширения. Сегодня они — настоящая экзотика. Герой статьи же оснащён традиционным силовым агрегатом и дополнительными моторами, сжигающими полешки.
Конечно, наколоть дрова и каким-то образом запихнуть их прямо в карбюратор — задача из области фантастики, которую никто не смог осуществить. Тогда как идея прямо во время движения производить из дерева газ, а потом подавать полученную энергию в ДВС, была популярна в течение нескольких десятилетий.
Называется чудо техники — газогенераторный автомобиль. Это устройство, чей силовой агрегат «кушает» газ, добытый из прессованных брикетов, полешек или угля. Интересно, что и от традиционного источника энергии машина не откажется. Она одинаково хорошо принимает и древесину, и бензин.
Принцип работы устройства
Стандартный газогенератор представляет собой довольно громоздкий цилиндр вытянутой формы.
@hodor.lol
Сама конструкция выглядит следующим образом:
- Внутренняя часть почти полностью забивается углём, дровами, торфом и прочим органическим сырьём, пригодным для применения.
- В нижней области цилиндра создаются условия, благоприятные для горения топлива — температура, достигающая 1 500°С. Только в такой среде выделяются водород и окись углерода.
- Также ёмкость оснащается системой охлаждения. Сюда поступает вырабатываемый газ, где он проходит процедуру уменьшения удельной калорийности топлива. Обычно система располагается под днищем кузова транспортного средства.
- Дальше газ проходит через несколько фильтров, которые удаляют ненужные компоненты.
- Потом уже очищенное сырьё поступает в отсек, где смешивается с кислородом.
- Последний этап — готовый состав подаётся в силовой агрегат.
Как можно заметить, вся система отличалась довольно крупными габаритами и занимала большую часть полезной площади. Но оно того стоило — благодаря собственному, а порой и бесплатному сырью, подобную технику могли эксплуатировать предприятия, находящиеся за несколько сотен, а то и тысяч, километров от заправочной станции. Этот «жирный» плюс в течение длительного времени не мог перевесить обширный список минусов:
- небольшой километраж за одну заправку;
- снижение грузоподъёмности;
- уменьшение полезной площади грузового отсека;
- дополнительные ремонтные и обслуживающие манипуляции;
- длительный запуск генератора;
- уменьшение мощности двигателя.
@pay.diary.ru
Где заправиться в лесу?
Древесина — главный источник энергии для силовых агрегатов, оборудованных газогенераторной системой. Потому особенно актуальной подобная техника была там, где было много дров — в строительном производстве, на лесоповалах. При старых способах заготовки древесины более 30% сырья превращалось в отходы. Их и применяли для заправки газогенераторной техники.
Справка. По существующим правилам строго запрещалось использование ценных пород древесины.
Работать агрегат мог как на твёрдых сортах, так и на мягких. Главное условие — на полешках не должно было быть гнили. Интересно, что в 30-е года, в эпоху расцвета газгена, Научный автотракторный завод СССР даже провёл исследование, которое показало, что наиболее пригодные дрова из берёзы, бука и дуба. Чуркам, которым отводилась роль оригинального топлива, придавалась прямоугольная форма высотой 6 см. Если использовались различные отходы сельхозпроизводства (солома, опилки, шишки и прочее), их предварительно спрессовывали в небольшие брикеты, а только потом «кормили» ими машину.
Золотая пора газогенераторных автомобилей
Наиболее широкое применение газген приобрёл в 30-е и 40-е года прошлого столетия. Причём разработки велись сразу в нескольких странах — Швеция, Германия, СССР. В них была наибольшая потребность в транспортных средствах, и именно здесь было плохо разведано нефтяное месторасположение. Достичь лучших результатов удалось специалистам из советских научно-исследовательских институтов.
С 1935 года началось активное внедрение новой технологии. В основном газогенераторные автомобили использовались в лесозаготовительной, строительной промышленности, ГУЛАГах. Переработке подвергались знаменитые «полуторки», ЗИС-5, пассажирские автобусы.
@pay.diary.ru
За период с 1935 по 1941 год было выпущено порядка трёхсот разнообразных вариантов газгенной установки. Причём только десять из них были допущены к серийному производству. В военное время, с учётом сложившихся событий, конструкция была доработана таким образом, чтобы установку можно было собрать прямо на месте, без использования специальных приспособлений.
Справка. По словам жителей северных регионов, технику, передвигающуюся на древесине, можно было наблюдать даже в 70-е года прошлого столетия.
Германия также активно занималась разработкой дровяных моделей. Особенно на фоне дефицита традиционных видов топлива, вызванного началом Второй мировой войны. Основные действия развернулись на мощностях заводов Volkswagen и Mercedes. Интересно, что оба концерта не только успешно справились с поставленной задачей, но и умудрились не выйти за привычные габариты серийных «легковушек». А инженеры «Фольксваген» даже выпустили концепт дровяного армейского джипа — Volkswagen TYP-82, прозванного в народе «кюбельваген».
@seriouswheels.com
Автомобили на дровах в современном мире
Сегодня основное достоинство газогенераторных установок — автономная работа — утратило актуальность. Но с учётом экологической обстановки и популярности «зелёных» автомобилей второе преимущество, а именно — возможность работы без вредных выбросов, выходит на первый план.
Как показывают многочисленные опыты, газогенераторные силовые агрегаты выделяют выхлопные газы, сходные по составу с моторами, работающих на пропан-бутане или метане. Несмотря на это, актуальность подобной техники стремится к нулю.
Забыть о ней не позволяют многочисленные «кулибины» и жители Северной Кореи. Последние очень активно используют дровяную технологию, ведь страна настолько изолирована от внешнего мира, что недостатку традиционных видов топлива удивляться не стоит. Именно здесь полешки приходят на выручку тем, кто оказался в столь незавидном положении.
Принцип работы газового генератора | Строительный портал
В поисках альтернативного источника энергии пришло понимание, что не обязательно добывать газ в шахтах, чтобы затем сжигать его в котлах и двигателях внутреннего сгорания, горючий газ можно добывать из отходов производства и древесины. Газогенератор или как его еще называют генератор газов путем сжигания местного топлива – дров, торфа, древесного угля, опилок и других отходов древесины, а также иногда других органических остатков способны выделять/генерировать горючие газы, такие как СО, СН4, Н2 и другие. Вариантов использования полученного газа несколько, но в любом случае в основу каждого устройства положен принцип газогенератора. О том, как работает газогенератор, из каких элементов он состоит, а также какие процессы проходят внутри него, мы расскажем в данной статье. Также рассмотрим варианты дальнейшего использования полученного газа и места, где можно устанавливать подобные агрегаты.
- Преимущества и недостатки генераторов газа
- Принцип работы газового генератора – газогенератора
- Типы газогенераторов
- Место установки газового генератора
- Дровяной газовый генератор своими руками
Итак, какие же существуют варианты использования газа, полученного в газогенераторе?
Первый – горючий газ направляется к газовой плите на кухне и используется для приготовления пищи. Второй – горючий газ сжигается сразу же в пиролизном котле отопления с газогенератором, соответственно, используется для отопления дома или теплиц. Кстати, подобные котлы могут называться газовым котлом на дровах, твердотопливным пиролизным котлом, газогенераторным котлом на дровах. Все они могут использоваться как для бытовых нужд, так и для отопления огромных производств и цехов или предприятий. Третий – горючий газ может направляться в двигатель внутреннего сгорания, который служит приводом насосной станции или генератора электроэнергии. Газовый генератор на дровах позволяет получать электроэнергию в тех регионах, где нет возможности провести линии электропередач, выполнить прокладку газопровода и затруднен подвоз газа в баллонах. Помимо автономности у газогенераторов есть и другие преимущества, которые мы раскроем ниже.
Преимущества и недостатки генераторов газа
В качестве примера рассмотрим преимущества и недостатки газогенераторных котлов отопления. Пиролизные котлы относятся к категории твердотопливных, но существенно отличаются от обычных печей на дровах или угле, где происходит обычный процесс сгорания топлива.
Преимущества газогенераторных котлов:
- КПД газогенераторных котлов находится в диапазоне 80 – 95 %, в то время как КПД обычного твердотопливного котла редко превышает 60 %.
- Регулируемый процесс горения в газогенераторном котле – одна закладка дров может гореть от 8 до 12 часов, для сравнения в обычном котле горение длится 3 – 5 часов. В газогенераторных котлах с верхним горением сгорание дров длится до 25 часов, а уголь может гореть 5 – 8 дней.
- Топливо сгорает полностью, поэтому чистить зольник и газоход приходится не часто.
- Благодаря тому, что процесс горения можно регулировать (мощность регулируется в диапазоне 30 – 100 %), работу котла можно автоматизировать, как например, газового или жидкотопливного.
- Выброс вредных веществ в атмосферу из газогенератора минимален.
- Газогенераторные котлы экономнее обычных.
- Топливо для газогенераторов не обязательно должно быть подсушено до 20 % влажности, существуют модели котлов, в которых можно использовать древесину до 50 % влажности и даже свежесрубленную.
- Возможность загрузки в котел неколотых поленьев до 1 м длиной и даже больше.
- Помимо дров и отходов древесной промышленности в пиролизных котлах можно утилизировать резину, пластмассу и другие полимеры.
- Высокая безопасность котла по сравнению с обычным твердотопливным котлом обеспечивается автоматикой и материалами, из которых изготовлен агрегат, а в особенности камеры сгорания.
Если говорить о газогенераторах, которые используются для производства электроэнергии, то они обладают точно такими же достоинствами, такими как экологичность, экономичность, высокий КПД, высокое октановое число 110 – 140, универсальность в плане используемого топлива и большая эффективность в зимнее время.
Недостатки газогенераторных котлов:
- На газовый генератор цена в 1,5 – 2 раза выше, чем на обычный твердотопливный котел.
- В большинстве своем газогенераторы энергозависимы, так как для подсоса воздуха используется вентилятор, но также существуют модели, которые могут работать и без электричества.
- Если использовать газогенераторный котел на мощности ниже 50 %, то наблюдается нестабильное горение – как результат выпадение в осадок дёгтя, который скапливается в газоходе.
- Температура обратки отопления не должна быть ниже 60 °С, иначе в газоходе будет выпадать конденсат.
- Обычно газогенераторы требовательны к влажности топлива, но как уже писалось выше, есть модели, в которых можно сжигать даже свежесрубленную древесину.
Других существенных недостатков газогенераторов не выявлено.
Кстати, газогенераторы – не такое уж и новое изобретение. Еще в середине прошлого века, когда большая часть нефтяных ресурсов Германии шла на вооружение, в качестве топлива для автомобилей использовались дрова. Даже на грузовые автомобили устанавливались газогенераторы. Современные агрегаты не слишком далеко ушли в своей конструкции, но, тем не менее, основательно усовершенствованы.
Принцип работы газового генератора – газогенератора
В генераторе газов или газогенераторе из твердого топлива добывается горючий газ. Основной секрет заключается в том, что в камеру сгорания подается воздух, объема которого недостаточно для полного сгорания топлива, при этом соблюдается высокая температура порядка 1100 – 1400 °С. Полученный газ охлаждается и направляется к потребителю или двигателю внутреннего сгорания, если, например, планируется добывать электричество. Более детально принцип работы газогенератора рассмотрим ниже, уточнив какой процесс в каком элементе агрегата происходит.
Устройство газового генератора на древесине
Рассмотрим устройство газогенератора бытового назначения. Сразу хотелось бы отметить, что пиролизные котлы с газогенератором отличаются от предложенной схемы, так как сгорание газа происходит внутри котла во второй камере сгорания. Мы же рассмотрим лишь сам газогенератор, на выходе из которого получается горючий газ.
Схема газогенератора:
Корпус газогенератора изготовлен из листовой стали и имеет сварные швы. Самая распространенная форма корпуса – цилиндрическая, но она вполне может быть и прямоугольной. К нижней части корпуса приварено днище и ножки, на которых будет стоять газогенератор.
Бункер или камера заполнения служит для загрузки внутрь газогенератора топлива. Он также имеет цилиндрическую форму и изготовлен из малоуглеродистой стали. Бункер установлен внутри корпуса газогенератора и закреплен болтами. На крышке люка, ведущего в бункер, на кромках использован асбестовый уплотнитель или прокладка. Так как асбест запрещен для использования в жилых помещениях, то существуют модели газогенераторов, уплотнители крышки которой изготовлены из другого материала.
Камера сгорания находится в нижней части бункера и изготовлена из жаропрочной стали, иногда внутренняя поверхность камеры сгорания отделывается керамикой. В камере сгорания происходит горение топлива. В нижней ее части происходит крекинг смол, для чего там установлена горловина, изготовленная из жаропрочной хромистой стали. Между корпусом и горловиной находится прокладка – уплотнительный асбестовый шнур. В средней части камеры сгорания находятся фурмы для подачи воздуха. Фурмы представляют собой калиброванные отверстия, которые соединяются с воздухораспределительной коробкой, связанной с атмосферой. Фурмы и распределительная коробка также изготавливаются из жаропрочной стали. На выходе из воздухораспределительной коробки установлен обратный клапан, который препятствует выходу горючего газа из газогенератора. Чтобы повысить мощность двигателя или иметь возможность использовать дрова повышенной влажности (более 50 %), перед воздухораспределительной коробкой можно установить вентилятор, который будет нагнетать внутрь воздух.
Колосниковая решетка служит для того, чтобы поддерживать раскаленные угли. Она располагается в нижней части газогенератора. Через отверстия решетки зола от сгоревших углей проваливается в зольник. Чтобы колосниковую решетку можно было очищать от шлака, ее средняя часть сделана подвижной. Для поворота чугунных колосников предусмотрен специальный рычаг.
Загрузочные люки оснащены герметично закрывающимися крышками. Например, верхний загрузочный люк откидывается горизонтально и уплотнен асбестовым шнуром. В креплении крышки есть специальный амортизатор – рессора, которая приподнимает крышку в случае избыточного давления внутри камеры. Сбоку корпуса есть также два загрузочных люка: один сверху – для добавления топлива в зону восстановления, второй снизу – для удаления золы. Отбор газа производится в зоне восстановления, поэтому чаще всего в верхней части газогенератора, но также возможно отведение газа и из нижней части агрегата. Отбор газа производится через патрубок, к которому приварены трубы газопровода. Не обязательно сразу же выводить газ за пределы корпуса газогенератора, пока он горячий, его можно использовать для подогрева и подсушивания дров или другого топлива в камере загрузки. Для этого отводящий газопровод проводится по кольцевой вокруг камеры, между корпусом газогенератора и бункером.
Фильтр «Циклон» и фильтр тонкой очистки располагаются за корпусом газогенератора. Они изготовлены из труб, наполненных фильтрующими элементами.
Прежде чем поступить в фильтр тонкой очистки, газ проходит через охладитель. А после фильтра тонкой очистки очищенный газ поступает в смеситель, где смешивается с воздухом. И только затем газо-воздушная смесь поступает в двигатель внутреннего сгорания.
Более наглядно последовательность движения горючего газа, после того как он вышел из газогенератора, показана на схеме ниже.
Дрова или другое топливо горит в камере сгорания, окисляясь воздухом, поступающим в камеру сгорания через фурмы из воздухораспределительной коробки. Полученный горючий газ поступает в фильтр Циклон, где очищается. Затем охлаждается в фильтре грубой очистки. Затем уже охлажденный газ поступает в фильтр тонкой очистки, а затем в смеситель. Из смесителя полученная смесь поступает в двигатель.
Процесс превращения топлива в газ
И все же: как из твердого топлива получается газ? Внутри газогенератора происходит некий процесс превращения, который разбит на несколько этапов, происходящих в разных зонах:
Зона подсушки находится в верхней части бункера. Здесь температура порядка 150 – 200 °С. Топливо подсушивается горячим газом, который движется по кольцевому трубопроводу, как было описано выше.
Зона сухой перегонки расположена в средней части бункера. Здесь без доступа воздуха и при температуре 300 – 500 °С топливо обугливается. Из древесины выделяются кислоты, смолы и другие элементы сухой перегонки.
Зона горения находится внизу камеры сгорания в зоне, где расположены фурмы, через которые поступает воздух. Здесь при подаче воздуха и температуре 1100 – 1300 °С обугленное топливо и элементы сухой перегонки сгорают, в результате чего образуются газы СО и СО2.
Зона восстановления находится выше зоны горения между колосниковой решеткой и зоной горения. Здесь газ СО2 поднимается вверх, проходит через раскаленный уголь, взаимодействует с углеродом (С) угля и на выходе образуется газ СО – окись углерода. В данном процессе также участвует влага из топлива, поэтому помимо СО образуется СО2 и Н2.
Зоны горения и восстановления называются зоной активной газификации. В результате генераторный газ состоит из нескольких компонентов:
- Горючие газы: СО (оксид углерода), Н2 (водород), СН4 (метан) и СnНm (непредельные углеводороды без смол).
- Балласт: СО2 (углекислый газ), О2 (кислород), N2 (азот), Н2О (вода).
Полученный газ охлаждается до температуры окружающей среды, затем очищается от муравьиной и уксусной кислоты, золы, взвешенных частиц и смешивается с воздухом.
Типы газогенераторов
Различают три типа газогенераторов: прямого процесса газогенерации, обратного и горизонтального.
Газогенераторы прямого процесса могут сжигать уголь полукокс и антрацит – топливо небитуминозное. Конструктивное отличие данного типа агрегатов в том, что воздух поступает через колосниковую решетку снизу, а забор газа производится сверху. В газогенераторах прямого процесса влага из топлива не попадает в зону горения, поэтому ее подводят специально. Обогащение генераторного газа водородом из воды повышает мощность генератора.
Газогенераторы опрокинутого или обращенного процесса предназначены для сжигания смолистого топлива – дров, древесного угля и отходов. Их конструктивное отличие в том, что воздух подается в среднюю часть – в зону горения, а забор газа производится ниже зоны горения – в зольнике. Обычно в агрегатах такого типа отобранный горячий газ используется для подогрева топлива в бункере.
Газогенераторы горизонтального или поперечного процесса газификации отличаются тем, что воздух в них подводится сбоку – в нижней части корпуса, причем подается он с высокой скоростью дутья через фурмы. Отбор газа производится напротив фурмы через газоотборную решетку. Активная зона газификации в газогенераторе горизонтального процесса очень мала и сосредоточена между концом фурмы и газоотборной решеткой. Время пуска такого генератора намного меньше, также он легко приспосабливается к смене режимов работы.
Место установки газового генератора
Газогенераторы и газогенераторные котлы отопления можно устанавливать как внутри жилых помещений, например, в подвалах и цокольных этажах, так и на улице.
Так называемые пеллетные котлы чаще всего устанавливают в доме, так как их загрузка не сопряжена с большим количеством мусора, а также мешки с пеллетами весят немного и могут храниться где-то рядом с котлом.
Газогенераторы на дровах, а в особенности на дровах большой длины, имеет смысл устанавливать на улице недалеко от места хранения дров. Так можно будет подвезти дрова на тачке непосредственно к котлу или газогенератору и не спускать их в подвал дома. Стоящий на улице котел избавляет от грязи и золы в подвале. Особенно это актуально для деревянных домов, где повышенные нормы пожаробезопасности. Внешний корпус котла изготавливается из нержавеющей стали, которая не подвержена коррозии. Также котлы теплоизолированы насыпной теплоизоляцией, чтобы температура окружающей среды минимально влияла на процесс газификации и скорость пуска котла. Система регулирования размещается в стальном кожухе под крышкой, чтобы на нее не попадали осадки. Дымовая труба имеет двойные стенки. Если вас интересует, как подключить газовый генератор, если он стоит на улице, то ответ прост – трубы прокладываются в земле, чтобы они минимально охлаждались, если это котел отопления. Трубы отопления подходят к котлу снизу, а сам котел устанавливается так, чтобы при длительных перерывах в использовании он не замерзал.
Кстати, как уже отмечалось, длительность процесса горения топлива в котле может быть от 12 часов и достигать 25 часов. В зависимости от мощности котла и площади отапливаемого помещения, его придется топить раз в два дня, а иногда и раз в неделю. Чтобы сохранить вырабатываемое котлом тепло на столь длительный период, используется теплоаккумулятор.
Дровяной газовый генератор своими руками
В том чтобы изготовить газогенератор своими руками, нет ничего сверхсложного. Многие используют такой агрегат для бытовых нужд или устанавливают на автомобиль. Перед тем как начать изготавливать газогенератор самостоятельно, необходимо ознакомиться с принципом его действия и выбрать подходящую для себя схему работы.
Понадобятся – бочка, трубы или старая батарея радиаторов, фильтры тонкой и грубой очистки газа, вентилятор. С другой стороны набор элементов может быть самым разным, все зависит от фантазии исполнителя.
Ниже посмотрите видео пример газогенератора самостоятельного изготовления.
Схема газогенратора:
В интернете можно найти как фото, так и чертежи по монтажу газовых генераторов и пиролизных котлов. Есть даже умельцы, которые берут за основу готовый проверенный котел и полностью повторяют его в домашних условиях. Получается дешевле намного.
Схема газогенераторного котла:
Отличие пиролизного котла от обычного газогенератора в том, что он состоит из двух камер сгорания: в одной сгорает топливо и образуется газ, а в другой – сгорает газ и находится теплообменник. Устройство и принцип работы газогенератора мы уже рассмотрели, добавьте в него только вторую камеру сгорания, которая должна располагаться вверху, и теплообменник сверху. Иногда теплообменник располагают сбоку. Также не забудьте о разных типах газогенераторов, так что вторая камера сгорания может находиться не только сверху.
При сборе дымохода постарайтесь собирать его в последовательности, обратной движению дыма, так на его стенках будет меньше оседать всякой гадости. Сам дымоход лучше сделать легкоразбираемым, чтобы его можно было легко и быстро чистить. Пространство вокруг котла отопления должно быть свободным, так как он нагревается в процессе работы. После монтажа котла придется изучить его «повадки» и подобрать оптимальный для себя режим работы, при котором сгорают все смолы.
Хотелось бы отметить, что газогенератор может рассматриваться не только как сжигатель полезной древесины, но и как утилизатор отходов. В нем можно сжигать остатки линолеума, пакетов, мешков, резины, пластиковых бутылок и другого бытового мусора.
Как работают печи для пиццы | Аутентичная духовка
Полное объяснение того, как работают печи для пиццы
Внутри кирпичной печи разжигается огонь дровами или, в некоторых случаях, газом.
Тепло, выделяемое используемым источником энергии, нагревает внутреннюю массу духового шкафа. Кирпичная печь на дровах (или газе) спроектирована так, чтобы сохранять тепло и излучать его на ровную поверхность. Для правильного приготовления пицца должна быть равномерной сверху и снизу. Ваш огонь может полностью выгореть или, в идеале, просто остаться раскаленным пеплом и углями.
Пиццу следует готовить прямо на очаге, а запекать — на противне. Идеальная температура пода для приготовления пиццы составляет около 350-425 градусов по Цельсию. Тесто для пиццы должно быстро подняться, но не лопнуть. Содержание воды в тесте важно и зависит от температуры духовки.
Лучшие печи для пиццы сохраняют равномерное тепло в течение длительного времени и не требуют дополнительного нагрева. Для достижения наилучших результатов приготовления вам требуются продукты, предназначенные для СОХРАНЕНИЯ тепла при требуемых температурах приготовления… скажем, от 350 до 425 градусов по Цельсию на очаге и окружающем куполе.Мы называем это «парящей температурой» (период, в течение которого внутренняя температура остается такой же или подобной без добавления дополнительной энергии в течение определенного периода времени). Во время приготовления пицца должна быть равномерной и под ней, и сверху. Равномерная плотность и масса, а также изоляция. Нет учебника, чтобы показать вам это ……. Сотни печей позже вы сможете понять это так же, как и мы.
ДуховкиAuthentic Ovens имеют длительную равномерную температуру парения, что выделяет нас среди остальных. Равномерное тепло от цельного очага и купола из огнеупорного кирпича.Каждый внутренний кирпич в духовке склеен друг с другом, что делает его одним предметом, поэтому тепло передается равномерно. Изоляция на 100% состоит из керамического волокна, рассчитанного на температуру 1670 градусов Цельсия.
Для этого мы используем прессованный огнеупорный кирпич с высоким содержанием глинозема. Authentic Oven вложила много времени и денег в исследования по разработке правильной температуры парения, регулируя уровни плотности, чтобы сделать долгое парение, и регулируя содержание глинозема и толщину каждого кирпича, чтобы регулировать скорость передачи тепла.Ни один из продуктов из набора не обеспечивает такого удержания тепла. Комплектные и литые печи не могут достичь этого, поскольку в их конструкции нет качества и детализации.
Для достижения этой эффективной формулы во внутреннем куполеAuthentic Ovens используются специальные сжатые огнеупорные кирпичи. 2,5 г / см3 прессованного и 42% глинозема на КАЖДОЙ ПЕЧИ. Наша миссия — быть мировыми лидерами в производстве и дизайне кирпичных печей по внешнему виду и производительности.
Дровяные печи разной конструкции лучше подходят для разных видов готовки, поэтому подумайте, какой вид готовки вы хотите приготовить.По сути, чем больше плотность внутренней структуры духовки, тем она универсальнее, но первоначальный нагрев займет больше времени. Authentic Oven спроектирует и произведет бытовые или коммерческие печи в соответствии с вашими потребностями. Мы считаем, что качество, производимое в Новой Зеландии с использованием высокопроизводительных продуктов, — это правильный путь.
Определяющим отличием Authentic Oven от печей наших конкурентов является то, что используется прессованный огнеупорный кирпич с высоким содержанием глинозема. Наши духовые шкафы сохраняют тепло, как никакой другой продукт на рынке.Многие печи разливают в формы с продуктами, не содержащими глинозема и не сохраняющими тепло. Подлинные духовые шкафы также содержат 50 мм 100% -ной изоляции из керамического волокна, окружающей огнеупорные кирпичи и очаг, создавая равномерно нагретую поверхность для приготовления пищи и духовку.
Изоляция настолько эффективна, что, хотя внутренняя температура может достигать 800 ° C, внешняя облицовка достигает 55-75 ° C только в течение нескольких часов при постоянном нагреве. Настоящие дровяные печи сделаны из лучших доступных продуктов.Абсолютно бескомпромиссное качество — наша цель, и на сегодняшний день у нас более 2000 довольных клиентов по всему миру.
Традиционная система наружного переднего дымохода Authentic Oven разработана для работы внутри и снаружи помещений. Идеально всасывает дым с минимальными потерями тепла. Духовки с системой дымохода внутри области купола или сзади просто не так эффективны в удержании тепла, поскольку тепло уходит из дымохода, не передаваясь массе купола. См. Рисунок выше с изображением правильной конструкции системы дымохода.
После того, как ваш заказ будет размещен, вы можете зайти на завод и посмотреть, как продвигается строительство ваших печей. Вы оцените произведение искусства, которое является вашей подлинной духовкой.
Как работают печи для пиццы на дровах?
Как работают печи для пиццы на дровах? В дровяных печах используется остаточное тепло, живой огонь и раскаленные угли для создания различных условий для приготовления пищи, в том числе:
— Топка в печи
— Уголь в печи
— Сохраненное тепло
В этом разделе мы опишем механизм работы вашей духовки, а затем опишем различные стили приготовления пищи на дровах в следующем разделе.
Приготовление на огне
При приготовлении пищи на живом огне духовой шкаф Forno Bravo готовит одновременно тремя способами, как показано на следующих трех рисунках:
— Отраженное тепло
— Конвекция
— Проводящее тепло
Благодаря отражающему теплу, пламя живого огня отражается от купола на вашу еду. Это отражающее тепло позволяет готовить пищу, например пиццу, а также заряжать пол для приготовления пищи, возвращая тепло в пол, чтобы заменить тепло, теряемое при приготовлении пищи.
Поскольку духовка Forno Bravo дышит, всасывая холодный воздух через нижнюю половину отверстия духовки и выбрасывая горячий воздух через верхнюю половину отверстия, она постоянно перемещает горячий влажный воздух через верхнюю часть блюд. В то время как современные конвекционные печи используют вентиляторы и нагревательные змеевики для перемещения горячего сухого воздуха внутри духовки, ничто не может сравниться с естественной конвекцией.
Наконец, тепло, накопленное на полу, передается непосредственно в пищу, которую кладут на нее. Это справедливо как для хлеба и пиццы, которые кладут прямо на пол, так и для кастрюль и сковородок, установленных на нем.
Именно эта уникальная кулинарная способность позволяет вам приготовить итальянскую пиццу, домашний хлеб и отличное жаркое в печи Forno Bravo, а также то, что делает приготовление пищи на дровах непохожим на любой другой способ кулинарии.
Угольки в печи
Есть много блюд, которым не нужен или не нужен сильный жар живого огня и очень горячая духовка на 700ºF. Для этого типа приготовления дайте огню погаснуть и дайте духовке остыть. Вы можете использовать тепло углей и горячую духовку для запекания, подрумянивания, поджаривания и гриля, а также для того, чтобы ваша духовка сохраняла достаточно тепла для более длительных периодов приготовления.
Приготовление с сохранением тепла
Для выпечки хлеба и других блюд при температуре, при которой вы обычно готовите в обычной духовке, ваша духовка будет готовить в течение нескольких часов с сохраненным теплом. Вы должны разгребать угли с огня, а затем закрыть дверцу духовки, чтобы температура в духовке снизилась.
С помощью этого типа приготовления можно выпекать хлеб, десерты и мелкое жаркое, а при понижении температуры духовки можно медленнее готовить бобы, супы и тушеные блюда, а также мясо и ребрышки длительного приготовления.
Принцип работы водогрейного котла на дровах и 3 преимущества |
Водогрейный котел в некоторых случаях просто необходим Водогрейные котлы представляют собой изделие из металла, в котором происходит сгорание твердого топлива, в результате чего выделяется тепло и нагревается теплоноситель в специальном баке. Вода используется в качестве теплоносителя в водогрейных котлах.
Водонагреватель на дереве: характеристики
Водонагреватель — один из самых простых и удобных способов нагрева воды для различных нужд в частных домах или других помещениях.Помимо горячей воды, которую можно получить, затопив столб горячей воды, пользователь получает тепло путем обогрева помещения, в котором он находится.
Водонагревательные колонки немного отличаются, основные отличия между ними следующие :
- Материал для изготовления печи, некоторые колонны горячей воды оснащены чугунной печью, которая служит намного дольше.
- Материал самой емкости, в которой находится вода. Лучше всего бак из нержавеющей стали, но цена на такие изделия немного выше.Через центр бака от топки проходит дымоходная труба, от которой нагревается вода.
- В некоторых моделях бак и топка устанавливаются отдельно, и это считается большим преимуществом, так как позволяет установить душевую лейку практически в любом удобном положении. Но при этом нагрев воды происходит несколько медленнее, чем в тех моделях, где бак и печь соединены в единое целое.
Водонагреватели бывают нескольких типов
Для того, чтобы водонагреватель работал исправно и прослужил долгое время, необходимо, чтобы резервуар для воды был постоянно полон.
Обычно бак наполняется снизу через шланг или трубу, подсоединенную к штуцеру.
Нагретая вода поднимается вверх к смесителю, а холодная вода продолжает поступать снизу. Для того, чтобы циркуляция имела место, необходимо, чтобы давление в системе было не ниже 0,06 МПа, при меньшем давлении столб воды работать не может.
Титан на дровах: описание и принцип работы
Первые титаны появились в 19 веке и с тех пор принцип действия этого изделия не изменился.Чтобы получить горячую воду, необходимо загрузить в топку дрова или уголь. В результате их сгорания выделяется тепло и горячий воздух, который вместе с дымом поднимается по дымоходу. А дымоход, в свою очередь, проходит через емкость с водой. Под воздействием тепла вода начинает циркулировать, горячая вода собирается в верхней части емкости, из которой попадает в смеситель или в душ, а холодная вода поступает снизу.
Титан на дереве используется для производства горячей воды
К достоинствам такой конструкции можно отнести следующие параметры :
- Современный титан предусматривает возможность подключения к центральному водопроводу, а также возможность установки электронагревательного элемента для поддержания температуры воды.Титаны изготовлены из современных материалов, что позволяет снизить вес всей конструкции.
- Котел на дровах позволяет быстро нагреть воду. После начала процесса горения горячая вода может быть готова через 20-30 минут. А благодаря большому объему бака (90 — 100 литров) можно выучить много горячей воды.
- Модели водонагревателей достаточно удобны, особенно в частном секторе, где нет возможности подключения к центральному водопроводу.Также твердотопливные титаны удобны и экономичны в финансовом отношении как при покупке, так и при эксплуатации.
Но есть некоторые нюансы в работе титана — это постоянный контроль работы титана при сжигании топлива, очистка от продуктов сгорания, очистка трубы и т. Д.
Водонагреватель на дровах для бытовых нужд и бассейна
Не всегда человеку удается построить баню на дачном участке или дачном участке, где можно стирать и стирать одежду, и поэтому многие пытаются обзавестись устройством для нагрева воды твердым топливом.
Такое устройство популярно в отдаленных населенных пунктах по ряду причин :
- Для возможности работать автономно, для получения горячей воды необходимы только дрова или другое твердое топливо. В то же время такой водонагреватель очень экономичен, так как не потребляет электричество, газ и само устройство в финансовом отношении относительно дешево.
- Простая конструкция и простое управление, а также долговечность использования данного типа водонагревателя. Надежность в работе, лишь бы всегда были вода и топливо, а горячую воду можно было получить практически в любое время.
- Энергоэффективность — при небольшом количестве топлива можно нагреть большое количество воды, а если в течение дня, например, поддерживать огонь в топке постепенно, используя горячую воду и закачивая в бак холодную воду, то это можно удовлетворить потребность людей в горячей воде практически на целый день.
- Кроме водонагревателей, используемых в быту, некоторые дачи используют водонагревательное оборудование для бассейна.
Дровяной обогреватель может работать автономно
Визуально такой водонагреватель представляет собой свернутую в спираль трубу, к ней можно приварить ножки и сетку, под которой разводится костер.
В один патрубок трубы поступает холодная вода, а из второго уже теплая. Но такие конструкции можно использовать для небольших бассейнов.
Котел на дровах: прибор
Водонагреватели на дровах хоть и появились давно, но до сих пор не утратили своей актуальности. У основного котла на дровах есть такие характеристики, как вес, объем бака и, конечно же, основная часть котла — топка, ее объем и из какого материала она сделана. Современные корпуса выполнены из металла, а внутри установлены специальные экраны, предохраняющие котел от чрезмерного нагрева.Такой бойлер обычно имеет небольшие габариты, поэтому его легко установить на даче или в ванной.
Котел на дровах лучше всего выбирать с чугунной печью
Чтобы выбрать подходящий котел, следуйте советам :
- Котел на дровах лучше выбирать с отдельной топкой и баком, чтобы смеситель поливочный можно было установить в любом удобном положении. Бак лучше всего выбирать из нержавеющей стали, что позволит котлу прослужить намного дольше.
- Выбор лучшего котла с чугунной топкой, так как такие топки служат намного дольше, чем топка из металла.
По возможности лучше приобрести котел со встроенным ТЭНом, который позволит одновременно нагревать воду, а также поддерживать температуру воды после сгорания топлива.
Как сделать водонагреватель на дровах своими руками
Самодельный обогреватель на дровах можно сделать своими руками. Для этого понадобится бак, духовка, трубы для воды и для дымохода, крепеж и сварочный аппарат, дрель и другие детали.
Сам процесс сборки состоит из нескольких этапов :
- В качестве нагревательного элемента используется печка, поверх которой устанавливается бак, главное при сварке всей конструкции — герметичность уплотнения. Труба от топки должна проходить через центр емкости. Верхняя часть бака тоже приварена с герметичностью.
- Сделать водогрейный котел можно немного иначе — из целого большого воздушного шара. Для этого воздушный шарик разрезают на две части.В одной части прорезают дверцу духовки и под зольник, между топкой и воздуходувкой устанавливают решетку, делают петли и навешивают дверцы.
- Остальная часть цилиндра приварена металлическими листами снизу и сверху, чтобы оставалось место для дымохода. После этого две части цилиндра свариваются друг с другом для обеспечения герметичности, а затем свариваются водопроводные трубы.
Водонагреватель можно изготовить ручным инструментом
Такой водонагреватель можно сделать практически из любого подручного материала: из старой емкости, трубных бутылок.Просто нужно выбрать для себя определенную модель и на основе этого образца сделать водонагревательный агрегат для дома или для другого помещения. После того, как все будет готово, необходимо сначала налить воду в емкость и проверить ее на герметичность, а после можно попробовать начать нагрев воды, проверив всю конструкцию.
При обнаружении нарушений необходимо разобрать всю конструкцию и устранить все недостатки.
Обзор видов: водогрейный котел (видео)
Несмотря на большое количество всевозможного современного отопительного оборудования, водогрейные котлы, твердотопливные титаны не утратили своей актуальности и продолжают широко применяться не только в загородных домах, но и в некоторых многоквартирных домах старой постройки.Баня будет доступна каждому!
«машин, которые бегают по деревьям» Джона Гудмана (журнал Works That Work)
автор: Джона Гудман (3044 слова)
Машины, работающие на дровах, могут показаться фантастикой в стиле стимпанк или одержимостью на заднем дворе какого-то сумасшедшего мастерицы, но в какой-то момент они были обычным явлением во многих частях Европы, и технология, которая их использует, все еще находит практическое применение сегодня.
Фото на обложке: Иоганн Линелл на Volvo, который он и двое друзей установили газогенератором. За 20 дней 2007 года они проехали 5420 километров по Швеции на энергии, вырабатываемой семью кубометрами древесины. (Фотография любезно предоставлена Иоганном Линеллом.)
В глубине лесов континентальной Швеции Йохан Линелл останавливается, его двигатель не работает. Он и двое друзей выходят из машины и идут веером через деревья, возвращаясь с руками, полными еловых шишек и мертвого дерева. В задней части машины Линелл снимает с петель верх высокого стального ящика, который возвышается над отверстием в багажнике.Дым поднимается, и пламя следует за ним, когда он сбрасывает добытые дрова внутрь. Из нижней части заляпанной смолой стопки толстые сварные трубы карабкаются по кузову автомобиля и змейкой уходят в передний бампер, где они входят в двигатель, как трубки для кормления пациента. В считанные минуты машина оживает, плавно движется по массивной древесине.
На короткое время, 70 лет назад почти все гражданские автомобили в Европе работали таким образом. По мере того как Вторая мировая война затягивалась, а бензина становилось все меньше, древесина стала основным альтернативным топливом для транспортных средств.К 1945 году около миллиона европейских автомобилей работали на газификации древесины с использованием модификаций, аналогичных модификациям Volvo Линелла. Принцип работы удивительно прост: сжигая бочку из дерева или угля до тех пор, пока она не разовьется до внутренней температуры от 900 ° до 1200 ° C (от 1650 ° до 2200 ° F), а затем ограничивая подачу воздуха в огонь, газификаторы производят горючий углерод. монооксид, который можно охлаждать, фильтровать и направлять непосредственно в двигатель обычного автомобиля.
Автомобиль с приводом от дерева был изобретен в 1905 году английской автомобильной компанией Thornycroft, но прошло еще 20 лет до того, как французский химик Жорж Имбер сделал практическую возможность путешествовать на древесном газе.Благодаря переработанной камере сгорания, в которой использовалось всасывание от двигателя для втягивания газа вниз через горячую сердцевину горящих поленьев, его модель могла создавать намного больше окиси углерода, чем предыдущие итерации. Это также обеспечивало устойчивое горение, так как гравитация и вибрация транспортного средства вытряхивали пепел из кучи, оседая на месте новое топливо. К 1930-м годам четыре европейских правительства активно исследовали газификаторы Имберта с целью их использования в общественном транспорте: политически нейтральные Швеция и Финляндия стремились достичь топливной автономии в нестабильном регионе; Италия Муссолини, находящаяся под торговым эмбарго Лиги Наций после вторжения в Эфиопию, искала источник топлива, альтернативный нефти; а нацистская Германия готовилась к войне.
Даже автомобили, работающие на древесном газе, нуждаются в инфраструктуре снабжения: в 1945 году в Финляндии было 70 деревообрабатывающих заводов, а в Германии были тысячи складов древесины специально для автомобильного топлива. Из 17 мест, где Линелл и его друзья останавливались за дровами во время поездки, только в четырех были готовые к употреблению, предварительно порубленные дрова.
Падение Германии в пропасть сюрреалистично задокументировано в сохранившихся экземплярах спонсируемого государством автомобильного журнала Motor Schau . И пронацистское пропагандистское, и банальное автомобильное издание, в его выпусках 1939 года представлены автогонщики с символикой СС, мотоциклы, тестирующие вермахт, и украшенные свастикой митинги, посвященные автомобилю Kraft durch Freude или Volkswagen Beetle.В 1940 году, когда каждый ежемесячный выпуск объявляет о падении еще одной европейской столицы, начинают появляться статьи о транспортных средствах на древесном газе, рекламируя технологию как топливо национальной гордости, которое освободит Германию от зависимости от иностранных поставщиков. В период с 1941 по 1942 год, когда потребности военных привели к сокращению поставок нефти для гражданского населения Германии более чем на 50%, страницы Motor Schau заполнены растущей рекламой газификаторов, а также крепких алкогольных напитков.
«Древесный газ дешев, экономичен и избавляет вас от зависимости от бензина, сырой нефти и нефти.Так читает объявление Motor Schau , автомобильного журнала нацистской эпохи. Транспорт, работающий на древесном газе, особенно привлекает тоталитарных режимов, стремящихся к независимости от мировой торговли, и до сих пор используется в Северной Корее. (Из журнала Motor Schau , 1941 г.)
К 1943 году характерные высокие цилиндрические печи были обязательными на большинстве транспортных средств в странах, оккупированных нацистами, поскольку ресурсы жидкого топлива направлялись прямо в вооруженные силы, особенно в Люфтваффе.В 2013 году греческий механик Александрос Топалоглоу сказал исследователю Алексии Папазафейропулу, что, несмотря на ограничения военного времени, греки поддерживали активный рынок бензина на черном рынке, обманывая чиновников, зажигая газификаторы на своих автомобилях непосредственно перед приближением к немецким контрольно-пропускным пунктам. Когда Германия начала терять территорию в 1944 году, по крайней мере, пятьдесят танков Tiger были дооснащены древесно-газовыми установками, и наказания за езду на бензине без письменного разрешения регионального генерала — даже для военных — стали жесткими.
Адольф Гитлер осматривает автомобиль, работающий на древесном газе. Изначально опубликованное в выпуске журнала Motor Schau за 1941 год, изображение располагалось над цитатой из нацистского лидера: «Эти автомобили по-прежнему будут иметь особое значение после войны, потому что рост автомобилизации будет означать, что у нас никогда не будет достаточно масла, что оставляет нам зависит от импорта. Это родное топливо полезно для отечественного хозяйства ». (Из журнала Motor Schau , 1941)
Личные взгляды Гитлера на автомобили, работающие на древесном газе, можно прочесть в выпуске журнала Motor Schau за 1941 год вместе с веселыми фотографиями Дер Фюрера с демонстрации газификаторов Mercedes-Benz.«Это автомобили, которые будут иметь особое значение после войны», — сказал он. «Нефть поступает из-за границы, но это топливо нашей родины». Четыре катастрофических года спустя автомобили-газификаторы Берлина действительно приобрели мрачный символизм. Жестокой зимой 1946 года они бесполезно ржавели на улицах, когда берлинцы крушили мебель и вырывали деревья с корнем, отчаянно ища дрова в развалинах немецкой столицы.
Кажется, вам нравятся хорошие истории.
Подпишитесь на нашу нечастую рассылку, чтобы получать больше историй прямо на свой почтовый ящик.В начале 2000-х, когда Линелл решил сделать свой собственный автомобиль на дровах и газе, он видел только один раз. Транспортные средства на древесном топливе в Европе являются исключительной прерогативой любителей, и его единственным источником запчастей и информации было местное радио-шоу под названием Serk I Fin , или «Найди и найди». В эфире Линелл изложил свой план, и его сравнили с Инге Найман, пожилой слушательницей, которая пережила Вторую мировую войну и все еще имела элементы газогенератора, оставшиеся с того периода. Это был прорыв, поскольку, как это ни удивительно, в наличии было немного другого, хотя в 1945 году в Швеции было более 60 000 транспортных средств, работающих на дровах, включая лодки, автобусы, тракторы и четверть мотоциклов страны.
(Фото любезно предоставлено Иоганном Линеллом)
Сегодня любители делятся советами в Интернете, а современные технологии позволяют «лесорубам» во всем мире извлекать выгоду из опыта таких авторитетов, как финский Веса Микконен и голландский псевдоним «Голландец Джон». Однако создаваемые ими газификаторы по-прежнему имеют много общего со своими предшественниками времен Второй мировой войны и отличаются особой привередливостью, требующей глубокого знания их конструкции, причуд и темпераментов.По словам Датча Джона, «единственный человек, который может водить машину, работающую на древесном газе, — это человек, который ее сделал».
Даже серийно выпускаемые версии 1940-х годов, такие как немецкий 3TO Opel Blitz Lastwagen 1943 года, поставлялись с толстыми иллюстрированными руководствами по эксплуатации, в которых подробно описывается, как каждую неделю Lastwagen необходимо очищать и тщательно промывать, а также каждый месяц его неплотный пробковый газовый фильтр. необходимо удалить, почистить и переустановить. Запуск двигателя, хотя и занимает 20 минут, в основном включает в себя поднесение спички к дровам, но контроль потоков газа и воздуха вокруг двигателя, что имеет решающее значение для таких задач, как движение в гору, пересечение долины или остановка более чем на три часа. , требует освоения сочетания четырех рычагов и ручки.Газификация производит значительные количества азота, инертного газа, который разбавляет топливную смесь, в результате чего автомобили, работающие на древесном газе, имеют малую мощность, и выжимать из них лучшее — путем разумной регулировки клапанов и вентиляционных отверстий — такое же искусство как наука.
«Когда вы едете медленно, вы видите больше», — говорит Линелл. «Это похоже на то, как будто страна преображается в зависимости от вашей машины. Я почувствовал то же самое годом ранее, когда проехал 500 км (311 миль) на мопеде, который я переоборудовал для работы на этаноле.Вы видите совершенно новый мир ».
Однако нет причин, по которым технология газификации должна оставаться в прошлом веке. Именно поэтому финский энтузиаст работы с древесным газом Юха Сипиля построил самый передовой в мире автомобиль, работающий на древесном газе, El Kamina, модифицированный грузовик с полностью автоматизированным двигателем. система газификации, управляемая компьютером, встроенным в ее приборную панель. Хотя это всего лишь прототип, это автомобиль на древесном газе, которым может управлять кто угодно. Сипиля — больше, чем просто любитель; он твердо верит в возобновляемые источники энергии и в то, что люди могут жить «вне сети».Он также является основателем Volter Oy, энергетической компании, занимающейся исследованиями газификации древесины, а также создателем десятиэтажного экологического поселка Кемпеле, а с мая 2015 года — премьер-министром Финляндии.
В 2010 году финское общество провело бурную общественную дискуссию о возможном возвращении к заменителям топлива военного времени, особенно к газификации древесины. В 1945 году 80% автомобилей в Финляндии — 46 000 — работали на газогенераторах, и только в 1944 году было потреблено более 2 000 000 м 3 (70 630 000 футов 3) древесины.Полный переход к системе транспортировки древесины произошел всего за два года. Теперь такие инновации, как El Kamina, показывают, что многие недостатки процесса можно преодолеть с помощью новых технологий. Что самое убедительное, Финляндия — одна из немногих стран в мире, где деревья могут быть действительно устойчивым источником топлива, с 23 миллионами гектаров (88 800 квадратных метров) бореальных круглых лесов и населением всего 5,5 миллиона человек.
Йохан Линелл чистит охладитель своего Вольво, работающего на древесном газе, который он сделал из старого стального дизельного бака.Охлаждение газа делает его более плотным и конденсирует воду из топливной смеси, так что на двигатель передается больше мощности. После использования Йохан обнаружил, что внутренняя часть холодильника будет покрыта загадочным кремообразным веществом. «Это напомнило мне вазелин». (Фото любезно предоставлено Иоганном Линеллом)
Ярно Хаапакоски, генеральный директор Volter Oy с 2011 года, объясняет, что семье из шести человек, живущей в образцовой деревне Кемпеле, которая питается и обогревается от большой установки газификации древесины, требуется всего 20 м³ (706 футов³) древесины в год. .По данным Metla, Финского научно-исследовательского института леса, в финских лесах ежегодно производится 104,5 миллиона кубометров новой древесины, чего почти достаточно для удовлетворения энергетических потребностей всех жителей Финляндии. Более того, горящие деревья представляют собой «замкнутый углеродный цикл»: углекислый газ, выделяемый деревьями при сжигании, примерно равен углекислому газу, который они вытягивают из воздуха в процессе роста.
Есть и обратная сторона. Древесный газ — это в первую очередь окись углерода, а окись углерода не имеет запаха, легче воздуха и исключительно ядовита.При атмосферной концентрации всего 0,5% он может убить, а всего 0,03% достаточно, чтобы вызвать потерю сознания. В одном из инцидентов в Хельсинки во время войны были замечены пассажиры, садившиеся в ожидающее такси холодным днем. Через десять минут такси не двинулось с места, прохожие открыли двери и обнаружили пассажиров без сознания, отравленных утечкой газа в закрытый отсек автомобиля. Треть из примерно 25 000 жертв отравления угарным газом в военное время в Финляндии пострадали во время вождения своих автомобилей, что часто приводило к катастрофическим последствиям, а подходы к обнаружению угарного газа во время войны зачастую были грубыми.Дания, например, установила мышей или канареек в клетках возле газогенераторов для проверки на наличие смертельных газов. Но сегодня Хаапакоски не беспокоится. По его словам, детекторы намного сложнее, а горелки могут быть построены с устройствами защиты от сбоев и аварийной сигнализации.
И это не первое возрождение древесного газа. Между возрождением этой технологии в Финляндии 21 века и ее расцветом в Европе военного времени интерес к технологиям резко возрос в 1970-е годы после глобального нефтяного кризиса. Некоторые интересы были оборонными, например, Швеция, разработавшая три типа аварийных газогенераторов, готовых к серийному производству во время кризиса.Но большая часть интереса возникла в развивающихся странах с наиболее острой потребностью: в сельских районах Азии, Африки и Латинской Америки.
Потенциал оказался огромным. Любые углеродные отходы могут быть газифицированы, будь то рисовая шелуха, пшеничная мякина, скорлупа грецких орехов, семена фруктов, опилки, солома, торф или кукурузные початки. Фильтры могут быть сделаны из масла, угля, пробки, воды, ткани, фарфоровой крошки или сизаля. А при наличии необходимого опыта можно построить эффективные газификаторы для автомобилей или электрогенераторов из бочек с нефтью и ржавых труб.Крупные газифицирующие электростанции были эффективны в определенных местах, таких как лесопилки в Сапире, Парагвае и Восточном мысе Южной Африки, сушилка для кокосовых орехов в Шри-Ланке, работающая на газифицированной скорлупе кокосовых орехов, или несколько сотен небольших электростанций для газификации рисовой шелухи заводы в Китае. Аварийные установки, такие как Power Pallet, генератор газификатора, разработанный в Калифорнии, недавно показали себя многообещающими в качестве средства оказания помощи при стихийных бедствиях в Либерии. Но в наши дни производство метана из сточных вод оказалось гораздо более успешным в качестве автономного альтернативного источника энергии.В бедных странах горючие твердые вещества, такие как скорлупа орехов и солома, по-прежнему могут быть товаром, даже если они дешевы, в то время как метан создается из отходов.
Йохан Линелл и его друзья Микаэль Андерберг и Мартин Йоханссон начали строительство своего Volvo, работающего на древесном газе, в начале 2007 года. К июлю он был готов, и они отправились в путешествие на дровах протяженностью 5420 км. Швеция. Поездка заняла 20 дней, несмотря на то, что максимальная скорость автомобиля составляла 90 км / ч (56 миль / ч), потому что остановки каждые 50 км (31 миль) для дозаправки их оригинального бака газификатора 1942 года замедляли прогресс.
Отчасти их маршрут был продиктован необходимостью найти лес. Собирать еловые шишки и поваленные ветром деревья можно только в экстренных случаях. Для эффективной газификации древесина должна состоять менее чем на 20% из воды, а это значит, что древесину необходимо тщательно высушить, прежде чем ее можно будет использовать. Влажная древесина не только снижает мощность двигателя за счет добавления пара в смесь и использования тепла для испарения; он также может вызвать «зависание древесины» из-за того, что горение будет настолько медленным, что древесина не сможет попасть в горелку. «Это похоже на мосты и не упадет туда, где огонь», — объясняет Линелл.«Центр становится холодным, процесс образования газа останавливается». Он также может распространять сильное тепло в неправильные части системы. «Если вам не повезло, — говорит Линелл, — это их плавит». А если вы вынуждены собирать корм, вы не можете просто использовать что-либо. «Если вы найдете сухое дерево, которое немного подсохло, вы можете использовать его, но это не может быть сосна, — говорит он, — это должна быть ель. Большая мертвая рождественская елка. Не то, что у тебя дома. Большой ». Газификаторы также не могут сжигать топливо всех форм и размеров.Куски дерева одинакового размера обеспечивают постоянную скорость горения, необходимую для предотвращения «падения давления», внезапной потери мощности. Во время своего путешествия по Швеции Линелл и его друзья буксировали трейлер с импровизированной машиной для рубки древесины, состоящей из бензопилы, поршня и двигателя старого автомобиля.
(Фото любезно предоставлено Иоганном Линеллом)
Поездка покинула Линелла с вопросами: «Я подумал:« Могу ли я что-нибудь сделать с этими знаниями? » Могу ли я получить прибыль? Начать бизнес? » Я понял, что газификация автомобилей не годится.Он функционирует, но требует больших затрат. В современном стиле жизни слишком много работы, слишком много времени и слишком грязно. Даже если бы у вас была инфраструктура, я не думаю, что люди ее использовали бы ». Однако сельскохозяйственные приложения выглядели многообещающими, главным образом потому, что« вы более стационарны — у вас может быть своя собственная куча дров ». Линелл применил свои навыки, чтобы 68-летний трактор и переделали его для работы по деревьям, поваленным ветром. Он решил провести весь 2008 год, проживая самодостаточную, углеродно-нейтральную жизнь на своей семейной ферме в Даларне, Швеция, выращивая картофель, морковь, свеклу, репу и салат на своей новой машине.В конце концов, бизнес-плана не было, и он не получил прибыли. «Я просто взял старый трактор и немного дров в лесу и принялся за работу».
кофейных зерен, обжарка древесины и нагрев между
Часть IV: Жаровни на дровахВ нашей серии блогов из четырех статей Beans, Burners, and the Heat in Between описываются различные методы обжарки, в которых используются разные источники энергии.Предыдущие статьи в этой серии включают Часть 1: Газовые горелки , Часть II: Газовые горелки предварительного смешивания и Часть III: Электрический нагрев . И последнее, но не менее важное: теперь мы хотели бы закончить наш обзор старейшей техникой обжарки, которая использовалась веками — древней, но все еще интригующей, эта техника обжарки продолжает очаровывать мастеров обжарки и жарочные заведения по всему миру — Часть IV: Дровяная печь Ростеры .
Нагревание, приготовление пищи или запекание с помощью жаровни на дровах существует с незапамятных времен.Причина использования жаровни на дровах в настоящее время не обязательно кроется в доступности, хотя в некоторых случаях это может быть проблемой. Это, скорее, возможность расширить спектр вкусов. Обжарочные машины на дровах от Coffee-Tech — это многотопливные аппараты. Их можно использовать практически с любым типом топлива с аналогичной теплотворной способностью, если оно подходит для съедобного продукта. Варианты топлива варьируются от древесных пеллет, и деревянных бочек для вина, от до отходов переработки кофе.
Ключевое различие между машинами с дровяной печью Coffee-Tech и традиционными обжарщиками кофе, которые существуют уже более века, заключается в расположении камеры сгорания горелки , а также в ее функциях управления. В традиционных жаровнях камера сгорания расположена под барабанным отсеком. В современных машинах камера сгорания полностью внешняя. Он отводит тепло через изолированную втулку, которая исходит из камеры сгорания, передавая тепло барабану.Это позволяет полностью и равномерно распределять тепло , что обеспечивает быстрое и безопасное прожаривание. Разница между двумя конструкциями — традиционным и современным — выражается в режиме регулирования температуры. В традиционных машинах у оператора есть только один шанс сделать все правильно. От начала до конца все должно быть точно синхронизировано в зависимости от количества угля или древесины и наличия первичного и вторичного воздуха. Тепло не может быть отключено задним числом.
Усовершенствованная жаровня на дровах от Coffee-Tech имеет пневматический привод, который направляет тепло в духовку или поочередно отводит его через заслонку для отходов, чтобы полностью отключить тепло.Кроме того, оператор определяет скорость модуляции и повышения температуры (а также другие параметры) с помощью цифрового преобразователя частоты , который управляет всасыванием воздуха воздуходувкой барабана через барабан. При увеличении всасывания воздуха тепло увеличивается, так как воздух, попадающий в камеру для обжарки, вынужден проходить через горящие дрова. Комбинация нагнетаемого кислорода и горящего материала является неограниченным источником тепла. Настолько, что металл может светиться и излучать, если вы не будете достаточно осторожны.Используя только эти два, можно получить полный контроль над всем температурным диапазоном профиля , так же как и в каждой точке предварительного нагрева.
С практической точки зрения, можно стабильно поддерживать состояние предварительного нагрева на 180 градусов в течение неограниченного периода времени, независимо от того, закончился ли горящий материал и вам нужно добавить еще при открытии дверцы камеры сгорания. На самом деле это сложно сделать с помощью газа. Подъем и опускание в определенном диапазоне неизбежны.Но не с разработанной нами жаровней на дровах. Это всегда было проблемой номер один для тех, кто мечтает обжарить кофе на дровах.
Обжарка древесины стала возможной благодаря излучению и конвекции . Однако тепла, производимого при сжигании древесины, отличается по своему составу от тепла, производимого с использованием металла, керамики, газового пламени или электричества. При использовании дерева в качестве источника тепла воздух, который передает тепло, содержит много влаги, и множество других полезных ингредиентов, от смолы, ароматизаторов и сахаров до масел. Результат запекания дровами впечатляет. Поскольку тепло передается через воздух, обжарка происходит особенно равномерно и быстро. Он не страдает от проблем, известных в других методах, таких как пригорание и опрокидывание. Кофейные зерна сохраняют янтарно-коричневый оттенок с шелковистым блеском и насыщенной окраской, что свидетельствует об изобилии масел , сахаров и других важных ингредиентов кофе. Их присутствие может сделать кофе более темным с точки зрения степени обжарки, чем он есть на самом деле.Однако темный насыщенный цвет не является результатом древесного элемента зерен — явление, знакомое по небрежной обжарке. Это результат изобилия сортов кофе. Фактически, то же самое можно сказать обо всех обжарочных машинах Coffee-Tech, независимо от используемого метода нагрева.
При выборе древесины следует учитывать:- уровни влажности
- Плотность и скорость горения
- калорийность
- ароматическая ценность, высокое / низкое присутствие смолы
- токсичность
После того, как сорт древесины будет рассмотрен должным образом, мы можем перейти к практическому опыту.Мы можем начать с объединения древесины таких деревьев как дуб , бук или оливковый в качестве основы вместе с фруктовыми деревьями, такими как яблоня , виноградная лоза , орех , груша или цитрусовые. , для дополнительных специй. Не рекомендуется использовать древесину из сосны или кедра из-за высокого содержания исключительно ароматической смолы. Использование древесины, обработанной от насекомых или продезинфицированной — железнодорожных шпал, промышленных отходов, МДФ и т. Д. — строго запрещено.Их сжигание опасно для операторов, потребителей и окружающей среды в целом.
Еще одно важное отличие: в традиционных обжарочных машинах необходимо было поджигать уголь или дрова во внешнем контейнере, чтобы сажа не покрывала барабан изнутри. Это обычно происходит, когда дерево загорается. В современных жаровнях на дровах камера сгорания внешняя. Он имеет отдельное соединение для избыточного тепла, которое передает тепло духовке. В случае необходимости тепло можно перенаправить в дымоход через дополнительный сбросной вентиль, выключив выключатель горелки.Дым и побочные продукты, такие как сажа, затем выпускаются , не проходя через барабан. Это можно сделать, даже если обжарщик кофе выключен. Таким образом, в барабан не происходит всасывания воздуха, даже минимального.
Жаровня на дровах предлагает новое измерение обжарки даже при использовании одного древесного происхождения. Это больше не будет прежним ароматом. Новые ароматы будут добавлены из дерева. Он отлично подходит для приготовления эспрессо — особенно, если он богат робустой.Половину, образовавшуюся при обжарке, лучше всего использовать в качестве трута при жарке с древесиной. Во многих отношениях обжарка с использованием дров — это «зеленых». По крайней мере, дрова сжигали люди всегда. Возможно, наш мир лучше подходит для сжигания дерева, чем для других горючих материалов. По крайней мере, в это можно верить.
Рам А. Евги
к началу
Изолированная глиняная печь для пиццы и хлеба: 17 ступеней (с изображениями)
Некоторые идеи дизайна
Печь для выпечки хлеба обычно имеет толстый внутренний слой, сделанный из твердого, сохраняющего тепло материала (т.е.е. высокая тепловая масса), которая будет удерживать тепло в течение 3 часов или около того. Идея состоит в том, чтобы развести в нем огонь, дать ему нагреться, а затем соскрести угли и положить тесто, закрыть дверцу и дать хлебу испечься. С другой стороны, в печи для пиццы горит огонь — или, по крайней мере, в ней есть тлеющие угли, — пока пицца печется. Ему не нужен тепловой конденсатор, как в печи для выпечки хлеба, но он должен работать намного горячее. Оба типа подходов требуют хорошего термостойкого изолятора.Эта конструкция удовлетворяет потребности как пекаря пиццы, так и пекаря хлеба за счет наличия внутреннего слоя материала с высокой тепловой массой и окружающего его термостойкого изоляционного слоя. Чем лучше изоляция, тем меньше тепла может уйти, поэтому вы получите оптимальную энергию от своего топлива.
Конструкция
Внешняя часть духовки состоит из трех слоев, каждый из которых выполняет определенную функцию:
1. Внутренний слой: глина, смешанная с песком. Это огнеупорный материал, т.е.е. он выдерживает высокую температуру. Он также хрупкий, и его необходимо защищать внешними слоями. Этот слой обладает высокой теплоемкостью и поэтому помогает равномерно распределять тепло и отводить тепло обратно в центр духовки. Его толщина составляет около 3 см.
2. Средний, изоляционный слой. Этот слой должен быть теплостойким, а также действовать как изолятор. В качестве материала был выбран вермикулит (он же «перлит»), связанный с глиной. Его толщина составляет около 10 см. Этот слой также обеспечивает первую часть структурной прочности конструкции.
3. Внешний корпус. Поскольку помогает каждый кусочек утеплителя, этот слой также сделан из вермикулита, однако он скреплен цементом, что делает ракушечник твердым. Поскольку этот слой не слишком нагревается, можно использовать цемент, который при высоких температурах отслаивается и теряет прочность.
4. Атмосферостойкий слой: слой наружного цемента будет удерживать самую сильную влагу во время дождя, но позволяет глине высыхать по мере старения. Можно также выложить плитку снаружи для декоративного эффекта.
Внутренняя высота входа должна составлять 63,9% внутренней высоты купола в его самой высокой точке. Кто и как это рассчитал, остается для меня загадкой.
Дымоход, обеспечивающий хорошую тягу, необходим для отвода горячего воздуха и дыма из печи, поэтому, как показывает практическое правило, высота дымохода должна быть не меньше высоты внутреннего купола.
Примечание для академиков, инженеров и других замечательных математически вдохновленных людей:
Я не делал формальных вычислений, хотя однажды я читал курсы термодинамики и структурной инженерии в университете.К сожалению, пиво тогда было интереснее. Спустя год и регулярного использования конструкция конструкции неплохо сохранилась.
Также маловероятно, что эта печь когда-либо будет достаточно горячей для обжига низкотемпературной глиняной посуды — я пробовал.
Глава 2. Обугливание древесины и продукты, которые она дает
Глава 2. Обугливание древесины и продукты, которые она дает2.1 Карбонизация
2.2 Эффективность карбонизации
2.3 Измерение урожайности
2.4 Что происходит во время карбонизации
2,5 Стадии в образование древесного угля
2.6 Использование тепла эффективно карбонизация
2,7 Непрерывная карбонизация
2,8 Классификация систем ретортного нагрева
2.9 Свойства продуктов карбонизации
Карбонизация — это особая форма этого процесса в химической технологии, называемого пиролизом, который представляет собой расщепление сложных веществ на более простые при нагревании.Карбонизация — это термин, используемый, когда сложные углеродсодержащие вещества, такие как древесина или сельскохозяйственные остатки, разлагаются при нагревании на элементарный углерод и химические соединения, которые также могут содержать некоторое количество углерода в своей химической структуре. Термин карбонизация также применяется к пиролизу угля с получением кокса.
Этап карбонизации в процессе производства древесного угля является наиболее важным из всех этапов, поскольку он имеет такую силу, чтобы влиять на весь процесс от выращивания дерева до конечного распределения продукта пользователю.
Тем не менее, карбонизация сама по себе относительно не дорогостоящий этап. Несмотря на то, что реторты могут иметь высокие капитальные затраты, они не требуют много труда на единицу продукции. Обычно стадия карбонизации может составлять около 10% от общих затрат от выращивания и сбора дерева до доставки готового древесного угля на склад. Но эффективность преобразования на стадии карбонизации возвращается к точке, где древесина собирается. Высокий выход при переработке означает, что меньше древесины нужно выращивать, заготавливать, сушить, транспортировать и загружать в реторту или другую установку карбонизации.
Конкретный способ обугливания древесины также может повлиять на общий выход, поскольку он влияет на количество образующейся мелочи. Штрафы могут вообще не иметь сбыта или продаваться только после довольно дорогостоящего процесса брикетирования.
Три основных фактора, которые влияют на выход конверсии:
(a) Содержание влаги в древесине во время карбонизации.
(b) Тип используемого оборудования для карбонизации.
(c) Тщательность, с которой выполняется процесс.
Эффективность карбонизации выражается как выход древесного угля в валовом выражении (на стороне реторты или печи), выраженный в процентах от древесины, загруженной или использованной для ее производства. Обычно учитывается только фактически использованная древесина. Таким образом, несгоревшая древесина, которая может быть переработана, вычитается из использованной древесины, даже если она представляет собой скрытую форму неэффективности. С другой стороны, если используется косвенный нагрев, как в ретортах или в печи типа Swartz, в которой используется внешняя колосниковая решетка, количество древесины, использованной при нагреве, должно быть включено в древесину, используемую для производства древесного угля.Можно принять во внимание, что в некоторых случаях эта древесина может быть более низкого качества.
Древесина и древесный уголь должны измеряться стандартными методами. Они не обязательно должны быть одинаковыми для обоих материалов, но они должны быть согласованными, чтобы результаты были сопоставимы. Другими словами, необходимо придерживаться последовательной методологии измерения. Правильно измеренная эффективность преобразования позволяет сравнивать различные методы производства древесного угля. Также эти измерения необходимы для управления крупными предприятиями по производству древесного угля.
Самая точная измерительная система сравнивает все величины на основе веса. Во избежание осложнений из-за различного содержания влаги, используемая древесина выжимается из расчета на сухую кость, а древесный уголь взвешивается как кость и не содержит мелких частиц. если влажность присутствует, ее необходимо определить и учесть. Для применения такой системы необходимо наличие оборудования для взвешивания и определения влажности древесины и древесного угля. К сожалению, в большинстве случаев производства древесного угля это случается редко.Это метод, наиболее подходящий для исследований по переработке и для крупных промышленных предприятий. Не имея встроенных ошибок, это последняя система отсчета.
Практический метод, широко стандартизованный в Южной Америке, особенно в сталелитейной промышленности Бразилии, использует измерение объема. Как использованная древесина, так и произведенный древесный уголь измеряются в кубических метрах с поправкой на ошибки штабелирования и уплотнения. Древесина измеряется в магазинах (штабелированные кубические метры), и каждая стереосистема принимается равной 0.65 твердых кубометров. Система учитывает эффект усадки топливной древесины при сушке и уменьшение объема, которое происходит при транспортировке и обработке древесного угля из-за оседания. Это оседание является результатом истирания острых углов кускового древесного угля и образования мелкодисперсного древесного угля, который практически не имеет коммерческой ценности.
Допуск на усадку топливной древесины основан на экспериментах по изучению эффекта сушки, разборки и переупаковки, как это происходит, когда кучу сухой древесины транспортируют из леса на угольную фабрику.Результаты показывают, что стопка из 100 складов древесины эвкалипта сжимается до 84 складов после 3-4 месяцев сушки, а когда та же самая стопка складывается заново, ее новый объем составляет всего 79 стэров. Таким образом, допускается уменьшение на 15% для сушки и на 21% для сушки и переупаковки. На истинное содержимое груды дров также сильно влияет метод штабелирования. Опыт — единственный способ решить эту проблему, чтобы определить, был ли объем древесины завышен из-за нечестной укладки.
Объем древесного угля измеряют, помещая его в проволочную корзину с основанием один квадратный метр и высотой несколько более метра.Коммерческий кубический метр древесного угля считается имеющим истинный объем в один кубический метр только при измерении на стороне доменной печи, то есть на складском складе. Сбоку от печи для обжига древесного угля считается, что кубический метр товарного древесного угля имеет истинный объем 1,1 кубического метра. Таким образом допускается усадка древесного угля при транспортировке и производство бесполезной мелочи. Стандартный выход бразильских печей для обжига древесного угля, использующих эту систему, составляет 1 кубический метр коммерческого древесного угля из каждых 2.2 дома дров. Измерение объема для определения выхода древесного угля подвержено определенным внутренним ошибкам, но это простой метод, легко понимаемый и может выполняться «на открытом воздухе». Он имеет большое преимущество при покупке и продаже древесного угля, поскольку он автоматически препятствует фальсификации смачивание древесного угля и смешивание его с песком и землей. Причина в том, что эти действия не влияют на объем. Кроме того, существует стимул для осторожной транспортировки древесного угля, чтобы минимизировать снижение товарного объема за счет оседания и производства мелких частиц. .Температура, до которой нагревается уголь в печи, влияет на показатель выхода, изменяя содержание в нем летучих смолистых веществ. Мягко обожженный древесный уголь, полученный, когда температура не поднимается выше примерно 400 ° C, может иметь содержание летучих веществ примерно 30%, что эквивалентно выходу примерно 42% в пересчете на сухой вес костей. При 500 ° C летучие вещества составляют всего около 13%, а выход составляет около 33% в пересчете на сухую кость. Следовательно, чтобы сравнивать равные с равными, разные виды древесного угля должны иметь примерно одинаковое содержание летучих веществ.
Во время пиролиза или карбонизации древесину нагревают в каком-либо закрытом сосуде, вдали от кислорода воздуха, который в противном случае позволил бы ей воспламениться и сгореть дотла. Без кислорода мы заставляем древесное вещество разлагаться на множество веществ, главным из которых является древесный уголь, черное пористое твердое вещество, состоящее в основном из элементарного углерода. Другими составляющими являются зола от исходной древесины в количестве от 0,5 до 6% в зависимости от породы древесины, количества коры, загрязнения землей и песком и т. Д.и смолистые вещества, которые распределяются через пористую структуру древесного угля. А также древесный уголь. Производятся жидкие и газообразные продукты, которые могут быть собраны из паров, отводимых, если древесный уголь производится в реторте. Жидкости конденсируются, когда пары горячей реторты проходят через конденсатор с водяным охлаждением. Неконденсирующиеся газы проходят и обычно сжигаются для рекуперации содержащейся в них тепловой энергии. Этот древесный газ, как его еще называют, имеет низкую теплотворную способность (около 10% от природного газа).
Другие продукты, кроме древесного угля, обычно называют побочными продуктами. Много лет назад восстановление содержащихся в них химикатов было процветающей отраслью во многих развитых странах. С появлением нефтехимической промышленности эта отрасль побочных продуктов стала нерентабельной, поскольку в большинстве случаев химические вещества можно производить из нефти с меньшими затратами. Более подробная информация по этой проблеме будет дана позже.
По мере того, как древесина нагревается в реторте, она проходит определенные стадии на пути к превращению в древесный уголь.Было изучено образование древесного угля в лабораторных условиях, и были выделены следующие этапы процесса конверсии.
— от 20 до 110 ° С
Древесина поглощает тепло при сушке, выделяя влагу в виде водяного пара (пара). Температура остается на уровне 100 ° C или чуть выше, пока древесина не станет сухой.
— от 110 до 270 ° С
Конечные следы воды выделяются, и древесина начинает разлагаться с выделением некоторого количества окиси углерода, двуокиси углерода, уксусной кислоты и метанола.Поглощается тепло.
— от 270 до 290 ° С
Это точка, в которой начинается экзотермическое разложение древесины. Выделяется тепло, и разрушение продолжается самопроизвольно, если древесина не охлаждается ниже этой температуры разложения. Смешанные газы и пары продолжают выделяться вместе с некоторым количеством смолы.
— от 290 до 400 ° С
По мере продолжения разрушения структуры древесины выделяемые пары включают горючие газы монооксид углерода, водород и метан вместе с газообразным диоксидом углерода и конденсируемыми парами: водой, уксусной кислотой, метанолом, ацетон и т. Д.и смолы, которые начинают преобладать при повышении температуры.
— от 400 до 500 ° С
При 400 ° C превращение древесины в древесный уголь практически завершается. Древесный уголь при этой температуре все еще содержит заметные количества смолы, возможно, 30% по весу, захваченной в структуре. Этот мягко обожженный древесный уголь нуждается в дальнейшем нагревании, чтобы удалить больше смолы и, таким образом, повысить фиксированное содержание углерода в древесном угле примерно до 75%, что является нормальным для коммерческого древесного угля хорошего качества.
Чтобы удалить эту смолу, древесный уголь подвергается дополнительным тепловым воздействиям, чтобы поднять его температуру примерно до 500 ° C, таким образом завершая стадию карбонизации.
При карбонизации происходит значительный тепловой поток внутрь и наружу древесины, подвергающейся обугливанию. Правильный контроль над ними влияет на эффективность и качество производства древесного угля. Тепловые потоки можно рассчитать и отобразить на диаграмме теплового баланса процесса. Для этого нужны знания теплотехники, но основные принципы понять нетрудно.Подвод тепла должен происходить от сжигания какого-либо топлива, что обычно означает дерево в случае производства древесного угля. Даже если мы используем экзотермическое тепло от карбонизации или тепло, выделяемое при сжигании отходящего газа из реторты, любое дополнительное тепло будет исходить от сжигания некоторого количества древесины и, следовательно, представляет собой потерю. Сгоревшее дерево нельзя превратить в древесный уголь.
Три основных этапа, требующих ввода тепла при производстве древесного угля:
— Сушка древесины.— Повышение температуры сухой древесины в печи до 270 ° C для начала самопроизвольного пиролиза, который сам выделяет тепло.
— Окончательный нагрев примерно до 500-550 ° C для удаления смолы и увеличения содержания связанного углерода до приемлемого значения для хорошего коммерческого древесного угля.
Идеальным процессом карбонизации был бы такой процесс, который не требовал бы внешнего тепла для проведения карбонизации. Экзотермическое тепло процесса будет улавливаться вместе с теплом, выделяемым при сжигании отходящих газов и жидких побочных продуктов, и этого в целом будет достаточно для высушивания остаточной влаги в древесине, повышения ее до температуры самопроизвольного пиролиза, а затем нагрева. до температуры, достаточной для удаления остаточных смол.На практике из-за потерь тепла через стенки карбонизатора и плохой сушки сырья достичь этой цели практически невозможно. Однако некоторые системы, особенно большие реторты для горячего промывочного газа, близки к идеалу, когда климат местности позволяет надлежащим образом сушить древесное сырье.
Ни одна древесина не будет обугливаться, пока она практически не высохнет. Однако вода в сырой древесине обычно составляет около 50% сырого веса древесины, и все это должно быть испарено, прежде чем древесина начнет пиролиз с образованием древесного угля.
Наиболее экономично высушить как можно больше этой влаги с помощью солнечного тепла до того, как древесина будет обуглена. В засушливых регионах саванны это довольно просто, так как древесину можно оставить на 12 месяцев или более для высыхания без серьезных потерь из-за нападения насекомых или гниения. Во влажных тропиках два или три месяца могут быть практическим пределом, прежде чем потери от насекомых и гниения станут недопустимыми. Потеря выхода древесного угля из-за чрезмерного содержания влаги должна быть сбалансирована с потерей древесного вещества из-за биологического разрушения.
Важные факторы, связанные с сушкой и хранением древесного сырья, описаны в главе 4.
Одним из наиболее важных шагов в производстве древесного угля стало применение концепции непрерывного карбонизирования. Посредством последовательного прохождения древесного сырья через ряд зон, где выполняются различные стадии карбонизации, можно добиться экономии в использовании рабочей силы и тепла, тем самым снижая производственные затраты и увеличивая выход из заданного количества древесины. .
Концепция непрерывного карбонизатора, в котором древесина движется вертикально вниз при нагревании и карбонизации, довольно очевидно вытекает из идеи доменной печи для выплавки чугуна. Но для того, чтобы получить древесный уголь в кусковой форме, оказалось необходимым отказаться от идеи получения тепла для сушки загрузки и нагрева ее до точки карбонизации путем сжигания части загруженной древесины. Это оказалось слишком сложно контролировать. Процесс нагрева пришлось изменить на использование горячего бескислородного газа, вырабатываемого извне и продуваемого нисходящим потоком древесины.Таким образом, операция находилась под полным контролем, и оказалось возможным производить правильно обожженный древесный уголь и при этом обеспечивать его выход в кусковой форме. Кроме того, древесный уголь никогда не был загрязнен золой, поскольку карбонизатор всегда работает при температуре ниже точки горения накала.
Рекуперация тепла, выходящего из верхней части карбонизатора, была достигнута путем сжигания газа и паров в контролируемых условиях в печах с горячим дутьем, аналогичных тем, которые используются при выплавке чугуна, с последующей продувкой этого горячего газа в реторту в соответствующих точках, так что карбонизация завершился первым ударом горячего газа о древесный уголь, выходящий из зоны самопроизвольного пиролиза.Затем газ прошел вверх по башне, отдавая свое тепло в противоточной форме нисходящему заряду древесины. Готовый древесный уголь в нижней части реторты охлаждали до того, как он достигнет основания, путем вдувания холодного бескислородного топливного газа и извлечения его непосредственно ниже точки входа горячего газа, выходящего из печи с горячим дутьем. Топливный газ, нагретый за счет охлаждения древесного угля, затем поступал в дутьевые печи для сжигания воздухом для получения горячего промывочного газа, который подавался обратно в установку для удаления остаточной смолы с древесного угля, а затем поднимался в градирню, отдавая свой воздух. тепло к нисходящей загрузке древесины.Положение различных зон в башне можно было контролировать, регулируя скорость нагнетания газа и его температуру, а также скорость, с которой древесина поступала наверх, а древесный уголь удалялся у основания.
Этот тип реторты, известный под общим названием «непрерывная вертикальная реторта для горячей промывки газа», обычно называют ретортой Ламбьотта в честь ее изобретателя (Lambiotte, 1942, 1952). Это, вероятно, самый сложный процесс производства древесного угля из-за качества и выхода древесного угля, который он производит, но есть и другие системы непрерывного производства древесного угля, которые успешно используются в коммерческих целях.Наиболее известная из них использует печь непрерывного действия с несколькими подами для обжига, также известную как обжарочная печь Herreshoff в честь ее изобретателя. Подобно тому, как реторта для промывочного газа заимствует большую часть своей технологии у доменной печи, многоподовая печь представляет собой простую передачу технологии из химической и металлургической промышленности, где она представляет собой знакомую установку, используемую для обжига сульфидной руды перед дальнейшей переработкой.
Ростер Herreshoff находится в невыгодном положении по сравнению с ретортой для промывочного газа в том, что он может обрабатывать только мелко измельченную древесину или кору и т. Д. И, следовательно, может производить только порошкообразный древесный уголь, который должен быть брикетами для продажи.Такие брикеты непригодны для использования в обычной металлургии. Единственный экономический рынок — барбекю, который требует довольно сложного потребительского рынка.
Ростер Herreshoff производит древесный уголь и смесь горячих газов и паров. Эта газовая смесь является загрязнителем окружающей среды. Поскольку в настоящее время извлекать из него побочные продукты неэкономично, единственное его применение — сжигание для производства технологического тепла, например, для приведения в движение брикетов или получения пара, который может пропускаться через турбины для выработки энергии.Если тепло не может быть экономически выгодно, то газ просто сжигается в высокой трубе.
Ростер Herreshoff интересен своей простотой. Он работает непрерывно, получая тепло, необходимое для окончательной сушки и карбонизации сырья, путем сжигания его части за счет контролируемого поступления воздуха в топки по мере продвижения материала сверху вниз. Если бы он мог обрабатывать древесину в виде кусков, это была бы идеальная непрерывная система.
Все другие предложенные системы непрерывного действия, а их много, основанные на движущихся лентах, винтовых конвейерах, псевдоожиженном слое и т.п., хотя они могут производить древесный уголь, обычно терпят неудачу по экономическим причинам.
В последнее время, особенно после роста цен на нефть в семидесятые годы, появился ряд систем, нацеленных на производство горячего газа для технологического нагрева взамен нефти или газа. Они основаны на сжигании мелко измельченной древесины или коры и т. Д. В камерах сгорания с контролируемым впуском воздуха и в некоторых случаях с использованием принципа сжигания в псевдоожиженном слое. с помощью этой системы слой опилок или другого топлива поддерживается во взвешенном состоянии путем продувки воздухом, а древесине позволяют сгореть во взвешенном состоянии с использованием кислорода в воздушной струе.Такие системы могут производить древесный уголь в порошкообразной форме, регулируя скорость подачи так, чтобы обугленные частицы древесины удалялись из псевдоожиженного слоя с достаточной скоростью, чтобы предотвратить их полное сгорание. Поддержание непрерывной работы системы, при которой печь не становится слишком горячей или слишком холодной, с сырьем с различным содержанием влаги и тонкостью помола, требует хорошего контроля. Такие системы могут быть интересны, потому что они могут быть построены намного меньше, чем хорошо зарекомендовавший себя обжарочный аппарат Herreshoff, для которого требуется около 100 тонн сырья в сутки в качестве минимальной загрузки.Были сделаны экстравагантные заявления о преимуществах, особенно от извлечения побочных продуктов, которые могут быть получены из таких систем, но, похоже, они все еще нуждаются в промышленном подтверждении. При желании побочные продукты могут быть собраны из газового потока, выходящего из конвертера, или горячий газ может быть сожжен в котле или печи. Поскольку они могут производить только порошкообразный древесный уголь, материал, имеющий довольно ограниченную коммерческую полезность, они вряд ли могут решить проблемы производства древесного угля улучшенными методами в развивающихся странах.
Карбонизаторы можно классифицировать по типу используемой системы отопления. Есть три разных типа.
Тип 1. Тепло для карбонизации генерируется путем сгорания части загруженной древесины, чтобы обеспечить теплом для карбонизации остальной части. Скорость горения регулируется количеством воздуха, поступающего в печь, яму, насыпь или реторту. Это традиционная система, используемая для производства большей части древесного угля в мире. Этот метод используется в хорошо зарекомендовавшем себя обжарочном аппарате Herreschoff.Это эффективная система при правильном управлении, поскольку тепло вырабатывается именно там, где оно необходимо, и нет проблем с теплопередачей. Карбонизаторы с псевдоожиженным слоем и другие типы карбонизаторов с мешалкой также полагаются на эту систему. Его главный недостаток в простом оборудовании заключается в том, что сгорает чрезмерное количество древесины, поскольку поступающий воздух не контролируется.
Тип 2. Тепло для карбонизации этим методом получают путем сжигания топлива, обычно древесины или, возможно, древесного газа, вне реторты и обеспечения его прохождения через стенки к древесине, содержащейся в герметичной реторте.Большинство ранних ретортных систем, построенных для подачи химикатов для древесины до подъема нефтехимической промышленности, обогревались этой системой. Система довольно неэффективна в использовании тепловой энергии, так как трудно получить хороший поток тепла через металлические стенки реторты в упакованную внутри древесину, поскольку контакт древесины со стенками настолько неравномерен. Часто происходит перегрев стенок реторты, что приводит к их повреждению. Этот метод все еще используется сегодня для некоторых реторт простого типа, таких как «реторта масляного барабана», которая была продвинута в Карибском бассейне, и реторта Константина, разработанная в Австралии (19).
Тип 3. В этой системе древесина нагревается за счет прямого контакта с горячим инертным газом, циркулирующим под давлением вентилятора через реторту. Передача тепла этой системой хорошая, поскольку горячий газ напрямую контактирует с нагреваемой древесиной. Поскольку газ не содержит кислорода, внутри реторты не происходит горения, а теплопередача охлаждает газ, который необходимо отводить и повторно нагревать, чтобы его можно было снова использовать для обогрева.
Самыми известными примерами этой системы являются ретортные системы с ламбиотом и Reichert.Реторта для ламбиота или непрерывного горячего промывочного газа описана в п. 2.7 выше. Реторта Reichert — это реторта периодического действия, которая нагревает древесную загрузку, чтобы преобразовать ее в древесный уголь, путем циркуляции горячего бескислородного газа через загрузку с помощью вентилятора и системы нагревательных печей. Во многих отношениях эта система напоминает реторту для промывочного газа периодического действия без преимущества непрерывной подачи. Другой пример — печь Шварца, разработанная много лет назад в Европе. Эта печь имеет внешнюю топку или решетку, и горячий дымовой газ от дров, сжигаемых в этой решетке, проходит через загрузку для ее нагрева.Объединенные отходящие газы проходят вверх по дымовой трубе печи в воздух.
Эта система отопления, хотя и превосходна в технологическом отношении, более сложна, чем Система 1 (сжигание части загруженной древесины), и, если нет веских причин для ее использования, как в случае с ретортой для горячего промывочного газа, стоимость использования его нельзя оправдать по сравнению с простым процессом Системы 1. Более подробная информация по этим аспектам приведена в Главе 3 и Справочнике (33).
2.9.1 Древесный уголь
2.9.2 Пиролиновая кислота
Карбонизация древесины приводит к появлению сложной номенклатуры изделий; твердые, жидкие и газообразные. Десятки химикатов можно было бы извлечь из жидкого конденсата, если бы это было экономически целесообразно.
Сегодня, когда индустрия дистилляции древесины затмевает, основной причиной обугливания древесины является получение древесного угля. Любые выгоды, которые можно получить от переработки побочных продуктов в настоящее время, незначительны, а в случае новых установок, вероятно, нерентабельны.Ниже приведены свойства основных продуктов, которые могут быть получены при карбонизации древесины. Древесный уголь из-за его важности рассматривается более подробно.
2.9.1 Древесный уголь
2.9.1.1 Влагосодержание
2.9.1.2 Летучие кроме воды
2.9.1.3 Фиксированное содержание углерода
2.9.1.4 Зольность
2.9.1.5 Обычный древесный уголь анализ
2.9.1.6 Физические свойства
2.9.1.7 Адсорбционная способность
2.9.1.8. химический состав древесного угля
Большинство спецификаций, используемых для контроля качества древесного угля, были разработаны в сталелитейной или химической промышленности. при экспорте древесного угля покупатели, как правило, используют эти промышленные требования к качеству, даже несмотря на то, что основным рынком сбыта импортного древесного угля может быть рынок домашней кулинарии или барбекю. Этот фактор следует иметь в виду, поскольку промышленные и бытовые требования не всегда одинаковы, и разумная оценка фактических требований рынка к качеству может позволить поставки подходящего древесного угля по более низкой цене или в больших количествах, выгодных как для покупателя, так и для продавца.
Качество древесного угля определяется различными свойствами, и, хотя все они в определенной степени взаимосвязаны, они измеряются и оцениваются отдельно. Эти различные факторы качества обсуждаются ниже.
2.9.1.1 Влагосодержание
Древесный уголь, только что полученный из открытой печи, содержит очень мало влаги, обычно менее 1%. Поглощение влаги из влажности самого воздуха происходит быстро, и со временем происходит увеличение влажности, которое даже без увлажнения дождем может довести содержание влаги до 5-10% даже в хорошо обожженном древесном угле.Когда древесный уголь не сжигается должным образом или когда пиролиновые кислоты и растворимые смолы были смыты дождем на древесный уголь, как это может случиться при сжигании ям и насыпей, гигроскопичность древесного угля увеличивается, а естественное или равновесное содержание влаги в древесном угле может возрасти до 15% и даже больше.
Влага является примесью, которая снижает теплотворную способность или теплотворную способность древесного угля. Там, где древесный уголь продается на вес, поддержание высокого содержания влаги путем смачивания водой часто практикуется нечестными торговцами.Объем и внешний вид древесного угля практически не изменяется при добавлении воды. По этой причине оптовые покупатели древесного угля предпочитают покупать либо валовым объемом, например. в кубических метрах, или купить на вес и определить с помощью лабораторных испытаний влажность и скорректировать цену для компенсации. На небольших рынках продажа часто идет поштучно.
Практически невозможно предотвратить случайное увлажнение древесного угля дождем во время транспортировки на рынок, но хорошая практика заключается в хранении древесного угля под крышкой, даже если он был закуплен в больших количествах, поскольку содержащаяся в нем вода должна испаряться при горении и представляет собой прямую потерю мощности нагрева.Это происходит потому, что испарившаяся вода попадает в дымоход и редко конденсируется, чтобы отдать тепло, которое она содержит на предмете, нагреваемом в печи.
Спецификации качества древесного угля обычно ограничивают содержание влаги примерно 5-15% от общего веса древесного угля. Содержание влаги определяется сушкой в печи взвешенного образца древесного угля. Выражается в процентах от начальной влажной массы.
Имеются данные о том, что древесный уголь с высоким содержанием влаги (10% или более) имеет тенденцию к дроблению и образованию мелких частиц при нагревании в доменной печи, что делает его нежелательным при производстве чугуна.
2.9.1.2 Летучие вещества, кроме воды
Летучие вещества, содержащиеся в древесном угле, кроме воды, включают все те жидкие и смолистые остатки, которые не полностью удаляются в процессе карбонизации. Если карбонизация продолжительна и при высокой температуре, то содержание летучих веществ низкое. Когда температура карбонизации низкая и время нахождения в реторте короткое, содержание летучих веществ увеличивается. (33)
Эти эффекты отражаются на выходе древесного угля, произведенного из древесины заданной массы.при низких температурах (300 C) возможен выход древесного угля около 50%. При температурах карбонизации 500-600 ° C летучие вещества ниже, и выход реторты обычно составляет 30%. При очень высоких температурах (около 1000 ° C) содержание летучих почти равно нулю, а выходы падают примерно до 25%. Как указывалось ранее, древесный уголь может реабсорбировать смолы и пиролиновые кислоты из дождевой воды при сжигании ям и аналогичных процессах. Таким образом, древесный уголь может хорошо сгореть, но из-за этого фактора в нем будет высокое содержание летучих веществ.Это вызывает дополнительные вариации в угле, сгоревшем в яме! влажный климат. Резорбированные кислоты вызывают коррозию древесного угля и приводят к гниению джутовых мешков, что является проблемой во время транспортировки. Также он не горит чисто.
Летучие вещества в древесном угле могут варьироваться от 40% или более до 5% или менее. Он измеряется путем нагревания вдали от воздуха взвешенного образца сухого угля при 900 ° C до постоянного веса. Потеря веса — это летучая вещь. Летучие вещества обычно указываются без содержания влаги, т.е.е. летучие вещества — влага или (В.М. — влага)
Высоколетучий древесный уголь легко воспламеняется, но может гореть дымным пламенем. Древесный уголь с низким содержанием летучих веществ трудно разжечь, и он очень чисто горит. Хороший коммерческий древесный уголь может иметь чистое содержание летучих веществ (без влаги) около 30%. Древесный уголь с высоким содержанием летучих веществ менее хрупкий, чем обычный твердый уголь с низким содержанием летучих веществ, поэтому при транспортировке и погрузочно-разгрузочных работах образуется меньше мелких частиц. Кроме того, он более гигроскопичен и, следовательно, имеет более высокое естественное содержание влаги.
2.9.1.3 Фиксированное содержание углерода
Содержание фиксированного углерода в древесном угле колеблется от низкого примерно 50% до высокого примерно 95%. Таким образом, древесный уголь состоит в основном из углерода. Содержание углерода обычно оценивается как «разница», то есть все остальные составляющие вычитаются из 100 в процентах, а остаток принимается как процент «чистого» или «фиксированного» углерода. Содержание фиксированного углерода является наиболее важным компонентом в металлургии, поскольку именно фиксированный углерод отвечает за восстановление оксидов железа в железной руде с образованием металла.Но промышленный пользователь должен найти баланс между рыхлой природой древесного угля с высоким содержанием связанного углерода и большей прочностью древесного угля с более низким содержанием связанного углерода и более высоким содержанием летучих веществ для достижения оптимальной работы доменной печи. (33)
2.9.1.4 Зольность
Зольность определяется путем нагревания взвешенной пробы до красного тепла с доступом воздуха для сжигания всех горючих веществ. Этот остаток — зола. Это минеральные вещества, такие как глина, кремнезем, оксиды кальция и магния и т. Д., оба присутствуют в исходной древесине и собраны в виде загрязнения из земли во время обработки.
Зольность древесного угля варьируется от 0,5% до более 5% в зависимости от породы древесины, количества коры, содержащейся в древесине в печи, и количества загрязнения землей и песком. Кусковой древесный уголь хорошего качества обычно имеет зольность около 3%. Мелкодисперсный древесный уголь может иметь очень высокое содержание золы, но если просеивается материал менее 4 мм, остаток плюс 4 мм может иметь зольность около 5-10%.
2.9.1.5 Типичный анализ древесного угля
Чтобы проиллюстрировать диапазон состава товарного древесного угля, в таблице 1 приведен состав случайных образцов древесного угля из различных пород древесины и различных систем карбонизации. В общем, из любой древесины и всех систем карбонизации можно производить древесный уголь, не выходя из коммерческих ограничений.
В таблице 2 приведены изменения в составе древесного угля, обнаруженные в шихте доменной печи на большом угольном заводе в Минас-Жерайсе, Бразилия.Весь этот древесный уголь был изготовлен с использованием кирпичных печей типа улей. Используемая древесина была либо смешанной породой из естественных лесов региона, либо древесиной эвкалипта с плантаций.
Таблица 1. Некоторые типичные анализы древесного угля
Порода древесины Метод производства | Влагосодержание % | Ясень % | Летучие вещества -% | Углерод фиксированный % | Насыпная плотность сырца, кг / м 3 | Насыпная плотность в измельченном виде кг / м 3 | Высшая теплотворная способность кДж / кг Сухая масса для печи | Примечания | |
Дакама | Земляной котлован | 7.5 | 1,4 | 16,9 | 74,2 | 314 | 708 | 32410 | Пылевидное топливо для вращающихся печей 1 / |
Wallaba | » | 6.9 | 1,3 | 14,7 | 77,1 | 261 | 563 | 35580 | 1 / |
Каутабалли | » | 6.6 | 3,0 | 24,8 | 65,6 | 290 | 596 | 29990 | 1 / |
Тропическая древесина смешанных пород | » | 5.4 | 8,9 | 17,1 | 68,6 | Мелкие частицы древесного угля низкого качества 1 / | |||
» | » | 5.4 | 1,2 | 23,6 | 69,8 | Уголь домашний 1 / | |||
Wallaba | Земляной холм | 5.9 | 1,3 | 8,5 | 84,2 | Образец хорошо обожженного 1/ | |||
» | » | 5.8 | 0,7 | 46,0 | 47,6 | Образец мягкого обжига 1/ | |||
Дуб | Переносная печь для обжига стали | 3.5 | 2,1 | 13,3 | 81,1 | 32500 | 2/ | ||
скорлупа кокоса | » | 4.0 | 1,5 | 13,5 | 83,0 | 30140 | 4/ | ||
Эвкалипт Салинья | Реторта | 5.1 | 2,6 | 25,8 | 66,8 | 3/ |
1 / = Гайана. 2 / = Великобритания 3 / = Бразилия. 4 / = Фиджи.
Таблица 2. Характеристики древесного угля для доменных печей
Химический и физический состав сухой основы древесного угля — весовая | Диапазон Макс.Мин. | Среднее значение за год | Древесный уголь считается отличным одолженным | |
Углерод | 80% | 60% | 70% | 75 — 80% |
Ясень | 10% | 3% | 5% | 3–4% |
Летучие вещества | 26% | 15% | 25% | 20–25% |
Насыпная плотность — при получении (кг / м³) | 330 | 200 | 260 | 250–300 |
Насыпная плотность — сухая | 270 | 180 | 235 | 230–270 |
Средний размер (мм) при получении | 60 | 10 | 35 | 20–50 |
Содержание штрафов — в полученном виде (<6.35 мм) | 22% | 10% | 15% | 10% макс. |
Содержание влаги — при получении | 25% | 5% | 10% | 10% макс. |
Диапазоны и среднегодовые значения относятся к древесному углю, используемому на металлургических заводах. Это смесь 40% древесного угля эвкалипта, произведенного в печах, эксплуатируемых компанией, и 60% древесного угля из гетерогенной древесины, произведенного в печах, эксплуатируемых в частном порядке. Древесный уголь «от хорошего до превосходного» относится к углю, производимому из древесины эвкалипта в печах компании.
2.9.1.6 Физические свойства
Свойства, описанные до сих пор, называются химическими, но физические свойства, особенно для промышленного древесного угля, не менее важны.Физические свойства имеют большое значение в производстве древесного угля. Древесный уголь — самое дорогое сырье в шихте доменной печи. Физические свойства древесного угля влияют на производительность доменной печи, тогда как химические свойства больше связаны с количеством древесного угля, необходимого на тонну чугуна, и составом готового чугуна или стали. (29)
Доменный уголь должен быть прочным на сжатие, чтобы выдерживать раздавливающую нагрузку доменной шихты типа «шихта».Эта прочность на сжатие, всегда меньшая, чем у конкурента древесного угля, металлургического кокса из угля, определяет практическую высоту и, следовательно, эффективность и производительность доменной печи. Способность противостоять растрескиванию при обращении с ним важна для поддержания постоянной проницаемости шихты печи для воздушного потока, что имеет жизненно важное значение для поддержания производительности печи и единообразия операций.
Были разработаны различные тесты для измерения сопротивления разрушению; свойство довольно сложно определить объективно.Эти испытания основаны на измерении устойчивости древесного угля к разрушению или разрушению, позволяя образцу упасть с высоты на твердый стальной пол или путем сотрясения образца в барабане для определения разрушения по размеру через заданное время. Результат выражается в процентах прохождения и удержания на экранах различного размера. Древесный уголь с плохой стойкостью к растрескиванию дает больший процент мелких частиц при испытании образца. Уголь мелкой фракции нежелателен в доменной печи, так как он блокирует поток воздуха, дующего в печь.Хрупкий древесный уголь также может раздавиться под тяжестью заряда и вызвать засорение.
2.9.1.7 Адсорбционная способность
Древесный уголь — важное сырье для производства активированного угля. (См. Главу 6). Некоторые данные могут быть полезны в тех случаях, когда производители древесного угля продают древесный уголь, который будет превращен в активированный уголь на специализированных предприятиях. (27)
В процессе производства обычный древесный уголь не является очень активным адсорбционным материалом для жидкостей или паров, поскольку его мелкодисперсная структура заблокирована смолистыми остатками.Чтобы превратить древесный уголь в «активированный», эту структуру необходимо вскрыть, удалив смолистые остатки. Наиболее широко используемый сегодня метод заключается в нагревании измельченного древесного угля в печи до слабого красного каления в атмосфере перегретого пара. Пар предотвращает сгорание древесного угля, исключая кислород. Между тем летучие смолы можно отогнать и унести с паром, оставляя структуру пор открытой. Обработанный древесный уголь сливают в закрытые емкости и дают остыть.Активационные печи обычно являются непрерывными, то есть порошкообразный древесный уголь непрерывно проходит каскадно через горячую печь в атмосфере пара.
После активации древесный уголь проверяется на соответствие требованиям качества, чтобы определить его способность обесцвечивать путем адсорбции водянистые растворы, такие как сок сахара-сырца, ромовое вино и т. Д.; масла, такие как растительное масло, и для адсорбции растворителей, таких как этилацетат, в воздухе. Адсорбционная способность обычно бывает специфической. Сорта производятся для водных растворов, другие — для масел, а другие — для паров.Испытания измеряют адсорбционную способность. Есть небольшие различия в готовом продукте, изготовленном из необработанного древесного угля разного происхождения, но, как правило, все они пригодны для использования при правильном сжигании. Хороший базовый уголь для производства активированного угля может быть получен из древесины Eucalyptus grandis в кирпичных печах.
Древесный уголь для адсорбции газов и паров обычно производится из древесного угля из скорлупы кокосовых орехов. Этот древесный уголь обладает высокой адсорбционной способностью и сопротивляется измельчению в адсорбционном оборудовании — очень важный фактор.
2.9.1.8 Химический состав древесного угля
В состав древесного угля входят углерод, смола и зола. Относительные пропорции каждого из них отражают зольность древесины, из которой был сделан древесный уголь, и температуру, при которой карбонизация была прекращена. Чтобы дать представление о том, как эти значения могут варьироваться, приводятся следующие данные, полученные из работы по австралийскому эвкалипту. См. Таблицы 3 и 4. (11, 24). Хотя многие виды были изучены, здесь приводятся результаты только для двух видов, представляющих международный интерес, Eucalyptus saligna и camaldulensis.Более полная таблица этих результатов приведена в (20).
Таблица 3 Летучие вещества и выход древесного угля при различных температурах
Виды | Температура карбонизации C | ||||||||
350 | 400 | 450 | 500 | 590 | 700 | 800 | 950 | ||
Euc camaldulensis | |||||||||
% летучих | 39.4 | 35,8 | 31 | 26 | 16,7 | 4,4 | 0 | 0 | |
% доходность | 49.7 | 46,8 | 43,6 | 40,7 | 36,2 | 31,5 | 30,1 | 30,1 | |
Euc saligna | |||||||||
% летучих | 40.4 | 37,8 | 30 | 24,9 | 15,8 | 4,1 | 0 | 0 | |
% доходность | 49.9 | 47,9 | 42,6 | 39,8 | 35,4 | 31,1 | 29,8 | 29,8 | |
Среднее значение 15 видов | |||||||||
% летучих | 39.8 | 35,3 | 29,9 | 24,6 | 16,2 | 4,6 | ,5 | 0 | |
% доходность | 47.4 | 44,1 | 40,7 | 37,8 | 34,1 | 30 | 28,7 | 28,5 |
Таблица 4 Неорганическое содержание коры заболони и сердцевины древесины
Виды | В процентах | частей на миллион | ||||||||||||
% Ясень | % кремнезема | п. | Ca | мг | К | Na | AL | Fe | Mn | Zn | S | Класс | ||
Euc camaldulensis | ||||||||||||||
кора | 9.65 | 1,768 | 385 | 32150 | 2765 | 4185 | 1060 | 130 | 70 | 415 | 15 | — | 2455 | |
заболонь | .49 | .004 | 155 | 675 | 220 | 1858 | 303 | 20 | 38 | 83 | 5 | — | 910 | |
сердцевина | .07 | след | 14 | 235 | 100 | 53 | 33 | 8 | 18 | 7 | 4 | — | — | |
Euc saligna | ||||||||||||||
кора | 9.19 | 1,208 | 185 | 32030 | 1700 | 3250 | 1955 | 125 | 75 | 330 | 8 | 1660 | 2615 | |
заболонь | .43 год | 0,056 | 100 | 550 | 250 | 900 | 215 | 15 | 50 | 15 | 9 | 660 | 440 | |
сердцевина | .07 | .002 | 5 | 280 | 60 | 100 | 60 | 10 | 25 | 4 | 4 | 340 | 65 |
2.9.2 Пиролигнистая кислота
2.9.2.1 Уксусная кислота
2.9.2.2 Метанол и ацетон
2.9.2.3 Смолы
Водяной конденсат паров, покидающих реторту, известен как пиролиновая кислота. нерастворимые в воде смолы одновременно конденсируются и отделяются от водной фазы при стоянии. Состав пиролининовой кислоты чрезвычайно сложен, и можно упомянуть только основные составляющие. Урожайность важна для определения экономики восстановления и зависит от типа обугленной древесины.Европейский бук, древесина твердых пород, которая сформировала основу европейской промышленности, имеет высокое содержание пентозановых сахаров, что дает высокий выход ценной уксусной кислоты. С другой стороны, древесина эвкалипта дает гораздо меньший выход уксусной кислоты и других продуктов. Тип установки карбонизации также влияет на урожайность. Невозможно дать определенные прогнозы урожайности; Прежде чем вкладывать деньги в восстановление побочных продуктов, необходимо провести точные крупномасштабные испытания.
Для справки, ниже приведены типичные выходы, полученные при использовании пиролиевой кислоты, полученной при карбонизации лиственных пород северного полушария.
Урожайность на 1000 кг воздушно-сухой древесины | |
уксусная кислота | 50 кг |
Метанол | 16 кг |
Ацетон и метилацетон | 8 кг |
Смолы растворимые | 190 кг |
Смолы нерастворимые | 50 кг |
2.9.2.1 Уксусная кислота
Уксусная кислота является наиболее ценным продуктом с точки зрения общей денежной прибыли, которую можно извлечь из пиролиновой кислоты. Хотя количество уксусной кислоты, продаваемой в качестве побочного продукта при перегонке древесины в настоящее время, довольно невелико, кислота от перегонки древесины востребована для определенных целей, поскольку она достаточно чиста. Метод, используемый для извлечения кислоты из конденсата, обычно представляет собой экстракцию растворителем неочищенного кислого щелока с использованием этилацетата после разделения растворимых смол и метанола / ацетона.Уксусная кислота переходит в этилацетатную фазу. Этилацетат выделяют в аппарате и возвращают в экстракционную колонну. Уксусную кислоту очищают перегонкой. Могут быть произведены несколько марок, которые различаются по чистоте и содержанию кислоты.
2.9.2.2 Метанол и ацетон
В связи с низкими ценами на эти продукты, производимые нефтехимическим способом, и высокой стоимостью отделения их как чистых сортов от пиролистной кислоты, их обычно извлекают в виде смеси, которая также содержит метилацетон.Смесь продается как растворитель для использования в лакокрасочной промышленности.
Смешанный растворитель восстанавливается путем перегонки водной фазы после декантации нерастворимого гудрона. Жидкость перегоняется в первичном кубе, а уксусная кислота, метанол, ацетон и т. Д. Варятся. Растворимые смолы остаются в аппарате. Пары фракционируют в колонне, и фракция неочищенного смешанного метанольного растворителя (около 85% метанола) отделяется от смеси уксусной кислоты и воды. Эту последнюю смесь очищают, как описано выше, экстракцией уксусной кислоты растворителем.Неочищенный метанол может быть подвергнут дальнейшей очистке, но цена, как правило, этого не позволяет, и он продается как смешанный растворитель.
2.9.2.3 Смолы
Нерастворимый деготь является полезным продуктом в ветеринарии в качестве антисептика, а также в качестве средства защиты древесины и герметика. Полученный путем перегонки древесины хвойных пород, его обычно называют стокгольмским дегтем. Его просто декантацией от конденсата. Ароматические вещества, ценные в медицине и парфюмерии, можно отделить от этой смолы сложными химическими процессами.Если бы этот гудрон производился в развивающихся странах, он, вероятно, нашел бы его на местных рынках по разумной цене.
Растворимую смолу труднее продать. Этот материал представляет собой сложную смесь высококонденсированных, но смешиваемых с водой веществ, для которых, похоже, существует очень мало применений. Его использовали в качестве добавки к глине при производстве кирпича для производства пористых кирпичей, и, конечно же, его можно сжигать в качестве топлива.
Смолы, образующиеся при перегонке древесины, должны признаваться загрязняющими веществами в окружающей среде и, следовательно, не должны попадать в потоки.Сточные щелоки всех видов, образующиеся при регенерации побочных продуктов, должны сбрасываться в закрытые неглубокие пруды, а воде позволять испариться, оставляя смолистые остатки. После того, как они накопились, их можно сжечь, чтобы исключить риск, который они представляют для потока жизни, рыбы, водных ресурсов и т. Д. Этот метод хорошо работает в районах, где чистое испарение превышает чистое количество осадков, то есть там, где древесный уголь производится в полузасушливом климате, но во влажных тропиках он явно не работает.
В качестве альтернативы можно сжигать смолы и все летучие вещества, кроме водного компонента.Во многих отношениях это лучший способ использования материала, чем инвестирование в схемы восстановления побочных продуктов. Из-за большого количества энергии, необходимой для испарения воды, лучше всего сжигать смесь газа и конденсируемых газов как горячий неконденсированный газ как можно ближе к оборудованию для карбонизации.
.